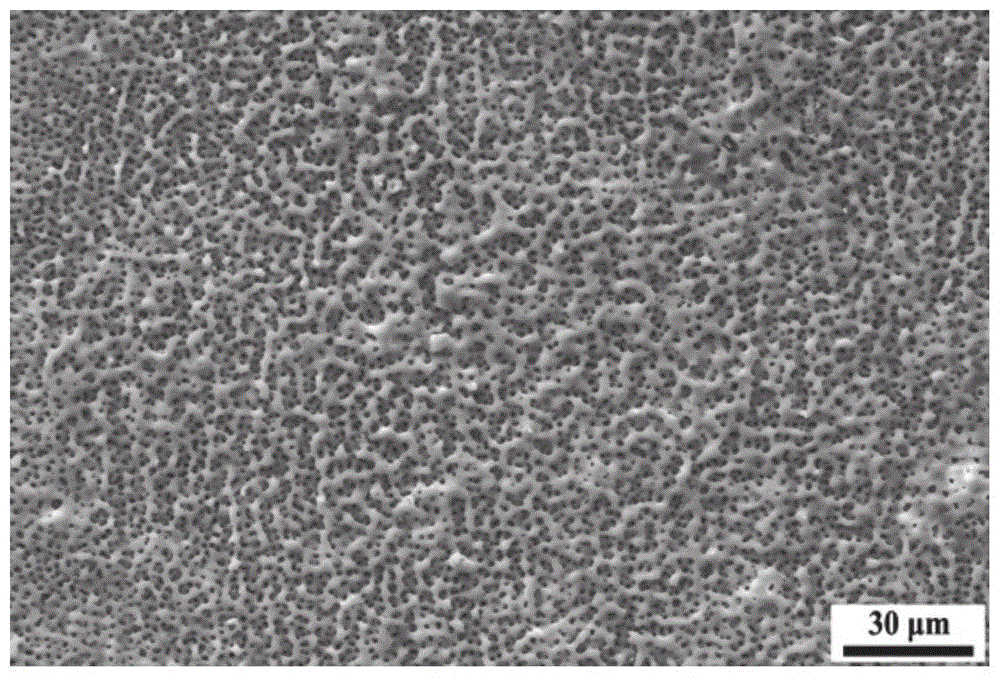
本发明涉及材料表面处理领域,具体涉及一种镁合金超高孔隙率微弧氧化涂层及其制备方法与应用。
背景技术:
公开该背景技术部分的信息仅仅旨在增加对本发明的总体背景的理解,而不必然被视为承认或以任何形式暗示该信息构成已经成为本领域一般技术人员所公知的现有技术。
近年来,微弧氧化技术在镁合金表面处理领域内的应用愈来愈广泛。利用微弧氧化技术可以在镁合金表面制备形成一层以氧化镁为主相的陶瓷涂层,该陶瓷涂层不仅与基体结合牢固,而且具有硬度高、绝缘性好等特点,因此可以大幅增强镁合金基体的耐磨性、耐腐蚀性。
从涂层表面的微观组织结构上讲,微弧氧化涂层最显著的特点就是其并不是一层完全封闭的涂层,而是在其最外层中分布着一些显微孔洞。这些孔洞是由于微弧氧化过程中高压放电击穿所遗留下来的痕迹,是微弧氧化技术所不可避免的。之前,为了使镁合金具有更高的耐蚀性和机械性能,大量的研究均致力于如何减少甚至完全去除微弧氧化处理后涂层中的孔洞结构。
近年来,随着镁合金在各种特殊功能领域内的拓展应用,提高镁合金的比表面积对于其功能实现和表达显示出愈加重要的意义。一些研究者敏锐地认识到,镁合金表面微弧氧化涂层中的显微孔洞结构在诸如催化、能源、环境等领域内是一种有益结构。因此,在某些场合下,使微弧氧化涂层中的显微孔洞结构更发达、涂层孔隙率更高反而成为一种新的追求目标。
先前,研究者在减少微弧氧化涂层中孔洞结构的技术途径中最常用的就是通过调节微弧氧化过程中的各种电参数,从而控制微弧放电击穿效应,进而优化孔洞的生长。然而,发明人发现在期望获得发达微弧氧化涂层中孔洞结构时,利用上述的反向调节工艺参数进行微弧氧化处理却往往导致微弧氧化涂层的结构疏松、结合强度下降、机械性能大幅降低。可见,开发具有优良结合强度和机械性能的超高孔隙率微弧氧化涂层具有重要意义。
技术实现要素:
为了解决现有技术的不足,本发明提供了一种镁合金超高孔隙率微弧氧化涂层及其制备方法与应用,该方法充分结合了阴极微弧电沉积处理和阳极微弧氧化处理的各自优势,仅用一套电源装置即可制备形成高质量的目标涂层,得到具有优良结合强度和机械性能的超高孔隙率微弧氧化涂层,为镁合金超高孔隙率微弧氧化涂层的制备提供了一种新思路。
为实现上述技术目的,本发明第一方面提供一种镁合金超高孔隙率微弧氧化涂层的制备方法,其特征在于,所述制备方法包括以下步骤:
(1)将清洗干净的镁合金样品置于浸蚀液中进行预处理;
(2)将预处理后的镁合金样品置于超声波清洗液中进行超声波清洗,之后取出吹干待用;
(3)将超声波清洗后的样品置于阻挡膜制备液中进行超声波浸泡处理,之后取出样品置于烘箱中烘干固化,结束后取出冷却待用;
(4)将步骤(3)所得样品置于阴极电解液中,以该样品作阴极,以石墨片作阳极,进行阴极微弧电沉积处理;
(5)将阴极微弧电沉积处理后的样品置于阳极电解液中,以该样品作阳极,以不锈钢作阴极,进行阳极微弧氧化处理;
(6)将样品依次用水和乙醇冲洗干净,吹干。
本发明第二方面提供一种上述制备方法得到的超高孔隙率微弧氧化涂层,所述微弧氧化涂层孔隙率不低于50%,微孔孔径为0.5~3μm。
本发明第三方面提供一种上述的镁合金超高孔隙率微弧氧化涂层在环境、催化、能源、军工、航天航空及汽车、纺织或机械领域的应用。
本发明的一个或多个具体实施方式至少具有以下有益效果:
(1)镁合金依次经过预处理、超声波清洗、阻挡膜制备、阴极微弧电沉积处理和阳极微弧氧化处理后,可在合金表面制备一具有优良结合强度和机械性能的超高孔隙率微弧氧化涂层,该微弧氧化涂层孔隙率不低于50%,微孔孔径为0.5~3μm。
(2)本发明所述镁合金超高孔隙率微弧氧化涂层的制备方法,各步骤压茬进行、目标明确,充分结合了阴极微弧电沉积处理和阳极微弧氧化处理的各自优势,仅用一套电源装置即可形成高质量的目标涂层。
(3)本发明为镁合金超高孔隙率微弧氧化涂层的制备提供了一种新思路,对推广高比表面积镁合金在催化、能源、环境等领域内的应用也有一定的价值。
附图说明
构成本发明的一部分的说明书附图用来提供对本发明的进一步理解,本发明的示意性实施例及其说明用于解释本发明,并不构成对本发明的不当限定。
图1为本发明实施例1制备的涂层的表面显微形貌图;
图2为本发明实施例1制备的涂层经划格法进行涂层附着力测试后的表面形貌图;
图3为本发明实施例2制备的涂层的表面显微形貌图;
图4为对比例1中制备的涂层的表面显微形貌图;
图5为对比例2中制备的涂层的表面显微形貌图。
具体实施方式
应该指出,以下详细说明都是示例性的,旨在对本发明提供进一步的说明。除非另有指明,本文使用的所有技术和科学术语具有与本发明所属技术领域的普通技术人员通常理解的相同含义。
需要注意的是,这里所使用的术语仅是为了描述具体实施方式,而非意图限制根据本发明的示例性实施方式。如在这里所使用的,除非上下文另外明确指出,否则单数形式也意图包括复数形式,此外,还应当理解的是,当在本说明书中使用术语“包含”和/或“包括”时,其指明存在特征、步骤、操作、器件、组件和/或它们的组合。
正如背景技术所介绍的,针对采用反向调节微弧氧化工艺参数来获得发达孔洞结构时会导致微弧氧化涂层的结构疏松、结合强度下降、机械性能大幅降低的问题,本发明提出了一种镁合金超高孔隙率微弧氧化涂层的制备方法,其特征在于,所述制备方法包括以下步骤:
(1)将清洗干净的镁合金样品置于浸蚀液中进行预处理;
(2)将预处理后的镁合金样品置于超声波清洗液中进行超声波清洗,之后取出吹干待用;
(3)将超声波清洗后的样品置于阻挡膜制备液中进行超声波浸泡处理,之后取出样品置于烘箱中烘干固化,结束后取出冷却待用;
(4)将步骤(3)所得样品置于阴极电解液中,以该样品作阴极,以石墨片作阳极,进行阴极微弧电沉积处理;
(5)将阴极微弧电沉积处理后的样品置于阳极电解液中,以该样品作阳极,以不锈钢作阴极,进行阳极微弧氧化处理;
(6)将样品依次用水和乙醇冲洗干净,吹干。
其中,预处理的目的是在镁合金基体上形成密集的点蚀坑,使得后续涂层的生长在粗糙的基体上进行,有利于提高涂层的孔隙率。
超声波清洗的目的一方面是清除掉预处理反应生成的疏松腐蚀产物,另一方面是在碱性的溶液环境中中和预处理残留的酸液又不至于引起新的腐蚀。
阻挡膜制备的目的是在合金基体表面上固化一层绝缘涂层,以利于阴极微弧电沉积处理过程中的起弧放电。
阴极微弧电沉积处理的目的一方面是利用阴极电解液中的有效成分进行膜层的生长,防止直接进行阳极微弧氧化处理对预处理过程中制备的点蚀坑的边缘引发优先熔融从而削弱预处理的作用;另一方面是防止直接进行阳极微弧氧化处理容易在合金表面的显微尖端局部发生异常放电而导致涂层结构疏松、机械性能降低。
阳极微弧氧化处理的目的是通过各种电参数和电解液组分的配合最终制备一具有优良结合强度和机械性能的超高孔隙率微弧氧化涂层。
在本发明的一个或多个实施方式中,所述步骤(1)中,预处理的操作条件为:浸蚀液温度为10~30℃,处理时间为15~50s;浸蚀液的组成为:磷酸体积分数5~15%、氟化钠0.5~3g/l、其余为水。
在本发明的一个或多个实施方式中,所述步骤(2)中,超声波清洗的操作条件为:超声波清洗液温度为10~35℃,清洗时间为1~5min;所述超声波清洗液的组成为:氢氧化钠3~8g/l、柠檬酸铵0.5~3g/l、其余为水。不限定超声波频率,常用的超声波清洗设备(30-100khz)均可。
在本发明的一个或多个实施方式中,所述步骤(3)中,阻挡膜制备的操作条件为:浸泡时间30~60s,烘干温度为80~150℃,烘干时间为15~30min;
所述阻挡膜制备液的组成为:三硅酸镁5~10g/l、乙二醇5~20ml/l、其余为乙醇。
在本发明的一个或多个实施方式中,所述步骤(4)中,阴极微弧电沉积处理的操作条件为:电压为100~250v,占空比为10~30%,频率为80~150hz,时间为2~4min。
在本发明的一个或多个实施方式中,所述阴极电解液的组成为:硝酸铝50~100g/l、其余为乙醇。
在本发明的一个或多个实施方式中,所述步骤(5)中,阳极微弧氧化处理的操作条件为:电压为300~450v,占空比为5~30%,频率为500~1000hz,时间为3~10min。
在本发明的一个或多个实施方式中,所述阳极电解液的组成为:六偏磷酸钠2~10g/l、二水合氟化钾5~15g/l、硝酸银0.2~3g/l、葡萄糖0.2~3g/l、其余为水,电解液使用前需缓慢滴加氨水使溶液由澄清变浑浊并再次变澄清为止。
本发明第二方面提供一种上述制备方法得到的超高孔隙率微弧氧化涂层,所述微弧氧化涂层孔隙率不低于50%,微孔孔径为0.5~3μm。
本发明第三方面提供一种上述的镁合金超高孔隙率微弧氧化涂层在环境、催化、能源、军工、航天航空及汽车、纺织或机械领域的应用。
为了使得本领域技术人员能够更加清楚地了解本发明的技术方案,以下将结合具体的实施例与对比例详细说明本发明的技术方案。
实施例1
将镁合金按照如下步骤进行处理:
(1)将清洗干净的镁合金样品置于组成为:磷酸体积分数10%、氟化钠1.5g/l、其余为水的浸蚀液中进行预处理,浸蚀液温度为20℃,浸泡20s。
(2)将样品从浸蚀液中取出,用水冲洗后,置于组成为:氢氧化钠5g/l、柠檬酸铵1.5g/l、其余为水的超声波清洗液中进行超声波清洗,超声波清洗液温度为25℃,清洗3min,之后取出样品吹干待用。
(3)将经过第(2)步处理所得样品置于组成为:三硅酸镁8g/l、乙二醇15ml/l、其余为乙醇的阻挡膜制备液中进行超声波浸泡处理,浸泡时间40s,之后取出样品置于烘箱中烘干固化,烘干温度100℃,烘干时间20min,结束后取出冷却待用。
(4)将经过第(3)步处理所得样品置于组成为:硝酸铝80g/l、其余为乙醇的阴极电解液中,以待处理样品作阴极,以石墨片作阳极,进行阴极微弧电沉积处理,施加电压150v,占空比15%,频率100hz,时间3min。
(5)将经过第(4)步处理所得样品置于按如下组成配置的阳极电解液:六偏磷酸钠5g/l、二水合氟化钾10g/l、硝酸银1g/l、葡萄糖1g/l、其余为水、最后缓慢滴加氨水使溶液由澄清变浑浊并再次变澄清为止,以待处理样品作阳极,以不锈钢作阴极,进行阳极微弧氧化处理,施加电压380v,占空比8%,频率800hz,时间6min。
(6)依次用水和乙醇冲洗干净,吹干。
将制备所得样品进行扫描电镜观察,其表面显微形貌如图1所示,可以观察到,涂层表面孔洞结构发达,经统计分析,涂层孔隙率大于55%,微孔孔径为1.2μm。按照gb/t9286-1998标准通过划格法进行涂层附着力测试,测试后样品表面形貌如图2所示,结果显示该涂层附着力评级为1级。利用数显显微硬度计测量该涂层的显微硬度为813hv。
实施例2
将镁合金按照如下步骤进行处理:
(1)将清洗干净的镁合金样品置于组成为:磷酸体积分数15%、氟化钠3g/l、其余为水的浸蚀液中进行预处理,浸蚀液温度为20℃,浸泡40s。
(2)将样品从浸蚀液中取出,用水冲洗后,置于组成为:氢氧化钠5g/l、柠檬酸铵1.5g/l、其余为水的超声波清洗液中进行超声波清洗,超声波清洗液温度为25℃,清洗5min,之后取出样品吹干待用。
(3)将经过第(2)步处理所得样品置于组成为:三硅酸镁8g/l、乙二醇15ml/l、其余为乙醇的阻挡膜制备液中进行超声波浸泡处理,浸泡时间40s,之后取出样品置于烘箱中烘干固化,烘干温度100℃,烘干时间20min,结束后取出冷却待用。
(4)将经过第(3)步处理所得样品置于组成为:硝酸铝100g/l、其余为乙醇的阴极电解液中,以待处理样品作阴极,以石墨片作阳极,进行阴极微弧电沉积处理,施加电压200v,占空比20%,频率100hz,时间3min。
(5)将经过第(4)步处理所得样品置于按如下组成配置的阳极电解液:六偏磷酸钠5g/l、二水合氟化钾10g/l、硝酸银2g/l、葡萄糖2g/l、其余为水、最后缓慢滴加氨水使溶液由澄清变浑浊并再次变澄清为止,以待处理样品作阳极,以不锈钢作阴极,进行阳极微弧氧化处理,施加电压400v,占空比15%,频率600hz,时间10min。
(6)依次用水和乙醇冲洗干净,吹干。
将制备所得样品进行扫描电镜观察,其表面显微形貌如图3所示,可以观察到,涂层表面孔洞结构发达,经统计分析,涂层孔隙率大于60%,微孔孔径为1.4μm。涂层附着力测试结果显示该涂层附着力评级为1级。利用数显显微硬度计测量该涂层的显微硬度为861hv。
对比例1
将镁合金按照如下步骤进行处理:
(1)将清洗干净的镁合金样品置于组成为:磷酸体积分数10%、氟化钠1.5g/l、其余为水的浸蚀液中进行预处理,浸蚀液温度为20℃,浸泡20s。
(2)将样品从浸蚀液中取出,用水冲洗后,置于组成为:氢氧化钠5g/l、柠檬酸铵1.5g/l、其余为水的超声波清洗液中进行超声波清洗,超声波清洗液温度为25℃,清洗3min,之后取出样品吹干待用。
(3)将经过第(2)步处理所得样品置于按如下组成配置的阳极电解液:六偏磷酸钠5g/l、二水合氟化钾10g/l、硝酸银1g/l、葡萄糖1g/l、其余为水、最后缓慢滴加氨水使溶液由澄清变浑浊并再次变澄清为止,以待处理样品作阳极,以不锈钢作阴极,进行阳极微弧氧化处理,施加电压380v,占空比8%,频率800hz,时间6min。
(4)依次用水和乙醇冲洗干净,吹干。
将制备所得样品进行扫描电镜观察,其表面显微形貌如图4所示,可以观察到,涂层表面孔洞结构相比实施例1而言表现为欠发达,经统计分析,涂层孔隙率小于40%;另外,涂层上明显可见较疏松的组织,其面积占比可达50%;涂层附着力测试结果显示该涂层附着力评级为2级,硬度仅为214hv。
对比例2
将镁合金按照如下步骤进行处理:
(1)将清洗干净的镁合金样品置于组成为:硅酸钠10g/l、氟化钠5g/l、氢氧化钠8g/l、其余为水的电解液中,以待处理样品作阳极,以不锈钢作阴极,进行阳极微弧氧化处理,施加电压380v,占空比8%,频率800hz,时间10min。
(2)依次用水和乙醇冲洗干净,吹干。
将制备所得样品进行扫描电镜观察,其表面显微形貌如图5所示,可以观察到,涂层表面孔洞结构相比实施例1而言表现为十分欠发达,经统计分析,涂层孔隙率小于10%,微孔孔径明显相比实施例1而言较大,可达5μm。
以上所述仅为本发明的优选实施例而已,并不用于限制本发明,对于本领域的技术人员来说,本发明可以有各种更改和变化。凡在本发明的精神和原则之内,所作的任何修改、等同替换、改进等,均应包含在本发明的保护范围之内。
本文用于企业家、创业者技术爱好者查询,结果仅供参考。