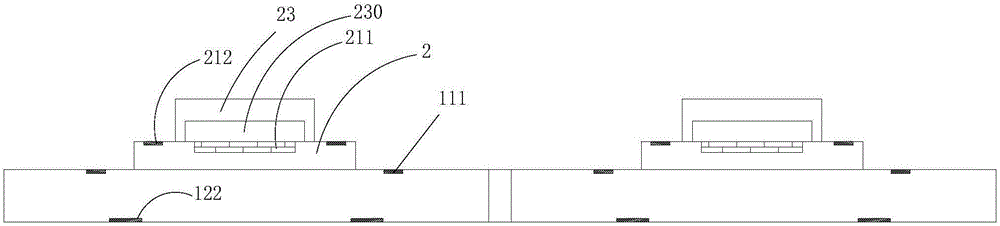
本发明涉及半导体芯片封装领域,尤其涉及MEMS(Micro Electro Mechanical systems,微机电系统)芯片的封装结构以及封装方法。
背景技术:
MEMS(Micro Electro Mechanical systems,微机电系统)技术是建立在微米/纳米技术基础上的21世纪前沿技术,是指对微米/纳米材料进行设计、加工、制造、测量和控制的技术。它可将机械构件、光学系统、驱动部件、电控系统集成为一个整体单元的微型系统。微机电系统不仅能够采集、处理与发送信息或指令,还能够按照所获取的信息自主地或根据外部的指令采取行动。它采用微电子技术和微加工技术相结合的制造工艺,制造出各种性能优异、价格低廉、微型化的传感器、执行器、驱动器和微系统,相对于传统的机械,它们的尺寸更小,厚度更薄,系统的自动化、智能化和可靠性水平更高。MEMS器件的应用领域相当广阔,市场需求强劲,正成为业界争相研发的热点。
由于MEMS芯片大小与常规的毫米或者厘米的功能模块之间存在很大的差异,因此需要通过封装来实现电信号在不同尺度的模块间的相互传递,近年来,MEMS封装技术取得了很大的进展,出现了众多的MEMS封装技术。
技术实现要素:
本发明解决的问题是提供MEMS芯片封装结构以及封装方法,降低MEMS芯片封装结构尺寸,提高MEMS芯片封装的集成度且便于MEMS芯片与其他尺度的电路电连接。
本发明提供一种MEMS芯片封装结构,包括:基板,具有彼此相对的正面以及背面;MEMS芯片,具有彼此相对的正面以及背面,所述MEMS芯片的背面贴合于所述基板的正面上;ASIC芯片,位于所述基板的背面;互连线路,设置于所述基板上,所述MEMS芯片与所述ASIC芯片分别与所述互连线路电连接。
优选的,所述MEMS芯片与所述ASIC芯片沿基板的厚度方向上相互对齐。
优选的,所述MEMS芯片封装结构还包括:封盖,具有收容腔;所述MEMS芯片的正面具有功能区和位于功能区周边的多个焊垫,所述焊垫与所述功能区电连接,所述封盖覆盖于所述MEMS芯片的正面上,所述收容腔罩住所述功能区。
优选的,所述基板的背面上设置有焊接凸起,所述焊接凸起与所述互连线路电连接,所述焊接凸起用于与外部电路电连接。
优选的,所述焊接凸起的高度大于所述ASIC芯片的高度。
优选的,所述基板的正面设置有与所述互连线路电连接的第一焊垫,所述焊垫与所述第一焊垫通过金属线电连接。
优选的,所述MEMS芯片封装结构还包括:塑封层,所述塑封层包覆所述MEMS芯片以及所述金属线。
优选的,所述ASIC芯片倒装于所述基板上。
优选的,所述基板的材质为硅基底或者陶瓷或者玻璃基板或者PCB板。
本发明还提供一种MEMS芯片封装方法,其特征在于,包含如下步骤:提供MEMS芯片,具有彼此相对的正面以及背面;提供基板,具有彼此相对的正面以及背面,所述基板上设置有互连线路;提供ASIC芯片;将所述MEMS芯片的背面贴合于所述基板的正面并将所述MEMS芯片与所述互连线路电连接;将所述ASIC芯片贴合于所述基板的背面并将所述ASIC芯片与所述互连线路电连接。
优选的,所述MEMS芯片与所述ASIC芯片沿基板的厚度方向上相互对齐。
优选的,在将所述MEMS芯片与所述基板贴合之前包含如下步骤:提供封盖,所述封盖具有收容腔;所述MEMS芯片的正面具有功能区和位于功能区周边的多个焊垫,所述焊垫与所述功能区电连接,将所述封盖覆盖于所述MEMS芯片的正面上,所述收容腔罩住所述功能区。
优选的,所述MEMS芯片通过如下步骤实现与所述互连线路电连接,包括:所述基板的正面设置有与所述互连线路电连接的第一焊垫,采用引线键合工艺将所述焊垫与所述第一焊垫通过金属线电连接。
优选的,将所述MEMS芯片与所述互连线路电连接之后,采用塑封工艺形成塑封层,所述塑封层包覆所述MEMS芯片以及所述金属线。
优选的,在形成塑封层之后,还包含如下步骤:采用倒装工艺将所述ASIC芯片倒装于所述基板的背面上;采用丝网印刷工艺或植球工艺或电镀工艺在所述基板的背面形成焊接凸起,所述焊接凸起用于与外部电路电连接。
优选的,在形成塑封层之后,还包含如下步骤:采用丝网印刷工艺或植球工艺或电镀工艺在所述基板的背面形成焊接凸起,所述焊接凸起用于与外部电路电连接;采用倒装工艺将所述ASIC芯片倒装于所述基板的背面上。
本发明的有益效果是降低MEMS芯片封装结构尺寸,提高MEMS芯片封装的集成度且便于MEMS芯片与其他尺度的电路电连接。
附图说明
图1为本发明优选实施例MEMS芯片封装结构示意图。
图2至图7本发明优选实施例MEMS芯片封装方法示意图。
具体实施方式
以下将结合附图对本发明的具体实施方式进行详细描述。但这些实施方式并不限制本发明,本领域的普通技术人员根据这些实施方式所做出的结构、方法、或功能上的变换均包含在本发明的保护范围内。
需要说明的是,提供这些附图的目的是为了有助于理解本发明的实施例,而不应解释为对本发明的不当的限制。为了更清楚起见,图中所示尺寸并未按比例绘制,可能会做放大、缩小或其他改变。此外,在实际制作中应包含长度、宽度及深度的三维空间尺寸。另外,以下描述的第一特征在第二特征之“上”的结构可以包括第一和第二特征形成为直接接触的实施例,也可以包括另外的特征形成在第一和第二特征之间的实施例,这样第一和第二特征可能不是直接接触。
请参考图1,为本发明优选实施例MEMS芯片封装结构示意图,MEMS芯片封装结构包括:基板1,具有彼此相对的正面以及背面;MEMS芯片2,具有彼此相对的正面以及背面,MEMS芯片2的背面贴合于基板1的正面上;ASIC芯片3,位于基板1的背面上;互连线路(图1中未绘示),设置于基板1上,MEMS芯片2与ASIC芯片3分别与所述互连线路电连接。
通过将MEMS芯片2与ASIC芯片3沿基板1厚度方向上排布,相比于将MEMS芯片以及ASIC芯片水平排布于基板的同侧,缩小了基板1的尺寸,降低了MEMS芯片2与ASIC芯片3集合封装的封装结构的尺寸,提高了封装结构的集成度。
优选的,MEMS芯片2与ASIC芯片3沿基板1的厚度方向上相互对齐。所谓相互对齐是指,MEMS芯片2与ASIC芯片3两者中较小的芯片位于较大的芯片沿基板厚度方向上的投影区域内。
MEMS芯片2的正面具有功能区211和位于功能区211周边的多个焊垫212,焊垫212与功能区211电连接。MEMS芯片2上设置有封盖23,封盖23上设置有收容腔230,封盖23覆盖于MEMS芯片2的正面上,收容腔230罩住功能区211为MEMS芯片2的功能区211营造密封环境。
于本实施例中,封盖23的材质为玻璃或者硅。封盖23通过黏胶或者金属键合方式与MEMS芯片2的正面盖合。在两者盖合的过程中可以抽真空或者在收容腔230内充入实现MEMS芯片2功能所需要的气体或者在收容腔230内充入电绝缘物质,比如凝胶类、油类。
于本实施例中,焊垫212未收容于收容腔230之中,且暴露在封盖23之外,如此,方便采用打线工艺形成金属线将焊垫212与互连线路电连接。当然,于本发明的其他实施例中,也可以采用TSV工艺实现焊垫212与互连线路电连接,若采用TSV工艺,焊垫212被封盖覆盖也不影响焊垫212与互连线路的电连接。
基板1的正面11上设置有与互连线路电连接的第一焊垫111,焊垫212与第一焊垫111通过金属线24电连接。
金属线24的材质为金、铜、铝、钨中的一种或几种的组合,或包含上述一种或几种材料在内的金属合金。
塑封层25至少包覆MEMS芯片2以及金属线24。塑封层的材质为环氧树脂或者塑封胶等可以用来塑封的材料。
于本实施例中,塑封层可以将封盖23、MEMS芯片2以及金属线24均包覆起来且形成平坦的顶表面。
基板1的背面上设置有焊接凸起121,焊接凸起121与互连线路电连接,焊接凸起121用于与外部电路电连接。
于本实施例中,焊接凸起121的高度大于ASIC芯片3的高度。如此,焊接凸起121与外部电路板电连接时,ASIC芯片3位于外部电路板与基板1之间,起到防护ASIC芯片3的作用。
ASIC芯片3倒装于基板1的背面上。具体的,在ASIC芯片3上设置金属凸块(bump)31,基板1的背面12上具有第二焊垫122,金属凸块31与第二焊垫122压合(bonding)电连接。
在ASIC芯片3芯片上设置有底部填充胶32。
于本实施例中,第一焊垫111与第二焊垫122可以为基板1的互连线路裸露的引脚。
基板1的材质为硅基底或者陶瓷或者玻璃基板或者PCB板。
本发明还提供一种MEMS芯片封装方法。包含如下步骤:
步骤1,请参考图2,提供MEMS芯片2以及基板1将MEMS芯片2的背面贴合于基板1的正面上。
MEMS芯片2具有彼此相对的正面以及背面,MEMS芯片2的正面具有功能区211和位于功能区211周边的多个焊垫212。MEMS芯片2上设置有封盖23,封盖23上设置有收容腔230,封盖23覆盖于MEMS芯片2的正面上,收容腔230罩住功能区211。焊垫212未收容于收容腔230之中,且暴露在封盖23之外。
本实施例中,封盖23的材质为硅,MEMS芯片2与封盖23的盖合可以采用晶圆级的工艺,即MEMS芯片晶圆与封盖晶圆盖合,然后采用刻蚀工艺使得封盖晶圆暴露出焊垫212,然后进行切割形成单个MEMS芯片与封盖23盖合的结构体。
基板1,具有彼此相对的正面以及背面,基板1上设置有互连线路(图3中未绘示);基板1的正面11上设置有与互连线路电连接的第一焊垫111,基板1的背面12上设置有与互连线路电连接第二焊垫122。多个基板1网格状排布形成大基板,大基板可以一体成型,在后续工艺中通过切割工艺将多个基板1彼此分离。
步骤2,请参考图3,采用打线工艺形成金属线24,金属线24的两端分别与焊垫212以及第一焊垫111电连接。
步骤3,请参考图4,采用塑封工艺在基板1的正面上形成塑封层25,塑封层25包覆封盖23、MEMS芯片2以及金属线24并形成平坦的顶表面。
塑封层至少包覆MEMS芯片以及金属线。塑封层的材质为环氧树脂或者塑封胶等可以用来塑封的材料。
步骤4,请参考图5,在基板1的背面上形成焊接凸起121,焊接凸起121与互连线路电连接,焊接凸起121用于与外部电路电连接。焊接凸起121可以是BGA型,且使用焊料合金的丝网印刷工艺、或通过植球工艺、或通过电镀工艺形成。BGA(球栅阵列)互连是通常通过焊接或部分熔融金属球到接合焊盘上形成的、用于与对等导体形成物理和电接触的圆形导体。可替换地,SMT互连可以是导电金属柱(例如铜)。
步骤5,请参考图6,采用倒装工艺在基板1的背面上倒装ASIC芯片3。ASIC芯片3上设置金属凸块(bump)31,金属凸块31与第二焊垫122压合(bonding)电连接。
于本实施例中,MEMS芯片2与ASIC芯片3沿基板1的厚度方向上相互对齐。所谓相互对齐是指,MEMS芯片2与ASIC芯片3两者中较小的芯片位于较大的芯片沿基板厚度方向上的投影区域内。
步骤6,请参考图7,采用底部填充胶工艺在ASIC芯片3上形成底部填充胶32。
本发明采用的是扇出(fan-out)晶片级封装WLP类型的技术,其允许制造组件不受芯片大小的限制。该封装不像用传统WLP处理那样在硅晶片上实现,而是来自人工晶片成形载体。在工艺的初始阶段期间,来自晶片(诸如硅晶片)的切块组件转变为人造或重构载体。
最后,通过切割工艺形成如图1所示的MEMS芯片封装结构。
应当理解,虽然本说明书按照实施方式加以描述,但并非每个实施方式仅包含一个独立的技术方案,说明书的这种叙述方式仅仅是为清楚起见,本领域技术人员应当将说明书作为一个整体,各实施方式中的技术方案也可以经适当组合,形成本领域技术人员可以理解的其他实施方式。
上文所列出的一系列的详细说明仅仅是针对本发明的可行性实施方式的具体说明,它们并非用以限制本发明的保护范围,凡未脱离本发明技艺精神所作的等效实施方式或变更均应包含在本发明的保护范围之内。
本文用于企业家、创业者技术爱好者查询,结果仅供参考。