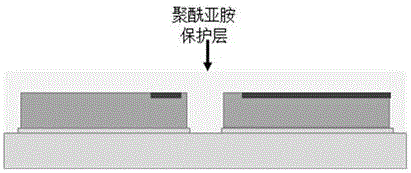
本发明涉及一种高频芯片的低损耗互连工艺方法,属于微电子器件互连封装领域,可用于高频段甚至太赫兹频段电子器件间的低损耗金属互连和集成封装。
背景技术:
在高频芯片(如固态集成放大器)的实际应用中,对于波导封装方案的需求显而易见,其中的金属互连技术对确保器件良好的信号传输性能至关重要,特别是封装中对反射、插入损耗及制作成本低的要求。研究表明,随着频率和带宽的不断增加,现有的封装互连技术已不能满足需求。美国国防部先进研究计划署(DARPA)2012年制定的DAHI(Diverse Accessible Heterogeneous Integration)计划中,已有相应的项目在开展这方面研究。特别是进入太赫兹频段,极高的频率和带宽都对现有微波波段的波导封装互连技术提出了更高的挑战。
目前的高频固态集成放大器在研究过程中存在如下问题:
(1)损耗问题:在高频固态集成放大器模块的波导封装中,模块中芯片和波导之间低损耗的过渡连接是当前的迫切需求,目前常用金属线键合互连的方式来实现芯片与传输线(微带线、共面波导)之间的连接,是封装中的关键技术。随着工作频率的提升,金属互连的延迟和功耗在不断增加,互连已经取代晶体管尺寸,成为决定电路性能的主要因素和限制其外来发展的瓶颈。
(2)焊盘尺寸:出于降低功耗的考虑,高频芯片(>100GHz)出现了焊盘面积(<30μm)和焊盘间距(10μm左右)过小的问题,达到传统金丝键合技术极限,实际操作困难。
技术实现要素:
本发明为克服上述技术缺陷,提出了一种高频芯片的低损耗互连工艺方法,采用MEMS微加工工艺技术,可以具有封装密度大、互连线短、寄生效应小等优点,有利于高频高速应用,还可以实现同一功能集成板上多芯片的一次性互连,缩短工艺制作周期,可用于高频段甚至太赫兹频段电子器件间的低损耗金属互连和集成封装。
本发明的技术方案如下:
一种高频芯片的低损耗互连工艺方法,其特征在于步骤为:
(1)芯片或微带线基片通过焊料平整贴装在用于支撑的基底上,以确保后续微纳加工工艺的进行;
(2)在芯片或微带线基片上均匀涂覆聚酰亚胺厚胶形成聚酰亚胺保护层,用于保护芯片、微带线基片免受后续工艺损伤;
(3)在聚酰亚胺保护层上涂覆光刻胶,并通过光刻,将芯片、微带线基片的焊盘区域的聚酰亚胺保护层暴露出来;
(4)利用干法刻蚀除去暴露区域的聚酰亚胺保护层,露出芯片或微带线基片上的金属焊盘或焊接区域;
(5)除去聚酰亚胺保护层上的光刻胶,得到聚酰亚胺保护层;
(6)在聚酰亚胺保护层上和芯片或微带线基片的金属焊盘或焊接区域上制备金属生长层,主要作为后续互连区域金属层电镀加厚的种子层;
(7)在金属生长层上涂覆光刻胶,通过光刻在非互连区域制作周期性排列的通孔图案,露出通孔图案下面的金属生长层,主要是作为后续制备用于去除聚酰亚胺胶的通孔的掩膜;
(8)采用湿法刻蚀,去除通孔位置处的金属生长层,露出聚酰亚胺保护层,然后去除所有光刻胶,在金属生长层上预留出除胶通孔;
(9)在上面喷涂厚光刻胶,并通过光刻露出互连区域的金属生长层,形成后续电镀步骤的掩膜;
(10)以互连区域的金属生长层为种子层,通过电镀的方式加厚互连区域的金属生长层,随后去除厚光刻胶,实现芯片间金属互连线的制作;
(11)采用反应离子刻蚀,去除聚酰亚胺保护层,同时剥离去除非互连区域的金属生长层,实现芯片与微带线基片之间或不同芯片之间的金属互连。
上述互连工艺步骤(1)中所采用的焊料可以是导电银胶、或者是低温预型焊片(SnPb、SnPbIn等)。
上述互连工艺中,芯片的焊盘可以是Al焊盘、或者Au焊盘。
上述互连工艺步骤(1)中,贴装后,芯片和相邻微带线基片的上表面之间或不同芯片的上表面之间的高度差小于5μm。
上述互连工艺中,步骤(6)中采用磁控溅射或蒸镀的方式生长金属生长层;金属生长层的成分根据不同焊盘具有不同材质。
上述互连工艺步骤(9)中,所述厚光刻胶的厚度为10-15μm,根据电镀时间选择确定厚光刻胶的厚度。
上述互连工艺步骤(10)中,所述电镀加厚的金属生长层的厚度为15-20μm。
本发明的有益效果如下:
本发明采用MEMS微加工工艺技术,不同芯片之间或芯片和微带线基片之间金属互连的跨接距离短,寄生效应引入损耗小,提高器件的频率特性;互连金属尺寸、形状可控行好;可实现同一功能基板上多芯片集成的一次性互连,缩短工艺制作周期。
附图说明
图1为本发明将芯片和微带线基片贴装在基底上的示意图;
图2为在图1中的芯片和微带线基片上形成聚酰亚胺保护层的示意图;
图3为将图2中的芯片和微带线基片上涂覆一层光刻胶并光刻露出焊盘区域上方聚酰亚胺保护层的示意图;
图4为将图3中的芯片和微带线基片上焊盘区域露出的示意图;
图5为去掉图4中所有光刻胶的示意图;
图6为在图5中的整个上表面形成金属生长层的示意图;
图7为在图6基础上形成通孔图案的示意图;
图8为将图7中的通孔的金属生长层去掉并去除所有光刻胶后的示意图;
图9为在图8的基础上在芯片和微带线基片上喷涂厚光刻胶并光刻露出焊盘区域的示意图;
图10为在图9基础上形成加厚金属层并除去光刻胶后的示意图;
图11为在图10基础上去除芯片和微带线基片上非焊盘区域的聚酰亚胺保护层的示意图;
图12为图11中形成互连结构后的俯视示意图。
具体实施方式
如图1-12所示,一种高频芯片的低损耗互连工艺方法,其步骤为:
(1)芯片或微带线基片通过焊料平整贴装在用于支撑的基底上,以确保后续微纳加工工艺的进行;
(2)在芯片或微带线基片上均匀涂覆聚酰亚胺厚胶形成聚酰亚胺保护层,用于保护芯片、微带线基片免受后续工艺损伤;
(3)在聚酰亚胺保护层上涂覆光刻胶,并通过光刻,将芯片、微带线基片的焊盘区域的聚酰亚胺保护层暴露出来;
(4)利用干法刻蚀除去暴露区域的聚酰亚胺保护层,露出芯片或微带线基片上的金属焊盘或焊接区域;
(5)除去聚酰亚胺保护层上的光刻胶,得到聚酰亚胺保护层;
(6)在聚酰亚胺保护层上和芯片或微带线基片的金属焊盘或焊接区域上制备金属生长层,主要作为后续互连区域金属层电镀加厚的种子层;
(7)在金属生长层上涂覆光刻胶,通过光刻在非互连区域制作周期性排列的通孔图案,露出通孔图案下面的金属生长层,主要是作为后续制备用于去除聚酰亚胺胶的通孔的掩膜;
(8)采用湿法刻蚀,去除通孔位置处的金属生长层,露出聚酰亚胺保护层,然后去除所有光刻胶,在金属生长层上预留出除胶通孔;
(9)在上面喷涂厚光刻胶,并通过光刻露出互连区域的金属生长层,形成后续电镀步骤的掩膜;
(10)以互连区域的金属生长层为种子层,通过电镀的方式加厚互连区域的金属生长层,随后去除厚光刻胶,实现芯片间金属互连线的制作;
(11)采用反应离子刻蚀,去除聚酰亚胺保护层,同时剥离去除非互连区域的金属生长层,实现芯片与微带线基片之间或不同芯片之间的金属互连。
上述互连工艺步骤(1)中所采用的焊料可以是导电银胶、或者是低温预型焊片(SnPb、SnPbIn等)。
上述互连工艺中,芯片的焊盘可以是Al焊盘、或者Au焊盘。
上述互连工艺步骤(1)中,贴装后,芯片和相邻微带线基片的上表面之间或不同芯片的上表面之间的高度差小于5μm。
上述互连工艺步骤(2)中,采用匀胶机进行涂覆,匀胶机转速1500转/min,厚度通过时间控制,完全覆盖所有芯片/微带线基片;坚膜:120℃,60min。
上述互连工艺步骤(3)中,采用深沟槽涂胶机喷涂光刻胶,胶厚约为10 μm;前烘:120 ℃,60 min;曝光时间:80 second;显影时间:3 min。
上述互连工艺步骤(4)中,采用反应离子刻蚀机(RIE)进行刻蚀。
上述互连工艺中,步骤(6)中采用磁控溅射或蒸镀的方式生长金属生长层;金属生长层的成分根据不同焊盘具有不同材质。
对于Au焊盘:Cr(黏着层)-Au(生长曾),厚度为200nm-200nm;
对于Al焊盘:Ti(Al/Cr)(黏着层)-Pt(Pd/Cu)(扩散阻挡层)-Au(生长层),厚度200nm-200nm-200nm。
上述互连工艺步骤(9)中,所述厚光刻胶的厚度为10-15μm,根据电镀时间确定。
上述互连工艺步骤(10)中,所述电镀加厚的金属生长层的厚度为15-20μm。
本文用于企业家、创业者技术爱好者查询,结果仅供参考。