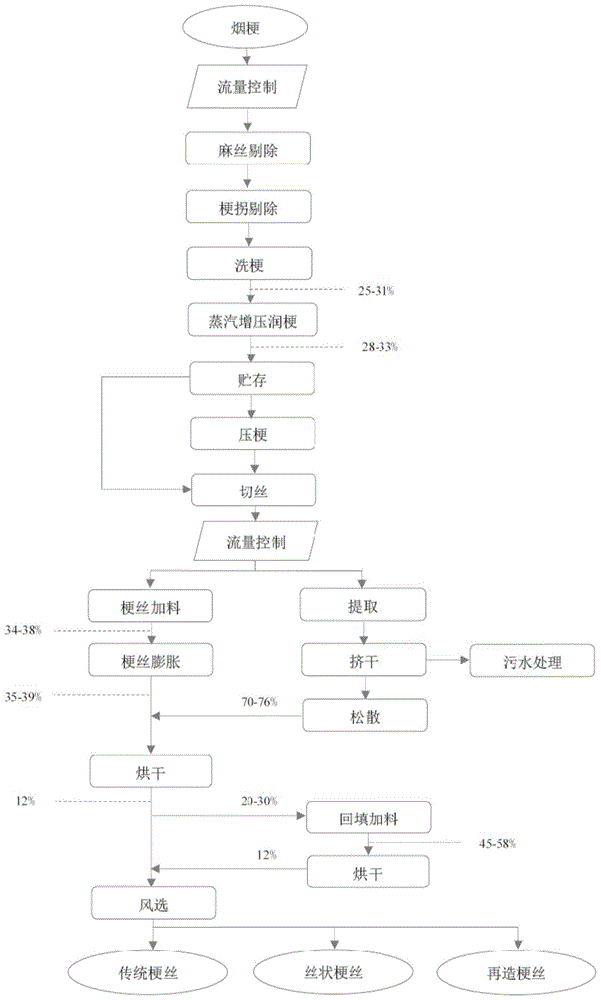
本发明属于烟草行业,更具体地说,涉及多品种梗丝的制备方法及设备。
背景技术:
近年来,随着梗丝加工工艺和设备在烟草行业的逐渐完善,梗丝的加工质量得到了明显提高,需求也不断增加,特色梗丝的种也开始多样化,但目前来说这些特色梗丝生产线往往还是单线生产,也就是说特定的生产线只能生产一种对应的特色梗丝。目前市场上流行的三种特色梗丝分别是传统梗丝(薄片状)、丝状梗丝(丝状)、再造梗丝(丝状)等。
传统梗丝成膨化薄片状,主要用于标准烟支的烟丝掺配,它保留了梗丝的原有口感,其品质跟丝叶相比相差较远,且由于其形状和叶丝有差别,融合度低,所以掺配量小,一般只用于低档烟的烟丝掺配中。丝状梗丝相对于传统梗丝来说,物理特性有所区别,其外形成丝状,与叶丝接近,但丝状梗丝的组成成分任然是梗丝成分,燃烧时浊气较重,感官体验不如叶丝,丝状梗丝常用于中低档烟丝掺配中。再造梗丝相对于传统梗丝和丝状梗丝来说,再造梗丝在组成成分得到突破,它不仅外形成丝状接近于叶丝,其组成成分经过提取和回填加料处理后也接近于叶丝,感官体验较好,再造梗丝常用于中高档烟丝以及细支烟烟丝掺配中。
原有的传统梗丝生产线以生产传统梗丝为主,无法直接生产丝状梗丝,如果想要把传统梗丝继续加工为丝状梗丝,只能将生产好的传统梗丝进行复切处理,通过机械轧切机构进行机械加工,这种加工方式简单粗暴,生产出来的丝状梗丝造碎特别大。再比如,近期开始流行的再造梗丝,由于其物理性质和化学性质都高度接近于叶丝,所以在掺配时,再造梗丝的掺配比例相较于传统梗丝和丝状梗丝大大增加,而且还能在高档烟中使用,且不影响感官体验。目前的再造梗丝生产线相对于传统梗丝和丝状梗丝线来说更为复杂,但现在的再造梗丝线并不能兼容传统梗丝和丝状梗丝的生产。对于烟厂来说,当需要加工不同特色的梗丝时就需要使用不同的生产线,也就是三种特色梗丝就需要三条生产线才能完成任务。这样厂房投入大,设备投入多,人员安排数量多,造成了极大的浪费。
技术实现要素:
本发明提供一种多品种梗丝的制备方法,能够实现在一条生产线上制备不同的梗丝。
本发明的多品种梗丝的制备方法,包括第一至六段制备工艺,可用于制备传统梗丝、丝状梗丝,或者,包括第一至八段制备工艺,可用于制备传统梗丝、丝状梗丝、再造梗丝;
第一段制备工艺:包括依次进行的梗拐剔除工序、洗梗工序、蒸汽增压润梗工序;
第二段制备工艺:包括将烟梗压薄的压梗工序;
第三段制备工艺:包括切丝工序;
第四段制备工艺:包括依次进行的梗丝加料工序、梗丝膨胀工序;
第五段制备工艺:包括干燥工序;
第六段制备工艺:包括风选工序;
第七段制备工艺:包括依次进行的浸泡提取工序、挤干工序、松散工序;
第八段制备工艺:包括依次进行的回填加料工序、干燥工序;
第一段制备工艺输出的烟梗可依次经过第三段制备工艺、第四段制备工艺、第五段制备工艺、第六段制备工艺,制成传统梗丝,即,传统梗丝制备工艺流程为:烟梗→梗拐剔除→洗梗→蒸汽增压润梗→切丝→梗丝加料→梗丝膨胀→干燥→风选→传统梗丝;
第一段制备工艺输出的烟梗可依次经过第二段制备工艺、第三段制备工艺后输出的梗丝,可依次经第四段制备工艺、第五段制备工艺、第六段制备工艺,制成丝状梗丝,即,丝状梗丝制备工艺流程为:烟梗→梗拐剔除→洗梗→蒸汽增压润梗→压梗→切丝→梗丝加料→梗丝膨胀→干燥→风选→丝状梗丝;
第一段制备工艺输出的烟梗可依次经过第二段制备工艺、第三段制备工艺后输出的梗丝,可依次经第七段制备工艺、第五段制备工艺、第八段制备工艺、第六段制备工艺,制成再造梗丝,即,再造梗丝制备工艺流程为:烟梗→梗拐剔除→洗梗→蒸汽增压润梗→压梗→切丝→浸泡提取→挤干→松散→干燥→回填加料→干燥→风选→再造梗丝。
优选的,第一段制备工艺还包括麻丝剔除工序,所述麻丝剔除工序设置在梗拐剔除工序之前。
优选的,第一段制备工艺还包括实现物料缓冲的贮存工序,所述贮存工序设置在所述蒸汽增压润梗工序之后。
优选的,烟梗经流量控制单元进行处理量的精确控制后送入第一段制备工艺,第三段制备工艺输出的梗丝经过流量控制单元进行处理量的精确控制后送入下一段制备工艺。
优选的,洗梗工序输出的烟梗水分含量为25-31%,蒸汽增压润梗工序输出的烟梗水分含量为28-33%,梗丝加料工序输出的梗丝水分含量为34-38%,梗丝膨胀工序输出的梗丝水分含量为35-39%,松散工序输出的梗丝水分含量为70-76%,第八段制备工艺的回填加料工序输出的梗丝水分含量为45-58%,第八段制备工艺的干燥工序输出的梗丝水分含量为11.5-12.5%,当第五段制备工艺连接第六段制备工艺时,第五段制备工艺的干燥工序输出的梗丝水分含量为11.5-14.5%,当第五段制备工艺连接第八段制备工艺时,第五段制备工艺的干燥工序输出的梗丝水分含量为20-30%。
优选的,第五段制备工艺的干燥工序采用气流干燥,干燥时间为7-20秒,介质风的温度为210-240℃。
优选的,第八段制备工艺的干燥工序采用流化床干燥和导热油烘丝干燥,回填加料工序输出的梗丝进入流化床内悬浮干燥3-4分钟,干燥热风温度为80-130℃,然后进入导热油烘丝机中干燥3-8分钟,干燥温度为80-130℃。
优选的,浸泡提取工序采用顺流提取方式,浸泡提取时间为20-50分钟,温度为室温至48℃之间。
优选的,当第二段制备工艺连接第三段制备工艺时,压梗工序输出的烟梗厚度为0.5-1.3mm,切丝工序输出的梗丝厚度为0.07-0.18mm。
本发明还提供一种多品种梗丝的制备设备,具备制备传统梗丝、丝状梗丝、再造梗丝等多种功能。
本发明的多品种梗丝的制备设备,包括第一至六段制备单元,可用于制备传统梗丝、丝状梗丝,或者,包括第一至八段制备单元,可用于制备传统梗丝、丝状梗丝、再造梗丝;
第一段制备单元:包括依次连接的用于剔除烟梗中的梗拐的梗拐剔除单元、用于清洗烟梗的洗梗单元、用于润梗的蒸汽增压润梗单元;
第二段制备单元:包括用于将烟梗压薄的压梗单元;
第三段制备单元:包括用于切烟梗的切丝单元;
第四段制备单元:包括依次连接的用于加料的梗丝加料单元、用于实现梗丝膨胀的梗丝膨胀单元;
第五段制备单元:包括用于干燥梗丝的干燥单元;
第六段制备单元:包括用于筛选梗丝的风选单元;
第七段制备单元:包括依次连接的用于浸泡梗丝的浸泡提取单元、用于挤出浸泡液的挤干单元、用于松散成团梗丝的松散单元;
第八段制备单元:包括依次连接的用于加料的回填加料单元、用于干燥梗丝的干燥单元;
第一段制备单元输出的烟梗可依次经过第三段制备单元、第四段制备单元、第五段制备单元、第六段制备单元,制成传统梗丝,即,传统梗丝制备设备包括:梗拐剔除单元→洗梗单元→蒸汽增压润梗单元→切丝单元→梗丝加料单元→梗丝膨胀单元→干燥单元→风选单元;
第一段制备单元输出的烟梗可依次经过第二段制备单元、第三段制备单元后输出的梗丝,可依次经第四段制备单元、第五段制备单元、第六段制备单元,制成丝状梗丝,即,丝状梗丝制备设备包括:梗拐剔除单元→洗梗单元→蒸汽增压润梗单元→压梗单元→切丝单元→梗丝加料单元→梗丝膨胀单元→干燥单元→风选单元;
第一段制备单元输出的烟梗可依次经过第二段制备单元、第三段制备单元后输出的梗丝,可依次经第七段制备单元、第五段制备单元、第八段制备单元、第六段制备单元,制成再造梗丝,即,再造梗丝制备设备包括:梗拐剔除单元→洗梗单元→蒸汽增压润梗单元→压梗单元→切丝单元→浸泡提取单元→挤干单元→松散单元→干燥单元→回填加料单元→干燥单元→风选单元。
本发明的多品种梗丝的制备设备将三种梗丝的共用设备设置为主线设备,各种梗丝的专用设备作为旁线,再经过辅联设备相互贯通,当生产不同特征梗丝时,开启主线设备和相应梗丝的专用设备以及相应的辅联设备即可,实现不同特征梗丝的制备功能。
相比于现有技术,本发明的有益效果为:
(1)相对于单独的梗丝加工工艺,本发明实现了一线多用,效率高;
(2)本发明将三条生产线融合为一条生产线,降低了设备的占地面积,减少了设备投入;
(3)本发明采用现有先进设备,简化了工艺流程,降低了成本,提高了产品质量和感官品质。
附图说明
图1为本发明多品种特色梗丝的制备工艺流程图。
具体实施方式
下面结合实施例和说明书附图对本发明作进一步的说明。
本发明的多品种特色梗丝制备方法利用一条生产线配合特定的设备,实现了能同时生产多种特色梗丝的目的,一线多用的生产模式相比于现有的专线生产模式,大大的降低了产品多样化生产的资金投入,减小了设备占地面积。
本发明具备制备传统梗丝、丝状梗丝、再造梗丝等多种功能。实现方式是将三种梗丝的共用设备设置为主线设备,各种梗丝的专用设备作为旁线,再经过辅联设备相互贯通。当生产不同特征梗丝时,开启主线设备和相应梗丝的专用设备以及相应的辅联设备即可,实现不同特征梗丝的制备功能。
对于传统梗丝生产来说,其外形呈薄片状,现有传统梗丝生产工艺流程为:烟梗→流量控制→风选除杂→洗梗→一次润梗→一次贮存→二次润梗→二次贮存→切丝→流量控制→回潮加料→梗丝膨胀→烘干→风选→传统梗丝;
本发明涉及的传统梗丝生产工艺流程为:烟梗→流量控制→麻丝剔除→梗拐剔除→洗梗→蒸汽增压润梗→贮存→切丝→流量控制→梗丝加料→梗丝膨胀→烘干→风选→传统梗丝。相对于原有工艺流程,新式传统梗丝生产工艺增加了“梗拐剔除”,使梗丝感官品质得到了提升;并用更为简单高效的“蒸汽压力润梗”代替了“一次润梗”、“一次贮存”、“二次润梗”和“二次贮存”,减少了设备投入。
对于丝状梗丝生产来说,其外形呈丝状,物理形态接近于叶丝,现有的丝状梗丝生产线的工艺形式主要是在传统梗丝生产线的基础上,对成品的传统梗丝进行机械式的复切,这种加工工艺对梗丝的造碎非常大,其生产工艺流程为:烟梗→流量控制→风选除杂→洗梗→一次润梗→一次贮梗→二次润梗→二次贮存→切丝→流量控制→回潮加料→梗丝膨胀→烘干→风选→梗丝复切→丝状梗丝;
本发明涉及的丝状梗丝生产工艺为:烟梗→流量控制→麻丝剔除→梗拐剔除→洗梗→蒸汽增压润梗→贮存→压梗→切丝→流量控制→梗丝加料→梗丝膨胀→烘干→风选→丝状梗丝。本发明涉及的丝状梗丝生产线在新式传统梗丝的基础上增加了“压梗”工艺,在提高原梗润透性的基础上实现了“薄压细切”,使原梗压片厚度为0.5~1.3mm(优选0.8mm),切丝厚度为0.07~0.18mm(优选0.12mm),去除了原有工艺的“复切”工序,确保切丝一切成型,减小了梗丝造碎,得率可达到≥80%。另外本发明涉及的丝状梗丝生产线也进行了梗拐剔除,使梗丝感官品质得到了提升。
对于再造梗丝来说,其外形成丝状,物理形态和感官品质都接近或超过叶丝,再造梗丝生产工艺为:烟梗→流量控制→麻丝剔除→梗拐剔除→洗梗→蒸汽增压润梗→贮存→压梗→切丝→流量控制→提取→挤干(污水处理)→松散→烘干→回填加料→烘干→风选→再造梗丝。再造梗丝属于新型梗丝生产工艺,再造梗丝和丝状梗丝相比,再造梗丝不仅在物理形状上和叶丝相近,其组成成分经过“提取”和“回填加料”后,对梗丝进行了“再造”,所以其感官质量也接近或超过叶丝,这种加工工艺生产的梗丝大大提高了梗丝与叶丝的融合度及梗丝的感官质量,提高了梗丝在中高档烟、细支烟以及新形卷烟中的用量,大幅度提高了梗丝的经济价值。
结合图1,本发明的工艺流程包含3种特色梗丝的制备,通过工艺路线的切换,以及设备参数的调整,可以对3种特色梗丝的生产线任意选择一种进行生产,这三种特色梗丝分别是传统梗丝、丝状梗丝、再造梗丝。
一、传统梗丝的制备工艺及设备
结合图1,传统梗丝的工艺流程为:烟梗→流量控制→麻丝剔除→梗拐剔除→洗梗→蒸汽增压润梗→贮存→切丝→流量控制→梗丝加料→梗丝膨胀→烘干→风选→传统梗丝。传统梗丝的工艺流程各步骤具体如下:
流量控制工序:烟梗经过流量控制单元进行投料,流量控制单元采用现有设备,其结构一般是喂料机 计量管 电子秤的形式,流量控制单元能精确控制投料的流量,同时还能计量单位时间内投料的重量。
麻丝剔除工序:经过流量控制的烟梗在进行梗拐剔除前,需要先进入麻丝剔除单元进行麻丝剔除,麻丝不仅会堵塞梗拐剔除的筛分机构,而且当它混入烟丝后还会影响烟支的口感,对感官体验造成不良影响。
梗拐剔除工序:去除麻丝后,烟梗需进行梗拐剔除,梗拐中木质素含量极高,梗丝中如果含有木质素超标会对烟支的口感造成不良影响,降低烟支的感官体验。
梗拐剔除单元优先选用“智能化梗拐剔除系统”,例如实用新型专利(公开号cn211026998u)公开的梗拐剔除系统。“智能化梗拐剔除系统”是用滚筒筛 视觉系统剔除的组合方式对烟梗进行剔除。烟梗先通过滚筒筛进行尺寸筛选,烟梗中的细碎梗、超大梗拐及杂物通过滚筒筛筛除,剩下的尺寸合适的烟梗进入视觉系统进行形状筛除。视觉系统属于智能化设备,它能分析烟梗和梗拐的形状区别,对梗拐进行精确剔除。经过滚筒筛 视觉系统进行组合剔除梗拐的方法,相较与传统的梗拐剔除方法,其设备运行稳定,效率高,智能化程度高,剔除的准确度更精准,产品的纯净度更高。
洗梗工序:梗拐剔除后,进行洗梗,洗梗的主要目前是洗去烟梗表面的杂质,同时对烟梗进行初步润湿,洗梗后水分含量一般为25%-31%。洗梗单元一般选用现有的洗梗机,在要求更高的情况下,可以采用“蒸汽洗梗机”,加大烟梗的润透度。
蒸汽增压润梗工序:洗梗后进行蒸汽增压润梗,蒸汽增压润梗为特色工艺,采用的也是特色设备。
传统工艺需要一次蒸汽润梗,一次贮存,二次蒸汽润梗,二次贮存,贮柜要有布料行车并具有“翻炒”功能,每次蒸汽润梗后贮存时间较长,所以原有工艺不仅设备复杂,而且为了润透烟梗需要使用很长的时间进行贮存,其生产效率低。蒸汽增压润梗单元采用“蒸汽增压烟梗回潮机”,例如实用新型专利(公开号cn201691038u)公开的蒸汽润梗设备。“蒸汽增压烟梗回潮机”是将烟梗通入带蒸汽的螺旋推进器中,在螺旋推进器的进、出料口带有特制汽锁,这种特制汽锁能锁住含有0.1~0.25mpa蒸汽压力的壳体,使其在连续加料和连续卸料的条件下保持0.1~0.25mpa蒸汽压力。正常使用时,螺旋推进器中烟梗直接和蒸汽接触,螺旋推进器下部含有滤水网,所有冷凝水被疏水阀排走,确保烟梗在螺旋推进器中是“蒸”而非“煮”,此时螺旋推进器内部温度在110~170℃间可调可控。烟梗在高温高压作用下能迅速舒张毛细水道,达到快速润透的效果,蒸汽压力润梗后,且烟梗的热敏性不高,在高温高压作用下对其纤维成分并不会造成破坏。蒸汽压力润梗工艺相对于传统润梗工艺来说,设备组成要简单的多,而且烟梗的润透效果好,润透时间快。一般情况下,蒸汽压力润梗润透烟梗的时间在3-7min,水分28-33%,可以做到即润即用,相对于传统工艺来说节省了贮存柜等一批设备。
贮存工序:蒸汽压力润梗后在贮存单元进行贮存,由于蒸汽压力润梗的效果远远好于传统润梗,烟梗的润透性和水分均匀性都达到一个比较理想的状态,所以此处的贮存的主要作用是为后道工序提供一个物料缓冲,使连续生产过程中蒸汽压力润梗后不积料也不停料,以便于后道能连续流畅的进行生产。
切丝工序:对于丝状梗丝和再造梗丝来说,贮存后下一步就开始压梗,但对于传统梗丝来说,贮存后下一步就开始切丝。切丝单元一般选用现有的切丝设备,传统梗丝由于没有经过压梗处理,切丝机切出来的梗丝成薄片状态。
流量控制工序:烟梗切丝后进入流量控制单元,同样,该流量控制单元也采用料机 计量管 电子秤的形式,喂料机具有一定的缓冲功能,计量管配合皮带秤能定量投料,同时还能计量单位时间内投料的重量。
梗丝加料工序:经过流量控制的传统梗丝下一步就开始梗丝加料,梗丝加料单元一般选用现有的加料设备,优选滚筒回潮加料机,梗丝回潮加料后水分一般在34-38%。
梗丝膨胀工序:回潮加料后就开始梗丝膨胀,梗丝膨胀单元一般选用闪蒸机,梗丝膨胀后水分一般在35-39%。
烘干工序:膨胀后的梗丝需要去除水分进行烘干处理,为兼顾再造梗丝生产,干燥单元选用“梗丝低速气流干燥系统”,例如实用新型专利(公开号cn2616873y)公开的新型梗丝流化干燥机。“梗丝低速气流干燥系统”烘干时间一般为7-20秒,介质风的温度为210-240℃。相对于传统设备,“梗丝低速气流干燥系统”干燥出来的梗丝的填充值更高,水分均匀性更好,干燥路径短、风速低、造碎低、能耗低、设备结构紧凑,烘干后梗丝水分一般在11.5-14.5%。
风选工序:烘干后进行风选,风选的作用是选出合格的膨胀梗丝,同时去除膨胀不好的梗丝、梗签等杂质。风选单元优选“精细化多级风选系统”,精细化多级风选系统”采用并联风选室 串联物料通道的形式对梗丝进行一级一级风选,它的特点是风选气料比为10:1,风选效率为≥95%,精细风选纯净度为≥99.7%,循环取风能耗小,结构合理造碎小。风选合格后的梗丝就是最终产品传统梗丝。
二、丝状梗丝的制备工艺及设备
丝状梗丝相对于传统梗丝来说,其物理形态有所差别,传统梗丝成薄片状,而丝状梗丝成细丝状。丝状梗丝从物理形态上来讲更接近于叶丝,与叶丝的融合度高,易于卷包。
结合图1,丝状梗丝的工艺流程为:烟梗→流量控制→麻丝剔除→梗拐剔除→洗梗→蒸汽增压润梗→贮存→压梗→切丝→流量控制→梗丝加料→梗丝膨胀→烘干→风选→丝状梗丝。
相对于传统梗丝的工艺来说,丝状梗丝的工艺在切丝前多了一道压梗的处理工艺,压梗单元为压梗机。经过压梗后的烟梗厚度只有0.5~1.3mm(优选0.8mm),切丝厚度为0.07~0.18mm(优选0.12mm),去除了原有工艺的“复切”工序,确保切丝一切成型,减小了梗丝造碎,得率可达到≥80%。除此之外,丝状梗丝和传统梗丝的处理工艺基本相同。
三、再造梗丝的制备工艺及设备
再造梗丝相对于传统梗丝来说,除了它们的物理形态有所差别外,它们的内部组分也发生了变化。而再造梗丝相对于丝状梗丝来说,它们的物理形态相同,不同的是内部组成成分发生了变化,具体来说再造梗丝是在丝状梗丝外形的基础上,将丝状梗丝内原有的梗丝组成成分,通过提取的方式将梗丝“洗白”,去除不需要的组分,再通过加料回填的方法,将想要的叶丝组成成分(从叶丝生产线的边角料中提取而来)添加到梗丝中,使梗丝不仅在物理形态上和叶丝相同,其感官体验也基本和叶丝相同。这样的加工工艺让梗丝与叶丝的融合度进一步加强,为高品质香烟掺配梗丝提供了必要条件。
结合图1,再造梗丝的工艺流程为:烟梗→流量控制→麻丝剔除→梗拐剔除→洗梗→蒸汽增压润梗→贮存→压梗→切丝→流量控制→提取→挤干(污水处理)→松散→烘干→回填加料→烘干→风选→再造梗丝。从第1步工艺到第10步工艺,再造梗丝和丝状梗丝的加工方式相同,但第10步工艺的下一道工艺,丝状梗丝是进行梗丝加料,而再造梗丝则是进行提取。
提取工序:梗丝进行提取时,浸泡提取单元优选“连续顺流提取机组”,梗丝需要在提取设备中适度浸泡,梗丝提取过程为顺流提取方式,让梗丝充分吸收提取介质,提取介质优选水,浸泡提取时间为20~50分钟,提取温度为室温到48℃之间。
挤干工序:提取后进行挤干,挤干是将梗丝中的提取液完全挤出,让梗丝成为“一张白纸”。挤干单元优选“高频振动脱水机” “链板式挤干机”。
“高频振动脱水机”通过高频振动使梗丝迅速脱水,脱水后的梗丝水分还很高,柔性较好,进入“链板式挤干机”后脱水梗丝在相向运动的链板挤压作用下,把水分尽量挤干。经过“高频振动脱水机” “链板式挤干机”处理后,梗丝水分一般在70-76%。挤干工艺挤出的浸泡液内还有大量的烟梗成分,依据环保要求这些溶液不能直排,需要做污水处理。污水处理设备优先喷雾干燥机,喷雾干燥能够将浸泡液干燥为粉末,这些干粉便于运输和处理。梗丝在挤干时,会在挤压力的作用下聚成团,但由于此时梗丝的水分含量高,柔韧性好,梗丝本身不会在挤压力作用下造碎。
松散工序:成团的梗丝下一工艺就是进行松散,松散单元优选松散机,松散机采用柔性拨料棒作为螺旋推进器,在松散时减小了梗丝的造碎。经过松散处理的梗丝水分含量为70-76%。
烘干工序:松散后进行烘干,干燥单元选用“梗丝低速气流干燥系统”,“梗丝低速气流干燥系统”烘干时间一般7-20秒,介质风的温度为210-240℃。烘干后梗丝水分一般在20-30%。
回填加料工序:经过烘干处理后,梗丝进行回填加料,回填加料是在干燥的“白纸”中加入需要添加的叶丝成分,让梗丝从组成成分上更接近于叶丝,实现其“再造”过程。
回填加料单元优选回填加料机,回填加料机类似于松散机,它也是采用柔性拨料棒作为螺旋推进器,在松散时减小了梗丝的造碎,同时在旋转轴上带有喷嘴,能将回填料均匀地喷洒在物料上,再通过拨料棒的搅拌推进将回填料拌匀。回填加料后,梗丝的水分含量为45-58%。
烘干工序:回填加料后的梗丝下一步进行烘干,烘干需要进行的是低温保香烘干,以防止回填料的香味因高温而挥发。干燥单元优选流化床 智能导热油烘丝机。
由于回填加料以后,梗丝的表面的粘度很高,采用“流化床”干燥可以让梗丝在流化床内干燥是处于悬浮状态,避免粘性梗丝与设备直接接触而粘壁,流化床干燥时间为3~4分钟,干燥热风温度为80~130℃,梗丝经过流化床干燥后,其表面水分降低,粘度减小;“智能导热油烘丝机”热效率高,热量分布均匀,管路简单,温度适应范围广,“智能导热油烘丝机”在对梗丝进行干燥的时间为3~8分钟,干燥温度为80~130℃。采用“流化床” “智能导热油烘丝机”进行烘丝,其烘干温度低,加热均匀,避免了致香组分挥发,有效实现了低温保香烘丝。经过烘干处理后,梗丝水分降低为11.5-12.5%,此时的梗丝相较于原梗来说,其物料性质和组成成分均发生改变,故被称为“再造梗丝”。
风选工序:再造梗丝烘干后下一道工艺进行风选,和传统梗丝、丝状梗丝一样,风选单元优选“精细化多级风选系统”。风选合格后的梗丝就是最终产品再造梗丝。
上述实施例仅是本发明的优选实施方式,应当指出:对于本技术领域的普通技术人员来说,在不脱离本发明原理的前提下,还可以做出若干改进和等同替换,这些对本发明权利要求进行改进和等同替换后的技术方案,均落入本发明的保护范围。
本文用于企业家、创业者技术爱好者查询,结果仅供参考。