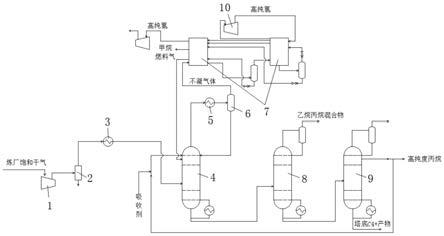
1.本发明涉及一种饱和干气分离方法,具体是一种炼厂饱和干气的分离方法。
背景技术:
2.炼厂饱和干气主要来源于原油的一次加工和二次加工,如常减压蒸馏、加氢裂化、延迟焦化、重整、歧化等过程中副产的气体,主要包含有氢气、甲烷、乙烷、丙烷等组分。目前,炼厂饱和干气大多直接用于工业或民用燃料,造成资源的严重浪费。乙烷、丙烷可作为乙烯裂解装置的原料,用于生产乙烯、丙烯,可以有效降低乙烯裂解原料成本,提高企业经济效益。
3.目前炼厂饱和干气的分离方法主要有深冷分离法、中冷油吸收法、变压吸附法及浅冷油吸收法等,各种方法各具特点。深冷分离法回收率高,工艺成熟,但设备投资大,能耗较高;中冷油吸收法投资低、适应性强,但回收率较低,吸收剂循环量和损失大,能耗较高;变压吸附能耗低,操作简单,但占地面积大,吸收效果较差,产品纯度低、回收率低。
4.专利公告号cn106609161a提出了一种分离炼厂饱和干气的方法,该方法采用c4作为吸收剂,在主吸收塔中吸收经压缩、冷却后的饱和干气中的c2馏分及更重组分,主吸收塔的塔底物流送至解吸塔,解吸塔顶得到回收的c2浓缩气。吸收塔压力约3.0~4.5mpag,吸收塔塔顶温度约5℃~25℃,塔底温度100℃~160℃。解吸塔塔顶温度55℃~65℃,塔底温度100℃~160℃。该方法设有再吸收塔和稳定塔,采用稳定汽油作为吸收剂,吸收主吸收塔顶气体中带出的c4吸收剂,富吸收油进入稳定塔,稳定塔塔顶温度40℃~80℃,塔底温度150℃~200℃。该方法c2回收率约97%,c2和c3总回收率约94%,但吸收剂循环量及损失量大,吸收塔、解吸塔、稳定塔塔底温度高,能耗相对较高。
5.专利公告号cn104560194a提出了一种炼厂饱和干气回收系统及回收方法,该方法采用碳四或碳五作为吸收剂,设有凝液汽提塔,压缩机段间凝液送往凝液汽提塔,汽提后产品直接送往乙烯装置裂解炉。该方法另设有再吸收塔,再吸收剂为汽油。该方法的c2和c3总回收率约96%,但吸收剂循环量及损失量较大,吸收塔、解吸塔塔底温度均较高,能耗较高。
6.专利公告号cn109553504a提出了一种采用浅冷油吸收技术回收炼厂饱和干气的方法及装置,该方法采用c4作为吸收剂,吸收塔塔顶温度约5℃~25℃,塔底温度100℃~160℃。解吸塔塔顶温度55℃~65℃,塔底温度100℃~160℃,解吸塔底液相大部分作为循环吸收剂返回吸收塔,小部分送至汽油稳定塔处理。再吸收塔采用稳定汽油作为吸收剂,吸收主吸收塔顶气体中带出的c4吸收剂,富吸收油进入稳定塔,稳定塔塔顶温度40℃~80℃,塔底温度120℃~150℃。该方法c2回收率约98%,c2和c3总回收率约95%,但吸收剂循环量及损失量大,吸收塔、解吸塔、稳定塔塔底温度高,能耗相对较高,且氢气无法得到回收。
7.综上所述,目前炼厂气体回收利用主要针对催化干气,饱和干气回收利用研究较少。现有的从饱和干气中分离c2/c3的工艺存在能耗高、投资大、塔及其它设备规模大、c2/c3回收率低、氢气无法回收及干气不干等问题。
技术实现要素:
8.本发明的目的在于提供一种炼厂饱和干气的分离方法,以解决上述背景技术中提出的问题。
9.为实现上述目的,本发明提供如下技术方案:
10.一种炼厂饱和干气的分离方法,包括下述步骤:
11.s1、炼厂饱和干气经过气体压缩机逐级压缩到3~4.5mpag,再经除杂和干燥设备除杂、干燥后,经冷却器冷却到
‑
15~
‑
35℃,进入吸收塔;
12.s2、吸收塔采用丙烷或富含丙烷的c3馏分作为吸收剂,所述吸收剂从塔顶进入吸收塔,在吸收塔中与饱和干气逆流接触,吸收饱和干气中的c2及c2以上组分;所述吸收塔的塔顶温度为
‑
35~0℃;
13.s3、吸收塔的塔顶气相进入冷凝器,经过冷媒水或丙烯冷却至
‑
15~
‑
40℃后进入分液罐;分液罐分离出的气相进入冷箱系统进行冷却分离,得到高纯度氢气和甲烷燃料气;分液罐分离出的液相返回吸收塔;
14.s4、吸收塔的塔底物料送至解吸塔进行后续处理。
15.作为本发明进一步的方案:在步骤s4中的后续处理步骤如下:
16.解吸塔的塔顶得到乙烷、丙烷混合组分,解吸塔的塔底c3 组分进入脱丙烷塔继续分离;
17.脱丙烷塔的塔顶分离得到高纯度丙烷,一部分作为循环吸收剂返回吸收塔,另一部分作为丙烷产品分出装置,塔底得到c4 液相送入后续装置处理。
18.作为本发明进一步的方案:所述吸收塔的理论塔盘20~70层,进料位置10~40层,塔顶压力为3~4.5mpag,塔底温度50~90℃;吸收塔设有多个中段回流。
19.作为本发明进一步的方案:所述解吸塔的理论塔盘15~70层,进料位置5~40层,塔顶压力为1.5~3mpag,塔顶温度为5~30℃,塔底温度60~85℃。
20.作为本发明进一步的方案:所述脱丙烷塔的理论塔盘15~80层,进料位置10~50层,塔顶压力为0.6~1.5mpag,塔顶温度为15~35℃,塔底温度60~90℃。
21.作为本发明进一步的方案:所述冷箱系统分为两段,每段均为多级换热器串联冷却,在两段之间设置一台膨胀机;气体自分液罐的罐顶出来,进入冷箱第一段冷却至
‑
45~
‑
40℃后,再进入冷箱第二段继续冷却到
‑
165~
‑
160℃,分离出甲烷、高纯氢气;
22.冷箱第二段出口的高纯氢气再进入膨胀机,膨胀至0.2~0.8mpag,温度
‑
125~
‑
115℃,再作为冷量返回第二段冷箱的级间继续换热;从冷箱系统出来的甲烷燃料气、高纯氢换热后温度>0℃,氢气加压后进入后续处理设施,甲烷燃料气并入炼厂燃料气管网;
23.其中,在冷箱系统的每一级间均设有气液分离设备,气相进入下一级冷箱继续冷却,而液相经节流膨胀后返回至上一级作为冷量回收。
24.与现有技术相比,本发明的有益效果是:
25.本发明以丙烷作为吸收剂,不使用乙烯机和再吸收塔,采用冷媒水和丙烯机提供冷量,膨胀机和冷箱回收冷量,在中冷(
‑
15~
‑
35℃)的条件下,对炼厂各装置产出的饱和干气进行吸收分离,解决现有炼厂饱和干气中c2、c3分离过程中存在的能耗高、投资大、塔及其它设备规模大、c2/c3回收率低、氢气无法回收及干气不干等问题。
26.本发明采用丙烷或富含丙烷的c3馏分作为吸收剂,在中冷条件下进行吸收,吸收
剂用量大幅降低,塔及其它设备的规模大幅减小,投资低,提高乙烷、丙烷回收率,同时可回收得到纯度较高的氢气。
附图说明
27.图1为一种炼厂饱和干气的分离方法的结构示意图。
28.图中:1、气体压缩机;2、除杂和干燥设备;3、冷却器;4、吸收塔;5、冷凝器;6、分液罐;7、冷箱系统;8、解吸塔;9、脱丙烷塔;10、膨胀机。
具体实施方式
29.下面结合具体实施方式对本专利的技术方案作进一步详细地说明。
30.请参阅图1,一种炼厂饱和干气的分离方法,包括下述步骤:
31.s1、炼厂饱和干气经过气体压缩机1逐级压缩到3~4.5mpag,再经除杂和干燥设备2除杂、干燥后,经冷却器3冷却到
‑
15~
‑
35℃,进入吸收塔4;在中冷(
‑
15~
‑
35℃)的条件下,对炼厂各装置产出的饱和干气进行吸收分离,可大幅降低吸收剂用量,提高乙烷、丙烷回收率,同时可回收得到纯度较高的氢气。
32.s2、吸收塔4采用丙烷或富含丙烷的c3馏分作为吸收剂,所述吸收剂从塔顶进入吸收塔4,在吸收塔4中与饱和干气逆流接触,吸收饱和干气中的c2及c2以上组分;所述吸收塔4的塔顶温度为
‑
35~0℃;本发明采用丙烷或富含丙烷的c3馏分作为吸收剂,在中冷条件下进行吸收,吸收剂用量大幅降低,塔及其它设备的规模大幅减小,投资低。
33.s3、吸收塔4的塔顶气相进入冷凝器5,经过冷媒水或丙烯冷却至
‑
15~
‑
40℃后进入分液罐6;分液罐6分离出的气相进入冷箱系统7进行冷却分离,得到高纯度氢气和甲烷燃料气;分液罐6分离出的液相返回吸收塔4;
34.s4、吸收塔4的塔底物料送至解吸塔8进行后续处理。
35.其中,在步骤s4中的后续处理步骤如下:
36.解吸塔8的塔顶得到乙烷、丙烷混合组分,解吸塔8的塔底c3 组分进入脱丙烷塔9继续分离;
37.脱丙烷塔9的塔顶分离得到高纯度丙烷,一部分作为循环吸收剂返回吸收塔4,另一部分作为丙烷产品分出装置,塔底得到c4 液相送入后续装置处理。
38.另外,所述吸收塔4的理论塔盘20~70层,进料位置10~40层,塔顶压力为3~4.5mpag,塔底温度50~90℃;吸收塔4设有多个中段回流。所述解吸塔8的理论塔盘15~70层,进料位置5~40层,塔顶压力为1.5~3mpag,塔顶温度为5~30℃,塔底温度60~85℃。所述脱丙烷塔9的理论塔盘15~80层,进料位置10~50层,塔顶压力为0.6~1.5mpag,塔顶温度为15~35℃,塔底温度60~90℃。
39.具体的,所述冷箱系统7分为两段,每段均为多级换热器串联冷却,在两段之间设置一台膨胀机10;气体自分液罐6的罐顶出来,进入冷箱第一段冷却至
‑
45~
‑
40℃后,再进入冷箱第二段继续冷却到
‑
165~
‑
160℃,分离出甲烷、高纯氢气;冷箱第二段出口的高纯氢气再进入膨胀机10,膨胀至0.2~0.8mpag,温度
‑
125~
‑
115℃,再作为冷量返回第二段冷箱的级间继续换热;从冷箱系统7出来的甲烷燃料气、高纯氢换热后温度>0℃,氢气加压后进入后续处理设施,甲烷燃料气并入炼厂燃料气管网;其中,在冷箱系统7的每一级间均设有
气液分离设备,气相进入下一级冷箱继续冷却,而液相经节流膨胀后返回至上一级作为冷量回收。本发明以丙烷作为吸收剂,不使用乙烯机和再吸收塔,采用冷媒水和丙烯机提供冷量,膨胀机和冷箱回收冷量,在中冷(
‑
15~
‑
35℃)的条件下,对炼厂各装置产出的饱和干气进行吸收分离,解决现有炼厂饱和干气中c2、c3分离过程中存在的能耗高、投资大、塔及其它设备规模大、c2/c3回收率低、氢气无法回收及干气不干等问题。
40.在本实施例中,饱和干气和吸收剂的组成如下表所示:
[0041] 饱和干气吸收剂质量流量t/h86.9970摩尔组成(mol%)
ꢀꢀ
氢气56.123 氮气4.247 一氧化碳0.103 氧气0.043 二氧化碳0.640 甲烷18.011 乙烯0.379 乙烷13.7670.168硫化氢
‑ꢀ
丙烯0.0270.275丙烷3.97299.550c41.9540.007c50.472 c6 0.263 水
‑ꢀ
[0042]
炼厂饱和干气自炼厂其它装置来,进入气体压缩机1,经四段压缩后将压力提高到3.85mpag。增压后的饱和干气经过除杂及干燥后,再经冷却器3冷却到
‑
20℃左右,进入吸收塔4。吸收塔4以丙烷为吸收剂,从塔顶进入,吸收气体中的c2及以上组分。吸收塔4的理论板数优选为50层,操作压力为3.72mpag,塔顶温度
‑
25.5℃,塔底温度69.7℃。吸收塔4顶气体进入冷箱系统7处理,分离得到高纯氢和甲烷燃料气。吸收塔4塔底物料送至解吸塔8处理。解吸塔8的理论板数优选为25层,操作压力为2.3mpag,塔顶温度约21℃,塔底温度72.2℃,解吸塔8塔顶分离出乙烷、丙烷混合组分,送往下游乙烯裂解装置,其中丙烷量与炼厂饱和干气中的丙烷量基本相等;解吸塔8塔底c3 组分,进入脱丙烷塔9进一步分离。脱丙烷塔9的理论板数优选为38层,操作压力为0.8mpag,塔顶温度约22.7℃,塔底温度79.8℃,脱丙烷塔9塔顶分离出的高纯度丙烷,本实施例全部作为循环吸收剂返回吸收塔4,丙烷产品无量;脱丙烷塔9塔底出来的c4 液相送入后续装置处理。
[0043]
分离后的产品如下表所示:
[0044][0045]
在本实施例中,乙烷回收率99.63%,丙烷回收率97.39%,c2和c3回收率98.97%,氢气回收率86.93%。
[0046]
上面对本专利的较佳实施方式作了详细说明,但是本专利并不限于上述实施方式,在本领域的普通技术人员所具备的知识范围内,还可以在不脱离本专利宗旨的前提下做出各种变化。
再多了解一些
本文用于企业家、创业者技术爱好者查询,结果仅供参考。