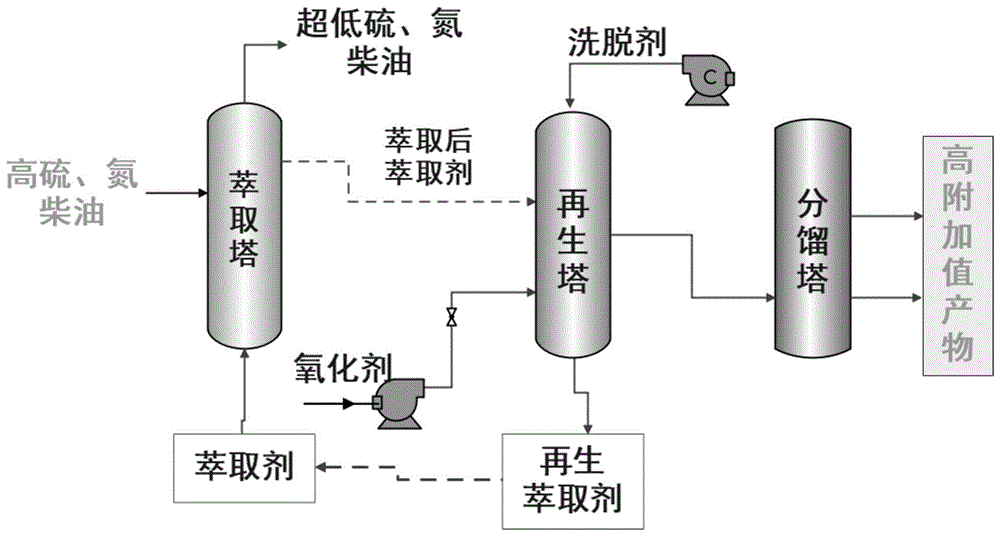
本发明属于石油化工领域,涉及一种柴油中硫、氮化物的脱除工艺以及产物回收过程,具体而言是通过萃取、氧化等过程油品中含硫、氮化物的脱除及分离回收高附加值产物。
背景技术:
柴油中硫、氮等有害组分会造成sox和nox排放,危害生态环境和人体健康。世界各国明确要求控制柴油中硫、氮含量以减缓愈发严重的环境污染现象。柴油清洁生产是解决这一问题的有效办法。目前,工业上广泛采用的加氢脱硫法需要高温、高压和消耗氢气等苛刻的反应条件来脱除油品中硫、氮化物。除此以外,油品中的碱性氮化物还易与催化剂酸性催化活性位点作用,导致催化剂中毒失活。非加氢脱硫方法具有反应条件温和、能耗低等优势,因此备受研究者关注,例如广泛发展的萃取脱硫和氧化脱硫技术。但是,但是普通直接萃取法存在单独使用效率低,萃取剂再生困难等问题;传统氧化法可能会使油品发生氧化副反应,降低油品燃烧值,存在选择性差、副反应多等缺点。亟需一种能同时解决上述问题的技术用于柴油的清洁生产。目前人们已提出多种方法耦合以获得较高的脱硫率。
专利[cn101333457a]提供了一种汽油的催化氧化脱硫与吸附结合的方法用于汽油中含硫化物的脱除。将氧化剂加入水中,混合得到水溶液再将水溶液于汽油混合,以氧气未氧化剂进行氧化处理;再进行吸附脱除硫化物得到脱硫汽油。
专利[cn1718681a]采用高剪切分散乳化技术强化石油油品与氧化剂的反应,将油品中的有机硫化合物氧化成砜,再采用萃取或吸附方法与碱金属或碱土金属的氢氧化物反应从而脱硫。
专利[cn10826932a]采用燃油与水溶性氧化剂在界面传质强化反应器中进行氧化脱硫反应,将硫化物氧化为砜类产物。经油水分离后通过选择性吸附脱除砜类产物,从而达到脱硫的目的。
以上技术均采用一种先氧化后萃取或吸附的方法对油品中的硫化物进行脱除,但是以氧气、双氧水等强氧化剂参与的油品体系,若直接将油品与氧化剂混合,在脱硫脱氮的同时,可能造成油品共氧化,直接引起油品中含氧量提升,燃烧值骤降。因此,氧化脱硫过程中的这一问题亟待解决。
技术实现要素:
基于上述目前存在的共性问题,本发明将萃取和催化氧化耦合,发展一类新型反应型萃取超深度脱硫脱氮方法,并资源化回收高附加值氧化产物。
对应设计的反应工艺如图1所示,单元操作分为三个模块:(1)反应萃取模块:实现萃取硫、氮化物;(2)萃取剂再生模块:用于萃取剂再生,以及萃取的硫、氮化物选择性催化氧化和氧化产物分离;(3)产物分离模块:高附加值的硫、氮化物的氧化产物分离纯化过程。
具体地,一种反应型萃取脱硫脱氮及高附加值产物回收的工艺,步骤如下:
(1)常温下,将柴油通过萃取塔,与萃取剂进行混合,选择性超深度萃取脱除柴油中硫、氮化物;
(2)步骤(1)中柴油和萃取剂经过分离后,得到萃取后的萃取剂和超深度脱硫脱氮后的清洁油品;其中,萃取后的萃取剂可回收循环利用。
(3)步骤(2)中萃取后的萃取剂经由连续操作转入再生塔中,在氧化剂和反萃取剂的作用下,将萃取的硫、氮化物选择性转化为氧化产物,所述的氧化产物是高附加值的砜、靛红或靛蓝,再生后的萃取剂转入萃取塔继续使用;
(4)进入分离操作,根据氧化产物的沸点、极性差异,分馏、闪蒸得到高附加值氧化产物。
步骤(1)中,所述的萃取剂为活性离子液体或多孔离子液体。所述柴油与萃取剂的质量比例为20:1~20:20。
进一步地,步骤(1)中,所述活性离子液体包括但不限于:由烷基咪唑盐、吡啶盐、季磷盐或季铵盐等与金属氯盐通过离子交换获得的活性离子液体。其特点是:不仅对油品中的硫、氮化物有萃取作用,还含有高效的选择性催化活性中心。
其中,所述金属氯盐为氯化钨、氯化钼、氯化钒、氯化钛或氯化铁。
进一步地,步骤(1)中,所述多孔离子液体包括但不限于:由烷基咪唑盐、吡啶盐、季磷盐或季铵盐作为阳离子,双(三氟甲基磺酰亚胺)盐、四氟硼酸盐或六氟磷酸盐作为阴离子,通过离子交换形成具有位阻的离子液体;多孔部分包括但不限于活性微孔氮化硼、钛硅分子筛、金属有机框架;具有位阻的离子液体和多孔部分通过氢键作用形成的多孔离子液体。其特点是:对油品中的硫、氮化物有萃取作用,能有效吸收气体类氧化剂,如氧气,还含有高效的选择性催化活性中心。
步骤(3)中,所述氧化剂为氧气、双氧水或叔丁基过氧化氢,氧气的用量为:10~120ml/min,双氧水或叔丁基过氧化氢的用量为:氧/硫摩尔比保持为2~10。
步骤(3)中,所述反萃取剂为n,n-二甲基甲酰胺、甲苯或乙腈极性溶剂,用量为:反萃取剂/离子液体的质量比例为20:1~20:20。
步骤(3)中,所述选择性转化的条件为:温度为30-150℃,压力为1-2mpa。
步骤(4)中,所述的分馏、闪蒸温度为100-500℃。
本发明的有益效果为:
本发明提出的方法既可在温和、低能耗条件下深度脱除柴油中的芳香性硫、氮化物,又能选择性分离回收高附加值氧化产物。最重要的是发展了一类具有催化功能的反应型萃取剂,将催化氧化过程从油相反应转移到萃取剂相,可直接避免油品的氧化,符合分子炼油理念,提升石油中每个分子的价值,与现有加氢技术实现互补,有望成为未来有应用前景的超深度脱硫脱氮技术。
附图说明
图1为本发明柴油反应萃取脱硫脱氮及产物回收工艺的流程示意图。
具体实施方法
以下结合实施例具体说明一种柴油反应萃取脱硫脱氮及产物回收工艺,本发明技术方案不局限于以下所列举的具体实施方式,还包括各具体实施方式之间的任意组合。
本发明中所述的一种反应型萃取脱硫脱氮及高附加值产物回收的工艺包括3个单元操作:萃取单元操作、氧化再生单元操作和分离提纯单元操作。该3个单元操作分别对应工艺中包含的萃取塔装置、氧化再生塔装置(含洗脱塔)和分离塔装置以及相关配套装置和设备。
本发明提供的一种反应型萃取脱硫脱氮及高附加值产物回收的工艺,包括如下步骤:先将柴油通过萃取塔,萃取脱除柴油中硫、氮化物得到超低含量污染物的柴油;再将萃取剂转移到氧化再生塔,加入氧化剂,如鼓入空气、氧气或加入双氧水,由催化氧化法将硫、氮化物氧化;经过氧化工艺的萃取剂进入洗脱过程,将萃取剂和氧化产物洗脱分离,并进行萃取剂的再生;氧化产物进入分离塔,闪蒸分馏获得不同种类的高附加值砜类、靛红、靛蓝等其他产品。
实施例1
萃取剂ts-1@[c16mim][ntf2]的制备过程为将双(三氟甲基磺酰亚胺)锂盐与氯代十六烷基甲基咪唑按等摩尔量混合,加入水进行溶解,搅拌30min,多次用去离子水洗去无机锂盐,经干燥获得[c16mim][ntf2]离子液体。取5重量份的钛硅分子筛ts-1分散于100重量份甲醇中,加入50重量份的[c16mim][ntf2],加热至100℃,搅拌12h,真空干燥后获得萃取剂ts-1@[c16mim][ntf2]。小试成功制备后,按比例放大进行小批量的制备并应用于此工艺。
将100重量份的柴油(含硫、含氮)和20重量份的ts-1@[c16mim][ntf2]缓缓进入萃取塔中,混合液的温度控制在60℃,机械搅拌混合,20min后停止搅拌,静置5-20min,液体分成上下两层,硫、氮化物被萃取至下层的萃取剂ts-1@[c16mim][ntf2]中,上层为超低污染物含量的柴油,不同硫、氮化物的萃取结果如表1、2所示。再将萃取剂和所分离污染物转移到氧化再生塔,100℃进行反应并鼓入氧气,ts-1@[c16mim][ntf2]萃取剂同时具备催化氧化性质,可将硫、氮化物氧化成相应的氧化物,不同硫、氮化物转化为对应氧化产物如表3、4所示。氧化后的萃取溶液进入洗脱过程,将萃取剂和氧化产物洗脱分离,并进行萃取剂ts-1@[c16mim][ntf2]的再生;经反萃取剂洗脱后的氧化产物进入分馏塔,分馏出不同种类的高附加值产品。
表1不同硫化物的萃取结果
表2氮化物的萃取结果
表3不同硫化物转化为对应氧化产物
表4不同氮化物转化为对应氧化产物
实施例2
萃取剂bn-900@[bpy][fecl4]的制备过程为将氯代丁基吡啶鎓盐与无水三氯化铁按等摩尔量混合,加入水进行溶解,搅拌30min,多次用去离子水洗涤,经干燥获得[bpy][fecl4]。取5重量份的微孔氮化硼bn-900分散于100重量份甲醇中,加入50重量份的[bpy][fecl4],加热至100℃,搅拌12h,真空干燥后获得萃取剂bn-900@[bpy][fecl4]。小试成功制备后,按比例放大进行小批量的制备并应用于此工艺。
将100重量份的柴油(含硫、含氮)和8重量份的bn-900@[bpy][fecl4]缓缓进入萃取塔中,混合液的温度控制在50℃,机械搅拌混合,20min后停止搅拌,液体在常温环境下静置20-50min,液体分成上下两层,硫、氮化物被萃取至下层的萃取剂bn-900@[bpy][fecl4]中,上层为超低污染物含量的柴油,不同硫、氮化物的萃取结果如表5、6所示。再将萃取剂和所分离污染物转移到氧化再生塔,50℃进行反应并鼓入氧气,bn-900@[bpy][fecl4]萃取剂同时具备催化氧化性质,可将硫、氮化物氧化成相应的氧化物,不同硫、氮化物转化为对应氧化产物如表3、4所示。氧化后的萃取溶液进入洗脱,将萃取剂和氧化产物洗脱分离,并进行萃取剂bn-900@[bpy][fecl4]的再生;经反萃取剂洗脱后的氧化产物进入分馏塔,分馏出不同种类的高附加值产品。
表5不同硫化物的萃取结果
表6不同氮化物的萃取结果
实施例3
萃取剂pmo-uio-66@[p66614][br]的制备过程为将一定量磷钼酸加入到uio-66的合成过程,超声处理30min后,将溶液转移到带有内部聚四氟乙烯的不锈钢高压釜中,并在120℃反应24h。冷却至室温后,离心,洗涤,并在80℃下干燥。使用管式电炉将前驱体在n2中于不同温度下活化2小时。获得pmo-uio-66材料。取5重量份pmo-uio-66分散于甲醇中,加入50重量份[p66614][br],加热至100℃,搅拌12h,真空干燥后获得萃取剂pmo-uio-66@[p66614][br]。小试成功制备后,按比例放大进行小批量的制备并应用于此工艺。
将100重量份的柴油(含硫、含氮)和8重量份的pmo-uio-66@[p66614][br]缓缓进入萃取塔中,混合液的温度控制在50℃,机械搅拌混合,20min后停止搅拌,液体在常温环境下静置20-50min,液体分成上下两层,硫、氮化物被萃取至下层的萃取剂pmo-uio-66@[p66614][br]中,上层为超低污染物含量的柴油,不同硫、氮化物的萃取结果如表7、8所示。再将萃取剂和所分离污染物转移到氧化再生塔,50℃进行反应并鼓入氧气,pmo-uio-66@[p66614][br]萃取剂同时具备催化氧化性质,可将硫、氮化物氧化成相应的氧化物,不同硫、氮化物转化为对应氧化产物如表3、4所示。氧化后的萃取溶液进入洗脱,将萃取剂和氧化产物洗脱分离,并进行萃取剂pmo-uio-66@[p66614][br]的再生;经反萃取剂洗脱后的氧化产物进入分馏塔,分馏出不同种类的高附加值产品。
表7不同硫化物的萃取结果
表8不同氮化物的萃取结果
本文用于企业家、创业者技术爱好者查询,结果仅供参考。