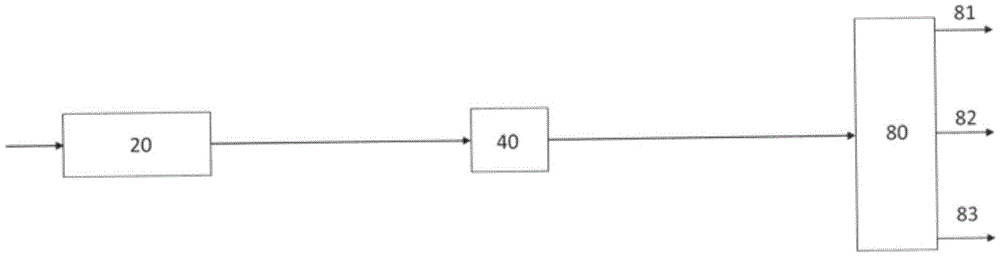
本公开涉及废塑料的回收利用,以及涉及在分级分离之前,通过初级裂化和气相催化氢化将废塑料转化成烃燃料和其它烃化合物。
背景技术:
:每年在大自然界中都会产生大量的塑料。由此产生的环境影响最近已经被意识到。它不仅破坏了自然的美感,而且人们意识到特别是在海洋中形成大量的微粒。这些微粒被生活在海洋中的鱼类和其它生物吸收,严重影响它们的健康。与此同时,众所周知,由于CO2被认为是全球变暖的一个主要因素,因此向大气中排放的CO2可以有利地减少。有利的是,可以减少石油产品的提取,从而降低CO2排放。限制这种提取的一种方法是再利用和/或再循环由石油产品制成的材料。因此,如果塑料材料被回收利用,并且通过减少石油产品的提取来限制额外的二氧化碳向大气中的排放,这对环境是有利的。这可以通过例如将塑料材料再循环以由废塑料生产烃燃料来实现。已经尝试以不同的方法对废塑料材料进行再回收利用,以获得不同的烃流体。然而,仍然需要一种有效的方法,优选在能量方面自给自足,并且用于特定烃燃料的最优生产。技术实现要素:本发明的一个目的涉及一种再利用废塑料生产液体燃料、气体和烃化合物的方法和系统。本发明的另一个目的是再利用在该方法中获得的能量,使该方法在能量方面自给自足,该方法仅使用有限量的提取石油产品,从而减少潜在的人类产生的CO2排放。这些目的是根据本文描述的本发明的方面和实施方式来实现的。在本发明的一个方面,提供了一种由废塑料生产燃料和额外烃的方法,包括以下步骤:-提供至少一种塑料材料;-使所述至少一种塑料材料经历初级裂化以获得第一烃流体;所述第一烃流体为气体;-使所述第一烃气体经历催化氢化以获得第二烃流体;-分级分离所述第二烃流体以获得至少一种最终产物。在一个实施方式中,该方法还包括在所述催化氢化步骤之后的冷凝步骤,其中所述第二烃流体通过至少所述催化氢化和冷凝步骤获得,以及其中所述第二烃流体是多相烃流体。在另一实施方式中,该方法还包括在所述冷凝步骤之后的分离步骤,其中所述第二烃流体至少通过所述催化氢化、冷凝和分离步骤获得,以及其中所述第二烃流体是在分离过程由所述多相烃流体获得的第一烃液体。在又一实施方式中,根据前述任一项目的方法还包括在催化氢化步骤之前进行的氢化前催化裂化步骤,以及其中所述第一烃流体至少通过所述初级裂化和氢化前催化裂化步骤获得。在又一实施方式中,该方法还包括在催化氢化步骤之后进行的氢化后催化裂化步骤,以及其中所述第二烃流体至少通过所述催化氢化和氢化后催化裂化步骤获得。在又一实施方式中,该方法的初级裂化通过无氧热裂化反应器进行。在又一实施方式中,该方法既不包括以下步骤中的任何一个,也不包括它们的组合:氢化裂化、氢化转化和氢化脱烷基。在另一实施方式中,该方法包括催化氢化步骤,条件是催化氢化不是氢化裂化、氢化转化和/或氢化脱烷基。在又一实施方式中,催化氢化在0.1巴至10巴的压力范围内,优选在0.7巴至2巴的范围内,例如约1巴下进行。在又一实施方式中,催化氢化在300℃至550℃的温度范围内,优选在380℃至460℃之间,例如约420℃下进行。在又一实施方式中,该方法还包括在分级分离之前将所述第二烃流体循环到储存罐的步骤。在又一实施方式中,重组分被再循环到初级裂化、催化裂化和/或催化氢化步骤或到所述储存罐。在又一实施方式中,在再循环到初级裂化、催化裂化和/或催化氢化步骤或到所述储存罐之前,使重组分经历重组分裂化步骤。在根据本发明的另一方面,提供了一种用于将废塑料回收成液态烃化合物的废物回收系统,包括:-初级裂化反应器,其能够接收至少一种塑料材料并通过初级裂化由所述至少一种塑料材料生产第一烃流体,所述第一烃流体为气体;-催化氢化反应器,其能够接收所述第一烃流体并通过催化氢化产生第二烃流体,-和分级分离器,其能够分级分离所述第二烃流体以获得至少一种最终产物,其中,所述初级裂化反应器与所述催化氢化反应器流体连接,以及所述催化氢化反应器与所述分级分离器流体连接。在一个实施方式中,该系统进一步包括冷凝器,用于与所述催化氢化反应器一起生产所述第二烃流体,并导致所述第二烃流体是多相烃流体,以及其中所述催化氢化反应器通过所述冷凝器进一步与所述分级分离器流体连接。在另一实施方式中,该系统还包括冷凝后分离器,用于分离所述多相烃流体以提供第一烃液体和第一不可冷凝的烃气体,以及其中所述冷凝器还通过所述冷凝后分离器与所述分级分离器流体连接。在又一实施方式中,该系统进一步包括氢化前催化裂化反应器,其中所述初级裂化反应器进一步通过所述氢化前催化裂化反应器与所述催化氢化反应器流体连接。在又一实施方式中,该系统进一步包括氢化后催化裂化反应器,其中所述催化氢化反应器进一步通过所述氢化后催化裂化反应器与所述分级分离器流体连接。在又一实施方式中,该系统还包括用于在分级分离之前储存第二烃流体的储存罐,其中所述催化氢化反应器至少通过所述储存罐与分级分离器流体连接。在又一实施方式中,该系统进一步包括用于向所述初级裂化反应器提供热量的气体燃烧器,所述气体燃烧器与所述冷凝后分离器流体连接。在又一实施方式中,该系统进一步包括重组分裂化反应器,所述重组分裂化反应器与所述分级分离器流体连接,用于接收从分级分离过程获得的重组分,以及其中所述重组分裂化反应器进一步与所述初级裂化反应器、所述氢化前催化裂化反应器、所述氢化后催化裂化反应器和/或所述催化氢化反应器流体连接。在又一实施方式中,该系统还包括分级分离后冷凝器、不可冷凝气体分离器和气体燃烧器,所述分级分离后冷凝器与所述分级分离器流体连接,用于接收从分级分离过程获得的轻组分,以及其中所述分级分离后冷凝器还与所述不可冷凝气体分离器流体连接,用于分离轻的不可冷凝烃气体;所述不可凝气体分离器进一步与所述气体燃烧器流体连接。在本发明的另一方面,提供了本文所述的系统或本文所述的方法用于由废塑料生产燃料和额外烃中的用途。在进一步的用途中,燃料是柴油。附图说明现在将参照附图更详细地描述根据本发明的由废塑料生产燃料和额外烃的方法和系统。附图示显示了实施本发明的一种方式,并且不应被解释为对落入本发明范围内的其它可能实施方式的限制。图1显示了本发明的第一实施方式,其以包括初级裂化、催化氢化和分级分离的流程图的形式呈现;图2显示了本发明的第二实施方式,其以包括初级裂化、催化氢化、分级分离、冷凝和分离的流程图的形式呈现;图3显示了本发明的第三实施方式,其以包括初级裂化、催化氢化、分级分离和氢化前催化裂化的流程图的形式呈现;图4显示了本发明的第四实施方式,其以包括初级裂化、催化氢化、分级分离和氢化后催化裂化的流程图的形式呈现;图5显示了本发明的第五实施方式,其以包括初级裂化、催化氢化、分级分离和重组分裂化的流程图形式呈现,其产物可以再注入;图6显示了本发明的第六实施方式,其以包括初级裂化、催化氢化、分级分离和用于重组分的再注入的几个路径的流程图的形式呈现;图7显示了本发明的第七实施方式,其以包括初级裂化、催化氢化、分级分离和在分级分离之后分离的不可冷凝气体的再循环的流程图的形式呈现;图8显示了本发明的第八实施方式,其以作为根据本发明的详细的实施方式的流程图的形式呈现;图9A显示了本发明的另一实施方式,其以包括初级裂化、分级分离和催化氢化的流程图的形式呈现;图9B显示了本发明的另一实施方式,其以包括如图9A所示的初级裂化、分级分离和催化氢化,但包括额外的组件的流程图的形式呈现。图10显示了在实验1中使用的实验装置的概况;图11显示了当最初在20000h-1和300℃下筛选氧化铝负载催化剂时,在实验1中获得的转化结果;图12显示了在实验2中获得的产物的碳数分布。具体实施方式“废塑料”应理解为完全或主要由塑料材料制成的废物,即废物中非塑料材料的水平应优选不超过10wt%。“塑料材料”应理解为大范围的高分子量的合成或半合成有机聚合物,例如聚烯烃、丙烯酸树脂、聚酯、硅橡胶和聚氨酯。塑料材料的实例为HDPE、LDPE、PP、PS、PET、ABS和PVC。“初级裂化”应该理解为塑料材料的分子被分解成小分子的过程。在一个实施方式中,小分子是主要具有C1-C40,例如C1-C30长度的烃。初级裂化包括热解以及其它裂化类型,例如所有类型的无氧热裂化。初级裂化在初级裂化反应器中进行。“催化氢化”应被理解为使用氢气使不饱和烃饱和的过程。虽然不能排除有限的裂化作用,但催化氢化的主要作用是饱和化。因此,它有别于氢化裂化、氢化转化和氢化脱烷基过程。氢化裂化、氢化转化和氢化脱烷基是具有如下目的裂化过程:减少烃的长度,并因此以中组分,C11-C20(对于柴油是典型的)的较长链为代价来获得更多的轻组分,通常是C6-C10,而中组分的较长链是本发明的最大目标。对于有限的裂化作用,应理解为小于10wt%,优选小于5wt%,例如优选小于3wt%的进料烃被裂化。催化氢化可能涉及也可能不涉及催化剂的作用。催化氢化在催化氢化反应器中进行。“催化裂化”应理解为将直链分子裂化成直链较短分子的过程。它通常对芳族化合物的作用有限,碳数低于C7的较轻分子几乎不被裂化。所谓“催化裂化”的优选实施方式使用催化剂。然而,它涵盖了无催化剂的裂化器的替代用途,即非催化裂化,如蒸汽裂化或延迟焦化。催化裂化在催化裂化反应器中进行。“重组分裂化”应理解为如下的裂化过程:即使来自分级分离的重组分的直链分子裂化成直链较短的分子。该过程可以在添加或不添加催化剂的情况下进行。优选地,该过程在没有催化剂的情况下进行。重组分裂化在重组分裂化反应器中进行。“停留时间”应理解为特定分子在反应器中存在的时间,即从进入反应器到离开反应器的时间。“分级分离”应理解为用于获得具有良好分离度的几个组分的过程,即在组分中仅具有相似长度的烃链的最小重叠,即如果分离的组分包含C6至C10,则由分级分离器产生的以下组分将包含至多50wt%的C6至C10,优选至多25wt%的C6至C10,例如至多20wt%的C6至C10,如最多15wt%的C6至C10,更优选最多10wt%的C6至C10,如最多5wt%的C6至C10。分级分离可以是蒸馏或多个冷凝步骤。分级分离在分级分离器中进行。“催化剂”应理解为引起或加速化学反应的物质,其本身不会在过程中受到化学影响或被消耗。然而,催化剂可能由于杂质而显示出降低的能力,并且需要再生。“第一烃流体”应理解为流体,即进入催化氢化反应器中的催化氢化步骤的液体和/或气体或进入如附加方法和系统中所述的分级分离器中的分级分离步骤而没有进行催化氢化的液体和/或气体。第一烃流体可包含50wt%或更少,例如45wt%或更少,例如40wt%或更少,例如35wt%或更少,例如30wt%或更少,例如25wt%或更少,例如20wt%或更少,例如15wt%或更少,例如10wt%或更少,例如5wt%或更少,例如1wt%或更少的水含量。在一个实施方式中,第一烃流体是气体。在另一实施方式中,第一烃流体是多相烃流体。“第二烃流体”应理解为流体,即在进行催化氢化后进入分级分离器中的分级分离步骤的液体和/或气体。第二烃流体可包含50wt%或更少,例如45wt%或更少,例如40wt%或更少,例如35wt%或更少,例如30wt%或更少,例如25wt%或更少,例如20wt%或更少,例如15wt%或更少,例如10wt%或更少,例如5wt%或更少,例如1wt%或更少的水含量。第二烃流体优选为液体。在一个实施方式中,第二烃流体是多相烃流体。“多相烃流体”应理解为具有至少两相的流体,例如液相和气相、两个液相、两个液相和两个气相、两个液相和一个气相以及两个气相和一个液相。所述流体可包含50wt%或更少,例如45wt%或更少,例如40wt%或更少,例如35wt%或更少,例如30wt%或更少,例如25wt%或更少,例如20wt%或更少,例如15wt%或更少,例如10wt%或更少,例如5wt%或更少,例如1wt%或更少的水含量。“不可冷凝气体”应理解为一种气体,其在冷凝的特定设置(压力和温度)下不会冷凝,因此在冷凝过程后仍保持气体状态。“轻组分”应理解为从分级分离过程中获得的组分,其中该组分包括分离的最短烃链。这通常是在汽油中存在的烃链。在一个实施方式中,轻组分主要包含C6-C10烃。在另一实施方式中,轻组分包含至少99wt%的C6-C10烃,例如至少98wt%的C6-C10烃,例如95wt%的C6-C10烃,例如至少90wt%的C6-C10烃,例如85wt%的C6-C10烃,例如至少80wt%的C6-C10烃,例如75wt%的C6-C10烃,例如至少70wt%的C6-C10烃,例如65wt%的C6-C10烃,例如至少60wt%的C6-C10烃,例如50wt%的C6-C10烃。“中组分”应理解为从分级分离过程中获得的组分,其中,当分离时,该组分包括中等长度的烃链。这通常是在柴油中存在的烃链。在一个实施方式中,中组分主要包含C11-C20烃,这是柴油中使用的标准长度。在另一实施方式中,中组分包含至少99wt%的C11-C20烃,例如至少98wt%的C11-C20烃,例如95wt%的C11-C20烃,例如至少90wt%的C11-C20烃,例如85wt%的C11-C20烃,例如至少80wt%的C11-C20烃,例如75wt%的C11-C20烃,例如至少70wt%的C11-C20烃,例如65wt%的C11-C20烃,例如至少60wt%的C11-C20烃,例如50wt%的C11-C20烃。“重组分”应理解为从分级分离过程中获得的组分,其中,当分离时,该组分包括超长长度的烃链。这种组分也可以称为重油。在一个实施方式中,重组分主要包含C21及以上的烃。在另一实施方式中,重组分包含至少99wt%的C21及以上烃,例如至少98wt%的C21及以上烃,例如95wt%的C21及以上烃,例如至少90wt%的C21及以上烃,例如85wt%的C21及以上烃,例如至少80wt%的C21及以上烃,例如75wt%的C21及以上烃,例如至少70wt%的C21及以上烃,例如65wt%的C21及以上烃,例如至少60wt%的C21及以上烃,例如50wt%的C21及以上烃。这里可互换使用的“A和B通过C流体连接”或“A和B经过C流体连接”应理解为流体能够从A流向C,并进一步从C流向B。A、B和C应理解为本文所述的系统的组件。进料规格、分类和预处理在一个实施方式中,所述至少一种塑料材料在所述初级裂化之前被预处理。在另一实施方式中,该系统还包括用于在被所述初级裂化反应器接收之前预处理所述至少一种塑料材料的装置,例如用于切碎的装置和/或用于干燥的装置。如果所需的塑料材料被污染到中间产物或最终产物或副产物规格不符合要求的程度,则对所需的塑料材料进行清洁,必要时根据相同的原则标准进行干燥。污染物可能是有机物、玻璃、沙子、泥土颗粒形式或任何其它形式的污染物,如家庭或工业废料存在的污染物,或在收集、输送或处理和储存阶段添加到材料中的污染物。污染水平应尽可能低,优选不超过10wt%,甚至优选小于5%,或甚至更好小于1%或2%。主要以水的形式存在于塑料材料表面的水含量应该尽可能低,并且优选不高于5wt%,优选小于3%,或者甚至更好小于1%。如果水含量太高,例如高于5wt%,可能需要干燥。原料中的高含水量,例如10wt%、15wt%、20wt%或25wt%的水是可能的,但是由于设备的生产量较低,生产能力可能最终会较低。进入初级裂化反应器的水可以通过不可冷凝气体分离器或储存罐从过程中进一步向下产出的油和气体中分离和提取出来。在又一实施方式中,至少一种塑料材料是HDPE、LDPE、PP和/或PS。在这一过程中合意的塑料成分是HDPE、LDPE、PP和/或PS。各种类型的PET、PVC和ABS塑料不太合意,在标准设备中优选保持在1wt%以下,但是如果设备配备有处理单元或去除这些塑料类型的处理可能产生的额外不需要的化学元素的化学添加剂,则可能更高:·PET含有氧,其可能导致油产物中形成醇、酸、酮、醛、酯和其它含氧化合物。·除了油产物中的氰化物、胺和酰胺之外,ABS在氯存在时可能会产生二噁英,在硫存在时可能会产生硫醇。这也可能导致不可冷凝气体燃烧过程中NOx的增加。·PVC含有超过50wt%的氯,可能有利于上述一些分子的形成,加上HCl和氯的形成。·除了产生不需要的分子,PET、PVC和ABS也将通过形成更少的烷烃来降低该工艺的生产能力。在又一实施方式中,通过切碎和/或分类所述至少一种塑料材料来预处理所述至少一种塑料材料。在一个实施方式中,材料可以被切碎成可处理的碎片,优选在5mm至500mm尺寸范围内,更优选在10mm至250mm尺寸范围内,甚至更优选在10mm至100mm的尺寸范围内。在一个优选的实施方式中,塑料材料在引入初级裂化之前不熔融。在另一实施方式中,材料可以储存在缓冲料斗中,或者填充在料斗中,例如输送到初级裂化反应器的输送机。在一个实施方式中,在选择和任选的预处理之后,塑料材料通过进料系统被进料到初级裂化反应器。进料系统可以包括配料仓和螺旋输送机。也可以使用现有技术中已知的其它进料系统。在一个实施方式中,螺旋输送机可以在一个或几个阶段包括塑料进料的压缩,以减少进料到初级裂化反应器中的空气量。初级裂化初级裂化的步骤在初级裂化反应器中进行。初级裂化应理解为热解以及其它裂化类型,例如所有类型的无氧热裂化。在一个优选的实施方式中,初级裂化是热解。在一个更优选的实施方式中,初级裂化是无氧热裂解。在另一实施方式中,初级裂化反应器是热解反应器。在又一实施方式中,初级裂化反应器是无氧热裂化反应器。在整个说明书中,术语热解可与术语初级裂化和无氧热裂化互换使用。提供主要来自C1-C40,如C1-C30的烷烃和烯烃的碳分布的主要初级裂化反应是:存在产生碳和氢的初级裂化反应副反应:如本领域已知的,还会有产生环烷烃(环状烷烃)的反应,但也有这里没有列出的芳烃和多芳烃。如反应(2)所述,在裂化塑料的初级裂化过程中,一些副产物以固体碳颗粒或烧焦物的形式形成。在进一步处理之前,优选将固体颗粒从反应器中除去并任选冷却,以避免自燃。这样的处理之一可以是燃烧,以便为初级裂化反应器产生热量。氢气与碳平行形成,并在本发明的后续工艺步骤中消耗,主要是在催化氢化步骤中消耗。初级裂化反应器中的停留时间通常可以在0.1小时至10小时之间,优选在20分钟至90分钟之间,甚至更优选在30分钟至60分钟之间变化。初级裂化反应器也可以接收来自分级分离的部分或全部重组分的补充进料。初级裂化可以在有或没有催化剂的情况下进行。在一个实施方式中,初级裂化在没有催化剂的情况下进行。在一个实施方式中,初级裂化反应器不包含改变离开初级裂化反应器的烃组成的催化剂(热裂化模式)。没有催化剂将降低初级裂化的操作成本(opex),并简化反应器的设计(capex)。在另一实施方式中,初级裂化器包含催化剂,例如已知的沸石类催化剂或基于活性金属(例如镍、镉、钼等)的催化剂。在一个实施方式中,反应器可以包含硅铝酸盐以降低最佳反应温度。这些被消耗,并随固体烧焦物组分一起排出。根据本领域已知的技术,反应器还可以包含矿物质如氧化钙以捕获Cl和S。得到的组分是固体,也将与烧焦物组分一起排出。上面提到的硅铝酸盐和钙矿物质不被认为是催化剂,因为它们在该过程中被消耗。在一个实施方式中,初级裂化反应器在约420℃下操作,即在反应器的终端出口处测得的生产的烃的温度约为420℃。更通常地,初级裂化反应器将在300℃至550℃之间,优选380℃至460℃之间的温度下操作。在整个说明书中,初级裂化反应器的工作温度由终端出口,即反应器最后一个区域的出口,在提取到下一个工艺步骤之前的温度来定义。根据反应器设计和操作参数,初级裂化反应器中的不同区域可能具有不同的温度。例如,一些初级裂化反应器显示出从接收至少一种塑料材料的入口到初级裂化反应器的出口的逐渐上升的温度梯度,在初级裂化反应器的出口处形成的产物,即第一烃流体,离开初级裂化反应器。在一个实施方式中,进料到初级裂化器中的塑料在进入反应器时汽化。在另一实施方式中,初级裂化器包括具有中等温度的第一熔融室,以产生中间熔融塑料产物。一些反应器可以具有几个出口和几个入口,使得能够在反应器的不同区域中进行第一烃流体或其它气体(例如加热初级裂化器的燃烧器的燃烧气体)的工艺优化提取和/或注入/再注入。在一个实施方式中,操作压力将保持在1巴左右。在另一实施方式中,操作压力在0.1巴至10巴的范围内,例如在0.5巴至5巴的范围内,例如在0.7巴至2巴的范围内,例如在0.9巴至1.1巴的范围内。在一个实施方式中,初级裂化反应器在0.7巴至2巴的压力范围,优选0.9巴至1.1巴的压力范围,例如1巴,以及在300℃至550℃,优选380℃至460℃,例如约420℃的温度下操作。在一个实施方式中,初级裂化反应器在0.9巴至1.1巴的范围内和380℃至460℃的温度下操作。出口处产物的最佳温度和压力会变化。这将取决于,即,进料的性质和初级裂化反应器的设计。初级裂化将会产生不可冷凝的气体——主要是碳长度为1到6的烷烃。不可冷凝气体可以在使用空气燃烧的气体燃烧器中燃烧,从而向初级裂化反应器提供热量。不可冷凝气体的产生将取决于进料的性质,例如塑料的类型以及初级裂化反应器的操作参数,例如温度和压力。不可冷凝气体的量优选调节到足以在运行操作期间加热初级裂化反应器。如果由于任何原因出现不可冷凝气体的短缺,提高初级裂化反应器的温度或塑料材料在初级裂化反应器中的停留时间将增加不可冷凝气体的产生,从而纠正短缺。额外地和/或补充地,用于燃烧的额外燃料可以由商业燃料源供应。商业燃料源也是为初级裂化过程的启动而设计的:在启动达到稳定运行操作之前,初级裂化反应器需要用易燃烧的商业燃料加热。这通常需要进行几个小时。可能的燃料的实例是碳、汽油、柴油、任何类型的重油、液化石油气(LPG)、天然气(NG)、不可冷凝气体等。来自气体燃烧器的燃烧气体(高温)将与返回的废气(传热至初级裂化反应器后的较低温度)混合,并从初级裂化反应器的出口再循环,以降低温度并确保气体速度,使反应器内的塑料获得良好的传热。在一个实施方式中,再循环率可以暂定为所产生废气的10%至70%。在另一实施方式中,废气的温度可以从400℃到800℃之间变化,优选500℃到600℃之间变化,更优选为约550℃。这些温度将取决于许多参数,其中包括塑料进料和反应器的类型。在一个优选的实施方式中,初级裂化反应器是间接加热型的,即主要热源不与反应器中的废塑料进料混合。初级裂解后过滤和冷却在又一实施方式中,该方法还包括在初级裂化步骤后的过滤和任选的冷却。在一个实施方式中,在例如热解之后离开初级裂化反应器的第一烃流体被过滤以除去在初级裂化器中形成的碳颗粒,并且不作为固体例如烧焦物排出。为了保护下游的工艺单元,例如沙子、玻璃和未反应的塑料的污染物也需要与在初级裂化反应器的底部/端部的烧焦物和固体一起被收集,或者在被离开初级裂化器的流体输送时过滤。由作为第一烃气体的第一烃流体携带的颗粒预期具有一到数百μm的尺寸。颗粒的数量预计会随着入口水含量、塑料类型、污染物和热解反应器的性能而变化。本领域已知的过滤方法可用于此目的。在一个实施方式中,过滤器将被设计成去除高达至少95%的大于5微米的颗粒。在另一实施方式中,过滤将使用旋风过滤器进行。在另一实施方式中,通过热交换器将气体温度调节到下游预期的温度。选在过滤后调节温度。在另一实施方式中,通过减压装置,例如压力控制阀或其它压力控制装置,将气体压力调节到下游预期的压力。氢化反应器在初级裂化和任选的过滤、温度和压力调节之后,第一烃流体将在催化氢化反应器中经历催化氢化。或者,如在本文公开的附加方法和系统中所述,可以对来自分级分离过程的至少一种产物进行催化氢化。原则上,含有双键或三键的所有不饱和烃分子如烯烃、炔烃、芳烃等,可能在催化氢化过程中发生反应,导致分子变为饱和。氢化的实例如下所示:-CH=CH- H2=>-CH2-CH2-(3)烯烃氢气烷烃催化氢化在气相中进行。在一个优选的实施方式中,该过程在例如压力和温度高于进入催化氢化反应器的气体进料的露点的条件下运行。在另一实施方式中,气体中的潜在冷凝物在进入催化氢化反应器之前,即在催化氢化反应器的上游排出。在一个实施方式中,操作压力将保持在1巴左右。在另一实施方式中,操作压力在0.1巴至10巴的范围内,例如在0.5巴至5巴的范围内,例如在0.7巴至2巴的范围内,例如在0.9巴至1.1巴的范围内。1巴下的工作温度通常在150℃至280℃之间,优选在190℃至270℃之间。在一个实施方式中,工作温度将保持在190℃至200℃左右。在另一实施方式中,工作温度为约270℃。在又一实施方式中,催化氢化是在1巴的操作压力和在150℃至280℃之间,优选190℃至230℃之间,例如在约200℃的温度下进行。在一个实施方式中,通过在沿着催化氢化反应器的几个不同位置添加氢气来改善催化氢化。因此,通过催化剂的氢气浓度分布得到改善。氢气通常由反应(2)中详述的分解产生的初级裂化反应提供。因此,第一烃流体预期会含有一些氢气。然而,在一些实施方式中,添加外部氢气可能是必要的。许多类型的反应器可用于催化氢化。在一个实施方式中,使用填充床反应器。在另一实施方式中,使用固定床反应器,例如填充有蜂窝结构的固定床反应器。在另一实施方式中,使用流化床反应器。在一个实施方式中,反应器的空速(SV)在50000h-1至200h-1的范围内。Sv计算为待处理流体的流量除以反应器的床体积。对于填充床反应器,该范围优选为50000h-1至10000h-1,例如50000h-1至30000h-1,例如30000h-1至20000h-1,例如20000h-1至15000h-1,例如15000h-1至10000h-1。对于固定床反应器,预期范围为10000h-1至200h-1,例如10000h-1至5000h-1,例如5000h-1至2000h-1,例如2000h-1至1000h-1,例如1000h-1至500h-1,例如500h-1至200h-1。催化氢化反应器可以具有开放式结构。在一个实施方式中,流动开口(flowopening)将为0.1mm至10mm,例如0.5mm至8mm,例如1mm至6mm,例如1.5mm至5mm,优选2mm至4mm。众所周知,许多催化剂对氢化作用良好,可用于本申请。例如,如Cu-Mn/Al2O3的催化剂可以用于催化氢化反应。也可以使用其它具有良好性能的氢化催化剂,例如Ru/C、Pt/ASA或PtPd/ASA(其中,ASA为无定形二氧化硅-氧化铝)和CoMo/γ-Al2O3。在一个实施方式中,催化氢化反应器直接从分级分离器或在重组分已经经历重组分裂化之后从分级分离器接收重组分的补充进料。催化剂表面上焦炭或其它杂质的形成可以使催化剂失活。因此,可能需要催化剂的再生。在一个实施方式中,如本领域已知,催化氢化反应器配备有原位清洁/再生系统。在另一实施方式中,再生可以在从反应器中提取催化剂后在设备或专用设备中进行。在一个实施方式中,在进入催化氢化之前,催化氢化在气体的初级裂化和任选的过滤和冷却之后进行。在该实施方式中,在进入催化氢化之前(指示优选温度低于270℃),热交换器冷却来自初级裂化的气体(指示优选温度为420℃)。在一个实施方式中,最终产物所需的规格是EN590,并且在一些情况下,初级裂化和催化氢化的组合而不进行进一步的加工,例如额外的催化裂化,将不会产生预期的产率和质量。催化裂化在另一实施方式中,气体可以在初级裂化和任选的过滤和冷却之后经历额外的裂化步骤。为了提高生产率,特别是为了使在最终产物中的长链分子如C21及以上,如C21-C40,如C21-C30断裂,可以选择该附加步骤。额外的催化裂化步骤可以发生在催化氢化之前(氢化前催化裂化)或之后(氢化后催化裂化)。在整个说明书中,催化裂化和催化裂化反应器指氢化前催化裂化和氢化后催化裂化,以及氢化前催化裂化反应器和氢化后催化裂化反应器。催化裂化反应器将主要将直链分子裂化成直链较短的分子。它通常对芳族化合物的作用有限,碳数低于C7的较轻分子几乎不被裂化。该催化剂将会使C-C键裂化,但也可能导致分子异构化。在一个实施方式中,催化裂化反应器中测量的温度保持在420℃左右,但是催化裂化反应器也可以在350℃至550℃之间,优选在380℃至460℃之间的温度下操作。在一个实施方式中,操作压力为1巴左右。在又一实施方式中,操作压力在0.1巴至10巴的范围内,例如在0.5巴至5巴的范围内,例如在0.7巴至2巴的范围内,例如在0.9巴至1.1巴的范围内。在又一实施方式中,催化裂化是在1巴的操作压力和在350℃至550℃之间,优选380℃至460℃之间,例如在约420℃的温度下进行。可以使用多种类型的反应器。在一个实施方式中,使用填充床反应器。在另一实施方式中,使用固定床反应器,例如填充有蜂窝结构的固定床反应器。在又一实施方式中,使用流化床反应器。在一个实施方式中,反应器的空速(SV)可以典型地在50000h-1至200h-1的范围内。对于填充床反应器,通常的范围为50000h-1至10000h-1,例如50000h-1至30000h-1,例如30000h-1至20000h-1,例如20000h-1至15000h-1,例如15000h-1至10000h-1。对于固定床反应器,通常的范围为10000h-1至200h-1,例如10000h-1至5000h-1,例如5000h-1至2000h-1,例如2000h-1至1000h-1,例如1000h-1至500h-1,例如500h-1至200h-1。催化反应器可以具有开放式结构。在一个实施方式中,流动开口将为0.1mm至10mm,例如0.5mm至8mm,例如1mm至6mm,例如1.5mm至5mm,优选2mm至4mm。已知许多催化剂对催化裂化作用良好,并且可以根据本发明来使用,例如用于催化裂化的超稳定Y沸石(USY)。也可以使用其它具有良好性能的催化裂化催化剂,例如酸性沸石催化剂,其中USY是一个实例。也使用混合金属硫化物或贵金属催化剂。催化剂表面上焦炭或其它杂质的形成将会使催化剂失活。由此,将催化剂的再生有利地进行。在一个实施方式中,反应器装配有原位清洁/再生系统,如本领域已知的,例如使用空气、水或惰性气体混合物来再生催化剂的系统。在另一实施方式中,再生可以在从催化裂化反应器中提取催化剂后在设备或专用设备中进行。氢化前催化裂化反应器或氢化后催化裂化反应器还可以直接从分级分离器(即,没有被进一步处理)或在重组分已经经历重组分裂化之后从分级分离器接收部分或全部的重组分的补充进料。在另一实施方式中,重组分裂化器可以在将从分级分离器获得的重组分重新注入工艺的上游之前对其进行处理。因此,可以增加从分级分离中获得的轻组分和中组分的产量。在一个实施方式中,催化裂化器优选在比氢化反应器更高的温度下运行,特别是在接近初级裂化反应器的温度范围内,例如优选在420℃左右的温度下运行。因此,从设备能量效率的角度来看,催化裂化优选为氢化前催化裂化。因此,从初级裂化反应器流出的气体在进入氢化前催化裂化反应器之前既不需要冷却,也不需要减压。在氢化前催化裂化之后,在进入催化氢化反应器之前可能需要冷却,以便将氢化前催化裂化器出口处的第一烃流体的温度从例如420℃的工作温度降低到低于270℃。在另一实施方式中,催化裂化可以是氢化后催化裂化。这有利于氢气消耗的优化。与催化裂化相比,催化氢化消耗大量的氢气,并且氢气主要来自初级裂化。在来自初级裂化反应的氢气量有限的情况下,氢化后的催化裂化可以为减少从工业气体供应商处购买的额外氢气消耗的手段。然而,使用氢化后催化裂化可能导致不饱和分子的再生成,并且需要将从催化氢化获得的气体加热到催化裂化所需的温度,这是耗能的。冷凝和分离在一个实施方式中,在催化氢化和/或氢化后催化裂化之后布置冷凝器,以使产生的烃流体流入冷凝器。或者,冷凝器可以布置在分级分离器之前和/或初级裂化之后。在冷凝器中,温度降低以实现冷凝。从例如270℃或200℃(催化氢化反应器的出口)或420℃(催化裂化反应器或初级裂化反应器的出口)的温度,气体在0.5巴至1巴,最优选0.7巴至0.9巴的压力下冷却至优选100℃至130℃,更优选110℃。在另一实施方式中,从例如380℃至460℃的温度(初级裂化反应器),气体被冷却至60℃至180℃。因此,大部分气体被冷凝并形成多相烃流体,该多相烃流体包括至少第一不可冷凝气体和第一烃液体。在另一实施方式中,冷凝器的出口温度为110℃,以保持水处于汽相并促进水从烃液体(油)中分离。优选地,温度保持在高于60℃,因为在较低的温度下,例如低于60℃,存在不期望的蜡沉积的风险。在另一实施方式中,冷凝后的流体,即多相烃流体通过冷凝后分离器,其中将烃液体组分(可能含有有限的水组分,优选最多0.2%)与不可冷凝气体组分(可能含有少量水蒸汽)分离。在另一实施方式中,第二烃流体在任选冷却以及任选纯化(见下文)后,被转移至储存罐。在一个实施方式中,储存罐的温度在60℃至80℃的范围内,优选在60℃左右。在另一实施方式中,第二烃流体在进入储存罐之前被进一步净化。在又一实施方式中,分离进一步导致第一不可冷凝的烃气体的形成,以及其中至少一部分所述第一不可冷凝的烃气体被再循环至气体燃烧器并在其中燃烧,以向所述初级裂化提供热量。在又一实施方式中,至少一部分的所述第一不可冷凝的烃气体在燃烧之前经历进一步处理,例如进一步冷凝和分离。烃液体的纯化在另一实施方式中,在催化氢化和/或催化裂化后除去杂质。或者,在初级裂化后除去杂质。杂质可以通过一个或多个过滤器除去。杂质可能是酸、醇、其它含氧有机化合物、HCl和H2S,这是最常见的杂质。对于烃液体,将在冷凝后分离器和储罐之间的任何位置进行这样的纯化。在一个实施方式中,第二烃流体的纯化将在储存罐中进行。在一个实施方式中,向烃液体中加入少量水/NaOH溶液,或者任何中和酸的物质,例如CaO或Ca(OH)2。下面列出了一些发生的纯化反应:醇:R-OH NaOH=R-ONa H2O(4)酸:R-COOH NaOH=R-COONa H2O(5)硫化氢:H2S 2NaOH=Na2S 2H2O(6)盐酸:HCl NaOH=NaCl H2O(7)形成的钠盐溶于水,可以从储存罐中的烃流体中分离出来。分级分离在催化氢化之后,任选地随后进行如上所述的进一步处理,第二烃流体被分级分离以分离不同的烃混合物。或者,如在本文公开的附加方法和系统中所述,可以对第一烃流体进行分级分离。分级分离过程可以是蒸馏或多个冷凝步骤,以便获得具有良好分离度的几个组分。在一个优选实施方式中,第二烃流体通过蒸馏分级分离。在另一实施方式中,分级分离步骤以蒸馏来进行。在另一实施方式中,第二烃流体,例如储存罐中的第一烃液体为例如60℃,在进入分级分离之前被加热到例如160℃。这允许基于它们各自的物理和化学性质(例如沸点)来控制最终产物组分。先前的初级裂化预计会产生过剩能量,其中一部分可用于分级分离。在又一实施方式中,第一烃液体在分级分离之前被加热。分级分离器可以使用填充床、筛板、钟形底部、填充材料或确保良好气/液接触的其它材料。接触的质量对获得塔内的组分的良好分离非常重要。在一个实施方式中,可以使用填充床。在一个实施方式中,设想从分级分离器中收集三种组分,轻组分、中组分和重组分。在又一实施方式中,从所述分级分离步骤获得三种最终产物,它们是轻组分,例如主要是C6至C10;中组分,例如主要是C11至C20;和重组分,例如主要是C21及以上。通常地,轻组分在冷凝后在塔的顶部收集。中组分,通常是柴油产物,在塔的底部和顶部之间收集,其中质量符合规范。重组分在塔的低点收集。组分的定义在文献和行业中各不相同,这取决于关注的焦点,但也因为所涉及的化学并不严格按照碳的数量来划分。根据本发明,组分应被理解为并由下面定义:·轻组分:主要是C6至C10·柴油(中组分):主要是C11到C20。·重组分:主要是C21和更高。在又一实施方式中,轻组分被冷凝且任选地分离,导致至少一种轻的不可冷凝烃气体,以及其中至少一部分所述轻的不可冷凝的烃气体被再循环至气体燃烧器并在其中燃烧,以向所述初级裂化提供热量。在又一实施方式中,从分级分离器获得的产物(“组分”)的数量可以少于或多于三个,即两个、四个、五个或六个。在又一实施方式中,碳原子的范围可以不同于如上所述。例如,C6至C11、C12至C21和C22及更高。再沸器位于塔的底部。再沸器向分级分离器提供必要的热量,特别是蒸发消耗的热量。在一个实施方式中,分级分离器在真空下操作,但是也可以设计成在任何压力,通常至多50巴的压力下操作。在另一实施方式中,分级分离器设计成在真空下操作,进料在进入分级分离器之前在预热器中被预热至约160℃。在该温度下,进料将为大约50/50wt%的蒸汽和液体的分配比。由于加热后的混合进料流,在分级分离器之前引入闪蒸容器,以确保充分的液-汽分离,从而蒸汽不会产生湍流并干扰分级分离器的平衡。在另一实施方式中,塔(Column)的直径为1000mm,高度为15000mm。在一个实施方式中,塔的顶部操作压力为100毫巴,以将底部温度保持在290℃。为了给分级分离器提供一些工艺灵活性,可以在不同的进料位置将进料引入分级分离器,并且可以调节侧排(sidedraw)的位置。如本领域技术人员所知,这种分级分离器将不再详述。如前所述,重组分可以部分或全部再循环到工艺中。它可以被进料到初级裂化反应器、氢化前催化裂化反应器中,或者进料到氢化后催化裂化反应器,而不需要任何显著的处理,或者当它们存在于工艺中时,在这些反应器中的几个中同时进料。在一个实施方式中,重组分在没有特定化学处理的情况下再循环到反应器中。尽管优选将组分加热至汽化,以便获得烃气体组分。重组分可以全部或部分返回到初级裂化反应器,在这种情况下,蒸发可能是不必要的。或者,重组分可以全部或部分返回到催化裂化器。这些再循环回路通常根据模型或观察到的过程操作参数进行设计和激活。如流程工业中已知的那样,由于不同反应器的负荷可能不同,再循环可能需要工艺调整。或者,它可以被进料到专用重组分催化裂化器,如下所述。重组分裂化在另一实施方式中,该方法包括在重组分裂化反应器中进行重组分裂化的步骤,该反应器仅针对来自分级分离的重组分进行运行。这样,较轻组分(即碳链比重组分短的组分,例如柴油)的一般工艺产率随着重组分中较长的烃链裂化成较短的链(例如在柴油范围内)而增加。在一个实施方式中,这种替代方案优于整个烃气体的催化裂化(氢化前催化裂化或氢化后催化裂化),因为当气体较轻时,防止了气体的潜在“柴油组分”不希望地裂化成较轻的组分。在另一实施方式中,液体重组分在进入重组分催化裂化器之前被加热和蒸发至接近420℃的温度。重组分催化裂化器可以在350℃和550℃之间,优选在380℃和460℃之间的温度下操作,其中温度范围是为1巴下操作定义的。在一个实施方式中,操作压力保持在1巴的左右,但是操作被认为是在0.1巴至10巴的压力范围内,例如在0.5巴至5巴的压力范围内,例如在0.7巴至2巴的压力范围内,例如在0.9巴至1.1巴的压力范围内。在一个实施方式中,重组分的催化裂化是在350℃和550℃之间的温度,以及优选在380℃和460℃之间的温度,例如约420℃的温度下进行。在另一实施方式中,重组分催化裂化是在0.1巴至10巴,优选1巴的操作压力和350℃至550℃,优选380℃至460℃的温度下进行的。在一个实施方式中,来自重组分裂化的所得的流是气相,并且可以在氢化前或氢化后引入上游的催化氢化反应器、分级分离器或催化裂化反应器。当重组分裂化产生的流被进料到催化氢化时,它应该被冷却到催化氢化反应器的温度,例如如上所述在1巴下低于270℃。如果在催化氢化后将所得的流直接引入分级分离器或储存罐,该流将被冷却至储存罐的温度,例如约60℃。此外,当进行重组分裂化时,重要的是确保有足够的氢以确保裂化后不存在双键,因为重组分的重组分裂化可能在反应过程中形成双键。因此,在一个实施方式中,可以添加额外的工业氢气源。不可冷凝气体在初级裂化和附加处理过程中,可能会形成不可冷凝气体。初级裂化后的不可冷凝气体组分将包含碳数主要小于或等于6的烷烃、烯烃、炔烃和环烃。在催化氢化或催化裂化之后分离后,它将主要由碳数为1至6的烷烃组成。在本文中,“主要小于或等于6的碳数”应理解为优选至少50wt%的碳数低于6,例如至少55wt%的碳数低于6,例如至少60wt%的碳数低于6,更优选至少65wt%的碳数低于6,例如至少70wt%的碳数低于6,例如至少75wt%的碳数低于6,例如至少80wt%的碳数低于6,最优选至少85wt%的碳数低于6,例如至少90wt%的碳数低于6,例如至少95wt%的碳数低于6,例如至少97wt%的碳数低于6,例如至少99wt%的碳数低于6。在一个实施方式中,分离后的第一不可冷凝气体被进一步冷却至部分冷凝,通常产生包含气体、油和水的三相流体。在一个实施方式中,气体被冷却至35℃左右。然后流体被分离。不可冷凝气体分离器的一个实施方式是罐内的改进的旋风分离器,实现气、油和水的三相分离。在另一实施方式中,气体被转移到本领域已知的气体洗涤器/过滤器,以确保气体是清洁的,没有像S和Cl这样的污染物,并且在大约相同的温度(例如35℃)下运行。然后,在连续和稳定状态操作期间,清洁的不可冷凝气体将在气体燃烧器中燃烧,以加热初级裂化反应器。分级分离后不可冷凝气体分离在另一实施方式中,冷凝后获得的多相烃组合物直接进料到分级分离中,无需预先分离。在这种情况下,冷凝可以更温和,旨在使多相组合物达到分级分离器入口处所需的压力和温度条件。在这种情况下,来自分级分离的轻组分被进料到分级分离后冷凝器,然后在不可冷凝气体分离器中分离。在又一实施方式中,任选在冷凝器中冷却后,将离开催化氢化或氢化后催化裂化的多相烃流体组合物进料到分级分离中。服务和副产物设备的热管理热管理是过程和操作管理的重要组成部分。根据良好的工艺工程原则,利用热交换器优化热消耗。在一个实施方式中,热油用于在较高温度范围内携带和交换热量,而水用于在较低温度范围内进行热交换。设备中的气体回路清洁的不可冷凝气体与空气混合并燃烧,以产生如前所述操作初级裂化反应器所需的能量。在气体燃烧器中燃烧的不可冷凝气体,连同初级裂化废气的再循环部分,将使烟气中的NOx水平低于当地排放限值。烟气优选在排放前冷却。废水和废渣可能存在来自任选的入口塑料干燥设备、不可冷凝气体分离器、储存罐和设备操作中的废水。废水也可能来自不可冷凝气体洗涤器。也可能存在来自从初级裂化器、初级裂化后的颗粒清洁过滤器、催化再生单元等出来的碳颗粒的收集、输送和分离过程的水。对于这类废水,将通常使用本领域已知的技术来处理废水。固体处理产生的固体,主要是初级裂解产生的烧焦物,但也包括污染物颗粒、剩余的塑料、来自旋风型过滤器和其它过滤器产生的固体残留物等,被收集并进一步处理。这将优选地被输送到本说明书范围之外的专门加工设备中。物料平衡来自本文所述废塑料方法的主要最终产物是包含在中组分中的柴油,其试验性转化率(tentativeconversionratio)为20wt%至80wt%(重量百分比),例如25%至35%、35%至45%、45%至55%、55%至65%或65%至75%。另外,试验性产生5wt%至70wt%的轻组分,例如10%至20%、20%至30%、30%至40%、40%至50%或50%至60%的轻组分。此外,试验性产生3wt%至25wt%的重组分。在初级裂化过程中,可能会形成一些灰分/碳和不可冷凝气体。灰分产生的量通常在1wt%至30wt%之间变化,不可冷凝气体可以通常在1wt%至30wt%之间变化。永久/不可冷凝气体和灰分/碳可重新用于能源生产,以加热初级裂化反应器。将切碎后的废塑料加入到连续运行的工艺中,该工艺包括初级裂解、气相催化氢化和分级分离,提供了高效率、高产量以及稳定和可预测质量的燃料。此外,当产生的气体的轻组分用于加热连续的初级裂化过程时,它导致几乎能源中性的方法。由废塑料生产烃的附加方法和系统在附加方法中,来自废塑料的燃料和另外的烃通过包括以下步骤的方法生产-提供至少一种塑料材料;-使所述至少一种塑料材料经历初级裂化以获得第一烃流体;-分级分离所述第一烃流体以获得至少一种产物,-使所述至少一种产物中的至少一种经历催化氢化以获得最终产物。在一个实施方式中,催化氢化在气体上进行。在另一实施方式中,通过分级分离获得的至少一种产物被加热以产生所述气体。因此,催化氢化处于气相,并且产物可以在进入催化氢化之前被加热至气相。在另一实施方式中,该方法包括在所述分级分离步骤之前的冷凝步骤,其中所述第一烃流体通过至少所述初级裂化和冷凝步骤获得。在另一实施方式中,该方法包括在所述分级分离步骤之前和任选地在所述冷凝步骤之前的氢化前催化裂化步骤,其中所述第一烃流体通过至少所述初级裂化和氢化前催化裂化以及任选的冷凝步骤获得。在又一实施方式中,从所述分级分离步骤获得至少三种产物,它们是轻组分,例如主要是C6至C10;中组分,例如主要是C11至C20;和重组分,例如主要是C21及以上。在另一实施方式中,所述轻组分被冷凝且任选地分离,导致至少一种轻的不可冷凝烃气体,以及至少一部分所述轻的不可冷凝的烃气体被再循环至气体燃烧器并在其中燃烧,以向所述初级裂化提供热量。因此,分级分离轻组分可以任选地在冷却后通过分级分离后冷凝器和不可冷凝气体分离器进一步处理,以便从轻组分中分离不可冷凝气体。类似于其它实施方式,轻的不可冷凝气体可用于加热如上所述的初级裂化反应器,并将产生一定量的不可冷凝气体用于燃烧。唯一的区别在于,在该实施方式中,与如上所述的其它实施方式相比,轻的不可冷凝气体将不会被饱和/氢化,因此将包含烯烃。低碳烷烃和烯烃之间的热值差异可以忽略不计,因此,预计将向初级裂化反应器提供类似的热量。在另一实施方式中,液体轻组分从不可冷凝气体分离器获得。液体轻组分用作汽油或进一步加工。在又一实施方式中,所述至少一部分所述轻的不可冷凝的烃气体在所述气体燃烧器中燃烧之前,在氢气分离器中进行进一步处理以从不可冷凝的烃气体中分离氢气。在另一实施方式中,氢气被再循环用于催化氢化步骤。在另一实施方式中,经历催化氢化的至少一种产物是所述中组分。这种配置的主要好处是,在分级分离之前,在轻组分和重组分的氢化中不消耗氢气。这减少了所需的外部氢气的量,并且从分级分离中获得的特定组分,例如包含柴油的中组分,可以选择性被氢化。在又一实施方式中,所述重组分被再循环到分级分离器上游的初级裂化、催化裂化或冷凝的一个或多个步骤中。在再一实施方式中,在再循环到分级分离器上游的初级裂化、催化裂化或冷凝的一个或多个步骤之前,使所述重组分经历重组分裂化步骤。在另一实施方式中,所述重组分在经历重组分裂化步骤之前被蒸发,重组分裂化器在气相中操作。因此,在一个实施方式中,在分级分离之后,重组分可以在如上所述的重组分裂化反应器中裂化,并且裂化的重组分产物被再循环到分级分离器以增加较轻组分的产率,例如包含柴油的中组分的产率。这种替代配置将增加产率,但是柴油质量/组成将保持不变,因为可以预期分级分离器以大约相同的方式分离所得组分,无论它是在氢化反应器的下游还是上游,该反应器不应该显著裂化分子。不管配置如何,该组分都会发生氢化。在另一方面,一种用于将废塑料回收成液态烃化合物的废物回收系统,包括:-初级裂化反应器,其能够接收至少一种塑料材料并由所述至少一种塑料材料生产第一烃流体;-分级分离器,其用于所述第一烃流体的分级分离以获得至少一种产物,和-催化氢化反应器,其能够接收所述至少一种产物中的至少一种并生产最终产物,其中,描述了所述初级裂化反应器与所述分级分离器流体连接,以及所述分级分离器与所述催化氢化反应器流体连接。在一个实施方式中,所述第一烃流体是气体。在一个实施方式中,该系统进一步包括用于使从所述分级分离器获得的所述至少一种产物中的至少一种气化的加热器,以及其中所述分级分离器通过所述加热器与所述催化氢化反应器流体连接。催化氢化反应器设计为用于气相,可以增加一个加热器,该加热器用于使在进入催化氢化反应器之前将从分级分离器出来的产物气化。在另一实施方式中,所述系统还包括在分级分离前冷凝所述第一烃流体的冷凝器,以及其中所述初级裂化反应器和分级分离器通过所述冷凝器流体连接。在又一实施方式中,所述系统进一步包括重组分裂化反应器,所述重组分裂化反应器与所述分级分离器流体连接,用于接收从所述分级分离过程获得的重组分,以及其中所述重组分裂化反应器与所述初级裂化反应器和/或所述第一烃流体进一步流体连接。在再一实施方式中,该系统还包括分级分离后冷凝器、不可冷凝气体分离器和气体燃烧器,所述分级分离后冷凝器与所述分级分离器流体连接,用于接收从分级分离过程获得的轻组分,以及其中所述分级分离后冷凝器还与所述不可冷凝气体分离器流体连接,用于分离不可冷凝烃气体;所述不可冷凝气体分离器进一步与所述气体燃烧器流体连接。在另一实施方式中,该系统还包括用于从所述不可冷凝气体中分离氢气的氢气分离器;所述氢气分离器与所述气体燃烧器和所述催化氢化反应器流体连接。然而,在初级裂化过程中产生的氢气不一定伴随着分级分离出的产物至催化氢化。将出现在分级分离器的轻组分中发现H2。如在一个实施方式中所考虑的,如果不是轻组分构成产物,则可以从该轻组分中提取H2,以重新引入至催化氢化反应器的工艺中。例如,可以从返回燃烧器的不可冷凝气体中提取H2。图1示出了本发明的第一实施方式,其包括初级裂化反应器(20),该反应器通过初级裂化能够将至少一种塑料材料转化为作为气体的第一烃流体。第一烃流体通过流体连接被引导至通过催化氢化能够将第一烃流体转化为第二烃流体的催化氢化反应器(40)。第二烃流体通过流体连接被引导至分级分离器(80),其用于将第二烃流体分级分离成三种产物,即轻组分(81)、中组分(82)和重组分(83)。图2示出了本发明的第二个实施方式,其包括初级裂化反应器(20),随后的催化氢化反应器(40)。废塑料被进料到初级裂化反应器(20),产生作为气体的第一烃流体。然后,第一烃流体经历催化氢化(40),形成第二烃流体。在一个替代实施方式中,在初级裂化反应器(20)的出口处存在例如在图8(27)所示的过滤器(图2中未示出)。在催化氢化(40)之后,烃流体在冷凝器(60)中冷凝,并在冷凝后分离器(65)中分离,导致第一不可冷凝气体和作为第二烃流体的第一烃液体以进入分级分离器。第一烃液体被进料到分级分离器(80),并被分离成轻组分(81)、中组分(82)和重组分(83)。在替代实施例(未示出)中,第二实施方式还包括将第一烃液体进料到储存罐,并在进入分级分离器(80)之前对其进行预热。从冷凝后分离器(65)获得的第一不可冷凝的烃气体被进料到与初级裂化反应器(20)相连的气体燃烧器(19)。此外,第一不可冷凝烃气体优选在进入不可冷凝气体分离器(未示出)之前在第二冷却器(未示出)中冷却,并且在被送到气体燃烧器(19)之前在洗涤器中洗涤。这将结合图8进一步阐述。工艺工程领域的技术人员熟悉的变化也可以是这些示意性流程图的一部分。图3示出了本发明的第三实施方式,其中废塑料被进料至初级裂化反应器(20)。在第一烃流体在催化氢化反应器(40)中被催化氢化之前,作为气体离开初级裂化反应器(20)的烃流体然后在氢化前催化裂化反应器(30)中经历催化裂化。所得烃流体然后在冷凝器(60)中冷凝,并在冷凝后分离器(65)中分离第一不可冷凝的烃气体和第一烃液体。第一烃液体被进料至分级分离器(80)以将第二烃流体分级分离成三种产物,即轻组分(81)、中组分(82)和重组分(83)。第一不可冷凝烃气体被再循环至气体燃烧器(19)加热初级裂化反应器(20)。塑料被进料到初级裂化反应器(20),产生烃流体,该烃流体被进料到氢化前催化裂化器(30)。或者(未示出),也可以包括如图8所示的在初级裂化反应器(20)出口处的颗粒过滤器。在催化裂化(30)之后,第一烃流体/气体被进料至催化氢化反应器(40)。或者(未示出),可以包括如图8所示的在氢化前催化裂化反应器(30)出口处的冷却器。催化氢化后,第二烃流体在冷凝器(60)中冷凝,并在冷凝后分离器(65)中分离。工艺工程领域的技术人员熟悉的变化也可以是这个示意性流程图的一部分。特别地,图8和图3的流程图的比较可以得到多个单元的指示(在图8中),这些单元可以包括在基于图1至7和图9所示的流程图的其它实施方式中。图4示出了本发明的第四实施方式,其中进行氢化后催化裂化。塑料被进料到初级裂化反应器(20),产生第一烃流体。作为气体的第一烃流体然后被进料到催化氢化反应器(40)。或者(未示出),可以包括如图8所示的在初级裂化反应器(20)出口处的过滤器。在催化氢化(40)之后,所得的烃流体在进料到冷凝器(60)和冷凝后分离器(65)之前在氢化后催化裂化器(50)中裂化,产生第一不可冷凝的烃气体和第一烃液体。第一烃液体被进料至分级分离器(80)以分级分离成三种产物,即轻组分(81)、中组分(82)和重组分(83)。第一不可冷凝烃气体被再循环至气体燃烧器(19)加热初级裂化反应器(20)。工艺工程领域的技术人员熟悉的变化也可以是这个示意性流程图的一部分。图5示出了本发明的第五实施方式,其中在重组分裂化反应器(35)中的专用重组分催化裂化之后,催化氢化反应器(40)可以接收重组分(83)的补充进料。重组分裂化反应器(35)可以在将重组分(83)重新注入工艺的上游之前对其进行处理,具有增加轻组分和中组分产量的优点。来自重组分裂化的所得的流是气相,并且可以引入至催化氢化反应器(40)的上游或分级分离器(80)的上游。这个过程类似于图2中的过程,但是其是针对重组分(83)。不从设备除去,或者在任选加热后返回到一个或几个反应器中,而是在任选加热后将一部分进料到重组分裂化反应器(35)中,然后将该反应器的出口重新引入到主工艺流中,或者在催化氢化(40)的上游或下游,或者两者都引入。如流程工业中已知的那样,由于不同反应器的负荷可能不同,再循环可能需要工艺调整。本领域技术人员熟悉的补充流程项目(例如图8的详细图表中所表示的那些)和变化也是本发明的一部分。图6示出了根据本发明的第六实施方式,其中初级裂化反应器(20)接收部分或全部重组分(83)的补充进料,而在分级分离器(80)和初级裂化反应器(20)之间没有显著处理。这个过程类似于图3中的过程,但是其是针对重组分(83)。催化氢化反应器(40)也可以接收重组分(83)的补充进料,而无需任何显著的处理。在催化氢化反应器之前或之后的催化裂化反应器也可以接收部分或全部重组分的补充进料,存在或不存在中间重组分裂化。该实施方式代表了重组分(83)在没有额外处理的情况下进入该过程的替代再循环。尽管优选将重组分(83)加热至汽化,以便获得烃气体组分。重组分(83)可以全部或部分返回到初级裂化反应器(20),在这种情况下,蒸发可能不是必要的。或者,重组分(83)可以全部或部分返回至氢化前催化裂化反应器(30)。这些再循环回路通常根据模型或观察到的过程操作参数进行设计和激活。如流程工业中已知的那样,由于不同反应器的负荷可能不同,再循环可能需要工艺调整。工程工艺领域技术人员熟悉的补充过程项目(例如图8的详细图表中所表示的那些)和变化也是该示意性的流程图的一部分。图7示出了本发明的第七实施方式,其中从冷凝器冷凝(60)后获得的多相烃组合物被直接进料至分级分离器(80)。在这种情况下,冷凝可以更温和,旨在使多相组合物达到分级分离入口处所需的压力和温度条件。轻组分(81)在不可冷凝气体分离器(95)中分离之前被进料至分级分离后冷凝器(85)。进一步说明的是,废塑料进料被处理并进料至初级裂化反应器(20),在此之后,该过程类似于图3所述的过程,直到烃流体到达冷凝器(60)。在这种情况下,冷凝(60)产物不经分离直接进料至分级分离器(80)。轻组分(81)被冷凝,不可冷凝气体在不可冷凝气体分离器(95)中被分离,然后被进料至气体燃烧器(19)。或者,如图8所示,在不可冷凝气体进入气体燃烧器(19)的途中洗涤器对其进行清洁。工程工艺领域技术人员熟悉的补充过程项目(例如图8的详细图表中所表示的那些)和变化也是本发明的一部分。图8示出了本发明的第八实施方式,示出了详细的图。在第八实施方式中,废塑料进料(10)被装载在料斗(11)中,由输送机(12)清空,将其进料到初级裂化反应器(20)。通常通过工艺副产物的燃烧产生热量,该副产物优选不可冷凝的气体或烧焦物。在过渡期间,如启动反应器时,可以燃烧其它商业燃料来产生热量。不可冷凝气体或任何喷射的燃料在燃烧室中燃烧。所产生的废气可以从初级裂化反应器(20)的一个或几个区域提取(22)并部分再循环(23),其余的作为烟气(24)排放到大气中。废气的再循环使得能够微调初级裂化反应器(20)的不同区域中的热传递。注意,在该实施方式中,初级裂化反应器(20)是间接加热型的,该废气(22,23,24)在任何时候都不接触在初级裂化反应器(20)中经历裂化的烃相。在初级裂化之后,所产生的烃气体在流入氢化前催化裂化反应器(30)之前在过滤器(27)中被清除颗粒,从而缩短烃分子。所得的烃气体流向冷却器(37),然后进入催化氢化反应器(40)。在氢化后,烃气体在冷凝器(60)中冷凝,以产生至少第一不可冷凝的烃气体(气相)和第一烃液体(液态油相),然后在冷凝后分离器(65)中分离。第一烃液体(66)被泵送到储存罐(70)。第一烃液体可以是本领域已知的用钙或钠的氢氧化物纯化的对象。来自储存罐(70)的油(第一烃液体)在进入分级分离器(80)之前在热交换器(77)处被加热。分级分离器(80)将第一烃液体分离成三种烃组分:轻组分(81)、中组分(82)和重组分(83)。来自冷凝后分离器(65)的第一不可冷凝烃气体(91)包括主要来自C1至C6的轻的“不可冷凝”气体、蒸汽和较重烃气体组分的混合物。第一不可冷凝的烃气体(91)在第二冷却器(92)中冷却,然后进料入不可冷凝的气体分离器(95)。在第二冷却器(92)中,蒸汽和较重的烃组分分别冷凝成水和第二烃液体(液体油组分)。第二烃液体(96)然后在不可冷凝气体分离器(95)中被提取,并经由储存罐(70)被送到分级分离器(80)。或者,第二烃液体被直接送至分级分离器(未示出)。水被提取(195),并且精制的第一不可冷凝烃气相(97)首先被进料到洗涤器(99),然后被进料至与初级裂化反应器(20)连接布置的气体燃烧器(19)。当启动初级裂化反应器(20)时,或者在不可冷凝气体产量太低的情况下,可以向气体燃烧器(19)供应商业燃料的补充供应(18)。在裂化塑料的初级裂化过程(20)中,一些副产物以固体碳颗粒(120)或烧焦物的形式形成。从反应器中除去固体颗粒(120),并优选在进一步处理之前冷却,以避免自燃。这些固体(120)可用于燃烧过程,以便为初级裂化反应器(20)产生热量。在一个实施方式中,初级裂化反应器(20)可以包含硅铝酸盐以降低最佳反应温度。这些硅铝酸盐被消耗,并随固体部分(120)一起排出。根据本领域已知的技术,反应器(20)还可以包含矿物质(如CaO)以捕获Cl和S。所得的部分是固体,也将与固体部分(120)一起排出。上面提到的硅铝酸盐和钙矿物不被认为是催化剂,因为它们在该过程中被消耗。产生的固体,主要是初级裂解反应器产生的固体(如烧焦物)(120),但也包括污染物颗粒、剩余的塑料、来自旋风型过滤器(127)和其它过滤器产生的固体残留物等,被收集并进一步处理。这将优选地被输送到本说明书范围之外的专门加工设备中。在图8中示意性地示出了废塑料进料设备,由料斗(11)和输送机(12)组成。虽然在图1至7中没有详细描述,但是在一些实施方式中,它也可以是这些图中所表示的方法的一部分。过滤已经示意性地表示在图8中。虽然在图1至7中没有表示,但是在一些实施方式中,它也可以是这些图中所表示的方法的一部分。图9A示出了由废塑料生产燃料和额外烃的方法的另一实施方式。废塑料经历初级裂化,例如热解(20),产生第一烃流体。第一烃流体被进料至分级分离器(80p)以将流体分离成三种不同的组分,即轻组分(81p)、中组分(82p)和重组分(83p)。分级分离器被设计用于接收未经催化氢化处理的流体。轻组分(81p)部分或全部再循环至分级后分离冷凝器(85)和不可冷凝气体分离器(95),以提取水(195)、液体轻组分(81pl)和不可冷凝气体(91l),其在用于加热所述初级裂化反应器(20)的气体燃烧器(19)使用。液体轻组分(81pl)可被提取并原样出售,或进一步转化。中组分(82p)-包括柴油碳链,但可能具有太高的烯烃比率而不能被认为是柴油-使其经历催化氢化(40),以减少不饱和键的数量,得到可用的柴油产品(82ph)。重组分(83p)可以原样使用,或者如本申请其它地方所述在重组分裂化(35)之后,送回到分级分离器(80)上游的工艺中。在该实施方式中,在分级分离之前没有从第一烃流体中除去水,这就是为什么在分级分离器的设计中必须考虑大量蒸汽的原因。图9B示出了图9A中实施方式的更详细和优选的实施方式。废塑料经历初级裂化,例如热解(20),产生作为气体的第一烃流体。第一烃流体在进入分级分离(80p)之前被过滤器(27)过滤和清洁。过滤提取固体(127)。此外,在进入分级分离(80p)之前,第一烃流体在冷凝器(60)中被冷却并且至少部分冷凝。分级分离器(80p)将流体分离成三种不同的组分,即轻组分(81p)、中组分(82p)和重组分(83p)。分级分离器被设计用于接收未经催化氢化处理的流体。轻组分(81p)部分或全部再循环至分级分离后冷凝器(85)和不可冷凝气体分离器(95),以提取水(195)、液体轻组分(81pl)和不可冷凝气体(91l),其在用于加热所述初级裂化反应器(20)的气体燃烧器(19)使用。液体轻组分(81pl)可被提取并原样出售,或进一步转化。中组分(82p)-包括柴油碳链,但可能具有太高的烯烃比率而不能被认为是柴油-使其经历催化氢化(40),以减少不饱和键的数量,得到可用的柴油产品(82ph)。由于催化氢化反应器(40)处于气相,以及中组分(82p)优选处于液相,中组分(82p)在进入催化氢化(40)之前被热交换器(78)加热成气体。重组分(83p)可以原样使用,或者如本申请其它地方所述(由虚线示出),在重组分裂化(35)之后,被送回到在分级分离器(80p)的上游工艺中。在进入重组分裂化反应器(35)之前,重组分首先在加热器/蒸发器(34)中被加热。在该实施方式中,在分级分离之前没有从第一烃流体中除去水,这就是为什么在分级分离器的设计中必须考虑大量蒸汽的原因。在这种配置中,初级裂化过程中产生的氢气仍可用于催化氢化,这将在下面解释。来自初级裂化(20)的氢气将与分级分离器(80p)的轻组分(81p)一起被收集。它可以在氢气分离器(100)中从不可冷凝的轻组分(91l)分离,优选在洗涤(99)之后(如果洗涤可用)。然后,氢气在催化氢化反应器(40)的上游再循环(101)。该氢气分离器(100)例如可以是膜分离器。作为替代方案,氢气可以在启动工艺时直接供应到反应器中,或者在任何时候作为补充。应当理解,即使在附图的描述中保留了相同的编号,只要所描述的过程发生,不同实施方式中的组件的设计可以不同。实验上述过程为实验的目标。实验1:模型气体混合物的催化氢化在第一实验中,在实验室的模型气体混合物上测试了催化氢化的可行性和各种催化剂。在该实验中,在不同的催化剂上测试了(稀释的)模型气体的催化氢化。为了测量催化剂活性,选择模型气体为含有乙烯和丙烯的烯烃混合物。测量了这两种烯烃的转化率。在如图10所示的实验装置中,来自气体容器(1)的气体混合物与来自液体容器(2)的水混合,并通过预热器(3)。然后,气体/蒸汽混合物通过催化氢化反应器(填充床反应器)(4),然后进入蒸汽冷凝(5)和气体分离单元(6),然后气体在微型GC(9)中分析,水被收集在收集容器(13)中。来自气体容器(1)的气体进入预热器(3)的热区域,其中气体与来自液体容器(2)的水混合,水几乎瞬间蒸发成蒸汽。气体的流量由MFC(质量流量控制器)(7)控制,水流由HPLC-泵(8)控制。使用的水用MilliporeMilli-DI系统去离子,并从容器中供给。预热器(3)和反应器(4)位于可垂直分割的两区管式炉中。炉中的两个温度区域彼此独立控制,温度设定为催化剂床的入口温度尽可能接近所需温度。温度由四个热电偶监控,两个在预热器(3)中,两个在反应器(4)中。在催化剂床开始时测量入口温度,在床结束时测量出口温度。实验在150℃、200℃、250℃和300℃的温度和环境压力下进行;在某些情况下,还研究了350℃。表I:模型气体成分所研究的催化剂在20000h-1的空速下测试的。为了避免床中的梯度,使用烧结α-氧化铝将催化剂床稀释6倍。当达到稳态运行并在每个测试点进行验证时,至少提取三个气体样本。如果发现三次连续的气相色谱分析是相同的(其间的最小时间间隔为10分钟),则认为条件是稳定的,并将实验条件更改为新的测试点。使用瓦里安(Varian)CP-4900双通道微型气相色谱仪(一个5A分子筛PLOT柱和一个PoraPlot柱,具有双TCD检测器)进行气体分析。催化剂通过本领域已知的初湿浸渍法制备。制备了一系列δ-氧化铝上的负载金属,并在模拟代表塑料热解反应器的预期进料的气体混合物中对乙烯和丙烯的氢化进行了测试。结论:如图11所示,观察到良好的转化率,尤其是Cu-Mn/Al2O3催化剂。实验2:热解反应器烃气体的催化氢化在本实验中,我们对一个每天5吨塑料的处理能力的示范设备生产的热解产品(烃流体)的一部分进行了氢化测试。如图12所示,从热解反应中获得的烃气体然后在示范间歇蒸馏塔中进行分级分离,焦点集中在柴油燃料的典型温度范围,即140℃至380℃,以提供主要由柴油C10-C20制成的烃组合物。一部分馏出物在类似于图10所示装置的实验装置中使用实验1中的催化剂在气相中氢化,剩余部分馏出物未经处理。参照实验装置,气体容器(1)中的气体是氢气,而液体容器(2)中的液体是馏出物。两个烃样品-一个氢化,另一个未处理(未氢化),通过荧光指示剂吸附进行烃类型分析,如表II所示。结果列于表II。表II测试单位未氢化氢化的方法饱和化合物%v/v35,256,1ASTMD1319芳族化合物%v/v9,87,5ASTMD1319烯烃%v/v55,036,4ASTMD1319结论:从表II可以看出,氢化产物中的烯烃水平明显降低。因此,氢化有助于显著增加烃的饱和分数。附图标记1:气体容器2:液体容器3:预热器4:催化氢化反应器5:冷凝器6:分离器7:MFC8:HPLC-泵9:微型GC10:废塑料进料11:料斗12:输送机13:收集容器18:补充供应19:气体燃烧器20:初级裂化反应器22:初级裂化反应器气体提取物23:用于再循环的初级裂化反应器提取气体25:排出的烟气27:过滤器30:氢化前催化裂化反应器34:加热器/蒸发器35:重组分裂化反应器37:冷却器40:催化氢化反应器50:氢化后催化裂化反应器60:冷凝器65:冷凝后分离器66:第一烃液体70:储存罐77:分级分离前的热交换器78:催化氢化前的热交换器80:分级分离器80p:设计用于接收未经催化氢化处理的流体的分级分离器81:轻组分81p:具有较高烯烃比率的轻组分81pl:由81p的分离得到的液体轻组分82:中组分(柴油)82p:具有较高烯烃比率的中组分82ph:82p氢化后的中组分83:重组分83p:具有较高烯烃比率的重组分85:分级分离后冷凝器91:第一不可冷凝烃气体91:由81p产生的轻的不可冷凝烃气体92:第二冷却器95:不可冷凝气体分离器96:第二烃液体97:精制的第一不可冷凝烃气体99:洗涤器100:氢气分离器101:氢气120:来自初级裂化反应器的固体(烧焦物)127:来自过滤的固体170:从储存罐中提取的水和净化液195:从不可冷凝气体分离器中提取的水当前第1页1 2 3 
再多了解一些
本文用于企业家、创业者技术爱好者查询,结果仅供参考。