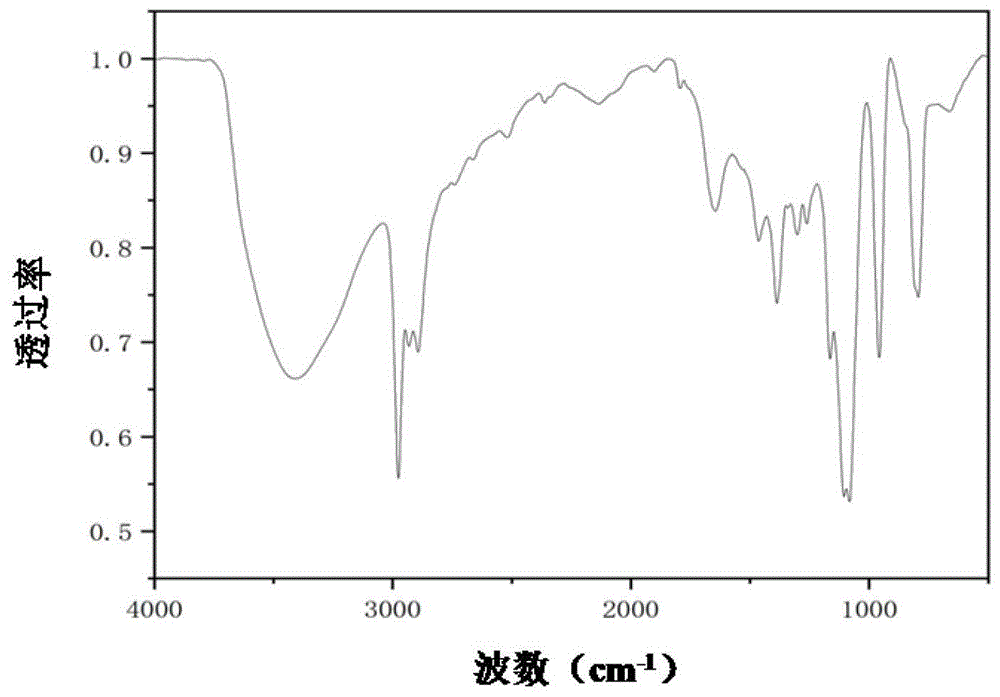
本发明涉及金属防护技术领域,尤其涉及一种防护涂料及其制备方法和应用。
背景技术:
金属材料因其优良的机械性能、导电性以及可铸造性,广泛应用于建筑工业、机械制造业、化学化工等应用领域。而因大部分金属在热力学上的不稳定性,在使用中往往会出现自发腐蚀的趋势,造成重大的经济损失。在金属防护领域中,在金属表面涂敷膜层及有机涂层具有成本低、操作简单以及实用性强等特点,是目前应用最广泛的金属材料防护手段。然而,现有金属防护涂层价格普遍昂贵,且在疏水疏油、附着性、抗腐蚀性方面存在一定的局限。
技术实现要素:
本发明旨在至少解决现有技术中存在的技术问题之一。为此,本发明提出一种防护涂料,疏水疏油性好、附着性好、抗腐蚀性能强。
同时,本发明还提供所述防护涂料的制备方法和应用。
具体地,本发明采用的技术方案如下:
本发明第一方面是提供一种防护涂料,所述防护涂料的制备原料包括:双水解官能团硅烷、多水解官能团硅烷;所述双水解官能团硅烷为含有两个与si连接的可水解官能团的硅烷,所述多水解官能团硅烷为含有两个以上与si连接的可水解官能团的硅烷。
根据本发明第一方面的防护涂料,至少具有如下有益效果:
本发明将双水解官能团硅烷、多水解官能团硅烷共同使用,双水解官能团硅烷、多水解官能团硅烷含有可水解官能团,可利用可水解官能团实现与无机材料(如金属、玻璃、二氧化硅等)发生偶联反应,同时双水解官能团硅烷、多水解官能团硅烷中的不可水解基团可与有机物质进行反应,因此在涂料中采用双水解官能团硅烷、多水解官能团硅烷可实现无机材料与有机物质的化学连接。在将涂料涂敷在金属等无机材料基底表面时,双水解官能团硅烷使涂料具有液体排斥作用,赋予涂料优异的疏水疏油性和抗腐蚀作用,而多水解官能团硅烷可给涂料带来良好的物理化学稳定性,使涂料具有附着性好的特点。
在本发明的一些实施方式中,所述可水解基团包括-or、-nhxry、-sr、-coor、x、-on=cr2中的任意一种或多种,其中r为c1~c20直链或支链烷基、环烷基、芳烯基及其衍生基团,x为0~2,x y=2或3,x为卤素。
在本发明的一些实施方式中,所述双水解官能团硅烷包括r2-si-m2、si2r'm2r4、环状的[sir2o]n中的任意一种或多种;其中,每个r独立地选自c1~c20直链或支链烷基、c1~c20直链或支链取代烷基、环烷基、芳烯基及其衍生基团,r'包括但不限于-o-、-ch2-、-nr-、-s-、-nr-r-nr-、-r-o-r-;m为可水解基团,每个m相同或者不同。
在本发明的一些实施方式中,所述双水解官能团硅烷包括二甲基二甲氧基硅烷、二甲基二乙氧基硅烷、二乙基二甲氧基硅烷、二乙基二乙氧基硅烷、二丙基二甲氧基硅烷、二丙基二乙氧基硅烷、二甲基二氯硅烷、二甲基二氨甲基硅烷、二乙基二氯硅烷、二乙基二氨甲基硅烷、n-β-氨乙基-γ-氨丙基甲基二甲氧基硅烷、二甲基二丁酮肟基硅烷中的任意一种或多种。
在本发明的一些实施方式中,所述多水解官能团硅烷包括r4-m1-si-mm1、si2r'mm2r6-m2、si3r'2mm3r8-m3、si4r'3mm4r10-m4中的任意一种或多种;其中,每个r独立地选自c1~c20直链或支链烷基、c1~c20直链或支链取代烷基、环烷基、芳烯基及其衍生基团,每个r'独立地选自-o-、-ch2-、-nr-、-s-、-nr-r-nr-、-r-o-r-;m为可水解基团,每个m相同或者不同,m1、m2、m3和m4的范围大于2且小于等于10,且4-m1≥0,6-m2≥0,8-m3≥0,10-m4≥0。所述多水解官能团硅烷中的r、r'和m与双水解官能团硅烷中的r、r'和m可以相同,也可以不相同。
在本发明的一些实施方式中,所述多水解官能团硅烷包括甲基三甲氧基硅烷、甲基三乙氧基硅烷、乙基三甲氧基硅烷、乙基三乙氧基硅烷、四甲氧基硅烷、四乙氧基硅烷、二(三乙氧基硅基)甲烷、1,2-二(三乙氧基甲硅烷基)乙烷、甲基三丁酮肟基硅烷、γ-氨丙基-三乙氧基硅烷、γ-(2,3-环氧丙氧基)丙基三甲氧基硅烷、乙烯基三丁酮肟基硅烷、γ-甲基丙烯酰氧基丙基三甲氧基硅烷、γ-缩水甘油醚氧丙基三甲氧基硅烷、γ-巯丙基三乙氧基硅烷、γ-巯丙基三甲氧基硅烷、n-β-(氨乙基)-γ-氨丙基甲基二甲氧基硅烷、γ-氨丙基三甲氧基硅烷、乙烯基三甲氧基硅烷、乙烯基三乙氧基硅烷中的任意一种或多种。
在本发明的一些实施方式中,所述防护涂料的制备原料还包括催化剂。在催化剂作用下,防护涂料中的双水解官能团硅烷、多水解官能团硅烷可与基材进行高效的缩合反应。
在本发明的一些实施方式中,所述催化剂为碱。基础的硅烷分子通常有四个取代基,含有不同取代基的硅烷分子的物理化学性质存在明显的差异。硅烷分子在酸性或碱性条件下的反应特征也存在显著的差异,当使用酸作为催化剂时,缩合反应较慢,而使用碱作为催化剂时,缩合反应较快。而且,酸与活泼金属难以共存,将使涂料无法应用于活泼金属的防护,存在显著的使用局限,而碱则受活泼金属的影响较小。
在本发明的一些实施方式中,所示碱的ph为8~12。
在本发明的一些实施方式中,所述碱包括有机碱和/或无机碱,所述有机碱包括二乙胺、三乙胺、二乙烯三胺、乙醇钠、异丙醇铝、四甲基氢氧化铵、n,n-二甲苯胺、喹啉、吡啶、正丁基锂中的任意一种或多种,所述无机碱包括氨水、偏铝酸钠、氢氧化钠、氢氧化钾、氢氧化钙、碳酸铵、氰化钾、氢化钠、叔丁醇钾、碳酸钠中的任意一种或多种。
在本发明的一些实施方式中,所述防护涂料的制备原料还包括溶剂。所述溶剂可选择水和/或有机溶剂,所述有机溶剂包括水溶性溶剂和非水溶性溶剂。优选地,所述溶剂包括水和有机溶剂。所述水溶性溶剂包括醇类、酮类、醚类、酯类等,如甲醇、乙醇、异丙醇、丙酮、甲乙酮、乙醚、二异丙醚、四氢呋喃、乙酸乙酯、乙酸甲酯、环氧丙烷、丙酮、甲基丁酮、甲基异丁酮、乙二醇单甲醚、乙二醇单乙醚、乙二醇单丁醚等及其混合物;所述非水溶性溶剂包括苯、甲苯、二甲苯、苯乙烯、丁基甲苯、乙烯基甲苯、三氯乙烯、二氯甲烷、氯苯、二氯苯、二硫化碳、四氯化碳、正戊烷及其异构体、正己烷及其异构体、环己烷及其异构体、辛烷、十六烷、液体石蜡等中的任意一种或多种。
在本发明的一些实施方式中,所述双水解官能团硅烷与多水解官能团硅烷的摩尔比为(0.001~999):1,优选0.01~100:1,进一步优选0.05~50:1,更优选0.1~10:1。
在本发明的一些实施方式中,所述催化剂的质量为双水解官能团硅烷、多水解官能团硅烷总质量的1%~10%。
在本发明的一些实施方式中,所述溶剂包括水和有机溶剂,所述溶剂的质量为双水解官能团硅烷、多水解官能团硅烷总质量的1%~1000%,优选50%~300%。
本发明的第二方面是提供上述防护涂料的制备方法,包括如下步骤:将所述防护涂料的制备原料混合。
具体地,将所述双水解官能团硅烷、多水解官能团硅烷和催化剂溶于溶剂中,反应得到所述防护涂料。
更具体地,将所述双水解官能团硅烷、多水解官能团硅烷溶于有机溶剂中,得到溶液1;将催化剂溶于水中,得到溶液2;将所述溶液1和溶液3混合,反应得到所述防护涂料。
在本发明的一些实施方式中,所述反应的温度为0~200℃,优选10~100℃;反应的时间为0.01~500h,优选20min~100h,更优选20~250min。
本发明的第三方面是提供一种防护涂层,所述防护涂层由上述防护涂料制得。
本发明还提供所述防护涂层的制备方法,包括如下步骤:将所述防护涂料涂覆在基材表面,固化得到所述防护涂层。
在本发明的一些实施方式中,所述涂覆的温度为-20~200℃,优选10~100℃;所述固化的温度为10~200℃,优选50~150℃;固化的时间为0.01~100h,优选20min~100h,更优选20~250min。
在本发明的一些实施方式中,所述涂覆、固化步骤可重复进行,即在固化后可再继续涂覆、固化,如此循环。重复次数可以为1~1000次,优选1~10次。
在本发明的一些实施方式中,所述防护涂料在基材表面的涂覆量为1ml:1~15cm2,优选1ml:5~10cm2。
在本发明的一些实施方式中,所述涂覆方法包括但不限于喷涂、浸涂、旋涂等。
在本发明的一些实施方式中,所述基材为无机基材,包括金属、钢材、玻璃、木材、二氧化硅中的任意一种或多种,优选金属、钢材。
在本发明的一些实施方式中,所述金属包括铁、铜、铝中的任意一种或多种。
本发明还提供一种无机材料,所述无机材料包括无机基材以及覆盖在所述无机基材表面的防护涂层。
相对于现有技术,本发明具有如下有益效果:
本发明基于含可水解基团的硅烷分子的反应特性,成功地将疏水有机硅体系应用于防护涂料的制备中,本发明的防护涂料经涂覆、固化形成的涂层具有优良的强度与韧性、附着力、疏水疏油性和抗腐蚀效果,适用于各类基材,尤其是金属等无机基材的表面防护。本发明的防护涂层可以与各类硅烷耦合剂复配,因此,在防护涂层表面还可以涂覆多层防护涂料或者含有硅烷偶联剂的各类涂料,具有良好的可拓展性,能满足不同的应用需要。
而且,本发明的制备原料成本较低、来源广泛且化学性质稳定、无毒,合成工艺简单方便,具有很好的经济和社会效益。
附图说明
图1为实施例1的防护涂料的红外光谱图;
图2为玻璃表面喷涂实施例1的防护涂料前后的实物对照图;
图3为铁片表面喷涂实施例2的防护涂料前后,在3.5%的盐水中浸泡4天后的效果对照图;
图4为铁片表面喷涂实施例2的防护涂料前后,在ph=3的盐酸溶液中浸泡4天后的效果对照图;
图5为铁片表面喷涂实施例2的防护涂料前后,在ph=1的盐酸溶液中浸泡7天后的效果对照图;
图6为防护涂层在经附着力测试之后的效果图;
图7为不同催化剂条件下的防护涂层经附着力测试之后的效果对比图。
具体实施方式
以下结合具体的实施例进一步说明本发明的技术方案。
实施例1
先将甲基三甲氧基硅烷和二甲基二甲氧基硅烷按照摩尔比为1:1混合溶于质量分数为硅烷总量的135%的乙醇中,添加质量分数为1%(基于硅烷总量)的二乙胺和20%(基于硅烷总量)的水,在室温条件下搅拌反应20min,得到硅烷水解液,即防护涂料。将硅烷水解液喷涂在基材(铁片/铝片/铜片/玻璃)表面(涂覆量1ml:9cm2),在50℃的环境下固化1h,固化之后将得到的硅烷水解液重复涂覆于基材(铁片/铝片/铜片/玻璃)表面,喷涂-固化-喷涂过程重复3次,即获得有机硅金属防护涂层。
实施例2
先将γ-氨丙基-三乙氧基硅烷和二甲基二甲氧基硅烷按照摩尔比为1:1混合溶于质量分数为硅烷总量的150%的异丙醇中,添加质量分数为2%(基于硅烷总量)的三乙胺和30%(基于硅烷总量)的水,在30℃条件下搅拌反应30min,得到硅烷水解液。将硅烷水解液喷涂在基材(铁片/铝片/铜片/玻璃)表面,在50℃的环境下固化1h,固化之后将得到的硅烷水解液重复涂覆于基材(铁片/铝片/铜片/玻璃)表面,喷涂-固化-喷涂过程重复2次,即获得有机硅金属防护涂层。
实施例3
先将甲基三甲氧基硅烷和二乙基二甲氧基硅烷按照摩尔比为1:2混合溶于质量分数为硅烷总量的165%的丙酮中,添加质量分数为3%(基于硅烷总量)的氢氧化钠和40%(基于硅烷总量)的水,在40℃条件下搅拌反应40min,得到硅烷水解液。将硅烷水解液喷涂在基材(铁片/铝片/铜片/玻璃)表面,在75℃的环境下固化2h,固化之后将得到的硅烷水解液重复涂覆于基材(铁片/铝片/铜片/玻璃)表面,喷涂-固化-喷涂过程重复3次,即获得有机硅金属防护涂层。
实施例4
先将γ-环氧丙氧丙基-丙基三甲氧基硅烷和二乙基二乙氧基硅烷按照摩尔比为1:1混合溶于质量分数为硅烷总量的180%的乙醚中,添加质量分数为4%(基于硅烷总量)的异丙醇铝和50%(基于硅烷总量)的水,在50℃条件下搅拌反应50min,得到硅烷水解液。将硅烷水解液喷涂在基材(铁片/铝片/铜片/玻璃)表面,在90℃的环境下固化3h,固化之后将得到的硅烷水解液重复涂覆于基材(铁片/铝片/铜片/玻璃)表面,喷涂-固化-喷涂过程重复4次,即获得有机硅金属防护涂层。
实施例5
先将γ-巯丙基三甲氧基硅烷和二甲基二氯硅烷按照摩尔比为1:3混合溶于质量分数为硅烷总量的195%的乙酸乙酯中,添加质量分数为5%(基于硅烷总量)的氢氧化钾和60%(基于硅烷总量)的水,在90℃条件下搅拌反应60min,得到硅烷水解液。将硅烷水解液喷涂在基材(铁片/铝片/铜片/玻璃)表面,在95℃的环境下固化1h,固化之后将得到的硅烷水解液重复涂覆于基材(铁片/铝片/铜片/玻璃)表面,喷涂-固化-喷涂过程重复5次,即获得有机硅金属防护涂层
实施例6
先将甲基三乙氧基硅烷和二甲基二氨甲基硅烷按照摩尔比为5:1混合溶于质量分数为硅烷总量的210%的丁酸甲酯中,添加质量分数为6%(基于硅烷总量)的四甲基氢氧化铵和70%(基于硅烷总量)的水,在60℃条件下搅拌反应90min,得到硅烷水解液。将硅烷水解液喷涂在基材(铁片/铝片/铜片/玻璃)表面,在90℃的环境下固化1h,固化之后将得到的硅烷水解液重复涂覆于基材(铁片/铝片/铜片/玻璃)表面,喷涂-固化-喷涂过程重复6次,即获得有机硅金属防护涂层。
实施例7
先将二(三乙氧基硅基)甲烷和二甲基二乙氧基硅烷按照摩尔比为2:1混合溶于质量分数为硅烷总量的300%的异丙醇中,添加质量分数为1%(基于硅烷总量)的二乙胺和20%(基于硅烷总量)的水,在60℃条件下搅拌反应90min,得到硅烷水解液。将硅烷水解液喷涂在基材(铁片/铝片/铜片/玻璃)表面,在90℃的环境下固化1h,固化之后将得到的硅烷水解液重复涂覆于基材(铁片/铝片/铜片/玻璃)表面,喷涂-固化-喷涂过程重复6次,即获得有机硅金属防护涂层。
对比例1
本对比例与实施例7的区别在于,将二乙胺替换为等质量的浓硫酸,即,将碱催化改为酸催化。
对比例2
本对比例与实施例7的区别在于,没有添加二(三乙氧基硅基)甲烷。
对比例3
本对比例与实施例7的区别在于,没有添加二甲基二乙氧基硅烷。
表1.防护涂料的原料组成
注:表1中a:b表示多水解官能团硅烷与双水解官能团硅烷的摩尔比;
c表示催化剂质量与多水解官能团硅烷、双水解官能团硅烷总质量的百分比;
d表示有机溶剂质量与多水解官能团硅烷、双水解官能团硅烷总质量的百分比;
e表示水的质量与多水解官能团硅烷、双水解官能团硅烷总质量的百分比。
性能测试:
(1)实施例1的防护涂料的红外光谱图如图1所示。根据图1可知,在3500cm-1处为oh-的伸缩振动峰;2960cm-1处为甲基的c-h反对称伸缩振动;在1100cm-1处有一宽峰,为si-o-si伸缩振动峰;说明硅烷进行了水解缩聚作用,形成了聚硅氧烷pdms;650cm-1处为醇类物质的-oh峰,进一步说明硅烷水解生成了醇类物质;1460cm-1处为亚甲基的弯曲振动峰,而1380cm-1为甲基的弯曲振动峰;720cm-1处为亚甲基(-ch2-)n(n≥4)的摇摆振动峰,进一步说明实施例1的水解液中进行了聚合反应,成功合成出具有聚硅氧烷pdms的防护涂料。
(2)在玻璃表面喷涂实施例1的防护涂料后,结果如图2所示。图2反映,防护涂料所形成的涂层具有好高的透明度,玻璃的透明度相较喷涂前(空白对照)没有发生明显的改变。
(3)在铁片表面喷涂实施例2的防护涂料后,使铁片在3.5%的盐水中浸泡4天,并与未喷涂防护涂料的铁片(空白对照)进行比较,结果如图3所示。从图3可以看出,未喷涂防护涂料的铁片在3.5%的盐水中浸泡4天后出现明显的锈蚀,边缘锈蚀情况尤其严重,而具有防护涂层的铁片只出现极其轻微的锈蚀。
在铁片表面喷涂实施例2的防护涂料后,使铁片在ph=3的盐酸溶液中浸泡4天,并与未喷涂防护涂料的铁片(空白对照)进行比较,结果如图4所示。从图4可以看出,未喷涂防护涂料的铁片的整个表面都被盐酸严重腐蚀,而具有防护涂层的铁片则没有出现任何腐蚀痕迹。
在铁片表面喷涂实施例2的防护涂料后,使铁片在ph=1的盐酸溶液中浸泡7天,并与未喷涂防护涂料的铁片(空白对照)进行比较,结果如图5所示。从图5可以看出,未喷涂防护涂料的铁片的边缘被盐酸严重腐蚀,而具有防护涂层的铁片则没有出现任何腐蚀痕迹。
(4)采用实施例7、对比例1~3对铁片进行涂覆形成防护涂层,对铁片表面的防护涂层进行接触角、附着力(划格法)测试,同时以未进行任何涂覆的铁片作为空白对照,测试结果如下表2所示。
表2.防护涂层性能测试结果
根据以上结果能够看出,选用碱性催化剂催化,并以双官能团硅烷和多功能团硅烷组合得到的防护涂层性能最好。
实施例3~6的测试结果与实施例1、2、7相似,不再赘述。
上述实施例为本发明较佳的实施方式,但本发明的实施方式并不受上述实施例的限制,其他的任何未背离本发明的精神实质与原理下所作的改变、修饰、替代、组合、简化,均应为等效的置换方式,都包含在本发明的保护范围之内。
本文用于企业家、创业者技术爱好者查询,结果仅供参考。