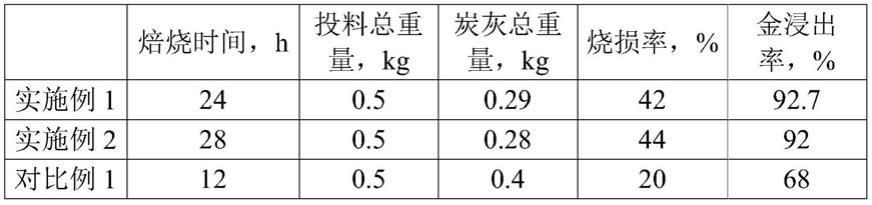
1.本公开涉及冶金技术领域,具体地,涉及一种从载金炭中回收金的方法。
背景技术:
2.在金矿的全泥氰化炭浆工艺过程中,由于活性炭的反复使用以及机械磨损等原因,会产生大量载金炭,这些载金炭的含金品位从几十克/吨至几百克/吨不等,如果不能有效回收其中含有的金,则必然会降低炭浆厂的选冶回收率。然而,这些载金炭具有颗粒较细、杂质较多且品位变化大等特点,这导致无法采用解吸工艺回收其中的金。因此,亟需一种能够从载金炭中有效回收金的方法。
技术实现要素:
3.本公开的目的是提供一种从载金炭中回收金的方法。
4.为了实现上述目的,本公开提供一种从载金炭中回收金的方法,该方法包括:
5.s010.将载金炭制成载金炭球团;
6.s020.将所述载金炭球团于焙烧炉内进行焙烧,得到炭灰,其中,焙烧的条件包括:焙烧温度为800~850℃,焙烧时间为24~28h;
7.s030.将所述炭灰调浆后进行氰化浸出,获取浸出液并对其进行解析电解处理,得到固体金。
8.可选地,步骤s020中,所述将所述载金炭球团于焙烧炉内进行焙烧,得到炭灰,包括:
9.s021.将部分所述载金炭球团置于焙烧炉内并完全覆盖焙烧炉内的引燃物,以使所述载金炭球团被引燃;
10.s022.待步骤s021中添加的部分所述载金炭球团被引燃后,将剩余部分所述载金炭球团沿焙烧炉内壁加入焙烧炉中进行焙烧。
11.可选地,所述载金炭由金矿的全泥氰化炭浆工艺过程产生,包括磨损颗粒炭、磨损粉状炭、车间回收炭和安全筛木屑。
12.可选地,步骤s010中,所述将载金炭制成载金炭球团,包括:
13.将所述载金炭与粘合剂、添加剂和水混合后,送入制团机压制得到所述载金炭球团。
14.可选地,
15.以所述载金炭球团的总重量为基准,所述磨损颗粒炭的用量为20~35重量%,所述磨损粉状炭的用量为20~35重量%,所述车间回收炭的用量为20~35重量%,所述安全筛木屑的用量为5~10重量%,所述粘合剂的用量为7~9重量%,所述添加剂的用量为12~15重量%,水的用量为7~9重量%;
16.优选地,以所述载金炭球团的总重量为基准,所述磨损颗粒炭的用量为20~25重量%,所述磨损粉状炭的用量为20~25重量%,所述车间回收炭的用量为20~25重量%,所
述安全筛木屑的用量为5~7重量%,所述粘合剂的用量为7~8重量%,所述添加剂的用量为14~15重量%,水的用量为7~8重量%。
17.可选地,所述粘合剂包括膨润土、无机粘接剂、有机粘接剂和复合粘接剂中的至少一种,所述添加剂包括固化剂、催化剂、增塑剂和促进剂中的至少一种。
18.可选地,所述载金炭球团的直径为30~50cm,含金品位为200~300g/t。
19.可选地,所述方法还包括在焙烧过程中,向焙烧炉内添加助燃剂的操作,其中,所述助燃剂选自柴油、煤气、焦炭和木材中的至少一种,优选为柴油。
20.可选地,氰化浸出的条件包括:炭灰浆的质量分数为38~40%,ph为10.5~11.5,nacn用量为4~6kg/t。
21.可选地,步骤s010中,在将载金炭制成载金炭球团之前,还包括对所述载金炭进行预处理的操作,其中,所述预处理包括:
22.将所述载金炭进行洗涤2~3次,然后于80~100℃的条件下烘干。
23.通过上述技术方案,本公开的方法通过采用制团
‑
焙烧
‑
氰化提金工艺,能够简单、高效地回收选厂废料
‑
载金炭中的金,具体地,该方法对选厂废料
‑
载金炭中的金的回收率不低于90%。
24.本公开的其他特征和优点将在随后的具体实施方式部分予以详细说明。
具体实施方式
25.以下对本公开的具体实施方式进行详细说明。应当理解的是,此处所描述的具体实施方式仅用于说明和解释本公开,并不用于限制本公开。
26.本公开提供一种从载金炭中回收金的方法,该方法包括:s010.将载金炭制成载金炭球团;s020.将所述载金炭球团于焙烧炉内进行焙烧,得到炭灰,其中,焙烧的条件包括:焙烧温度为800~850℃,焙烧时间为24~28h;s030.将所述炭灰调浆后进行氰化浸出,获取浸出液并对其进行解析电解处理,得到固体金。
27.本公开发明人研究发现,载金炭球团焙烧后的烧损率对载金炭中金的回收率有较大影响,具体地,载金炭球团的烧损率越大,金的回收率越高。本公开通过对载金炭球团的焙烧条件进行调控,有效提升了载金炭球团的烧损率,从而显著提升了载金炭中金的回收率。具体地,在步骤s020中的焙烧条件下进行焙烧后,载金炭球团的烧损率不低于42%,载金炭中的金的回收率不低于90%。
28.通过上述技术方案,本公开的方法通过采用制团
‑
焙烧
‑
氰化提金工艺,能够简单、高效地回收选厂废料
‑
载金炭中的金,此外,该方法还具有工艺流程简单、工艺条件易控、设备简单以及投资成本较低的优点。
29.根据本公开,为了降低焙烧过程中金的损失,步骤s020中,在将所述载金炭球团于焙烧炉内进行焙烧,得到炭灰时,可以先将部分所述载金炭球团置于焙烧炉内并完全覆盖焙烧炉内的引燃物,以使所述载金炭球团被引燃,然后待添加的部分所述载金炭球团被引燃后,再将剩余部分所述载金炭球团沿焙烧炉内壁加入焙烧炉中进行焙烧。
30.在本公开中,具体地,所述引燃物可以是焦炭或者木柴,在进行焙烧前,可以先将所述引燃物点燃,待其燃烧旺盛后将其置于焙烧炉内的筛板上作为底火,在底火达到焙烧温度后,将部分载金炭球团置于焙烧炉内并完全覆盖引燃物。沿焙烧炉内壁加入剩余部分
的载金炭球团,能够在焙烧炉中间留出“火心”,方便焙烧过程中产生的燃气逸出,从而减少焙烧过程中的载金炭飞灰,降低金损失。在焙烧过程中,为了确保载金炭球团能够进行持续、高效的燃烧,可以向焙烧炉内通风,具体地,可以利用鼓风机向焙烧炉内鼓风。
31.在焙烧过程中,可以每隔一段时间对焙烧炉炉内的载金炭球团进行上下翻搅,使粉末状或颗粒状的炭灰落入筛板下方,同时把胶结状的炭灰清理出焙烧炉,防止筛板堵塞,影响鼓风效果。在焙烧后期可以减小风量,将燃烧的火焰逐渐调小,防止炭灰飞溅而影响金的回收率,直至无火,载金炭焙烧完毕,待冷却后将其装入桶中。
32.根据本公开,所述载金炭由金矿的全泥氰化炭浆工艺过程产生,例如可以包括磨损颗粒炭、磨损粉状炭、车间回收炭和安全筛木屑。
33.具体地,磨损颗粒炭和磨损粉状炭是在全泥氰化炭浆工艺的浸出过程中由于机械磨损而产生的废炭,其中,磨损颗粒炭的含金品位较高,约为750~860g/t,磨损粉状炭的含金品位较低,约为20~40g/t。车间回收炭是指从全泥氰化炭浆工艺的浸出车间和电解车间的地面清扫回收的废炭,由于含有粘土杂质,因此其含金品位较低,约为50~60g/t。安全筛木屑产自尾矿安全筛,其含金品位较高,约为330~400g/t。
34.根据本公开,步骤s010中,在将所述将载金炭制成载金炭球团时,可以将所述载金炭与粘合剂、添加剂和水混合后,送入制团机压制得到所述载金炭球团。
35.根据本公开,在制备载金炭球团时,各组分的用量可以在一定的范围内选择,例如,以所述载金炭球团的总重量为基准,所述磨损颗粒炭的用量可以为20~35重量%,所述磨损粉状炭的用量可以为20~35重量%,所述车间回收炭的用量可以为20~35重量%,所述安全筛木屑的用量可以为5~10重量%,所述粘合剂的用量可以为7~9重量%,所述添加剂的用量可以为12~15重量%,水的用量可以为7~9重量%。
36.优选地,以所述载金炭球团的总重量为基准,所述磨损颗粒炭的用量可以为20~25重量%,所述磨损粉状炭的用量可以为20~25重量%,所述车间回收炭的用量可以为20~25重量%,所述安全筛木屑的用量可以为5~7重量%,所述粘合剂的用量可以为7~8重量%,所述添加剂的用量可以为14~15重量%,水的用量可以为7~8重量%。
37.根据本公开,所述粘合剂和所述添加剂可以在一定的范围内选择,例如,所述粘合剂可以包括膨润土、无机粘接剂、有机粘接剂和复合粘接剂中的至少一种,所述添加剂包括固化剂、催化剂、增塑剂和促进剂中的至少一种。其中,上述各添加剂的具体选择可以是领域内常规的,此处不再赘述。
38.根据本公开,所述载金炭球团的直径为30~50cm,含金品位为200~300g/t。
39.具体地,本公开发明人发现,当载金炭球团的含金品位为200~300g/t时,从载金炭球团中回收金的回收率以及效率均较高,因此,本公开中在制备载金炭球团时,可以根据各类载金炭的含金品位,对各类载金炭的添加量进行调控,以进一步提升金的回收率以及效率。
40.根据本公开,为了加快载金炭球团的燃烧,在焙烧过程中,还可以向焙烧炉内添加助燃剂,其中,所述助燃剂选自柴油、煤气、焦炭和木材中的至少一种,优选为柴油。
41.根据本不公开,所述氰化浸出的条件可以在一定的范围内变化,例如,所述氰化浸出的条件可以包括:炭灰浆的质量分数为38~40%,ph为10.5~11.5,nacn用量为4~6kg/t。
42.在本公开中,焙烧后得到的炭灰通常呈现胶结状、粉状或颗粒状,因此,为了提升氰化浸出的效率,在进行调浆之前,还可以对炭灰进行水淬,已将胶结状炭灰分散为小粒度状态。氰化浸出可以在搅拌槽中进行,为了保证氰化浸出的效果,提高金的浸出率,可以对搅拌槽内进行送风。
43.根据本公开,在全泥氰化炭浆工艺过程中,由于长期处于水环境中,载金炭的水分含量较高,而且其在吸附金的同时也会黏附水体中的泥沙等杂质,这会增加焙烧难度以及生产成本,因此,步骤s010中,在将载金炭制成载金炭球团之前,还可以对所述载金炭进行预处理,以除去其中的水分和杂质。其中,所述预处理可以包括:将所述载金炭进行洗涤2~3次,然后于80~100℃的条件下烘干。
44.下面通过实施例来进一步说明本公开,但是本公开并不因此而受到任何限制。
45.本公开实施例中涉及的原料、试剂、仪器及设备,如无特殊说明,均可通过购买获得。
46.实施例1
47.按照如下方法从载金炭中回收金:
48.(1)将22重量%的磨损颗粒炭、22重量%的磨损粉状炭、22重量%的车间回收炭用量、5.5重量%的安全筛木屑、7.1重量%的膨润土、14.3重量%的催化剂和7.1重量%的水混匀,送入制团机中制成直径为30~50cm、且含金品位为200g/t的载金炭球团,其中,磨损颗粒炭、磨损粉状炭、车间回收炭和安全筛木屑预先经过洗涤和烘干处理;
49.(2)将长度为20cm左右的焦炭点燃,待其燃烧旺盛后放入焙烧炉内的筛板上作为底火,在底火温度达到800℃后,加入载金炭球团并将燃烧的焦炭完全覆盖,同时开启鼓风机,进行载金炭球团的焙烧,为加快载金炭球团的焙烧速度,可添加适量柴油作为助燃剂,直到球团燃烧温度达到800℃,然后沿焙烧炉内壁间断性添加载金炭球团,保证焙烧炉中间流出“火心”以便燃气逸出,焙烧24h后,焙烧结束,收集炭灰;
50.(3)将收集得到的炭灰进行水淬,使胶结状的炭灰分散成粒度较小的颗粒状,然后经调浆后进行氰化浸出工序,氰化浸出在机械式搅拌槽中完成,氰化浸出过程中对搅拌槽内送风,以保证氰化浸出的效果,提高金的浸出率,产生的贵液返回解析电解工艺,收集解析电解工艺产生的固体金,其中,氰化浸出的条件包括:炭灰浆的质量分数为40%,ph为10.5~11.5,nacn用量为4kg/t。
51.焙烧过程中,称量并记录投入焙烧炉内的载金炭球团的投料总重量,焙烧结束后,称量并记录收集到的炭灰总重量,计算烧损率(烧损率=(投料总重量
‑
炭灰总重量)/投料总重量
×
100%)并检测金浸出率。
52.实施例2
53.按照实施例1的方法从载金炭中回收金,不同的是:步骤(2)中的焙烧时间如表1所示。
54.对比例1~3
55.按照实施例1的方法从载金炭中回收金,不同的是:步骤(2)中的焙烧时间如表1所示。
56.表1
[0057][0058][0059]
实施例3
[0060]
按照实施例1的方法从载金炭中回收金,不同的是:步骤(2)中的焙烧温度如表2所示。
[0061]
对比例4~5
[0062]
按照实施例1的方法从载金炭中回收金,不同的是:步骤(2)中的焙烧温度如表2所示。
[0063]
表2
[0064][0065]
实施例4~6
[0066]
按照实施例1的方法从载金炭中回收金,不同的是:步骤(1)中制备载金炭球团时,各原料的用量如表3所示。
[0067]
对比例6
[0068]
按照实施例1的方法从载金炭中回收金,不同的是:步骤(1)中制备载金炭球团时,各原料的用量如表3所示。
[0069]
表3
[0070]
[0071][0072]
由表1~3可以看出,本公开的方法能够有效回收载金炭中的金,且回收率较高。
[0073]
以上详细描述了本公开的优选实施方式,但是,本公开并不限于上述实施方式中的具体细节,在本公开的技术构思范围内,可以对本公开的技术方案进行多种简单变型,这些简单变型均属于本公开的保护范围。
[0074]
另外需要说明的是,在上述具体实施方式中所描述的各个具体技术特征,在不矛盾的情况下,可以通过任何合适的方式进行组合,为了避免不必要的重复,本公开对各种可能的组合方式不再另行说明。
[0075]
此外,本公开的各种不同的实施方式之间也可以进行任意组合,只要其不违背本公开的思想,其同样应当视为本公开所公开的内容。
再多了解一些
本文用于企业家、创业者技术爱好者查询,结果仅供参考。