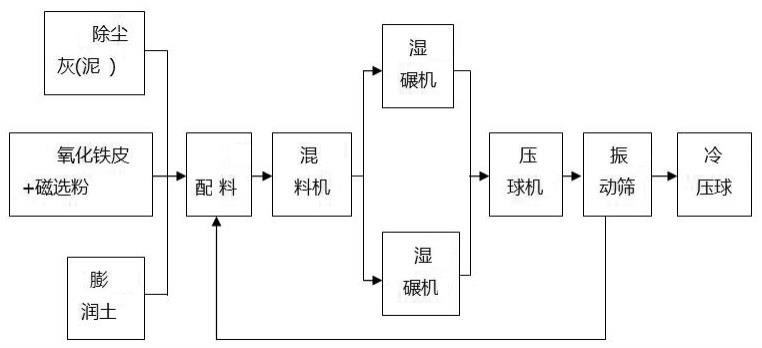
1.本发明涉及一种转炉除尘灰氧化还原压块制备方法及其应用方法,属于冶金固废资源循环利用技术领域。
背景技术:
2.随着转炉炼钢生产的发展,炼钢工艺的日趋完善,目前转炉区域大多采用的是干法静电除尘技术,简称cg法和lt法。它是一种转炉烟气净化及煤气回收干式系统,该除尘方式不用大量浊环水洗涤烟气,而是采用转炉煤气高温高效换热器或蒸发冷却器 静电除尘器 煤气冷却器系统,这对我国转炉炼钢节能减排、实现负能炼钢起到了积极的推动作用。其产生的钢铁固体废渣
‑‑
除尘灰,具有资源再利用价值。除尘灰是炼钢副产品,最好的处理方式是送选烧厂造球烧结后应用于炼钢。在钢铁企业,近些年越来越多人开始注意怎样再次利用烟尘。对除尘灰的综合利用在国内实现除尘灰再利用价值的最大化。转炉除尘灰是在转炉吹炼过程中产生的粉尘,其含有大量氧化铁和钙等氧化物,具有较高的二次利用价值,但是由于其具有产生的温度高、金属化程度高、粒度细、比表面积大、氧化亚铁自燃、扬尘二次污染大等特性,造成其综合利用困难。转炉除尘灰的产生量较大,若不能有效利用,会造成资源浪费,还将占用库房、土地、污染环境,甚至缴纳大额度固废税,以及面临环保处罚等。
3.转炉除尘灰的利用,目前主要有三种方法:转底炉直接还原处理转炉除尘灰和配入烧结原料返回烧结转高炉再到炼钢利用,以及冷压造球返回炼钢利用的方法。
4.1、转底炉直接还原技术的应用;转底炉技术最早发源于美国,发展于日本,技术日趋成熟后被国内钢厂引进。处理原料包括钢铁厂含锌粉尘、氧化铁皮、铁精矿、钒钛磁铁矿、铜渣等。2010年5月由中国钢研院提供工艺技术整体解决方案的山东日照2
×
20万吨固废回收转底炉生产线建成,主要用于固废处理。该生产线的产品是锌粉和金属化球团,金属化球团的金属化率可达75~85%,总投资4亿多元,生产成本1200元/吨。转底炉直接还原技术虽然还原效果不错,但该项目投资过大生产运行成本过高,吨处理成本高达1200元。
5.2、转炉除尘灰返回烧结转高炉再到炼钢利用;以往多为配入烧结原料返回烧结转高炉再到炼钢利用,转炉除尘灰作为烧结原料返回烧结转高炉再到炼钢利用的方法流程长、档次低、能耗大,且增加烧结和高炉操作难度,还易造成烧结故障、影响高炉炉衬寿命。
6.3、冷压造球返回炼钢利用的方法;明显优于前两种方法,得到了广泛应用。冷压造球返回炼钢利用的方法流程虽然短,但往往需要对除尘灰进行加水消解等预处理、需配加价格较高的粘结剂、还需进行成品烘干等,成本仍然较高;且受除尘灰及配料成分、水份等波动影响对加工工艺、粘结剂选择等有较高要求,球团强度很难保证,容易出现在炼钢配加时堵料仓和入炉后快速熔化、热稳定性差、灰分残留等问题。例如:中国发明专利申请2019110718016、名称“一种转炉除尘灰压砖及其制备和利用的方法”,是将含铁固废混合,加入粘合剂,采用压球机冷压成球后自然晾干,然后直接加入转炉生产中应用。存在问题是:
①
强度低只有640n,转炉落差大,物料互相碰撞,易破碎。
②
温度高,粘合剂失效、水分迅
20、高炉灰20-40、磁选粉15-20、轧钢氧化皮20-30、粘合剂(膨润土)5、水3;具体数据要根据用户和实际需求进行调整。
22.本发明创新点:如果将未经高温还原的半成品球团(成型的压块)直接应用于炼钢转炉,由于转炉温度过高,作为粘合剂的膨润土会失效,水分会迅速蒸发,球团会产生快速膨胀而粉化,并随烟气排走,故而,此时还不能直接应用于炼铁炼钢生产,必须要经过氧化还原后,才能真正的应用于生产。试验结果表明,含铁固废经混料压制成球后,再经过氧化还原处理,球团抗压强度可达3000n以上,全铁品位提高10%以上,产品指标完全达到烧结矿的技术质量标准,满足炼铁、炼钢生产原料需要。
23.经实验检测,球团在1150℃环境下还原20分钟后,全铁含量提升了14.96%;在1250℃环境下还原60分钟后,金属化率提高到25.20%。
24.氧化还原技术原理:转炉除尘灰氧化还原压块在氧化还原设备达到一定温度时,含铁固废球团内部的c与co2发生反应生成co,co与氧化铁发生反应即是还原原理。
25.co fe2o3=fe3o4 co2co fe3o4=feo co2co feo=fe co2本发明提高了球团的强度、含铁率及金属化率,直接代替废钢应用于转炉炼钢生产,减少了生产工序,降低了运营成本。
26.本发明的有益效果:a本发明以转炉除尘灰为主料掺配其它固废物料冷压压块,再进行氧化还原,然后与废钢一同加入转炉进行循环利用。该方法工艺、设备要求简单,操作简便易行,氧化还原的除尘灰压块强度适宜,含铁品位较高,储存、转运、配加方便,加入转炉可以替代部分铁矿和废钢,还能起到一定造渣作用;既实现了废弃资源的有效利用、保护了环境,还有效降低炼钢成本,具有良好的社会效益和经济效益。
27.b采用转炉除尘灰氧化还原压块后与废钢一同加入转炉回收利用的形式,相比直接返烧结利用和压球后转炉利用,工艺、设备和操作等各方面更加简便,能耗、成本等更低,在较低成本前提下实现了除尘灰中铁、钙等资源的高效回收。
28.c所制成的转炉除尘灰氧化还原压块使用量折合吨钢在4~33kg,本发明所述转炉除尘灰氧化还原压块中,主要组分最终质量比:转炉除尘粗灰和细灰合计在40%左右,高炉灰25%左右,磁选粉与轧钢氧化皮合计30%左右,既可实现转炉除尘灰的批量化利用,还为其它含铁固废回收利用提供了一条新径。
29.d转炉除尘灰氧化还原压块加入转炉后,在兑入铁水后的高温作用下,部分组分脱水生成的 cao与矿渣中的活性sio2和a12o3又反应生成具有较强耐热性的无水硅酸钙和无水铝酸钙,使氧化还原压块具有一定的高温强度,提升热稳定性。
30.e除尘灰氧化还原压块通过废钢斗加入转炉,物料适用性强,转炉除尘灰氧化还原压块不会破碎粉化,也不会发生堵料问题;且重量较轻、强度较低的转炉除尘灰氧化还原压块先于废钢落入转炉底,可有效减轻废钢对炉底内衬的直接冲击;再者除尘灰氧化还原压块的加入可使转炉炼钢初期炉渣碱度提高,降低mgo在渣中的溶解度,减少转炉冶炼前期炉衬的侵蚀,故可有效降低转炉的护炉成本。
参照附图1。
45.在实施例中,转炉除尘灰氧化还原压块为球团,配料技术要求:a球团中全铁含量的确定:铁多渣少;b球团中碳含量的确定:碳低不足无法完成充分还原碳高影响转炉冶炼生产;c球团颗粒级配的要求:颗粒级配合理,增加球团强度;d粘合剂的应用:增加强度,辅助还原;e球团水分的确定:水分过低m影响湿碾,水分过高,增加时长。
46.本发明实施例中,转炉除尘灰氧化还原压块的制备方法,包括以下步骤:步骤一、备料:将转炉除尘粗灰、转炉除尘细灰、高炉灰、钢渣磁选粉、轧钢氧化皮、粘合剂(膨润土)打入罐仓;步骤二、配料:各物料根据配料方案称量后通过皮带输送机送入混料机;各组分的质量份数比如下:转炉除尘粗灰30-50、转炉除尘细灰10-20、高炉灰20-40、磁选粉15-20、轧钢氧化皮20-30、粘合剂(膨润土)5、水3;步骤三、混料:使用混料机对各物料进行搅拌混合,过程控制计量缓续加水搅拌,搅拌均匀后卸料并由皮带输送至中间仓;步骤四、物料中各组分在中间仓中,进入下一道湿碾机,再通过皮带输送机送入压球机;步骤五、压制成型:将制坯料从湿碾机出料后进入入压砖机的冲压系统,压制成型后脱模制得转炉除尘灰压球毛坯;步骤六:转炉除尘灰压块在氧化还原;转炉除尘灰砖毛坯下线后进入氧化还原炉,通过定时定温进行氧化还原,然后转炉除尘灰压块在高温送入转炉炼钢,为转炉炼钢减少能耗。
47.本发明实施例中,一种转炉除尘灰氧化还原压块的应用方法,将转炉除尘灰氧化还原压块后与废钢一同加入转炉进行循环利用的方法,替代部分废钢。
48.包括以下步骤:步骤一:备料:除尘灰氧化还原压块送入废钢间堆放好,视为小型废钢备用,炉次除尘灰氧化还原压块用量,整体控制在废钢和除尘灰氧化还原压块合计重量的40%以下;除尘灰氧化还原压块使用量为:吨钢4~33kg;步骤二:装料:先在废钢斗的中后部、底层装入废钢,再将转炉除尘灰氧化还原压块装入废钢斗剩余空间;步骤三:添加:在转炉兑铁水前,将步骤二装载的废钢及转炉除尘灰氧化还原压块一次性加入转炉。
49.本实施例中,以转炉除尘灰为主要原料的除尘灰氧化还原压块,由以下重量份的原料制成:转炉除尘粗灰、转炉除尘细灰、高炉灰、磁选粉、轧钢氧化皮、粘合剂(膨润土)及水。所用原料成分见下表1.表1实施例1原料成分(wt%)原料caosio2mgoso3al2o3tfeh2o转炉除尘灰6.952.601.330.100.3853.913.50高炉灰7.623.101.460.130.8745.770.67
磁选粉32.7513.8614.01 3.0542.65 轧钢氧化皮
ꢀꢀꢀꢀꢀ
74.69-膨润土
ꢀꢀꢀꢀꢀꢀ
5.76所述转炉除尘灰氧化还原压块的制备方法包括以下步骤:步骤一、将转炉除尘粗灰、转炉除尘细灰、高炉灰、磁选粉、轧钢氧化皮、粘合剂(膨润土)打入罐仓;步骤二、配料:各物料根据配料方案称量后通过皮带输送机送入混料仓再送入混料机混料;各物料的重量份分别为:转炉除尘灰45、转炉除尘细灰15、高炉灰25、磁选粉18%、轧钢氧化皮27%、粘合剂(膨润土)5、水3;步骤三、混料:使用混料机对各物料进行搅拌混合,混合达到1/500标准。过程控制计量缓续加水搅拌,搅拌均匀后卸料并由皮带输送至中间仓;步骤四、物料中各组分在中间仓中,进入下一道湿碾机,再通过皮带输送机送入压球机;步骤五、压制成型:将制坯料从湿碾机出料后进入入压砖机的冲压系统,压制成型后脱模制得转炉除尘灰压球毛坯;步骤六、转炉除尘灰压块在氧化还原:转炉除尘灰砖毛坯下线后进入氧化还原炉,通过定时定温1000-1300℃进行氧化还原,然后转炉除尘灰压块在高温送入转炉炼钢,为转炉炼钢减少能耗。
50.球团氧化还原前后化学成分变化对比表化学成分全铁金属铁氧化亚铁三氧化二铁碳金属化率还原前58.640.5-63.924.40.85还原后73.6018.536.3-025.2经实验检测,球团在1150℃环境下还原20分钟后,全铁含量提升了14.96%;在1250℃环境下还原60分钟后,金属化率提高到25.20%。
51.这种高品质的球团无论在炼铁还是炼钢生产中使用,都是非常受欢迎的优质材料。
52.经过试验结果表明,转炉除尘灰经混料压制成球后,再经过氧化还原处理,压块抗压强度可达3000n以上,全铁品位提高10%以上,产品指标完全达到烧结矿的技术质量标准,满足炼铁、炼钢生产原料需要。
53.已有技术多为配入烧结原料返回烧结转高炉再到炼钢利用,随着技术的发展,不少企业开始采用冷压造球返回炼钢利用。配入烧结原料返回烧结转高炉再到炼钢利用的方法流程长、档次低、能耗大,且增加烧结和高炉操作难度,还易造成烧结故障、影响高炉炉衬寿命;冷压造球返回炼钢利用的方法流程虽然短,但往往需要对除尘灰进行加水消解等预处理、需配加价格较高的粘结剂、还需进行成品烘干等,成本仍然较高;且受除尘灰及配料成分、水份等波动影响对加工工艺、粘结剂选择等有较高要求,球团强度很难保证,容易出现在炼钢配加时堵料仓和入炉后快速熔化、热稳定性差、灰分残留等问题。所以,如何能更简单、有效的实现转炉除尘灰的回收利用,对钢铁企业实现资源循环利用、降低生产成本、增强可持续发展能力,有着十分重要的意义。
再多了解一些
本文用于企业家、创业者技术爱好者查询,结果仅供参考。