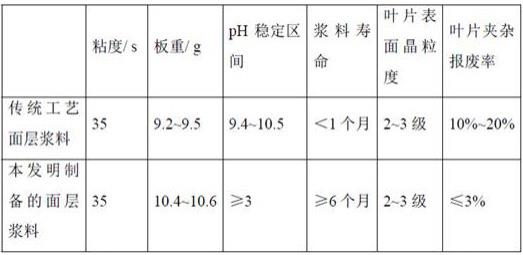
1.本发明涉及航空发动机涡轮叶片精密铸造技术领域,具体涉及适用于机械手自动涂制的长寿命型壳面层浆料制备方法。
背景技术:
2.镍基高温合金承温能力高,具有良好的综合性能,已成为先进航空发动机涡轮叶片首选材料,在军用和民用航空发动机的发展中有十分重要的地位。由于具备复杂的外形结构,精密铸造工艺是涡轮叶片成型的关键,而陶瓷型壳技术又是精密铸造中的核心关键技术。陶瓷型壳的质量直接影响了涡轮叶片的表面质量与尺寸精度,随着不断提高的浇注温度与更为复杂的浇注条件,对陶瓷型壳的性能提出了更为严苛的要求。优秀的陶瓷型壳应满足良好的常温强度、高温强度、透气性、热膨胀性、热震稳定性、热化学稳定性、导热性与溃散性等性能要求。
3.陶瓷型壳是通过逐层涂覆工艺制备而成,面层浆料的要求尤其苛刻。面层浆料的特点:1)良好的涂覆性,完全复制蜡模的细节;2)高温下能够承受金属液冲击;3)不与合金发生明显的化学反应。由于涡轮叶片具有阻尼台、缘板、榫齿等多种结构,面层浆料的涂覆性决定了型壳的质量,最终影响到铸件的质量及合格率。随着精密铸造过程自动化程度的不断提高,机械手自动制壳已成为型壳制备的主要方式。由于自动制壳过程中,不能像手工制壳一样对面层涂制过程进行干预,叶片尖角、凹槽等区域经常出现浆料无法涂覆的情况,进而导致叶片夹杂、毛刺、砂眼、多余金属等缺陷,这对面层浆料的涂挂性能提出了更高的要求。同时由于面层浆料使用频率低,浆料更新相对较慢,浆料的寿命也影响到工艺过程的稳定性及叶片成本。因此,开发一种具有良好涂挂性及长寿命的型壳面层浆料,以满足机械手自动制壳的涂制要求,对提高精密铸造过程稳定性及降低叶片研制成本意义重大。
技术实现要素:
4.针对现有技术的缺陷,本发明的目的是提供适用于机械手自动涂制的长寿命型壳面层浆料制备方法。
5.本发明解决技术问题采用如下技术方案:本发明提供了适用于机械手自动涂制的长寿命型壳面层浆料制备方法,包括以下步骤:步骤一、陶瓷粉料准备:1)选取粒度d50在15~25μm的锆英粉,粒度d50在5~10μm的铝酸钴粉为面层粉料,粉料比例为锆英粉:铝酸钴粉=6~9:1;2)按比例称取合适数量的锆英粉及铝酸钴粉,放入v型混料机中充分混合,混料机转速为8~15r/min,混合时间2h;步骤二、粘结剂及有机助剂混合溶液准备:1)选取粘结剂、有机助剂;其中有机助剂为:渗透剂、消泡剂、加强剂、成膜剂;
2)按粘结剂的体积量分别取0.3%~0.9%的渗透剂及消泡剂加入粘结剂中,再按粘结剂重量称取2%~5%的加强剂及成膜剂加入粘结剂中,配制成混合溶液,开启搅拌机搅拌5~10min,得到混合溶液,待用;步骤三、面层浆料制备:1)按粉液比为3~5:1的比例称取陶瓷粉体及混合溶液,边搅拌边将陶瓷粉体缓慢加入到混合溶液中,在搅拌机中搅拌2~6h,转速为900~1500r/min,搅拌过程中采用冷却水控制配料桶温度,温度控制范围为21~25℃;2)用隔膜泵将配制好的浆料转移至l型搅拌桶中,继续搅拌48h~72h;3)采用规格为6mm
×
100ml的流杯粘度计及150
×
150mm的钢板测试浆料的粘度及板重,浆料粘度调节至30~35s,板重调节至9.5~11.0g,面层浆料制备完成。
6.优选地,所述锆英粉中的成分,杂质元素;铝酸钴中的成分:39%~42%。
7.优选地,所述粘结剂为硅溶胶,硅溶胶的ph值为3~5。
8.优选地,所述硅溶胶加入0.1~0.5%铝离子进行改性,含量为29~31%,粒径为10~20nm。
9.优选地,所述渗透剂为t型渗透剂或v12型润湿剂。
10.优选地,消泡剂为正辛醇或burst100。
11.优选地,加强剂为聚合物polymer。
12.优选地,成膜剂为海藻酸铵。
13.与现有技术相比,本发明具有如下的有益效果:本发明提供了一种适用于机械手自动涂制的长寿命型壳面层浆料制备方法,该方法以锆英粉、铝酸钴粉为陶瓷材料,以al离子改性硅溶胶为粘结剂,并添加适量有机助剂组成混合溶液,通过快速搅拌、l型搅拌机稳定搅拌、浆料调节等工艺步骤所制得的型壳面层浆料,由于进行了陶瓷粉体粒度级配,以及添加了适量的有机助剂(润湿剂、消泡剂、加强剂、成膜剂等),特别是创新性的引入了成膜剂,使其具有极佳的流动性及涂覆性;同时,由于采用的硅溶胶进行了al离子改性,是一种宽ph值稳定的硅溶胶,与陶瓷粉体具有良好的亲和性,在ph值大于3的环境中能够长期稳定,不会发生胶凝现象,因此浆料寿命能够达到6个月甚至更长时间。本发明方法所制备的型壳面层浆料,用于涡轮叶片型壳机械手自动涂制,很好的解决了一般面层浆料出现的堆料、露蜡、气泡等涂制问题,以及使用寿命不足一个月的寿命短问题,满足航空发动机涡轮叶片机械手自动涂制的使用要求。
具体实施方式
14.下面结合具体实施例,对本发明实施例中的技术方案进行清楚、完整地描述,显然,所描述的实施例仅仅是本发明一部分实施例,而不是全部的实施例。基于本发明中的实施例,本领域普通技术人员在没有做出创造性劳动前提下所获得的所有其他实施例,都属于本发明保护的范围。
15.本发明实施例适用于机械手自动涂制的长寿命型壳面层浆料制备方法,包括以下步骤:
步骤一、陶瓷粉料准备:1)选取粒度d50在15~25μm的锆英粉,粒度d50在5~10μm的铝酸钴粉为面层粉料,粉料比例为锆英粉:铝酸钴粉=6~9:1;2)按比例称取合适数量的锆英粉及铝酸钴粉,放入v型混料机中充分混合,混料机转速为8~15r/min,混合时间2h;步骤二、粘结剂及有机助剂混合溶液准备:1)选取粘结剂、有机助剂;其中有机助剂为:渗透剂、消泡剂、加强剂、成膜剂;2)按粘结剂的体积量分别取0.3%~0.9%的渗透剂及消泡剂加入粘结剂中,再按粘结剂重量称取2%~5%的加强剂及成膜剂加入粘结剂中,配制成混合溶液,开启搅拌机搅拌5~10min,得到混合溶液,待用;步骤三、面层浆料制备:1)按粉液比为3~5:1的比例称取陶瓷粉体及混合溶液,边搅拌边将陶瓷粉体缓慢加入到混合溶液中,在搅拌机中搅拌2~6h,转速为900~1500r/min,搅拌过程中采用冷却水控制配料桶温度,温度控制范围为21~25℃;2)用隔膜泵将配制好的浆料转移至l型搅拌桶中,继续搅拌48h~72h;3)采用规格为6mm
×
100ml的流杯粘度计及150
×
150mm的钢板测试浆料的粘度及板重,浆料粘度调节至30~35s,板重调节至9.5~11g,面层浆料制备完成。
16.本实施例的锆英粉中的成分,杂质元素;铝酸钴中的成分:39%~42%。
17.本实施例的粘结剂为硅溶胶,硅溶胶的ph值为3~5。
18.本实施例的硅溶胶加入0.1~0.5%铝离子进行改性,含量为29~31%,粒径为10~20nm。
19.本实施例的渗透剂为t型渗透剂或v12型润湿剂;消泡剂为正辛醇或burst100;加强剂为聚合物polymer;成膜剂为海藻酸铵。
20.实施例1.制备适用于机械手自动涂制的长寿命型壳面层浆料,工艺过程及步骤如下:步骤一、陶瓷粉料准备:1)选取粒度d50在15μm的锆英粉,粒度d50在5μm的铝酸钴粉为面层粉料,粉料比例为锆英粉:铝酸钴粉=8:1;2)按比例称取合适数量的锆英粉及铝酸钴粉,放入v型混料机中充分混合。混料机转速为8r/min,混合时间2h;步骤二、粘结剂及有机助剂混合溶液准备:1)选取的粘结剂为硅溶胶,ph值3,%含量为29%;有机助剂为:t型渗透剂或v12型润湿剂、消泡剂正辛醇或burst100、加强剂polymer、成膜剂海藻酸铵;2)按硅溶胶的体积量分别取0.5%的渗透剂及消泡剂加入硅溶胶中,再按硅溶胶重量称取2.5%的加强剂及成膜剂加入硅溶胶中,配制成混合溶液,开启搅拌机搅拌5min,待用;
步骤三、面层浆料制备1)按粉液比为4:1的比例称取陶瓷粉体及混合溶液,边搅拌边将陶瓷粉体缓慢加入到混合溶液中,在搅拌机中搅拌2h,转速为900r/min,搅拌过程中采用冷却水控制配料桶温度,温度控制范围为21℃;2)用隔膜泵将配制好的浆料转移至l型搅拌桶中,继续搅拌48h;3)采用规格为φ6mm
×
100ml的流杯粘度计及150
×
150mm的钢板测试浆料的粘度及板重,浆料粘度调节至30s,板重调节至9.5g,面层浆料制备完成。
21.实施例2.制备适用于机械手自动涂制的长寿命型壳面层浆料,工艺过程及步骤如下:步骤一、陶瓷粉料准备:1)选取粒度d50在25μm的锆英粉,粒度d50在10μm的铝酸钴粉为面层粉料,粉料比例为锆英粉:铝酸钴粉=8:1;2)按比例称取合适数量的锆英粉及铝酸钴粉,放入v型混料机中充分混合。混料机转速为15r/min,混合时间2h;步骤二、粘结剂及有机助剂混合溶液准备:1)选取的粘结剂为硅溶胶,ph值5,%含量为31%;有机助剂为:t型渗透剂或v12型润湿剂、消泡剂正辛醇或burst100、加强剂polymer、成膜剂海藻酸铵;2)按硅溶胶的体积量分别取0.5%的渗透剂及消泡剂加入硅溶胶中,再按硅溶胶重量称取2.5%的加强剂及成膜剂加入硅溶胶中,配制成混合溶液,开启搅拌机搅拌10min,待用;步骤三、面层浆料制备1)按粉液比为4:1的比例称取陶瓷粉体及混合溶液,边搅拌边将陶瓷粉体缓慢加入到混合溶液中,在搅拌机中搅拌6h,转速为1500r/min,搅拌过程中采用冷却水控制配料桶温度,温度控制范围为25℃;2)用隔膜泵将配制好的浆料转移至l型搅拌桶中,继续搅拌72h;3)采用规格为6mm
×
100ml的流杯粘度计及150
×
150mm的钢板测试浆料的粘度及板重,浆料粘度调节至35s,板重调节至11.0g,面层浆料制备完成。
22.实施例3.制备适用于机械手自动涂制的长寿命型壳面层浆料,工艺过程及步骤如下:步骤一、陶瓷粉料准备:1)选取粒度d50在20μm的锆英粉,粒度d50在7.5μm的铝酸钴粉为面层粉料,粉料比例为锆英粉:铝酸钴粉=8:1;2)按比例称取合适数量的锆英粉及铝酸钴粉,放入v型混料机中充分混合。混料机转速为12.5r/min,混合时间2h;步骤二、粘结剂及有机助剂混合溶液准备:1)选取的粘结剂为硅溶胶,ph值4,%含量为30%;有机助剂为:t型渗透剂或v12型润湿剂、消泡剂正辛醇或burst100、加强剂polymer、成膜剂海藻酸铵;2)按硅溶胶的体积量分别取0.5%的渗透剂及消泡剂加入硅溶胶中,再按硅溶胶重
量称取2.5%的加强剂及成膜剂加入硅溶胶中,配制成混合溶液,开启搅拌机搅拌7.5min,待用;步骤三、面层浆料制备1)按粉液比为4:1的比例称取陶瓷粉体及混合溶液,边搅拌边将陶瓷粉体缓慢加入到混合溶液中,在搅拌机中搅拌4h,转速为1150r/min,搅拌过程中采用冷却水控制配料桶温度,温度控制范围为23℃;2)用隔膜泵将配制好的浆料转移至l型搅拌桶中,继续搅拌56h;3)采用规格为6mm
×
100ml的流杯粘度计及150
×
150mm的钢板测试浆料的粘度及板重,浆料粘度调节至32.5s,板重调节至10.5g,面层浆料制备完成。
23.采用本发明制备的面层浆料与采用未改性、不添加聚合物的碱性硅溶胶配制的传统面层浆料对比见表1。
24.表1 本发明实施例3制备面层浆料与传统浆料性能对比(相同粘度)表1对于本领域技术人员而言,显然本发明不限于上述示范性实施例的细节,而且在不背离本发明的精神或基本特征的情况下,能够以其他的具体形式实现本发明。因此,无论从哪一点来看,均应将实施例看作是示范性的,而且是非限制性的,本发明的范围由所附权利要求而不是上述说明限定,因此旨在将落在权利要求的等同要件的含义和范围内的所有变化囊括在本发明内。
25.此外,应当理解,虽然本说明书按照实施方式加以描述,但并非每个实施方式仅包含一个独立的技术方案,说明书的这种叙述方式仅仅是为清楚起见,本领域技术人员应当将说明书作为一个整体,各实施例中的技术方案也可以经适当组合,形成本领域技术人员可以理解的其他实施方式。
再多了解一些
本文用于企业家、创业者技术爱好者查询,结果仅供参考。