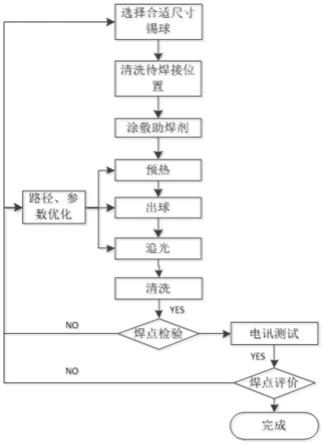
1.本发明涉及电子装联技术领域,具体涉及一种狭小深腔内焊点的激光喷锡焊接方法。
背景技术:
2.相控阵雷达是目前应用比较广泛的一种雷达体制。随着系统设计朝向体积小型化,结构复杂化,功能集成化方向发展,对雷达的体积和重量提出了极高的要求。天线单元作为相控阵雷达的核心部件,为了提高系统集成,大量使用射频连接器实现电气互联。这是由于射频连接器具有体积小、重量轻、射频性能优越、损耗低等优点。
3.射频连接器与微带电路的互联一般采用手工烙铁方式焊接实现,但对于狭小深腔结构,手工焊接无法操作,或者操作困难,很难形成有效焊点。此外,对于工作频段在ku、ka或更高频段的系统来说,不仅对射频连接器的焊接质量提出了要求,甚至对其焊点形貌也提出了需求。因此,急需寻找一种焊接工艺解决现有手工焊接难操作,焊点成品率低,一致性差等问题。
4.鉴于上述缺陷,本发明创作者经过长时间的研究和实践终于获得了本发明。
技术实现要素:
5.本发明的目的在于解决射频连接器与微带电路的现有焊接方式难操作,焊点成品率低,一致性差的问题,提供了一种狭小深腔内焊点的激光喷锡焊接方法。
6.为了实现上述目的,本发明公开了一种狭小深腔内焊点的激光喷锡焊接方法,所述狭小深腔为金工件,微带板和射频连接器所形成的的凹槽,所述焊点为射频连接器内导体与微带焊盘的互联;
7.激光喷锡焊接方法包括以下步骤:
8.s1:选择合适尺寸锡球:根据焊点形成所需焊料体积选择锡球直径;
9.s2:清洗待焊接位置;
10.s3:涂敷助焊剂:采用助焊剂装置在射频连接器内导体与微带板焊盘处自动喷涂或刷涂焊剂;
11.s4:激光预热:采用激光加热待焊接位置进行预热,激光器能量输出5%~20%,设备总功率为150w,时间为1~10s,光斑直径为1.5~3mm;
12.s5:出球:锡球从供球系统滑出至喷嘴位置,激光加热锡球,熔融的锡球喷射实现射频连接器内导体与微带板焊盘互联;
13.s6:追光:进行1~2次追光,用于锡球滴落时待焊接位置加热,或用于降低锡球滴落后待焊接位置冷却速率,防止缩孔等缺陷;
14.s7:清洗焊点。
15.所述金工件为铝合金或者铝硅合金,所述微带板螺装、胶接或焊接于所述金工件上,所述射频连接器外导体螺装、胶接或焊接于所述金工件上,所述焊点为射频连接器内导
体与微带焊盘的互联。
16.所述射频连接器内导体镀金处理,所述微带板焊盘表面镀金或热风整平锡铅处理。
17.所述步骤s1锡球直径为0.1~1.8mm,锡球材料为snagcu或snpb。
18.所述连接器内导体直径为d,长度为l,有效焊接长度l0,所述焊盘宽度为w,长度为l,连接器内导体距焊盘高度h,有效焊接高度h0≈h d。锡球体积v
锡球
≈所需焊料体积v
焊料
,其中从而计算出所需锡球直径。
19.所述步骤s2中采用人工或设备清洗待焊接部位,所述设备清洗为超声清洗、等离子清洗、水清洗中的任意一种。
20.所述步骤s5中激光器能量输出为25%~70%,时间为50~100ms,光斑直径为0.5~2mm。
21.所述步骤s6中追光时激光器能量输出为5%~25%,时间为0.1~5s,光斑直径为1.5~3mm。
22.所述步骤s7中采用人工或水清洗设备清洗焊点。
23.所述激光焊接过程在氮气或氩气氛围内实施。
24.用显微镜观察焊点形态,根据焊料铺展面积和润湿角调整所用锡球直径,焊料铺展不足,选择直径大的锡球;润湿角过大(》90
°
),选择直径小的锡球。根据焊点质量调整追光次数进行工艺路径优化和工艺参数优化。进行电性能测试,根据测试结果进一步调整锡球直径,并进行工艺路径和工艺参数优化。
25.所述焊点焊料铺展均匀连续,润湿角小于30
°
~50
°
。经检测发现,在连接器内导体侧和微带板焊盘侧均形成了均匀连续的金属间化合物,焊接质量合格。电性能测试驻波比小于2.5,满足指标要求。
26.与现有技术比较本发明的有益效果在于:
27.1、本发明的一种狭小深腔内焊点的激光喷锡焊接方法,采用激光喷锡焊接方法,通过选择合适锡球尺寸,优化工艺路径,合理设置工艺参数,实现狭小深腔内焊点的可靠性互联。本发明采用激光喷锡焊接工艺,非接触且精准定位,解决了手工焊接无法实现或操作困难问题。通过优化工艺路径和合理设置参数,实现自动化焊接,提升了焊接效率。通过定量锡球施加,可获得较为稳定的焊点形貌,电性能一致性好。
28.2、本发明提供一种狭小深腔内焊点的激光喷锡焊接方法,通过调整追光次数和工艺参数获得合格焊点,成功解决了电讯结构设计所决定的焊接操作空间有限,手工操作无法实现或操作困难,焊点成品率低、一致性差等问题。
29.3、本发明提供的一种狭小空间内焊点的激光喷锡焊接方法,制备所得的电性件经过严苛的环境试验(200次温度循环(-55℃~100℃)和随机振动(x、y、z三个方向,加速度均方根值13.88grms))考核,电性能指标仍满足产品要求。
附图说明
30.图1为实施例1、2的焊接结构示意图;
31.图2为实施例1、2的焊接结构剖面图;
32.图3为实施例1~4的射频连接器示意图;
33.图4为焊料简化模型示意图;
34.图5为激光喷锡焊接工艺优化示意图;
35.图6为实施例3、4的焊接结构示意图;
36.图7为实施例3、4的焊接结构剖面图。
37.图中数字表示:
38.1-金工件;11-金工件腔体;12-金工件凸台;2-微带板;21-微带板焊盘;22-隔离孔;23-微带板开槽;3-射频连接器;31-外导体;32-内导体。
具体实施方式
39.以下结合附图,对本发明上述的和另外的技术特征和优点作更详细的说明。
40.实施例1
41.如图1~2所示,为本实施例的焊接结构图。金工件1为铝硅合金,微带板2为多层结构且焊接区域开槽,射频连接器3包括外导体31和内导体32(图3),微带板2与射频连接器外导体31均焊接在金工件1上,射频连接器内导体32搭接在微带板2焊盘21上,采用激光喷锡焊接工艺实现电气互联。微带板焊盘21两侧0.28mm处有隔离孔22设计,焊接时不允许短路。射频连接器3表面和多层微带板2焊盘镀金处理。
42.金工件腔体11尺寸5mm
×
4.5mm
×
2.35mm,微带板开槽23区域宽度2mm,深度3mm,其余深度2.35mm。射频连接器内导体32直径d=0.38mm,长度l=1.2mm,微带板焊盘21长l
×
宽w=2mm
×
1mm。
43.一种狭小深腔内焊点的激光喷锡焊接工艺操作步骤如下:
44.步骤(1)锡球直径d根据焊点形成所需焊料体积v焊料选择,焊料简化模型如图4所示。锡球体积v
锡球
≈v
焊料
,其中,其中连接器内导体有效焊接长度l0=1.0mm,连接器内导体距焊盘高度h取平均值为0.15mm,有效焊接高度h0≈0.53mm,计算所得d=0.86mm。根据厂家现有锡球,选取锡球直径0.89mm。锡球材料为63sn/37pb。
45.步骤(2)采用无纺布或棉球蘸取酒精或异丙醇清洗待焊接部位;
46.步骤(3)助焊剂装置在连接器内导体和微带板焊盘处自动刷涂助焊剂,助焊剂类型rma型,毛刷直径2mm,刷涂时间0.4s;
47.步骤(4)焊接系统移至待焊接位置上方,激光预热,激光器能量输出9%(设备总功率150w),时间2.5s,光斑直径2mm。
48.步骤(5)锡球从供球系统滑至喷嘴位置,激光加热锡球,焊料熔化喷射形成焊点。激光器能量输出37%,时间75ms,光斑直径1mm。
49.步骤(6)追光,一次追光激光器能量输出14%,时间650ms,光斑直径1.5mm,二次追光激光器能量输出12%,时间700ms,光斑直径1.5mm。
50.步骤(7)采用水清洗设备清洗焊点。
51.激光焊接过程在氮气氛围内实施。
52.激光喷锡焊接工艺优化示意图如图5所示。采用上述焊接工艺,可实现非接触、局部受热、精准定位、高效率焊接。与传统手工焊接相比,焊点润湿角呈锐角小于30
°
~50
°
,而手工焊锡量不好控,润湿角接近90
°
,焊点形态一致性差。与传统手工焊接相比,20单元阵列天线焊点操作周期可缩短50%以上,。采用扫描电镜观察发现,焊接部位形成了均匀连续的金属间化合物,厚度在0.5~3μm之间,焊接质量合格。电性能测试驻波比均小于2.5,一致性较好,满足设计要求。经环境试验(200次温度循环(-55℃~100℃)和随机振动(x、y、z三个方向,加速度均方根值13.88grms))考核后,电性能测试驻波比仍小于2.5,满足产品使用要求。
53.实施例2
54.与实施例1相同,如图1~2所示,为本实施例的焊接结构图。
55.步骤(1)选取锡球直径0.89mm,锡球材料为sn96.5ag3cu0.5。
56.步骤(2)、(3)、(4)同实施例1。
57.步骤(5)锡球从供球系统滑至喷嘴位置,激光加热锡球,焊料熔化喷射形成焊点。激光器能量输出45%,时间70ms,光斑直径1.1mm。
58.步骤(6)追光,一次追光激光器能量输出20%,时间620ms,光斑直径1.5mm,二次追光激光器能量输出16%,时间750ms,光斑直径1.5mm。
59.步骤(7)采用水清洗设备清洗焊点。
60.激光焊接过程在氮气氛围内实施。
61.本实施例可获得同实施例1相同的焊接质量和电测结果。
62.实施例3
63.如图6~7所示,为实施例3的焊接结构图。金工件1为铝硅合金,微带板2为多层结构且焊接区域开槽,射频连接器3包括外导体31和内导体32,微带板2、微带板2与射频连接器外导体31均焊接在金工件1上,射频连接器内导体32搭接在微带板2焊盘21上,采用激光喷锡焊接工艺实现电气互联。微带板焊盘21两侧0.28mm处有隔离孔22设计,焊接时不允许短路。射频连接器3表面和多层微带板2焊盘镀金处理。
64.金工件凸台12与微带板距离4.26mm,微带板开槽23区域宽度
×
深度=4.6mm
×
2mm,开槽区域与金工件台阶13距离1.28mm。射频连接器内导体32直径d=0.38mm,长度l=1.2mm,微带板焊盘21长l
×
宽w=2mm
×
1mm。
65.一种狭小深腔内焊点的激光喷锡焊接工艺操作步骤如下:
66.步骤(1)、(2)同实施例1。
67.步骤(3)助焊剂装置在连接器内导体和微带板焊盘处自动刷涂助焊剂,助焊剂类型rma型,毛刷直径2mm,刷涂时间0.3s。
68.步骤(4)焊接系统移至待焊接位置上当,激光预热,激光器能量输出8%(设备总功率150w),时间2.5s,光斑直径2mm。
69.步骤(5)锡球从供球系统滑至喷嘴位置,激光加热锡球,焊料熔化喷射形成焊点。激光器能量输出32%,时间72ms,光斑直径1mm。
70.步骤(6)追光,激光器能量输出14%,时间650ms,光斑直径1.5mm。
71.步骤(7)同实施例1。
72.激光焊接过程在氮气氛围内实施。
73.该结构形式内的焊点,必须采用细的烙铁头才能施焊,且需倾斜一定角度才可获得合格焊点,对工人水平要求极高,但仍存在润湿角偏大、操作一致性差等问题。采用上述激光喷锡焊接工艺,润湿角得到明显改善,焊点形态一致性好,20单元阵列天线焊点操作周期可缩短50%以上。采用扫描电镜观察发现,焊接部位形成了均匀连续的金属间化合物,厚度在0.5~3μm之间,焊接质量合格。电性能测试比均小于2.0,一致性较好,满足设计要求。经环境试验(200次温度循环(-55℃~100℃)和随机振动(x、y、z三个方向,加速度均方根值13.88grms))考核后,电性能测试驻波比仍小于2.0,满足产品使用要求。
74.实施例4
75.与实施例3相同,如图6~7所示,为本实施例的焊接结构图。
76.一种狭小深腔内焊点的激光喷锡焊接工艺操作步骤如下:
77.步骤(1)连接器内导体有效焊接长度l0=1.0mm,连接器内导体距焊盘高度h取平均值为0.1mm,有效焊接高度h0≈0.48mm,计算所得d=0.82mm。根据厂家现有锡球,选取锡球直径0.89mm。锡球材料为63sn/37pb。
78.步骤(2)~(7)同实施例3。
79.根据焊点质量和电性能测试调整锡球直径0.76mm。调整步骤(5)激光器能量输出30%,时间70ms,光斑直径1mm。其余参数同实施例3。
80.本实施例可获得同实施例3相同的焊接质量和电测结果。
81.以上所述仅为本发明的较佳实施例,对本发明而言仅仅是说明性的,而非限制性的。本专业技术人员理解,在本发明权利要求所限定的精神和范围内可对其进行许多改变,修改,甚至等效,但都将落入本发明的保护范围内。
再多了解一些
本文用于企业家、创业者技术爱好者查询,结果仅供参考。