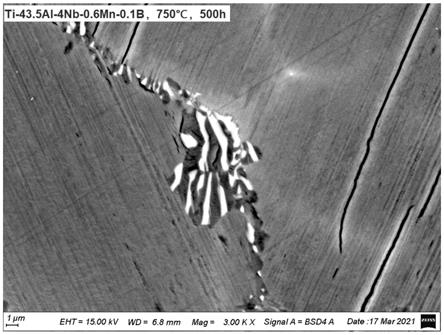
一种可抑制有序
ω
相生成的tial合金及其制备方法
技术领域
1.本发明属于tial金属间化合物材料技术领域,涉及一种可抑制有序ω相生成的tial合金,也可称之为高温γ
‑
tial基合金。
背景技术:
2.轻质高强的tial合金作为用于先进航空发动机减重的高温结构材料,具有高熔点、低密度、良好的力学性能等特点,近年来表现出巨大的市场前景。随着航空航天工业的快速发展,航空航天飞行器对其发动机的要求越来越严格。涡轮叶片是航空发动机的核心零部件,一直处于高温、高压、高速的工作环境中,承受着离心力、气动力、温度应力等循环交变载荷作用,服役环境非常恶劣。这就要求使用的高温结构材料具备耐高温,高的比强度和比刚度等性能特点,以满足先进动力装置和新型飞行器研制的需要。
3.航空发动机用tial合金的应用温度目前仍在650℃~750℃范围内,但是tial合金仍然具有应用于更高温度甚至900℃的潜力。tnm(ti
‑
43.5al
‑
4nb
‑
1mo
‑
0.1b)合金的应用是变形tial合金的巨大成功。在热加工温度区间内,由于β相的含量比较高使得tnm合金热加工性能良好,而后续的热处理又可以将脆性的室温β0相(也称b2相)含量控制在较低水平以保证塑性。由于添加了多种β相稳定元素来提升合金的高温变形能力,合金的凝固初生相为β相,室温以β0相和γ相为主,另外还有少量α2相。
4.但是,tnm合金在实际应用中也出现了一些亟待解决的问题。目前开发的多种不同成分的tial合金中,合金凝固及热加工后显微组织通常处于热力学非平衡状态,在期望服役温度(650~850℃)区间内显微组织将缓慢向平衡态演变。tnm合金是目前国际上唯一一种可以在750℃工作的tial合金,并且从2017年起,该合金被用于制造普惠公司的gtf发动机pw1100g系列的末级(第三级)低压涡轮叶片。但tnm合金叶片在服役6个月到一年后出现多次空中叶片失效事故,其中一个主要原因是该合金在服役温度下ω相的析出,造成材料脆化严重,从而导致空中叶片失效。普惠公司正在根据faa的适航指令(ad
‑
2019
‑
25
‑
01和ad
‑
2020
‑
08
‑
04)分批将tnm叶片替换下来。由此可见,tnm合金的研究和应用尚不成熟。主要表现为过饱和α2相的溶解以及有序ω相和正交相的析出,同时,由于β0相的不稳定性,有序ω相非常容易自β0相的内部产生。目前,还没有单相有序ω相合金力学性能的研究,但是硬度测试的结果表明有序ω相的硬度约为11.2gpa,明显高于α2相和γ相,为硬脆相。多项研究表明有序ω相的存在会对tial的高温性能产生不利影响,故一般认为其是有害相。tial合金中有序ω相的存在会严重影响tial合金的显微组织稳定性,从而降低了tial合金的长时服役性能,是目前tial合金亟待研究解决的问题之一。
技术实现要素:
5.本发明的目的在于解决传统tnm合金(ti
‑
43.5al
‑
4nb
‑
1mo
‑
0.1b)中由于存在有序ω相而导致高温性能不佳的问题,而提供一种可抑制有序ω相生成的tial合金及其制备方法。该tial合金通过添加一定量的mn元素成功抑制了有序ω相生成。
6.为实现上述目的,本发明所提供的技术解决方案是:
7.一种可抑制有序ω相生成的tial合金,其特殊之处在于:按原子百分含量含有43%
‑
45%al、4%nb、0.6%
‑
1%mn、0.1%b,余量为ti和不可避免的杂质。所述tial合金的钼当量为2~3;
8.所述钼当量的公式为:
9.[mo]=mo% nb%/3.3 mn%/0.6 ta%/4 w%/2 cr%/0.6 co%/0.9 v%/1.4 fe%/0.5 ni%/0.8。
[0010]
进一步地,所述tial合金中含有α2相、β0相以及γ相,不包含ω相。
[0011]
进一步地,所述mn的原子百分含量为0.6%
[0012]
进一步地,原子百分含量为:43.5%al、4%nb、0.6%mn、0.1%b,余量为ti和不可避免的杂质。
[0013]
进一步地,所述不可避免的杂质为h、o、n。
[0014]
同时,本发明还提供了以下两种上述可抑制有序ω相生成的tial合金的制备方法。
[0015]
第一种方法为:
[0016]
1)配料
[0017]
按照所述原子百分含量称取零级海绵钛、纯铝、nb
‑
al中间合金、纯锰、纯硼,并混合均匀;
[0018]
2)熔炼
[0019]
对步骤1)混合均匀的原材料进行熔炼,得到合金铸锭。
[0020]
进一步地,步骤2)中,采用电弧熔炼法对步骤1)混合均匀的原材料进行熔炼,得到合金铸锭。即将步骤1)得到的混合试样置于真空非自耗电弧熔炼炉的坩埚内进行熔炼,熔炼多次,从第二次起每次熔炼都需要将铸锭翻面以保证铸锭的均匀性,熔炼真空度低于0.1pa,熔炼电流控制在适当范围内(比如:0.2ka~0.3ka)。该方法适用于小规模制备合金。
[0021]
第二种方法为:
[0022]
1)配料
[0023]
按照所述原子百分含量称取零级海绵钛、纯铝、nb
‑
al中间合金、纯锰、纯硼,并混合均匀;
[0024]
2)电极制备
[0025]
将步骤1)混合均匀的原材料压制成多个电极焊棒,并将多个电极焊棒接成一次熔炼用电极;
[0026]
3)熔炼
[0027]
对步骤2)得到的电极进行多次(2
‑
3次即可)熔炼,获得成分均匀的铸棒。
[0028]
进一步地,步骤2)中,通过炉内等离子氩弧焊将多个电极焊棒接成一次熔炼用电极。
[0029]
进一步地,步骤3)中,采用真空自耗或者真空自耗和真空凝壳炉结合的方法制得成分均匀的铸棒。本发明适用与大规模工业制备合金。
[0030]
上述原料的规格为,纯铝99.999%,纯锰99.8%,纯硼99.9%,nbal中间合金质量百分百:nb为72.63%,al为27.19%。
[0031]
与现有技术相比,本发明具有的优点和有益效果为:
[0032]
1.本发明通过在tial合金中加入一定量对有序ω相生成有抑制效果的合金元素mn,提高高温γ
‑
tial合金在高温下的组织稳定性,成功抑制住了β0相中有序ω相的析出,制备出了可抑制有序ω相生成的tial合金,解决了传统tnm合金(ti
‑
43.5al
‑
4nb
‑
1mo
‑
0.1b)中由于存在有序ω相而导致高温性能不佳的问题。
[0033]
2.tial合金的性能对成分与组织构成非常敏感,首先,本发明成分中加入的nb是β相稳定元素,可以获得具有较好变形能力的β0相和γ相,但是同时也促进了有序ω相的析出,而一般认为有序ω相是有害相;其次,本发明中加入的mn元素对有序ω相的析出具有抑制作用,通过合理调控mn元素的含量达到了抑制β0相中有序ω相析出的预期效果,mn元素的加入降低了tial合金中有序ω相的析出温度,使得ω相在750℃左右的服役温度内不会析出;最后,通过本发明预定成分制备出的tial合金经过高温长时保温后β0相中不存在脆性的有序ω相,为解决传统tnm合金中由于存在有序ω相而导致高温性能不佳的问题提供了解决思路。
[0034]
3.严格执行本发明的工艺过程,制备出的铸锭金相组织结构稳定性好,且本发明工艺简单,很容易在实际生产中得到应用。
附图说明
[0035]
图1为实施例1中tial合金ti
‑
43.5al
‑
4nb
‑
0.6mn
‑
0.1b经过750℃保温500h热处理后放大3000倍的sem组织形貌;
[0036]
图2为实施例1中tial合金ti
‑
43.5al
‑
4nb
‑
0.6mn
‑
0.1b经过750℃保温500h热处理后放大8000倍的sem组织形貌;
[0037]
图3为实施例1中tial合金ti
‑
43.5al
‑
4nb
‑
0.6mn
‑
0.1b经过750℃保温1000h热处理后放大3000倍的sem组织形貌;
[0038]
图4为实施例1中tial合金ti
‑
43.5al
‑
4nb
‑
0.6mn
‑
0.1b经过750℃保温1000h热处理后放大8000倍的sem组织形貌;
[0039]
图5为实施例1中tial合金ti
‑
43.5al
‑
4nb
‑
0.8mn
‑
0.1b经过750℃保温500h热处理后放大8000倍的sem组织形貌;
[0040]
图6为实施例1中tial合金ti
‑
43.5al
‑
4nb
‑
1mn
‑
0.1b经过750℃保温500h热处理后放大8000倍的sem组织形貌;
[0041]
图7为实施例1中tial合金ti
‑
44.5al
‑
4nb
‑
0.6mn
‑
0.1b经过750℃保温1000h热处理后放大8000倍的sem组织形貌;
具体实施方式
[0042]
以下结合附图和具体实施例对本发明的内容作进一步的详细描述:
[0043]
实施例1
[0044]
本实施例是一种可抑制有序ω相生成的tial合金原子百分比为:ti
‑
43.5al
‑
4nb
‑
0.6mn
‑
0.1b,余量为ti;tial合金的制备通过以下步骤实现:
[0045]
步骤1)配料
[0046]
将零级海绵钛、a00级高纯铝、nb
‑
al中间合金、高纯锰、高纯硼按照成分配比
51.8at%ti、43.5at.%al、4at.%nb、0.6at.%mn、0.1at.%b配制成重量约为40g的试样并混合均匀;
[0047]
步骤2)熔炼铸锭
[0048]
将步骤1)中的试样置于真空非自耗电弧熔炼炉的坩埚内进行熔炼,熔炼五次,从第二次起每次熔炼都需要将铸锭翻面以保证铸锭的均匀性,熔炼真空度低于0.1pa,熔炼电流控制在适当范围内,五次熔炼后获得重量约为40g,直径400mm~500mm的纽扣铸锭;
[0049]
步骤3)线切割
[0050]
将步骤2)中的tial合金纽扣铸锭使用线切割机均分为四块试样;
[0051]
步骤4)热处理
[0052]
电阻炉加热至750℃,取步骤3)的四块试样中的任意两块放入炉中,分别恒温保温500小时和1000小时后,取出试样用水淬火;
[0053]
步骤5)打磨金相,至样品表面呈镜面且无划痕
[0054]
利用扫描电子显微镜(sem)在背散射电子条件下观察发现,参见图1
‑
图4;ti
‑
43.5al
‑
4nb
‑
0.6mn
‑
0.1b合金中主要含有α2相、β0相以及γ相,放大至8000倍并未在β0相中发现有序ω相。
[0055]
实施例2
[0056]
本实施例是一种可抑制有序ω相生成的tial合金原子百分比为:ti
‑
43.5al
‑
4nb
‑
0.8mn
‑
0.1b,余量为ti;tial合金的制备通过以下步骤实现:
[0057]
步骤1)配料
[0058]
将零级海绵钛、a00级高纯铝、nb
‑
al中间合金、高纯锰、高纯硼按照成分配比51.6at%ti、43.5at.%al、4at.%nb、0.8at.%mn、0.1at.%b配制成重量约为40g的试样并混合均匀;
[0059]
步骤2)熔炼铸锭
[0060]
将步骤1)中的试样置于真空非自耗电弧熔炼炉的坩埚内进行熔炼,熔炼五次,从第二次起每次熔炼都需要将铸锭翻面以保证铸锭的均匀性,熔炼真空度低于0.1pa,熔炼电流控制在适当范围内,五次熔炼后获得重量约为40g,直径400mm~500mm的纽扣铸锭;
[0061]
步骤3)线切割
[0062]
将步骤2)中的tial合金纽扣铸锭使用线切割机均分为四块试样;
[0063]
步骤4)热处理
[0064]
电阻炉加热至750℃,取步骤3)的四块试样中的任意两块放入炉中,分别恒温保温500小时和1000小时后,取出试样用水淬火;
[0065]
步骤5)打磨金相,至样品表面呈镜面且无划痕
[0066]
利用扫描电子显微镜(sem)在背散射电子条件下观察发现,ti
‑
43.5al
‑
4nb
‑
0.8mn
‑
0.1b合金中主要含有α2相、β0相以及γ相,放大至8000倍并未在β0相中发现有序ω相,参见图5。
[0067]
实施列3
[0068]
本实施例是一种可抑制有序ω相生成的tial合金原子百分比为:ti
‑
43.5al
‑
4nb
‑
1mn
‑
0.1b,余量为ti;tial合金的制备通过以下步骤实现:
[0069]
步骤1)配料
[0070]
将零级海绵钛、a00级高纯铝、nb
‑
al中间合金、高纯锰、高纯硼按照成分配比51.4at%ti、43.5at.%al、4at.%nb、1at.%mn、0.1at.%b配制成重量约为40g的试样并混合均匀;
[0071]
步骤2)熔炼铸锭
[0072]
将步骤1)中的试样置于真空非自耗电弧熔炼炉的坩埚内进行熔炼,熔炼五次,从第二次起每次熔炼都需要将铸锭翻面以保证铸锭的均匀性,熔炼真空度低于0.1pa,熔炼电流控制在适当范围内,五次熔炼后获得重量约为40g,直径400mm~500mm的纽扣铸锭;
[0073]
步骤3)线切割
[0074]
将步骤2)中的tial合金纽扣铸锭使用线切割机均分为四块试样;
[0075]
步骤4)热处理
[0076]
电阻炉加热至750℃,取步骤3)的四块试样中的任意两块放入炉中,分别恒温保温500小时和1000小时后,取出试样用水淬火;
[0077]
步骤5)打磨金相,至样品表面呈镜面且无划痕
[0078]
利用扫描电子显微镜(sem)在背散射电子条件下观察发现,ti
‑
43.5al
‑
4nb
‑
1mn
‑
0.1b合金中主要含有α2相、β0相以及γ相,放大至8000倍并未在β0相中发现有序ω相,参见图6。
[0079]
实施例4
[0080]
本实施例是一种可抑制有序ω相生成的tial合金原子百分比为:ti
‑
44.5al
‑
4nb
‑
0.6mn
‑
0.1b,余量为ti;tial合金的制备通过以下步骤实现:
[0081]
步骤1)配料
[0082]
将零级海绵钛、a00级高纯铝、nb
‑
al中间合金、高纯锰、高纯硼按照成分配比50.8at%ti、44.5at.%al、4at.%nb、0.6at.%mn、0.1at.%b配制成重量约为40g的试样并混合均匀;
[0083]
步骤2)熔炼铸锭
[0084]
将步骤1)中的试样置于真空非自耗电弧熔炼炉的坩埚内进行熔炼,熔炼五次,从第二次起每次熔炼都需要将铸锭翻面以保证铸锭的均匀性,熔炼真空度低于0.1pa,熔炼电流控制在适当范围内,五次熔炼后获得重量约为40g,直径400mm~500mm的纽扣铸锭;
[0085]
步骤3)线切割
[0086]
将步骤2)中的tial合金纽扣铸锭使用线切割机均分为四块试样;
[0087]
步骤4)热处理
[0088]
电阻炉加热至750℃,取步骤3)的四块试样中的任意两块放入炉中,分别恒温保温500小时和1000小时后,取出试样用水淬火;
[0089]
步骤五:打磨金相,至样品表面呈镜面且无划痕
[0090]
利用扫描电子显微镜(sem)在背散射电子条件下观察试样,发现ti
‑
44.5al
‑
4nb
‑
0.6mn
‑
0.1b合金中主要含有α2相、β0相以及γ相,放大至8000倍并未在β0相中发现有序ω相,参见图7。γ
‑
tial合金的成分设计时根据需要al原子百分含量可以在42%~48%内变化,随al含量提高,合金抗氧化性能提高、强度降低、室温塑性总体呈提高趋势。tial合金中al含量最明显的作用是影响合金的凝固类别,只有低al含量的合金才可能实现塑性较好的β凝固,即初始凝固相为β相的tial合金。本发明限定合金成分中al原子百分含量在43%~
45%,目的就是使合金为塑性较好的β凝固类型,同时也保证了其强度等其他力学性能在期望值以内。
[0091]
实施例5
[0092]
本实施例是一种tial合金原子百分比为:ti
‑
43.5al
‑
4nb
‑
0.5mn
‑
0.1b,余量为ti;所述的tial合金的制备通过以下步骤实现:
[0093]
1)配料
[0094]
将零级海绵钛、a00级高纯铝、nb
‑
al中间合金、高纯锰、高纯硼按照成分配比51.9at%ti、43.5at.%al、4at.%nb、0.5at.%mn、0.1at.%b配制成一定重量的试样并混合均匀;
[0095]
2)熔炼铸锭
[0096]
将步骤1)中的试样置于真空非自耗电弧熔炼炉的坩埚内进行熔炼,熔炼多次,熔炼真空度低于0.1pa,熔炼后获得纽扣铸锭;
[0097]
3)切割
[0098]
步骤2)中的tial合金纽扣铸锭切割为多块试样;
[0099]
4)热处理
[0100]
电阻炉加热至750℃,取步骤3)试样中的任意两块放入炉中,分别恒温保温500小时和1000小时后,取出试样淬火;
[0101]
5)打磨金相
[0102]
打磨抛光至样品表面呈镜面且无划痕。
[0103]
利用扫描电子显微镜(sem)在背散射电子条件下观察试样,发现ti
‑
43.5al
‑
4nb
‑
0.5mn
‑
0.1b合金中主要含有α2相、β0相以及γ相,放大至8000倍仍然并未在β0相中发现有序ω相。但是由于tial合金的工业应用需要对其进行锻造,这就要求其具有一定的塑性,而在其各组成相当中β0相具有较好的塑性,适当增加β0相含量可以有效提升tial合金的塑性。由于本发明设计的初衷之一是为优化tnm合金性能提供解决思路,并且设计成分时参照了[mo]当量公式,计算得tnm的[mo]当量为2.21,而ti
‑
43.5al
‑
4nb
‑
0.6mn
‑
0.1b的[mo]当量也为2.21,ti
‑
43.5al
‑
4nb
‑
0.5mn
‑
0.1b的[mo]当量则低于2.21。也就是说当本发明合金中的mn原子百分比含量低于0.6%时则会造成合金整体的[mo]当量低于tnm合金,而过低的[mo]当量会降低tial合金中β0相含量从而降低塑性,不利于工业锻造。因此本发明在设计合金成分时放弃了mn原子百分比含量低于0.6%的成分,即本实施例仅作为对比示例,不在本发明范围之内。
[0104]
实施例6
[0105]
本实施例是一种tial合金原子百分比为:ti
‑
43.5al
‑
4nb
‑
1.1mn
‑
0.1b,余量为ti;所述的tial合金的制备通过以下步骤实现:
[0106]
1)配料
[0107]
将零级海绵钛、a00级高纯铝、nb
‑
al中间合金、高纯锰、高纯硼按照成分配比51.3at%ti、43.5at.%al、4at.%nb、1.1at.%mn、0.1at.%b配制成一定重量的试样并混合均匀;
[0108]
2)熔炼铸锭
[0109]
将步骤1)中的试样置于真空非自耗电弧熔炼炉的坩埚内进行熔炼,熔炼多次,熔
炼真空度低于0.1pa,熔炼后获得纽扣铸锭;
[0110]
3)切割
[0111]
将步骤2)中的tial合金纽扣铸锭切割为多块试样;
[0112]
4)热处理
[0113]
电阻炉加热至750℃,取步骤3)试样中的任意两块放入炉中,分别恒温保温500小时和1000小时后,取出试样淬火;
[0114]
5)打磨金相
[0115]
打磨抛光至样品表面呈镜面且无划痕。
[0116]
利用扫描电子显微镜(sem)在背散射电子条件下观察试样,发现ti
‑
43.5al
‑
4nb
‑
1.1mn
‑
0.1b合金中主要含有α2相、β0相以及γ相,放大至8000倍虽然没有在β0相中发现有序ω相,但是合金中mn含量过多,经保温会在β0相区域内形成laves相,同样是有害相,对tial合金服役性能有不利影响。因此本发明在设计合金成分时放弃了mn原子百分比含量高于1%的成分,即本实施例仅作为对比示例,不在本发明范围之内。
[0117]
以上所述,仅为本发明的具体实施方式,但本发明的保护范围并不局限于此,任何熟悉本技术领域的技术人员在本发明公开的技术范围内,可轻易想到各种等效的修改或替换,这些修改或替换都应涵盖在本发明的保护范围之内。
再多了解一些
本文用于企业家、创业者技术爱好者查询,结果仅供参考。