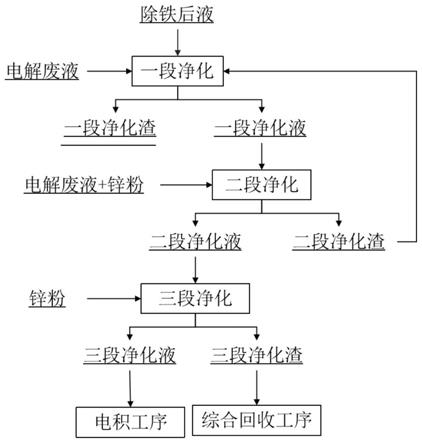
1.本发明涉及化工冶金处理技术领域,尤其涉及一种湿法冶金领域的氧压浸出锌冶炼净化除杂工艺。
背景技术:
2.氧压浸出工艺是通过氧压浸出釜将锌精矿反应生成硫酸锌溶液和硫磺单质,由于产出的硫磺在储存运输方面较传统工艺产出的硫酸更方便,因此氧压浸出工艺慢慢成为锌冶炼的主流。但氧压浸出产生的浸出液和传统焙烧浸出液有一定的差别,尤其是在离子价态等方面。氧压浸出产出的浸出液经过除铁后产出除铁后液,除铁后液中zn、cd、co、ni等离子价态与传统的除铁后液不同。传统工艺净化工序分正向锑盐净化工艺及逆向锑盐净化工艺,正向锑盐净化工艺是在一段净化过程中加入锌粉产出一段净化渣,即铜镉渣,二段净化过程中加入锌粉、硫酸铜、锑盐产出二段净化渣,即镍钴渣。逆向锑盐净化是一段净化除去镍钴,产出镍钴渣,二段净化除去铜镉,产出铜镉渣。传统净化的工艺锌粉单耗较高,行业内平均水平在60kg锌粉/t
·
zn,同时锑盐加入的多少会对下游电积产生影响。传统工艺的除铁后液ph值为5.0
‑
5.2,然后通过冷却塔降温控制温度55
‑
60℃,按照液体镉、铜含量的8
‑
12倍加入锌粉,反应时间1
‑
1.5。得到的一段净化渣中含锌36.8
‑
45%,含铜5.6
‑
6.2%,镉10.6
‑
12%,钴0.08%左右。得到的二段净化渣中含锌58.26%,其中单质锌占比80%,镉2
‑
4%,钴0.2
‑
0.3%。二段净化渣中单质锌占比较高导致在净化过程中锌粉消耗量大,得到的一段净化渣和二段净化渣需分开单独处理回收其中的锌、铜、镉。
3.为了降低锌粉单耗,产出优质的净化后液,避免对电积造成影响,开发一种氧压浸出锌冶炼净化除杂新工艺具有很大的现实意义。
技术实现要素:
4.本发明要解决的技术问题是提供一种工艺简单、锌粉单耗更少、成本更低、能够更有效地降低溶液中铜、镉、钴、镍杂质,同时能避免因锑盐加入对下游电积产生影响的新型氧压浸出锌冶炼净化除杂工艺。
5.为解决上述技术问题,本发明采用如下技术方案:一种新型氧压浸出锌冶炼净化除杂工艺,其特征在于:按以下步骤进行:
6.步骤1:将电解废液加入至除铁后液中,调整溶液ph为4.5
‑
4.8;再加入二段净化渣,控制反应温度为60
‑
65℃,反应时间为1.5
‑
2h;反应结束后固液分离,得到一段净化液和一段净化渣。传统工艺的除铁后液ph值为5.0
‑
5.2,然后通过冷却塔降温控制温度55
‑
60℃,按照液体镉、铜含量的8
‑
12倍加入锌粉,反应时间1
‑
1.5。本发明与传统相比的优点在于一段净化不用加入锌粉,通过加入二段净化渣代替锌粉,利用二段渣内过量锌粉置换出合格的一段净化液。
7.步骤2:将步骤1所得的一段净化液泵送至一段净化槽,再加入电解废液调整ph至4.8
‑
5.0,再加入锌粉,锌粉加入量为含钴量的300倍,控制反应温度为80
‑
85℃,反应时间为
2
‑
2.5h;反应结束后固液分离,得到二段净化渣和二段净化液。传统工艺的ph为5.0
‑
5.2,反应温度85
‑
90℃,反应时间2.5
‑
3h。
8.步骤3:将步骤2所得的二段净化液泵送至三段净化槽,再加入锌粉,锌粉加入量为含镉量的8
‑
12倍,反应温度为65
‑
75℃,反应结束后固液分离,得到三段净化渣和三段净化液;三段净化液输送至电解工序电解锌,三段净化渣和一段净化渣合并后输送至综合回收工序回收铜、镉、钴。
9.步骤1中,除铁后液为氧压浸出工艺产出的浸出液再经过针铁矿除铁法产出的除铁后液,其ph为5.0左右。
10.在步骤2中,二段净化产出的二段净化渣全部返回至一段净化,作为一段净化工序的净化剂。
11.步骤1中的电解废液的成分包括有h
:165
‑
175g/l、zn
2
:50
‑
55g/l。
12.步骤1和步骤2中的二段净化渣均为逆向锑盐净化法所得的二段净化渣,即镍钴渣,其主要成分为过量锌粉,单质锌含量为50
‑
56%、镉为4
‑
6%、钴为0.05
‑
0.07%、铅为10
‑
15%。
13.步骤1中的一段净化液的成分包含有zn
2
:140
‑
165g/l、cu
2
<0.0005g/l、cd
2
<0.1g/l、co:10
‑
16g/l。当然,上述数据根据矿内有价金属含量的不同可能会发生变化;一段净化渣的主要成分包括有:zn为17
‑
23%、pb为3
‑
5%、cu为7
‑
13%、cd为7
‑
13%。
14.步骤2中的二段净化液的成分包含有zn
2
:145
‑
165g/l、cu
2
<0.0005g/l、cd
2
:0.001
‑
0.004g/l、co<0.0005g/l。
15.步骤3中的三段净化渣包含有锌15
‑
20%,还可以有镉微量。
16.步骤3中的三段净化液包含有zn
2
:145
‑
165g/l、cu
2
<0.0005g/l、cd
2
<0.001g/l、co<0.0005g/l。
17.与传统的净化除杂工艺相比,本发明工艺具有以下优点:
18.第一、通过将二段净化渣全部返回至一段净化,作为一段净化的净化剂,进而代替传统净化除杂工艺的锌粉,从而有效降低了锌粉加入量。再结合本发明的控制参数,利用离子活度在反应中控制二段净化渣中镍、钴和除铁后液中硫酸反应再次进入一段净化液中;
19.第二、一段净化和二段净化在加入二段净化渣和锌粉前,首先采用电解废液将溶液ph进行调整,调整后酸度较小,更有利于锌粉和二段净化渣与溶液中铜、镉、钴、镍等元素发生置换反应;
20.第三、本发明工艺产出的一段净化渣中含有铜、镉、钴、镍,便于后续工序综合回收铜、镉、钴等金属,实现同时处理铜、镉、钴镍渣。
21.第四、本发明在二段净化过程中加入电解废液,再加入锌粉,通过控制参数,避免了传统工艺加入硫酸铜和锑盐等活化剂,从而避免了对电积后续造成的影响。
附图说明
22.图1为本发明的工艺流程图。
具体实施方式
23.下面结合附图1通过具体实施例对本发明做进一步说明:
24.实施例1:氧压浸出除铁后液成分如下:
25.元素zncucdco含量(g/l)1450.271.120.014
26.按以下步骤进行:
27.步骤1:将电解废液加入至除铁后液(150m3)中,调整溶液ph为4.5;再加入二段净化渣,控制反应温度为60℃,反应时间为2h;反应结束后固液分离,得到一段净化液和一段净化渣;
28.步骤2:将步骤1所得的一段净化液泵送至一段净化槽,再加入电解废液调整ph至5.0,再加入锌粉,锌粉加入量为含钴量的300倍(即630kg),控制反应温度为85℃,反应时间为2h;反应结束后固液分离,得到二段净化渣和二段净化液;
29.步骤3:将步骤2所得的二段净化液泵送至三段净化槽,再加入锌粉,锌粉加入量为含镉量的8倍(即1.344t)(加入量按二净后镉0.004g/l换算);反应温度为70℃,反应结束后固液分离,得到三段净化渣和三段净化液。三段净化液输送至电解工序电解锌,三段净化渣和一段净化渣合并后输送至综合回收工序回收铜、镉、钴。
30.结果:该工艺产出的一段净化渣和三段净化液主要成分如下:
31.元素zncucdco一段净化渣含量(%)32.95.4610.60.073三段净化液含量(g/l)1480.000470.00090.00043
32.产出的三段净化液中铜、镉、钴杂质含量均满足电积要求。去除率=[1
‑
(三段净化液中me含量/氧压浸出除铁后液中me含量)]*100%,me代表金属含量。其中铜的去除率为99.8%、镉的去除率99.9%、钴的去除率96.9%。
[0033]
实施例2:氧压浸出除铁后液成分如下:
[0034]
元素zncucdco含量(g/l)145.50.231.150.016
[0035]
按以下步骤进行:
[0036]
步骤1:将电解废液加入至除铁后液(100m3)中,调整溶液ph为4.8;再加入二段净化渣,控制反应温度为64℃,反应时间为1.5h;反应结束后固液分离,得到一段净化液和一段净化渣;
[0037]
步骤2:将步骤1所得的一段净化液泵送至一段净化槽,再加入电解废液调整ph至4.8,再加入锌粉,锌粉加入量为含钴量的300倍即(480kg),控制反应温度为85℃,反应时间为2.5h;反应结束后固液分离,得到二段净化渣和二段净化液;
[0038]
步骤3:将步骤2所得的二段净化液泵送至三段净化槽,再加入锌粉,锌粉加入量为含镉量的12倍即(1380kg);反应温度为70℃,反应结束后固液分离,得到三段净化渣和三段净化液。三段净化液输送至电解工序电解锌,三段净化渣和一段净化渣合并后输送至综合回收工序回收铜、镉、钴。
[0039]
结果:该工艺产出的一段净化渣和三段净化液主要成分如下:
[0040]
元素zncucdco一段净化渣含量(%)34.26.489.460.066
三段净化液含量(g/l)148.60.000670.000850.00023
[0041]
产出的三段净化液中铜、镉、钴杂质含量均满足电积要求。去除率=[1
‑
(三段净化液中me含量/氧压浸出除铁后液中me含量)]*100%,me代表金属含量。其中铜的去除率为99.7%、镉的去除率99.9%、钴的去除率98.5%。
[0042]
以上已将本发明做一详细说明,以上所述,仅为本发明之较佳实施例而已,当不能限定本发明实施范围,即凡依本技术范围所作均等变化与修饰,皆应仍属本发明涵盖范围内。
再多了解一些
本文用于企业家、创业者技术爱好者查询,结果仅供参考。