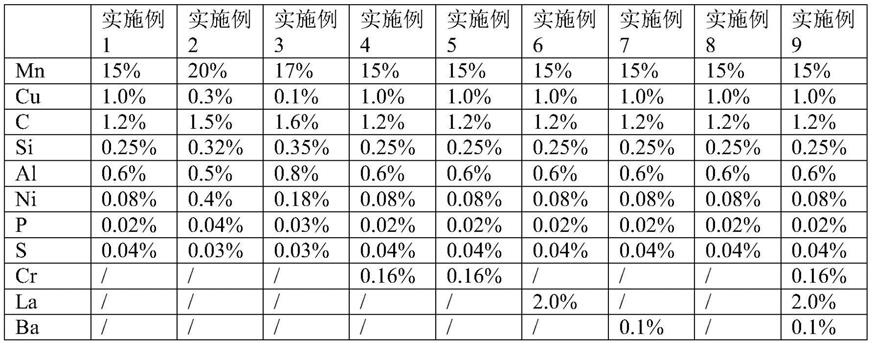
1.本技术涉及阀体领域,更具体地说,它涉及一种阀体铸件及其铸造工艺。
背景技术:
2.阀门是用来开闭管路、控制流向、调节和控制输送介质的参数(温度、压力和流量)的管路附件,具有截止、调节、导流、防止逆流、稳压、分流或溢流泄压等功能。
3.阀门通常由阀体、阀芯、密封圈与阀芯控制组件组成,其中阀体是阀门的主要组成部件,一般通过铸造制得,铸造过程中,阀体的表面易产生裂纹,影响了阀门的质量,导致阀门的整体性能下降,无法满足实际使用的要求,有待改进。
技术实现要素:
4.为了改善阀体铸造过程中其表面易产生裂纹的问题,本技术提供一种阀体铸件及其铸造工艺。
5.第一方面,本技术提供一种阀体铸件的铸造工艺,采用如下的技术方案:一种阀体铸件的铸造工艺,包括以下步骤:s1.熔炼:将钢材熔炼为钢水;s2.模具准备:按照图纸尺寸要求制得阀体模具,将阀体模具放入型砂盒中,得到砂型;s3.浇注阀体:将s1中的钢水浇注到s2中的砂型中,浇注温度为1350
‑
1400℃,浇注时间为25
‑
30s,浇注完成后,保温静置30
‑
50min,降温至300
‑
400℃取出,得到铸件;s4.热割冒口:将s3中的铸件升温至600
‑
650℃并保温6
‑
8h,接着降温至350
‑
400℃,出炉进行热割冒口,热割冒口结束后铸件的温度>200℃;s5.正火热处理:将经s4处理后的铸件加热到850
‑
870℃,并保温2
‑
3h,然后用淬火油冷却至100℃以下;s6.回火处理:将经s5处理后的铸件升温至400
‑
700℃,保温16
‑
24h,再降温至250
‑
350℃,然后出炉冷却到室温;s7.表面处理:将经s6处理后的铸件经打磨,抛光后得到成品阀体铸件。
6.通过采用上述技术方案,热割冒口步骤前对铸件进行退火,以减少铸件内部的残余应力,再对铸件进行热割冒口,减少了铸件常温气割时因铸件与周围环境温差较大,导致铸件内部产生热应力,进而使得铸件表面产生裂纹的情况;同时采用淬火油进行淬火,相比于水淬,降低了铸件的冷却速率,进而降低了铸件内部的马氏体区的冷却速率,减少了奥氏体向马氏体转变过程中产生的热应力和组织应力,进而减少了淬火过程中裂纹的产生。
7.采用上述铸造工艺,使得铸件在铸造过程中其表面不易产生裂纹,减少了对制得的成品阀体铸件的质量的影响,进而减少了对制得的成品阀体铸件的整体性能的影响,使得制得的成品阀体铸件可满足实际使用的要求,减少了成品阀体铸件因质量不合格导致的材料浪费,有利于降低阀体铸件的铸造成本,并具有一定的节能效果。
8.优选的,所述钢材包括如下重量百分比的化学成分:mn:15%
‑
20%、cu:0.1%
‑
1.0%、c:1.2%
‑
1.6%、si:0.25%
‑
0.35%、al:0.5%
‑
0.8%、ni:0.08%
‑
0.4%、p≤0.04、s≤0.04,余量为fe及不可避免的杂质。
9.通过采用上述技术方案,高锰钢的耐磨性和结构强度较好,适用于阀体铸件的使用需要;高锰钢的导热性能较差,cu的导热性能较好,加入cu可改善高锰钢的导热性能,当铸件出炉冷却至室温时,减少了铸件由于导热性能较差导致铸件与外界环境温差较大,进而使得铸件内部应力增加的情况,从而减少了铸件在冷却时其表面产生裂纹的情况。
10.c的加入可提高铸件的强度和硬度。
11.al作为脱氧剂使用,可减少铸件内出现气孔的情况,并可减少铸件中的fe与氧反应生成的氧化亚铁,从而减少了铸件中残留的氧化亚铁,氧化亚铁的溶解度随温度下降而减小,进而减少了氧化亚铁在浇注后降温的过程中在晶界处析出,进而割裂晶粒之间的连接的情况,从而降低了铸件的热裂倾向。
12.al的加入还能细化铸件内部的晶粒,增加晶界的数量,进而可抑制裂纹的产生和扩展,有利于提高铸件的力学性能。
13.加入少量的si,可提高al的脱氧能力。
14.ni的加入有利于提高铸件的韧性和防腐性,还有利于提高铸件的高温抗氧化性、扩大铸件内的奥氏体区、细化晶粒。
15.优选的,所述钢材的化学成分中还包括cr,cr和ni的质量比为(2.0
‑
2.2):1。
16.通过采用上述技术方案,cr的加入可促使钢材内铁素体的形成,提高钢材中的cr/ni比,可提高钢材中铁素体的含量,进而可提高钢材的塑性和韧性,从而减少了制得的铸件表面在铸造过程中产生裂纹的情况。
17.优选的,在热割冒口步骤之后将铸件加热至730
‑
750℃,保温2
‑
4h,然后冷却至室温。
18.通过采用上述技术方案,钢材中c、cr含量较高,导致钢材的硬度较大,使得铸件在冷却过程中,铸件的收缩受到阻碍进而在铸件内产生应力,导致铸件内部应力变大,在热割冒口后进行退火,可进一步减少铸件的内部应力,有利于铸件后续进行加工,并进一步减少了铸件表面产生裂纹的情况。
19.优选的,按重量百分比计,所述钢材中的化学成分还包括2.0%
‑
2.4%la。
20.通过采用上述技术方案,加入la可使钢材中的硫化物夹杂形成更为稳定的球状硫化物,减少了对钢材的危害,降低了钢材的裂纹倾向,从而减少了铸件表面裂纹的产生。
21.优选的,按重量百分比计,所述钢材中的化学成分还包括0.01%
‑
0.2%ba。
22.通过采用上述技术方案,ba与al、si复合脱氧,可达到更好的脱氧效果,减少了钢材中夹杂物的含量,还可细化钢材内的结晶组织,提高钢材的韧性,从而综合减少了制得的铸件表面产生裂纹的情况。
23.优选的,回火处理的步骤为:将铸件以每小时50
‑
60℃的加热速率升温至400
‑
500℃,保温20
‑
24h,再以每小时50
‑
60℃的速率在炉内降至250
‑
350℃,然后出炉冷却到室温。
24.通过采用上述技术方案,c含量大于0.1%时会导致钢材内的片状马氏体晶体出现和增多,进而降低了钢材的抗裂性能,在400
‑
500℃下进行回火,钢材内部发生应力松弛过程,减少了晶粒间产生的裂纹,从而减少了铸件表面裂纹的产生,同时以一定的速度进行升
温和降温,减少了升温速率或冷却速率过快导致铸件内部的应力增大的情况,从而进一步减少了铸件表面裂纹的产生。
25.第二方面,本技术提供一种阀体铸件,由上述铸造工艺制得。
26.综上所述,本技术具有以下有益效果:1、本技术的铸造工艺通过在热割冒口步骤前对铸件进行退火,以减少铸件内部的残余应力,再对铸件进行热割冒口,减少了铸件内部产生热应力,进而使得铸件表面产生裂纹的情况,同时采用淬火油进行淬火,降低了铸件内部的马氏体区的冷却速率,减少了奥氏体向马氏体转变过程中产生的热应力和组织应力,进而减少了淬火过程中裂纹的产生,使得制得的成品阀体铸件可满足实际使用的要求,有利于降低阀体铸件的铸造成本,并具有一定的节能效果。
27.2、本技术中优选采用在钢材的化学成分中加入gu和al,加入cu可改善高锰钢的导热性能,减少了铸件由于导热性能较差导致铸件与外界环境温差较大,进而使得铸件内部应力增加的情况,al的加入可减少铸件内出现气孔的情况,并可减少铸件中残留的氧化亚铁,进而减少了氧化亚铁在浇注后降温的过程中在晶界处析出,进而割裂晶粒之间的连接的情况,从而降低了铸件的热裂倾向。
28.3、本技术中优选采用在钢材的化学成分中加入cr,cr的加入可促使钢材内铁素体的形成,提高钢材中的cr/ni比,可提高钢材中铁素体的含量,进而可提高钢材的塑性和韧性,从而减少了制得的铸件表面在铸造过程中产生裂纹的情况。
具体实施方式
29.以下结合实施例对本技术作进一步详细说明。
30.淬火油购于广州海力润滑科技有限公司,型号为u8 132。
31.以下实施方式中所用原料除特殊说明外均可来源于普通市售。实施例
32.实施例1本技术公开了一种阀体铸件的铸造工艺,包括以下步骤:s1.熔炼:将钢材置于1550℃的熔炉中熔炼为钢水;s2.模具准备:按照图纸尺寸要求制得阀体模具,将阀体模具放入型砂盒中,得到砂型,将砂型在650℃下烘15min,随后降温至350℃备用;s3.浇注阀体:将s1中的钢水浇注到s2中的砂型中,浇注温度为1350℃,浇注时间为30s,浇注完成后,保温静置50min,降温至300℃取出,得到铸件;s4.热割冒口:将s3中的铸件升温至600℃并保温8h,接着降温至350℃,出炉进行热割冒口,热割冒口结束后铸件的温度>200℃;s5.正火热处理:将经s4处理后的铸件加热到850℃,并保温3h,然后用淬火油冷却至100℃;s6.回火处理:将经s5处理后的铸件升温至400℃,保温24h,再降温至250℃,然后出炉冷却到室温;s7.表面处理:将经s6处理后的铸件经打磨,抛光后得到成品阀体铸件。
33.其中,钢材的各组分含量如下表1
‑
1所示。
34.实施例2本技术公开了一种阀体铸件的铸造工艺,包括以下步骤:s1.熔炼:将钢材置于1550℃的熔炉中熔炼为钢水;s2.模具准备:按照图纸尺寸要求制得阀体模具,将阀体模具放入型砂盒中,得到砂型,将砂型在650℃下烘15min,随后降温至350℃备用;s3.浇注阀体:将s1中的钢水浇注到s2中的砂型中,浇注温度为1400℃,浇注时间为25s,浇注完成后,保温静置30min,降温至400℃取出,得到铸件;s4.热割冒口:将s3中的铸件升温至650℃并保温6h,接着降温至400℃,出炉进行热割冒口,热割冒口结束后铸件的温度>200℃;s5.正火热处理:将经s4处理后的铸件加热到870℃,并保温2h,然后用淬火油冷却至80℃;s6.回火处理:将经s5处理后的铸件升温至700℃,保温16h,再降温至350℃,然后出炉冷却到室温;s7.表面处理:将经s6处理后的铸件经打磨,抛光后得到成品阀体铸件。
35.其中,钢材的各组分含量如下表1
‑
1所示。
36.实施例3本技术公开了一种阀体铸件的铸造工艺,包括以下步骤:s1.熔炼:将钢材置于1550℃的熔炉中熔炼为钢水;s2.模具准备:按照图纸尺寸要求制得阀体模具,将阀体模具放入型砂盒中,得到砂型,将砂型在650℃下烘15min,随后降温至350℃备用;s3.浇注阀体:将s1中的钢水浇注到s2中的砂型中,浇注温度为1370℃,浇注时间为28s,浇注完成后,保温静置40min,降温至350℃取出,得到铸件;s4.热割冒口:将s3中的铸件升温至630℃并保温7h,接着降温至380℃,出炉进行热割冒口,热割冒口结束后铸件的温度>200℃;s5.正火热处理:将经s4处理后的铸件加热到860℃,并保温3h,然后用淬火油冷却至100℃;s6.回火处理:将经s5处理后的铸件升温至550℃,保温20h,再降温至300℃,然后出炉冷却到室温;s7.表面处理:将经s6处理后的铸件经打磨,抛光后得到成品阀体铸件。
37.其中,钢材的各组分含量如下表1
‑
1所示。
38.实施例4与实施例1的区别在于,钢材的化学成分中加入cr,各组分含量如下表1
‑
1所示。
39.实施例5与实施例4的区别在于,s4的步骤为:将s3中的铸件升温至600℃并保温8h,接着降温至350℃,出炉进行热割冒口,热割冒口结束后铸件的温度>200℃,将铸件加热至730℃,保温4h,然后冷却至室温。
40.各组分含量如下表1
‑
1所示。
41.实施例6与实施例1的区别在于,钢材的化学成分中加入la,各组分含量如下表1
‑
1所示。
42.实施例7与实施例1的区别在于,钢材的化学成分中加入ba,各组分含量如下表1
‑
1所示。
43.实施例8与实施例1的区别在于,s6的步骤为:将铸件以每小时50℃的加热速率升温至400℃,保温24h,再以每小时50℃的速率在炉内降至250℃,然后出炉冷却到室温。
44.各组分含量如下表1
‑
1所示。
45.实施例9本技术公开了一种阀体铸件的铸造工艺,包括以下步骤:s1.熔炼:将钢材置于1550℃的熔炉中熔炼为钢水;s2.模具准备:按照图纸尺寸要求制得阀体模具,将阀体模具放入型砂盒中,得到砂型,将砂型在650℃下烘15min,随后降温至350℃备用;s3.浇注阀体:将s1中的钢水浇注到s2中的砂型中,浇注温度为1350℃,浇注时间为30s,浇注完成后,保温静置50min,降温至300℃取出,得到铸件;s4.热割冒口:将s3中的铸件升温至600℃并保温8h,接着降温至350℃,出炉进行热割冒口,热割冒口结束后铸件的温度>200℃,将铸件加热至730℃,保温4h,然后冷却至室温;s5.正火热处理:将经s4处理后的铸件加热到850℃,并保温3h,然后用淬火油冷却;s6.回火处理:将铸件以每小时50℃的加热速率升温至400℃,保温24h,再以每小时50℃的速率在炉内降至250℃,然后出炉冷却到室温;s7.表面处理:将经s6处理后的铸件经打磨,抛光后得到成品阀体铸件。
46.其中,钢材的各组分含量如下表1
‑
1所示。
47.实施例10本技术公开了一种阀体铸件的铸造工艺,包括以下步骤:s1.熔炼:将钢材置于1550℃的熔炉中熔炼为钢水;s2.模具准备:按照图纸尺寸要求制得阀体模具,将阀体模具放入型砂盒中,得到砂型,将砂型在650℃下烘15min,随后降温至350℃备用;s3.浇注阀体:将s1中的钢水浇注到s2中的砂型中,浇注温度为1400℃,浇注时间为25s,浇注完成后,保温静置30min,降温至400℃取出,得到铸件;s4.热割冒口:将s3中的铸件升温至650℃并保温6h,接着降温至400℃,出炉进行热割冒口,热割冒口结束后铸件的温度>200℃,将铸件加热至750℃,保温2h,然后冷却至室温;s5.正火热处理:将经s4处理后的铸件加热到870℃,并保温2h,然后用淬火油冷却;s6.回火处理:将铸件以每小时60℃的加热速率升温至500℃,保温20h,再以每小时60℃的速率在炉内降至350℃,然后出炉冷却到室温;s7.表面处理:将经s6处理后的铸件经打磨,抛光后得到成品阀体铸件。
48.其中,钢材的各组分含量如下表1
‑
2所示。
49.实施例11
本技术公开了一种阀体铸件的铸造工艺,包括以下步骤:s1.熔炼:将钢材置于1550℃的熔炉中熔炼为钢水;s2.模具准备:按照图纸尺寸要求制得阀体模具,将阀体模具放入型砂盒中,得到砂型,将砂型在650℃下烘15min,随后降温至350℃备用;s3.浇注阀体:将s1中的钢水浇注到s2中的砂型中,浇注温度为1370℃,浇注时间为28s,浇注完成后,保温静置40min,降温至350℃取出,得到铸件;s4.热割冒口:将s3中的铸件升温至630℃并保温7h,接着降温至380℃,出炉进行热割冒口,热割冒口结束后铸件的温度>200℃,将铸件加热至740℃,保温3h,然后冷却至室温;s5.正火热处理:将经s4处理后的铸件加热到860℃,并保温3h,然后用淬火油冷却;s6.回火处理:将铸件以每小时55℃的加热速率升温至450℃,保温22h,再以每小时55℃的速率在炉内降至300℃,然后出炉冷却到室温;s7.表面处理:将经s6处理后的铸件经打磨,抛光后得到成品阀体铸件。
50.其中,钢材的各组分含量如下表1
‑
2所示。
51.实施例12与实施例8的区别在于,s6的步骤为:将铸件以每小时70℃的加热速率升温至400℃,保温24h,再以每小时70℃的速率在炉内降至250℃,然后出炉冷却到室温。
52.各组分含量如下表1
‑
2所示。
53.实施例13与实施例8的区别在于,s6的步骤为:将铸件以每小时50℃的加热速率升温至300℃,保温24h,再以每小时50℃的速率在炉内降至250℃,然后出炉冷却到室温。
54.各组分含量如下表1
‑
2所示。
55.实施例14与实施例8的区别在于,s6的步骤为:将铸件以每小时50℃的加热速率升温至700℃,保温24h,再以每小时50℃的速率在炉内降至250℃,然后出炉冷却到室温。
56.各组分含量如下表1
‑
2所示。
57.对比例对比例1与实施例1的区别在于,以未经本技术的s4步骤处理、且s6步骤中采用水进行冷却的钢材作为空白对照组。
58.对比例2与实施例1的区别在于,s4的步骤为:将s3中的铸件升温至600℃并保温8h,接着降温至350℃。
59.各组分含量如下表1
‑
2所示。
60.对比例3与实施例1的区别在于,s4的步骤为:将s3中的铸件进行热割冒口,热割冒口结束后铸件的温度>200℃。
61.各组分含量如下表1
‑
2所示。
62.对比例4与实施例1的区别在于,将淬火油替换为水,各组分含量如下表1
‑
2所示。
63.表1
‑
1组分含量表表1
‑
2组分含量表2组分含量表需要指出的是,表格中的%为重量百分号,每个实施例或对比例中钢材的余量为fe及不可避免的杂质。
64.性能检测试验按照实施例1
‑
14和对比例1
‑
4的铸造工艺制得成品阀体铸件,作为试样。
65.(1)裂纹试验一:观察各个试样表面是否出现裂纹及裂纹数量并记录,裂纹数量以“ ”计,“ ”越多,裂纹数量越多,试验结果如下表2所示。
66.(2)裂纹试验二:将实施例1、4
‑
8、12
‑
14的试样升温至1200℃,室温下冷却,记录试样表面出现裂纹的时间,出现裂纹的时间越长,标明试样越不易产生裂纹,试验结果如下表2所示。
67.(3)韧性试验(以冲击吸收能量表征韧性):将实施例1、4、7的试样按照标准gb/t 229
‑
2007《夏比摆锤冲击试验方法》测定冲击吸收能量,冲击吸收能量越大,韧性越好,测定结果如下表2所示。
68.表2各实施例和对比例的测试结果表
综上所述,可以得出以下结论:1.结合实施例1和对比例1
‑
2并结合表2可以看出,热割冒口步骤前对铸件进行退火可减少铸件表面裂纹的产生,其原因可能是:割冒口步骤前对铸件进行退火可减少铸件内部的残余应力。
69.2.结合实施例1和对比例1、3并结合表2可以看出,对铸件进行热割冒口可减少铸件表面裂纹的产生,其原因可能是:对铸件进行热割冒口,减少了铸件常温气割时因铸件与周围环境温差较大,导致铸件内部产生热应力,进而使得铸件表面产生裂纹的情况。
70.3.结合实施例1和对比例1、4并结合表2可以看出,采用淬火油进行淬火有利于减少铸件表面裂纹的产生,其原因可能是:采用淬火油进行淬火,相比于水淬,降低了铸件的冷却速率,进而降低了铸件内部的马氏体区的冷却速率,减少了奥氏体向马氏体转变过程中产生的热应力和组织应力,进而减少了淬火过程中裂纹的产生。
71.4.结合实施例1、4并结合表2可以看出,在钢材的化学成分中加入cr有利于减少铸件表面裂纹的产生,其原因可能是:cr的加入可促使钢材内铁素体的形成,提高钢材中的cr/ni比,可提高钢材中铁素体的含量,进而可提高钢材的塑性和韧性,从而减少了制得的铸件表面在铸造过程中产生裂纹的情况。
72.5、结合实施例1、4
‑
5并结合表2可以看出,在热割冒口后进行退火,有利于减少铸件表面裂纹的产生,其原因可能是:钢材中c、cr含量较高,导致钢材的硬度较大,使得铸件在冷却过程中,铸件的收缩受到阻碍进而在铸件内产生应力,导致铸件内部应力变大,在热割冒口后进行退火,可进一步减少铸件的内部应力,从而进一步减少了铸件表面产生裂纹的情况。
73.6、结合实施例1、6并结合表2可以看出,在钢材的化学成分中加入la有利于减少铸件表面裂纹的产生,其原因可能是:加入la可使钢材中的硫化物夹杂形成更为稳定的球状硫化物,减少了对钢材的危害,降低了钢材的裂纹倾向,从而减少了铸件表面裂纹的产生。
74.7、结合实施例1、7并结合表2可以看出,在钢材的化学成分中加入ba有利于减少铸件表面裂纹的产生,其原因可能是:ba与al、si复合脱氧,可达到更好的脱氧效果,减少了钢材中夹杂物的含量,还可细化钢材内的结晶组织,提高钢材的韧性,从而综合减少了制得的铸件表面产生裂纹的情况。
75.8、结合实施例1、8、12
‑
14并结合表2可以看出,在400
‑
500℃下进行回火、同时以一定的速度进行升温和降温有利于减少铸件表面裂纹的产生,其原因可能是:c含量大于0.1%时会导致钢材内的片状马氏体晶体出现和增多,进而降低了钢材的抗裂性能,在400
‑
500℃下进行回火,钢材内部发生应力松弛过程,减少了晶粒间产生的裂纹,从而减少了铸件表面裂纹的产生,同时以一定的速度进行升温和降温,减少了升温速率或冷却速率过快导致铸件内部的应力增大的情况,从而进一步减少了铸件表面裂纹的产生。
76.本具体实施例仅仅是对本技术的解释,其并不是对本技术的限制,本领域技术人员在阅读完本说明书后可以根据需要对本实施例做出没有创造性贡献的修改,但只要在本技术的权利要求范围内都受到专利法的保护。
再多了解一些
本文用于企业家、创业者技术爱好者查询,结果仅供参考。