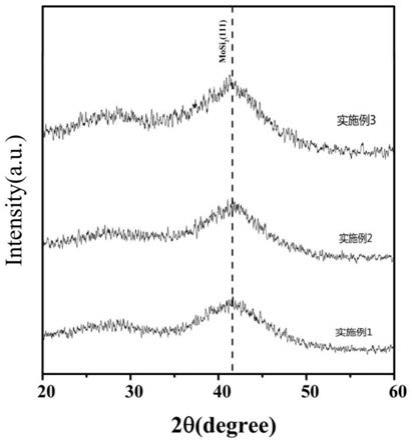
1.本发明涉及防护材料技术领域,尤其涉及一种薄膜材料及其制备方法和应用。
背景技术:
2.随着航空航天事业的飞速发展,对于航空发动机的传动机构如齿轮、花键能否承受恶劣的工作环境是航空发动机能否稳定运行的前提。这不仅要求发动机的传动机构具有较高的硬度韧性以及耐磨性能,而且其使用寿命也至关重要。另一方面,传动机构之间需要承受不同零部件之间的摩擦,较大的摩擦系数会降低传动机构之间传递效率,而低的摩擦系数在不仅能够减小传动机构的磨损,而且能够提高传动效率。同时,在保证发动机传动机构稳定运行的前提下,减小其对空中环境的影响也应该被考虑到。薄膜技术的发展对提高材料表面硬度、韧性以及降低表面的摩擦系数具有显著的效果。
3.近年来,人们发现过渡金属硅化物具有高硬度、高耐磨性和抗氧化性,作为硬质防护薄膜,在改善材料性能方面具有显着效果。二硅化钼作为一种过渡金属硅化物,具有金属和陶瓷的双重性能,具有较高的耐磨性、耐腐蚀性和抗氧化性。同时mosi2也是一种可再生、无毒、环保的材料,这使其成为防护薄膜的首要选择。但是,mosi2其固有的脆性限制其力学性能的进一步提高。
技术实现要素:
4.有鉴于此,本发明的目的在于提供一种薄膜材料及其制备方法和应用。本发明提供的薄膜材料硬度高,断裂韧性好。
5.为了实现上述发明目的,本发明提供以下技术方案:
6.本发明提供了一种薄膜材料,包括钼元素、硅元素和贵金属元素,所述贵金属元素为金或银,所述钼元素的含量为28~35at.%,所述硅元素的含量为60~70at.%,所述贵金属元素的含量为0.5~1.5at.%,所述贵金属元素以单原子形式存在。
7.优选地,所述贵金属元素的含量为0.8~1.0at.%。
8.优选地,所述钼元素的含量为30.6at.%,所述硅元素的含量为68.9at.%,所述金的含量为0.5at.%。
9.优选地,所述钼元素的含量为31.7at.%,所述硅元素的含量为67.5at.%,所述金的含量为0.8at.%。
10.优选地,所述钼元素的含量为32.4at.%,所述硅元素的含量为66.1at.%,所述金的含量为1.5at.%。
11.优选地,所述钼元素的含量为32.3at.%,所述硅元素的含量为66.7at.%,所述银的含量为1.0at.%。
12.本发明还提供了上述技术方案所述的薄膜材料的制备方法,包括以下步骤:
13.利用mosi2靶材和贵金属靶材,在衬底表面同时进行磁控溅射沉积,得到所述薄膜材料,所述贵金属靶材为au靶材或ag靶材。
14.优选地,所述磁控溅射沉积时,溅射所述mosi2靶材的直流恒定电流为0.5a,溅射所述贵金属靶材的功率为0~50w,且溅射所述贵金属靶材的功率不为0。
15.优选地,所述磁控溅射沉积的工作压强为0.6~0.8pa。
16.本发明还提供了上述技术方案所述的薄膜材料或上述技术方案所述制备方法制得的薄膜材料在航空发动机传动机构中的应用。
17.本发明提供了一种薄膜材料,包括钼元素、硅元素和贵金属元素,所述贵金属元素为金或银,所述钼元素的含量为28~35at.%,所述硅元素的含量为60~70at.%,所述贵金属元素的含量为0.5~1.5at.%,所述贵金属元素以单原子形式存在。本发明中,贵金属au或ag单原子的引入,可以调控mosi2的微观结构,限制mosi2的晶粒尺寸,提高mosi2薄膜的致密度,改善其本征脆性提高其韧性,进而提高薄膜材料的硬度和断裂韧性。且少量au单原子或ag单原子的掺杂在保证mosi2本身耐磨性能的同时,提高其韧性,并降低其在油润滑条件下的摩擦系数。本发明证明了过渡族金属硅化物在发动机传动机构中的应用潜力,同时对发动机传动机构轻量化设计起到一定的影响。因此该方法制备出的薄膜材料在航空发动机的传动机构中具有良好的发展应用的前景,对发动机传动机构具有重要意义。
18.本发明还提供了上述技术方案所述薄膜材料的制备方法,本发明采用磁控溅射沉积技术制备薄膜材料,方法简单,快捷,流程短。
19.进一步地,本发明可通过改变贵金属靶材的功率来控制贵金属单原子的含量;可通过控制磁控溅射沉积的时间来控制薄膜材料的厚度。
附图说明
20.图1为实施例1~3制备的不同薄膜材料的xrd图;
21.图2为实施例2制备的薄膜材料的高分辨图;
22.图3为实施例2制备的薄膜材料的对应选区电子衍射图;
23.图4为对比例2制备的薄膜材料的高分辨图;
24.图5为对比例2制备的薄膜材料的对应选区电子衍射图;
25.图6为实施例1~3和对比例1~2制备的薄膜的摩擦系数曲线。
具体实施方式
26.本发明提供了一种薄膜材料,包括钼元素、硅元素和贵金属元素,所述贵金属元素为金或银,所述钼元素的含量为28~35at.%,所述硅元素的含量为60~70at.%,所述贵金属元素的含量为0.5~1.5at.%,所述贵金属元素以单原子形式存在。
27.在本发明中,所述薄膜材料的厚度优选为1~1.5μm。
28.在本发明中,所述贵金属元素的含量优选为0.8~1.0at.%。在本发明中,所述贵金属元素取代mosi2中的si原子。
29.在本发明中,所述钼元素和硅元素以mosi2的形式存在,所述mosi2对应c40六方结构并向(111)面优先取向。
30.在本发明的一个具体实施例中,所述钼元素的含量为30.6at.%,所述硅元素的含量为68.9at.%,所述金的含量为0.5at.%或
31.所述钼元素的含量为31.7at.%,所述硅元素的含量为67.5at.%,所述金的含量
为0.8at.%或
32.所述钼元素的含量为32.4at.%,所述硅元素的含量为66.1at.%,所述金的含量为1.5at.%或
33.所述钼元素的含量为32.3at.%,所述硅元素的含量为66.7at.%,所述银的含量为1.0at.%。
34.本发明还提供了上述技术方案所述的薄膜材料的制备方法,包括以下步骤:
35.利用mosi2靶材和贵金属靶材,在衬底表面同时进行磁控溅射沉积,得到所述薄膜材料,所述贵金属靶材为au靶材或ag靶材。
36.在本发明中,所述磁控溅射沉积时,溅射所述mosi2靶材的直流恒定电流优选为0.5a,溅射所述贵金属靶材的功率优选为0~50w,且溅射所述贵金属靶材的功率优选不为0。
37.在本发明中,所述磁控溅射沉积的工作压强优选为0.6~0.8pa。
38.在本发明中,所述磁控溅射沉积时,靶材和衬底的距离独立地优选为10~15cm。
39.在本发明中,所述磁控溅射沉积前优选通过涡轮分子泵将镀膜室的真空度抽至1
×
10
‑4pa,并通入80sccm的ar作为溅射气体。在本发明中,所述ar的纯度优选为99.99%。
40.在本发明中,所述衬底优选为si片。在本发明中,所述磁控溅射沉积时,所述衬底优选不施加温度和偏压。
41.在本发明中,所述si片在使用前优选进行预处理,所述预处理优选为依次用乙醇、丙酮和去离子水超声清洗,然后烘干。在本发明中,每次所述超声清洗的时间优选为15分钟。本发明对所述烘干的具体方式没有特殊的限定,能够完全除去去离子水即可。
42.在本发明中,所述mosi2靶材和贵金属靶材的纯度均优选为99.95wt%。
43.本发明还提供了上述技术方案所述的薄膜材料或上述技术方案所述制备方法制得的薄膜材料在航空发动机传动机构中的应用。
44.本发明对所述应用没有特殊的限定,采用本领域技术人员熟知的方式即可。
45.为了进一步说明本发明,下面结合实例对本发明提供的薄膜材料及其制备方法和应用进行详细地描述,但不能将它们理解为对本发明保护范围的限定。
46.实施例1
47.准备工作:
48.采用磁控溅射沉积技术,将mosi2靶(99.95%)和au靶(99.95%)固定在溅射靶材位置,距离衬底12cm处,其中mosi2靶材的直流电源的电流为0.5a,au靶材的射频电源的功率为10w,控制磁控溅射的压强为0.8pa,衬底不施加温度和偏压,薄膜制备过程中ar离子轰击靶材表面,同时控制氩气流量为80sccm。将样品进行力学和油摩擦磨损测试,样品在润滑油基础油pao4中,通过摩擦实验机测得制备薄膜的摩擦系数,收集摩擦后的磨屑和样品。
49.实验结果:
50.通过xrd(见图1)和hrtem(见图2)分析,图3为实施例2制备的薄膜材料的对应选区电子衍射图,证明所得到的mo
‑
si
‑
au薄膜结构为c40六方结构,并且xrd中没有观察到au的衍射峰,au以单原子的形式存在于mosi2晶格中。通过xps确定所制备的薄膜中mo原子的含量为30.6at.%,si原子为68.9at.%,au原子为0.5at.%。其硬度为13.4gpa,其断裂韧性为2.36mpa
·
m
1/2
,在油润滑条件下通过摩擦实验机测得其摩擦系数为0.11(见图6)。
51.实施例2
52.准备工作:
53.采用磁控溅射沉积技术,将mosi2靶(99.95%)和au靶(99.95%)固定在溅射靶材位置,距离衬底12cm处,其中mosi2靶材的直流电源的电流为0.5a,au靶材的射频电源的功率为15w,控制磁控溅射的压强为0.8pa,衬底不施加温度和偏压,薄膜制备过程中ar离子轰击靶材表面,同时控制氩气流量为80sccm。将样品进行力学和油摩擦磨损测试,样品在润滑油基础油pao4中,通过摩擦实验机测得制备薄膜的摩擦系数,收集摩擦后的磨屑和样品。
54.实验结果:
55.通过xrd(见图1)证明所得到的mo
‑
si
‑
au薄膜结构为c40六方结构,并且xrd中没有观察到au的衍射峰,au以单原子的形式存在于mosi2晶格中。通过xps确定所制备的薄膜中mo原子的含量为31.7at.%,si原子为67.5at.%,au原子为0.8at.%。其硬度为15.4gpa,其断裂韧性为2.55mpa
·
m
1/2
,在油润滑条件下通过摩擦实验机测得其摩擦系数为0.09(图6)。
56.实施例3
57.准备工作:
58.采用磁控溅射沉积技术,将mosi2靶(99.95%)和au靶(99.95%)固定在溅射靶材位置,距离衬底12cm处,其中mosi2靶材的直流电源的电流为0.5a,au靶材的射频电源的功率为20w,控制磁控溅射的压强为0.8pa,衬底不施加温度和偏压,薄膜制备过程中ar离子轰击靶材表面,同时控制氩气流量为80sccm。将样品进行力学和油摩擦磨损测试,样品在润滑油基础油pao4中,通过摩擦实验机测得制备薄膜的摩擦系数,收集摩擦后的磨屑和样品。
59.实验结果:
60.通过xrd(见图1)证明所得到的mo
‑
si
‑
au薄膜结构为c40六方结构,并且xrd中没有观察到au的衍射峰,au以单原子的形式存在于mosi2晶格中。通过xps确定所制备的薄膜中mo原子的含量为32.4at.%,si原子为66.1at.%,au原子为1.5at.%。其硬度为13.5gpa,其断裂韧性为2.47mpa
·
m
1/2
,在油润滑条件下通过摩擦实验机测得其摩擦系数为0.11(图6)。
61.实施例4
62.准备工作:
63.采用磁控溅射沉积技术,将mosi2靶(99.95%)和ag靶(99.95%)固定在溅射靶材位置,距离衬底12cm处,其中mosi2靶材的直流电源的电流为0.5a,ag靶材的射频电源的功率为15w,控制磁控溅射的压强为0.8pa,衬底不施加温度和偏压,薄膜制备过程中ar离子轰击靶材表面,同时控制氩气流量为80sccm。将样品进行力学和油摩擦磨损测试,样品在润滑油基础油pao4中,通过摩擦实验机测得制备薄膜的摩擦系数,收集摩擦后的磨屑和样品。
64.实验结果:
65.通过xrd和hrtem证明所得到的mo
‑
si
‑
ag薄膜结构为c40六方结构,并且xrd中没有观察到ag的衍射峰,ag以单原子的形式存在于mosi2晶格中。通过xps确定所制备的薄膜中mo原子的含量为32.3at.%,si原子为66.7at.%,ag原子为1.0at.%。其硬度为15.2gpa,其断裂韧性为2.49mpa
·
m
1/2
,在油润滑条件下通过摩擦实验机测得其摩擦系数为0.09。
66.对比例1
67.准备工作:
68.采用磁控溅射沉积技术,将mosi2靶(99.95%)和au靶(99.95%)固定在溅射靶材
位置,距离衬底12cm处,mosi2靶材直流电源的电流为0.5a,au靶材的射频电源的功率为0w,控制溅射压强为0.8pa,衬底不施加温度和偏压,薄膜制备过程中ar离子轰击靶材表面,同时控制氩气流量为80sccm。将样品进行力学和油摩擦磨损测试,样品在润滑油基础油pao4中,通过摩擦实验机测得制备薄膜的摩擦系数,收集摩擦后的磨屑和样品。
69.实验结果:
70.通过xrd和hrtem证明所得到的mosi2薄膜结构为c40六方结构。通过xps确定所制备的薄膜中mo原子的含量为33.3at.%,si原子为66.7at.%。其硬度为10.9gpa,其断裂韧性为2.10mpa
·
m
1/2
,在油润滑条件下通过摩擦实验机测得其摩擦系数为0.17(图6)。
71.对比例2
72.准备工作:
73.采用磁控溅射沉积技术,将mosi2靶(99.95%)和au靶(99.95%)固定在溅射靶材位置,距离衬底12cm处,其中mosi2靶材的直流电源的电流为0.5a,au靶材的射频电源的功率为50w,控制磁控溅射的压强为0.8pa,衬底不施加温度和偏压,薄膜制备过程中ar离子轰击靶材表面,同时控制氩气流量为80sccm。
74.实验结果:
75.通过xrd和hrtem(图4),图5为对比例2制备的薄膜材料的对应选区电子衍射图,证明所得到的mo
‑
si
‑
au薄膜结构为c40六方结构,在选区电子衍射对应的高分辨中观察到au(111)的衍射环说明au原子部分形成团从mosi2晶格中析出。xps分析得到mo原子的含量为34.6at.%,si原子为63.0at.%,au原子为2.4at.%。其硬度为9.9gpa,其断裂韧性为2.04mpa
·
m
1/2
,在油润滑条件下通过摩擦实验机测得的摩擦系数为0.14(图6)。
76.以上所述仅是本发明的优选实施方式,并非对本发明作任何形式上的限制。应当指出,对于本技术领域的普通技术人员来说,在不脱离本发明原理的前提下,还可以做出若干改进和润饰,这些改进和润饰也应视为本发明的保护范围。
再多了解一些
本文用于企业家、创业者技术爱好者查询,结果仅供参考。