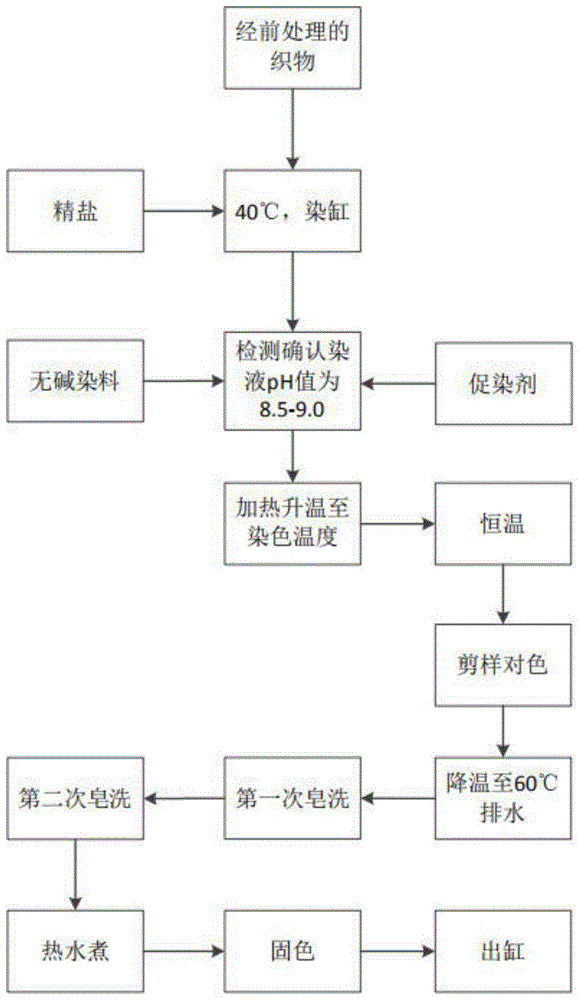
本发明涉及纺织品染色技术领域,尤其涉及一种省时环保的无碱染色工艺。
背景技术
为了提高棉质织物的固色效果,现有技术的染色工艺采用一盐三碱工艺,其中的盐需要分两次添加,添加两次盐后添加染色料,后续在染色料添加后的染色过程中还需要分三次添加纯碱,以保持染液的pH值为11左右,多次添加纯碱使得人机互动时间过长,且设备能耗高,存在工艺步骤繁多,排出的染液含有纯碱量大,废水处理的成本高的问题。
技术实现要素:
本发明提出了一种省时环保的无碱染色工艺,具有步骤简单、染色用时短、环保节能的优点,解决了现有技术的棉质织物的染色工艺步骤繁多,染色时间过长、能耗高和废水处理的成本高的技术问题。
为达此目的,本发明采用以下技术方案:
一种省时环保的无碱染色工艺,用于棉质织物的染色,包括以下步骤:
S1)在装有自来水的染缸中加入精盐,溶解并搅拌均匀后,再将经前处理的织物浸没在所述染缸的液体里;
S2)加入染色料,然后再加入促染剂,并通过调整所述促染剂的加入量使含有所述染色料的染液的pH值符合设定范围值,使得所述染液呈弱碱性;
S3)对所述染液进行加热,使所述染液的温度达到染色温度,使所述染液保持恒温;
S4)使所述染液的温度降低至60℃,然后将所述染缸中的所述染液排出,再依次对所述织物进行第一次皂洗、第二次皂洗、热水煮和固色步骤后出缸,完成对所述织物的染色。
进一步的,步骤S2)中,所述促染剂为非离子型表面活性剂,并且所述促染剂为含有环氧乙烷官能团的化合物;
所述染色料为无碱活性染色料,所述染色料为含有端羟基活性基团的化合物。
具体的,步骤S2)中,所述促染剂的原液的pH值为8.0。
具体的,所述染液的pH值的设定范围值为8.5-9.0;所述染液中的所述促染剂的添加量为2.8-3.3g/L。
优选的,步骤S3)中,所述染色温度为80-84℃,恒温时间为40min。
优选的,步骤S1)中,所述自来水的水温为40℃;所述精盐的添加量为135-150g/L。
优选的,步骤S3)中,加热的升温速度为2℃/min;
步骤S4)中,降温的温度下降的速度为1.5℃/min。
可选的,步骤S4)中,排出所述染液前还包括对所述织物进行剪样对色的步骤。
进一步的,经步骤S1)至S4)染色后的所述织物的耐水色牢度为3-4级。
优选的,步骤S2)中,染色料的添加量为0.2-4owf%。
本发明的技术方案的有益效果为:所述的省时环保的无碱染色工艺,染色过程中无需添加纯碱,操作步骤简单,时间短且能耗低,排出的染液不含纯碱,COD指标不超过800mg/L,染液废水处理的成本相对较低,相对采用纯碱的染色工艺更为环保。
附图说明
图1是本发明一个实施例的工艺流程图。
具体实施方式
在本说明书的描述中,参考术语“实施例”、“示例”等的描述意指结合该实施例或示例描述的具体特征、结构、材料或者特点包含于本发明的至少一个实施例或示例中。在本说明书中,对上述术语的示意性表述不一定指的是相同的实施例或示例。而且,描述的具体特征、结构、材料或者特点可以在任何的一个或多个实施例或示例中以合适的方式结合。
尽管已经示出和描述了本发明的实施例,本领域的普通技术人员可以理解:在不脱离本发明的原理和宗旨的情况下可以对这些实施例进行多种变化、修改、替换和变型,本发明的范围由权利要求及其等同物限定。
下面结合附图1及具体实施方式进一步说明本发明的技术方案。
一种省时环保的无碱染色工艺,用于棉质织物的染色,包括以下步骤:
S1)在装有自来水的染缸中加入精盐,溶解并搅拌均匀后,再将经前处理的织物浸没在所述染缸的液体里;
S2)加入染色料,然后再加入促染剂,并通过调整所述促染剂的加入量使含有所述染色料的染液的pH值符合设定范围值,使得所述染液呈弱碱性;
S3)对所述染液进行加热,使所述染液的温度达到染色温度,使所述染液保持恒温;
S4)使所述染液的温度降低至60℃,然后将所述染缸中的所述染液排出,再依次对所述织物进行第一次皂洗、第二次皂洗、热水煮和固色步骤后出缸,完成对所述织物的染色。
为了提高棉质织物的固色效果,现有技术的染色工艺采用一盐三碱工艺,其中的盐需要分两次添加,添加两次盐后添加染色料,后续在染色料添加后的染色过程中还需要分三次添加纯碱,以保持染液的pH值为11左右,多次添加纯碱使得人机互动时间过长,且设备能耗高,存在工艺步骤繁多,排出的染液含有纯碱量大,废水处理的成本高的问题。
本发明的所述省时环保的无碱染色工艺,通过添加促染剂使染液呈弱碱性,从而可免去染色过程中添加纯碱的需要,染色料与促染剂发生化学反应可提高染色的效果和色牢度,操作步骤简单,染色用时短且能耗低,排出的染液不含纯碱,COD指标不超过800mg/L,染液废水处理的成本相对较低,相对采用纯碱的染色工艺更为环保。
步骤S1中,所述的前处理包括现有技术的退浆、煮炼、漂白、丝光和烧毛环节。其中,步骤S4)中的第一次皂洗、第二次皂洗、热水煮和固色步骤为现有技术的后处理工艺。
进一步的,步骤S2)中,所述促染剂为非离子型表面活性剂,并且所述促染剂为含有环氧乙烷官能团的化合物;
所述染色料为无碱活性染色料,所述染色料为含有端羟基活性基团的化合物。
环氧乙烷官能团,含有张力较大的三元环,在80-84℃的温度下以及弱碱条件下,含有亲核的端羟基活性基团的染色料可与含有环氧乙烷官能团的促染剂发生开环反应,从而形成稳定的含醚键,可提高染色料在织物表面的附着力,进而提高织物的耐水色牢度。其化学反应式如下:
具体的,所述促染剂的原液的pH值为8.0。
促染剂的原液的pH值为8.0,可通过增加所述染色料的添加量,使染液的pH值提高,有利于提高促染剂与染色料的化学反应的充分性,保障固色效果。
具体的,步骤S2)中,所述染液的pH值的设定范围值为8.5-9.0;所述染液中的所述促染剂的添加量为2.8-3.3g/L。
检测发现现有供应的自来水的pH值为6.5-7.8之间,在添加促染剂之前的染缸中的自来水的初始pH值与8.5-9.0的设定范围值的差距较小,只要按照2.8-3.3g/L的添加量即可控制所述染液的pH值满足8.5-9.0的要求,通过测定pH来限制促染剂的用量,更为环保,如果所述促染剂的添加量过少,则难以使得所述染液形成pH值为8.5-9.0的弱碱的环境,容易影响所述促染剂与所述染色料的反应效果,如果所述促染剂的添加量过多,则使得染液的碱性过强,提高了后续废水处理的成本。
优选的,步骤S3)中,所述染色温度为80-84℃,恒温时间为40min。
在80-84℃的温度条件下,所述促染剂与染色料的染色效果较好,染色制品的色牢度更高;如果染色温度低于80℃,则染色效果欠佳,如果染色温度高于85℃,则容易导致促染剂分解,影响了织物的固色效果。
具体的,步骤S1)中,所述自来水的水温为40℃;所述精盐的添加量为135-150g/L。
精盐可降低纤维染色过程中的电荷效应,从而提高染色料的上染率。精盐的使用量是根据染色料用量来决定,颜色越深染色料的用量越大,相应的精盐的用量也越大,例如实施例中的染色要求为黑色,精盐的用料为140g/L。
具体的,步骤S3)中,加热的升温速度为2℃/min;
步骤S4)中,降温的温度下降的速度为1.5℃/min。
步骤S3)的加热升温和步骤S4的降温的速度都不宜过快,以避免因染液的温度不均匀,导致出现染色织物出现色斑或者色泽不均匀的问题。
进一步的,步骤S4)中,排出所述染液前还包括对所述织物进行剪样对色的步骤。
通过剪样对色确认经染色的织物与客户提供的色板的颜色和色深是否吻合。
进一步的,经步骤S1)至S4)染色后的所述织物的耐水色牢度为3-4级。
本发明经染色后的所述织物的表面无色渍,本发明的染色织物的耐水色牢度根据《GB/T 5713-2013纺织品色牢度试验耐水色牢度》标准检测,耐水色牢度为3-4级,且pH值为4.5-8.5之间的纺织产品属于《GB 18401-2010国家纺织产品基本安全规范》的A类或B类产品,可用于直接与皮肤接触的衣物。
优选的,步骤S2)中,染色料的添加量为0.2-4owf%。
具体可根据客户的提供的样品颜色选择染色料或者不同染色料的组合,在保障染色效果的前提下,各染色料的添加量控制在0.2-4owf%范围内,以降低废水的处理成本。
实施例1至5和对比例1至5
1、以26S双纱平纹棉布为待染色的织物,以表1和表2对应所列的原料成分、工艺参数和检测结果,根据以下步骤进行各实施例和各对比例的织物的染色处理:
S1)在装有水温为40℃的自来水的染缸中加入精盐,溶解并搅拌均匀后,再将经前处理的织物浸没在所述染缸的液体里;
S2)加入染色料,然后再加入促染剂(选用佛山宇丰染料有限公司生产的促染剂2020),并通过调整所述促染剂的加入量使含有所述染色料的染液的pH值符合设定范围值;
S3)以2℃/min的加热速度对所述染液加热,使所述染液的温度达到染色温度,使所述染液保持恒温40min;
S4)以1.5℃/min的降温速度使所述染液的温度降低至60℃,然后将所述染缸中的所述染液排出,再依次对所述织物进行第一次皂洗、第二次皂洗、热水煮和固色步骤后出缸,即完成所述织物的染色;
其中,步骤S2)中,所述染色料为非离子型表面活性剂,并且所述染色料含有环氧乙烷官能团;所述染色料为无碱活性染色料,所述染色料含有端羟基活性基团;所述促染剂的原液的pH值为8.0。
2、根据《GB/T 5713-2013纺织品 色牢度试验 耐水色牢度》标准检测各个实施例或对比例的染色织物的耐水色牢度,以及染色后排出的染液的COD指标。
表1 各实施例的有关数据和检测结果
表2 各对比例的有关数据和检测结果
根据以上表1和表2的数据分析说明如下:
1、对比例1采用的现有技术的一盐三碱染色工艺,制得的染色织物的耐水色牢度为3.1,染色后排出的染液的COD指标为1045mg/L。
2、实施例1-5的染色织物的耐水色牢度为3、3-4或4级,均不低于对比例1的3级的耐水色牢度;且实施例1-5的耐水色牢度均可达到《GB/T 5713-2013纺织品色牢度试验耐水色牢度》标准的耐水色牢度为3-4级的要求,只要制品织物的pH值保持在4.0-8.5的范围内,即属于A类或B类产品,可用于直接与皮肤接触的衣物,说明本发明的技术方案是有效的。
3、实施例1-5的染色后排出的染液的COD指标为735-783mg/L,相比对比例1的1045mg/L的COD指标,实施例1-5的更为环保。
4、对比例2和对比例3与实施例3相比的不同之处在于:染色温度不同,对比例2和对比例3的染色温度分别为76℃和88℃,对比例2的染色温度过低,对比例3的染色温度过高,超出了80-84℃的范围,染色温度低于80℃,效果欠佳,染色温度高于85℃,促染剂容易分解,导致对比例2和对比例3的耐水色牢度均为2-3级,达不到客户的质量要求。
5、对比例4与实施例3相比的不同之处在于:促染剂的添加量不同,对比例4的促染剂的添加量为3.5g/L,超过了促染剂添加量为2.8-3.3g/L的范围值的上限值,导致对比例4的染液的pH值超过了9.0的上限达到了9.3,但是对比例4的耐水色牢度为3-4级,并没有比实施例3的有明显的提高,而且也没有高于实施例5为4级的耐水色牢度值,故此,促染剂添加量设定为2.8-3.3g/L是合理的,添加量超过上限值没有明显的效果;并且,由于添加过多的促染剂,导致染液的pH增高,还导致染色后的废液的COD指标增高,因此,不仅增加的原料成本,还增加了后续的排污处理成本。
6、对比例5与实施例3相比的不同之处在于:对比例5的促染剂的添加量较少,对比例5的促染剂的添加量为2.5g/L,低于促染剂添加量为2.8-3.3g/L的范围值的下限值,导致对比例5的染液的pH值低于8.5的上限只有8.2,而对比例5的耐水色牢度为2-3级,不能满足客户的质量要求,故此,促染剂添加量设定为2.8-3.3g/L是合理的。
综上所述,工艺流程图如图1所示的本发明的上述实施例,所述的省时环保的无碱染色工艺,染色过程中无需添加纯碱,操作步骤简单,时间短且能耗低,排出的染液不含纯碱,COD指标不超过800mg/L,废水处理的成本相对较低,相对采用纯碱的染色工艺更为环保。
在本说明书的描述中,参考术语“一个实施例”、“一些实施例”、“示意性实施例”、“示例”、“具体示例”、或“一些示例”等的描述意指结合该实施例或示例描述的具体特征、结构、材料或者特点包含于本发明的至少一个实施例或示例中。在本说明书中,对上述术语的示意性表述不一定指的是相同的实施例或示例。而且,描述的具体特征、结构、材料或者特点可以在任何的一个或多个实施例或示例中以合适的方式结合。
尽管已经示出和描述了本发明的实施例,本领域的普通技术人员可以理解:在不脱离本发明的原理和宗旨的情况下可以对这些实施例进行多种变化、修改、替换和变型,本发明的范围由权利要求及其等同物限定。
以上结合具体实施例描述了本发明的技术原理。这些描述只是为了解释本发明的原理;而不能以任何方式解释为对本发明保护范围的限制。基于此处的解释;本领域的技术人员不需要付出创造性的劳动即可联想到本发明的其它具体实施方式;这些方式都将落入本发明的保护范围之内。
本文用于企业家、创业者技术爱好者查询,结果仅供参考。