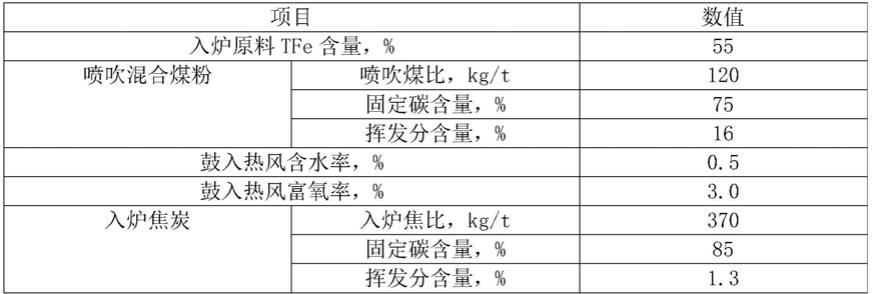
1.本发明涉及钢铁工业中炼铁技术领域,特别涉及大型高炉炉料直接还原率及其确定入炉焦比的计算方法。
背景技术:
2.作为当今世界生铁制造的主流工艺,高炉对于炼铁生产的重要性是不言而喻的,即表现为炼钢制造所用的铁水原料中,90%以上是来源于高炉工艺所生产。而高炉工艺对比其它炼铁工艺的优势,可以说是主要体现在如下几个方面:一是原燃料用料广泛,并且适应性强,甚至在某些外界制约条件下,可以使用较为劣质的原燃料,进行高炉日常生产;二是加工制造成本低,经过权威统计表明,高炉制造铁水工艺的成本,是先进所有存在炼铁工艺中成本最低的,使得企业能够在市场中获得较好得竞争性;三是热利用效率最高,作为世界上最大的单体容器,并且具有最高得热利用效率,使得其能够以最少得能源消耗数量,实现生铁加工制造,对于社会资源和环境保护具有重要意义;四是装备简单、一次性投资成本较低,且易于维护,工艺运行作业率与稳定率高;五是自控水平、监控手段丰富,使得炼铁操作者操作简便,同时劳动效率高,单人吨铁生产能力远远高炉其它工艺,而以上诸多优点所在,使得高炉在目前炼铁生产众多工艺中,地位仍是不可动摇的。而对于今天不同冶金企业的高炉炼铁生产来讲,冶炼工作者最为关注的核心问题之一,还是燃料消耗数量的多少,因为其与企业的运营成本息息相关。虽然高炉大型化、自控化的水平不断攀升,燃料消耗数量不断下降,但对于适合燃料消耗数量的确定,仍还是以经验为主,即表现在生产中,就是人为的来设定入炉焦炭和喷吹煤粉数量,从而组织日常生产。而在高炉所用燃料结构中,焦炭是占据着主体地位,其消耗数量的多少,直接决定燃料消耗数量与炼铁加工制造成本。而对于高炉冶炼过程来讲,入炉焦炭在炉内的消耗过程主要由以下两个过程所决定:首先,就是入炉焦炭中的碳与炉料中的氧所进行的直接还原反应,而在这一过程中,会消耗掉一定数量的焦炭;再有就是焦炭与下部热风混合后所产生的还原性气体,而这些还原性气体再与炉料所发生的间接还原反应,再消耗掉一定数量的焦炭,从而才能够完成高炉炉内的冶炼过程。但在这里需要说明的是,由于炉内冶炼进程中,所产生的还原性气体,具有较好的流动性,其反应进程也是优先于直接还原反应,因此说来,炼铁生产者是希望炉内间接还原比例多一些,直接还原能够少一些。为此,也就需要了解不同有效炉容下,不同原燃料和运行条件下的炉内间接还原比例与直接还原比例情况,并以此作为依据,分析出不同有效炉容高炉运行过程中的改进之处,如喷吹煤量控制水平,入炉焦炭消耗数量等等,从从而能够更加优化高炉生产,降低生铁冶炼成本。
3.而在日常生产过程中,炉料还原效率的好坏,还原进程的速率,对于高炉获得良好生产指标是具有重要意义的。因此无论是钢铁企业,还是外部院校研究机构,都对此十分重视,也纷纷采取措施,并从企业的实际出发,来改善高炉运行状态,如通过改进原燃料质量、炉体装备水平、改善外部辅助运行条件等不同举措,来改善高炉冶炼进程,提升高炉自身冶炼效率,从而实现低耗、高效化生产。在这里需要说明的是,随着装备技术、自控技术、监控
技术等进步,今天高炉的冶炼特点,较过去有了较大的区别,显著不同之一的就是喷吹煤量大幅度提升、入炉焦炭数量有较大程度减少,这也是高炉经济性的优势所在,与此同时,随着喷吹煤粉数量的增加、入炉焦炭数量的减少,也带来了炉内的冶炼进程较过去有较大变化,如炉料的直接还原比例和间接还原比例情况发生很大变化。现实来看,作为大型黑箱操作体容器的高炉,在炉内冶炼进程中,气、固、液三相共存,物理和化学反应过程及其复杂,因此,在这种复杂条件下,如何确定出不同运行条件下的炉内间接还原与直接还原比例,是困恼冶金工作者的一个难题之一。鉴于了解炉内还原反应进程的重要性,还是需要对此进行必要分析,以此作为指导高炉操作的依据。大部分企业,针对此类问题的判断,还是离不开如下几种方法措施,一是传统经验法,就是依据燃料消耗数量及结构种类,并结合高炉实际运行状态,人为的进行间接还原与直接还原比例判定;再有还有就是采用实验室和中试设备进行试验分析,依托实验室下可视化结果和所收集到的数据等等,来分析不同炉料在炉内的反应进程,以此来分析间接还原比例和直接还原比例。还有就是采用数值模拟技术,通过输入部分参数,并结合计算机仿真模拟,进行此类问题的解决,这目前也是比较新颖和前沿的技术方向之一。但这里还是需要指出的是,无论是采取何种判断方法作为炉内反应进行的依据,现实来看,都还是有其不完善之处的,如准确性、及时性以及实用差等缺点,因此,还是需要在炉内复杂的反应进程下,寻找出一种可靠且可实施的方法,分析出间接还原与直接还原所占比例,来真实掌握炉内炉料运行状态,从而找出高炉炉况需要改进之处,借此来实现入炉焦比数量的确定,从而实现低耗、高效化的生产。
4.而对于现炼炼铁工艺来说,实现炉内炉料较好的还原效果,是高炉冶炼工作者的第一任务,为此,就需要获得炉内适合的间接还原比例和直接还原比例,从而实现低燃料消耗下的高效冶炼。为此,就需要找出一种方法,来分析出炉内炉料间接和直接还原所占份额,而面对这个问题,不少国内外冶金企业和相关院校研究机构,也纷纷开展此方面工作,力图从不同角度来做到改善高炉运行状态,如通过采取外部措施,来改善炉内间接还原,降低直接还原效果的技术(见中国环利“强化高炉间接还原的方法及其专用气的制造方法”专利申请号:cn101818218a,“一种强化高炉间接还原的方法及其专用气的制造方法”专利申请号:cn101812555a,“处理金属矿石的方法和金属生产用的高炉”专利申请号:cn105793442b,“一种高炉配加高反应性焦炭后能量利用”专利申请号:cn102952910b等等),此类技术,通过采取不同的炉外或者炉内增加还原气体等措施,从而实现炉料间接还原比例的增加,来提高高炉的间接还原段的还原度,降低直接还原度,改善炉内运行环境,以最终实现低耗高产的效果。通过实施这些技术手段及措施,无论是从理论上,还是实际应用中,是可以实现炉内还原比例增加的,降低直接还原度,对于高炉生产是有一定益处的,但在这里需要指出的是,此类发明创造,仅仅给出增加还原比例的方法,但对于如何确定炉内间接还原和直接还原的份额,并未有所提及。还有就是一些计算性方法之类的新颖技术(见中国专利“高反应性焦炭下高炉直接还原度及煤气利用率的计算方法”专利申请号:cn102876823a,“一种高炉co利用率影响因素分析方法及系统”专利申请号:cn108009343a,“一种高炉冶炼水平分析系统”专利申请号:cn104313213b,“一种预测高炉煤气利用率的方法”专利申请号:cn102703627b等等),此类计算方法,是针对冶炼工艺遇到的不同问题,通过各种监测到的数据,采取的计算性解决方案,这类计算对于找寻冶炼过程中存在的问题,是具有重要意义,但这里也需要明确的是,指导本发明创造之前,还是未能够查询到与直接
还原有关的计算性方法。再有就是就是一些通过其它改善炉内运行状态的冶金技术(见中国专利“大型高炉分粒级矿焦混合装料方法”专利申请号:cn105803142b,“使还原过程的设计和操作最佳化的方法”专利申请号:cn1318610c,“一种高炉喷吹工艺”专利申请号:cn102643937a,“一种高炉全球团冶炼工艺”专利申请号:cn106119449b,“一种高炉冶炼炉料及高炉冶炼方法”专利申请号:cn107586903a,“一种合理使用多粒级烧结矿的高炉布料调节方法”专利申请号:cn110331244等等),此类发明创造的实施,通过采取优化工艺,改进原燃料结构,同时辅助以改进上下部调剂手段、优化炉顶布料等手段措施,实现高炉过程的冶炼效果改善,从而达到降低能耗,实现较好炉况运行的效果,且目前也广泛应用于不同企业的不同高炉,但这里还是要指出的是,此类措施虽有较好效果,但是其内容和方法上与炉内直接还原度的分析,并无关系。此外就是一些国内外可查阅到的文献资料(见期刊《武钢技术》“武钢高炉直接还原度及碳熔损率的计算与分析”2015年,53卷,4期,5
‑
8;《南方金属》“邯钢5号高炉直接还原度分析与计算”2014年,6期,59
‑
61;《钢铁钒钛》“低品位矿高炉碳消耗与铁直接还原度关系探究”2018年,39卷,1期,92
‑
95;《钢铁研究》“低品位复杂矿高炉直接还原度影响因素研究”2014年,46卷,6期10
‑
12等),此类文献资料针对炉内的不同的炉料反应过程等进行了详尽的论述,并对不同反应规律进行总结分析,并且有所提及炉内直接还原度的计算与分析,但此类文献中,所提及到的炉内直接还原度计算过程过于冗余复杂,准确性有待商榷,同时其也未能够给出入炉焦炭的控制水平建议。从以上可查询到的技术资料上来看,对于炉内炉料直接还原率和适合适的入炉焦比数量的判断,对于冶炼工作者来讲,仍然还是一个悬而未决的问题。
5.而本发明创造,是在实验室理论研究和工业长期生产实践基础上,是依据大型高炉冶炼过程中与炉料直接还原相关运行参数,来分析出炉内炉料直接还原率的计算方法,而在采用此技术后,通过分析不同有效炉容大型高炉,在不同运行参数条件下,从而得出炉内炉料直接还原率,可实现分析出不同有效炉容高炉运行过程中的改进之处,如入炉焦炭数量控制水平等,从而实现高炉低耗高效化冶炼。
技术实现要素:
6.本发明所要解决的技术问题是提供一种(),实现高炉低耗、高效化冶炼。
7.为实现上述目的,本发明采用以下技术方案实现:
8.大型高炉炉料直接还原率的计算方法,按公式(1)计算炉内炉料直接还原率:
[0009][0010]
公式中符号:
[0011]
drr为炉内炉料直接还原率,%;
[0012]
r
coke
为高炉入炉焦比,kg/t;
[0013]
k
c
为入炉焦炭固定碳含量,%;
[0014]
k
v
为入炉焦炭挥发分含量,%;
[0015]
tfe为入炉原料铁元素质量百分含量,%;
[0016]
pci为高炉喷吹煤比,kg/t;
[0017]
c
c
为喷吹混合煤粉固定碳含量,%;
[0018]
c
v
为喷吹混合煤粉挥发分含量,%;
[0019]
为鼓入热风含水率,%;
[0020]
为鼓入热风富氧率,%;
[0021]
h1为系数,取值为0.15;h2为系数,取值为0.31;h3为系数,取值为0.42;h4为系数,取值为4.75;h5为系数,取值为0.37;
[0022]
η1为量纲修正系数,取值为1.25,t/kg;η2为量纲修正系数,取值为0.92,t/kg;
[0023]
大型高炉的有效炉容适用范围为2000m3~6000m3;
[0024]
高炉入炉焦比范围为200kg/t~500kg/t;
[0025]
固定碳含量的范围为75%~95%;
[0026]
挥发分含量的范围为0.8%~6%;
[0027]
入炉原料中铁元素质量百分含量范围为45%~65%;
[0028]
高炉喷吹煤比范围为80kg/t~250kg/t,入炉焦炭中固定碳含量为50%~80%,入炉焦炭中挥发分含量范围为6%~40%;
[0029]
鼓入热风中的含水率范围为0.1%~2%;
[0030]
鼓入热风中的富氧率范围为0%~10%。
[0031]
大型高炉炉料直接还原率确定入炉焦比的计算方法,按公式(2)确定高炉入炉焦比的修正量,对高炉生产过程中入炉焦炭数量进行修订;
[0032][0033]
公式中符号:
[0034]
为高炉入炉焦比的修正量,kg/t;
[0035]
k1为量纲修正系数,取值为148.45,kg/t;
[0036]
λ1为系数,取值为5.77。
[0037]
与现有的技术相比,本发明的有益效果是:
[0038]
本技术通过分析不同有效炉容大型高炉,在不同运行参数条件下,从而得出炉内炉料直接还原率,分析出高炉适宜的入炉焦比控制水平,从而实现高炉低耗高效化冶炼。
具体实施方式
[0039]
下面结合实施例对本发明进一步说明:
[0040]
以下实施例对本发明进行详细描述。这些实施例仅是对本发明的最佳实施方案进行描述,并不对本发明的范围进行限制。
[0041]
实施例1(某钢铁厂有效炉容2580m3高炉应用为例说明)
[0042]
2580m3高炉相关运行参数详见表1。
[0043]
表1:2580m3高炉运行相关参数
[0044][0045]
还原率计算结果
[0046]
依据有效炉容2580m3高炉冶炼过程中与炉料直接还原相关运行参数,通过数学关系式(1),来实现高炉冶炼过程中直接还原情况的分析,分析结果见表2。
[0047]
表2:2580m3高炉炉内炉料直接还原率
[0048]
项目数值炉内炉料直接还原率drr,%51.72
[0049]
修正入炉焦比
[0050]
在分析出的炉内炉料直接还原率基础上,采用如上数学关系式(2),来实现高炉适合入炉焦比,的修正,入炉焦比的修正量见表3。
[0051]
表3:2580m3高炉入炉焦比的修正量
[0052]
项目数值高炉入炉焦比的修正量,kg/t348.29
[0053]
高炉取得效果
[0054]
2580m3高炉采用此技术后的应用效果见表4。
[0055]
表4:2580m3高炉应用效果
[0056]
项目入炉焦比,kg/t日产量,吨吨铁成本,元/吨实施前37058002200实施后348.2959502170效果
‑
21.71 150
‑
30
[0057]
通过分析出炉内炉料的直接还原率基础上,实现了适宜入炉焦炭数量的确定,此技术在2580m3高炉实施后,达到了降低入炉焦比21.71kg/t,日产量增加150吨,节约吨铁炼铁生产成本30元的良好运行效果,实现高炉低耗高效生产的目的。
[0058]
实施例2(某钢铁厂有效炉容3200m3高炉应用为例说明)
[0059]
高炉相关运行参数
[0060]
炉容3200m3高炉相关运行参数详见表5。
[0061]
表5炉容3200m3高炉运行相关参数
[0062][0063]
还原率计算结果
[0064]
依据有效炉容3200m3高炉冶炼过程中与炉料直接还原相关运行参数,采用入炉焦炭、入炉原料、喷吹煤粉、鼓入热风、富氧率等具体运行参数,通过数学关系式(1),来实现高炉冶炼过程中直接还原情况的分析,分析结果见表6。
[0065]
表6有效炉容3200m3高炉炉内炉料直接还原率
[0066]
项目数值炉内炉料直接还原率(注:drr),%44.36
[0067]
适宜入炉焦比数量
[0068]
在应用如上技术方案计算后,在分析出的炉内炉料直接还原率基础上,采用如上数学关系式(2),来实现高炉适合入炉焦比的分析,来进行入炉焦炭数量的确定,入炉焦比的修正量见表7。
[0069]
表7有效炉容3200m3高炉入炉焦比的修正量
[0070]
项目数值入炉焦比的修正量,kg/t308.99
[0071]
2.4高炉取得效果
[0072]
有效炉容3200m3高炉采用此技术后的应用效果见表8。
[0073]
表8炉容3200m3高炉应用效果
[0074]
项目入炉焦比,kg/t日产量,吨吨铁成本,元/吨实施前32077002100实施后308.9978002080效果
‑
11.01 200
‑
30
[0075]
通过分析出炉内炉料的直接还原率基础上,实现了入炉焦炭数量的确定,此技术在3200m3高炉实施后,达到了降低入炉焦比比
‑
11.01g/t,日产量增加100吨,节约吨铁炼铁生产成本20元的良好运行效果,实现高炉低耗高效生产的目的。
[0076]
实施例3(某钢铁厂有效炉容4038m3高炉应用为例说明)
[0077]
炉容4038m3高炉相关运行参数详见表9。
[0078]
表9炉容4038m3高炉运行相关参数
[0079][0080]
高炉炉内炉料直接还原率计算结果
[0081]
依据有效炉容4038m3高炉冶炼过程中与炉料直接还原相关运行参数,采用入炉焦炭、入炉原料、喷吹煤粉、鼓入热风、富氧率等具体运行参数,通过数学关系式(1),来实现高炉冶炼过程中直接还原情况的分析,分析结果见表10。
[0082]
表10有效炉容4038m3高炉炉内炉料直接还原率
[0083]
项目数值炉内炉料间接还原率drr,%41.71
[0084]
入炉焦比的修正量
[0085]
在应用如上技术方案计算后,在分析出的炉内炉料直接还原率基础上,采用如上数学关系式(2),来实现高炉适合入炉焦比的分析,来进行入炉焦炭数量的确定,入炉焦炭数量见表11。
[0086]
表11有效炉容4038m3高炉入炉焦比的修正量
[0087]
项目数值入炉焦比的修正量,kg/t294.50
[0088]
高炉取得效果
[0089]
4038m3高炉采用此技术后的应用效果见表12。
[0090]
表12有效炉容4038m3高炉应用效果
[0091]
项目入炉焦比,kg/t日产量,吨吨铁成本,元/吨实施前28094002050实施后294.5095002030效果 14.50 100
‑
50
[0092]
通过分析出炉内炉料的直接还原率基础上,实现了适宜入炉焦炭数量的确定,此技术在4038m3高炉实施后,采取适度提升入炉焦比14.50kg/t,稳定炉况,可实现日产量增加100吨,节约吨铁炼铁生产成本20元的良好运行效果,实现高炉低耗高效生产的目的。
[0093]
实施例4(某钢铁厂有效炉容4747m3高炉应用为例说明)
[0094]
效炉容4747m3高炉相关运行参数详见表13。
[0095]
表13效炉容4747m3高炉运行相关参数
[0096][0097]
高炉炉内炉料直接还原率计算结果
[0098]
依据有效炉容4747m3高炉冶炼过程中与炉料直接还原相关运行参数,采用入炉焦炭、入炉原料、喷吹煤粉、鼓入热风、富氧率等具体运行参数,通过数学关系式(1),来实现高炉冶炼过程直接还原情况的分析,分析结果见表14。
[0099]
表14有效炉容4747m3高炉炉内炉料直接还原率
[0100]
项目数值炉内炉料直接还原率(注:drr),%44.41
[0101]
入炉焦比的修正量
[0102]
在应用如上技术方案计算后,在分析出的炉内炉料直接还原率基础上,采用如上数学关系式(2),来实现高炉适合入炉焦比的分析,来进行入炉焦炭数量的确定,入炉焦炭数量见表15。
[0103]
表15有效炉容4747m3高炉入炉焦比的修正量
[0104]
项目数值入炉焦比的修正量,kg/t309.24
[0105]
高炉取得效果
[0106]
4747m3高炉采用此技术后的应用效果见表16。
[0107]
表16高炉应用效果
[0108]
项目入炉焦比,kg/t日产量,吨吨铁成本,元/吨实施前330103002000实施后309.24104501970效果
‑
20.76 150
‑
30
[0109]
通过分析出炉内炉料的直接还原率基础上,实现了适宜入炉焦炭的确定,此技术在4747m3高炉实施后,达到了降低入炉焦比比20.76kg/t,日产量增加150吨,节约吨铁炼铁生产成本30元的良好运行效果,实现高炉低耗高效生产的目的。
[0110]
实施例5(某钢铁厂有效炉容5500m3高炉应用为例说明)
[0111]
有效炉容5500m3高炉相关运行参数详见表17。
[0112]
表17有效炉容5500m3高炉运行相关参数
[0113][0114]
有效炉容5500m3高炉炉内炉料直接还原率计算结果
[0115]
依据有效炉容5500m3高炉冶炼过程中与炉料直接还原相关运行参数,采用入炉焦炭、入炉原料、喷吹煤粉、鼓入热风、富氧率等具体运行参数,通过数学关系式(1),来实现高炉冶炼过程中直接还原情况的分析,分析结果见表18。
[0116]
表18有效炉容5500m3高炉炉内炉料直接还原率
[0117]
项目数值炉内炉料直接还原率(注:drr),%44.81
[0118]
有效炉容5500m3高炉入炉焦比的修正量
[0119]
在应用如上技术方案计算后,在分析出的炉内炉料直接还原率基础上,采用如上数学关系式(2),来实现高炉适合入炉焦比的分析,来进行入炉焦炭数量的确定,入炉焦炭数量见表表19。
[0120]
表19有效炉容5500m3高炉入炉焦比的修正量
[0121]
项目数值入炉焦比的修正量,kg/t311.42
[0122]
高炉取得效果
[0123]
5500m3高炉采用此技术后的应用效果见表20。
[0124]
表20高炉应用效果
[0125]
项目入炉焦比,kg/t日产量,吨吨铁成本,元/吨实施前310120001950实施后311.42121001940效果
‑
1.42 100
‑
10
[0126]
通过分析出炉内炉料的直接还原率基础上,实现了适宜入炉焦比数量的确定,此技术在5500m3高炉实施后,采取适度提升入炉焦比1.42kg/t,稳定炉况,日产量增加100吨,节约吨铁炼铁生产成本10元的良好运行效果,实现高炉低耗高效生产的目的。
再多了解一些
本文用于企业家、创业者技术爱好者查询,结果仅供参考。