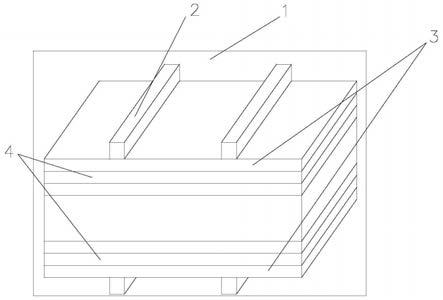
1.本发明涉及一种异质结光伏电池栅线电极制作方法。
背景技术:
2.相比于传统的太阳能晶硅电池结构,利用非晶硅薄膜与单晶硅衬底异质结结 构的异质结电池结合了单晶硅与非晶硅电池的优点,主要表现在:
3.1)效率提升潜力高。异质结电池采用的n型硅片,具有较高的少子寿命, 非晶硅钝化的对称结构也可以获得较低的表面复合速率,因而硅异质结 太阳电池的开路电压远高于传统单晶硅太阳电池,其效率潜力比当前使 用p型硅片的perc电池要高1.5%~2%。
4.2)异质结电池拥有更大的降成本空间。异质结电池结合了薄膜太阳能电池 低温的制造优点,整个工艺环节的温度一般在200℃左右,而传统的高 温扩散工艺形成pn结的温度在900℃以上。避免了传统的高温工艺, 不仅大大的节约燃料能源,而且低温加工环境实现了异质结电池薄片化, 减少硅的使用量,降低硅原料成本。
5.另外,异质结工艺流程相对简化,全部生产流程只需四步即可完成,而 perc为了实现23.9%的转化效率,需要叠加多种技术,工艺步骤多达 8步,由此带来了更高的成本。
6.3)具有更高的双面率。异质结电池的双面对称结构,正面和背面基本无颜 色差异,封装制备成双面电池组件之后,可以获得10%以上的年发电 量增益,而且其双面率(电池背面效率与正面效率之比)已经达到95%
7.4)低温度系数,稳定性高可有效降低热损失。太阳能电池的光电转换效率 一般是在25℃的条件下测试的,但实际使用时,由于日照原因工作温 度显然会高出,高温下的性能表现尤为重要。异质结组件的温度系数 (0.258%)小于常规p型电池的温度系数(0.46%),异质结电池组件 功率损失明显小于常规晶硅组件。
8.5)具有更低的光致衰减。p型组件通常会发生光致衰减现象,主要是由于 以“硼”为主要参杂元素的p型硅片会出现硼氧复合体,降低电池少子 寿命,产生光致衰减的困扰。而异质结电池的n型硅片以“磷”为主 要参杂元素,不存在硼氧复合因子,根除了初始光衰的可能性,衰减速 度非常慢。根据松下异质结组件户外衰减数据显示,异质结电池 10年衰减小于3%,25年发电量的下降仅为8%。
9.与传统晶硅光伏电池栅线电极的制造工艺不同,传统晶硅光伏电池栅线电 极是通过使用丝网印刷技术将银浆印刷在晶硅电池的减反膜上,通过高温烧结, 减反膜层被烧穿,银同硅片形成紧密欧姆接触。而异质结栅线电极制造工艺, 是在异质结电池表面的透明导电氧化膜上制造并和此导电膜欧姆接触电学连接 的金属栅线电极。
10.传统异质结光伏电池金属栅线电极是通过在导电透明膜栅印刷低温银浆, 通过固化形成金属栅线电极。低温栅线电极银浆料,相较于高温烧结型银浆料, 低温银浆生产工艺要求更高,含银量高,且运输过程必须采用冷链物流,采购 成本价格更高,大约是普通高温银浆的1.1~1.2倍。考虑到异质结电池需要双面 使用低温银浆,相同尺寸硅片异质结电池的银浆用量比普通晶硅电池的银浆用 量的2.5~3倍。显而易见,低温银浆的高耗量和
高成本已经成为异质结电池高成 本的主要原因之一。
11.为了实现降本的目标,大力推广异质结电池,就需要采用其它金属栅线电 极制作方式取代使用低温银浆制造栅线电极的工艺,大幅度降低异质结电池的 生产成本。
技术实现要素:
12.本发明所要解决的技术问题在于:提出一种异质结光伏电池栅线电极制作 方法,通过超声波焊接,直接将熔化的低温焊锡合金,和异质结光伏电池表面 导电透明金属氧化物膜直接焊接电学连接的低温焊锡合金直线带状异质结光伏 电池栅线电极。
13.这种异质结电池栅线电极制作方法,由于直接采用低成本的低温焊锡合金 和透明导电金属氧化膜直接焊接电学连接,形成异质结电池焊锡合金的焊接带 状栅线电极,取代使用高成本的低温银浆通过和透明导电膜采用树脂固化连接 形成栅线电极,异质结光伏电池的生产成本大幅下降。
14.同时,由于低温焊锡合金和透明导电金属氧化膜是通过共价键连接,粘接 强度也高于低温银浆中环氧体系和透明导电金属氧化膜的粘接强度。相似的, 低温银浆形成的栅线电极,和金属焊带连接时,都是锡
‑
锡焊接连接,金属焊带 与电池栅线电极的拉拔力也高于金属焊带和低温银浆栅线电极的粘接力,使这 种低温焊锡合金作为栅线电极的异质结电池串联连接有比较好的高低温环境下 的使用可靠性。
15.为解决传统异质结光伏电池使用高成本低温银浆所带来的问题,本发明的 技术方案是:
16.一种异质结光伏电池栅线电极制作方法,包括在n型衬底硅片的正反两面, 分布非晶硅膜,在非晶硅膜外又沉积一层透明导电金属氧化物膜形成正电极面和 负电极面,在正电极表面和负电极表面上,分布着栅线电极,制作方法如下:
17.一、异质结电池主体制成,即由n型晶硅制成衬底硅片,在硅片正反两面 分别沉积氢化非晶硅膜;
18.二、在正反非晶硅膜外,再分别沉积一层透明导电金属氧化物膜作为异质 结光伏电池的正电极面和负电极面;
19.三、将超声波焊接装置悬置在电池透明导电金属氧化物膜,即异质结光伏 电池的电极面表面上,通过超声焊接装置,将导电金属熔化,通过超声波空洞 效应将熔化导电金属与所述的电池透明导电金属氧化物膜进行直接焊接;
20.四、通过超声波焊接装置的超声焊头的连续线性移动,形成和异质结电池 导电透明金属氧化物膜直接焊接的电学连接的金属直线带状异质结光伏电池栅 线电极;
21.其中电池栅线电极即为在异质结光伏电池表面的导电透明氧化物膜上焊接 分布的连续导电金属合金直线带状物。
22.进一步地,在第一步和第二步中,n型衬底硅片的一面沉积p 型氢化非晶 硅膜,并在其上沉积出一层透明导电金属氧化物膜作为异质结光伏电池正电极 面;在n型衬底硅片的另一面沉积n 型氢化非晶硅膜,并在其上沉积出一层透 明导电金属氧化膜作为异质结光伏电池负电极面。
23.进一步地,在第三步中,所述的导电金属采用低温焊锡合金,所述的低温 焊锡合金为熔化温度低于200度的焊锡合金。
24.进一步地,所述电池栅线电极的宽度由焊接装置的焊头宽度决定,其厚度 由供给焊锡合金量的大小决定。
25.进一步地,在第三步中,将所述的导电金属放在电池表面透明导电金属氧 化膜上预定栅线电极的位置上,再用焊接装置直接静压在所述的导电金属上, 通过焊接装置的超声波将高频振动能量转成摩擦生热效应,直接将所述的导电 金属和电池导电透明金属氧化物膜接触面熔化焊接并电学连接,形成电池栅线 电极。
26.进一步地,所述的导电金属采用金属焊带,其金属截面为圆形、正方形、 长方形或梯形。
27.进一步地,所述的金属焊带表面镀低温焊锡合金。
28.进一步地,每个异质结光伏电池至少有一条连续的焊锡合金导电金属的正 栅线电极,和一条连续焊锡合金导电金属的负栅线电极;在同一异质结电池电 极表面的金属栅线电极之间,栅线电极相互平行,并且宽度尺寸保持一致。
29.进一步地,在第三步中,所述的焊接装置采用超声波焊接装置,其包括调 频装置、转换器、调压装置和焊头;首先所述的调频装置将低电频能转化成高 频电能,供给所述的转换器,所述的转换器将电能转换成用于超声波的高频机 械振动能,所述的调压装置将转变后的机械能传至所述的超声波焊头。
30.进一步地,在第二步中,异质结光伏电池表面的导电透明金属氧化物膜是 在异质结光伏电池硅片沉积完非晶硅薄膜之后,通过物理化学气相沉积的磁控 溅射工艺或者反应等离子体沉积镀膜工艺,制成的透明导电氧化物膜,其收集 载流子并向电池表面的栅线电极传输。
31.有益效果:本发明提供一种异质结光伏电池栅线电极制作方法,利用超声 波的空洞效应将低温焊锡合金与异质结光伏电池导电透明金属氧化膜进行直接 焊接,实现和电池透明导电金属氧化膜的欧姆接触,形成所述异质结电池栅线 电极,或者利用焊头静压金属焊带在透明导电金属氧化膜上,通过超声波将高 频机械动能转换成摩擦生热使其直接焊接在透明导电金属氧化膜表面,完成金 属焊带和透明导电金属氧化膜的欧姆接触,将金属焊带和电池栅线电极合为一 体,形成所述异质结电池栅线电极,有效保证了金属焊带和透明导电金属氧化 膜焊接的质量和效果,降低银浆消耗量,从而降低电池的制作成本。
附图说明
32.图1示出本发明的异质结光伏电池截面示意图。
33.图2示出本发明的异质结光伏电池栅线电极和金属焊带连接后与其他所述 异质结光伏电池的连接
34.其中:1.异质结光伏电池
35.ꢀꢀꢀꢀꢀ
2.异质结光伏电池低温焊锡合金栅线电极
36.ꢀꢀꢀꢀꢀ
3.异质结光伏电池表面导电透明金属氧化物膜
37.ꢀꢀꢀꢀꢀ
4.异质结光伏电池氢化非晶硅膜
38.ꢀꢀꢀꢀꢀ
5.和异质结光伏电池表面低温焊锡合金栅线电极连接的金属焊带
具体实施方式
39.如图所示,在一个实施例中,本案实施采用的是158.75*158.75n型单晶5 主栅电池片异质结光伏电池。
40.传统异质结光伏电池的栅线电极是将低温银浆丝印到光伏电池的正负栅线 电极表面的透明导电氧化膜上,经过高温固化,银浆中环氧树脂跟透明导电膜 固化粘接,银浆中银粉导电形成栅线电极。
41.采用本发明的异质结光伏电池栅线电极的制作方式,使用50w超声波焊接 装置,超声波焊头宽度为1毫米,移动速度为500mm/分钟,将s
‑
140焊 锡合金熔化。随着超声波焊头的连续移动,在异质结光伏电池的导电透明氧化 膜上形成158mm*1mm的焊锡合金和电池表面透明导电氧化膜电学连接的带状 电池栅线电极。在电池表面完成5次相同尺寸焊锡合金和电池表面导电透明氧 化膜的焊接,在电池表面形成5条158mm*1mm的焊锡合金带状5主栅栅线电 极。
42.由于主栅栅线电极的总宽度是细栅栅线电极总宽度的n倍,传统栅线电极 制造工艺中,主栅栅线电极的银浆用量也是细栅栅线电极银浆用量的n倍。因 此,本设施案列中,主栅采用焊锡合金和电池表面导电透明氧化膜焊接制造工 艺,细栅栅线电极仍将采用低温银浆印刷固化制造工艺。
43.本实施案列中异质结光伏电池的细栅栅线电极仍然采用低温银浆印刷方式 制作方式完成。采用hc449型号低温银浆。在电池透明导电膜上印刷96根宽度 35微米,高12微米的细栅线电极栅线。
44.从中泰证券异质结报告中,对158尺寸硅片中,不同栅线电极数量电池片 的低温银浆使用量。
45.5bb电池表面细栅栅线电极和5条主栅栅线电极均采用低温银浆高温固化 方式,低温银浆用量为300mg。
46.mbb电池表面采用细栅栅线电极和9条圆形主栅栅线电极均采用低温银浆 高温固化方式。由于圆形主栅所需焊接栅线电极比较窄,因此,制作栅线电极 银浆用量比5bb电池结构少,为160mg。
47.swct电池表面只有细栅栅线电极,主栅则采用导电膜加铜丝低温合金的 栅线电极方式。因此,使用的低温银浆用量最少,为90mg。
[0048][0049]
本发明实施案例采用的是主栅栅线电极采用超声波焊接熔化焊锡合金和电 池表面透明导电膜焊接,形成5条焊锡合金带状栅线电极的制造工艺,电池表 面的细栅栅线电极依然采用低温银浆印刷,高温固化的方式,。因此低温银浆 制造细栅栅线电极的使用量和swct相似,为90mg,比5bb异质结电池低温 银浆用量减少70%,比mbb异质结电池低温银浆用量减少40%。
[0050]
而且采用焊锡合金焊接形成异质结光伏电池主栅栅线电极方式,和目前主 流的perc电池栅线电极制作成本相比,在异质结双面对称使用银浆用量的情 况下,只比传统晶硅percmbb电池的银浆用量稍多(90mg对74mg)。
[0051]
多主栅与perc电池的结合
[0052][0053]
但由于本实施案列主栅栅线电极结构采用5bb的主栅栅线电极,和mbb 栅线电极结构相比,焊带成本没有增加,因此使用本发明的低温焊锡合金焊接 栅线电极的异质结电池的主栅栅线电极生产成本和目前晶硅perc电池mbb栅 线电极结构生产成本相似。达到了降低异质结电池成本的目的。
[0054]
并且在后期电池串焊工艺中,不使用导电膜加铜丝低温合金的swct主栅 栅线电极串联方式,在电池串焊工艺中,可以继续采用目前传统焊接机进行电 池串焊(只需要把焊接温度调低),这样,不但大幅度降低了低温银浆的使用 量和带来的电池生产高成本,也使采用本发明焊锡合金焊接主栅栅线电极的电 池间串焊连接成本大幅降低,同时还避开了导电膜加铜丝低温合金的主栅栅线 电极方式可能的专利纠纷。
[0055]
采用本专利实施的异质结电池导电透明金属氧化物膜上焊锡合金栅线电极, 在进行异质结光伏电池间串联焊接时,通过使用镀锡铜焊带和光伏电池的主栅 栅线电极焊接完成。镀锡铜焊带外面镀了15um~30um一个相似结构的snbi镀 层。和主栅焊带进行焊接的时候,和电池片上焊锡合金焊接栅线电极有非常好 的相融性和较强的剥离强度。可以非常容易达到2n/mm的水平,满足国际标准 对焊带和电池栅线电极焊接剥离强度的要求。对采用本发明栅线电极制作方法 的异质结电池可靠性有了保障。
[0056]
从本实施案列来看,使用本发明主栅栅线电极采用低温焊锡合金和电池表 面透明导电金属氧化膜通过超声波焊接形成带状主栅栅线电极,细栅栅线电极 采用低温银浆固化成栅线电极制作的5栅异质结光伏电池,从栅线电极的制作 成本看,已经非常接近目前常规的晶硅percmbb(多主栅)光伏电池的银浆 制作成本,与传统异质结光伏电池使用银浆用量相比,有了巨大的下降。因此 采用本发明利用低温焊锡合金和电池表面导电透明氧化膜焊接形成电池栅线电 极的制作方式不仅可以替代低温银浆制作异质结光伏电池栅线电极的工艺方法, 而且栅线电极的制作成本可以明显下降。促进了异质结高效电池的发展。
[0057]
最后需要说明的是,以上实施例仅用以说明本发明的技术方案而非限制性 技术方案,本领域的普通技术人员应当理解,那些对本发明的技术方案进行修 改或者等同替换,而不脱离本技术方案的宗旨和范围,均应涵盖在本发明的权 利要求范围。
再多了解一些
本文用于企业家、创业者技术爱好者查询,结果仅供参考。