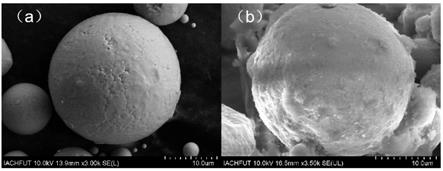
1.本发明属于磁性材料技术领域,具体涉及一种低损耗软磁复合材料的制备方法。
背景技术:
2.软磁复合材料以其优异的直流偏置性能以及良好的频率稳定性被广泛应用在光伏逆变器、电动汽车、变频空调等领域。随着开关频率不断提高,对软磁复合材料的损耗也更加关注,如何在保证优异直流偏置性能的前提下降低软磁复合材料的损耗是目前研究的热点。
3.损耗分离研究发现,应用频段在大约100khz以下,软磁复合材料的损耗主要以磁滞损耗为主。而当应用频段提高至几百khz,软磁复合材料的磁滞损耗与涡流损耗都占有一定比例,降低总损耗就必须同时考虑降低软磁复合材料的磁滞损耗与软磁复合材料的涡流损耗。目前,降低软磁复合材料磁滞损耗的方法主要还是集中在提升软磁复合材料的密度,降低软磁复合材料内部的有效退磁场,例如通过粉末的粒度配比来实现压制密度的提升,或者通过表面改性的方式对磁粉进行绝缘包覆,得到较薄的绝缘层。但粉末的粒度配比方式多种多样,需要对磁粉颗粒进行筛分处理,较为繁琐,而表面改性的方式大多利用有机/无机复合绝缘,两层绝缘层绝缘效果虽好,可以有效降低涡流损耗,但该非磁性复合绝缘层却很难做薄,导致磁滞损耗依然很高。而涡流损耗主要与粉末颗粒的粒径以及软磁复合材料的电阻率有关,虽然减小粉末整体粒径有助于降低涡流损耗,但较小的磁粉会因为流动性差和易通过模具间隙喷出而遇到磁芯难以压制成形及拉伤模具等问题,所以要想降低软磁复合材料的涡流损耗,在不大幅降低磁粉尺寸的前提下,只能提升软磁复合材料的电阻率。因此,选用一种或多种电阻率较高的绝缘物并实现对磁粉颗粒致密均匀的包覆是得到低损耗软磁复合材料的关键。
技术实现要素:
4.为了避免工序繁琐的磁粉粒度配比,同时解决复合绝缘时,磁滞损耗与涡流损耗难以同时保持较低水平的问题,本发明提供一种低损耗软磁复合材料的制备方法。
5.一种低损耗软磁复合材料的制备操作步骤如下:(1)将氯化镁粉末、氯化铝粉末与金属磁粉按照质量比1:1:10~30进行混合,加入到浓度98%乙醇溶液中均匀搅拌,得到混合溶液;所述金属磁粉为铁硅磁粉、气雾化铁硅铝磁粉、铁镍磁粉中的一种;(2)在混合溶液中加入氨水充分反应,并进行加热烘干,并过80目筛网,得到复合粉末;所述氨水加入的量为混合溶液质量的1%~5%;(3)将所得复合粉末在氮气的保护气氛下进行两步煅烧,得到热处理粉末;(4)将所得热处理粉末在模具中压制成形、退火处理,得到具有氧化镁和氧化铝复合绝缘层的低损耗软磁复合材料;
所述低损耗软磁复合材料的电阻率为8.05
×
109μω
∙
cm~9.997
×
109μω
∙
cm、密度为5.93~7.26g/cm3;100khz/1v条件下,相对磁导率μ为52.66~68.22;500khz/50mt时,损耗p
cv
为1241~3522mw/cm3,其中磁滞损耗为585~1838mw/cm3,涡流损耗为656~1684mw/cm3。
6.进一步地具体技术方案如下:所述步骤(1)中,所述金属磁粉的粉末粒径为20~180μm。
7.所述步骤(2)中,烘干温度为80~100℃。
8.所述步骤(3)中,所述两步煅烧:第一步煅烧温度为400~600℃,第二步煅烧温度为800~1000℃,保温60~180min,随炉冷却。
9.所述步骤(4)中,成形压强为1700~2100mpa。
10.所述步骤(4)中,所述退火处理,先在180~240℃保温30~90min,再将退火温度提高至700~800℃,保温45~100min。
11.本发明的有益技术效果体现在以下方面:(1)本发明中得到的氧化镁与氧化铝复合氧化物具有较高的电阻率,对于降低软磁复合材料的涡流损耗具有很好的作用,且这种绝缘氧化物在煅烧过程中不会与磁粉发生化学反应,不会影响磁粉颗粒的固有属性。
12.(2)本发明中通过两步煅烧得到绝缘氧化物均匀致密地附着在磁粉颗粒表面,可通过简单控制氯化镁和氯化铝的用量实现较薄的绝缘层,从而实现较高的压制密度,有效降低软磁复合材料的磁滞损耗。
13.(3)本发明中以相对磁导率级别为60(
±
8%)的气雾化铁硅铝软磁复合材料为例,1号为常规有机/无机复合绝缘工艺制备的样品,2号为采用本发明工艺制备的样品。并对两种方法制得的气雾化铁硅铝软磁复合材料进行损耗、密度以及电阻率测试,再对500khz/50mt测试的损耗进行拟合,分离出磁滞损耗与涡流损耗,它们的对比数据如表1所示。
14.可见,用本发明工艺制备得到的磁芯密度和电阻率均相对较高,对应的磁滞损耗和涡流损耗均低于常规有机/无机复合绝缘工艺制备的样品。图1为实施例2中气雾化铁硅铝原粉与采用本发明工艺煅烧后的绝缘磁粉颗粒扫描电镜照片,可见,图1(a)中原粉颗粒表面有鳞片状结构,通过本发明工艺煅烧后,图1(b)中磁粉颗粒表面生成了一层均匀且致密的绝缘层,表面较平整,有利于压制成形,得到较好的磁性能。
附图说明
15.图1中(a)为气雾化铁硅铝原粉颗粒扫描电镜照片图;
图1中(b)为本发明工艺煅烧后的气雾化铁硅铝绝缘磁粉颗粒扫描电镜照片图。
具体实施方式
16.一种低损耗软磁复合材料的制备操作步骤如下:实施例1:(1)选取氯化镁60g,氯化铝60g,铁硅磁粉600g(质量比为1:1:10),其中铁硅磁粉的粉末粒径为20~180μm,再加入300g浓度98%的乙醇溶液,混合之后搅拌均匀,得到混合溶液。
17.(2)在混合溶液中加入51g氨水,氨水加入的量为混合溶液质量的5%,充分反应,在80℃的温度下进行烘干,并过80目筛网,得到复合粉末。
18.(3)将所得复合粉末放入管式炉中,在氮气的保护气氛下先升温至600℃,保温60min;再升温至1000℃,保温60min,随炉冷却,得到热处理粉末。
19.(4)制备低损耗软磁复合材料(4.1)将热处理粉末过80目筛网,在油压机中,2100mpa的压强下进行双向浮动压制,得到软磁复合材料的生坯;(4.2)将所述生坯置于氮气保护下的退火炉中,先在180℃下,保温30min;再将退火温度提高至700℃,保温45min;随炉冷却至室温,制得低损耗软磁复合材料。
20.本实施例1制备的低损耗软磁复合材料的性能指标:电阻率为9.997
×
109μω
·
cm,密度为6.72g/cm3;经绕线测试的性能指标:100khz/1v条件下,相对磁导率μ=52.66;损耗:500khz/50mt时,p
cv
=3522mw/cm3,其中磁滞损耗为1838mw/cm3,涡流损耗为1684mw/cm3。
21.实施例2一种低损耗软磁复合材料的制备操作步骤如下:(1)选取氯化镁30g,氯化铝30g,气雾化铁硅铝磁粉600g(质量比为1:1:20),其中气雾化铁硅铝磁粉的粉末粒径为20~180μm,再加入300g浓度98%的乙醇溶液,混合搅拌均匀,得到混合溶液。
22.(2)在混合溶液中加入28.8g氨水,氨水加入的量为混合溶液质量的3%,充分反应,在90℃的温度下烘干,过80目筛网,得到复合粉末。
23.(3)将复合粉末放入管式炉中,在氮气的保护气氛下先升温至500℃,保温120min;再升温至900℃,保温120min,随炉冷却,得到热处理粉末。参见图1(b),煅烧后的气雾化铁硅铝绝缘磁粉颗粒表面生成了一层均匀且致密的绝缘层,表面较平整。
24.(4)制备低损耗软磁复合材料(4.1)将热处理粉末过80目筛网,在油压机中,1900mpa的压强下进行双向浮动压制,得到软磁复合材料的生坯;(4.2)将所述生坯置于氮气保护下的退火炉中,先在210℃下,保温60min;再将退火温度提高至750℃,保温75min;随炉冷却至室温,制得低损耗软磁复合材料。
25.本实施例2制备的低损耗软磁复合材料的性能指标:电阻率为8.565
×
109μω
·
cm,密度为5.93g/cm3;经绕线测试的性能指标:100khz/1v条件下,相对磁导率μ=61.20;损耗:500khz/50mt时,p
cv
=1241mw/cm3,其中磁滞损耗为585mw/cm3,涡流损耗为656mw/cm3。
26.实施例3
一种低损耗软磁复合材料的制备操作步骤如下:(1)选取氯化镁20g,氯化铝20g,铁镍磁粉600g(质量比为1:1:30),其中磁粉的原粉粒径为20~180μm,再加入300g浓度98%的乙醇溶液,混合之后搅拌均匀,得到混合溶液。
27.(2)在混合溶液中加入9.4g氨水,氨水加入的量为混合溶液质量的1%,充分反应,在100℃的温度下进行烘干,并过80目筛网,得到复合粉末。
28.(3)将复合粉末放入管式炉中,在氮气的保护气氛下先升温至400℃,保温180min;再升温至800℃,保温180min,随炉冷却,得到热处理粉末。
29.(4)制备低损耗软磁复合材料(4.1)将热处理粉末过80目筛网,在油压机中,1700mpa的压强下进行双向浮动压制,得到软磁复合材料的生坯;(4.2)将所述生坯置于氮气保护下的退火炉中,先在240℃下,保温90min;再将退火温度提高至800℃,保温100min;随炉冷却至室温,制得低损耗软磁复合材料。
30.本实施例3制备的低损耗软磁复合材料的性能指标:电阻率为8.025
×
109μω
·
cm,密度为7.26g/cm3;经绕线测试的性能指标:100khz/1v条件下,相对磁导率μ=68.22;损耗:500khz/50mt时,p
cv
=1337mw/cm3,其中磁滞损耗为603mw/cm3,涡流损耗为734mw/cm3。
31.以上所述,仅是本发明的较好实施例,不对本发明做任何限制,依据本发明方法所做的任何修改及等同变化,仍属于本发明的保护涵盖范围。
再多了解一些
本文用于企业家、创业者技术爱好者查询,结果仅供参考。