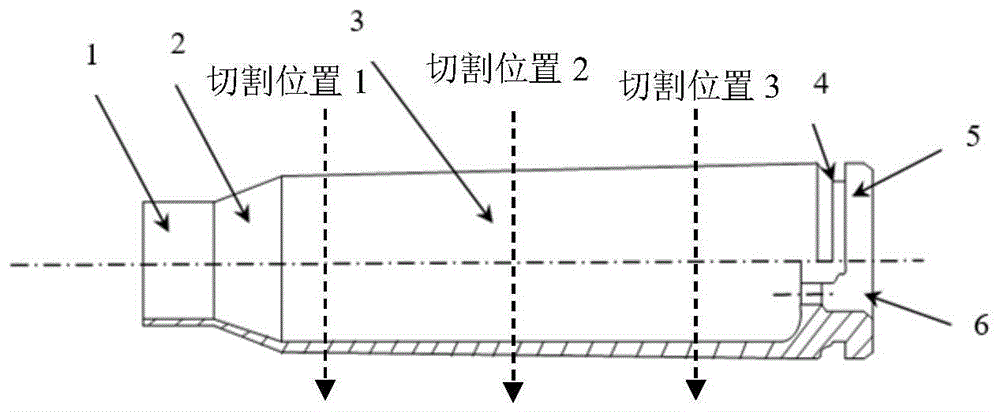
本发明涉及铝药筒的表面处理,具体涉及一种铝药筒的微弧氧化处理方法。
背景技术:
:铝合金药筒其重量只有黄铜药筒重量的30%,钢药筒重量的36%,装铝药筒的全弹只有黄铜药筒全弹的65%。此外,铝的弹性模量只有钢的1/3,有利于发射后的顺利退壳。采用铝质药筒,能够有效对单兵作战效能和高射速航空武器装备的战技指标,此外,铝药筒可大大减轻对武器零件的磨损,有利于提高武器寿命。但是普通的铝药筒存在致命的缺陷:1)铝的熔点在680℃左右,耐烧蚀性能差,如果考虑连续发射的情况,其内表面温度将上升更快,很容易达到或超过铝的熔点,所以铝质药筒的内表面必须要做合适的防高温处理,如果表面处理不过关,容易发生药筒烧蚀,甚至烧蚀枪炮内膛;2)铝药筒可以和弹膛实现贴膛配合,当接触表面的摩擦力总和大于作用在药筒上的轴向力的时候,药筒就不能移动,并且对内堂也会进行磨损,所以铝药筒外部需要进行耐磨减摩处理。目前现有的单一的表面处理技术(如微弧氧化、磁控溅射等)无法实现上述功能,如果采用复合膜层或者两种及以上膜层相互结合的形式,会大大提高铝药筒的生产成本。本发明则提出了一种铝药筒获得不同性能膜层的微弧氧化处理方法,既可以在铝药筒内部获得一种均匀的耐烧蚀微弧氧化膜层,也可以在铝药筒外部获得一种耐磨、减摩微弧氧化膜层。技术实现要素:本发明提供一种铝药筒的微弧氧化处理方法,解决的技术问题是在铝药筒内壁形成均匀分布且抗烧蚀的微弧氧化涂层,在铝药筒外壁形成耐磨、减摩微弧氧化膜层。本发明解决上述技术问题所采用的技术方案为:一种铝药筒的微弧氧化处理方法,其特征在于包括以下制备工艺步骤:1)清洁:将铝药筒进行清洁;2)抛光:将铝药筒外壁进行抛光,然后采用可剥离的电绝缘性保护涂层涂覆在铝药筒的外壁;3)铝药筒内壁进行微弧氧化:将铝药筒置入微弧氧化电解液中对铝药筒内壁进行微弧氧化,其中电解液为:硅酸钠2~8g/l,硼砂0.5~1g/l,铝酸钠1~3g/l,氢氧化钠0.5~2g/l,二氧化钛与氧化锌均为1~3g/l;4)铝药筒外壁进行微弧氧化:对铝药筒进行清洁,然后去除电绝缘性涂层,将铝药筒的筒口堵闭,将铝药筒置入微弧氧化电解液中对铝药筒外壁进行微弧氧化,其中电解液为:硅酸钠2~8g/l,硼砂0.5~1g/l,铝酸钠1~3g/l,氢氧化钾0.5~2g/l,石墨烯2~5g/l,二硫化钼0.1~1g/l,碳化硅0.5~3g/l;5)封孔:将铝药筒的内外微弧氧化膜层进行封孔。铝药筒内壁微弧氧化的电解液为:硅酸钠2~8g/l,硼砂0.5~1g/l,铝酸钠1~3g/l,氢氧化钠0.5~2g/l,二氧化钛与氧化锌均为1~3g/l;在硅酸钠体系中加入铝酸钠、二氧化钛与氧化锌会使得微弧氧化膜层更致密均匀,并且沉积二氧化钛膜层,可以耐烧蚀,而过多的含量会使得膜层形成困难。铝药筒外壁微弧氧化的电解液为:硅酸钠2~8g/l,硼砂0.5~1g/l,铝酸钠1~3g/l,氢氧化钾0.5~2g/l,石墨烯2~5g/l,二硫化钼0.1~1g/l,碳化硅0.5~3g/l;在硅酸钠体系中加入石墨烯、二硫化钼、碳化硅,不仅会让膜层更加致密达到耐磨效果,而且会使膜层更加的光滑,如果添加过量会导致电解液导电性能较差,成膜效果差。本发明中的内壁是指铝药筒内部能够与电解液接触的所有内表面,外壁是指在铝药筒的筒口堵闭后能够与电解液接触的所有外表面。作为优选,所述步骤2)中,抛光后铝药筒外壁的粗糙度ra为0.2~1.6;保护涂层为聚乙醇缩丁醛。为了使得涂层在剥离过程中对基体损害较小所以需要将外壁的粗糙度控制在1.6以内,而低于0.2以后会大大增加加工成本,而采用聚乙醇缩丁醛可以更好的从基体上剥离。作为优选,所述步骤3)中,微弧氧化电参数设定为:i)第一阶段:正电压530~550v,负电压50~250v,频率为800~1500hz,占空比为5~20%,电解液温度保持在15~40℃,微弧氧化时间为15~20min;ii)第二阶段正电压480~500v,负电压50~250v,频率为800~1500hz,占空比为5~20%,电解液温度保持在15~40℃,微弧氧化时间为15~20min;iii)第三阶段:正电压430~450v,负电压50~250v,频率为800~1500hz,占空比为5~20%,电解液温度保持在15~40℃,微弧氧化时间为15~20min。电参数工艺分了三个阶段,第一阶段使得基体会快速沉积一层较厚的膜层,第二阶段与第三阶段分别用来修复微弧氧化膜层较大的孔洞与微裂纹。由于铝药筒内部空间较为狭窄,为了保持内部电解液成分与温度的稳定,作为优选,所述步骤3)中,微弧氧化过程中通过冷却装置对铝药筒内的电解液进行冷却,所述冷却装置包括供铝药筒内电解液流出的出液管以及供液体回流到铝药筒内的回液管,所述出液管和回液管之间设有提供动力的第一电机以及换热器。如果不对铝药筒内部进行降温,微弧氧化过程中会因为温度过高导致膜层在氧化过程中烧蚀。微弧氧化过程中通过补液装置将铝药筒外的电解液不断补充到铝药筒内,所述补液装置包括将铝药筒内电解液抽到铝药筒外的抽液管,将铝药筒外的电解液补充到铝药筒内的进液管,为抽液和补液提供动力的第二电机。如果电解液补充不到位,铝药筒内部的电解液成分就不能控制在上述范围内,生成的膜层性能会降低。为了在相同时间下获得更高均匀的微弧氧化膜层的厚度,作为优选,所述步骤3)中,电解液采用外加直流电源并施加磁场,磁场强度为50~350gs。作为优选,所述步骤4)中,微弧氧化电参数设定为:i)第一阶段:正电压530~550v,负电压50~100v,频率为500~1000hz,占空比为5~20%,电解液温度保持在15~40℃,微弧氧化时间为5~10min;ii)第二阶段正电压480~500v,负电压50~250v,频率为500~1000hz,占空比为5~20%,电解液温度保持在15~40℃,微弧氧化时间为5~10min;iii)第三阶段:正电压430~450v,负电压50~100v,频率为500~1000hz,占空比为5~20%,电解液温度保持在15~40℃,微弧氧化时间为5~10min。电参数工艺分了三个阶段,第一阶段使得基体会快速沉积一层较厚的膜层,第二阶段与第三阶段分别用来修复微弧氧化膜层较大的孔洞与微裂纹。而该工艺的微弧氧化时间的范围要比内部微弧氧化时间要低,一个是由于外部微弧氧化电解液与内部成分不相同成膜速度较块,并且外部微弧氧化时间过长会降低膜层的摩擦性能。作为优选,所述步骤4)中,铝药筒内装有供冷却的水,且通过权利要求4所述的冷却装置进行冷却,所述出液管和回液管内为水。如果不对铝药筒内部进行降温,微弧氧化过程中会因为温度过高导致膜层在氧化过程中烧蚀。作为优选,所述步骤3)和步骤4)中,各铝药筒竖向位于电解液中,所述步骤3)中,各铝药筒的横向间距为30~40mm,所述步骤4)中,各铝药筒的横向间距为60~80mm。为了保持铝药筒之间相互不干扰,包括温度上升与电解液补充,但是如果间距太大会浪费空间生产数量会降低;而所述步骤4)中的间距范围要比所述步骤3)中的间距大是由于3)中的微弧氧化处理在筒内,而4)中的微弧氧化处理在筒外。作为优选,所述步骤5)中,采用电泳封孔,电泳漆采用环氧树脂透明漆,具体工艺为:i)电泳:采用微弧氧化电源,电压为20~60v,频率为50~80hz,占空比为75~90%,电泳时间为3~10s;该电泳处理仅仅为填充微弧氧化微孔洞,所以时间极短,并且不在表面形成一层可观察的漆膜。ii)电泳固化工艺:将电泳后铝药筒进行固化处理,温度为150~180℃,保温时间为25~45min。需要将电泳漆固化,并且达到哑光状态。与现有技术相比,本发明的优点在于:1)将铝药筒的外壁采用可剥离的电绝缘涂层进行涂覆,能够单独实现对铝药筒内壁进行微弧氧化,形成膜层,将铝药筒的筒口堵闭,可以单独实现对铝药筒外壁微弧氧化,形成膜层,内外壁采用不同的电解液,形成满足各自要求的氧化膜层。2)在铝药筒内壁形成的微弧氧化膜层,膜层更加均匀,且具有耐烧蚀,解决了铝药筒内部火药耐烧蚀与高温向铝药筒外部传递问题。3)在铝药筒外壁形成的微弧氧化膜层,膜层更加均匀,更加耐磨,摩擦系数更低,解决了铝药筒外部耐磨性能差,且与内膛摩擦较为严重等问题。附图说明图1为铝药筒示意图。其中,1为口部,2为斜肩,3为体部,4为插壳钩槽,5为底缘,6为底火室。图2为铝药筒内壁微弧氧化装置示意图。1~4为冷却装置,1为回液管,2为换热器,3为第一电机,4为出液管;5~7为补充装置,5为进液管,6为第二电机,7为抽液管,8为电解槽,9为电解液,10为铝药筒。图3为铝药筒外壁微弧氧化膜层制备装置示意图。1~4为冷却装置,1为回液管,2为换热器,3为第一电机,4为出液管;5为电解槽,6为电解液,7为铝药筒,8为密封橡皮塞。具体实施方式以下结合附图实施例对本发明作进一步详细描述。实施例1至实施例3中的铝药筒见图1所述,采用本发明的处理方法进行微弧氧化,如图2、图3所示,包括以下制备工艺步骤:1)清洁:将铝药筒进行清洁;将加工完成的铝药筒进行超声波水洗,时间为3~5min,去除屑渣以及颗粒状异物;为了能够快速完全去除表面油污,而表面不会产生其他元素的污染,然后将铝药筒进行酸洗3~5s,为了对去除表面油污进行补充,水洗后再采用naoh与na2sio3混合溶液进行碱蚀,其中naoh为2~10g/l,na2sio3为1~5g/l。2)抛光:将铝药筒外壁进行抛光,确保铝药筒外部如图1中的1~6部分表面粗糙度ra在0.2~1.6(实施例1为0.2,实施例2为1.0,实施例3为1.6);然后采用可剥离聚乙醇缩丁醛保护涂料对外部1~6处进行封装处理,确保在微弧氧化过程中一直保持绝缘性,并且导热性能较好。3)铝药筒内壁进行微弧氧化:将铝药筒置入微弧氧化电解液中对铝药筒内壁进行微弧氧化,为了在铝药筒内部均匀耐烧蚀微弧氧化膜层,将经过封装涂覆的铝药筒进行清洗后,将铝药筒按照图2方式进行微弧氧化,电参数工艺如表4所示,而磁场强度施加如表5所示,实施例1中铝药筒间距为35mm,实施例2中铝药筒间距为30mm,实施例3中药筒间距为40mm。图2中的铝药筒10内部的电解液由第一电机3提供动力通过出液管4进入换热器2中进行冷却后,通过回液管1流回电解槽8中,从而达到降温;而电解槽8中的电解液9由第二电机6提供动力经由抽液管7流入进液管5,最终进入铝药筒10内部对电解液进行补充。4)铝药筒外壁进行微弧氧化:完成铝药筒内部微弧氧化后采用去离子水进行清洗,并对外部涂层进行手动去除,并对铝药筒采用水洗后再采用naoh与na2sio3混合溶液进行碱蚀,如表1中各个实施例碱蚀成分。完成清洗后将铝药筒内部填充冷却去离子水,并按照如图3所示进行封装。将经过封装后的铝药筒放入电解液中,微弧氧化电参数设定如表6所示。实施例1中铝药筒间距为60mm,实施例2中铝药筒间距为70mm,实施例3中药筒间距为80mm。在铝药筒外部微弧氧化过程中,通过第一电机3提供动力将去离子水从铝药筒7中抽到出液管4中,经过换热器2进行冷却后,再由回液管1进入铝药筒7中,从而达到降温,通过密封橡皮塞8进行密封让整个过程为密封状态,不与电解液接触。5)封孔:将铝药筒的内外微弧氧化膜层进行封孔,封孔工艺如表7所示。对比例如表1~7参数所示。对内壁形成的微弧氧化膜层采用显微镜对膜厚进行测量,如图1所示进行切割,并对断面采用显微镜进行膜厚测量,每个截面进行5次测量,如表8所示。从表8中可以看出,对比例虽然膜层厚度要高一些,但是从标准差的结果可以看出,对比例测量值离散性要高于实施例1~3,因此,本实施例的膜层更加均匀,具有更好的耐烧蚀性能。根据标准gjb323a-1996《烧蚀材料烧蚀试验方法》进行火焰烧蚀试验,结果如表9所示。采用销-盘摩擦磨损试验机测试所制陶瓷膜层的摩擦系数喝磨损性能,对磨副采用y80硬质合计,硬度为hra89.5,试验条件为常温常压,干摩擦,滑动距离为500m,载荷为20n,滑动速度为0.8m/s,试样磨损前后称重用感量为10-5的分析天平,测量三次取平均值,计算磨损失重。试样摩擦系数按如下公式计算:f=f/w(其中,f为摩擦系数,f为样品表面摩擦力,w为样品表面所加载荷)。从表10可以看出,本发明的耐磨损失重量远低于对比例。表1本发明实施例和对比例的超声冲洗、酸洗、碱蚀工艺表2本发明实施例和对比例的铝药筒内部电解液配置表3本发明实施例和对比例的铝药筒外部电解液配置表4本发明实施例和对比例的铝药筒内部微弧氧化膜层电参数工艺表5本发明实施例磁场强度参数表编号磁场强度/gs实施例150实施例2150实施例3350对比例0表6本发明实施例和对比例的铝药筒外部微弧氧化膜层电参数工艺表7本发明实施例和对比例的封孔处理工艺表表8本发明实施例和对比例的显微镜测量膜层厚度表表9本发明实施例和对比例的火焰烧蚀试验结果编号氧-乙炔火焰烧蚀10s实施例1不脱落实施例2不脱落实施例3不脱落对比例脱落表10本发明实施例和对比例的摩擦系数与耐磨损失编号摩擦系数耐磨损失重量/mg实施例10.04-0.120.03实施例20.03-0.130.009实施例30.05-0.100.05对比例0.15-0.232.46当前第1页12
再多了解一些
本文用于企业家、创业者技术爱好者查询,结果仅供参考。