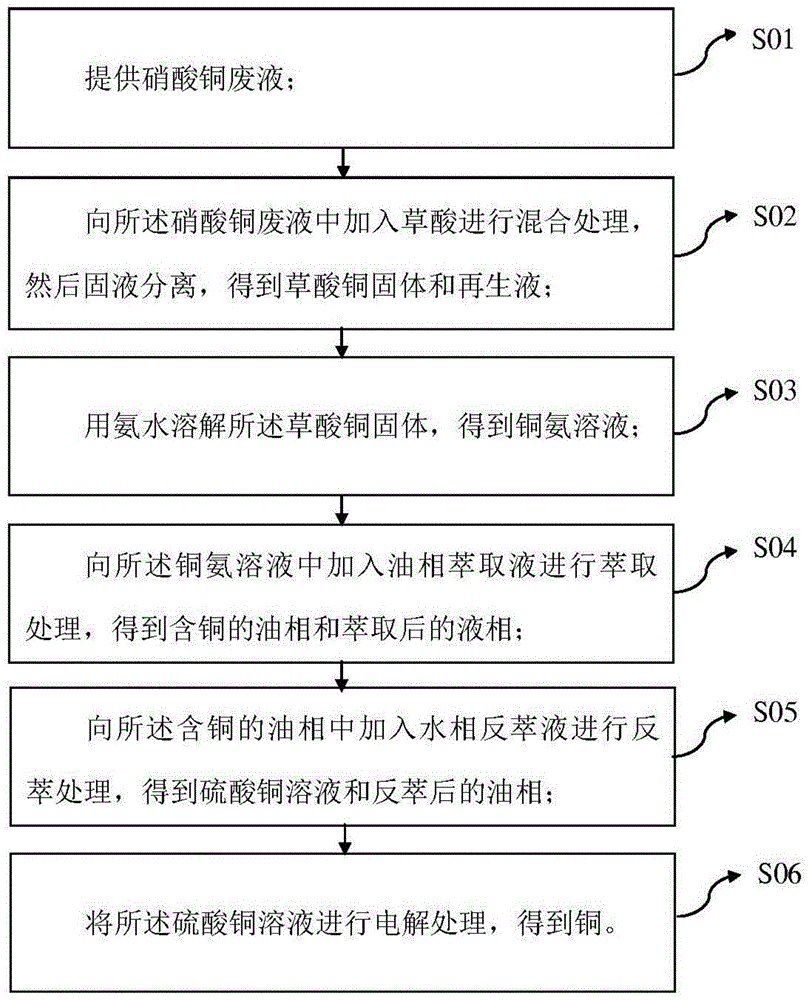
本申请属于废液回收技术领域,尤其涉及一种铜回收方法。
背景技术:
由于硝酸铜溶液自身的氧化性和对铜的强腐蚀能力,直接将硝酸铜溶液电解回收铜的过程中,电解效率极低,而且操作不当会泄露剧毒的红棕色氮氧化物气体,因此,市场上一般不采用直接电解的方法来回收铜。
目前,从而硝酸铜废液中回收铜的方法主要有置换法、中和沉淀法,这些方法回收的铜纯度低,因此使用价值低,同时还会进一步产生新的污染源,后续需要大量的人力物力进行提铜后的废液处理,尤其是废液中总氮的处理,因产生高总氮废液,废液处理成本高,废液资源难以实现再生循环利用。
因此,相关技术有待改进。
技术实现要素:
本申请的目的在于提供一种铜回收方法,旨在解决从硝酸铜废液中回收铜的纯度低,且废液总氮高难以循环利用的技术问题。
为实现上述申请目的,本申请采用的技术方案如下:
一种铜回收方法,包括如下步骤:
提供硝酸铜废液;
向所述硝酸铜废液中加入草酸进行混合处理,然后固液分离,得到草酸铜固体和再生液;
用氨水溶解所述草酸铜固体,得到铜氨溶液;
向所述铜氨溶液中加入油相萃取液进行萃取处理,得到含铜的油相和萃取后的水相;
向所述含铜的油相中加入水相反萃液进行反萃处理,得到硫酸铜溶液和反萃后的油相;
将所述硫酸铜溶液进行电解处理,得到铜。
本申请提供的铜回收方法是从硝酸铜废液中回收铜的方法,具体地,先向硝酸铜废液中加入草酸使铜沉淀分离出来即得到草酸铜固体,然后将草酸铜固体溶于氨水,依次进行萃取处理和反萃处理,从而使铜转换成即安全又容易电解沉积的硫酸铜溶液,最终电解硫酸铜溶液即可以得到铜固体。该回收过程中,分离草酸铜固体后得到的再生液可重新用于蚀铜工序,而萃取后的水相和反萃后的油相可在各自对应的上一步骤中重复使用,这样整个工艺过程能实现再生循环利用,如此使得该铜回收方法的系统不易产生新的污染源,难以产生高总氮废水,使得废水处理成本低,而且能从硝酸铜废液中回收变成纯度极高的电解铜,因此,本申请的该铜回收方法具有很好的应用前景。
附图说明
为了更清楚地说明本申请实施例中的技术方案,下面将对实施例或现有技术描述中所需要使用的附图作简单地介绍,显而易见地,下面描述中的附图仅仅是本申请的一些实施例,对于本领域普通技术人员来讲,在不付出创造性劳动的前提下,还可以根据这些附图获得其他的附图。
图1是本申请实施例提供的铜回收方法的流程示意图;
图2是本申请实施例提供的铜回收方法具体循环过程示意图;
图3是本申请实施例提供的铜回收方法得到的铜的xrd(x射线衍射)图。
具体实施方式
为了使本申请要解决的技术问题、技术方案及有益效果更加清楚明白,以下结合实施例,对本申请进行进一步详细说明。应当理解,此处所描述的具体实施例仅仅用以解释本申请,并不用于限定本申请。
本申请中,术语“和/或”,描述关联对象的关联关系,表示可以存在三种关系,例如,a和/或b,可以表示:单独存在a,同时存在a和b,单独存在b的情况。其中a,b可以是单数或者复数。字符“/”一般表示前后关联对象是一种“或”的关系。
应理解,在本申请的各种实施例中,上述各过程的序号的大小并不意味着执行顺序的先后,部分或全部步骤可以并行执行或先后执行,各过程的执行顺序应以其功能和内在逻辑确定,而不应对本申请实施例的实施过程构成任何限定。
在本申请实施例中使用的术语是仅仅出于描述特定实施例的目的,而非旨在限制本申请。在本申请实施例和所附权利要求书中所使用的单数形式的“一种”、“所述”和“该”也旨在包括多数形式,除非上下文清楚地表示其他含义。
本申请实施例说明书中所提到的相关成分的重量不仅仅可以指代各组分的具体含量,也可以表示各组分间重量的比例关系,因此,只要是按照本申请实施例说明书相关组分的含量按比例放大或缩小均在本申请实施例说明书公开的范围之内。具体地,本申请实施例说明书中所述的质量可以是μg、mg、g、kg等化工领域公知的质量单位。
本申请实施例提供一种铜回收方法,如图1所示,该铜回收方法包括如下步骤:
s01:提供硝酸铜废液;
s02:向所述硝酸铜废液中加入草酸进行混合处理,然后固液分离,得到草酸铜固体和再生液;
s03:用氨水溶解所述草酸铜固体,得到铜氨溶液;
s04:向所述铜氨溶液中加入油相萃取液进行萃取处理,得到含铜的油相和萃取后的水相;
s05:向所述含铜的油相中加入水相反萃液进行反萃处理,得到硫酸铜溶液和反萃后的油相;
s06:将所述硫酸铜溶液进行电解处理,得到铜。
本申请提供的铜回收方法是从硝酸铜废液中回收铜的方法,具体地,先向硝酸铜废液中加入草酸使铜沉淀分离出来即得到草酸铜固体,然后将草酸铜固体溶于氨水,依次进行萃取处理和反萃处理,从而使铜转换成即安全又容易电解沉积的硫酸铜溶液,最终电解硫酸铜溶液即可以得到铜固体。该回收过程中,分离草酸铜固体后得到的再生液可重新用于蚀铜工序,而萃取后的水相和反萃后的油相可在各自对应的上一步骤中重复使用,这样整个工艺过程能实现再生循环利用,如此使得该铜回收方法的系统不易产生新的污染源,难以产生高总氮废水,使得废水处理成本低,而且能从硝酸铜废液中回收变成纯度极高的电解铜,因此,本申请的该铜回收方法具有很好的应用前景。
上述步骤s01中,硝酸铜废液一般是指含有铜离子和残留的硝酸溶液的废水,广泛存在于电镀以及粉体冶金领域,其中含有铜离子的量一般约40~60g/l,因此具有很好的回收利用价值。本申请可以通过收集硝酸铜废液,为铜回收提供原始材料来源。
上述步骤s02中,利用铜的化合物在硝酸环境中的不同溶解度将铜沉淀分离出来,具体是向收集的硝酸铜废液中加入草酸进行混合处理,然后固液分离,得到草酸铜固体和再生液;其中草酸不但能在硝酸环境下与铜离子生成沉淀,同时还能增加溶液的酸度(溶液中h 的平衡浓度为酸度),其中的反应原理如下:
h2c2o4 cu(no3)2=cuc2o4↓ 2hno3
在一实施例中,上述混合处理包括:曝气1h~3h,然后静置6h~8h,这样使两者充分反应;上述固液分离包括隔膜压滤分离。具体地,向收集的硝酸铜废液中加入草酸搅拌并曝气1h~3h后,静置自然沉降6h~8h,从而使混合液实现明显的固液分层,然后将混合液通入隔膜压滤机中进行压滤,得到的滤液为再生液,滤饼即为草酸铜固体;草酸铜固体进行后续的铜回收工艺,而再生液可以与硝酸溶液混合用于刻蚀铜线,具体地分析再生液的酸度和参数后,补加相应硝酸及添加剂(如蚀刻安定剂),使酸度为3-5m(mol/l)后,回到腐蚀铜的生产工序进行工作。
进一步地,上述步骤中,加入的草酸与硝酸铜废液的质量比为5.5%~7.5%,该质量比的草酸量可以和硝酸铜废液中铜离子充分反应。
上述步骤s03中,为草酸铜固体的溶解过程,通过加入氨水可以使草酸铜固体完全溶解,形成铜氨溶液;进一步地,所用的氨水的质量分数为8%~12%,该浓度范围内的氨水可以更好溶解草酸铜固体。因氨水溶解草酸铜固体的过程中会产生大量的热,同时会使草酸根分解生产大量二氧化碳气体,因此可以在冷却(如冷却至10~15℃条件)和抽风的条件下,用氨水溶解上述草酸铜固体,这样使得草酸铜固体溶解过程更加稳定。
上述步骤s04中,为油相萃取液的萃取过程,向溶解后形成的铜氨溶液中加入油相萃取液进行萃取处理,得到含铜的油相和萃取后的水相;含铜的油相进行后续的铜回收步骤,而得到的萃取后的水相可以用于溶解前序步骤的草酸铜固体,具体地,将萃取后的水相和氨水一起用于溶解草酸铜固体。
在一个实施例中,油相萃取液可以是高位阻β-二酮类萃取剂,如质量分数为20%~30%的β-二酮类萃取剂,上述萃取剂对铜氨溶液中的铜离子具有很好的萃取效果,本实施例中优选mextral984h。具体地,可以按体积比o(油相)/w(水相)=3:1,向铜氨溶液中加入油相萃取液,从而使铜离子从水相转移至油相中。
上述步骤s05,为水相反萃液的反萃过程,向萃取处理后得到的含铜的油相中加入水相反萃液进行反萃处理,得到硫酸铜溶液和反萃后的油相;硫酸铜溶液可以直接进行电解处理得到电解铜,而反萃后的油相可以用于前序的萃取过程,具体地,反萃后的油相和前序的油相萃取剂一起用于萃取铜氨溶液,即向铜氨溶液中加入油相萃取剂和反萃后的油相进行萃取处理。
在一个实施例中,水相反萃液是硫酸溶液,如质量数为15%~20%的硫酸溶液。上述硫酸溶液可以对含铜的油相中的铜离子具有很好的反萃效果,具体地,可以按体积比o(油相)/w(水相)=1:1,向含铜的油相中加入上述硫酸溶液,从而使铜离子从油相转移至水相中,得到适合电解的硫酸铜溶液。
上述步骤s06中,为硫酸铜溶液的电解处理过程。可以将硫酸铜溶液直接泵入电解槽中进行直流电解使铜沉积在铜阴极板上,从而实现硝酸铜废液的电解回收,脱铜后的电解液则可收集返回至上述反萃处理步骤中进行反萃处理工作,如此形成了一个资源循环利用的体系,还实现了价值的最大化。
如图2所示,是本申请实施例提供的铜回收方法具体循环过程示意图,其详细介绍了使用的设备和操作流程;具体步骤如下:
(1)步骤s01:提供硝酸铜废液;
具体地,用硝酸铜废液桶收集硝酸铜废液,提供铜回收的原料来源。
(2)步骤s02:向硝酸铜废液中加入草酸进行混合处理,然后固液分离,得到草酸铜固体和再生液;
具体地,将硝酸铜废液桶中收集的硝酸铜废液通入搅拌沉淀桶中,加入质量比3.5%~4.5%的草酸搅拌并曝气2h后静置自然沉降6~8h,溶液实现明显的固液分层,然后通过气动隔膜泵将混合液泵入隔膜压滤机中进行压滤,得到的滤液为再生液存储于再生液桶中,滤饼为草酸铜固体;再生液泵入再生液调整桶(即调配槽)中分析其酸度和参数后,补加相应硝酸及添加剂回到硝酸蚀铜线的生产工序进行工作。
(3)步骤s03:用氨水溶解草酸铜固体,得到铜氨溶液;
具体地,将滤饼打碎后转入沉淀溶解桶的搅拌缸体内,加入质量分数为10%氨水进行混合,开启搅拌至固体完全溶解,形成铜氨溶液,其中搅拌缸带有冷却系统及抽风系统。
(4)步骤s04:向铜氨溶液中加入油相萃取液进行萃取处理,得到含铜的油相和萃取后的水相;
具体地,将铜氨溶液转入萃取槽中,加入油相萃取液进行萃取工作,油相萃取液为高位阻β-二酮类萃取剂,其质量含量为20%~30%;此过程中铜离子转移至油相萃取液中,萃取后的水相为脱铜后的溶液可收集储存回到上一步中进行草酸铜固体的溶解工作。
(5)步骤s05:向含铜的油相中加入水相反萃液进行反萃处理,得到硫酸铜溶液和反萃后的油相;
具体地,将萃取处理得到的含铜的油相转入反萃槽中,加入水相反萃液进行反萃工作,水相反萃液为质量含量为15%~20%的硫酸溶液;反萃后形成的水相即为硫酸铜溶液,而反萃后的油相则可以反回萃取槽中进行上一步的萃取工作。
(6)步骤s06:将上述硫酸铜溶液进行电解处理,得到铜。
具体地,将反萃得到的水相硫酸铜溶液直接泵入电解槽(阳极为铅板、钛板中的一种,考虑到成本问题优选为铅板;阴极为铜片或不锈钢板,考虑到铜品相及操作问题优选为铜片)中进行直流电解,使铜沉积在阴极板上,从而实现硝酸铜废液的电解铜回收,脱铜后的电解液则可收集返回至反萃槽中进行反萃工作,如此形成了一个资源循环利用的体系。
下面结合具体实施例进行说明。
实施例1
一种从硝酸铜废液中进行铜回收的方法,包括如下步骤:
提供硝酸铜废液样品,样品酸度(h 的平衡浓度)2.0mol/l,铜离子浓度48g/l。往1l上述硝酸铜废液中加入54g草酸,搅拌30min,曝气2h后静置自然沉降6~8h,过滤后对固体进行干燥处理,得到干燥的草酸铜固体92g;滤液主要成分为硝酸,其中酸度3.2mol/l,补加65%的硝酸后可以回到生产线继续使用。上述干燥的草酸铜固体用质量分数为10%的氨水溶解,待固体全部溶解得到铜氨溶液。向上述铜氨溶液中加入mextral984h萃取剂,其中体积比o/w=3:1,此时铜离子从水相转移至油相中,静置分层后水相收集后可以继续溶解草酸铜,油相为含铜的油相。按体积比o/w=1:1,向含铜的油相中加入质量分数为20%的硫酸溶液,进行反萃处理,得到硫酸铜溶液和反萃后的油相。其中的硫酸铜溶液经过电解处理(其中电流密度为300-600a/m3),在阴极得到35g高纯度的板状铜块,电解铜块的纯度在99%以上,其xrd图如图3所示。
以上所述仅为本申请的较佳实施例而已,并不用以限制本申请,凡在本申请的精神和原则之内所作的任何修改、等同替换和改进等,均应包含在本申请的保护范围之内。
本文用于企业家、创业者技术爱好者查询,结果仅供参考。