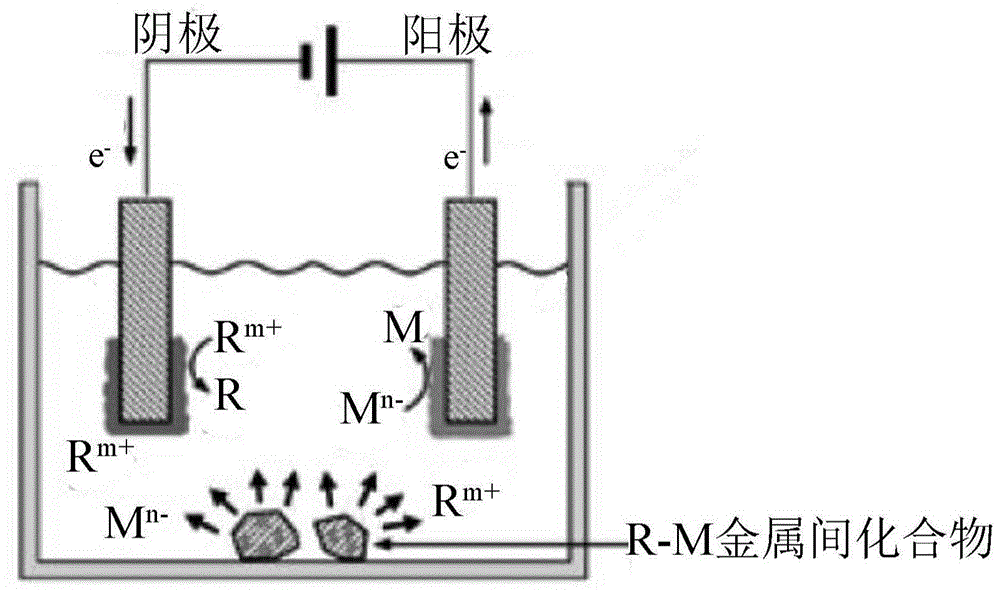
本发明涉及贵金属回收领域,更具体地讲,涉及一种从含贵金属催化剂中回收贵金属的方法。
背景技术:
目前,对于贵金属的回收一般采用湿法工艺和火法工艺。
湿法工艺一般采用强氧化性溶剂(如王水、hcl cl2等)将催化剂中的活性组分溶解,固液分离后得到含贵金属的溶液,然后通过进一步富集和传统精炼(溶剂萃取、离子交换、还原等)实现pt、pd、rh等贵金属的相互分离和提纯。虽然湿法工艺具有设备投资小、能耗低的优点,但仍然存在以下缺点:
(1)采用大量强氧化性溶剂对贵金属富集物进行长时间氧化溶解和络合,效率低,且产生了大量难处理有害废液;
(2)由于各贵金属络合物在水溶液中具有相似的化学性质,它们的相互分离需要通过冗长且复杂的处理(如离子交换、溶剂萃取、还原沉淀等)才能实现,回收效率低、环境影响大;
(3)浸出渣中通常还含有一定量的贵金属,导致贵金属回收率低(如铑回收率<90%)。
火法工艺是利用熔融态的铜、铁等捕集金属或铜锍、镍锍等硫化物共熔体对贵金属具有较强亲和力的特性,采用电弧熔炼、等离子体熔炼等技术实现贵金属的富集,然后同样采用强氧化性溶剂(如王水、hcl cl2等)将贵金属富集物溶解,接着通过进一步富集和传统精炼(溶剂萃取、离子交换、还原等)实现pt、pd、rh等贵金属的相互分离和提纯。火法工艺虽然具有处理量大、金属回收率高的优点,但存在设备投资大、能耗高等缺点。
技术实现要素:
针对现有技术中存在的不足,本发明的目的之一在于解决上述现有技术中存在的一个或多个问题。例如,本发明的目的之一在于提供一种操作简便、流程短、效率高、零排放且零污染的从含贵金属催化剂中回收贵金属的方法。
本发明提供了一种从含贵金属催化剂中回收贵金属的方法,可以包括以下步骤:利用活性金属r对催化剂中所含贵金属m进行合金化处理,分离后得到r-m金属间化合物,其中,活性金属r为na、ca、mg、li和ba中的一种,m为au、ag、pt、rh、pd、ir、os和ru中的至少一种;将r-m金属间化合物溶解在含活性金属阳离子rm 的卤化物熔盐中,施加电压进行电化学沉积,在阳极上获得贵金属单质,在阴极上获得活性金属单质,其中,m 表示电荷数。
本发明回收方法的原理包括:
首先,活性金属r与催化剂中的贵金属m通过合金化处理形成r-m金属间化合物。其次,将r-m金属间化合物溶解在含活性金属氧离子rm 的卤化物熔盐中,r-m金属间化合物溶解在熔盐中后,活性金属r以rm 离子形式存在,贵金属m以mn-离子形式存在。施加电压后电解,在阴极和阳极分别发生如下反应:
阴极:
rm me-→r(1)
阳极:
mn-→m ne-(2)
其中,r表示活性金属,可以为na(钠)、ca(钙)、mg(镁)、li(锂)和ba(钡)中的一种。m 表示r离子所带的正电荷。m表示贵金属,可以为au(金)、ag(银)、pt(铂)、rh(铑)、pd(钯)、ir(铱)、os(锇)和ru(钌)中的至少一种。n-表示m离子所带的负电荷。e-表示电子电量。
与现有技术相比,本发明的有益效果至少包括以下中的至少一项:
(1)本发明的方法通过将贵金属合金化后进行双极电解,可以一步得到贵金属,操作简便,流程短,效率高,处理时间短。
(2)本发明的方法能够实现对活性金属的回收再利用,实现活性金属的零消耗;
(3)本发明的方法在电解过程中施加的电压小于熔盐分解电压,熔盐不会分解,并且在阳极不会产生氯气等污染气体,且整个处理过程不会有废水等污染物的产生,环境友好,能够实现零排放、零污染。
附图说明
通过下面结合附图进行的描述,本发明的上述和其他目的和特点将会变得更加清楚,其中:
图1示出了本发明一个示例性实施例在熔盐中电解r-m金属间化合物示意图。
具体实施方式
在下文中,将结合附图和示例性实施例详细地描述根据本发明的从含贵金属催化剂中回收贵金属的方法。
本发明提供了一种从含贵金属催化剂中回收贵金属的方法,在本发明的从含贵金属催化剂中回收贵金属的方法的一个示例性实施例中,可以包括:
s01,利用活性金属r对催化剂中所含贵金属m进行合金化处理,分离后得到r-m金属间化合物,其中,活性金属r为na、ca、mg、li和ba中的一种,m为au、ag、pt、rh、pd、ir、os和ru中的至少一种。由于催化剂中可能含有载体,因此上述分离可以包括使载体与r-m金属间化合物之间进行分离。
s02,将r-m金属间化合物溶解在含活性金属阳离子rm 的卤化物熔盐中,施加电压进行电化学沉积,在阳极上获得贵金属单质,在阴极上获得活性金属单质,其中,m 表示电荷数。
进一步地,含贵金属m的催化剂可以为包含au、ag、pt、rh、pd、ir、os和ru中一种或两种以上贵金属元素的催化剂。例如,催化剂可以为pt-pd-rh三元失效汽车尾气净化催化剂,该汽车尾气净化催化剂可以由陶瓷载体、多孔涂层和铂族金属活性组分组成,铂族金属可以以1nm~10nm(纳米)的粒径大小分散在涂层中。再例如,催化剂还可以为pd-c催化剂、pt-c催化剂、ru-c催化剂或pt-pd-c催化剂等。当然,本发明的催化剂不限于此,含有贵金属的催化剂均可使用本发明的方法回收贵金属。
进一步地,利用活性金属r对催化剂中所含贵金属m进行合金化处理可以包括以下步骤:
将活性金属r与含贵金属m的催化剂分别置于反应器的相对侧,反应器抽真空后密封,分别控制活性金属r侧的温度为500℃~700℃,含贵金属m的催化剂侧的温度为700℃~1000℃,保温至反应结束,完成催化剂中所含贵金属m的合金化,得到r-m金属间化合物。例如,可以采用石英管或不锈钢作为反应器,将活性金属与催化剂分别置于石英管的两端,抽真空后密封。然后将密封后的石英管放入两段加热卧式管式炉进行加热,通过独立控制,使得活性金属与催化剂所在位置的温度不同。维持加热温度一段时间后,将密封的石英管从管式炉中抽出,放入水中急冷,完成活性金属与贵金属的合金化处理。对于催化剂而言,例如对于实际废弃的pt-pd-rh三元汽车尾气净化催化剂,其结构和表面形状复杂,通过上述的合金化方法,由于活性金属的饱和蒸气压较大,而贵金属的饱和蒸气压较小,活性金属能够挥发并以蒸气的形式与无挥发的贵金属反应,能够在催化剂表面及内部快速扩散迁移,最终形成r-m金属间化合物,合金化处理操作简单。
以上,优选地,可以在反应器中部附近的位置(例如,中部位置)加入金属钛以吸收反应器中的残余氧气。反应器中加热的时间使催化剂中的贵金属全部与活性金属生成金属间化合物即可。例如,反应器加热的时间可以是48小时~72小时。加入反应器中的活性金属可以是块状或者粒装,有利于活性金属的蒸发。加入的催化剂可以是经粉碎后的催化剂,催化剂的颗粒直径小,比表面积大,便于贵金属与活性金属反应。活性金属使用的量可以是合金化贵金属的理论用量,当然,为了确保将贵金属全部合金化,活性金属的添加量可以相比于理论用量多。
进一步地,利用活性金属r对催化剂中所含贵金属m进行合金化处理之前还包括对催化剂进行预处理后再进行粉碎处理。预处理可以包括对催化剂进行细磨、焙烧或溶浸处理以打开贵金属的包裹,或进行试剂还原处理。例如,由于pt-pd-rh三元失效汽车尾气净化催化剂结构及表面形状复杂,将pt-pd-rh三元失效汽车尾气净化催化剂预处理后粉碎,再利用活性金属r对催化剂中所含贵金属m进行合金化处理,将组成催化剂的载体与r-m金属间化合物分离,得到r-m金属间化合物。
进一步地,步骤s02中施加电压进行电化学沉积的示意图如图1所示。将r-m金属间化合物溶解在含活性金属阳离子rm 的卤化物熔盐中进行电解,在阴极上析出活性金属r,在阳极上析出贵金属m,分别发生上述反应(1)和(2)。施加的电压既需要大于贵金属氧化成金属的理论电极电势,也需要小于熔盐的分解电压,因此,施加的电压可以根据催化剂所含的贵金属种类在0.6v~1.6v之间选择。电解的温度可以设置在600℃~800℃。电解的温度越低,能耗越低,但电解的温度不能低于熔盐的熔点,因此,将温度控制在600℃~800℃。
以上,对于真实pt-pd-rh三元失效汽车尾气净化催化剂而言,回收真实使用催化剂中的贵金属相比于回收单一纯贵金属或贵金属合金,由于真实催化剂中的铂族金属是以10纳米左右大小分散在涂层中,且含量极低,合金化难度大。另外,真实的pt-pd-rh三元催化剂溶解在熔盐中的过程也会变得复杂,毕竟不只是ba-pt、na-au等简单的二元合金,而是多元合金。因此,设置的电解温度和电压需要综合考虑真实催化剂所具有的特性。
为了便于对pt-pd-rh三元失效汽车尾气净化催化剂中各贵金属进行分离回收,可以在电解过程中进行分步电解。具体分步电解过程包括:保持600℃~800℃的温度下,施加0.7v~0.85v的电压至rh从阳极析出完毕后回收金属rh,得到金属rh;然后调整电压至0.95v~1.1v至pd从阳极析出完毕后回收金属pd,得到金属pd;最后调整电压至1.2v~1.6v至pt从阳极析出完毕后回收金属pt,得到金属pt。通过上述进行分步电解,能够实现对rh、pd和pt的分步提取。优选地,分步电解的过程包括:保持600℃~800℃的温度下,施加0.8v的电压至rh从阳极析出完毕后回收金属rh,然后调整电压至1.0v至pd从阳极析出完毕后回收金属pd,最后调整电压至1.4v至pt从阳极析出完毕后回收金属pt。上述分别对应各个金属的电解电压为最适的电解电压。通过设置上述电解电压,能够较好的实现将各金属分别独立的电解沉积出来,可以较好地避免其中的两种或三种金属同时沉积出来而形成混合物,并且通过上述设置的电压能够有更好的电解效果,使贵金属的收得率更高。更优先地,为了节约能耗的同时进一步提高电解效率及贵金属回收率,将电解的温度与电压进行配合设置,具体地,包括在700℃~750℃下施加0.8v的电压电解回收rh,在700℃~780℃下施加1.0v的电压电解回收pd,在750℃~800℃下施加1.4v的电压电解回收pt,使用上述的温度区间和电压相互配合电解能够将rh、pd和pt的收得率平均提高2%左右。
进一步地,阳极和阴极之间的极间距可以控制在5cm~20cm之间。极间距小,能够增大电流效率;极间距过小可能会造成极间短路,因此,将极间距设置在5cm~20cm。优选地,将极间距设置在5cm~8cm,这样在确保不会发生极间短路的同时使电流效率达到最大化。
以上,通过上述设置的极间距与电解温度、电解电压相互配合,能够确保贵金属有好的电流效率和金属回收率。
进一步地,电解的时间可以为2小时以上,例如,可以为4小时。当然,本发明的电解时间不限于此,至熔盐中的贵金属不再电解沉积到阳极上即可。
进一步地,阴极可以为钼棒,阳极可以为碳棒。当然,本发明的阴极和阳极不限于此,阴极还可以为钨、钽等其它惰性金属。
进一步地,含活性金属阳离子rm 的卤化物熔盐可以为单一氯化物熔盐、单一氟化物熔盐、单一碘化物熔盐,或者不通种类熔盐的混合物等。例如,可以是氯化锂、氯化镁、氯化钠、氟化锂或碘化钠中的一种或两种以上的组合物。
为了更好地理解本发明的上述示例性实施例,下面结合具体示例对其进行进一步说明。
示例1
步骤1,将pd-c催化剂粉碎。
步骤2,利用活性金属li对pd-c催化剂进行合金化,生成li-pd金属间化合物。
步骤3,将li-pd金属间化合物溶于30mol%lif-70mol%licl熔盐后,施加电压进行电解,设置的电解温度为620℃,施加电压为1.0v,电解时间为3小时,在阳极上得到pd,在阴极上得到金属li。
示例2
步骤1,将pt-pd-rh三元催化剂粉碎后,利用活性金属na对催化剂进行合金化处理,生成na-pt-pd-rh金属间化合物。
步骤2,将催化剂的陶瓷基体与金属间化合物分离,得到分离后的na-pt-pd-rh金属间化合物。
步骤3,将金属间化合物溶于80mol%nai-20mol%nacl熔盐后,施加电压进行电解,设置极间距为8cm,温度为700℃,施加0.7v的电压至rh从阳极析出完毕后回收金属rh,得到金属rh;然后调整电压至0.95v至pd从阳极析出完毕后回收金属pd,得到金属pd;最后调整电压至1.2v至pt从阳极析出完毕后回收金属pt,得到金属pt。
示例3
步骤1,将pt-pd-rh三元催化剂粉碎后,利用活性金属na对催化剂进行合金化处理,生成na-pt-pd-rh金属间化合物。
步骤2,将催化剂的陶瓷基体与金属间化合物分离,得到分离后的na-pt-pd-rh金属间化合物。
步骤3,将金属间化合物溶于80mol%nai-20mol%nacl熔盐后,施加电压进行电解,设置极间距为8cm,温度为700℃,施加0.8v的电压至rh从阳极析出完毕后回收金属rh,得到金属rh;然后调整电压至1.0v至pd从阳极析出完毕后回收金属pd,得到金属pd;最后调整电压至1.4v至pt从阳极析出完毕后回收金属pt,得到金属pt。
示例4
步骤1,将pt-pd-rh三元催化剂粉碎后,利用活性金属na对催化剂进行合金化处理,生成na-pt-pd-rh金属间化合物。
步骤2,将催化剂的陶瓷基体与金属间化合物分离,得到分离后的na-pt-pd-rh金属间化合物。
步骤3,将金属间化合物溶于80mol%nai-20mol%nacl熔盐后,施加电压进行电解,设置极间距为8cm,温度为720℃,施加0.8v的电压至rh从阳极析出完毕后回收金属rh,得到金属rh;然后调整温度至750℃,电压至1.0v至pd从阳极析出完毕后回收金属pd,得到金属pd;最后调整温度至780℃,电压至1.4v至pt从阳极析出完毕后回收金属pt,得到金属pt。
上述示例2~示例4均电解至贵金属不再析出为止。分别计算上述示例2~示例4中各种贵金属回收的电流效率η如下表1所示,其中,
表1示例2~示例4各贵金属的电流效率统计
通过表1可以看出,对比示例2和示例3,示例3使用更适的电解电压会增加贵金属回收的电流效率。对比示例2和示例4,示例4分别根据不同的贵金属种类对应设置电解温度,可以进一步提高贵金属回收的电流效率。
尽管上面已经通过结合示例性实施例描述了本发明,但是本领域技术人员应该清楚,在不脱离权利要求所限定的精神和范围的情况下,可对本发明的示例性实施例进行各种修改和改变。
本文用于企业家、创业者技术爱好者查询,结果仅供参考。