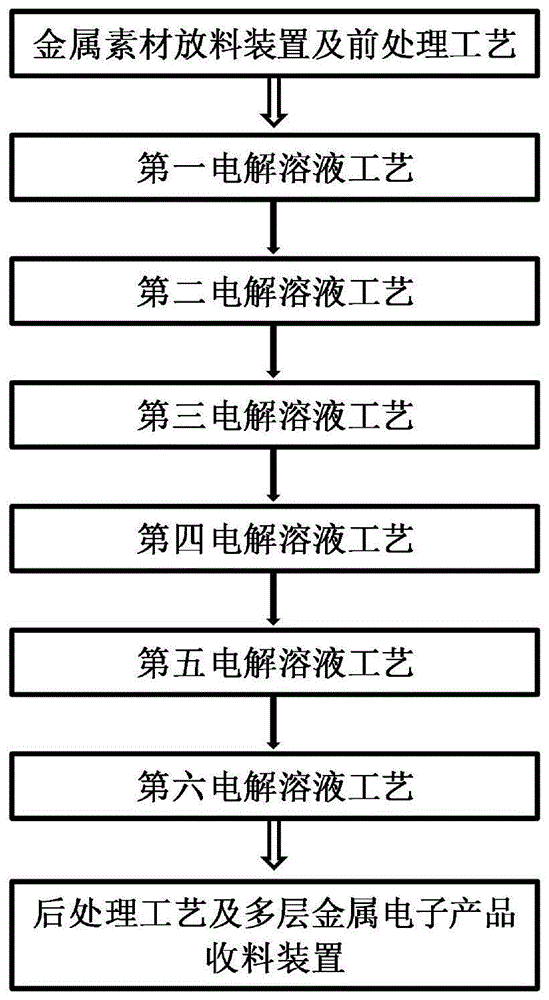
本发明涉及多层电解金属端子的技术领域,尤其是一种电解处理生产设备制备多层电解金属端子的连续生产方法。
背景技术:
多层电解金属端子是各种电子产业的重要基础原材料,具有优良的导电性、优异的插拔耐磨性及优异的耐腐蚀性能等,是生产制造精密、高端电子产品的重要原材料,在航天航空、医疗器械、现代电子信息产业的各种通信设备等领域具有越来越广泛的应用前景。因此,多层电解金属端子在前述领域中备受关注,尤其在目前现代电子信息产业发展迅猛的形势下,急需能够迅速对应生产制造多层电解金属端子的表面处理生产设备。
但是,目前的连续表面处理生产设备都是依据表面多层电解金属端子的规格要求,制造成套的固定整体模式的表面处理生产设备,面对多变的各种不同金属的表面多层电解金属端子的生产制造需求,由于金属种类的不同,既不能直接使用前述的表面处理生产设备进行生产制造,也不能将前述的生产设备不需要的工艺部分拆解替换成所需的工艺部分进行使用,因此,目前的表面处理生产设备满足不了多变的表面多层电解金属端子的生产制造需求。
专利文献1,日本发明专利,公开号jp2019-206730a,公开了一种在基材的表面上形成多层电解金属层以提高电子部件材料的性能,表面处理的金属材料的表面上电解ni、sn和ag,通过回流处理条件所形成的各层之间的ni3sn4、ag3sn合金得到ffc端子或fpc端子具有较好的接触电阻和耐插拔性能。
专利文献2,日本发明专利,公开号jp6267404b1,公开了一种能抑制了锡晶须的电解金属材料的方法,通过三层电解金属的组合,即下层构成元素ni、cr、mn、fe、co和cu,中间层是由下层元素和sn或in形成的合金,最上层由ag、au、pt、pd、ru、rh、os和ir与sn或in形成的合金;所述方法提供的材料即使暴露于高温环境下也保持了良好的可焊性和低的接触电阻,并且端子和连接器的插入力较低。
专利文献3,日本发明专利,公开号jp2020-111796a,公开了一种在基材上电解进金属下层、中间层和上层,通过将厚度和金属组成进行最佳组合,得到的材料具有能有效抑制锡晶须的特性、及耐磨性和高耐久性。
专利文献4,日本发明专利,公开号p2018-123422a,公开了一种三层电解金属层中进行sn镀层的常规镀层材料中,为了提高抗晶须性并进一步减小插入/拔出力,应减小sn镀层厚度的工艺方法,得到的材料具有可焊性和低接触电阻并且具有低的端子和连接器的插入力。
专利文献5,日本发明专利,公开号jp2008-177261a,公开了一种在导体表面形成镍磷合金层、中间电解钯用作防腐层、最表面电解金层的工艺方法,提供的电解金属材料几乎不被腐蚀,并确保了焊料的封装性能。
专利文献6,日本发明专利,wo2015-198914,公开了一种具有优异的耐腐蚀性的多层电解金属方法,通过至少包含电解铬、锡和镍,以及使用包含三胺化合物和氟化物的酸性锡-镍合金电解溶液在铬镀膜下方形成的电解金属层。
专利文献7,日本发明专利,公开号jp2018-159104a,公开了一种在保持导电性和强度的同时具有优异的镀覆性和弯曲加工的cu-cr-zr-ti合金材料,能适合用作端子、连接器、开关、插座继电器、引线框架等电子零件的材料,特别是散发大热量及传导大电流的电子零件的材料。
专利文献8,日本发明专利,公开号jp1989-83686a,公开了一种适用于形成用于将部件安装在金属化陶瓷基板上的ni-au合金的多层电解金属的方法,能提供电解金属层之间结合力强、耐腐蚀优异的电子产品。
专利文献9,中国发明专利,公开号cn101016639a,公开了一种钛基体电镀铂镀层工艺,制得的钛涂覆铂的电极材料具有良好结合力、镀层光亮致密的特点。
专利文献10,中国发明专利,公开号cn108130566a,公开了一种用于镍基高温合金表面电镀铂薄膜的电镀液及其电镀方法。
专利文献11,美国发明专利,公开号us3671408a,公开了一种铑铂合金的电镀方法,该方法可以在各种磷铜、铜、黄铜、镍、软钢、银等金属材料上进行电解,为了防止金属材料置换溶解进入铑铂合金溶液,预先在金属材料表面电解析出钯、金等,达到预防材料金属置换溶解维护铑铂合金溶液的目的,电镀方法的产品铑铂合金具有应力低、插拔耐磨性优异的特点。
专利文献12,日本发明专利,公开号p2020-169360a,公开了一种铋-锑合金电镀溶液,通过使用电镀液而形成的镀膜具有优异的滑动部件,可用于电镀的电镀液可以优选用作发动机部件例如汽油和柴油发动机的轴承的覆盖层。
专利文献13,中国发明专利,公开号cn110829080a,公开了一种导电端子,其由金属铜板制成,导电端子包括用来与对接连接器对接的接触区域,接触区域在金属铜板表面电镀形成有金属镀层;金属镀层至少包括第一铑合金镀层、第二铑合金镀层以及多个耐腐蚀层。在导电端子的表面电镀至少两层铑合金镀层,从而可以提高导电端子的抗电解腐蚀及化学腐蚀,提升了导电端子的性能,同时延长了导电端子的使用寿命。
专利文献14,中国发明专利,公开号cn111525314a,公开了一种端子表面电解多层金属的方法,导电端子包括用来与一个对接连接器对接的接触区域,接触区域在金属铜板表面电镀形成金属镀层;金属镀层至少包括第一铂镀层、第二铂镀层以及多个耐腐蚀层。在导电端子的表面电镀至少两层镀铂,从而可以使导电端子的抗电解腐蚀性及抗化学腐蚀性能增强,同时还降低了导电端子电镀的成本。
专利文献15,中国发明专利,公开号cn110350339a,公开了一种第一镀层为金属镍磷混合物镀层或者金属镍镀层、外表镀层为包括金属铑合金的多层电解金属端子具有优良的耐腐蚀和降低产品发生龟裂的特征。
专利文献16,中国发明专利,公开号cn111370894a,公开了一种可提高导电端子的防腐蚀性的表面电解多层金属的制造方法。
专利文献17,中国发明专利,公开号cn108400463a,公开了一种导电端子依次镀于铜素材外侧的镍钨合金、钯镍合金镀层,提高导电端子的防腐蚀性。
专利文献18,中国发明专利,公开号cn107546515a,公开了一种导电端子包括铜素材、镀于铜素材外侧的金属材料或合金及位于最外侧的铑或铑钌合金等材料,通过将导电端子的外层都有铑或铑钌合金,提高导电端子的防腐蚀性。
专利文献19,美国发明专利,公开号us3793162a,公开了一种电解析出的钌膜厚即使超过5μm以上也不发生断裂剥离的电子元器件的表面镀钌方法。
专利文献20,日本发明专利,公开号p2019-90086a,公开了一种电解镍磷钨合金电镀方法,能为模具表面提供高耐磨性和耐腐蚀性的合金电解镀层。
专利文献21,日本发明专利,公开号p2020-172675a,公开了一种连接器的端子材料和连接器的端子的制造方法,能够改善耐磨性和耐热性的用于连接器的端子材料和用于连接器的端子。
专利文献22,日本发明专利,p2019-203156a,公开了一种电解钯铜的合金溶液,可以获得很少有诸如针孔和裂纹的缺陷电解钯-铜合金箔,钯-铜合金镀液被广泛用于形成用于装饰品、牙科材料、电子材料、催化剂材料等的钯-铜合金箔。
专利文献23,日本发明专利,p2020-56057a,公开了一种连接器端子材料的制造方法,连接器端子和连接器端子材料,其能够改善耐磨性和耐热性。
专利文献24,中国发明专利,公开号cn108376850a,公开了一种导电端子镀层及连接器的制造方法,镀银锡合金方法提供耐腐蚀性优良的连接器产品。
针对在实际表面处理工业领域中没有能够满足多变的多层电解金属端子产品需求的多层电解金属连续生产方法及端子产品的问题,以及文献记载的导电端子相关的制备方法问题概述如下:
专利文献1~4提供的方法无法满足多变的生产制造多层电解金属端子的需求;专利文献5~12提供的多层电解金属方法及合金产品不能满足现代电子信息产业中高端电子产品所要求的优良的耐插拔耐磨性能及优异的耐腐蚀性能的特别需求;专利文献13~18的多层电解金属端子的表面处理工艺过于繁杂,需要有更加简洁具有同等功效的表面处理工艺;专利文献19~24的各种贵金属及合金的表面处理方法均不能满足端子表面多层电解金属工艺的需求。
技术实现要素:
本发明要解决的技术问题是:为了解决上述背景技术中存在的问题,提供一种电解处理生产设备制备多层电解金属端子的连续生产方法,通过模组方式,最大限度充分利用同一台连续表面处理生产设备,将各种不同电解溶液工艺进行排列组合,生产的多层电解金属端子产品种类繁多、具有优良的导电性、优异的插拔耐磨性和耐腐蚀性能等特点,完全能够满足多层电解金属端子产品的生产制造需求。
本发明解决其技术问题所采用的技术方案是:一种电解处理生产设备制备多层电解金属端子的连续生产方法,包括通用的金属素材放料装置及前处理工艺和后处理工艺及多层金属电子产品收料装置,还包括电解溶液工艺模组,所述电解溶液工艺模组包括六套独立的电解溶液工艺,分别为第一电解溶液工艺、第二电解溶液工艺、第三电解溶液工艺、第四电解溶液工艺、第五电解溶液工艺以及第六电解溶液工艺;每个电解溶液工艺从多个电解模组中根据产品规格性能需要进行选择,每个电解模组由2~4个相同的电解装置组成,通过2~6个不同的电解溶液工艺组合成的连续表面电解处理生产设备,制备得到在金属端子表面具有的2~6层金属薄膜的多层电解金属端子。
进一步具体地说,上述技术方案中,所述六套独立的电解溶液工艺的电解溶液各不相同,即六套独立的电解溶液工艺包括六种电解溶液;每个独立的电解溶液工艺由2~4个独立的电解槽组成,每个电解槽配备独立的电解用整流电源;六套独立的电解溶液工艺任意排列组合,构筑成能制造加工各种各样的多层电解金属端子的连续表面处理生产设备;当需要所述六种电解溶液以外的电解溶液时,可以将第七套的电解溶液工艺追加到所需的位置;或者当所述六套独立的电解溶液工艺当中有不需要的电解溶液工艺时,可以用第七套的电解溶液工艺取而代之。
进一步具体地说,上述技术方案中,所述金属薄膜包括第一电解金属薄膜、第二电解金属薄膜、第三电解金属薄膜、第四电解金属薄膜、第五电解金属薄膜以及第六电解金属薄膜,所述第一电解金属薄膜是镍、钨、金的单元金属、二元合金及三元合金;所述第二电解金属薄膜是钯、银、铂的单元金属、二元合金及三元合金;所述第三电解金属薄膜是金、镍、钴形成的二元合金;所述第四电解金属薄膜是金、银、锡的单元金属、二元合金及三元合金;所述第五电解金属薄膜是银、铂、钯形成的单元金属和二元合金;所述第六电解金属薄膜是金、锑、镍形成的单元金属和二元合金。
进一步具体地说,上述技术方案中,所述第一电解金属薄膜的膜厚范围0.38~2.54μm;所述第二电解金属薄膜的膜厚范围0.38~1.13μm;所述第三电解金属薄膜的膜厚范围0.05~0.76μm;所述第四电解金属薄膜的膜厚范围0.76~3.81μm;所述第五电解金属薄膜的膜厚范围0.25~0.54μm;所述第六电解金属薄膜的膜厚范围0.07~0.37μm。
进一步具体地说,上述技术方案中,金属素材的表面电解方式包括电解溶液浸入方式和电解溶液喷射方式;所述电解溶液浸入方式是将金属素材全部浸入电解溶液,或将金属素材局部浸入电解溶液,或通过遮蔽治具掩蔽金属素材局部后浸入电解溶液;所述电解溶液喷射方式是利用电解治具对金属素材不需要电解处理的部分进行遮蔽,通过电解溶液对金属素材表面进行喷射。
进一步具体地说,上述技术方案中,电解装置的整流电源包括高频整流电源、脉冲整流电源和脉冲周期性逆向电源,三种电源具有不同功能,得到不同性能的多层电解金属端子。
进一步具体地说,上述技术方案中,所述电解槽的电解阳极依据金属素材的形状、电解处理区域的变化、电解处理区域的形状和电解处理区域的面积大小而发生变化。
进一步具体地说,上述技术方案中,所述整流电源与电解阳极的不同组合,电解析出的金属薄膜具有不同性能。
进一步具体地说,上述技术方案中,电解析出的单元金属包括金、银、铂、钯、镍、钴、铑、铟、铁、钌、锡、锰、锌、铱、锑、铬和铜;电解析出的二元合金包括金钴、金镍、钯镍、锌锡、镍磷、金锡、金锑、铁镍、镍锡、镍钨、铑钌、镍钴、金银、铂银、银铜、银钨、铜钨、锌铜和锌锡;电解析出的三元合金包括镍金钨、金钴钨、金钯镍、金铁镍、镍磷钨、钴镍磷、钯镍磷、铜镍钨、镍锡铜、铁铑钌、钴铑钌、金锡铜、金银铜、金银锡、镍钴钯和铁镍锡。
进一步具体地说,上述技术方案中,所述电解析出的单元金属、二元合金和三元合金进行各种各样的排列组合,同时,在每个电解溶液工艺的多个电解装置上设定各种不同的电解条件,从而控制多层电解金属端子材料的性能,满足多种多样产品规格要求。
本发明的有益效果是:本发明的一种电解处理生产设备制备多层电解金属端子的连续生产方法,提供简单实用的生产设备操作步骤以及多层电解金属端子产品生产使用方法和产品性能评价方法;通过模组方式,最大限度充分利用同一台连续表面处理生产设备,将各种不同电解溶液工艺进行排列组合,生产的多层电解金属端子产品种类繁多、具有优良的导电性、优异的插拔耐磨性和耐腐蚀性能等特点;为生产制造精密、高端电子产品提供重要原材料基础;同时,有效地提高了多层电解金属端子连续生产设备的使用率,一机多用、极大地提高了生产效率。
附图说明
为了更清楚地说明本发明实施例或现有技术中的技术方案,下面将对实施例或现有技术描述中所需要使用的附图作简单地介绍,显而易见地,下面描述中的附图仅仅是本申请中记载的一些实施例,对于本领域普通技术人员来讲,在不付出创造性劳动的前提下,还可以根据这些附图获得其他的附图。
图1为本发明实施例的多层电解金属端子连续生产设备的流程示意图;
图2为本发明实施例1的电解镍钨合金溶液工艺模组的示意图;
图3为本发明实施例1的电解铂溶液工艺模组的示意图;
图4为本发明实施例1的电解金钴合金溶液工艺模组的示意图;
图5为本发明实施例1的第一电解金属端子的示意图;
图6为本发明实施例2的电解镍金钨合金溶液工艺模组的示意图;
图7为本发明实施例2的第二电解金属端子的示意图;
图8为本发明实施例3的电解镍溶液工艺模组的示意图;
图9为本发明实施例3的电解镍磷溶液工艺模组的示意图;
图10为本发明实施例3的电解钯溶液工艺模组的示意图;
图11为本发明实施例3的电解铑钌溶液工艺模组的示意图
图12为本发明实施例3的第三电解金属端子的示意图;
图13为本发明实施例4的电解钯镍合金溶液工艺模组的示意图;
图14为本发明实施例4的第四电解金属端子的示意图;
图15为本发明实施例5的电解铑铂合金溶液工艺模组的示意图;
图16为本发明实施例5的电解铂银合金溶液工艺模组的示意图;
图17为本发明实施列5的第五电解金属端子的示意图;
图18为本发明实施列1的样品1试验结果示意图;
图19为本发明实施列2的样品2试验结果示意图;
图20为本发明实施列3的样品3试验结果示意图;
图21为本发明实施列4的样品4试验结果示意图;
图22为本发明实施列1和2的样品1和样品2试验结果示意图;
图23为本发明实施列3和4的样品3和样品4试验结果示意图。
附图中的标号为:
10、金属素材;
11、第一导电轮;12、第二导电轮;13、第三导电轮;14、第四导电轮;
20、吹风嘴;
100、第一电解母槽;110、第二电解母槽;120、第三电解母槽;130、第四电解母槽;
200、第一电解子槽;210、第二电解子槽;220、第三电解子槽;230、第四电解子槽;
300、第一电解阳极;310、第二电解阳极;320、第三电解阳极;330、第四电解阳极;
400、第一喷射治具;410、第二喷射治具;420、第三喷射治具;
500、第一整流电源;510、第二整流电源;520、第三整流电源;530、第四整流电源;
600、第一电解金属端子;610、第二电解金属端子;620、第三电解金属端子;630、第四电解金属端子;640、第五电解金属端子。
具体实施方式
为了使本发明所解决的技术问题、技术方案及有益效果更加清楚明白,以下结合附图及实施例,对本发明进行进一步详细说明。应当理解,此处所描述的具体实施例仅仅用以解释本发明,并不用于限定本发明。
一种电解处理生产设备制备多层电解金属端子的连续生产方法,对金属材料10表面进行电解处理,通过电解溶液工艺析出金属薄膜,包括通用的金属素材放料装置及前处理工艺和后处理工艺及多层金属电子产品收料装置,还包括电解溶液工艺模组,电解溶液工艺模组包括六套独立的电解溶液工艺,分别为第一电解溶液工艺、第二电解溶液工艺、第三电解溶液工艺、第四电解溶液工艺、第五电解溶液工艺以及第六电解溶液工艺;每个电解溶液工艺从11个电解模组(见图2、图3、图4、图6、图8、图9、图10、图11、图13、图15、图16)中根据产品规格性能需要进行选择,每个电解模组由2~4个相同的电解装置组成,通过2~6个不同的电解溶液工艺组合成的连续表面电解处理生产设备,制备得到在金属端子表面具有的2~6层金属薄膜的多层电解金属端子。
六套独立的电解溶液工艺的电解溶液各不相同,即六套独立的电解溶液工艺包括六种电解溶液;每个独立的电解溶液工艺由2~4个独立的电解槽组成,每个电解槽配备独立的电解用整流电源,每个独立的电解槽配备的电解电源都能独立设定不同的电解条件。
第一电解溶液工艺的电解槽数量可以根据产品规格的要求进行选择。第二电解溶液工艺的电解槽数量也依据产品规格的要求进行选择。以此类推,第三电解溶液工艺的电解槽数量直至第六电解溶液工艺的电解槽数量也是依据产品规格的要求进行选择。
金属素材10优选端子连续材料,对材料的功能区通过多个不同的电解溶液工艺构成的多层电解金属连续生产设备及方法进行处理,优选符合多层电解金属端子产品的电解生产条件。
六套独立的电解溶液工艺任意排列组合,构筑成能制造加工各种各样的多层电解金属端子的连续表面处理生产设备;当需要六种电解溶液以外的电解溶液时,可以将第七套的电解溶液工艺追加到所需的位置;或者当六套独立的电解溶液工艺当中有不需要的电解溶液工艺时,可以用第七套的电解溶液工艺取而代之。
通过2~6个不同的电解溶液工艺进行电解析出得到在金属端子表面具有的2~6层金属薄膜。多层电解金属端子产品不局限于2~6层电解金属的范围,根据多层电解金属端子产品要求可以是更多层电解金属端子产品,并且每层既可以是电解单金属层、或是两种金属的合金层,也可以是三元合金或三元合金以上的多元合金,用于满足多层电解金属端子产品的特殊性能要求。
金属薄膜包括第一电解金属薄膜、第二电解金属薄膜、第三电解金属薄膜、第四电解金属薄膜、第五电解金属薄膜以及第六电解金属薄膜,第一电解金属薄膜是镍、钨、金的单元金属、二元合金及三元合金;第二电解金属薄膜是钯、银、铂的单元金属、二元合金及三元合金;第三电解金属薄膜是金、镍、钴形成的二元合金;第四电解金属薄膜是金、银、锡的单元金属、二元合金及三元合金;第五电解金属薄膜是银、铂、钯形成的单元金属和二元合金;第六电解金属薄膜是金、锑、镍形成的单元金属和二元合金。其中,第一电解金属薄膜需要具有良好的阻止金属素材中的金属迁移到电镀金属层中,以及阻止与其形成合金的倾向,才能保证多层电解金属端子产品的各种特殊功能,因此第一电解金属薄膜的膜厚需要具有较厚的范围才能满足要求。金属电子产品最表层的电解金属薄膜需要具有优良的导电性能,并具有较强的硬度、耐插拔、耐磨性能,因此金属电子产品最表层的电解金属薄膜的膜厚需要具有较薄的范围才能满足要求。金属电子产品最表层的电解金属薄膜的下层电解金属薄膜需要具有优良的耐插拔耐磨性能及优异的耐腐蚀性能,因此金属电子产品最表层的电解金属薄膜的下层电解金属薄膜的膜厚需要具有适中的范围才能满足要求。
第一电解金属薄膜的膜厚范围0.38~2.54μm;第二电解金属薄膜的膜厚范围0.38~1.13μm;第三电解金属薄膜的膜厚范围0.05~0.76μm;第四电解金属薄膜的膜厚范围0.76~3.81μm;第五电解金属薄膜的膜厚范围0.25~0.54μm;第六电解金属薄膜的膜厚范围0.07~0.37μm。
金属素材的表面电解方式包括电解溶液浸入方式和电解溶液喷射方式。
电解溶液浸入方式是将金属素材全部浸入电解溶液,或将金属素材局部浸入电解溶液,或通过遮蔽治具掩蔽金属素材局部后浸入电解溶液。
电解溶液喷射方式是利用电解治具对金属素材不需要电解处理的部分进行遮蔽,通过电解溶液对金属素材表面进行喷射。
如果金属素材的表面电解即可以采用表面局部的电解溶液浸入方式,又可以采用喷射方式,则优先采用喷射方式,当由于产品的形状及电解溶液的特性限制了喷射方式,则采用局部的电解溶液浸入方式。
电解装置的整流电源的选用依据电解溶液的特性和多层电解金属端子产品的规格要求,根据多层电解金属端子产品对电解析出的金属薄膜或金属膜厚的要求,电解装置的整流电源可选用高频整流电源、脉冲整流电源和脉冲周期性逆向电源,这三种电源具有不同功能,得到不同性能的多层电解金属端子。即,通过选取不同类型的整流电源,改善电解金属薄膜的性能,采用高频整流电源电解析出的金属形态晶格粗糙,致密性能较差;采用脉冲整流电源或脉冲周期性逆向电源电解析出的金属形态晶格规整细腻,致密性能优异;尤其有些电解析出合金呈现非晶态结构具有十分优异的耐腐蚀性能。
电解槽的电解阳极依据金属素材的形状、电解处理区域的变化、电解处理区域的形状和电解处理区域的面积大小而发生变化。电解阳极与金属素材之间距离的大小,影响电解金属的各种性能。
整流电源与电解阳极的不同组合,电解析出的金属薄膜具有不同性能。
电解析出的单元金属包括金(au)、银(ag)、铂(pt)、钯(pd)、镍(ni)、钴(co)、铑(rh)、铟(in)、铁(fe)、钌(ru)、锡(sn)、锰(mn)、锌(zn)、铱(ir)、锑(sb)、铬(cr)和铜(cu)等。
电解析出的二元合金包括金钴(au/co)、金镍(au/ni)、钯镍(pd/ni)、锌锡(zn/sn)、镍磷(ni/p)、金锡(au/sn)、金锑(au/sb)、铁镍(fe/ni)、镍锡(ni/sn)、镍钨(ni/w)、铑钌(rh/ru)、镍钴(ni/co)、金银(au/ag)、铂银(pt/ag)、银铜(ag/cu)、银钨(ag/w)、铜钨(cu/w)、锌铜(zn/cu)和锌锡(zn/sn)等。
电解析出的三元合金包括镍金钨(ni/au/w)、金钴钨(au/co/w)、金钯镍(au/pd/ni)、金铁镍(au/fe/ni)、镍磷钨(ni/p/w)、钴镍磷(co/ni/p)、钯镍磷(pd/ni/p)、铜镍钨(cu/ni/w)、镍锡铜(ni/sn/cu)、铁铑钌(fe/rh/ru)、钴铑钌(co/rh/ru)、金锡铜(au/sn/cu)、金银铜(au/ag/cu)、金银锡(au/ag/sn)、镍钴钯(ni/co/pd)和铁镍锡(fe/ni/sn)等。
电解析出的金属薄膜的性能主要包括三类:导电性能、插拔性能和耐腐蚀性能。
电解析出的金属薄膜的各种性能归纳在下表1中:
表1
将电解析出的单元金属、二元合金和三元合金分门别类,有效应用于多层电解金属端子的连续生产中,具体地,根据产品规格,对多层电解金属端子产品的导电性、耐腐蚀性、插拔式端子的耐磨性能等的要求,可以任意将电解析出的单元金属、二元合金和三元合金进行各种各样的排列组合,同时,在每个电解溶液工艺的多个电解装置上设定各种不同的电解条件,从而控制多层电解金属端子材料的性能,满足多种多样产品规格要求。多层电解金属端子产品中,在有些场合下,当用二元或三元电解溶液模组电解析出的二元合金或三元合金,金属电子产品性能上与两种或三种单金属的膜层具有同等以上功能。优选用较少的电解金属层,满足多层电解金属电解产品规格和性能的要求。
该电解处理生产设备制备多层电解金属端子的连续生产方法,各种电解溶液工艺的装配和拆卸简单易行;生产设备的电解治具,满足端子局部电解析出生产加工的需求;各种电解溶液工艺的组合容易进行;生产设备的连续运行的稳定性好;生产设备的机械化程度高。具体地,该电解处理生产设备制备多层电解金属端子的连续生产方法,利用实际生产设备,能够将连续金属素材加工生产成为电解金属端子产品,其制造核心为:通过电解溶液工艺的方式,最大限度充分利用同一台连续表面处理生产设备,将各种不同电解溶液工艺进行排列组合,电解生产的产品品种众多,具有优良的导电性、优异的插拔耐磨性和耐腐蚀性能等特点;为生产制造精密、高端电子产品提供重要原材料基础;由多套电解溶液工艺构成多层电解金属端子连续生产设备,有效地提高了电解金属连续生产设备的使用率,提高了多层电解金属端子连续生产设备的运转周期,一机多用、极大地提高了多层电解金属端子产品的生产效率。
实施例1
当设计的多层电解金属端子产品要求达到导电性能优异、耐腐蚀性能强的目标时,金属素材10表面的电解金属薄膜可从表1的cu、ni、ni/w、ni/w/au当中进行选择,本实施例1优选具有高硬度、高耐磨性及优异的耐腐蚀性特征的ni/w合金电解溶液。多层电解金属端子产品的中间的金属薄膜可从表1的相应栏中选取,本实施例1优选具有优异的耐腐蚀性能和良好导电性特征的pt电解溶液。多层电解金属端子产品最表面的电解金属薄膜可从表1的相应栏中选取,本实施例1优选具有优良导电性能及较好的耐磨性特征的au/co合金电解溶液。
见图1和图2,金属素材10通过金属素材放料装置及前处理之后,金属素材10被导入第一电解溶液工艺,第一电解溶液工艺采用镍钨合金电解溶液,第一电解溶液工艺由四个连续独立的电解槽组成,四个电解槽分别为第一电解母槽100、第二电解母槽110、第三电解母槽120和第四电解母槽130,每个电解母槽中配有脉冲周期性逆向电源,第一电解母槽100配置有第一整流电源500,第二电解母槽110配置有第二整流电源510,第三电解母槽120配置有第三整流电源520,第四电解母槽130配置有第四整流电源530,第一整流电源500、第二整流电源510、第三整流电源520和第四整流电源530均为脉冲周期性逆向电源,每个电解母槽内均设置有第一电解子槽200、第二电解子槽210、第三电解子槽220和第四电解子槽230,金属素材10通过每个电解槽的进出口的导向兼导电装置在电解子槽中间运行,导向兼导电装置包括第一导电轮11、第二导电轮12、第三导电轮13和第四导电轮14,第一电解子槽200的两侧设置有第一电解阳极300,第二电解子槽210的两侧设置有第二电解阳极310,第三电解子槽220的两侧设置有第三电解阳极320,第四电解子槽230的两侧设置有第四电解阳极330,第一电解阳极300与第一整流电源500的阳极输出连接,第二电解阳极310与第二整流电源510的阳极输出连接,第三电解阳极320与第三整流电源520的阳极输出连接,第四电解阳极330与第四整流电源530的阳极输出连接,第一整流电源500的阴极输出与第一导电轮11连接,第二整流电源510的阴极输出与第二导电轮12连接,第三整流电源520的阴极输出与第三导电轮13连接,第四整流电源530的阴极输出与第四导电轮14连接,每个电解槽之间都有吹风嘴20及水洗,防止金属素材10将过多的电解溶液带出。第一整流电源500、第二整流电源510、第三整流电源520和第四整流电源530通过正反脉冲周期性对金属素材10表面的电解析出及电解剥离的处理,能使电解析出的镍钨合金层具有高硬度、耐磨性能高及耐腐性能优异的特征。
见图2,第一电解溶液工艺结束后,经过至少3~7道水洗,进入见图3所示的第二电解溶液工艺,第二电解溶液工艺采用铂电解溶液,第二电解溶液工艺由三个连续独立的第一电解母槽100、第二电解母槽110和第三电解母槽120组成,三个电解母槽分别配置有第一整流电源500、第二整流电源510和第三整流电源520,三个整流电源均为高频整流电源,同时,三个电解母槽分别配置有第一喷射治具400、第二喷射治具410和第三喷射治具420,三个喷射治具均为轮式电解治具,该电解槽采用电解溶液喷射方式只对金属素材10的功能区进行电解,轮式电解治具配有与电解处理区域相对应的阳极,提高电解效率和电解金属质量;同样,每个电解槽之间都有吹风嘴20及水洗,其它操作与上述电解槽相似。三个整流电源通过轮式电解治具,只对金属素材10的功能区进行电解处理得到的铂金属层具有良好的导电性能,并在底镀层镍钨合金的衬托下具有良好的硬度及插拔耐磨性能。
见图3,第二电解溶液工艺结束后,经过至少3~7道水洗,进入见图4所示的第三电解溶液工艺,第三电解溶液工艺采用金钴合金电解溶液,第三电解溶液工艺由两个连续独立的第一电解母槽100和第二电解母槽110组成,两个电解母槽分别配置有第一整流电源500和第二整流电源510,两个整流电源均为高频整流电源,该电解槽采用电解溶液喷射方式只对金属材料的所述功能区进行电解,轮式电解治具配有与电解处理区域相对应的阳极,提高电解效率和电解金属层的质量,同样,每个电解槽之间都有吹风嘴20及水洗,其它操作与上述电解槽相似。两个整流电源通过轮式电解治具,只对金属素材10的功能区进行电解处理得到的金钴合金层具有良好的导电性能,并在底镀层铂和镍钨的衬托下具有良好的硬度及插拔耐磨性能。
见图5,实施例1得到的是从金属素材10开始的第一电解金属端子600,第一电解金属端子600具有三层金属层,分别为第一层镍钨、第二层铂、第三层金钴。第一层镍钨的膜厚为0.97μm,第二层铂的膜厚为0.57μm,第三层金钴的膜厚为0.05~0.07μm。
实施例2
见图1和图5,金属素材10通过金属素材放料装置及前处理之后,金属素材10被导入第一电解溶液工艺,第一电解溶液工艺采用镍金钨合金电解溶液,第一电解溶液工艺由四个连续独立的第一电解母槽100、第二电解母槽110、第三电解母槽120和第四电解母槽130组成,四个电解母槽分别配置有第一整流电源500、第二整流电源510、第三整流电源520和第四整流电源530,四个整流电源均为脉冲周期性逆向电源,每个电解母槽内均设置有第一电解子槽200、第二电解子槽210、第三电解子槽220和第四电解子槽230,金属素材10通过每个电解槽的进出口的导向兼导电装置在电解子槽中间运行,导向兼导电装置包括第一导电轮11、第二导电轮12、第三导电轮13和第四导电轮14,第一电解子槽200的两侧设置有第一电解阳极300,第二电解子槽210的两侧设置有第二电解阳极310,第三电解子槽220的两侧设置有第三电解阳极320,第四电解子槽230的两侧设置有第四电解阳极330,第一电解阳极300与第一整流电源500的阳极输出连接,第二电解阳极310与第二整流电源510的阳极输出连接,第三电解阳极320与第三整流电源520的阳极输出连接,第四电解阳极330与第四整流电源530的阳极输出连接,第一整流电源500的阴极输出与第一导电轮11连接,第二整流电源510的阴极输出与第二导电轮12连接,第三整流电源520的阴极输出与第三导电轮13连接,第四整流电源530的阴极输出与第四导电轮14连接,每个电解槽之间都有吹风嘴20及水洗,防止金属素材10将过多的电解溶液带出。四个整流电源通过正反脉冲周期性对金属素材10表面的电解析出及电解剥离的处理,能使电解析出的镍金钨合金层具有硬度高并且不易弯折脆裂、耐磨性能高及耐腐性能优异的特征。
第二电解溶液工艺和第三电解溶液工艺的操作与实施例1相同。
见图7,实施例2得到的是从金属素材10开始的第二电解金属端子610,第二电解金属端子610具有三层金属层,分别为第一层镍金钨,第二层铂、第三层金钴。第一层镍金钨的膜厚为1.05μm,第二层铂的膜厚为0.62μm,第三层金钴的膜厚为0.05~0.07μm。
实施例3
见图1和图8,金属素材10通过金属素材放料装置及前处理之后,金属素材10被导入第一电解溶液工艺,第一电解溶液工艺采用镍电解溶液,第一电解溶液工艺由四个连续独立的第一电解母槽100、第二电解母槽110、第三电解母槽120和第四电解母槽130组成,四个电解母槽分别配置有第一整流电源500、第二整流电源510、第三整流电源520和第四整流电源530,四个整流电源均为高频整流电源,每个电解母槽内均设置有第一电解子槽200、第二电解子槽210、第三电解子槽220和第四电解子槽230,金属素材10通过每个电解槽的进出口的导向兼导电装置在电解子槽中间运行,导向兼导电装置包括第一导电轮11、第二导电轮12、第三导电轮13和第四导电轮14,第一电解子槽200的两侧设置有第一电解阳极300,第二电解子槽210的两侧设置有第二电解阳极310,第三电解子槽220的两侧设置有第三电解阳极320,第四电解子槽230的两侧设置有第四电解阳极330,第一电解阳极300与第一整流电源500的阳极输出连接,第二电解阳极310与第二整流电源510的阳极输出连接,第三电解阳极320与第三整流电源520的阳极输出连接,第四电解阳极330与第四整流电源530的阳极输出连接,第一整流电源500的阴极输出与第一导电轮11连接,第二整流电源510的阴极输出与第二导电轮12连接,第三整流电源520的阴极输出与第三导电轮13连接,第四整流电源530的阴极输出与第四导电轮14连接,每个电解槽之间都有吹风嘴20及水洗,防止金属素材10将过多的电解溶液带出。
见图8,第一电解溶液工艺结束后,经过至少3~7道水洗,进入见图9所示的第二电解溶液工艺,第二电解溶液工艺采用镍磷合金电解溶液,第二电解溶液工艺由四个连续独立的第一电解母槽100、第二电解母槽110、第三电解母槽120和第四电解母槽130组成,四个电解母槽分别配置有第一整流电源500、第二整流电源510、第三整流电源520和第四整流电源530,四个整流电源均为高频整流电源,该电解槽采用电解溶液局部浸入方式只对金属素材10的功能区进行电解,局部电解治具配有与电解处理区域相对应的阳极,提高电解效率和电解金属层的质量;同样,每个电解槽之间都有吹风嘴20及水洗,其它操作与上述电解槽相似。
见图9,第二电解溶液工艺结束后,经过至少3~7道水洗,进入见图10所示的第三电解溶液工艺,第三电解溶液工艺采用钯电解溶液,第三电解溶液工艺由三个连续独立的第一电解母槽100、第二电解母槽110和第三电解母槽120组成,三个电解母槽分别配置有第一整流电源500、第二整流电源510和第三整流电源520,三个整流电源均为高频整流电源,该电解槽采用电解溶液局部浸入方式只对金属材料的所述功能区进行电解,局部电解治具配有与电解处理区域相对应的阳极,提高电解效率和电解金属层的质量,同样,每个电解槽之间都有吹风嘴20及水洗,其它操作与上述电解槽相似。
见图10,第三电解溶液工艺结束后,经过至少3~7道水洗,进入见图11所示的第四电解溶液工艺,第三电解溶液工艺采用铑钌合金电解溶液,第四电解溶液工艺由四个连续独立的第一电解母槽100、第二电解母槽110、第三电解母槽120和第四电解母槽130组成,四个电解母槽分别配置有第一整流电源500、第二整流电源510、第三整流电源520和第四整流电源530,四个整流电源均为高频整流电源,该电解槽采用电解溶液局部浸入方式只对金属材料的所述功能区进行电解,局部电解治具配有与电解处理区域相对应的阳极,提高电解效率和电解金属层的质量,同样,每个电解槽之间都有吹风嘴20及水洗,其它操作与上述电解槽相似。
第四电解溶液工艺结束后,经过至少3~7道水洗,进入第五电解溶液工艺,第五电解溶液工艺采用金钴合金电解溶液,第五电解溶液工艺由两个连续独立的第一电解母槽100和第二电解母槽110组成,两个电解母槽分别配置有第一整流电源500和第二整流电源510,两个整流电源均为高频整流电源,该电解槽采用电解溶液喷射方式只对金属材料的所述功能区进行电解,轮式电解治具配有与电解处理区域相对应的阳极,提高电解效率和电解金属层的质量,同样,每个电解槽之间都有吹风嘴20及水洗,其它操作与上述电解槽相似。
实施例3得到的是从金属素材10开始的第三电解金属端子620,第三电解金属端子620具有三层金属层,分别为第一层镍、第二层镍磷、第三层钯、第四层铑钌、第五层金钴,第一层镍的膜厚为1.76μm,第二层镍磷的膜厚为0.38μm,第三层钯的膜厚为0.38μm,第四层铑钌的膜厚为1.13μm,第五层金钴的膜厚为0.05~0.07μm。
实施例4
见图1和图8,金属素材10通过金属素材放料装置及前处理之后,金属素材10被导入第一电解溶液工艺,第一电解溶液工艺采用镍电解溶液,第一电解溶液工艺由四个连续独立的第一电解母槽100、第二电解母槽110、第三电解母槽120和第四电解母槽130组成,四个电解母槽分别配置有第一整流电源500、第二整流电源510、第三整流电源520和第四整流电源530,四个整流电源均为脉冲周期性逆向电源,每个电解母槽内均设置有第一电解子槽200、第二电解子槽210、第三电解子槽220和第四电解子槽230,金属素材10通过每个电解槽的进出口的导向兼导电装置在电解子槽中间运行,导向兼导电装置包括第一导电轮11、第二导电轮12、第三导电轮13和第四导电轮14,第一电解子槽200的两侧设置有第一电解阳极300,第二电解子槽210的两侧设置有第二电解阳极310,第三电解子槽220的两侧设置有第三电解阳极320,第四电解子槽230的两侧设置有第四电解阳极330,第一电解阳极300与第一整流电源500的阳极输出连接,第二电解阳极310与第二整流电源510的阳极输出连接,第三电解阳极320与第三整流电源520的阳极输出连接,第四电解阳极330与第四整流电源530的阳极输出连接,第一整流电源500的阴极输出与第一导电轮11连接,第二整流电源510的阴极输出与第二导电轮12连接,第三整流电源520的阴极输出与第三导电轮13连接,第四整流电源530的阴极输出与第四导电轮14连接,每个电解槽之间都有吹风嘴20及水洗,防止金属素材10将过多的电解溶液带出。
见图8,第一电解溶液工艺结束后,经过至少3~7道水洗,进入见图3所示的第二电解溶液工艺,第二电解溶液工艺采用钯镍合金电解溶液,第二电解溶液工艺由四个连续独立的第一电解母槽100、第二电解母槽110、第三电解母槽120和第四电解母槽130组成,四个电解母槽分别配置有第一整流电源500、第二整流电源510、第三整流电源520和第四整流电源530,四个整流电源均为高频整流电源,该电解槽采用电解溶液局部浸入方式只对金属素材10的功能区进行电解,局部电解治具配有与电解处理区域相对应的阳极,提高电解效率和电解金属质量;同样,每个电解槽之间都有吹风嘴20及水洗,其它操作与上述电解槽相似。
第二电解溶液工艺结束后,经过至少3~7道水洗,进入第三电解溶液工艺,第三电解溶液工艺采用金钴合金电解溶液,第三电解溶液工艺由两个连续独立的第一电解母槽100和第二电解母槽110组成,两个电解母槽分别配置有第一整流电源500和第二整流电源510,两个整流电源均为高频整流电源,该电解槽采用电解溶液喷射方式只对金属材料的所述功能区进行电解,轮式电解治具配有与电解处理区域相对应的阳极,提高电解效率和电解金属层的质量,同样,每个电解槽之间都有吹风嘴20及水洗,其它操作与上述电解槽相似。
见图14,实施例4得到的是从金属素材10开始的第四电解金属端子630,第四电解金属端子630具有三层金属层,分别为第一层镍、第二层钯镍、第三层金钴。第一层镍的膜厚为1.78μm,第二层钯镍的膜厚为0.45μm,第三层金钴的膜厚为0.15~0.23μm。
实施例5
见图1和图2,金属素材10通过金属素材放料装置及前处理之后,金属素材10被导入第一电解溶液工艺,第一电解溶液工艺采用镍电解溶液,第一电解溶液工艺由四个连续独立的第一电解母槽100、第二电解母槽110、第三电解母槽120和第四电解母槽130组成,四个电解母槽分别配置有第一整流电源500、第二整流电源510、第三整流电源520和第四整流电源530,四个整流电源均为脉冲周期性逆向电源,每个电解母槽内均设置有第一电解子槽200、第二电解子槽210、第三电解子槽220和第四电解子槽230,金属素材10通过每个电解槽的进出口的导向兼导电装置在电解子槽中间运行,导向兼导电装置包括第一导电轮11、第二导电轮12、第三导电轮13和第四导电轮14,第一电解子槽200的两侧设置有第一电解阳极300,第二电解子槽210的两侧设置有第二电解阳极310,第三电解子槽220的两侧设置有第三电解阳极320,第四电解子槽230的两侧设置有第四电解阳极330,第一电解阳极300与第一整流电源500的阳极输出连接,第二电解阳极310与第二整流电源510的阳极输出连接,第三电解阳极320与第三整流电源520的阳极输出连接,第四电解阳极330与第四整流电源530的阳极输出连接,第一整流电源500的阴极输出与第一导电轮11连接,第二整流电源510的阴极输出与第二导电轮12连接,第三整流电源520的阴极输出与第三导电轮13连接,第四整流电源530的阴极输出与第四导电轮14连接,每个电解槽之间都有吹风嘴20及水洗,防止金属素材10将过多的电解溶液带出。
见图8,第一电解溶液工艺结束后,经过至少3~7道水洗,进入见图2所示的第二电解溶液工艺,第二电解溶液工艺采用镍钨合金电解溶液,第二电解溶液工艺由四个连续独立的第一电解母槽100、第二电解母槽110、第三电解母槽120和第四电解母槽130组成,四个电解母槽分别配置有第一整流电源500、第二整流电源510、第三整流电源520和第四整流电源530,四个整流电源均为脉冲周期性逆向电源,每个电解母槽内均设置有第一电解子槽200、第二电解子槽210、第三电解子槽220和第四电解子槽230,金属素材10通过每个电解槽的进出口的导向兼导电装置在电解子槽中间运行,导向兼导电装置包括第一导电轮11、第二导电轮12、第三导电轮13和第四导电轮14,第一电解子槽200的两侧设置有第一电解阳极300,第二电解子槽210的两侧设置有第二电解阳极310,第三电解子槽220的两侧设置有第三电解阳极320,第四电解子槽230的两侧设置有第四电解阳极330,第一电解阳极300与第一整流电源500的阳极输出连接,第二电解阳极310与第二整流电源510的阳极输出连接,第三电解阳极320与第三整流电源520的阳极输出连接,第四电解阳极330与第四整流电源530的阳极输出连接,第一整流电源500的阴极输出与第一导电轮11连接,第二整流电源510的阴极输出与第二导电轮12连接,第三整流电源520的阴极输出与第三导电轮13连接,第四整流电源530的阴极输出与第四导电轮14连接,每个电解槽之间都有吹风嘴20及水洗,防止金属素材10将过多的电解溶液带出。
见图2,第二电解溶液工艺结束后,经过至少3~7道水洗,进入见图4所示的第三电解溶液工艺,第三电解溶液工艺采用铑铂合金电解溶液,第三电解溶液工艺由四个连续独立的第一电解母槽100、第二电解母槽110、第三电解母槽120和第四电解母槽130组成,四个电解母槽分别配置有第一整流电源500、第二整流电源510、第三整流电源520和第四整流电源530,四个整流电源均为高频整流电源,每个电解母槽内均设置有第一电解子槽200、第二电解子槽210、第三电解子槽220和第四电解子槽230,金属素材10通过每个电解槽的进出口的导向兼导电装置在电解子槽中间运行,导向兼导电装置包括第一导电轮11、第二导电轮12、第三导电轮13和第四导电轮14,第一电解子槽200的两侧设置有第一电解阳极300,第二电解子槽210的两侧设置有第二电解阳极310,第三电解子槽220的两侧设置有第三电解阳极320,第四电解子槽230的两侧设置有第四电解阳极330,第一电解阳极300与第一整流电源500的阳极输出连接,第二电解阳极310与第二整流电源510的阳极输出连接,第三电解阳极320与第三整流电源520的阳极输出连接,第四电解阳极330与第四整流电源530的阳极输出连接,第一整流电源500的阴极输出与第一导电轮11连接,第二整流电源510的阴极输出与第二导电轮12连接,第三整流电源520的阴极输出与第三导电轮13连接,第四整流电源530的阴极输出与第四导电轮14连接,在浸入电解溶液中金属素材10整体进行电解处理得到产品规格要求的膜厚产品,每个电解槽之间都有吹风嘴20及水洗,防止金属素材10将过多的电解溶液带出。
见图15,第三电解溶液工艺结束后,经过至少3~7道水洗,进入见图4所示的第四电解溶液工艺,第四电解溶液工艺采用金钴合金电解溶液,第四电解溶液工艺由两个连续独立的第一电解母槽100和第二电解母槽110组成,两个电解母槽分别配置有第一整流电源500和第二整流电源510,两个整流电源均为高频整流电源,该电解槽采用电解溶液喷射方式只对金属材料的所述功能区a进行电解,轮式电解治具配有与电解处理区域相对应的阳极,提高电解效率和电解金属层的质量,同样,每个电解槽之间都有吹风嘴20及水洗,其它操作与上述电解槽相似。
见图4,第四电解溶液工艺结束后,经过至少3~7道水洗,进入见图16所示的第五电解溶液工艺,第五电解溶液工艺采用铂银合金电解溶液,第五电解溶液工艺由两个连续独立的第一电解母槽100和第二电解母槽110组成,两个电解母槽分别配置有第一整流电源500和第二整流电源510,两个整流电源均为高频整流电源,该电解槽采用电解溶液喷射方式只对金属材料的所述功能区b进行电解,轮式电解治具配有与电解处理区域相对应的阳极,提高电解效率和电解金属层的质量,同样,每个电解槽之间都有吹风嘴20及水洗,其它操作与上述电解槽相似。
实施例5得到的是从金属素材10开始的第五电解金属端子640,第五电解金属端子640具有五层金属层,分别为第一层镍、第二层镍钨、第三层铑铂、第四层金钴、第五层铂银。
采用同种金属素材10为原料的多层电解金属端子样品1~4的混合气体腐蚀试验,试验条件:对电解金属端子产品功能区的环境腐蚀实验,混合气体浓度,二氧化硫(10ppm)、硫化氢(2ppm);温度35°、湿度75%,试验时间48小时。
试验样品条件如下所示:
见图5,样品1由实施例1制备而来,0.97μm的镍钨(第一层)、0.57μm的铂(第二层)、0.05~0.07μm的金钴(第三层)。
见图7,样品2由实施例2制备而来,1.05μm的镍金钨(第一层)、0.62μm的铂(第二层)、0.05~0.07μm的金钴(第三层)。
见图12,样品3由实施例3制备而来,1.76μm的镍(第一层)、0.38μm的镍磷(第二层)、0.38μm的钯(第三层)、1.13μm的铑钌(第四层)、0.05~0.07μm的金钴(第五层)。
样品4由实施例4制备而来,1.78μm的镍(第一层)、0.45μm的钯镍(第二层)、0.15~0.23μm的金钴(第三层)。
混合气体腐蚀试验结果如图18~21所示,样品1和样品2的腐蚀面积小、被腐蚀程度很低,具有十分优异的耐腐蚀性能,镍钨合金和镍金钨合金起到了十分重要的作用。
如图22和23所示,用微小方格实验方法统计试验后被腐蚀面积的百分比,试验样品的腐蚀率顺序结果为:样品2(腐蚀率0.2%)<样品1(0.5%)<样品3(2.1%)<样品4(9.8%);即样品2的镍金钨(第一层)、铂(第二层)和金钴(第三层),以及样品1的镍钨(第一层)、铂(第二层)和金钴(第三层)的电解金属电子产品具有十分优异的耐腐蚀性能,能优选为生产制造精密、高端电子产品的重要原材料。而样品3的镍(第一层)、镍磷(第二层)、钯(第三层)、铑钌(第四层)和金钴(第五层)的电解金属电子产品稍有一定程度的腐蚀,与样品1和样品2相比较则只有一般良好的耐腐蚀性能,只能用作中低端电子产品的原材料。比较样品4的镍(第一层)、钯镍(第二层)和金钴(第三层)的电解金属电子产品的耐腐蚀性能差,样品4有严重的腐蚀,该结果说明钯镍合金的耐腐蚀性能与铑钌合金比较差距很大,样品4只能用作对耐腐蚀性能要求不高的低端电解金属电子产品的原材料。
以上所述,仅为本发明较佳的具体实施方式,但本发明的保护范围并不局限于此,任何熟悉本技术领域的技术人员在本发明揭露的技术范围内,根据本发明的技术方案及其发明构思加以等同替换或改变,都应涵盖在本发明的保护范围之内。
本文用于企业家、创业者技术爱好者查询,结果仅供参考。