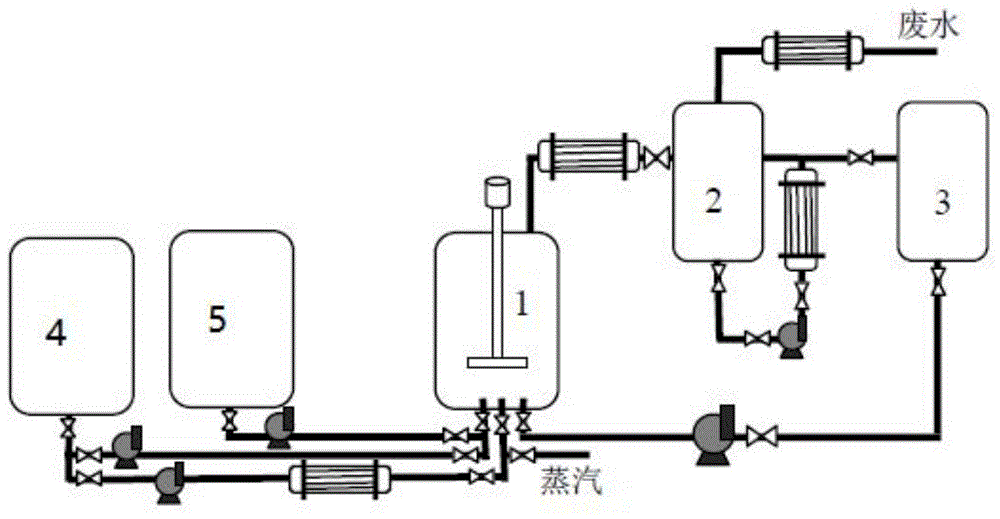
本发明涉及一种高酸值油脂无催化酯化、蒸馏同步脱酸工艺,属油脂化学利用、新能源及相关设备领域。
背景技术:
生物柴油(脂肪酸低级醇酯)是一种分子量与现有柴油非常接近的新型环保燃料,且原料来源于各种可再生油脂(如大豆油、菜籽油、梓油、微生物油脂及地沟油等)。虽然脂肪酸酯类生物柴油具有原料来源广、使用性能优、环保性能高、发动机启动性能好、可再生等优点;且大力发展生物柴油对能源安全、大气污染防治、环境改善及经济可持续发展等也具有重要的意义。但在实际运行当中还是遇到了诸多的瓶颈问题,如:可制备生物柴油的油脂大部分也是食用油脂,如大豆油、玉米油、菜籽油等,存在与民争粮问题;此外,梓油、桐油等木本油脂也基本具有各自的产业,用于合成特殊材料成本较高;微生物油脂不仅产量不足,且也存在成本问题;地沟油、酸化油等,虽然价格不高,但油品质量不佳,需要进一步处理方能使用。所以如何降低生物柴油原料的成本一直制约着行业发展,是市场急需解决的问题。
无论是大豆油、梓油还是微生物油脂等,其价格影响因素较固定,难以下降。只有地沟油等高酸值油脂可以在技术上想方设法来解决问题,一劳永逸。
针对高脂肪酸含量油脂的处理,目前主要有碱练(化学)和蒸馏(物理)两类方法。但无论是化学法碱练还是物理脱酸,都是直接去除油脂中的游离脂肪酸,不仅耗能、耗时、污染,且油品损耗较大;酯化是另一种常用的化学法,其不仅可将高酸值油脂中的脂肪酸转变为酯类,减小损失且有效避免了脂肪酸的后处理等。但目前的酯化工艺较为传统,使用催化剂需要后处理;即使提高温度,反应时间也往往在8小时以上,且高温影响产品品质。
技术实现要素:
本发明为一种高酸值油脂无催化酯化、蒸馏同步脱酸工艺。首先,本工艺对原料的要求不高,各类高酸值油脂皆能适用;其次,为了解决反应尾声降酸困难的关键问题提出了可使脂肪酸同步实现酯化脱除和蒸馏脱除的二合一工艺。从而实现缩短时间,减少损耗,提高产能,降低成本的目的。
本发明的技术方案为:一种高酸值油脂无催化酯化、蒸馏同步脱酸工艺,采用高酸值油脂和甘油作为原料,将油脂经过滤、脱水、脱胶预处理后装入反应釜中,加入适量的甘油;在真空下搅拌升温至200~210℃,反应30~60分钟;再升温至220~230℃,反应30~180分钟;最后将温度控制在220~240℃,并保证压力低于0.02mpa,从反应釜底部注入甘油或水蒸气,边酯化边蒸馏脱酸,当取样酸值低于2mgkoh/g时停止注入,当基本无溜出物时停止反应,降温出料即得到低酸值的脂肪酸甘油酯产品。
所述的高酸值油脂为各种酸化油、地沟油。
反应釜单独或多个串联使用。
生产过程中产生的甘油、脂肪酸经脱水处理后重新投入反应釜或直接注入串联后的首个反应釜进入反应系统循环使用。
有益效果:
本发明不仅为油脂化学利用行业提供了一种高酸值油脂无催化酯化、蒸馏同步脱酸工艺;还为生物柴油产业提供了一种高品质的脂肪酸甘油酯原料。本方法在工艺上实现了高酸值油脂酯化脱酸和蒸馏脱酸合二为一的同步脱酸,可快速高效的实现油脂的脱酸目的,从而实现缩短时间,减少损耗,提高产能,降低成本的目的。
本发明所用的原料为各种酸化油、地沟油高酸值油脂和甘油;所述的工艺可使油脂中的脂肪酸同步实现酯化脱除和蒸馏脱除,快速且低损耗的实现降酸价目的。可根据实际需要添加催化剂或增添多釜串联反应。
反应釜中的反应分为3个阶段:控温在200~210℃,真空脱水反应30~60分钟,甘油的初步酯化,低温避免甘油蒸发;2.升温至220~230℃,真空脱水反应30~180分钟,脂肪酸酯化主要阶段,高温促进酯化;3.控温在220~240℃,确保压力低于0.02mpa,并从反应釜底部注入甘油或水蒸气,边酯化边蒸馏脱酸,强化降酸阶段,补醇、蒸馏同步脱酸。
本发明几乎无需改进现有设备即可实现从高酸值油脂直接制备高纯度脂肪酸甘油酯的目的,生产过程中产生的甘油、脂肪酸经脱水(2)后可重新投入反应釜,在持续生产中实现“零损耗”。
附图说明
图1为酯化、蒸馏同步脱酸工艺简图。图中,反应釜(1)闪蒸(2)储罐(3)甘油罐(4)油脂罐(5)。
具体实施方式
一种高酸值油脂无催化酯化、蒸馏同步脱酸工艺。采用高酸值油脂和甘油作为原料,将油脂经过滤、脱水、脱胶等预处理后装入反应釜中,根据初始酸值加入适量的甘油;首先,在真空下搅拌升温至200~210℃,脱水反应30~60分钟,实现甘油的预酯化(防止升温减压后大量蒸馏并带出大量的脂肪酸);再升温至220~230℃,脱水反应30~180分钟,实现脂肪酸的大量酯化;最后将温度控制在220~240℃,并保证压力低于0.02mpa(硬脂酸在173℃时的饱和蒸汽压约为0.133kpa,甘油在低于20kpa时沸点也将降至230℃以下),从反应釜底部注入甘油或水蒸气,边酯化边蒸馏脱酸(补醇可有效提高羟基解离的氢离子浓度促进酯化反应;亦可保证可蒸馏甘油的含量;且高温低压可减少甘油聚合保证甘油的蒸馏和脂肪酸的脱除。此外,回收的甘油和脂肪酸皆可重复使用)。当取样酸值低于预期时(如:2mgkoh/g)停止注入,当基本无溜出物时停止反应,降温出料即可得到低酸值的脂肪酸甘油酯产品。此法可同步实现油脂中脂肪酸的酯化(化学法)和蒸馏脱除(物理脱酸),快速低损耗的实现降酸价目的。
本发明几乎无需改进现有设备即可实现从高酸值油脂直接制备高纯度脂肪酸甘油酯的目的,不仅大大降低了物理脱羧中脂肪酸的损失,提高了产量;还可有效降低酸价,缩短反应时间,提高酯化产物的品质。生产过程中产生的甘油、脂肪酸经脱水后可重新投入下一批次反应釜,在持续生产中实现“零损耗”。
所述的原料为地沟油等各类回收高酸值油脂和甘油;另可根据实际需要添加催化剂或增添多釜串联反应。
实施例1:
原料:地沟油(酸值78mgkoh/g),甘油;
将100份(以质量计,下同)预处理后的地沟油和12份甘油加入反应釜(1)中,开启搅拌并升温至205℃,压力为0.07mpa,脱水反应60分钟;再升温至220℃,脱水反应120分钟;最后将温度控制在230℃,压力为0.001mpa,从反应釜底部注入热甘油(110℃),边酯化边蒸馏脱酸。反应60分钟,取样酸值为1.94mgkoh/g,停止注入甘油,当基本无溜出物时停止反应。降温出料即可得到低酸值的脂肪酸甘油酯产品。所有馏分经闪蒸(2)脱水后注入储罐(3)可供下一釜使用。
实施例2:
原料:酸化油(酸值148mgkoh/g),甘油;
将100份预处理后的酸化油和15份甘油加入反应釜(1)中,开启搅拌并升温至210℃,压力为0.05mpa,脱水反应30分钟;再升温至230℃,脱水反应150分钟;最后将温度控制在240℃,压力为0.002mpa,从反应釜底部注入热甘油(110℃),边酯化边蒸馏脱酸。反应90分钟,取样酸值为1.98mgkoh/g,停止注入甘油,当基本无溜出物时停止反应,降温出料即可得到低酸值的脂肪酸甘油酯产品。所有馏分经脱水器(2)脱水后注入储罐(3)可供下一釜使用。
实施例3:
原料:地沟油(酸值51mgkoh/g),甘油;
将100份预处理后的地沟油和11份甘油加入反应釜(1)中,开启搅拌并升温至210℃,压力为0.03mpa,脱水反应20分钟;再升温至230℃,脱水反应70分钟;最后将温度控制在235℃,压力为0.001mpa,从反应釜底部注入热甘油(115℃),边酯化边蒸馏脱酸。反应30分钟,取样酸值为1.99mgkoh/g,停止注入甘油,当基本无溜出物时停止反应,降温出料即可得到低酸值的脂肪酸甘油酯产品。所有馏分经蒸馏釜(2)脱水后注入储罐(3)可供下一釜使用。
实施例4:
原料:酸化油脂(酸值106mgkoh/g),甘油;
将100份预处理后的酸化油脂和13份甘油加入反应釜(1)中,开启搅拌并升温至210℃,压力为0.04mpa,脱水反应60分钟;再升温至220℃,脱水反应200分钟;最后将温度控制在225℃,调整压力至0.001mpa,从反应釜底部注入蒸汽,边酯化边蒸馏脱酸。反应60分钟,取样酸值为1.93mgkoh/g,停止注入蒸汽,当基本无溜出物时停止反应,降温出料即可得到低酸值的脂肪酸甘油酯产品。所有馏分经蒸馏釜(2)脱水后注入储罐(3)可供下一釜使用。
实施例只在于表述实施方法,任何改变原料配比、反应温度、添加催化剂或采用本领域常规手段将多反应釜串联的(便于连续化生产),但仍采用此方法原理的依旧落入本专利的保护范围。
本文用于企业家、创业者技术爱好者查询,结果仅供参考。