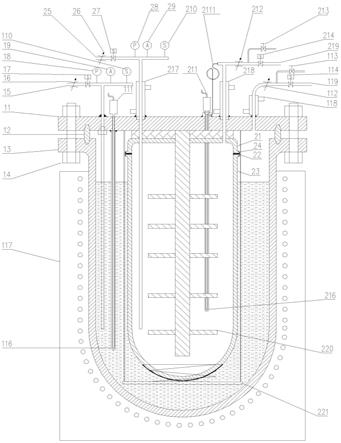
1.本发明属于化工和实验室检测领域,尤其涉及一种强腐蚀环境下使用的高温高压釜及使用方法。
背景技术:
2.化工生产中诸如氯化、磺化、烟气脱硫、脱硝等工艺过程中会有盐酸、硫酸、硝酸等物料出现。但是由于稀盐酸、稀硫酸和硝酸的腐蚀性较强,为保证设备的安全长周期运行,在腐蚀性环境下使用的材料都需要先进行材料相容性试验,以便确定所选材料是否满足使用要求。目前实验室进行腐蚀试验的高温高压釜材质主要有哈氏合金、蒙乃尔合金、钛材、聚四氟乙烯以及搪瓷等,但每种材料使用都有其限制,如聚四氟乙烯虽然能耐绝大多数化工介质腐蚀但使用温度在200℃以内,且耐压能力有限;搪瓷材料也能耐腐蚀,但是由于热膨胀和氢的作用极易造成搪瓷层发生暴瓷;金属材料对试验介质要求较多,不同金属对腐蚀性介质的相容性是不一样的,需要根据介质的腐蚀性选择不同材质的釜进行,金属材质的高温高压釜在腐蚀过程中还有可能形成难以清除的腐蚀产物,这些都会在无形中增加了成本。
技术实现要素:
3.为了克服现有高温高压釜耐压、耐腐蚀性不足的缺点,为此,本发明提供一种强腐蚀环境下使用的高温高压釜及使用方法。本发明采用以下技术方案:
4.一种强腐蚀环境下使用的高温高压釜,包括外釜组件和内釜组件,所述外釜组件包括外釜体、外釜盖,所述内釜组件包括套在外釜体内的且用于放置待测物的内釜体、盖合在内釜体上且位于外釜盖下方的内釜盖,所述外釜盖下方设置有用于弹性支撑内釜体的悬挂组件,所述外釜体与内釜体之间有填充导热液的缝隙。
5.使用上述的一种强腐蚀环境下使用的高温高压釜的方法,包括以下步骤:
6.s1、将待测物放置在内釜体中的试样挂架上,然后向内釜体中注入试验溶液,将内釜体置于悬挂组件的承托部上;
7.s2、将内釜体与内釜盖两部分对接,施加一定预紧力,使内釜体和内釜盖密封,调整悬挂组件中螺杆在套筒内长度并用第二紧固螺栓锁紧,长度保证悬挂组件的底部与外釜体内壁有缝隙;
8.s3、与内釜盖为一体结构的外釜盖将内层釜直接放置到外釜体内,向外釜体和内釜体之间输入导热液至一定深度且没过外釜体内的进气管出口,盖合外釜盖和外釜体并锁紧密封;
9.s4、密封内釜进气管、内釜排气管、外釜排气管,通过外釜体进气管向外釜体中通入惰性气体进行气密性试验,使外釜和内釜形成一个p’(p’<p0,p0为内釜安全工作所能承受的最大外压力)的压差,保压设定时间,查看内釜气管上压力变送器数值的变化来判断釜的密封性,如果内釜进气管上压力变送器的数值升高,则内釜需要重新密封,返回步骤s2;
如果不变则进入步骤s5;
10.s5、打开内釜进气管,启动联锁程序,将外釜釜内压力p
外
与内釜釜内压力p
内
设置成联锁,保证p
内
≤p
外
≤p
内
p’,同时向外釜和内釜通入增压气体;根据内釜的釜内的压力不断的调整外釜釜内的压力,保持外釜釜内压力与内釜釜内压力的关系为p
外
=p
内
p’,继续升压至气密性试验压力,约为试验压力的1.1倍,保压一段时间,观察外釜釜内的压力p
外
变化,外釜釜内压力不降低,则外釜气密性试验通过,按照要求进行泄压操作,而后进入步骤s6,若外釜气密性试验通不过,则返回步骤s3;
11.s6、为包覆在内外釜排气管上的冷凝器接通冷却水,根据试验需要,对内层容器内试验介质进行气体置换与饱和;
12.s7、升温;启动加热器对外釜进行加热,导热液自动将热量传递至内釜,通过内釜中的热电偶检测试验温度,加热直至设定温度,且保证在设定范围内波动,同时由于升温导致内外压力差变化,向外釜内通入增压气体,保持外釜釜内压力与内釜釜内压力的关系为p
内
≤p
外
≤p
内
p’,当温度升高产生的压力达不到试验要求时,进入步骤s8,如果能达到要求,则试验计时开始,经过设定的试验时间后,进入步骤s9;
13.s8、同步对内釜和外釜进行增压,使内釜釜内的压力最终达到试验要求,试验计时开始,经过设定的试验时间后,然后进入步骤s9;
14.s9、试验结束后,加热炉停止加热,装置自行降温,降温的同时,根据内釜的釜内压力,外釜排气管上的电磁阀适时开启,实现内釜、外釜同步降压,保证p
内
≤p
外
≤p
内
p’,待高温高压釜完全冷却以后,启动内釜截止阀,排尽内釜釜内气体后,关闭联锁程序,再启动外釜截止阀,排尽釜内增压气体;
15.s10、开盖,取试样,打开外釜盖,拆除内釜上的固定件,取下内釜体,而后取出试样。
16.本发明的优点在于:
17.(1)本发明设计的双层结构高温高压耐腐蚀釜,降低了环境对材料的要求,扩大了选材范围。本发明基于在内釜体和外釜体之间保持同步升压,可以将内釜体的压力传递到外釜体,而内釜体本身不承压或只承受少量外压,因此,内釜体仅仅需要做到耐腐蚀即可,由于腔体内设置的导热液可以直接对外釜体加温,这样内釜体受热更加均匀,实现试验所需要的耐高温高压腐蚀的釜。
18.(2)可极大的减少耐蚀金属的用量,并可实现一釜多用的功能,降低成本。
19.(3)本技术通过各安全调节组件和测量表组来准确调整进排气流量,调整内外釜的压力。
20.(4)热电偶套管起到保护热电偶的作用,冷凝器起到冷却进、排气管中气相的作用,降低强腐蚀介质对进、排气管的腐蚀。
21.(5)所述热电偶套管可与外釜排气管或内釜排气管连通,使得热电偶套管的内压与外压平衡,防止热电偶套管破裂。本发明中,优选热电偶套管可与内釜排气管连通。
22.(6)弹簧顶端安装有呈半球形或平板状的承托部,用于安放和承托内釜。弹簧主要是防止高温下内层容器和支柱的膨胀系数不同,实现预紧力的补偿,从而保证内釜的密封。
23.(7)支柱和螺杆的设置可以适用于不同的内外釜,并且方便调节。
24.(8)本技术内外釜根据不同的环境采用不同的材质,使得釜更加耐用。
25.(9)使用方法中联锁程序的设置,保证设备的使用安全。
附图说明
26.图1为本发明的结构示意图。
27.图2为悬挂组件的结构图。
28.图3为支持平台的俯视图。
29.图中标注符号的含义如下:
30.11
‑
外釜盖12
‑
密封垫13
‑
外釜体14
‑
第一紧固螺栓
31.15
‑
外釜进气管
32.16
‑
外釜第一流量调节阀17
‑
外釜第一电磁阀
33.18
‑
外釜压力测量组件19
‑
外釜安全阀
34.110
‑
外釜爆破片111
‑
外釜测温热电偶112
‑
外釜第二流量调节阀
35.113
‑
外釜截止阀114
‑
外釜第二电磁阀
36.116
‑
外釜热电偶套管117
‑
加热炉118
‑
外釜冷凝器
37.119
‑
外釜排气管
38.21
‑
内釜盖22
‑
内釜密封垫23
‑
内釜体24
‑
卡箍
39.25
‑
内釜进气管26
‑
内釜第一流量调节阀27
‑
内釜第一电磁阀
40.28
‑
内釜压力测量组件29
‑
内釜安全阀210
‑
内釜爆破片
41.211
‑
内釜测温热电偶2111
‑
热电偶压力平衡管
42.212
‑
内釜第二流量调节阀213
‑
内釜截止阀214
‑
内釜第二电磁阀
43.216
‑
内釜热电偶套管217
‑
内釜第一冷凝器
44.218
‑
内釜第二冷凝器219
‑
内釜排气管220
‑
试样挂架
45.221
‑
支持平台222
‑
承托部223
‑
弹簧224
‑
支柱
46.225
‑
第二紧固螺栓
具体实施方式
47.实施例1
48.如图1所示,一种强腐蚀环境下使用的高温高压釜及使用方法,包括外釜组件和内釜组件,所述外釜组件包括外釜体13、外釜盖11,所述内釜组件包括套在外釜体13内的且用于放置待测物的内釜体23、盖合在内釜体23上且位于外釜盖11下方的内釜盖21,所述外釜盖11下方设置有用于弹性支撑内釜体23的悬挂组件,所述外釜体13与内釜体23之间有填充导热液的缝隙。为了试验,所述高温高压釜需放置在加热炉117内。导热液使得内釜受热均匀。
49.所述内釜中设置有试样挂架,可以将试样按照内釜中的溶液量和实验要求,选择不同的安放位置。
50.所述外釜体13和外釜盖11为金属材质,所述内釜体23和内釜盖21为耐腐蚀耐高温材质。具体地说,所述外釜体13和外釜盖11采用碳钢、合金钢、不锈钢、耐蚀合金中的一种材质制造;使用温度在200℃以内时,所述内釜体23和内釜盖21采用聚四氟乙烯或其它耐腐蚀材料制备,使用温度200℃以上时,所述内釜体23和内釜盖21采用玻璃制备,当为强碱性环
境、含氢氟酸环境和玻璃不耐蚀环境下时,内釜体23和内釜盖21使用蒙乃尔合金等其它耐腐蚀材料制备。
51.釜盖上均设置有进气管、排气管、测温组件,进气管和排气管在釜外的端部上均设置有安全调节组件和测量表组,所述内釜盖21上的进气管、排气管、测温组件在釜外的端部均穿过外釜盖11。所述安全调节组件包括设置进气管上的进气流量调节阀、进气电磁阀、安全阀、爆破片,在排气管上的所述测量表组包括排气流量调节阀、排气电磁阀,还包括设置在排气管分支管路上的排气截止阀;所述测量表组包括设置在进气管上的压力表与变送器,通过调整进排气流量,调整内外釜的压力。所述测温组件包括伸入到内、外釜中的热电偶和套在热电偶外壁上的热电偶套管,具体地说,伸入到内釜体中的内釜测温热电偶和设置在其外侧的内釜热电偶套管,伸入到外釜体中的外釜测温热电偶和设置在其外侧的外釜热电偶套管。所述内釜热电偶套管可与外釜排气管或内釜排气管通过热电偶压力平衡管连通,使得内釜热电偶套管的内压与外压平衡,防止内釜热电偶套管破裂。本实施方式中,优选内釜热电偶套管与内釜排气管连通。
52.具体地说,如图1所示,所述外釜盖11上设置有外釜进气管15和外釜排气管119,且位于内釜体23的两侧,所述外釜进气管25的下端部靠近外釜体13的底部,所述外釜排气管119位于外釜体13腔的内部且与外釜盖11的底部平齐。所述外釜进气管15外端部上设置有外釜第一流量调节阀16、外釜第一电磁阀17、外釜压力测量组件18、外釜安全阀19、外釜爆破片110。所述外釜排气管119的外端部上设置有外釜第二流量调节阀112、外釜截止阀113、外釜第二电磁阀114。所述外釜排气管119上设置有外釜冷凝器118,所述外釜盖11上设置有伸入外釜体13内的外釜测温热电偶111和套在其外表面的外釜热电偶套管116。外釜压力测量组件18包括外釜压力表与压力变送器。
53.相同的,所述内釜盖21上设置有内釜进气管25和内釜排气管219,所述内釜进气管25的下端部靠近内釜体23的底部,所述内釜排气管219位于内釜体23腔的内部且与内釜盖21的底部平齐。所述内釜进气管25外端部上设置有内釜第一流量调节阀26、内釜第一电磁阀27、内釜压力测量组件28、内釜安全阀29、内釜爆破片210。所述内釜排气管的外端部上设置有内釜第二流量调节阀212、内釜截止阀213、内釜第二电磁阀214。所述内釜进气管25上设置有内釜第一冷凝器217,内釜排气管219上设置有内釜第二冷凝器218,所述内釜盖21上设置有伸入内釜体23内的内釜测温热电偶211和套在其内表面的内釜热电偶套管216。内釜压力测量组件28包括内釜压力表与压力变送器。
54.所述内釜测温热电偶211包括热电偶、设置在外釜盖11上的热电偶压力平衡管2111。所述内釜盖21上的内釜热电偶套管216可与外釜排气管119或内釜排气管219连通,优选与内釜排气管219连通,使得热电偶套管的内压与外压平衡,防止热电偶套管破裂。
55.为了实现外釜体13和外釜盖11的密封性,所述外釜体13和外釜盖11之间设置有用于密封的密封垫12,然后通过施加一定预紧力,然后使用第一紧固螺栓14固定实现密封。为了实现内釜体23和内釜盖21的密封,所述内釜体23和内釜盖21之间设置有内釜密封垫22,然后通过卡箍24固定实现密封。
56.如图2
‑
3所示,所述悬挂组件包括支持平台221、将支持平台221悬挂在外釜盖11底部的支柱224,所述支撑平台上固定有3根或4根螺杆,且环形阵列在支持平台221的外边缘,所述支柱224包括与螺杆对应的3根或4根套筒,分别与螺杆对应,对应的所述套筒的两端分
别与外釜盖11和支持平台221上的螺杆螺纹连接,套筒垂直方向上还设置有可抵住螺杆的第二紧固螺栓225,通过第二紧固螺栓225锁紧以确定支柱224的长度。所述平台中部设置有弹簧223,所述弹簧223的上方托住内釜体23底部的承托部222。所述承托部222呈半球形或平板状。弹簧223主要是防止高温下内层容器和支柱224的膨胀系数不同,实现预紧力的补偿,从而保证内釜的密封。
57.实施例2
58.使用实施例1所述的一种强腐蚀环境下使用的高温高压釜及使用方法的方法,按照要求开展超级奥氏体不锈钢在300℃、9mpa压力下,30%硫酸溶液中的耐均匀腐蚀性能测定。包括以下步骤:
59.s1、清洗并干燥试验试样,测量试样的几个尺寸与质量,配置30%质量分数的硫酸溶液,根据试样的表面积计算需要的溶液量,将待测物放置在内釜体23中的试样挂架上,然后向内釜体23中注入试验溶液,将内釜体23置于悬挂组件的承托部222上;
60.s2、将内釜体23与内釜盖21两部分对接,施加一定预紧力,使内釜体23和内釜盖21密封,调整悬挂组件中螺杆在套筒内长度并用第二紧固螺栓225锁紧,长度保证悬挂组件的底部与外釜体13内壁有缝隙;
61.s3、与内釜盖21为一体结构的外釜盖11将内层釜直接放置到外釜体13内,向外釜体13和内釜体23之间输入导热液至一定深度且没过外釜体13内的进气管出口,盖合外釜盖11和外釜体13并锁紧密封;
62.s4、密封内釜进气管25、内釜排气管219、外釜排气管119,通过外釜体13进气管向外釜体13中通入惰性气体进行气密性试验,使外釜和内釜形成一个p’的压差,设置内釜内外压差p’为0.3mpa,向外釜釜内通入0.3mpa的惰性气体,保压设定时间,查看内釜进气管上压力变送器的值是否变化来判断内釜密封性,如果内釜进气管上压力变送器的值升高,则需要重新密封,返回步骤s2,如果不变则进入步骤s5;
63.s5、打开内釜进气管,启动联锁程序,将外釜釜内压力p
外
与内釜釜内压力p
内
设置成联锁,保证p
内
≤p
外
≤p
内
p’,同时向外釜和内釜通入增压气体;根据内釜的釜内的压力不断的调整外釜釜内的压力,保持外釜釜内压力与内釜釜内压力的关系为p
外
=p
内
p’,由于300℃时水的饱和蒸汽压约为9mpa,所以气密性试验的压力在10~11mpa。保压设定时间后,观察外釜釜内的压力p
外
变化,若外釜釜内压力p
外
发生波动,说明外釜有泄露,返回步骤s3,否则进入步骤s6;
64.s6、为包覆在外釜排气管119、内釜进气管25和内釜排气管219上的冷凝器接通冷却水,根据试验需要,对内层容器内试验介质进行气体置换与饱和;
65.s7、升温;打开外釜第一流量调节阀16、内釜第一流量调节阀26、外釜第二流量调节阀112、内釜第二流量调节阀212,设置内釜内外的压差p’=0.3mpa、试验温度t=300℃、试验压力p=9mpa、试验周期t=168h、超温报警值t
超
=310℃、超压报警值p
超
=10mpa等试验参数,启动高温高压釜外釜釜内压力p外与内釜釜内压力p内联锁,启动加热与升压程序,控制程序根据设置自动升温至设定的试验温度,当温度升高产生的压力达不到试验要求时,进入步骤s8,如果能满足试验要求,则试验计时开始,经过设定的试验时间后,进入步骤s9;
66.s8、同步对内釜和外釜进行增压,使内釜釜内的压力最终达到试验要求,试验计时开始,经过设定时间后,然后进入步骤s9;内釜理论上先升温后升压与先升压后升温都可
以,优选的是先升温后升压,外釜伴随着内釜的升压也同步升压。
67.s9、试验结束后,加热炉停止加热,装置自行降温,降温的同时,根据内釜釜内的压力,外釜排气管119上的第二电磁阀214适时开启,实现内釜、外釜同步降压,保证p
内
≤p
外
≤p
内
p’,待高温高压釜完全冷却以后,启动内釜截止阀213,排尽内釜釜内气体后,关闭联锁程序,再启动外釜截止阀113,排尽釜内增压气体;具体地说,试验周期达到后,加热炉117断电,外釜第一电磁阀17与内釜第一电磁阀27关闭,高温高压釜进入自然冷却与泄压环节,控制系统会根据内釜压力p
内
控制外釜第二电磁阀114的开启与关闭来调节外釜釜内压力p
外
,使p
外
=p
内
p’,当内釜温度降低至30℃时,打开内釜排气管上的内釜截止阀213,排出内釜釜内气体,根据联锁关系,外釜釜内气体也会通过外釜排气管119同步排出。当内釜釜内气体排尽后,关闭联锁程序。再打开外釜排气管119上的外釜截止阀113,排尽外釜釜内气体。
68.s10、开盖,取试样,打开外釜盖11,拆除内釜上的固定件,取下内釜体,而后取出试样。清洗吹干后称重,根据试验前后的质量变化计算腐蚀速率,清洗内釜后晾干,并小心收好。
69.以上仅为本发明创造的较佳实施例而已,并不用以限制本发明创造,凡在本发明创造的精神和原则之内所作的任何修改、等同替换和改进等,均应包含在本发明创造的保护范围之内。
再多了解一些
本文用于企业家、创业者技术爱好者查询,结果仅供参考。