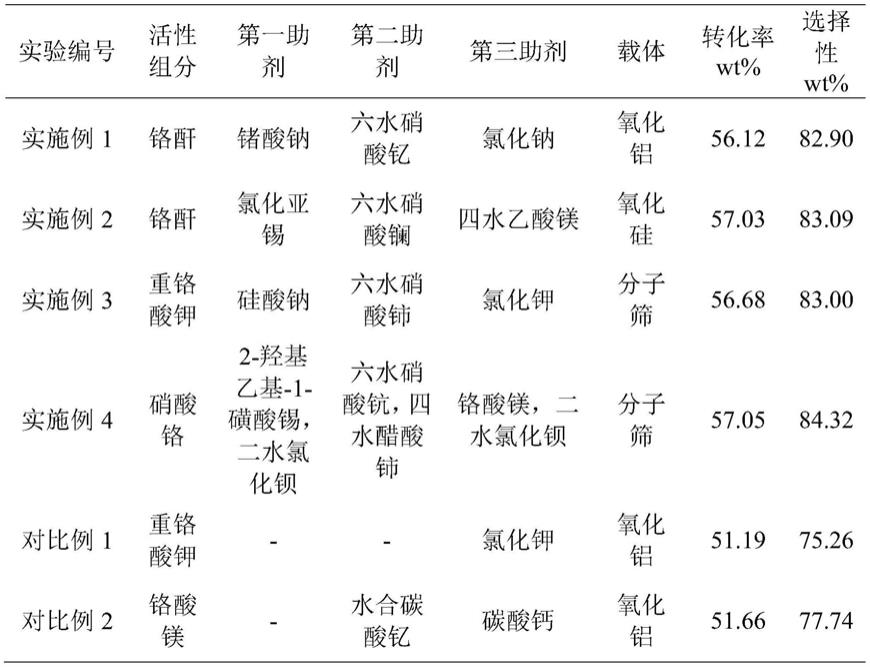
1.本发明涉及石化技术领域,具体涉及一种改性的铬系丙烷脱氢催化剂固定床载体、制备及应用方法。
背景技术:
2.丙烯在石化领域由于其下游产物的附加值高,利用率广等特点,收到各大石化炼厂的广泛关注。但由于技术所限,导致现阶段的产能无法满足使用需求。目前,获取丙烯的主要途径包括以下几个方面:催化裂化技术,蒸汽裂解技术,甲醇至烯烃技术(mto)以及丙烷直接脱氢技术(pdh)。现阶段,虽然超过半数的丙烯产能来自于催化裂化技术和蒸汽裂解技术,但是此两种方式存在着能耗大,并且收率低等不足等问题。此外,mto技术也由于其高昂的成本,导致其市场竞争力较低。因此,与此类获取丙烯技术相比,pdh技术由于其地投资,高回报,产物单一等特点,受到各大石化的热烈追捧,一跃成为最有效的获取丙烯的手段。
3.到目前为止,pdh技术中的lummus的catofin固定床工艺和uop的oleflex移动床工艺实现了大规模工业化。其中uop的oleflex移动床工艺则是采用pt
‑
sn/al2o3的球形催化剂,该类催化剂使用贵金属原子作为活性位点,同时为了保持催化剂的抗积碳能力,需要在临氢的条件下进行反应。但是,贵金属的高成本以及移动床催化剂的所需要的高强度载体则降低了该工艺的经济性,同时由于氢气的使用,在进行低丙烷脱氢反应时,也存在一定的安全隐患。
4.lummus的catofin固定床工艺采用cr/al2o3的条形催化剂,该类催化剂具有价格低廉,催化活性好,选择性高等特点。但是由于该类催化剂主要使用氧化铝为载体,其水热稳定性较差。因此,在使用过程中的水蒸气吹扫环节将大大降低其催化剂稳定性。最终将导致催化剂形成没有活性的铬铝致密相,极大的限制了该催化剂的使用寿命。
5.中国专利cn106582613中报道了使用稀土元素对载体进行改性的方法。但是由于稀土元素的引入,改变了催化剂表面的酸碱性,使得其催化剂性能有所下降,且抗积碳能力减弱。
6.综上所述,在提高载体稳定性的同时保持催化剂的性能,对现阶段铬系丙烷脱氢的载体进行改性是至关重要的。
技术实现要素:
7.为了解决铬系丙烷脱氢催化剂固定床载体稳定性较差的问题,本发明提供了一种改性的铬系丙烷脱氢催化剂固定床载体、制备及应用方法,该载体兼具催化剂脱氢性能,提高稳定性,并增加其在使用过程中的抗积碳能力。
8.为了达到上述技术效果,本发明提供了如下技术方案:
9.一种改性的铬系丙烷脱氢催化剂固定床载体,所述固定床载体包括多孔载体和以
多孔载体为基准计的质量分数为1
‑
40%的第一助剂,质量分数为1
‑
10%的第二助剂和质量分数为1
‑
10%的第三助剂,其中第一助剂为第ⅳa族元素中的一种或几种,第二助剂为稀土元素中的一种或几种的混合物,第三助剂为碱金属元素或碱土元素中的一种或几种。
10.进一步的技术方案为,所述固定床载体为具有多级孔道的尖晶石结构,钙钛矿结构,分子筛结构以及多孔碳结构中的至少一种,比表面为50~500m2/g,孔径范围为5~40nm。
11.进一步的技术方案为,所述固定床载体的比表面积为50~150m2/g,孔径范围为10~30nm。
12.进一步的技术方案为,所述多孔载体为铝石,硅石或分子筛中的一种或多种。
13.进一步的技术方案为,所述第ⅳa族元素选自第ⅳa族元素单质粉末,第ⅳa族元素氧化物,第ⅳa族元素卤化物,第ⅳa族元素硫化物,第ⅳa族元素硫酸盐,第ⅳa族元素硝酸盐或者第ⅳa族元素有机酸盐中的一种或多种。
14.进一步的技术方案为,所述稀土元素选自稀土金属单质,稀土金属卤化物,稀土金属氧化物,稀土金属硫化物,稀土金属硫酸盐,稀土金属硝酸盐或者稀土金属有机酸盐的一种或多种。
15.进一步的技术方案为,所述碱金属元素或者碱土金属元素选自其对应的单质,卤化物,氧化物,硫化物,硫酸盐,硝酸盐或者有机酸盐中的一种或多种。
16.本发明还提供了一种改性的铬系丙烷脱氢催化剂固定床载体的制备方法,包括以下步骤:1)将多孔载体,浓硝酸,田菁粉,软化水,第一助剂,第二助剂和第三助剂以100:6
‑
13:6
‑
10:60
‑
80:1
‑
40:1
‑
10:1
‑
10的质量比混合,捏合,随后在挤条机中成型,并在80℃~150℃下进行干燥8~12小时,得到条形固定床载体;2)将条形固定床载体在400℃~1000℃下进行焙烧1~10小时,得到改性的铬系丙烷脱氢催化剂固定床载体,其比表面积为50m2/g~450m2/g,孔径范围为3~40nm。
17.本发明还提供了一种改性的铬系丙烷脱氢催化剂固定床载体的应用方法,采用该载体制备铬系丙烷脱氢催化剂,其制备方法具体包括以下步骤:1)配置所需含活性组分元素的混合液,将权利要求8中所制得的改性的铬系丙烷脱氢催化剂固定床载体与混合液在真空条件下进行浸渍,搅拌,再陈化0.5~8小时,得到半成品脱氢催化剂;2)将半成品脱氢催化剂干燥0.5~8小时,然后在600~1000℃下焙烧0.5~12小时,得到一种改性的铬系丙烷脱氢催化剂固定床载体的制备的脱氢催化剂。
18.与现有技术相比,本发明具有如下有益效果:其一,在载体的制备过程中加入三种助剂,可以一步得到改性后的载体,随后仅需一步浸渍即可以达到催化剂的使用标准,相比于传统的浸渍法,本发明公开的制备方法简化了制备和生产过程;其二,相比于未改性的载体,本发明公开的改性载体中含有多种稳定结构,其中包括但不限于美铝尖晶石,钙铝尖晶石,镧铝钙钛矿结构,上述结构可以弥补纯氧化铝的配位缺陷,增强氧化铝配位结构上的稳定性。而多孔碳,硅铝分子筛结构则可以改变氧化铝结构的表面电性,从而改变酸碱性,更加符合铬系丙烷脱氢催化剂载体表面的酸碱性要求;其三,由于所述的载体结构和表面酸碱性的可调性,在催化剂的应用中,增强其丙烷脱氢过程中的转化率,选择性,稳定性以及抗积碳能力;此外,本发明所使用的原料来源简单易得,且可以根据使用需求进行调整,易于工业化生产,具有良好的应用前景。
具体实施方式
19.为使本发明实施例的目的、技术方案和优点更加清楚,下面对本发明的实施例进行详细、完整的描述,显然,所描述的实施例是本发明一部分实施例,而不是全部的实施例。基于本发明中的实施例,本领域普通技术人员在没有作出创造性劳动前提下所获得的所有其他实施例,都属于本发明保护的范围。
20.本技术领域技术人员可以理解,除非另外定义,这里使用的所有术语(包括技术术语和科学术语),具有与本发明所属领域中的普通技术人员的一般理解相同的意义。还应该理解的是,诸如通用字典中定义的那些术语,应该被理解为具有与现有技术的上下文中的意义一致的意义,并且除非被特定定义,否则不会用理想化或过于正式的含义来解释。
21.实施例1
22.在捏合机内加入120g铝石粉,9g氯化钠,12.2g锗酸钠,2g六水硝酸钇,以及5g田菁粉混合均匀;称取4g浓硝酸加到50g水中,配置成硝酸溶液,并将此溶液加入到拟薄水铝石和田菁粉混合物中,捏合1小时,并在4.5mm孔板上挤条;将挤好的条状载体在120℃下干燥2小时,切粒,以3℃每分的速度升温至900℃,在该温度下焙烧4
‑
8小时,得到固定床载体a;测得其吸水量为42%,比表面积150m2/g。称取24.5g铬酐,溶于42g水中,得到浸渍液;将100g上述载体a加入抽滤瓶中,抽真空2小时,真空度为
‑
100kpa;将39g浸渍液,缓慢加入抽滤瓶中,将湿润的催化剂每10分钟进行一次搅拌,直至催化剂表面风干。放入120℃烘箱中烘干8小时,得到干燥的催化剂;将干燥的催化剂在马弗炉中进行焙烧,焙烧温度为650℃,焙烧时间为4小时,升温速率为5℃每分,待催化剂自然降温至200℃以下时,得到固定床催化剂1。
23.实施例2
24.在捏合机内加入50g铝石粉,30g硅石粉,10g四水乙酸镁,7g氯化亚锡,5.35g六水硝酸镧,3g田菁粉混合均匀;称取10g浓硝酸加到45g水中,配置成硝酸溶液,并将此溶液加入到拟薄水铝石和田菁粉混合物中,捏合1小时,并在4.5mm孔板上挤条;将挤好的条状载体在120℃下干燥2小时,切粒,以3℃每分的速度升温至900℃,在该温度下焙烧4
‑
8小时,得到固定床载体b;测得其吸水量为40%,比表面为123m2/g。称取32.9g铬酐,溶于40g水中,得到浸渍液;将100g上述载体b加入抽滤瓶中,抽真空2小时,真空度为
‑
100kpa;将11.7g浸渍液缓慢加入抽滤瓶中,将湿润的催化剂每10分钟进行一次搅拌,直至催化剂表面风干。放入120℃烘箱中烘干8小时,得到干燥的催化剂;将干燥的催化剂在马弗炉中进行焙烧,焙烧温度为650℃,焙烧时间为4小时,升温速率为5℃每分,待催化剂自然降温至200℃以下时,得到固定床催化剂2。
25.实施例3
26.在捏合机内加入80g,zsm
‑
5分子筛,8g硅酸钠,3g氯化钾,3g六水硝酸铈,2g田菁粉混合均匀;称取1.5g浓硝酸加到30g水中,配置成硝酸溶液,并将此溶液加入到拟薄水铝石和田菁粉混合物中,捏合1小时,并在4.5mm孔板上挤条;将挤好的条状载体在120℃下干燥2小时,切粒,以3℃每分的速度升温至900℃,在该温度下焙烧4
‑
8小时,得到固定床载体c;测得其吸水量为41%,比表面为140m2/g。称取20g重铬酸钾,溶于42g水中,得到浸渍液;100g将上述载体c加入抽滤瓶中,抽真空2小时,真空度为
‑
100kpa;将11.7g浸渍液缓慢加入抽滤瓶中,将湿润的催化剂每10分钟进行一次搅拌,直至催化剂表面风干。放入120℃烘箱中烘干8小时,得到干燥的催化剂;将干燥的催化剂在马弗炉中进行焙烧,焙烧温度为650℃,焙
烧时间为4小时,升温速率为5℃每分,待催化剂自然降温至200℃以下时,得到固定床催化剂3。
27.实施例4
28.在捏合机内加入120g铝石粉,称取11g铬酸镁,5g六水硝酸钪,3g二水氯化钡,9g 2
‑
羟基乙基
‑1‑
磺酸锡,2g四水醋酸铈,溶于41g水中,6g田菁粉混合均匀;称取8g浓硝酸加到50g水中,配置成硝酸溶液,并将此溶液加入到拟薄水铝石和田菁粉混合物中,捏合1小时,并在4.5mm孔板上挤条;将挤好的条状载体在120℃下干燥2小时,切粒,以3℃每分的速度升温至900℃,在该温度下焙烧4
‑
8小时,得到固定床载体d;测得其吸水量为39%,比表面积102m2/g。称取30g硝酸铬,溶于40g水中,得到浸渍液;将100g上述载体d加入抽滤瓶中,抽真空2小时,真空度为
‑
100kpa;将12.7g浸渍液缓慢加入抽滤瓶中,将湿润的催化剂每10分钟进行一次搅拌,直至催化剂表面风干。放入120℃烘箱中烘干8小时,得到干燥的催化剂;将干燥的催化剂在马弗炉中进行焙烧,焙烧温度为750℃,焙烧时间为4小时,升温速率为5℃每分,待催化剂自然降温至200℃以下时,得到固定床催化剂4。
29.对照例1
30.在捏合机内加入100g铝石粉,5g氯化钾,其中加入3g田菁粉混合均匀;称取2.8g浓硝酸加到45g水中,配置成硝酸溶液,并将此溶液加入到拟薄水铝石和田菁粉混合物中,捏合1小时,并在4.5mm孔板上挤条;将挤好的条状载体在120℃下干燥2小时,切粒,以3℃每分的速度升温至900℃,在该温度下焙烧4
‑
8小时,得到对比例载体a;测得其吸水量为40%,比表面为178m2/g。称取20g重铬酸钾,溶于42g水中,得到浸渍液;将100g上述对比例载体a加入抽滤瓶中,抽真空2小时,真空度为
‑
100kpa;将11.7g浸渍液缓慢加入抽滤瓶中,将湿润的催化剂每10分钟进行一次搅拌,直至催化剂表面风干。放入120℃烘箱中烘干8小时,得到干燥的催化剂;将干燥的催化剂在马弗炉中进行焙烧,焙烧温度为650℃,焙烧时间为4小时,升温速率为5℃每分,待催化剂自然降温至200℃以下时,得到固定床对比剂1。
31.对照例2
32.捏合机内加入100g铝石粉,6g碳酸钙,以3g碳酸钇,3g田菁粉混合均匀;称取2.8g浓硝酸加到45g水中,配置成硝酸溶液,并将此溶液加入到拟薄水铝石和田菁粉混合物中,捏合1小时,并在4.5mm孔板上挤条;将挤好的条状载体在120℃下干燥2小时,切粒,以3℃每分的速度升温至900℃,在该温度下焙烧4
‑
8小时,得到对比例载体b;测得其吸水量为40%,比表面为158m2/g。称取34g铬酸酐,溶于40g水中,得到浸渍液;将100g上述对比例载体b加入抽滤瓶中,抽真空2小时,真空度为
‑
100kpa;将40g浸渍液缓慢加入抽滤瓶中,将湿润的催化剂每10分钟进行一次搅拌,直至催化剂表面风干。放入120℃烘箱中烘干8小时,得到干燥的催化剂;将干燥的催化剂在马弗炉中进行焙烧,焙烧温度为550℃,焙烧时间为8小时,升温速率为5℃每分,待催化剂自然降温至200℃以下时,得到固定床对比剂2。
33.对照例3
34.在捏合机内加入120g铝石粉,12.2g锗酸钠,以及5g田菁粉混合均匀;称取4g浓硝酸加到50g水中,配置成硝酸溶液,并将此溶液加入到拟薄水铝石和田菁粉混合物中,捏合1小时,并在4.5mm孔板上挤条;将挤好的条状载体在120℃下干燥2小时,切粒,以3℃每分的速度升温至900℃,在该温度下焙烧4
‑
8小时,得到固定床载体a;测得其吸水量为42%,比表面积150m2/g。称取24.5g铬酐,溶于42g水中,得到浸渍液;将100g上述载体a加入抽滤瓶中,
抽真空2小时,真空度为
‑
100kpa;将39g浸渍液,缓慢加入抽滤瓶中,将湿润的催化剂每10分钟进行一次搅拌,直至催化剂表面风干。放入120℃烘箱中烘干8小时,得到干燥的催化剂;将干燥的催化剂在马弗炉中进行焙烧,焙烧温度为650℃,焙烧时间为4小时,升温速率为5℃每分,待催化剂自然降温至200℃以下时,得到固定床对比剂3。
35.对照例4
36.在捏合机内加入120g铝石粉,9g氯化钠,以及5g田菁粉混合均匀;称取4g浓硝酸加到50g水中,配置成硝酸溶液,并将此溶液加入到拟薄水铝石和田菁粉混合物中,捏合1小时,并在4.5mm孔板上挤条;将挤好的条状载体在120℃下干燥2小时,切粒,以3℃每分的速度升温至900℃,在该温度下焙烧4
‑
8小时,得到固定床载体a;测得其吸水量为42%,比表面积150m2/g。称取24.5g铬酐,溶于42g水中,得到浸渍液;将100g上述载体a加入抽滤瓶中,抽真空2小时,真空度为
‑
100kpa;将39g浸渍液,缓慢加入抽滤瓶中,将湿润的催化剂每10分钟进行一次搅拌,直至催化剂表面风干。放入120℃烘箱中烘干8小时,得到干燥的催化剂;将干燥的催化剂在马弗炉中进行焙烧,焙烧温度为650℃,焙烧时间为4小时,升温速率为5℃每分,待催化剂自然降温至200℃以下时,得到固定床对照剂4。
37.对照例5
38.在捏合机内加入120g铝石粉,2g六水硝酸钇,以及5g田菁粉混合均匀;称取4g浓硝酸加到50g水中,配置成硝酸溶液,并将此溶液加入到拟薄水铝石和田菁粉混合物中,捏合1小时,并在4.5mm孔板上挤条;将挤好的条状载体在120℃下干燥2小时,切粒,以3℃每分的速度升温至900℃,在该温度下焙烧4
‑
8小时,得到固定床载体a;测得其吸水量为42%,比表面积150m2/g。称取24.5g铬酐,溶于42g水中,得到浸渍液;将100g上述载体a加入抽滤瓶中,抽真空2小时,真空度为
‑
100kpa;将39g浸渍液,缓慢加入抽滤瓶中,将湿润的催化剂每10分钟进行一次搅拌,直至催化剂表面风干。放入120℃烘箱中烘干8小时,得到干燥的催化剂;将干燥的催化剂在马弗炉中进行焙烧,焙烧温度为650℃,焙烧时间为4小时,升温速率为5℃每分,待催化剂自然降温至200℃以下时,得到固定床对照剂5。
39.对照例6
40.在捏合机内加入120g铝石粉,12.2g锗酸钠,2g六水硝酸钇,以及5g田菁粉混合均匀;称取4g浓硝酸加到50g水中,配置成硝酸溶液,并将此溶液加入到拟薄水铝石和田菁粉混合物中,捏合1小时,并在4.5mm孔板上挤条;将挤好的条状载体在120℃下干燥2小时,切粒,以3℃每分的速度升温至900℃,在该温度下焙烧4
‑
8小时,得到固定床载体a;测得其吸水量为42%,比表面积150m2/g。称取24.5g铬酐,溶于42g水中,得到浸渍液;将100g上述载体a加入抽滤瓶中,抽真空2小时,真空度为
‑
100kpa;将39g浸渍液,缓慢加入抽滤瓶中,将湿润的催化剂每10分钟进行一次搅拌,直至催化剂表面风干。放入120℃烘箱中烘干8小时,得到干燥的催化剂;将干燥的催化剂在马弗炉中进行焙烧,焙烧温度为650℃,焙烧时间为4小时,升温速率为5℃每分,待催化剂自然降温至200℃以下时,得到固定床对照剂6。
41.对照例7
42.在捏合机内加入120g铝石粉,9g氯化钠,12.2g锗酸钠,以及5g田菁粉混合均匀;称取4g浓硝酸加到50g水中,配置成硝酸溶液,并将此溶液加入到拟薄水铝石和田菁粉混合物中,捏合1小时,并在4.5mm孔板上挤条;将挤好的条状载体在120℃下干燥2小时,切粒,以3℃每分的速度升温至900℃,在该温度下焙烧4
‑
8小时,得到固定床载体a;测得其吸水量为
42%,比表面积150m2/g。称取24.5g铬酐,溶于42g水中,得到浸渍液;将100g上述载体a加入抽滤瓶中,抽真空2小时,真空度为
‑
100kpa;将39g浸渍液,缓慢加入抽滤瓶中,将湿润的催化剂每10分钟进行一次搅拌,直至催化剂表面风干。放入120℃烘箱中烘干8小时,得到干燥的催化剂;将干燥的催化剂在马弗炉中进行焙烧,焙烧温度为650℃,焙烧时间为4小时,升温速率为5℃每分,待催化剂自然降温至200℃以下时,得到固定床对照剂7。
43.对照例8
44.在捏合机内加入120g铝石粉,9g氯化钠,2g六水硝酸钇,以及5g田菁粉混合均匀;称取4g浓硝酸加到50g水中,配置成硝酸溶液,并将此溶液加入到拟薄水铝石和田菁粉混合物中,捏合1小时,并在4.5mm孔板上挤条;将挤好的条状载体在120℃下干燥2小时,切粒,以3℃每分的速度升温至900℃,在该温度下焙烧4
‑
8小时,得到固定床载体a;测得其吸水量为42%,比表面积150m2/g。称取24.5g铬酐,溶于42g水中,得到浸渍液;将100g上述载体a加入抽滤瓶中,抽真空2小时,真空度为
‑
100kpa;将39g浸渍液,缓慢加入抽滤瓶中,将湿润的催化剂每10分钟进行一次搅拌,直至催化剂表面风干。放入120℃烘箱中烘干8小时,得到干燥的催化剂;将干燥的催化剂在马弗炉中进行焙烧,焙烧温度为650℃,焙烧时间为4小时,升温速率为5℃每分,待催化剂自然降温至200℃以下时,得到固定床对照剂8。
45.试验例
46.一、丙烷脱氢试验
47.实施例1,2,3,4中得到的固定床催化剂1
‑
4与对比例1
‑
8中的固定床对比剂1合2分别进行丙烷脱氢试验;
48.采用的工艺流程为现有的固定床工艺流程,反应器为恒温反应器,具体控制参数如下:丙烷空速为1h
‑1,丙烷分压为50kpa,床层温度为600℃,结果如表1所示:
49.表1实施例丙烷脱氢评价数据
[0050][0051]
再多了解一些
本文用于企业家、创业者技术爱好者查询,结果仅供参考。