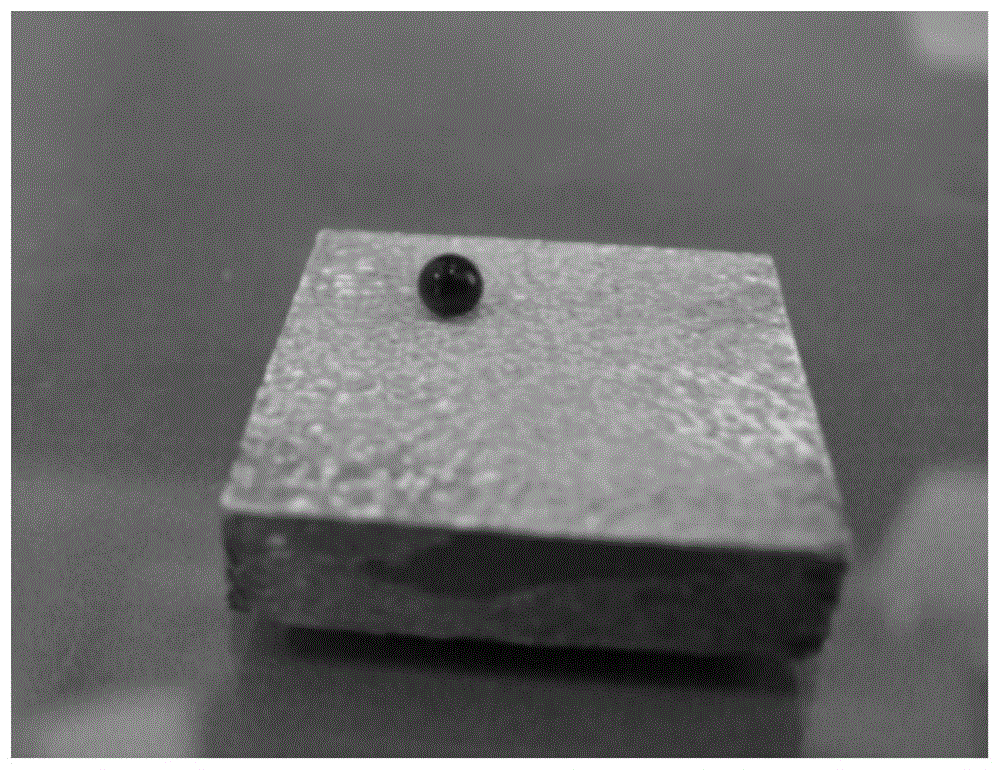
本发明属于功能材料技术领域,具体涉及一种超疏水涂料及其制备方法和应用。
背景技术:
超疏水涂层的制备肇始于人们对荷叶、玫瑰花瓣、沙漠甲虫等自然界的极端润湿现象的认识与研究,由于超疏水涂层具有自清洁、防覆冰、防腐、抗菌等优良性能,因而在玻璃、陶瓷砖瓦水泥、纺织品、金属等基材的涂层上有广泛的应用价值。制备超疏水表面通常从两个方面着手,一是使用低表面能物质,例如聚二甲基硅氧烷、含氟化合物等;二是构造微纳米复合粗糙结构。
相关技术中,制备超疏水表面的工艺通常复杂耗时,比如有的工艺中,基材需要经过打磨后再浸泡到酸液中刻蚀以形成一定的微纳米结构。有的工艺中,玻璃需要先进行蒙砂处理获得粗糙结构,再用硅烷在高温条件下处理。此外,由于含氟化合物的表面能最低可低至15.0mn/m,因此目前很多超疏水技术会使用含氟化合物,利用氟硅烷改性丙烯酸酯乳液来制备超疏水表面,但氟单体及其化合物价格高昂,难以应用到普通工业产品上。
有机硅在涂层中能表现出良好的疏水特性,例如聚二甲基硅氧烷,其分子链段柔顺,具有低表面能和高铺展性等表面特性,这些特性使其能够用于表面改性和控制,但聚二甲基硅氧烷的分子间作用力弱,与基材的结合性差,机械强度低,易划伤损坏,寿命短。而构造高粗糙度的模板法、静电纺织法和等离子蚀刻法等方法的工艺流程相对复杂,对生产设备要求高。虽然通过向聚合物中添加无机粉体材料(通常有二氧化硅、二氧化钛、氧化锌及其修饰物等),能利用粉体材料本身的疏水特性和表面粗糙度来提高原有涂层的疏水性能,最终获得超疏水复合材料。但高含量的无机粉体添加物使聚合乳液与基材的附着变差,影响原聚合乳液的成膜性能,还会造成体系粘度过高,喷涂、浸涂等涂布工艺受到限制的问题,还会降低涂层的透明度,使其应用场所大为减少,因此制备超疏水复合材料时,需要在粗糙度与透明度之间取得平衡。
技术实现要素:
本发明旨在至少解决现有技术中存在的上述技术问题之一。为此,本发明提供了一种超疏水涂料,该涂料可以涂覆于柔性或者刚性材料表面,也可以涂覆于平整或者粗糙的塑料、金属等材质基底上,能够实现自清洁、防水、防冻、防雾、流体减阻和防腐蚀功能,可以被广泛应用于建筑、家电、交通运输、服装、电子器件和液体运输等领域。
本发明还提供了上述超疏水涂料的制备方法。
本发明还提供了上述超疏水涂料的应用。
本发明的第一方面提供了一种超疏水涂料,制备原料包括硅烷化合物、微纳米颗粒和助剂,所述硅烷化合物和微纳米颗粒的质量比为(0.01~100):1,所述微纳米颗粒的粒径在1nm至100μm之间。
本发明中,“超疏水”指水滴落在表面不会被黏附,能够迅速以球状形态弹落或滑落,类似于荷叶表面的水滴状态。
本发明中,“超疏水”一般可以认为是材料的静态接触角大于150°,滚动角小于10°。
本发明的超疏水涂料,至少具有以下有益效果:
本发明的超疏水涂料配方中,硅烷化合物提供疏水性,微纳米颗粒提供粗糙结构与体系强度,助剂提供增强的涂层强度。具体而言,基于硅烷化合物提供的低表面能特性和微纳米颗粒提供的表面粗糙结构,在助剂的共同作用下,该涂料中的主体成分可在多种基材表面快速形成化学键,能够在众多基材表面实现超疏水性能。
本发明的超疏水涂料,利用小分子硅烷或者线性大分子硅烷之间的化学作用,可以在基材表面自发生成稳定的多尺度低表面能分子结构,同时硅烷体系还可以跟微纳米颗粒表面发生反应,从而让整个超疏水涂层稳定地附着在固体基材表面,无论是粗糙的织物、木材等基材,还是平整的玻璃与塑料等基材,本发明的超疏水涂料都可以使之超疏水化。
本发明的超疏水涂料,无需使用含长链烷基的超疏水织物整理剂,也不需要使用硅烷偶联剂,所使用的微纳米颗粒不限于纳米sio2,还可以是其他的无机和有机纳米粒子。
本发明的超疏水涂料,主要利用小分子硅烷或线性硅烷作低表面能物质来源,不需要使用正硅酸乙酯作硅源,不需要使用含氨基的组分作为催化剂,不需要加热,也无需添加固化剂。
本发明的超疏水涂料,由于可以与许多基底材料表面发生化学交联反应从而牢固地附着在基材表面,因此本发明的超疏水涂料所处理的基材不限于织物,还可以是许多其他的固体材料,也可适用于活性的金属表面。
本发明的超疏水涂料,可以在多种粗糙或平整的固体基材表面快速生成稳定的超疏水涂层。
本发明的超疏水涂料,原料成本低,涂料受温度影响小,并具有较好的透明度。
本发明的超疏水涂料,附着力好,适用范围广,尤其适用于各种管道和电子元器件。
本发明的超疏水涂料,数秒或数分钟内即可在基材表面实现超疏水效应。
本发明的超疏水涂料,可以无需添加正硅酸乙酯,在室温下即可调制,无需进行加热处理。
根据本发明的一些实施方式,所述硅烷化合物和微纳米颗粒的质量比为(0.1~10):1。
根据本发明的一些实施方式,所述硅烷化合物和微纳米颗粒的质量比为(0.3~3):1。
根据本发明的一些实施方式,所述硅烷化合物包括链状、支链状的r2-si-(or)2、si2r'(or)2r4、环状或线性的[sir2o]m、聚硅氧烷、改性聚硅氧烷、rn-si-(or)4-n、si2r'(or2)6-nrn、si3r'2(or)8-nrn、si4r'3(or)10-nrn、si(on=cr2)4,其中,r为c1-c20直链或支链烷基、环烷基、芳烯基及其衍生物;
m为1-100000;
n可以为0~8;
or包括nr2、酯基;
r'包括o、ch2、nr、s、nr-r-nr和r-o-r。
根据本发明的一些实施方式,所述硅烷化合物包括二甲基二甲氧基硅烷、二甲基二氯硅烷、甲基三甲氧基硅烷、含氢硅油、二乙基二甲氧基硅烷、二乙基二乙氧基硅烷、二丙基二甲氧基硅烷、二丙基二乙氧基硅烷、二甲基二乙氧基硅烷、聚甲基烷基硅氧烷、聚二甲基硅氧烷、含氢硅油、甲基三乙氧基硅烷、乙基三甲氧基硅烷、乙基三乙氧基硅烷、四甲氧基硅烷、四乙氧基硅烷、二(三乙氧基硅基)甲烷、1,2-二(三乙氧基甲硅烷基)乙烷、甲基三丁酮肟基硅烷、γ-氨丙基-三乙氧基硅烷和γ-环氧丙氧丙基-丙基三甲氧基硅烷中的至少一种。
根据本发明的一些实施方式,所述微纳米颗粒包括无机微纳米颗粒和有机微纳米颗粒。
根据本发明的一些实施方式,所述无机微纳米颗粒包括氧化硅、硅酸盐、碳酸盐、碳化物、硫酸盐、硫化物、钛酸盐、氢氧化物、石英粉、硅灰石、重晶石粉、白瑰粉、晶体碳酸钙、白云石粉、高岭土、纤维状滑石粉、含碳酸钙滑石粉、云母粉、硅藻土、片状滑石粉、天然石墨、硫酸钡、白炭黑、氧化铝、氧化锆、氧化锌、氧化钛和铝粉。
根据本发明的一些实施方式,所述有机微纳米颗粒包括再生纤维素、合成树脂和橡胶颗粒。
根据本发明的一些实施方式,所述微纳米颗粒包括二氧化钛颗粒和二氧化硅颗粒。
根据本发明的一些实施方式,所述微纳米颗粒的粒径在1nm至100μm之间。
根据本发明的一些实施方式,所述微纳米颗粒的粒径在10nm至5μm之间。
根据本发明的一些实施方式,所述微纳米颗粒的粒径在60nm至1μm之间。
根据本发明的一些实施方式,所述助剂包括氰基丙烯酸乙酯、环氧丙烯酸酯、3-氨基丙基三乙氧基硅烷、γ-甲基丙烯酰氧基丙基三甲氧基硅烷和环乙基丙烯酸酯。
根据本发明的一些实施方式,制备原料还包括溶剂。
溶剂提供了各组分的良好分散性与可涂覆性。
本发明的第二方面提供了制备上述超疏水涂料的方法,将所述硅烷化合物、微纳米颗粒和助剂在溶剂中混匀。
根据本发明的一些实施方式,将所述硅烷化合物、微纳米颗粒和助剂在溶剂中混匀的搅拌分散时间可以为0.01h~100h。
本发明制备上述超疏水涂料的方法,至少具有以下有益效果:
本发明的超疏水涂料,在室温下即可调制,无需进行加热处理。
本发明的超疏水涂料,容易施工,可以在金属、塑料等多种基材表面施工。
制备过程中,通过添加微纳米颗粒,提高表面粗糙度,发生了交联反应,形成稳定的超疏水三维结构,在极短时间内(秒或分钟时间内)便可得到超疏水涂层,制备工艺方便快捷。
根据本发明的一些实施方式,所述溶剂包括醇类溶剂、酮类溶剂、醚类溶剂和酯类溶剂。
根据本发明的一些实施方式,所述溶剂可以为与水混溶的溶剂。
根据本发明的一些实施方式,所述溶剂包括甲醇、乙醇、异丙醇、丙酮、甲乙酮、乙醚、二异丙醚、四氢呋喃、乙酸乙酯、乙酸甲酯、环氧丙烷、丙酮、甲基丁酮、甲基异丁酮、乙二醇单甲醚、乙二醇单乙醚和乙二醇单丁醚中的至少一种。
根据本发明的一些实施方式,所述溶剂可以为不溶于水的溶剂。
根据本发明的一些实施方式,所述溶剂包括苯、甲苯、二甲苯、苯乙烯、丁基甲苯、乙烯基甲苯、三氯乙烯、二氯甲烷、氯苯、二氯苯、二硫化碳、四氯化碳、正戊烷、正己烷、环己烷、辛烷、十六烷和液体石蜡等中的至少一种。
根据本发明的一些实施方式,所述溶剂与所述硅烷化合物的质量比为(0.01~1000):1。
根据本发明的一些实施方式,所述溶剂与所述硅烷化合物的质量比为(0.01~100):1。
根据本发明的一些实施方式,所述溶剂与所述硅烷化合物的质量比为(0.05~20):1。
本发明的第三方面提供了一种超疏水涂层,该超疏水涂层由上述的超疏水涂料制备得到。
根据本发明的一些实施方式,所述超疏水涂层的静态接触角大于150°,滚动角小于10°。
本发明的超疏水涂层,具有良好的耐磨耐久性能。
本发明的超疏水涂层,可以通过对无机粉体的修饰改性进一步增强各项性能,能适应于不同的应用需要。
本发明的超疏水涂层,涂覆于基材表面,基材可以为金属或非金属材质。
本发明的超疏水涂层,涂覆于基材表面,基材可以为金属,包括铝、铁、铜、锌、钛、镁、锡、镍、银及其合金和氧化物。
本发明的超疏水涂层,涂覆于基材表面,基材可以为塑料。
本发明的超疏水涂层,涂覆于基材表面,基材可以为陶瓷,包括玻璃陶瓷、氧化物陶瓷、氮化物陶瓷、碳化物陶瓷、硼化物陶瓷、氧化铝陶瓷、氧化锆陶瓷、氧化镁陶瓷、氮化硅陶瓷、氮化硼陶瓷、氮化铝陶瓷、氮化钛陶瓷、碳化硅陶瓷、碳化硼陶瓷、碳化钛陶瓷、碳化锆陶瓷等常规及功能陶瓷。
本发明的超疏水涂层,涂覆于基材表面,基材可以为复合材料。
本发明的超疏水涂层,涂覆于基材表面,基材可以为刚性基材。
本发明的超疏水涂层,涂覆于基材表面,基材可以为柔性基材。
本发明的超疏水涂层,涂覆于基材表面,基材可以为聚合物基材,包括聚烯烃类(聚乙烯、聚丙烯、聚苯乙烯、abs树脂、聚异丁烯等)、聚卤代烯烃类(聚四氟乙烯、聚偏氟乙烯、聚氯乙烯烃等)、聚醚类(聚甲醛、聚苯醚、氯化聚醚、聚苯硫醚、聚醚醚酮等)、聚酯类(聚碳酸酯、聚对苯二甲酸丁二醇酯、聚对苯二甲酸二甲酯、聚芳酯等)、聚丙烯酸及其衍生物类(聚丙烯腈、聚甲基丙烯酸甲酯、聚甲基丙烯酸乙酯、聚甲基丙烯酸丁酯等)、聚氨基甲酸酯、聚砜类(聚砜、聚芳砜和聚醚砜)、聚酰胺(脂肪族聚酰胺和芳香族聚酰胺,聚丁内酰胺、聚己内酰胺、聚7-胺基庚酸、聚辛内酰胺、聚11-胺基十一酸、聚十二内酰胺、聚己二胺己二酸、聚己二胺癸二酸、聚间苯二甲酰间苯二胺、聚对苯二甲酰对苯二胺、聚对苯二甲酰胺)、聚环氧树脂(缩水甘油类、非缩水甘油类,前者包括缩水甘油醚类、缩水甘油酯类、缩水甘油胺类,后者包括脂肪族类、环氧化烯烃类、新型环氧树脂类)、纤维素及其衍生物。
本发明的超疏水涂层,涂覆方法可以为旋涂、滴涂、浸涂、刷涂、刮涂和喷涂。
本发明的超疏水涂层,涂布后,干燥温度为0℃~200℃,干燥时间为0.01h~1000h。
附图说明
图1是实施例1的涂料涂布于木材表面滴加光学液滴的示意图。
图2是实施例1的涂料涂布于玻璃表面滴加光学液滴的示意图。
图3是实施例1的涂料涂布于聚四氟乙烯表面滴加光学液滴的示意图。
图4是实施例1的涂料涂布于纸张表面滴加光学液滴的示意图。
图5是实施例1的涂料制备的涂层的水柱冲刷试验示意图。
图6是实施例1的涂料涂布于棉布上的油水分离试验示意图。
图7是实施例1的涂料制备的涂层的连续沸水试验示意图。
图8是实施例2的涂层接触角测试结果图。
图9是实施例3的涂层接触角测试结果图。
图10是实施例4的涂层接触角测试结果图。
图11是实施例5的涂层接触角测试结果图。
图12是实施例6的涂层接触角测试结果图。
图13是实施例7的涂层接触角测试结果图。
图14是实施例8的涂层接触角测试结果图。
图15是实施例3的涂层的低温试验结果示意图。
图16是实施例4的涂层摩擦前的接触角测试结果。
图17是实施例4的涂层摩擦后的接触角测试结果。
具体实施方式
以下是本发明的具体实施例,并结合实施例对本发明的技术方案作进一步的描述,但本发明并不限于这些实施例。
实施例1
本实施例制备了一种超双疏涂料,具体制备过程为:
先在5g二甲基二甲氧基硅烷中依次加入20ml异丙醇、0.3g二氧化钛(100纳米)、3ml氰基丙烯酸乙醇,搅拌分散3min。
使用本实施例的超疏水涂料时,可以通过旋涂方式在基材表面涂布混合均匀的混合液。
70℃下空气干燥2min,然后用蒸馏水和乙醇冲洗涂层表面,在室温下空气干燥5min,即获得超疏水涂层。
实施例2
本实施例制备了一种超疏水涂料,具体制备过程为:
先在5g二甲基二氯硅烷中依次加入20ml异丙醇、2g甲基三甲氧基硅烷、0.5g二氧化硅(100纳米),5ml氰基丙烯酸乙醇,搅拌分散3min,通过喷涂方式在玻璃基材表面涂布混合均匀的混合液。
50℃下空气干燥5min,然后用蒸馏水和乙醇冲洗涂层表面,20℃下空气干燥3min,即获得超疏水涂层。
实施例3
本实施例制备了一种超疏水涂料,具体制备过程为:
先在5g二甲基二氯硅烷中依次加入10ml甲苯、0.6g二氧化硅(100纳米)、1.2g环氧丙烯酸酯,搅拌分散3min,通过浸涂方式在基材表面涂布混合均匀的混合液。
25℃下空气干燥5min,然后用蒸馏水和乙醇冲洗涂层表面,20℃下空气干燥10min,即获得超疏水涂层。
实施例4
本实施例制备了一种超疏水涂料,具体制备过程为:
先在0.5g二甲基二氯硅烷中加入10ml甲苯、1.4g甲基三甲氧基硅烷、0.5g二氧化硅(100纳米)、1.2g环氧丙烯酸酯,搅拌分散3min,通过刷涂方式在基材表面涂布混合均匀的混合液。
20℃下空气干燥3min,然后用蒸馏水冲洗涂层表面,20℃下空气干燥10min,即获得超疏水涂层。
实施例5
本实施例制备了一种超疏水涂料,具体制备过程为:
先在2g甲基三甲氧基硅烷中加入10ml甲苯、0.5g二氧化硅(100纳米)、3g氰基丙烯酸乙酯,搅拌分散3min,通过刷涂方式在基材表面涂布混合均匀的混合液。
20℃下空气干燥5min,然后用蒸馏水冲洗涂层表面,20℃下空气干燥10min,即获得超疏水涂层。
实施例6
本实施例制备了一种超疏水涂料,具体制备过程为:
先在1g甲基三甲氧基硅烷中加入10ml甲苯、0.3g二氧化硅(100纳米)、3g氰基丙烯酸乙醇、1g甲基三甲氧基硅烷、,搅拌分散3min,通过刷涂方式在基材表面涂布混合均匀的混合液。
25℃下空气干燥5min,然后用蒸馏水冲洗涂层表面,20℃下空气干燥10min,即获得超疏水涂层。
实施例7
本实施例制备了一种超疏水涂料,具体制备过程为:
先在0.5g含氢硅油中加入10ml甲苯、0.5g二氧化硅(100纳米)、5g氰基丙烯酸乙醇,搅拌分散3min,通过刷涂方式在基材表面涂布混合均匀的混合液。
25℃下空气干燥5min,然后用蒸馏水冲洗涂层表面,20℃下空气干燥10min,即获得超疏水涂层。
实施例8
本实施例制备了一种超疏水涂料,具体制备过程为:
先在0.5g含氢硅油中依次加入15ml己烷、1.2g二氧化硅(100纳米)、5g氰基丙烯酸乙醇,搅拌分散3min,通过刷涂方式在基材表面涂布混合均匀的混合液。
25℃下空气干燥5min,然后用蒸馏水冲洗涂层表面,20℃下空气干燥10min,即获得超疏水涂层。
实施例9
本实施例制备了一种超疏水涂料,具体制备过程为:
先在1g二乙基二乙氧基硅烷中加入10ml甲苯、0.2g二氧化硅(100纳米)、4g氰基丙烯酸乙酯,搅拌分散3min,通过刷涂方式在基材表面涂布混合均匀的混合液。
20℃下空气干燥5min,然后用蒸馏水冲洗涂层表面,20℃下空气干燥8min,即获得超疏水涂层。
实施例10
本实施例制备了一种超疏水涂料,具体制备过程为:
先在0.5gγ-氨丙基-三乙氧基硅烷中加入105ml甲苯、0.15g二氧化硅(100纳米)、4g氰基丙烯酸乙酯,搅拌分散3min,通过刷涂方式在基材表面涂布混合均匀的混合液。
20℃下空气干燥5min,然后用蒸馏水冲洗涂层表面,20℃下空气干燥8min,即获得超疏水涂层。
检测例1
将实施例1的涂料涂布于木材、玻璃、聚四氟乙烯和纸张表面,滴加光学液滴后,超双疏性能如图1至图4所示。
其中,图1为木材表面示意图,图2为玻璃表面示意图,图3为聚四氟乙烯表面示意图,图4为纸张表面示意图。
此外,进一步测试了实施例1的涂层的动态接触角,其中,前进角为165.43°,后退角为164.97°。
检测例2
以实施例1的涂料为试验对象,将涂料涂覆于玻璃基材表面,进行了水柱冲刷试验,结果如图5所示,从图5可以看出,涂层经水柱冲刷后,表面未附着任何水滴。
检测例3
以实施例1的涂料为试验对象,将实施例1的涂料涂布于棉布上进行油水分离试验,效果如图6所示。图6中,左侧为水,右侧为正十六烷。从图6可以看出,油水分离效果良好。
检测例4
以实施例1的涂层为试验对象,将涂料涂布于玻璃表面,进行连续沸水试验,结果如图7所示。从图7可以看出,涂层的稳定性良好。
检测例5
测试了实施例2至实施例8制备的涂层的接触角。结果如图8至图14所示。从图8至图14可以看出,各实施例制备的涂层均能达到超疏效果。
检测例6
测试了实例3的涂层在-80℃下冷冻5天后的接触角,结果如图15所示。从图15可以看出,涂层经过低温长时间冷冻后,仍然具有良好的超疏水性能。
检测例7
测试了实例4的涂层经摩擦后的接触角,摩擦测试的方法为:将涂层涂覆于玻璃基材上,将有玻璃片有涂层的一面覆于1500目砂纸,玻璃片上放置100g砝码,在外力作用下分别沿水平和垂直两个方向推10cm(推一次)。
摩擦前的接触角测试结果如图16所示。
摩擦后的接触角测试结果如图17所示。
对比图16和图17可以看出,摩擦前后接触角变化微小,说明书涂层具有较好的耐磨性能。
上面结合实施例对本发明作了详细说明,但是本发明不限于上述实施例,在所属技术领域普通技术人员所具备的知识范围内,还可以在不脱离本发明宗旨的前提下作出各种变化。
本文用于企业家、创业者技术爱好者查询,结果仅供参考。