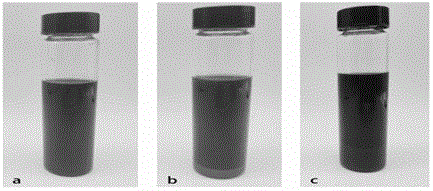
本发明涉及散热涂料领域,公开了一种水性环保石墨烯散热涂料及制备方法。
背景技术:
随着电子行业的高速发展,电子产品向微型化发展以及5g等高端技术的发展,电子系统的集成度也越来越高,高热密度成为一种发展趋势,由于散热不良导致的电子设备鼓胀越来越多。因而,电子行业的发展要求各种元器件高效工作,极小的元器件工作产生的热量需要及时快速散发以保证持久的工作寿命。如何有效解决电子元器件的散热问题成为整个电子行业发展亟待解决的关键问题。
传统的散热方法包括风冷、液冷等,但上述方法存在设施占用空间大、重量大、系统复杂等缺陷,无法满足电子器件微型化、小型化及精密化的趋势。散热涂料作为一种提高物体表面散热效率、降低体系温度的特种涂料,其制备方法简单经济。因此,听过散热涂料来解决电子器件的散热问题成为一个重要方向。
通常,散热涂料等的散热方式主要有通过接触的方式进行传导散热;凭借外界的流体流动来交换对流散热;以辐射形式将热量传给温度较低的周围环境中的散热方式。而大部分元器件较小,难以产生良好空间对流散热,主要依靠高效的热传导和热辐射散热。而传统的氮化硼、氮化硅、金属铝粉等用于散热涂料的散热效果难以达到要求。
电子器件的金属表面基本为热传导散热,而热辐射的系数较低,由于金属表面缺少热辐射效应,因此散热效果有限,难以适应高效散热的需要。石墨烯是一种具有高热传导系数的材料,导热系数高达5300w/(m·k),同时石墨烯具有极高的热辐射性,相比于金属,散热效率得到极大的提升。目前,已有将石墨烯制备成散热涂料,涂敷在需要散热的器件、金属表面,通过热传导、热辐射大幅提升了散热的效率。
为了石墨烯散热涂料具备良好的涂层成膜性和附着性,涂料中通常使用高分子成膜剂。中国发明专利申请号201410830903.2公开了一种高效石墨烯基散热涂料、其制备方法及应用,由石墨烯复合粉体1~15份、填料10~30份、高分子粘接剂30~50份、溶剂35~60份组成。然而,为了涂层成膜和附着,使用较多的高分子粘接剂,较多的高分子粘接剂不但使涂料粘稠石墨烯分散难度增加,而且会影响散热效果。尤其是,在一些需要高温的散热管道器件,使用高分子成膜粘接剂存在挥发份污染,容易老化致使涂层失效。
研究表明,采用无机成膜体系的石墨烯散热涂料,能够解决耐高温的问题。中国发明专利申请号201910192960.5公开了一种石墨烯水性散热涂料,此散热涂料以水为稀释剂,采用石墨烯分散液与导热粉分散浆作为复合导热填料组份。然而,石墨烯在无机涂料体系中的分散难度远远大于在高分子涂料体系中的分散。而且石墨烯极易与无机涂料体系分离沉降。
根据上述,现有方案中用于电子器件散热的石墨烯散热涂料,当利用高分子成膜剂时,需要较多成膜剂,由于成膜剂存在涂层存在挥发份污染,容易老化致使涂层失效;而利用无机成膜体系制备散热涂料时,石墨烯在无机涂料中的分散性差,石墨烯极易与无机涂料体系分离沉降,影响散热性能。
技术实现要素:
目前应用较广的石墨烯散热涂料,有机涂料需要较多成膜剂,存在涂层易老化失效且污染的问题;而无机涂料体系中的石墨烯分散性差,容易分离沉降的问题。针对此问题缺陷,本发明提出一种水性环保石墨烯散热涂料及制备方法。
本发明通过以下技术方案解决上述问题:
一种水性环保石墨烯散热涂料的制备方法,制备的具体过程为:
(1)先将石墨烯、木质素磺酸钠加入磷酸二氢铝溶液中,在球磨机中研磨分散,然后烘干,再加热进行高温处理,最后冷却研磨,出料,得到预处理石墨烯;各原料配比为,按重量份计,石墨烯8~12重量份、木质素磺酸钠0.1~0.2重量份、磷酸二氢铝溶液50~60重量份;
(2)先将步骤(1)得到预处理石墨烯、分散剂、铜粉、硅酸钠溶液加入篮式砂磨机中,然后研磨分散,出料,得到预分散浆料;各原料配比为,按重量份计,预处理石墨烯10~15重量份、分散剂0.5~1重量份、铜粉3~5重量份、硅酸钠溶液80~90重量份;
(3)先将步骤(2)得到的预分散浆料、α-氧化铝、氮化硅、氮化硼、增稠剂、消泡剂、防沉剂、去离子水、三聚磷酸钠加入球磨机,然后球磨分散均匀,出料,罐装,即得水性环保石墨烯散热涂料;各原料配比为,按重量份计,预分散浆料90~110重量份、α-氧化铝1~3重量份、氮化硅0.5~1重量份、氮化硼1~2重量份、增稠剂0.1~0.5重量份、消泡剂0.1~0.2重量份、防沉剂0.5~1重量份、去离子水15~20重量份、三聚磷酸钠0.1~0.2重量份。
为了获得安全环保、耐高温的石墨烯散热涂料,本发明选择硅酸钠涂料体系,通过将石墨烯分散在硅溶胶的无机粘接成膜物涂料体系中,涂料的耐高温性会大幅提升,同时无污染,耐久性好。针对石墨烯在硅酸钠涂料体系中分散性差,易分离沉降的问题,本发明创造性地采取以下解决方案。
本发明先将石墨烯、木质素磺酸钠加入磷酸~二氢铝溶液中研磨分散,控制各原料的配比(石墨烯、木质素磺酸钠、磷酸二氢铝溶液的重量比例为10:0.1~0.2:50~60),烘干后高温处理,冷却研磨得到预处理石墨烯。
选择木质素磺酸钠,主要是利用木质素磺酸钠优异的分散性,并且具有成本低、环境友好的优点,通过研磨分散,可使石墨烯均匀分散在磷酸二氢铝溶液中。
磷酸二氢铝溶液具有良好的热固化粘接特性,通过加入木质素磺酸钠后与石墨烯研磨分散,石墨烯均匀分散在磷酸二氢铝溶液中,烘干后再通过逐级高温处理,磷酸二氢铝脱水缩聚结合,不断形成陶瓷结合,从而在石墨烯的表面形成保护层,进一步通过研磨细化,可以得到有保护层的预处理石墨烯,获得的预处理石墨烯在硅酸钠溶液的无机涂料体系中易于分散。作为本发明的优选,步骤(1)所述磷酸二氢铝溶液的质量浓度为15~20%;所述烘干的温度为200~300℃,时间为20~40min;所述高温处理的过程为,先在400~500℃下处理10~20min,然后升温到900~1000℃处理5~10min。
本发明然后将有保护层的预处理石墨烯与分散剂、铜粉、硅酸钠溶液研磨分散得到预分散浆料。
铜粉的加入,可以有效保证涂料的散热导热性能。
分散剂选择聚羧酸盐,聚羧酸盐分散剂作为一种高分子分散剂,其聚羧酸主链易与预处理石墨烯颗粒发生表面吸附,阻碍了颗粒间的相互接近,从而获得持久的分散性,有效阻止石墨烯的团聚、沉降。作为本发明的优选,步骤(2)所述分散剂为聚羧酸盐。作为本发明的进一步优选,所述分散剂为聚羧酸盐分散剂5050、聚羧酸盐分散剂5040中的一种。
预处理石墨烯与硅酸钠溶液亲和性好,在分散剂的作用下,研磨分散后,使得预处理易于均匀分散在硅酸钠溶液中,有效克服了离析沉降问题。作为本发明的优选,步骤(2)所述硅酸钠溶液为40波美度(固含量35%左右)。
作为本发明的优选,步骤(2)所述研磨分散的转速为200~400r/min。
本发明最后将得到的预分散浆料与α-氧化铝、氮化硅、氮化硼、增稠剂、消泡剂、防沉剂、去离子水、三聚磷酸钠球磨分散均匀,即可得到水性环保石墨烯散热涂料。
α-氧化铝、氮化硅、氮化硼均是常用的散热填料,小粒径的上述填料均有良好的导热散热性能;本发明将预分散浆料与α-氧化铝、氮化硅、氮化硼及助剂球磨分散均匀得到散热涂料,涂料中分散的铜粉、α-氧化铝、氮化硅、氮化硼,可与石墨烯有效协同,使得得到的散热涂料通过硅酸钠粘接固化成膜,形成热传导、热辐射协同的散热网络,石墨烯分散均匀,进而协同发挥很好的散热效果。作为本发明的优选,步骤(3)所述α-氧化铝的粒径小于10μm;所述氮化硅的粒径小于20μm;所述氮化硼的粒径小于10μm。
本发明获得的散热涂料中,助剂主要有增稠剂、消泡剂、防沉剂。
作为本发明的优选,步骤(3)所述增稠剂为羧甲基纤维素钠、海藻酸钠、壳聚糖中的至少一种。
作为本发明的优选,步骤(3)所述消泡剂为硅油。
防沉剂通过吸水膨胀,可形成胶态,进而缔合网络结构,具有超强的束缚并隔离固体的能力,促使石墨烯悬浮,最终使得涂料形成的涂层中分布石墨烯分散均匀的散热网络。作为本发明的优选,步骤(3)所述防沉剂为钙基膨润土、钠基膨润土、凹凸棒、海泡石、硅藻土中的至少一种。
由上述方法制备得到的一种水性环保石墨烯散热涂料,其中的石墨烯在涂料中分散均匀,有效避免了离析沉降,同时涂料的散热性和耐热性优异。通过测试,制备的石墨烯散热涂料在静置24h后无明显沉降;散热效果测试中,涂覆涂料的铝板在恒温至180℃后,铝板在10s的温度为127.0~128.1℃,铝板在20s的温度为90.8~91.5℃,铝板在30s的温度为47.4~48.1℃。
本发明提供的一种水性环保石墨烯散热涂料及制备方法,将石墨烯、木质素磺酸钠加入磷酸二氢铝溶液在球磨机中研磨分散,然后烘干,进一步逐级高温处理,冷却研磨,得到预处理石墨烯;将得到预处理石墨烯、分散剂、铜粉、硅酸钠溶液加入篮式砂磨机研磨分散,得到预分散浆料;将预分散浆料、α-氧化铝、氮化硅、氮化硼、增稠剂、消泡剂、防沉剂、去离子水、三聚磷酸钠加入球磨机,球磨分散均匀,罐装,即可。
本发明提供了一种水性环保石墨烯散热涂料及制备方法,与现有技术相比,其突出的特点和优异的效果在于:
1、提出了利用木质素磺酸钠、磷酸二氢铝溶液预处理石墨烯制备水性环保石墨烯散热涂料的方法。
2、通过将石墨烯与木质素磺酸钠、磷酸二氢铝溶液研磨分散,使石墨烯均匀分散在磷酸二氢铝溶液,进一步热处理后,磷酸二氢铝形成陶瓷结合在石墨烯的表面形成保护层,得到的预处理石墨烯与硅酸钠溶液亲和性好,易于均匀分散在硅酸钠溶液中,进而在硅酸钠涂料中克服了石墨烯离析沉降问题。
3、通过加入聚羧酸盐分散剂,聚羧酸主链易与预处理石墨烯颗粒表面吸附,可阻碍了颗粒相互接近,从而获得持久的分散性,有效阻止石墨烯的团聚、沉降。
4、本发明的水性环保涂料中,分散了铜粉、α-氧化铝、氮化硅、氮化硼,与石墨烯协同,得到的散热涂料通过硅酸钠粘接固化成膜,形成热传导、热辐射协同的散热网络,获得的涂料散热性能和耐高温性优异,适合用于300~500℃的散热表面,可广泛用于高温管路散热等方面。
附图说明
图1为石墨烯散热涂料的静置沉降图;其中,a为实施例6的石墨烯散热涂料的静置沉降图;b为对比例1的石墨烯散热涂料的静置沉降图;c为对比例2的石墨烯散热涂料的静置沉降图。
具体实施方式
以下通过具体实施方式对本发明作进一步的详细说明,但不应将此理解为本发明的范围仅限于以下的实例。在不脱离本发明上述方法思想的情况下,根据本领域普通技术知识和惯用手段做出的各种替换或变更,均应包含在本发明的范围内。
实施例1
(1)先将石墨烯、木质素磺酸钠加入磷酸二氢铝溶液中,在球磨机中研磨分散,然后烘干,再加热进行高温处理,最后冷却研磨,出料,得到预处理石墨烯;磷酸二氢铝溶液的质量浓度为17%;烘干的温度为260℃,时间为28min;高温处理的过程为,先在460℃下处理14min,然后升温到960℃处理7min;
各原料配比为,按重量份计,石墨烯11重量份、木质素磺酸钠0.16重量份、磷酸二氢铝溶液54重量份;
(2)先将步骤(1)得到预处理石墨烯、分散剂、铜粉、硅酸钠溶液加入篮式砂磨机中,然后研磨分散,出料,得到预分散浆料;分散剂为聚羧酸盐;硅酸钠溶液为40波美度;研磨分散的转速为280r/min;
各原料配比为,按重量份计,预处理石墨烯13重量份、分散剂0.7重量份、铜粉4重量份、硅酸钠溶液86重量份;
(3)先将步骤(2)得到的预分散浆料、α-氧化铝、氮化硅、氮化硼、增稠剂、消泡剂、防沉剂、去离子水、三聚磷酸钠加入球磨机,然后球磨分散均匀,出料,罐装,即得水性环保石墨烯散热涂料;α-氧化铝的平均粒径为8μm;氮化硅的平均粒径为17μm;氮化硼的平均粒径为8μm;增稠剂为羧甲基纤维素钠;消泡剂为硅油;防沉剂为钙基膨润土;
各原料配比为,按重量份计,预分散浆料98重量份、α-氧化铝1.8重量份、氮化硅0.7重量份、氮化硼1.6重量份、增稠剂0.3重量份、消泡剂0.15重量份、防沉剂0.7重量份、去离子水17重量份、三聚磷酸钠0.16重量份。
实施例1制得的水性环保石墨烯散热涂料,其分散性测试的涂料静置情况、散热效果测试的铝板温度情况如表1所示。
实施例2
(1)先将石墨烯、木质素磺酸钠加入磷酸二氢铝溶液中,在球磨机中研磨分散,然后烘干,再加热进行高温处理,最后冷却研磨,出料,得到预处理石墨烯;磷酸二氢铝溶液的质量浓度为16%;烘干的温度为220℃,时间为35min;高温处理的过程为,先在420℃下处理18min,然后升温到920℃处理9min;
各原料配比为,按重量份计,石墨烯9重量份、木质素磺酸钠0.12重量份、磷酸二氢铝溶液58重量份;
(2)先将步骤(1)得到预处理石墨烯、分散剂、铜粉、硅酸钠溶液加入篮式砂磨机中,然后研磨分散,出料,得到预分散浆料;分散剂为聚羧酸盐;硅酸钠溶液为40波美度;研磨分散的转速为250r/min;
各原料配比为,按重量份计,预处理石墨烯11重量份、分散剂0.6重量份、铜粉3.5重量份、硅酸钠溶液88重量份;
(3)先将步骤(2)得到的预分散浆料、α-氧化铝、氮化硅、氮化硼、增稠剂、消泡剂、防沉剂、去离子水、三聚磷酸钠加入球磨机,然后球磨分散均匀,出料,罐装,即得水性环保石墨烯散热涂料;α-氧化铝的平均粒径为7μm;氮化硅的平均粒径为16m;氮化硼的平均粒径为7μm;增稠剂为海藻酸钠;消泡剂为硅油;防沉剂为钠基膨润土;
各原料配比为,按重量份计,预分散浆料95重量份、α-氧化铝1.5重量份、氮化硅0.6重量份、氮化硼1.2重量份、增稠剂0.2重量份、消泡剂0.12重量份、防沉剂0.6重量份、去离子水19重量份、三聚磷酸钠0.12重量份。
实施例2制得的水性环保石墨烯散热涂料,其分散性测试的涂料静置情况、散热效果测试的铝板温度情况如表1所示。
实施例3
(1)先将石墨烯、木质素磺酸钠加入磷酸二氢铝溶液中,在球磨机中研磨分散,然后烘干,再加热进行高温处理,最后冷却研磨,出料,得到预处理石墨烯;磷酸二氢铝溶液的质量浓度为19%;烘干的温度为280℃,时间为25min;高温处理的过程为,先在480℃下处理12min,然后升温到980℃处理6min;
各原料配比为,按重量份计,石墨烯11重量份、木质素磺酸钠0.18重量份、磷酸二氢铝溶液52重量份;
(2)先将步骤(1)得到预处理石墨烯、分散剂、铜粉、硅酸钠溶液加入篮式砂磨机中,然后研磨分散,出料,得到预分散浆料;分散剂为聚羧酸盐;硅酸钠溶液为40波美度;研磨分散的转速为350r/min;
各原料配比为,按重量份计,预处理石墨烯14重量份、分散剂0.9重量份、铜粉44.5重量份、硅酸钠溶液82重量份;
(3)先将步骤(2)得到的预分散浆料、α-氧化铝、氮化硅、氮化硼、增稠剂、消泡剂、防沉剂、去离子水、三聚磷酸钠加入球磨机,然后球磨分散均匀,出料,罐装,即得水性环保石墨烯散热涂料;α-氧化铝的平均粒径为9μm;氮化硅的平均粒径为18μm;氮化硼的平均粒径为9μm;增稠剂为壳聚糖;消泡剂为硅油;防沉剂为凹凸棒;
各原料配比为,按重量份计,预分散浆料105重量份、α-氧化铝2.5重量份、氮化硅0.9重量份、氮化硼1.8重量份、增稠剂0.4重量份、消泡剂0.18重量份、防沉剂0.8重量份、去离子水16重量份、三聚磷酸钠0.18重量份。
实施例3制得的水性环保石墨烯散热涂料,其分散性测试的涂料静置情况、散热效果测试的铝板温度情况如表1所示。
实施例4
(1)先将石墨烯、木质素磺酸钠加入磷酸二氢铝溶液中,在球磨机中研磨分散,然后烘干,再加热进行高温处理,最后冷却研磨,出料,得到预处理石墨烯;磷酸二氢铝溶液的质量浓度为15%;烘干的温度为200℃,时间为40min;高温处理的过程为,先在400℃下处理20min,然后升温到900℃℃处理10min;
各原料配比为,按重量份计,石墨烯8重量份、木质素磺酸钠0.1重量份、磷酸二氢铝溶液60重量份;
(2)先将步骤(1)得到预处理石墨烯、分散剂、铜粉、硅酸钠溶液加入篮式砂磨机中,然后研磨分散,出料,得到预分散浆料;分散剂为聚羧酸盐;硅酸钠溶液为40波美度;研磨分散的转速为200r/min;
各原料配比为,按重量份计,预处理石墨烯10重量份、分散剂0.5重量份、铜粉3重量份、硅酸钠溶液90重量份;
(3)先将步骤(2)得到的预分散浆料、α-氧化铝、氮化硅、氮化硼、增稠剂、消泡剂、防沉剂、去离子水、三聚磷酸钠加入球磨机,然后球磨分散均匀,出料,罐装,即得水性环保石墨烯散热涂料;α-氧化铝的平均粒径为5μm;氮化硅的平均粒径为14μm;氮化硼的平均粒径为5μm;增稠剂为羧甲基纤维素钠;消泡剂为硅油;防沉剂为海泡石;
各原料配比为,按重量份计,预分散浆料90重量份、α-氧化铝1重量份、氮化硅0.5重量份、氮化硼1重量份、增稠剂0.1重量份、消泡剂0.1重量份、防沉剂0.5重量份、去离子水20重量份、三聚磷酸钠0.1重量份。
实施例4制得的水性环保石墨烯散热涂料,其分散性测试的涂料静置情况、散热效果测试的铝板温度情况如表1所示。
实施例5
(1)先将石墨烯、木质素磺酸钠加入磷酸二氢铝溶液中,在球磨机中研磨分散,然后烘干,再加热进行高温处理,最后冷却研磨,出料,得到预处理石墨烯;磷酸二氢铝溶液的质量浓度为20%;烘干的温度为300℃,时间为20min;高温处理的过程为,先在500℃下处理10min,然后升温到1000℃处理5min;
各原料配比为,按重量份计,石墨烯12重量份、木质素磺酸钠0.2重量份、磷酸二氢铝溶液50重量份;
(2)先将步骤(1)得到预处理石墨烯、分散剂、铜粉、硅酸钠溶液加入篮式砂磨机中,然后研磨分散,出料,得到预分散浆料;分散剂为聚羧酸盐;硅酸钠溶液为40波美度;研磨分散的转速为400r/min;
各原料配比为,按重量份计,预处理石墨烯15重量份、分散剂1重量份、铜粉5重量份、硅酸钠溶液80重量份;
(3)先将步骤(2)得到的预分散浆料、α-氧化铝、氮化硅、氮化硼、增稠剂、消泡剂、防沉剂、去离子水、三聚磷酸钠加入球磨机,然后球磨分散均匀,出料,罐装,即得水性环保石墨烯散热涂料;α-氧化铝的平均粒径为10μm;氮化硅的平均粒径为20μm;氮化硼的平均粒径为10μm;增稠剂为海藻酸钠;消泡剂为硅油;防沉剂为硅藻土;
各原料配比为,按重量份计,预分散浆料110重量份、α-氧化铝3重量份、氮化硅1重量份、氮化硼2重量份、增稠剂0.5重量份、消泡剂0.2重量份、防沉剂1重量份、去离子水15重量份、三聚磷酸钠0.2重量份。
实施例5制得的水性环保石墨烯散热涂料,其分散性测试的涂料静置情况、散热效果测试的铝板温度情况如表1所示。
实施例6
(1)先将石墨烯、木质素磺酸钠加入磷酸二氢铝溶液中,在球磨机中研磨分散,然后烘干,再加热进行高温处理,最后冷却研磨,出料,得到预处理石墨烯;磷酸二氢铝溶液的质量浓度为17.5%;烘干的温度为250℃,时间为30min;高温处理的过程为,先在450℃下处理15min,然后升温到950℃处理8min;
各原料配比为,按重量份计,石墨烯10重量份、木质素磺酸钠0.15重量份、磷酸二氢铝溶液55重量份;
(2)先将步骤(1)得到预处理石墨烯、分散剂、铜粉、硅酸钠溶液加入篮式砂磨机中,然后研磨分散,出料,得到预分散浆料;分散剂为聚羧酸盐;硅酸钠溶液为40波美度;研磨分散的转速为300r/min;
各原料配比为,按重量份计,预处理石墨烯12.5重量份、分散剂0.75重量份、铜粉4重量份、硅酸钠溶液85重量份;
(3)先将步骤(2)得到的预分散浆料、α-氧化铝、氮化硅、氮化硼、增稠剂、消泡剂、防沉剂、去离子水、三聚磷酸钠加入球磨机,然后球磨分散均匀,出料,罐装,即得水性环保石墨烯散热涂料;α-氧化铝的平均粒径为8μm;氮化硅的平均粒径为18μm;氮化硼的平均粒径为8μm;增稠剂为壳聚糖;消泡剂为硅油;防沉剂为钙基膨润土;
各原料配比为,按重量份计,预分散浆料100重量份、α-氧化铝2重量份、氮化硅0.75重量份、氮化硼1.5重量份、增稠剂0.3重量份、消泡剂0.15重量份、防沉剂0.75重量份、去离子水17.5重量份、三聚磷酸钠0.15重量份。
实施例6制得的水性环保石墨烯散热涂料,其分散性测试的涂料静置情况、散热效果测试的铝板温度情况如表1及图1所示。
对比例1
(1)将石墨烯、分散剂、铜粉、硅酸钠溶液加入篮式砂磨机中,然后研磨分散,出料,得到预分散浆料;分散剂为聚羧酸盐;硅酸钠溶液为40波美度;研磨分散的转速为300r/min;
各原料配比为,按重量份计,石墨烯12.5重量份、分散剂0.75重量份、铜粉4重量份、硅酸钠溶液85重量份;
(2)将步骤(1)得到的预分散浆料、α-氧化铝、氮化硅、氮化硼、增稠剂、消泡剂、防沉剂、去离子水、三聚磷酸钠加入球磨机,然后球磨分散均匀,出料,罐装,即得水性环保石墨烯散热涂料;α-氧化铝的平均粒径为8μm;氮化硅的平均粒径为18μm;氮化硼的平均粒径为8μm;增稠剂为壳聚糖;消泡剂为硅油;防沉剂为钙基膨润土;
各原料配比为,按重量份计,预分散浆料100重量份、α-氧化铝2重量份、氮化硅0.75重量份、氮化硼1.5重量份、增稠剂0.3重量份、消泡剂0.15重量份、防沉剂0.75重量份、去离子水17.5重量份、三聚磷酸钠0.15重量份。
对比例1石墨烯没有与磷酸二氢铝复合进行预处理,而是直接使用石墨烯,其他制备条件与实施例6相同,制得的石墨烯散热涂料,其分散性测试的涂料静置情况、散热效果测试的铝板温度情况如表1及图1所示。
对比例2
(1)先将石墨烯、加入磷酸二氢铝溶液中,在球磨机中研磨分散,然后烘干,再加热进行高温处理,最后冷却研磨,出料,得到预处理石墨烯;磷酸二氢铝溶液的质量浓度为17.5%;烘干的温度为250℃,时间为30min;高温处理的过程为,先在450℃下处理15min,然后升温到950℃处理8min;
各原料配比为,按重量份计,石墨烯10重量份、磷酸二氢铝溶液55重量份;
(2)先将步骤(1)得到预处理石墨烯、分散剂、铜粉、硅酸钠溶液加入篮式砂磨机中,然后研磨分散,出料,得到预分散浆料;分散剂为聚羧酸盐;硅酸钠溶液为40波美度;研磨分散的转速为300r/min;
各原料配比为,按重量份计,预处理石墨烯12.5重量份、分散剂0.75重量份、铜粉4重量份、硅酸钠溶液85重量份;
(3)先将步骤(2)得到的预分散浆料、α-氧化铝、氮化硅、氮化硼、增稠剂、消泡剂、防沉剂、去离子水、三聚磷酸钠加入球磨机,然后球磨分散均匀,出料,罐装,即得水性环保石墨烯散热涂料;α-氧化铝的平均粒径为8μm;氮化硅的平均粒径为18μm;氮化硼的平均粒径为8μm;增稠剂为壳聚糖;消泡剂为硅油;防沉剂为钙基膨润土;
各原料配比为,按重量份计,预分散浆料100重量份、α-氧化铝2重量份、氮化硅0.75重量份、氮化硼1.5重量份、增稠剂0.3重量份、消泡剂0.15重量份、防沉剂0.75重量份、去离子水17.5重量份、三聚磷酸钠0.15重量份。
对比例2石墨烯与磷酸二氢铝复合时没有加入木质素磺酸钠,其他制备条件与实施例6相同,制得的石墨烯散热涂料,其分散性测试的涂料静置情况、散热效果测试的铝板温度情况如表1及图1所示。
对比例3
(1)先将石墨烯、木质素磺酸钠加入磷酸二氢铝溶液中,在球磨机中研磨分散,然后烘干,再加热进行高温处理,最后冷却研磨,出料,得到预处理石墨烯;磷酸二氢铝溶液的质量浓度为17.5%;烘干的温度为250℃,时间为30min;高温处理的过程为,先在450℃下处理15min,然后升温到950℃处理8min;
各原料配比为,按重量份计,石墨烯10重量份、木质素磺酸钠0.15重量份、磷酸二氢铝溶液55重量份;
(2)先将步骤(1)得到预处理石墨烯、分散剂、硅酸钠溶液加入篮式砂磨机中,然后研磨分散,出料,得到预分散浆料;分散剂为聚羧酸盐;硅酸钠溶液为40波美度;研磨分散的转速为300r/min;
各原料配比为,按重量份计,预处理石墨烯12.5重量份、分散剂0.75重量份、硅酸钠溶液85重量份;
(3)先将步骤(2)得到的预分散浆料、α-氧化铝、氮化硅、氮化硼、增稠剂、消泡剂、防沉剂、去离子水、三聚磷酸钠加入球磨机,然后球磨分散均匀,出料,罐装,即得水性环保石墨烯散热涂料;α-氧化铝的平均粒径为8μm;氮化硅的平均粒径为18μm;氮化硼的平均粒径为8μm;增稠剂为壳聚糖;消泡剂为硅油;防沉剂为钙基膨润土;
各原料配比为,按重量份计,预分散浆料100重量份、α-氧化铝2重量份、氮化硅0.75重量份、氮化硼1.5重量份、增稠剂0.3重量份、消泡剂0.15重量份、防沉剂0.75重量份、去离子水17.5重量份、三聚磷酸钠0.15重量份。
对比例3涂料中没有加入铜粉,其他制备条件与实施例6相同,制得的石墨烯散热涂料,其分散性测试的涂料静置情况、散热效果测试的铝板温度情况如表1所示。
对比例4
(1)先将石墨烯、木质素磺酸钠加入磷酸二氢铝溶液中,在球磨机中研磨分散,然后烘干,再加热进行高温处理,最后冷却研磨,出料,得到预处理石墨烯;磷酸二氢铝溶液的质量浓度为17.5%;烘干的温度为250℃,时间为30min;高温处理的过程为,先在450℃下处理15min,然后升温到950℃处理8min;
各原料配比为,按重量份计,石墨烯10重量份、木质素磺酸钠0.15重量份、磷酸二氢铝溶液55重量份;
(2)先将步骤(1)得到预处理石墨烯、分散剂、铜粉、硅酸钠溶液加入篮式砂磨机中,然后研磨分散,出料,得到预分散浆料;分散剂为聚羧酸盐;硅酸钠溶液为40波美度;研磨分散的转速为300r/min;
各原料配比为,按重量份计,预处理石墨烯12.5重量份、分散剂0.75重量份、铜粉4重量份、硅酸钠溶液85重量份;
(3)先将步骤(2)得到的预分散浆料、增稠剂、消泡剂、防沉剂、去离子水、三聚磷酸钠加入球磨机,然后球磨分散均匀,出料,罐装,即得水性环保石墨烯散热涂料;增稠剂为壳聚糖;消泡剂为硅油;防沉剂为钙基膨润土;
各原料配比为,按重量份计,预分散浆料100重量份、增稠剂0.3重量份、消泡剂0.15重量份、防沉剂0.75重量份、去离子水17.5重量份、三聚磷酸钠0.15重量份。
对比例4的涂料中没有加入α-氧化铝、氮化硅、氮化硼,其他制备条件与实施例6相同,制得的石墨烯散热涂料,其分散性测试的涂料静置情况、散热效果测试的铝板温度情况如表1所示。
上述性能指标的测试方法为:
(1)石墨烯散热涂料分散性测试:
将实施例1~6、对比例1~2得到的石墨烯散热涂料静置在样品瓶24h,观察沉降分层情况,结果如表1及图1所示;
(2)石墨烯散热涂料散热效果测试:
将实施例1~6、对比例1~4的涂料刮涂在厚度为3mm的铝板上,涂敷厚度为50μm,自然干燥24h作为测试样,然后将样品在烘箱中恒温至180℃,再将铝板移出,测试不同时间点(10s、20s、30s)的铝板温度变化,结果如表1所示。
由表1可知:
(1)本发明实施例1~6制得的石墨烯散热涂料在分散性测试中无明显沉降(实施例6的沉降情况如图1中a);对比例1的石墨烯散热涂料沉降明显,沉降后再次搅拌,沉降速度更快(对比例1的沉降情况如图1中b);对比例2的石墨烯散热涂料的静置后有一定的沉降,搅拌后仍会沉降(对比例1的沉降情况如图1中c)。
(2)本发明实施例1~6制得的石墨烯散热涂料在分散性测试中,不同时间点的铝板温度明显比对比例1~4的温度低,温度变化大,表现出更加优异的散热效果。
上述结果的原因为:实施例的石墨烯散热涂料中,石墨烯经木质素磺酸钠、磷酸二氢铝预处理形成保护层,得到的预处理石墨烯与硅酸钠溶液亲和性好,易于均匀分散在硅酸钠溶液中,克服了石墨烯离析沉降问题,同时聚羧酸盐分散剂可以进一步改善石墨烯的分散性,有效阻止石墨烯的团聚、沉降;另外,预处理的石墨烯与铜粉、α-氧化铝、氮化硅、氮化硼协同发挥作用,涂料通过硅酸钠粘接固化成膜,形成热传导、热辐射协同的散热网络,获得的涂料散热性能和耐高温性优异。对比例1的石墨烯没有与磷酸二氢铝复合,而是直接使用石墨烯,由于缺少表面改性处理,石墨烯与硅酸钠溶液的分散性较差,研磨配制的散热涂料极易沉降。对比例2的石墨烯与磷酸二氢铝复合时没有加入木质素磺酸钠,石墨烯的分散有限,石墨烯与磷酸二氢铝结合均匀受限,得到的预处理石墨烯表面包覆瓷质均匀性较差,硅酸钠溶液的分散性有限,研磨配制的散热涂料存在一定的沉降。对比例3的散热涂料中没有加入铜粉,仅仅依靠石墨烯的传导和热辐射,散热性能有限。对比例4的散热涂料中没有加入氮化硅粉、氮化硼,由于缺少高温热传导的协同作用,散热性能有限。上述测试过程有效验证了单纯的石墨烯分散涂料,存在团聚,影响散热效果,而通过复合其他易分散的α-氧化铝、氮化硅、氮化硼等,协同散热,使石墨烯的界面增加,防止过多的石墨烯团聚,解决石墨烯用于无机涂料体系容易分离沉降的问题。
表1:
本文用于企业家、创业者技术爱好者查询,结果仅供参考。