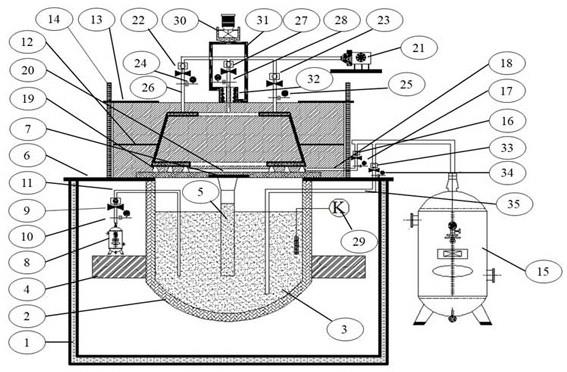
1.本发明属于有色金属铸造工艺装备与成型技术领域,具体涉及一种制备大型高强韧铝合金铸件的真空充型置顶激冷加压凝固装置及方法。
背景技术:
2.铝合金密度低、比强/刚度高、耐蚀性好、塑性好、加工性能优异,且具有良好的焊接性能,优良的导电性、导热性,在军工装备领域得到了广泛的应用。铝合金按照加工工艺主要可分为变形铝合金与铸造铝合金两类,其中铸造铝合金因具有良好的工艺流动性能与中等载荷承载能力,在导弹壳体、载油舱壳体、发动机附件机匣、发动机油路管道、汽车发动机缸体、汽车发动机缸盖等产品制造上得到了广泛的应用。
3.铸造铝合金传统的铸造成型工艺主要是重力浇铸,通过在浇铸系统布置补缩冒口、保温冒口来提高合金熔体的补缩效果,减少针孔、疏松与偏析等冶金缺陷的数量与严重程度。重力浇铸的充型能力主要取决于重力,因此合金熔体自直浇道充型至横浇道与内浇口,合金熔体不断冲刷铸型及铸型表层的涂料,严重时甚至在直浇道浇注时产生卷气涡流,在铸件内部形成严重的气孔与夹杂物缺陷,因此重力浇铸通常应用于民用铝合金铸件制备;军工装备大型铝合金铸件目前多选用低压充型浇铸工艺。低压充型浇铸工艺是使坩埚内的金属溶液在气体压力作用下,沿升液管自下而上平稳地进入铸型中,并保持压力直至铸件完全凝固为止,从而获得铸件。低压充型整体过程比较平稳,可有效减少氧化夹杂物与夹渣的形成,同时简化了铸件的浇注系统并节省了冒口,低压充型结束后尚未凝固的金属溶液可回流至坩埚内,金属溶液消耗少,铸件工艺出品率高。
技术实现要素:
4.研究发现,军工装备用大型高强韧铝合金铸件通常选用zl114a铝硅铸造合金或zl205a铝铜铸造合金,然而,zl114a铝硅铸造合金或zl205a铝铜铸造合金在采用低压充型浇铸工艺制备时,往往存在以下问题:(1)zl205a合金熔体静置处理后,在低压铸造机上再组装铸型与型芯,型芯装配时间长,zl205a合金熔体尚未浇铸时在坩埚内即产生了一定程度的比重偏析,导致低压充型浇铸后,铸件不同充型时长部位合金熔体的cu等高比重元素分布富集,极易产生偏析冶金缺陷。(2)铸型与型芯在低压铸造机上进行装配时,不可避免地将产生轻微碰撞摩擦,导致在铸型型腔内产生了一定数量的砂砾碎屑与涂料剥落碎屑,在低压充型时被合金熔体包裹在铸件内部,形成夹杂物缺陷,降低铸件的强度与塑韧性,严重恶化了合金材料的疲劳性能。(3)合金熔体经精炼除气与静置处理后,合金熔体内部的氢含量控制在了一定的成分范围内,当铸型与型芯组装装配时间偏长时,坩埚内的合金熔体会随着停置时间的延长不断吸氢,导致合金熔体内部的液态氢含量不断上升,低压充型后在铸件内部产生针孔、气孔冶金缺陷,削弱了合金材料的机械强度与疲劳性能。(4)现有的低压充型设备仅考虑了合金熔体的充型过程,对合金熔体的凝固过程未作考虑,这也就导
致了现有多数大型铝合金铸件采用低压充型浇铸工艺时,虽然有效提高了铸件的内在冶金质量,但浇铸所得的铸件经t5/t6热处理后,力学性能并未有明显的提升。总而言之,现有的低压充型设备与成型工艺很难同步实现军工装备大型铝合金铸件的高冶金质量、高力学性能与高尺寸精度同步精密成形制造。
5.为了解决现有的低压充型设备与工艺在制造大型高强韧铝合金铸件时,存在的炉内比重偏析程度高、铸型型腔微杂物碎屑多、铸件成形尺寸精度差、铸件内在冶金质量差、铸态组织粗大、铸件力学性能偏低及疲劳性能不高等问题,本发明提出了一种制备大型铝合金铸件的真空充型置顶激冷加压凝固装置及方法,所述装置集真空充型、置顶激冷、加压凝固于一体。与现有的低压充型装置与成型工艺相比,本发明的装置增加了熔体搅拌单元,在熔体浇铸前对熔体进行轻微搅拌可提高合金熔体的均匀化程度,避免了炉内比重偏析的出现;本发明的装置增加了熔体精炼净化处理单元,进一步降低了合金熔体浇铸前的液态氢含量,可有效减少疏松、针孔冶金缺陷的出现;本发明的装置增加了型腔真空悬浮净化处理单元,提高了铸型型腔内的纯净化程度,避免了夹杂物与夹渣冶金缺陷的出现,可显著提高铸件的疲劳性能;本发明的装置增加了熔体置顶激冷单元,显著细化了铸态晶粒组织,可在提高合金材料强度的同时显著提高合金材料的塑韧性;本发明的装置增加了熔体加压凝固单元,可进一步提高大型薄壁复杂结构铝合金铸件的致密度,进一步提高其内在冶金质量,可用于军工装备大型薄壁复杂结构铝合金铸件的精密铸造成型。
6.本发明的技术方案如下所述:一种制备大型铝合金铸件的真空充型置顶激冷加压凝固装置,所述装置包括熔体搅拌和升液单元、熔体精炼净化处理单元、铸型单元、型腔真空悬浮净化处理单元、熔体真空充型单元、熔体置顶激冷单元、熔体加压凝固单元;所述熔体搅拌和升液单元包括炉衬、坩埚、电磁搅拌装置、升液管、炉衬盖板、升液管闸板;所述坩埚和电磁搅拌装置置于炉衬内,所述炉衬盖板置于炉衬顶部,所述坩埚内盛装合金熔体;所述升液管的一端置于合金熔体中,所述升液管的另一端通过炉衬盖板与升液管闸板连接;所述熔体精炼净化处理单元包括精炼气体储气罐、精炼气体电磁阀、精炼气体流量计、精炼气体输气管;所述精炼气体储气罐、精炼气体电磁阀和精炼气体流量计置于炉衬内,所述精炼气体输气管置于合金熔体中;且所述精炼气体输气管通过精炼气体电磁阀和精炼气体流量计与精炼气体储气罐相连;所述铸型单元包括上铸型、下铸型、砂芯、上铸型型腔、下铸型型腔、铸型封腔条、铸型压板、铸型压板紧固杆、内浇口型腔、横浇道型腔;所述下铸型设置在炉衬盖板上方,所述上铸型设置在下铸型上方,所述上铸型和下铸型通过铸型封腔条密封;所述上铸型和下铸型与炉衬盖板通过铸型压板、铸型压板紧固杆进行螺接紧固;所述砂芯内置于下铸型和上铸型,所述砂芯与下铸型之间存在的空腔结构形成下铸型型腔,所述砂芯与上铸型之间存在的空腔结构形成上铸型型腔,所述下铸型型腔与上铸型型腔连通;所述下铸型内设置内浇口型腔和横浇道型腔;所述横浇道型腔通过内浇口型腔与下铸型型腔相连,且所述横浇道型腔通过升液管闸板与升液管相连;所述型腔真空悬浮净化单元包括:高压储气罐、型腔净化气体电磁阀、型腔净化气体流量计、型腔净化气体输气管、电控伺服真空泵、铸型左侧真空电磁阀、铸型右侧真空电
磁阀、铸型左侧真空流量计、铸型右侧真空流量计和铸型真空抽气管路;所述真空充型单元包括:铸型置顶真空电磁阀、铸型置顶真空流量计和熔体k型测温热电偶;所述高压储气罐通过管路一与型腔净化气体电磁阀、型腔净化气体流量计和型腔净化气体输气管相连;所述型腔净化气体输气管和内浇口型腔连通;所述电控伺服真空泵和铸型真空抽气管路之间设置三条并联支路,一条并联支路上设置铸型左侧真空电磁阀和铸型左侧真空流量计,另一条并联支路上设置铸型右侧真空电磁阀和铸型右侧真空流量计,还一条支路上设置铸型置顶真空电磁阀和铸型置顶真空流量计,所述铸型真空抽气管路与上铸型型腔连通;所述熔体k型测温热电偶置于合金熔体中;所述熔体置顶激冷单元包括置顶激冷水泵、置顶激冷水流管路和置顶水路冷凝器:所述置顶水路冷凝器位于上铸型的正上方,所述置顶水路冷凝器通过置顶激冷水流管路与置顶激冷水泵相连;所述熔体加压凝固单元包括高压加压气体电磁阀、高压加压气体流量计、高压加压气体输气管;高压储气罐通过管路二与高压加压气体电磁阀、高压加压气体流量计和高压加压气体输气管相连;所述高压加压气体输气管置于合金熔体内。
7.本发明还提供一种制备铝合金铸件的方法,所述方法是基于上述的装置。
8.根据本发明的实施方式,所述方法包括如下步骤:(a)熔体搅拌均匀处理:将合金熔体注入坩埚内,锁闭升液管闸板,启动电磁搅拌装置对合金熔体进行电磁搅拌;(b)熔体精炼净化处理:合金熔体经电磁搅拌处理后,打开升液管闸板,开启精炼气体电磁阀与精炼气体流量计,精炼气体储气罐中的精炼气体通过精炼气体输气管持续通入合金熔体内对合金熔体进行精炼净化处理;(c)型腔真空悬浮净化:锁闭升液管闸板,开启型腔净化气体电磁阀与型腔净化气体流量计,高压储气罐中的高压气体通过型腔净化气体输气管通入铸型单元内部,经由内浇口型腔与横浇道型腔注入下铸型型腔和上铸型型腔内部,沿下铸型型腔底部自下而上对型腔进行吹气净化;启动电控伺服真空泵,开启铸型左侧真空电磁阀、铸型右侧真空电磁阀、铸型左侧真空流量计与铸型右侧真空流量计,通过铸型真空抽气管路将沿下铸型型腔底部被高压气体吹起,呈悬浮状态的微砂砾、涂料碎屑等夹杂物抽离至下铸型型腔和上铸型型腔外部;(d)熔体真空充型:通过熔体k型测温热电偶调整合金熔体的浇铸温度,开启升液管闸板,锁闭铸型左侧真空电磁阀与铸型右侧真空电磁阀,开启铸型置顶真空电磁阀、铸型置顶真空流量计;调节电控伺服真空泵的真空度,合金熔体沿升液管、横浇道型腔、内浇口型腔实现下铸型型腔和上铸型型腔的真空充型;(e)熔体置顶激冷:当合金熔体完成真空充型填充至上铸型型腔顶部时,启动置顶激冷水泵,冷却水沿置顶激冷水流管路流通至置顶水路冷凝器处,对合金熔体实现激冷处理;(f)熔体加压凝固:开启高压加压气体电磁阀与高压加压气体流量计,高压储气罐内的高压气体通过高压加压气体输气管将高压气体输送至坩埚内部,使合金熔体沿升液管对下铸型型腔和上铸型型腔内的合金熔体实施持续的高压,使其在加压条件下进行凝固。
9.本发明还提供一种上述方法制备得到的铝合金铸件。
10.根据本发明的实施方式,所述铝合金铸件为大型高强韧铝合金铸件。
11.有益效果:本发明提出了一种制备大型铝合金铸件的真空充型置顶激冷加压凝固装置及方法。与传统的低压充型浇铸工艺相比,在合金熔体浇铸前对合金熔体进行了搅拌均匀处理与精炼净化处理,避免了炉内比重偏析,同时提高了合金熔体的纯净度,降低了合金熔体的液态氢含量;结合型腔真空悬浮净化与熔体真空充型浇铸成形工艺,提高了铸型型腔的内在洁净度,减少了夹渣冶金缺陷,显著提高了铝合金铸件的疲劳性能;通过熔体置顶激冷与熔体加压凝固,进一步提高了铸件的致密度,减少了针孔、疏松冶金缺陷的数量,可实现大型复杂薄壁结构铝合金铸件的高冶金质量、高力学性能与高尺寸精度精密铸造成形,实现军工装备与新能源汽车大型复杂结构精密铝合金铸件高冶金质量短周期低成本制造,经济效益显著。
附图说明
12.图1是本发明一个优选方案所述的装置的结构示意图;附图标记:1为炉衬,2为坩埚,3为合金熔体,4为电磁搅拌装置,5为升液管,6为炉衬盖板,7为升液管闸板,8为精炼气体储气罐,9为精炼气体电磁阀,10为精炼气体流量计,11为精炼气体输气管,12为铸型封腔条,13为铸型压板,14为铸型压板紧固杆,15为高压气体储气罐,16为型腔净化气体电磁阀,17为型腔净化气体流量计,18为型腔净化气体输气管,19为内浇口型腔,20为横浇道型腔,21为电控伺服真空泵,22为铸型左侧真空电磁阀,23为铸型右侧真空电磁阀,24为铸型左侧真空流量计,25为铸型右侧真空流量计,26为铸型真空抽气管路,27为铸型置顶真空电磁阀,28为铸型置顶真空流量计,29为熔体k型测温热电偶,30为置顶激冷水泵,31为置顶激冷水流管路,32为置顶水路冷凝器,33为高压加压气体电磁阀,34为高压加压气体流量计,35为高压加压气体输气管。
13.图2是实施例2制备的过渡段金属壳体铸件的结构意图。
14.图3是实施例3制备的尾段金属壳体铸件的结构示意图。
具体实施方式
15.《制备大型铝合金铸件的真空充型置顶激冷加压凝固装置》如前所述,本发明提供一种制备大型铝合金铸件的真空充型置顶激冷加压凝固装置,所述装置包括熔体搅拌和升液单元、熔体精炼净化处理单元、铸型单元、型腔真空悬浮净化处理单元、熔体真空充型单元、熔体置顶激冷单元、熔体加压凝固单元;所述熔体搅拌和升液单元包括炉衬1、坩埚2、电磁搅拌装置4、升液管5、炉衬盖板6、升液管闸板7;所述坩埚2和电磁搅拌装置4置于炉衬1内,所述炉衬盖板6置于炉衬1顶部,所述坩埚2内盛装合金熔体3;所述升液管5的一端置于合金熔体3中,所述升液管5的另一端通过炉衬盖板6与升液管闸板7连接;所述熔体精炼净化处理单元包括精炼气体储气罐8、精炼气体电磁阀9、精炼气体流量计10、精炼气体输气管11;所述精炼气体储气罐8、精炼气体电磁阀9和精炼气体流量计10置于炉衬1内,所述精炼气体输气管11置于合金熔体3中;且所述精炼气体输气管11通过
精炼气体电磁阀9和精炼气体流量计10与精炼气体储气罐8相连;所述铸型单元包括上铸型、下铸型、砂芯、上铸型型腔、下铸型型腔、铸型封腔条12、铸型压板13、铸型压板紧固杆14、内浇口型腔19、横浇道型腔20;所述下铸型设置在炉衬盖板6上方,所述上铸型设置在下铸型上方,所述上铸型和下铸型通过铸型封腔条12密封;所述上铸型和下铸型与炉衬盖板6通过铸型压板13、铸型压板紧固杆14进行螺接紧固;所述砂芯内置于下铸型和上铸型,所述砂芯与下铸型之间存在的空腔结构形成下铸型型腔,所述砂芯与上铸型之间存在的空腔结构形成上铸型型腔,所述下铸型型腔与上铸型型腔连通;所述下铸型内设置内浇口型腔19和横浇道型腔20;所述横浇道型腔20通过内浇口型腔19与下铸型型腔相连,且所述横浇道型腔20通过升液管闸板7与升液管5相连;所述型腔真空悬浮净化单元包括:高压储气罐15、型腔净化气体电磁阀16、型腔净化气体流量计17、型腔净化气体输气管18、电控伺服真空泵21、铸型左侧真空电磁阀22、铸型右侧真空电磁阀23、铸型左侧真空流量计24、铸型右侧真空流量计25和铸型真空抽气管路26;所述真空充型单元包括:铸型置顶真空电磁阀27、铸型置顶真空流量计28和熔体k型测温热电偶29;所述高压储气罐15通过管路一与型腔净化气体电磁阀16、型腔净化气体流量计17和型腔净化气体输气管18相连;所述型腔净化气体输气管18和内浇口型腔19连通;所述电控伺服真空泵21和铸型真空抽气管路26之间设置三条并联支路,一条并联支路上设置铸型左侧真空电磁阀22和铸型左侧真空流量计24,另一条并联支路上设置铸型右侧真空电磁阀23和铸型右侧真空流量计25,还一条支路上设置铸型置顶真空电磁阀27和铸型置顶真空流量计28,所述铸型真空抽气管路26与上铸型型腔连通;所述熔体k型测温热电偶29置于合金熔体3中;所述熔体置顶激冷单元包括置顶激冷水泵30、置顶激冷水流管路31和置顶水路冷凝器32:所述置顶水路冷凝器32位于上铸型的正上方,所述置顶水路冷凝器32通过置顶激冷水流管路31与置顶激冷水泵30相连;所述熔体加压凝固单元包括高压加压气体电磁阀33、高压加压气体流量计34、高压加压气体输气管35;高压储气罐15通过管路二与高压加压气体电磁阀33、高压加压气体流量计34和高压加压气体输气管35相连;所述高压加压气体输气管35置于合金熔体3内。
16.根据本发明的实施方式,所述坩埚2置于炉衬1正中间,且所述坩埚2的开口与所述炉衬1的开口齐平。
17.根据本发明的实施方式,所述炉衬盖板6置于炉衬1顶部用于封装所述炉衬1和坩埚2。
18.根据本发明的实施方式,所述升液管5的另一端通过炉衬盖板6的正中间部位与升液管闸板7连接。
19.根据本发明的实施方式,所述熔体搅拌和升液单元用于搅拌合金熔体3,并通过升液管闸板7的开启和锁闭控制合金熔体注入铸造单元。
20.根据本发明的实施方式,通过启动电磁搅拌装置4对合金熔体3进行电磁搅拌。
21.根据本发明的实施方式,所述熔体精炼净化处理单元用于对合金熔体3进行精炼净化处理。
22.根据本发明的实施方式,合金熔体3经电磁搅拌处理后,打开升液管闸板7,开启精炼气体电磁阀9与精炼气体流量计10,精炼气体储气罐8中的精炼气体通过精炼气体输气管11持续通入合金熔体3内对合金熔体3进行精炼净化处理。
23.根据本发明的实施方式,所述铸型单元用于铸件的铸造成型,优选地,所述下铸型内的下铸型型腔和所述上铸型内的上铸型型腔连通,用于铸造成铸件。
24.根据本发明的实施方式,所述型腔真空悬浮净化处理单元用于对上铸型型腔、下铸型型腔、内浇口型腔19和横浇道型腔20进行真空悬浮净化处理。
25.根据本发明的实施方式,锁闭升液管闸板7,开启型腔净化气体电磁阀16与型腔净化气体流量计17,高压储气罐15中的高压气体通过型腔净化气体输气管18通入铸型单元内部,经由内浇口型腔19与横浇道型腔20注入下铸型型腔和上铸型型腔内部,并沿下铸型型腔底部自下而上对型腔进行吹气净化;启动电控伺服真空泵21,开启铸型左侧真空电磁阀22、铸型右侧真空电磁阀23、铸型左侧真空流量计24与铸型右侧真空流量计25,通过铸型真空抽气管路26将沿下铸型型腔底部被高压气体吹起,呈悬浮状态的微砂砾、涂料碎屑等夹杂物抽离至下铸型型腔和上铸型型腔外部。
26.根据本发明的实施方式,所述熔体真空充型单元用于对上铸型型腔和下铸型型腔进行熔体填充。
27.根据本发明的实施方式,通过熔体k型测温热电偶29调整合金熔体3的浇铸温度,开启升液管闸板7,锁闭铸型左侧真空电磁阀22与铸型右侧真空电磁阀23,开启铸型置顶真空电磁阀27、铸型置顶真空流量计28;调节电控伺服真空泵21的真空度,合金熔体3沿升液管5、横浇道型腔20、内浇口型腔19实现下铸型型腔和上铸型型腔的真空充型。
28.根据本发明的实施方式,所述熔体置顶激冷单元用于对合金熔体进行激冷处理。
29.根据本发明的实施方式,当合金熔体3完成真空充型填充至上铸型型腔顶部时,启动置顶激冷水泵30,冷却水沿置顶激冷水流管路31流通至置顶水路冷凝器32处,对合金熔体实现激冷处理。
30.根据本发明的实施方式,所述熔体加压凝固单元用于对下铸型型腔和上铸型型腔内的合金熔体实施持续的高压,使其在加压条件下进行凝固。
31.根据本发明的实施方式,开启高压加压气体电磁阀33与高压加压气体流量计34,高压储气罐15内的高压气体通过高压加压气体输气管35将高压气体输送至坩埚2内部,使合金熔体3沿升液管5对下铸型型腔和上铸型型腔内的合金熔体实施持续的高压,使其在加压条件下进行凝固。
32.《制备铝合金铸件的方法》如前所述,本发明还提供一种制备铝合金铸件的方法,所述方法是基于上述的装置。
33.根据本发明的实施方式,所述方法包括如下步骤:(a)熔体搅拌均匀处理:将合金熔体3注入坩埚2内,锁闭升液管闸板7,启动电磁搅拌装置4对合金熔体3进行电磁搅拌;(b)熔体精炼净化处理:合金熔体3经电磁搅拌处理后,打开升液管闸板7,开启精炼气体电磁阀9与精炼气体流量计10,精炼气体储气罐8中的精炼气体通过精炼气体输气管11持续通入合金熔体3内对合金熔体3进行精炼净化处理;
(c)型腔真空悬浮净化:锁闭升液管闸板7,开启型腔净化气体电磁阀16与型腔净化气体流量计17,高压储气罐15中的高压气体通过型腔净化气体输气管18通入铸型单元内部,经由内浇口型腔19与横浇道型腔20注入下铸型型腔和上铸型型腔内部,沿下铸型型腔底部自下而上对型腔进行吹气净化;启动电控伺服真空泵21,开启铸型左侧真空电磁阀22、铸型右侧真空电磁阀23、铸型左侧真空流量计24与铸型右侧真空流量计25,通过铸型真空抽气管路26将沿下铸型型腔底部被高压气体吹起,呈悬浮状态的微砂砾、涂料碎屑等夹杂物抽离至下铸型型腔和上铸型型腔外部;(d)熔体真空充型:通过熔体k型测温热电偶29调整合金熔体3的浇铸温度,开启升液管闸板7,锁闭铸型左侧真空电磁阀22与铸型右侧真空电磁阀23,开启铸型置顶真空电磁阀27、铸型置顶真空流量计28;调节电控伺服真空泵21的真空度,合金熔体3沿升液管5、横浇道型腔20、内浇口型腔19实现下铸型型腔和上铸型型腔的真空充型;(e)熔体置顶激冷:当合金熔体3完成真空充型填充至上铸型型腔顶部时,启动置顶激冷水泵30,冷却水沿置顶激冷水流管路31流通至置顶水路冷凝器32处,对合金熔体实现激冷处理;(f)熔体加压凝固:开启高压加压气体电磁阀33与高压加压气体流量计34,高压储气罐15内的高压气体通过高压加压气体输气管35将高压气体输送至坩埚2内部,使合金熔体3沿升液管5对下铸型型腔和上铸型型腔内的合金熔体实施持续的高压,使其在加压条件下进行凝固。
34.根据本发明的实施方式,步骤(a)中,电磁搅拌磁感振动频率为60hz~100hz,磁场中心磁感应强度为40mt~100mt,搅拌转速为400r/min~800r/min,搅拌时间为10min~20min。
35.根据本发明的实施方式,步骤(b)中,精炼气体为混合气体,包含cl2、n2与ar,其质量比为cl220%~25%,n230%~35%,余量为ar;精炼净化时间为15min~25min,精炼气体流量为0.16l
·
min-1
~0.24l
·
min-1
,精炼净化后静置处理5min~10min。
36.根据本发明的实施方式,步骤(c)中,高压储气罐15中的气体为无水干燥压缩空气,型腔净化气体输气管18中的气体流量为0.2l
·
min-1
~0.5l
·
min-1
,铸型左侧真空流量计24与铸型右侧真空流量计25中的气体流量分别为0.4l
·
min-1
~0.8l
·
min-1
,电控伺服真空泵21中的真空度为0.02mpa~0.04mpa。
37.根据本发明的实施方式,步骤(d)中,合金熔体3的浇铸温度为690℃~720℃,铸型置顶真空流量计28中的气体流量为0.6l
·
min-1
~1.0l
·
min-1
,电控伺服真空泵21中的真空度为10-4
pa~10-2
pa。
38.根据本发明的实施方式,步骤(e)中,置顶激冷水流管路31中的冷却介质为去离子水,水温为10℃~20℃,水流量为0.25l
·
min-1
~0.50l
·
min-1
,置顶激冷水泵30与置顶水路冷凝器32工作时间为15min~30min。
39.根据本发明的实施方式,步骤(f)中,高压加压气体流量计34中的气体流量为1.2l
·
min-1
~1.6l
·
min-1
,高压加压气体输气管35沿升液管5作用于合金熔体3的气体压力为0.6mpa~1.0mpa。
40.根据本发明的实施方式,所述制备方法包括如下步骤:(a)熔体搅拌均匀处理:将坩埚2放置于炉衬1正上方,随后将电磁搅拌装置4、精炼气体储气罐8、精炼气体电磁阀9、精炼气体流量计10放置于炉衬1之内;将炉衬盖板6放置于
炉衬1上方,随后将合金熔体3由其他熔炼设备转运至坩埚2内,在熔体内放置熔体k型测温热电偶29、精炼气体输气管11与高压加压气体输气管35;在炉衬盖板6中间位置放置升液管5与升液管闸板7,锁闭升液管闸板7,启动电磁搅拌装置4对合金熔体3进行电磁搅拌;(b)置顶激冷装置组装:在炉衬盖板6上方放置上、下铸型,上下铸型间隙通过放置铸型封腔条12进行密封处理,上、下铸型与炉衬盖板6通过铸型压板13、铸型压板紧固杆15进行螺接紧固;下铸型包含有型腔净化气体输气管18、内浇口型腔19与横浇道型腔20,上铸型包含有铸型真空抽气管路26;置顶水路冷凝器32位于铸型正上方,通过置顶激冷水流管路31与其正上方的置顶激冷水泵30相连通;(c)熔体精炼净化处理:合金熔体3经电磁搅拌处理后,打开升液管闸板7,开启精炼气体电磁阀9与精炼气体流量计10,精炼气体储气罐8中的精炼气体通过精炼气体输气管11持续通入合金熔体3内对合金熔体3进行精炼净化处理;(d)型腔真空悬浮净化:锁闭升液管闸板7,开启型腔净化气体电磁阀16与型腔净化气体流量计17,高压储气罐15中的高压气体通过型腔净化气体输气管18通入下铸型型腔和上铸型型腔内部,经由内浇口型腔19与横浇道型腔20注入下铸型型腔和上铸型型腔内部,沿铸型铸型底部自下而上对型腔进行吹气净化;启动电控伺服真空泵21,开启铸型左侧真空电磁阀22、铸型右侧真空电磁阀23、铸型左侧真空流量计24与铸型右侧真空流量计25,通过铸型真空抽气管路26将沿下铸型型腔和上铸型型腔底部被高压气体吹起,呈悬浮状态的微砂砾、涂料碎屑等夹杂物抽离至下铸型型腔和上铸型型腔外部;(e)熔体真空充型:结合熔体k型测温热电偶29调整合金熔体3至规定的浇铸温度,开启升液管闸板7,锁闭铸型左侧真空电磁阀22与铸型右侧真空电磁阀23,开启铸型置顶真空电磁阀27、铸型置顶真空流量计28;调节电控伺服真空泵21的真空度,合金熔体3沿升液管5、内浇口型腔19与横浇道型腔20实现下铸型型腔和上铸型型腔的真空充型;(f)熔体置顶激冷:当合金熔体3完成真空充型填充至下铸型型腔和上铸型型腔顶部时,启动置顶激冷水泵30,冷却水沿置顶激冷水流管路31源源不断流通至置顶水路冷凝器32处,对合金熔体实现激冷处理;(g)熔体加压凝固:开启高压加压气体电磁阀33与高压加压气体流量计34,高压储气罐15内的高压气体通过高压加压气体输气管35将高压气体输送至坩埚2内部,作用于合金熔体3沿升液管5对下铸型型腔和上铸型型腔内的合金熔体实施持续的高压加压凝固。
41.《铝合金铸件》如前所述,本发明还提供一种上述方法制备得到的铝合金铸件。
42.根据本发明的实施方式,所述铝合金铸件为大型高强韧铝合金铸件。
43.根据本发明的实施方式,所述铝合金铸件冶金质量可达qj3185a-2018
ꢀⅰ
类铸件标准,内腔尺寸可达hb 6103-2004之ct6级~ct8级,成形尺寸壁厚可达2.0mm~60.0mm,铸造工艺出品率达60%~80%,铸件固态氢含量≤0.12ppm。
44.根据本发明的实施方式,所述铝合金铸件为zl114a时,制备的zl114a大型高强韧铝合金铸件经t6热处理后本体平均抗拉强度≥360mpa,平均屈服强度≥300mpa,平均延伸率≥7.0%,平均布氏硬度≥110hbs。
45.根据本发明的实施方式,所述铝合金铸件为zl205a时,制备的zl205a大型高强韧铝合金铸件经t6热处理后本体平均抗拉强度≥500mpa,平均屈服强度≥380mpa,平均延伸
率≥10.0%,平均布氏硬度≥140hbs。
46.下文将结合具体实施例对本发明做更进一步的详细说明。应当理解,下列实施例仅为示例性地说明和解释本发明,而不应被解释为对本发明保护范围的限制。凡基于本发明上述内容所实现的技术均涵盖在本发明旨在保护的范围内。
47.下述实施例中所使用的实验方法如无特殊说明,均为常规方法;下述实施例中所用的试剂、材料等,如无特殊说明,均可从商业途径得到。
48.实施例1:本实施例提供一种制备大型铝合金铸件的真空充型置顶激冷加压凝固装置,所述装置包括熔体搅拌和升液单元、熔体精炼净化处理单元、铸型单元、型腔真空悬浮净化处理单元、熔体真空充型单元、熔体置顶激冷单元、熔体加压凝固单元;所述熔体搅拌和升液单元包括炉衬1、坩埚2、电磁搅拌装置4、升液管5、炉衬盖板6、升液管闸板7;所述坩埚2和电磁搅拌装置4置于炉衬1内,所述炉衬盖板6置于炉衬1顶部,所述坩埚2内盛装合金熔体3;所述升液管5的一端置于合金熔体3中,所述升液管5的另一端通过炉衬盖板6与升液管闸板7连接;所述熔体精炼净化处理单元包括精炼气体储气罐8、精炼气体电磁阀9、精炼气体流量计10、精炼气体输气管11;所述精炼气体储气罐8、精炼气体电磁阀9和精炼气体流量计10置于炉衬1内,所述精炼气体输气管11置于合金熔体3中;且所述精炼气体输气管11通过精炼气体电磁阀9和精炼气体流量计10与精炼气体储气罐8相连;所述铸型单元包括上铸型、下铸型、砂芯、上铸型型腔、下铸型型腔、铸型封腔条12、铸型压板13、铸型压板紧固杆14、内浇口型腔19、横浇道型腔20;所述下铸型设置在炉衬盖板6上方,所述上铸型设置在下铸型上方,所述上铸型和下铸型通过铸型封腔条12密封;所述上铸型和下铸型与炉衬盖板6通过铸型压板13、铸型压板紧固杆14进行螺接紧固;所述砂芯内置于下铸型和上铸型,所述砂芯与下铸型之间存在的空腔结构形成下铸型型腔,所述砂芯与上铸型之间存在的空腔结构形成上铸型型腔,所述下铸型型腔与上铸型型腔连通;所述下铸型内设置内浇口型腔19和横浇道型腔20;所述横浇道型腔20通过内浇口型腔19与下铸型型腔相连,且所述横浇道型腔20通过升液管闸板7与升液管5相连;所述型腔真空悬浮净化单元包括:高压储气罐15、型腔净化气体电磁阀16、型腔净化气体流量计17、型腔净化气体输气管18、电控伺服真空泵21、铸型左侧真空电磁阀22、铸型右侧真空电磁阀23、铸型左侧真空流量计24、铸型右侧真空流量计25和铸型真空抽气管路26;所述真空充型单元包括:铸型置顶真空电磁阀27、铸型置顶真空流量计28和熔体k型测温热电偶29;所述高压储气罐15通过管路一与型腔净化气体电磁阀16、型腔净化气体流量计17和型腔净化气体输气管18相连;所述型腔净化气体输气管18和内浇口型腔19连通;所述电控伺服真空泵21和铸型真空抽气管路26之间设置三条并联支路,一条并联支路上设置铸型左侧真空电磁阀22和铸型左侧真空流量计24,另一条并联支路上设置铸型右侧真空电磁阀23和铸型右侧真空流量计25,还一条支路上设置铸型置顶真空电磁阀27和铸型置顶真空流量计28,所述铸型真空抽气管路26与上铸型型腔连通;所述熔体k型测温热电偶29置于合金熔体3中;
所述熔体置顶激冷单元包括置顶激冷水泵30、置顶激冷水流管路31和置顶水路冷凝器32:所述置顶水路冷凝器32位于上铸型的正上方,所述置顶水路冷凝器32通过置顶激冷水流管路31与置顶激冷水泵30相连;所述熔体加压凝固单元包括高压加压气体电磁阀33、高压加压气体流量计34、高压加压气体输气管35;高压储气罐15通过管路二与高压加压气体电磁阀33、高压加压气体流量计34和高压加压气体输气管35相连;所述高压加压气体输气管35置于合金熔体3内。
49.本实施例还提供一种基于上述装置制备铝合金铸件的方法,所述方法包括如下步骤:(a)熔体搅拌均匀处理:将zl114a合金熔体3注入坩埚2内,锁闭升液管闸板7,启动电磁搅拌装置4对合金熔体3进行电磁搅拌;(b)熔体精炼净化处理:合金熔体3经电磁搅拌处理后,打开升液管闸板7,开启精炼气体电磁阀9与精炼气体流量计10,精炼气体储气罐8中的精炼气体通过精炼气体输气管11持续通入合金熔体3内对合金熔体3进行精炼净化处理;(c)型腔真空悬浮净化:锁闭升液管闸板7,开启型腔净化气体电磁阀16与型腔净化气体流量计17,高压储气罐15中的高压气体通过型腔净化气体输气管18通入铸型单元内部,经由内浇口型腔19与横浇道型腔20注入下铸型型腔和上铸型型腔内部,沿下铸型型腔底部自下而上对型腔进行吹气净化;启动电控伺服真空泵21,开启铸型左侧真空电磁阀22、铸型右侧真空电磁阀23、铸型左侧真空流量计24与铸型右侧真空流量计25,通过铸型真空抽气管路26将沿下铸型型腔底部被高压气体吹起,呈悬浮状态的微砂砾、涂料碎屑等夹杂物抽离至下铸型型腔和上铸型型腔外部;(d)熔体真空充型:通过熔体k型测温热电偶29调整合金熔体3的浇铸温度,开启升液管闸板7,锁闭铸型左侧真空电磁阀22与铸型右侧真空电磁阀23,开启铸型置顶真空电磁阀27、铸型置顶真空流量计28;调节电控伺服真空泵21的真空度,合金熔体3沿升液管5、横浇道型腔20、内浇口型腔19实现下铸型型腔和上铸型型腔的真空充型;(e)熔体置顶激冷:当合金熔体3完成真空充型填充至上铸型型腔顶部时,启动置顶激冷水泵30,冷却水沿置顶激冷水流管路31流通至置顶水路冷凝器32处,对合金熔体实现激冷处理;(f)熔体加压凝固:开启高压加压气体电磁阀33与高压加压气体流量计34,高压储气罐15内的高压气体通过高压加压气体输气管35将高压气体输送至坩埚2内部,使合金熔体3沿升液管5对下铸型型腔和上铸型型腔内的合金熔体实施持续的高压,使其在加压条件下进行凝固。
50.上述步骤中,所述电磁搅拌磁感振动频率为100hz,磁场中心磁感应强度为100mt,搅拌转速为800r/min,搅拌时间为20min。
51.所述精炼气体为混合气体,包含cl2、n2与ar,其质量比为cl225%,n235%,余量为ar;精炼净化时间为25min,精炼气体流量为0.24l
·
min-1
,精炼净化后静置处理10min。
52.所述高压储气罐15中的气体为无水干燥压缩空气,型腔净化气体输气管18中的气体流量为0.5l
·
min-1
,铸型左侧真空流量计24与铸型右侧真空流量计25中的气体流量分别为0.8l
·
min-1
,电控伺服真空泵21中的真空度为0.04mpa。
53.所述合金熔体3的浇铸温度为720℃,铸型置顶真空流量计28中的气体流量为
1.0l
·
min-1
,电控伺服真空泵21中的真空度为10-2
pa。
54.所述置顶激冷水流管路31中的冷却介质为去离子水,水温为20℃,水流量为0.50l
·
min-1
,置顶激冷水泵30与置顶水路冷凝器32工作时间为30min。
55.所述高压加压气体流量计34中的气体流量为1.6l
·
min-1
,高压加压气体输气管35沿升液管5作用于合金熔体3的气体压力为1.0mpa。
56.采用本实施例制备的大型高强韧铝合金铸件冶金质量可达qj3185a-2018
ꢀⅰ
类铸件标准,内腔尺寸可达hb 6103-2004之ct6级,最小成形尺寸壁厚可达2.0mm,铸造工艺出品率达80%,铸件固态氢含量为0.10ppm。
57.实施例2:其他操作同实施例1,区别仅在于铝合金铸件的制备工艺参数不同,具体如下所述:所述电磁搅拌磁感振动频率为60hz,磁场中心磁感应强度为50mt,搅拌转速为450r/min,搅拌时间为12min。
58.所述精炼气体为混合气体,包含cl2、n2与ar,其质量比为cl222%,n232%,余量为ar;精炼净化时间为18min,精炼气体流量为0.18l
·
min-1
,精炼净化后静置处理6min。
59.所述高压储气罐15中的气体为无水干燥压缩空气,型腔净化气体输气管18中的气体流量为0.3l
·
min-1
,铸型左侧真空流量计24与铸型右侧真空流量计25中的气体流量分别为0.5l
·
min-1
,电控伺服真空泵21中的真空度为0.03mpa。
60.所述合金熔体3的浇铸温度为700℃,铸型置顶真空流量计28中的气体流量为0.7l
·
min-1
,电控伺服真空泵21中的真空度为10-3
pa。
61.所述置顶激冷水流管路31中的冷却介质为去离子水,水温为12℃,水流量为0.30l
·
min-1
,置顶激冷水泵30与置顶水路冷凝器32工作时间为18min。
62.所述高压加压气体流量计34中的气体流量为1.3l
·
min-1
,高压加压气体输气管35沿升液管5作用于合金熔体3的气体压力为0.7mpa。
63.图2所示为实施例2制备的过渡段金属壳体铸件的结构示意图,采用实施例2制备的过渡段金属壳体铸件内在冶金质量达到了qj3185a-2018
ꢀⅰ
类铸件标准,内腔尺寸为hb 6103-2004之ct8级,整体成形尺寸壁厚为12.0mm,铸造工艺出品率为65%,铸件固态氢含量为0.11ppm,经t6热处理后本体平均抗拉强度为362mpa,平均屈服强度为305mpa,平均延伸率为7.5%,平均布氏硬度为112hbs。
64.实施例3:其他操作同实施例1,区别仅在于铝合金铸件的制备工艺参数不同,具体如下所述:所述电磁搅拌磁感振动频率为80hz,磁场中心磁感应强度为60mt,搅拌转速为600r/min,搅拌时间为16min。
65.所述精炼气体为混合气体,包含cl2、n2与ar,其质量比为cl224%,n234%,余量为ar;精炼净化时间为20min,精炼气体流量为0.22l
·
min-1
,精炼净化后静置处理8min。
66.所述高压储气罐15中的气体为无水干燥压缩空气,型腔净化气体输气管18中的气体流量为0.4l
·
min-1
,铸型左侧真空流量计24与铸型右侧真空流量计25中的气体流量分别为0.6l
·
min-1
,电控伺服真空泵21中的真空度为0.04mpa。
67.所述合金熔体3的浇铸温度为710℃,铸型置顶真空流量计28中的气体流量为0.9l
·
min-1
,电控伺服真空泵21中的真空度为10-4
pa。
68.所述置顶激冷水流管路31中的冷却介质为去离子水,水温为16℃,水流量为0.45l
·
min-1
,置顶激冷水泵30与置顶水路冷凝器32工作时间为25min。
69.所述高压加压气体流量计34中的气体流量为1.5l
·
min-1
,高压加压气体输气管35沿升液管5作用于合金熔体3的气体压力为0.8mpa。
70.图3所示为实施例3制备的尾段金属壳体铸件的结构示意图,采用实施例3制备的尾段金属壳体铸件内在冶金质量达到了qj3185a-2018
ꢀⅰ
类铸件标准,内腔尺寸为hb 6103-2004之ct8级,整体成形尺寸壁厚为18mm,铸造工艺出品率为70%,铸件固态氢含量为0.09ppm,经t6热处理后本体平均抗拉强度为368mpa,平均屈服强度为311mpa,平均延伸率为7.9%,平均布氏硬度为114hbs。
71.对比例1:其他操作同实施例3,区别仅在于所述铝合金铸件在铸造过程中,不开启电磁搅拌。
72.对比例2:其他操作同实施例3,区别仅在于所述铝合金铸件在铸造过程中,不进行熔体加压凝固,仅采用常规的低压充型浇铸,充型加压压力仅为0.08mpa。
73.对比例3:其他操作同实施例2,区别仅在于所述铝合金铸件在铸造过程中,不进行熔体置顶激冷处理,仅通过合金熔体与铸型进行激冷凝固。
74.表1 实施例2-3和对比例1-3制备的铝合金铸件的测试结果
实施工艺冶金质量内腔尺寸工艺出品率固态氢含量t6态抗拉强度t6态屈服强度t6态延伸率t6态布氏硬度实施例2qj3185a-2018ⅰ类hb6103-2004ct8级65%0.11ppm3623057.5112实施例3qj3185a-2018ⅰ类hb6103-2004ct8级70%0.09ppm3683117.9114对比例1qj3185a-2018ⅲ类hb6103-2004ct10级50%0.18ppm3322644.3102对比例2qj3185a-2018ⅱ类hb6103-2004ct9级55%0.19ppm3242533.898对比例3qj3185a-2018ⅱ类hb6103-2004ct10级42%0.21ppm3122464.1102
对比例4:其他操作同实施例1,区别仅在于所述铝合金铸件在铸造过程中,不进行型腔真空悬浮净化处理。
75.表2 实施例1和对比例3制备的铝合金铸件的测试结果
实施工艺冶金质量内腔尺寸工艺出品率固态氢含量kt=1、r=0.1、f=50hz、试验应力=200mpa下的疲劳寿命实施例1qj3185a-2018ⅰ类hb6103-2004ct6级80%0.10ppm1.24
×
107对比例3qj3185a-2018ⅲ类hb6103-2004ct9级45%0.18ppm1.47
×
105综上,本发明综合考虑了合金熔体的匀质搅拌制备、熔体精炼净化处理与型腔真空悬浮净化,设计了一种用于制备铝合金铸件的装置,所述装置可同步实现合金熔体的真空充型、置顶激冷与加压凝固。在提高合金熔体纯净度与均匀化程度的基础上,避免了cu、v等高比重元素的炉内偏析,提高了合金熔体的均匀性程度;在合金熔体浇铸前对铸型型腔(上铸型型腔和下铸型型腔)进行了真空悬浮净化处理,提高了铸型型腔的纯净程度,减少了夹杂物与夹渣缺陷的数量,可显著提高铝合金铸件的内在冶金质量;通过在铸型顶部布设置顶水路冷凝器,在合金熔体完成真空充型后,可对合金熔体实施激冷工艺,形成自上而下的顺序凝固温度梯度,在提高铸件铸态组织致密度的同时,细化铸态晶粒组织,实现铸件
的细晶化铸造;同时在合金熔体完成真空充型与置顶激冷后,对合金熔体进行高压加压凝固,可进一步提高铸件的致密度,有效减少疏松、气孔、缩孔等冶金缺陷的数量及严重程度,实现大型铝合金铸件的高冶金质量、高力学性能与高尺寸精度精密铸造成形。
76.以上,对本发明的实施方式进行了说明。但是,本发明不限定于上述实施方式。凡在本发明的精神和原则之内,所做的任何修改、等同替换、改进等,均应包含在本发明的保护范围之内。
再多了解一些
本文用于企业家、创业者技术爱好者查询,结果仅供参考。