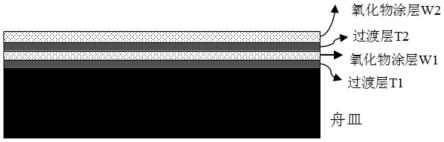
1.本发明涉及涂层技术领域,具体而言,涉及一种硬质合金烧结防粘涂层及其制备方法。
背景技术:
2.硬质合金由难熔金属硬质化合物和粘结金属通过粉末冶金工艺制成,具有高强度和硬度、良好的耐磨性和韧性、优异的耐热和耐腐蚀性等特点,用于制造切削刀具、采掘工具、钻具及高耐磨零部件等,被誉为“工业的牙齿”。其生产工艺主要包括粉末制备、混合、压制和烧结等。在烧结温度下,硬质合金中的粘结相与舟皿间润湿性好,易发生扩散和迁移。随着合金成分中的粘结剂含量增加,扩散反应加剧,导致产品更易出现粘舟、渗碳、变形等缺陷。因此,在硬质合金和舟皿间添加隔离层能有效改善产品烧结性能。
3.目前,硬质合金行业普遍使用的防粘涂料主要包括石墨、炭黑、金属氧化物、吐温、peg等,此类涂层所制备的涂层附着性较差,使用寿命短,一般仅可使用1次,且每次使用后需要将涂料去掉,重新刷涂新涂层,存在质量不稳定、工作环境差、人工多等缺点。
4.等离子喷涂技术采用高温高速等离子射流为热源,能熔化并喷涂所有具有物理熔点的材料,是目前应用最广的喷涂技术之一。等离子喷涂技术沉积效率高,生产成本低,可实现大尺寸件涂层的制备。
5.中国专利cn102744404a中公开的硬质合金的型坯烧结舟皿的表面防粘结方法,该专利利用等离子喷涂工艺制备氧化锆涂层,其使用次数可达10次,其重复使用次数偏低。专利cn110643929a公开了一种硬质合金烧结舟皿表面的防粘涂层及其制备方法,在舟皿表面喷涂碳化硅或氧化铝作为过渡层,再喷涂稀土氧化物作为工作层,所述涂层的烧结次数为40次左右。但目前所公开的喷涂舟皿所述烧结产品均为钴含量偏低的刀片或棒材类产品,未对中、高钴产品进行试验。而随着硬质合金成分中的钴含量增加,产品更易出现粘舟、渗碳等缺陷,导致涂层脱落,进而影响舟皿的使用寿命。
6.此外,由于氧化物涂层与舟皿间的热膨胀系数差异较大,若氧化物涂层过厚,更易引起涂层龟裂剥落。因此,现急需研发一种不易脱落、使用寿命长的涂层材料。
技术实现要素:
7.本发明提供了一种硬质合金烧结防粘涂层及其制备方法,能够有效解决上述方法。
8.本发明一方面提供了一种硬质合金烧结防粘涂层的制备方法,包括如下步骤:
9.步骤s1、对舟皿表面进行清洗、烘干,再进行喷砂处理;
10.步骤s2、将喷砂处理好的舟皿装夹到喷涂工作面,并进行预热;
11.步骤s3、在预热后的舟皿上等离子喷涂钨和/或钼,得到过渡层;
12.步骤s4、在过渡层表面等离子喷涂金属氧化物,得到工作层;
13.步骤s5、依次循环重复步骤s3和步骤s4。
14.本发明另一方面提供了一种由上述方法制得的硬质合金烧结防粘涂层。
15.本发明实施例的技术方案至少具有如下优点和有益效果:
16.本发明所制得的硬质合金烧结防粘涂层,通过采用仿贝壳层状交替结构涂层,增加氧化物涂层厚度,缓解涂层应力,提高涂层与舟皿的结合,增强涂层隔离防护作用,延长中、高钴硬质合金烧结舟皿使用寿命。
附图说明
17.为了更清楚地说明本发明实施例的技术方案,下面将对实施例中所需要使用的附图作简单地介绍,应当理解,以下附图仅示出了本发明的某些实施例,因此不应被看作是对范围的限定,对于本领域普通技术人员来讲,在不付出创造性劳动的前提下,还可以根据这些附图获得其他相关的附图。
18.图1为本发明实施例1提供的硬质合金烧结防粘涂层的剖面示意图;
19.图2为本发明实施例1提供的硬质合金烧结防粘涂层的金相图;
20.图3为本发明实施例1提供的硬质合金烧结防粘涂层的外观形貌图。
具体实施方式
21.为使本发明实施例的目的、技术方案和优点更加清楚,下面将对本发明实施例中的技术方案进行清楚、完整地描述。实施例中未注明具体条件者,按照常规条件或制造商建议的条件进行。所用试剂或仪器未注明生产厂商者,均为可以通过市售购买获得的常规产品。
22.本具体实施方式一方面提供了一种硬质合金烧结防粘涂层的制备方法,包括如下步骤:
23.步骤s1、对舟皿表面进行清洗、烘干,再进行喷砂处理;
24.步骤s2、将喷砂处理好的舟皿装夹到喷涂工作面,并进行预热;
25.步骤s3、在预热后的舟皿上等离子喷涂钨和/或钼,得到过渡层;
26.步骤s4、在过渡层表面等离子喷涂金属氧化物,得到工作层;
27.步骤s5、依次循环重复步骤s3和步骤s4。
28.在本方案中,所制得的涂层不局限于“2 2”的仿贝壳层状交替结构模式,还可根据实际应用需求,采用“3 3”或更多交替结构层的仿贝壳层状交替结构模式。
29.如此能够使舟皿表面粗化,有利于后续涂层与基体的结合。
30.进一步地,在步骤s1中,喷砂处理采用40-100目的刚玉砂砾,喷砂级别为sa3级。
31.喷砂的目的是使舟皿表面粗化,有利于后续涂层与基体的结合。
32.进一步地,在步骤s2中,预热温度为80-200℃。
33.预热的目的是为了去除舟皿基体表面水分,减少舟皿与涂层间热应力。
34.进一步地,在步骤s3中,等离子喷涂为:
35.主气为氩气,主气流量为20-80l/min;辅气为氢气,辅气流量为1-15l/min;送粉率为10-40g/min;喷涂距离为60-160mm。
36.进一步地,在步骤s4中,等离子喷涂为:
37.主气为氩气,主气流量为20-80l/min;辅气为氢气,辅气流量为4-25l/min;送粉率
为15-70g/min;喷涂距离为60-160mm。
38.进一步地,在步骤s4中,金属氧化物为氧化铝或稀土氧化物;
39.其中,稀土氧化物为氧化钇、氧化锆或氧化钇稳定氧化锆。
40.进一步地,氧化钇稳定氧化锆中的氧化钇掺杂含量≥8%。
41.实施例1
42.步骤s1、采用酒精和丙酮对舟皿进行清洗,去除表面油污,再将清洗后的舟皿进行烘干,烘干温度为100
±
10℃;
43.步骤s2、采用80目刚玉砂砾对烘干后的舟皿进行喷砂粗化处理,并将喷砂处理好的舟皿装夹到喷涂工作台上,采用等离子焰流对舟皿表面进行预热,预热温度为150℃;
44.步骤s3、采用等离子喷涂设备在舟皿表面喷涂金属钨中间过渡层t1,涂层厚度为50μm,喷涂工艺参数为:主气(氩气)流量为52l/min,辅气(氢气)流量为10l/min,送粉速度为25g/min,喷涂距离为90mm;
45.步骤s4、待过渡层t1冷却后,在过渡层t1表面等离子喷涂氧化钇稳定氧化锆涂层w1(氧化钇掺杂含量=10%),该涂层厚度为100μm,喷涂工艺参数为:主气(氩气)流量为50l/min,辅气(氢气)流量为12l/min,送粉速度为36g/min,喷涂距离为100mm;
46.步骤s5、待氧化钇稳定氧化锆涂层w1冷却后,在w1表面等离子喷涂金属钨中间过渡层t2,涂层厚度为50μm,喷涂工艺参数同步骤s3一致;
47.步骤s6、待金属钨中间过渡层t2冷却后,在其表面等离子喷涂氧化钇稳定氧化锆涂层w2,涂层厚度为120μm,喷涂工艺参数同步骤s4一致。
48.最终得到硬质合金烧结防粘涂层a1。
49.实施例2
50.步骤s1、采用酒精和丙酮对舟皿进行清洗,去除表面油污,再将清洗后的舟皿进行烘干,烘干温度为100
±
10℃;
51.步骤s2、采用80目刚玉砂砾对烘干后的舟皿进行喷砂粗化处理,并将喷砂处理好的舟皿装夹到喷涂工作台上,采用等离子焰流对舟皿表面进行预热,预热温度为190℃;
52.步骤s3、采用等离子喷涂设备在舟皿表面喷涂金属钼中间过渡层t1,涂层厚度为60μm,喷涂工艺参数为:主气(氩气)流量为55l/min,辅气(氢气)流量为12l/min,送粉速度为20g/min,喷涂距离为110mm;
53.步骤s4、待过渡层t1冷却后,在过渡层t1表面等离子喷涂氧化钇涂层w1,该涂层厚度为130μm,喷涂工艺参数为:主气(氩气)流量为48l/min,辅气(氢气)流量为10l/min,送粉速度为32g/min,喷涂距离为120mm;
54.步骤s5、待氧化钇涂层w1冷却后,在w1表面等离子喷涂金属钨中间过渡层t2,涂层厚度为60μm,喷涂工艺参数同步骤s3一致;
55.步骤s6、待金属钼中间过渡层t2冷却后,在其表面等离子喷涂氧化钇涂层w2,涂层厚度为150μm,喷涂工艺参数同步骤s4一致。
56.最终得到硬质合金烧结防粘涂层a2。
57.实验例1
58.将所制备的硬质合金烧结防粘涂层a1试烧钴含量高于15%的中、高钴硬质合金产品(如冲压模、钻齿类产品),可连续烧中高钴类硬质合金产品(钴含量15-20%)40次,高钴
类硬质合金产品(钴含量>20%)35次,过程中未出现涂层脱落。
59.将所制备的硬质合金烧结防粘涂层a2试烧钴含量高于15%的中、高钴硬质合金产品(如冲压模、钻齿类产品),可连续烧中高钴类硬质合金产品(钴含量15-20%)45次,高钴类硬质合金产品(钴含量>20%)38次,过程中未出现涂层脱落。
60.实验例2
61.如图2-3所示,对实施例1所制得的硬质合金烧结防粘涂层a1进行电镜扫描和拍照。
62.以上仅为本发明的优选实施例而已,并不用于限制本发明,对于本领域的技术人员来说,本发明可以有各种更改和变化。凡在本发明的精神和原则之内,所作的任何修改、等同替换、改进等,均应包含在本发明的保护范围之内。
再多了解一些
本文用于企业家、创业者技术爱好者查询,结果仅供参考。