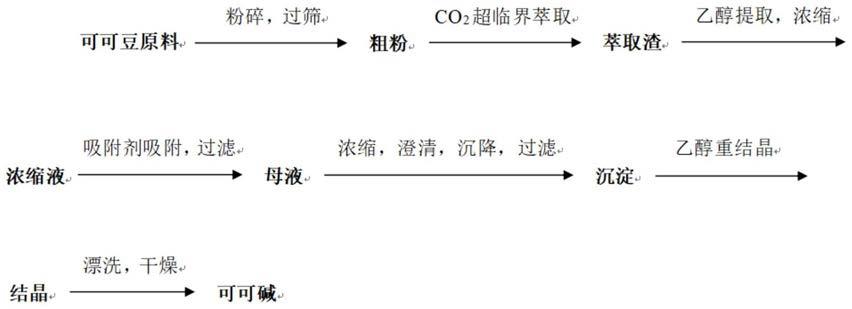
1.本发明涉及一种可可碱制备方法,具体为一种从可可豆中提取高含量可可碱的方法。
背景技术:
2.可可(theobroma cacao)是梧桐科可可属常绿乔木,原产美洲中部及南部,现广泛栽培于全世界的热带地区,在中国海南和云南南部有栽培,生长良好。可可豆是可可的种子,是制造可可粉和“巧克力糖”的主要原料,与咖啡、茶并称为世界上三大饮料。可可豆中主要包含多酚类化合物、脂质、蛋白质、纤维、矿物质、生物碱以及维生素等多种成分,具有兴奋中枢神经、疏通血管、抗氧化等作用。
3.可可碱(theobromine)属于黄嘌呤类化合物,是可可豆中主要的生物碱,在可可豆中的含量为1.5~3%。可可碱微溶于水,部分溶于沸水,几乎不容易乙醚和氯仿,可溶于浓酸并中度溶于氨水。
[0004][0005]
据报道,可可碱具有疏通血管,促进血管舒张,减少胆固醇在血管内的积累、减少炎症反应,降低血液中血小板形成凝聚,还具有预防心血管病和抑制动脉粥样硬化的作用。可可碱的抗氧化性比生物酚更强,能够捕获自由基。因此,具有较大的研究价值。
[0006]
传统制备可可碱的方法是化学合成的方法,工艺复杂,生产周期长。
[0007]
如中国专利cn 103724348a公开了一种可可碱的制备方法。将咖啡因加入强碱溶液中,反应得到咖啡因羧酸,与氰酸钠反应,得到可可碱羧酸,与强碱发生反应,闭环生成可可碱钠盐,可可碱钠盐用弱酸中和,得到可可碱。收率48%左右。此专利是采用化学合成的方法,咖啡酸加入氢氧化钠或氢氧化钾强碱溶液中进行反应,强碱的用量较大,对环境污染较大。中国专利cn 112142738 a同样采用化学合成的方法,经过缩、环合、亚化、酰化、闭合等步骤,生成可可碱,副产物少,但此方法步骤长,工艺步骤繁杂、生产周期长、副反应多,由此产生大量污水排放。
[0008]
中国专利cn110483519a提到一种从可可碱母液中回收可可碱的方法。可可碱母液中加氢氧化钠溶液调成中性母液,加萃取剂、分相剂得上层有机相溶液,浓缩干燥得粗品,加水,加氢氧化钠调ph值到10-11,升温至90℃,保温1h过滤,滤液降至40℃后用硫酸调ph到6.5-7,然后滤料并冲洗烘干,得到可可碱成品。但所用的化学试剂较多,对环境污染较大。
[0009]
如今,新兴了生物法和酶合成可可碱,但相关报道较少。生物法即通过基因重组获得菌株并通过发酵,以咖啡因为底物,用生物法制备可可碱。此法具有环保压力小、反应专
一性高等优点,但目前仅限于实验室阶段,受限于底物浓度,具有较大的研究空间。如专利cn 105524955 a是利用基因工程大肠杆菌全细胞生物法催化咖啡因去甲基化生成可可碱,环保高效,但对技术和设备要求极高,工业化生产难以实现。
技术实现要素:
[0010]
本发明的目的是提供一种从可可豆中提取可可碱的方法,克服现有可可碱制备方法存在的工艺复杂、环境污染及不利于工业化生产等问题。
[0011]
本发明的技术方案是:
[0012]
一种从可可豆中提取高含量可可碱的方法,其特殊之处在于,包括以下步骤:
[0013]
步骤1、超临界萃取;
[0014]
将可可豆原料粉碎,采用二氧化碳超临界萃取方法对原料进行萃取,除去脂溶性杂质,收集萃取渣;
[0015]
步骤2、乙醇提取、复合吸附剂除杂;
[0016]
步骤2.1、在步骤1的萃取渣中加入生石灰,搅拌均匀后加入乙醇溶液进行多次提取,过滤,合并并初步浓缩滤液;
[0017]
步骤2.2、向初步浓缩后的滤液中加入复合吸附剂,搅拌,进行脱色除杂,过滤后收集母液;
[0018]
步骤3、浓缩沉降,获得可可碱粗品;
[0019]
步骤3.1、初步浓缩步骤2收集的母液,并向其中加入壳聚糖,在设定温度下搅拌均匀;
[0020]
步骤3.2、将步骤3.1的溶液在设定温度下静置沉降设定时间;
[0021]
步骤3.3、过滤步骤3.2静置沉降后的溶液,收集滤渣,并干燥,获得可可碱粗品;
[0022]
步骤4、精制;
[0023]
步骤4.1、在步骤3获得的可可碱粗品中加入乙醇溶液与氨水,加热使其溶解;
[0024]
步骤4.2、加入活性炭进行脱色,过滤,收集滤液,并浓缩,低温静置设定时间后过滤,依次用热乙醇、纯化水漂洗滤渣,收集滤渣并干燥,获得可可碱。
[0025]
进一步地,步骤1中,二氧化碳超临界萃取方法的条件为:萃取压力为25~30mpa,萃取温度为45-50℃,萃取时间为3~4h,ⅰ级分离釜压力为5~8mpa,温度为40~45℃,ⅱ级分离釜压力为3~5mpa,温度为35~40℃。
[0026]
进一步地,步骤2.1中,生石灰的用量为可可豆原料质量的10%~20%。
[0027]
为了进一步提高可可碱的回收率,步骤2.1中,乙醇溶液的体积浓度为80%~90%,每次提取时,乙醇溶液的用量为可可豆原料质量的8~12倍;在65℃
±
5℃搅拌提取3次,每次2h;合并并初步浓缩滤液后,使得滤液中乙醇体积浓度为50%~60%。
[0028]
进一步地,步骤2.1中,乙醇溶液的体积浓度为85%。
[0029]
进一步地,步骤2.2中的复合吸附剂为活性炭和活性白土的混合物,其中活性炭占比为70~80%,活性白土占比为20~30%。
[0030]
进一步地,步骤2.2中复合吸附剂的用量为可可豆原料质量的10%~20%。
[0031]
进一步地,步骤2.2中复合吸附剂的用量为可可豆原料质量的15%,其中活性炭占比为75%,活性白土占比为25%。
[0032]
进一步地,步骤2.2中搅拌进行脱色除杂后,趁热过滤。
[0033]
进一步地,步骤3.1中初步浓缩时,将步骤2收集的母液浓缩至可可豆原料量的1~3倍量体积;所述设定温度为65℃,壳聚糖的添加量为初步浓缩后母液体积的5%~12%。
[0034]
进一步地,壳聚糖的添加量为初步浓缩后母液体积的9%。
[0035]
进一步地,步骤3.2中,所述设定温度为20℃,所述设定时间为48h。
[0036]
进一步地,步骤4.1中,乙醇溶液中乙醇的体积浓度为70%,质量为可可碱粗品质量的20~30倍量;氨水的质量为可可碱粗品质量的3%~5%,加热至70℃,使可可碱粗品溶解。
[0037]
进一步地,步骤4.2中活性炭的用量为可可碱粗品质量的3%~8%。
[0038]
进一步地,步骤4.2中浓缩滤液后在0~5℃温度下静置24h。
[0039]
本发明的有益效果是:
[0040]
1、本发明在可可碱分离过程中,摒弃了化学合成的传统工艺,利用优化的提取工艺从可可豆原料中提取高含量的可可碱。首先,采用超临界二氧化碳萃取技术除去原料中的脂溶性杂质;再用乙醇提取,并在提取时加入少量的生石灰,能够脱除原料中的鞣质等酸性杂质,利于后续工艺的处理,提高活性成分的收率,提高可可碱的纯度;然后再采用活性炭和活性白土组成的复合吸附剂进行脱色除杂;之后采用壳聚糖吸附有效成分,最后采用乙醇-氨水进行重结晶;回收率高达85%以上,纯度可以达到98%以上;
[0041]
相对传统化学合成方法及现有从可可碱母液中提取回收可可碱的方法,本发明工艺过程中不需要强酸强碱的参与,有机溶剂用量少,同时采用的乙醇安全环保,且可以通过蒸馏回收并循环利用,工艺过程简单安全且环保;
[0042]
相对生物法和酶合成法,本发明对技术和设备要求较低,易于实现工业化生产。
[0043]
2、本发明采用超临界萃取-提取-吸附-沉降-精制多个技术联合使用,避免使用柱层析,使步骤简单,操作方便,安全环保,生产成本低,适宜工业化生产。
[0044]
3、本发明采用超临界二氧化碳萃取技术除去可可豆中可可脂和可可色素等成分,这些成分会严重妨碍后续步骤中可可碱产品的析出。
[0045]
4、本发明经过大量试验,筛选出壳聚糖对可可碱进行吸附,试验验证,壳聚糖对可可碱有很好的吸附作用,选择性强,可有效地实现可可碱与杂质的分离,得到可可碱粗品。
附图说明
[0046]
图1为本发明方法流程图;
[0047]
图2为实施例1中提取出的可可碱含量hplc图谱;
[0048]
图3为实施例2中提取出的可可碱含量hplc图谱;
[0049]
图4为实施例3中提取出的可可碱含量hplc图谱;
[0050]
图5为实施例4中提取出的可可碱含量hplc图谱;
[0051]
图6为实施例5中提取出的可可碱含量hplc图谱;
[0052]
图7为实施例6中提取出的可可碱含量hplc图谱。
具体实施方式
[0053]
为使本发明的上述目的、特征和优点能够更加明显易懂,下面结合说明书附图对
本发明的具体实施方式做详细的说明,显然所描述的实施例是本发明的一部分实施例,而不是全部实施例。基于本发明中的实施例,本领域普通人员在没有做出创造性劳动前提下所获得的所有其他实施例,都应当属于本发明的保护的范围。
[0054]
在下面的描述中阐述了很多具体细节以便于充分理解本发明,但是本发明还可以采用其他不同于在此描述的其它方式来实施,本领域技术人员可以在不违背本发明内涵的情况下做类似推广,因此本发明不受下面公开的具体实施例的限制。
[0055]
实施例1
[0056]
(1)超临界萃取:取可可豆原料10kg(可可碱含量1.22%)粉碎至60目,采用二氧化碳超临界萃取技术对原料进行萃取,萃取压力为25mpa,温度45℃,时间3h,ⅰ级分离釜压力5mpa,温度40℃,ⅱ级分离釜压力3mpa,温度35℃,得到可可油脂类成分和萃取渣。
[0057]
(2)乙醇提取、复合吸附剂除杂:萃取渣用原料量10%的生石灰拌匀,再用8倍量的80%乙醇65℃搅拌提取3次,每次2h,过滤,滤液浓缩至乙醇浓度50%,加入原料质量10%的复合吸附剂(其中活性炭占比70%,活性白土占比30%),65℃搅拌1h,趁热过滤,收集母液。
[0058]
(3)浓缩沉降:上述母液浓缩至原料量的1倍量体积,加入浓缩液体积5%的壳聚糖65℃进行搅拌吸附,之后澄清30min,20℃放置48h,过滤,分别收集沉淀和滤液,沉淀干燥得可可碱粗品。
[0059]
(4)精制:粗品用20倍量的70%乙醇(含3%的氨水)70℃溶解后,加入粗品质量3%的活性炭70℃进行脱色1h,过滤,滤液浓缩至粗品量的一倍量,然后低温放置24h,过滤,用热乙醇、纯化水漂洗,得到沉淀,干燥,共0.107kg,可可碱含量为98.12%(见图2),收率1.07%,回收率为86.06%。
[0060]
实施例2
[0061]
(1)超临界萃取:取可可豆原料10kg(可可碱含量1.22%)粉碎至60目,采用二氧化碳超临界萃取技术对原料进行萃取,萃取压力为30mpa,温度50℃,时间4h,ⅰ级分离釜压力8mpa,温度45℃,ⅱ级分离釜压力5mpa,温度40℃,得到可可油脂类成分和萃取渣。
[0062]
(2)乙醇提取、复合吸附剂除杂:萃取渣用原料量20%的生石灰拌匀,再用12倍量的90%乙醇65℃搅拌提取3次,每次2h,过滤,滤液浓缩至乙醇浓度60%,加入原料质量20%的复合吸附剂(其中活性炭占比80%,活性白土占比20%),65℃搅拌1h,趁热过滤,收集母液。
[0063]
(3)浓缩沉降:上述母液浓缩至原料量的3倍量体积,加入浓缩液体积12%的壳聚糖65℃进行搅拌吸附,后澄清30min,20℃放置48h,过滤,分别收集沉淀和滤液,沉淀干燥得可可碱粗品。
[0064]
(4)精制:上述得到的粗品用30倍量的70%乙醇(含5%的氨水)70℃溶解,加入粗品质量8%的活性炭70℃进行脱色1h,过滤,滤液浓缩至粗品量的一倍量,低温放置24h,过滤,用热乙醇、纯化水漂洗,得到沉淀,干燥,共0.106kg,可可碱含量为98.92%(见图3),收率1.06%,回收率为85.95%。
[0065]
实施例3
[0066]
(1)超临界萃取:取可可豆原料10kg(可可碱含量1.22%)粉碎至60目,采用二氧化碳超临界萃取技术对原料进行萃取,萃取压力为28mpa,温度48℃,时间3.5h,ⅰ级分离釜压力6mpa,温度43℃,ⅱ级分离釜压力4mpa,温度38℃,得到可可油脂类成分和萃取渣。
[0067]
(2)乙醇提取、复合吸附剂除杂:萃取渣用原料量15%的生石灰拌匀,再用10倍量的85%乙醇65℃搅拌提取3次,每次2h,过滤,滤液浓缩至乙醇浓度55%,加入原料质量15%的粉末状复合吸附剂(其中活性炭占比75%,活性白土占比25%),65℃搅拌1h,趁热过滤,收集母液。
[0068]
(3)浓缩沉降:上述母液浓缩至原料量的2倍量体积,加入浓缩液体积9%的壳聚糖65℃进行搅拌吸附,后澄清30min,20℃放置48h,过滤,分别收集沉淀和滤液,沉淀干燥得可可碱粗品。
[0069]
(4)精制:上述得到的粗品用25倍量的70%乙醇(含4%的氨水)70℃溶解,加入粗品质量5%的活性炭70℃进行脱色1h,过滤,滤液浓缩至粗品量的一倍量,低温放置24h,过滤,用热乙醇、纯化水漂洗,得到沉淀,干燥,共0.106kg,可可碱含量为98.68%(见图4),收率1.06%,回收率为85.74%。
[0070]
实施例4
[0071]
(1)超临界萃取:取可可豆原料10kg(可可碱含量1.22%)粉碎至60目,采用二氧化碳超临界萃取技术对原料进行萃取,萃取压力为29mpa,温度49℃,时间3h,ⅰ级分离釜压力7mpa,温度44℃,ⅱ级分离釜压力5mpa,温度39℃,得到可可油脂类成分和萃取渣。
[0072]
(2)乙醇提取、复合吸附剂除杂:萃取渣用原料量18%的生石灰拌匀,再用9倍量的85%乙醇65℃搅拌提取3次,每次2h,过滤,滤液浓缩至乙醇浓度58%,加入原料质量18%的粉末状复合吸附剂(其中活性炭占比75%,活性白土占比25%),65℃搅拌1h,趁热过滤,收集母液。
[0073]
(3)浓缩沉降:上述母液浓缩至原料量的2倍量体积,加入浓缩液体积10%的壳聚糖65℃进行搅拌吸附,后澄清30min,20℃放置48h,过滤,分别收集沉淀和滤液,沉淀干燥得可可碱粗品。
[0074]
(4)精制:上述得到的粗品用28倍量的70%乙醇(含4%的氨水)70℃溶解,加入粗品质量7%的活性炭70℃进行脱色1h,过滤,滤液浓缩至粗品量的一倍量,低温放置24h,过滤,用热乙醇、纯化水漂洗,得到沉淀,干燥,共0.107kg,可可碱含量为98.08%(见图5),收率1.07%,回收率为86.02%。
[0075]
实施例5
[0076]
(1)超临界萃取:取可可豆原料10kg(可可碱含量1.22%)粉碎至60目,采用二氧化碳超临界萃取技术对原料进行萃取,萃取压力为27mpa,温度47℃,时间3.5h,ⅰ级分离釜压力5mpa,温度42℃,ⅱ级分离釜压力5mpa,温度37℃,得到可可油脂类成分和萃取渣。
[0077]
(2)乙醇提取、复合吸附剂除杂:萃取渣用原料量12%的生石灰拌匀,再用11倍量的85%乙醇65℃搅拌提取3次,每次2h,过滤,滤液浓缩至乙醇浓度53%,加入原料质量12%的粉末状复合吸附剂(其中活性炭占比80%,活性白土占比20%),65℃搅拌1h,趁热过滤,收集母液。
[0078]
(3)浓缩沉降:上述母液浓缩至原料量的2倍量体积,加入浓缩液体积7%的壳聚糖65℃进行搅拌吸附,后澄清30min,20℃放置48h,过滤,分别收集沉淀和滤液,沉淀干燥得可可碱粗品。
[0079]
(4)精制:上述得到的粗品用28倍量的70%乙醇(含4%的氨水)70℃溶解,加入粗品质量6%的活性炭70℃进行脱色1h,过滤,滤液浓缩至粗品量的一倍量,低温放置24h,过
滤,用热乙醇、纯化水漂洗,得到沉淀,干燥,共0.106kg,可可碱含量为98.38%(见图6),收率1.06%,回收率为85.48%。
[0080]
实施例6
[0081]
(1)超临界萃取:取可可豆原料10kg(可可碱含量1.22%)粉碎至60目,采用二氧化碳超临界萃取技术对原料进行萃取,萃取压力为26mpa,温度46℃,时间3h,ⅰ级分离釜压力8mpa,温度41℃,ⅱ级分离釜压力5mpa,温度36℃,得到可可油脂类成分和萃取渣。
[0082]
(2)乙醇提取、复合吸附剂除杂:萃取渣用原料量16%的生石灰拌匀,再用10倍量的85%乙醇65℃搅拌提取3次,每次2h,过滤,滤液浓缩至乙醇浓度51%,加入原料质量16%的粉末状复合吸附剂(其中活性炭占比75%,活性白土占比25%),65℃搅拌1h,趁热过滤,收集母液。
[0083]
(3)浓缩沉降:上述母液浓缩至原料量的2倍量体积,加入浓缩液体积11%的壳聚糖65℃进行搅拌吸附,后澄清30min,20℃放置48h,过滤,分别收集沉淀和滤液,沉淀干燥得可可碱粗品。
[0084]
(4)精制:上述得到的粗品用29倍量的70%乙醇(含5%的氨水)70℃溶解,加入粗品质量7%的活性炭70℃进行脱色1h,过滤,滤液浓缩至粗品量的一倍量,低温放置24h,过滤,用热乙醇、纯化水漂洗,得到沉淀,干燥,共0.108kg,可可碱含量为98.08%(见图7),收率1.08%,回收率为86.82%。
再多了解一些
本文用于企业家、创业者技术爱好者查询,结果仅供参考。