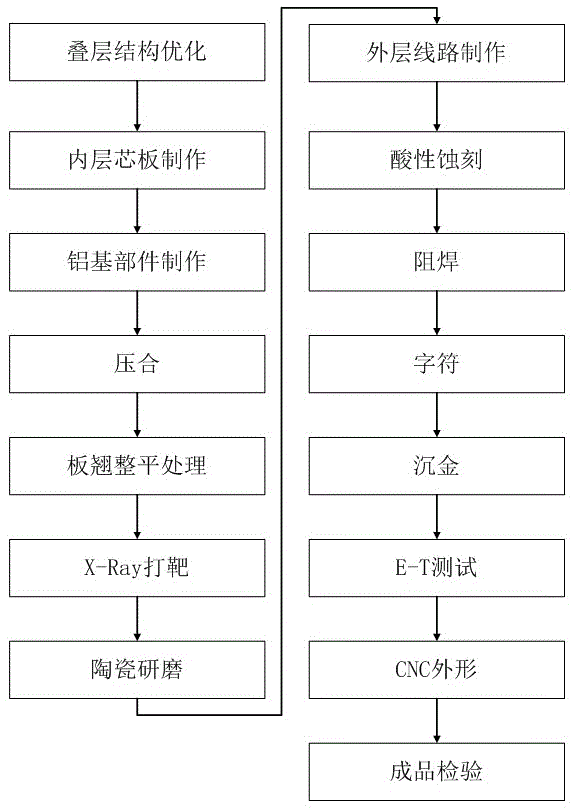
本发明涉及PCB板的技术领域,具体为一种改善铝基混压结构层压板翘的控制方法及PCB板。
背景技术
目前汽车电源模块产品,主要以厚铜芯板压合铝基结构为主,依托面铜、孔铜、高导热粘结片及金属铝基实现产品快速导热,由于金属铝基与铜芯板是两种不同物性的材料,在高温压合时,其涨缩变化不一致,极易出现板翘超标(翘曲度≥1.5%),影响产品平整度,对客户后续贴片质量有潜在影响。
技术实现要素:
基于此,有必要提供一种改善铝基混压结构层压板翘的控制方法及PCB板。
一种改善铝基混压结构层压板翘的控制方法,包括
S1、叠层结构优化,选取预设厚度和硬度的铝基和内层芯板,使铝基和内层芯板中的芯板介质层的厚度比值≥10:1;
S2、内层芯板制作;
S3、铝基部件制作,铝基开料后,对铝基预先热压1次;
S4、压合,将内层芯板和铝基采用真空层压机压合在一起;
S5、板翘整平处理,压合后,用板翘整平机进行整平处理;
S6、X-Ray打靶;
S7、陶瓷研磨;
S8、外层线路制作;
S9、酸性蚀刻;
S10、阻焊;
S11、字符;
S12、沉金;
S13、E-T测试;
S14、CNC外形;
S15、成品检验。
在其中一个实施例中,所述芯板介质层的厚度≤0.15mm。
在其中一个实施例中,所述铝基和芯板介质层的厚度比值为15:1。
在其中一个实施例中,所述S2中内层芯板制作的方法为:
第一步、内层开料;
第二步、钻孔;
第三步、沉铜;
第四步、VCP一铜;
第五步、检验;
第六步、树脂塞孔;
第七步、陶瓷研磨;
第八步、贴干膜;
第九步、内层线路制作;
第十步、酸性蚀刻;
第十一步、内层蚀检;
第十二步、棕化。
在其中一个实施例中,所述铝基部件制作的方法为:
第一步、铝基开料;
第二步、铝基预热压处理;
第三步、钻定位孔;
第四步、砂带研磨;
第五步、化学粗化;
第六步、成品清洗。
在其中一个实施例中,所述芯板介质层的厚度为0.1mm。
在其中一个实施例中,所述对铝基预先热压包括常规热压方法和快速热压方法。
在其中一个实施例中,所述常规热压方法的参数为:进炉温度为140℃,升温速率1.8℃-2.2℃/min,压力30 kg -40kg/cm2,200℃保温压合≥60min。
在其中一个实施例中,所述快速热压方法的参数为:进炉温度为160℃-200℃,升温速率5℃-10℃/min,压力30 kg -40kg/cm2,200℃保温压合20min。
改善铝基混压结构层压板翘的控制方法得到的PCB板,所述PCB板包括铝基和内层芯板,所述铝基和内层芯板通过半固化片压合,所述内层芯板包括芯板介质层,铝基和芯板介质层的厚度比值≥10:1。
上述改善铝基混压结构层压板翘的控制方法,选取预设厚度的铝基和内层芯板,使铝基和内层芯板中的芯板介质层的厚度比值≥10:1,既可以使整个PCB板更加轻薄,降低板翘又能满足PCB板的耐高压要求,同时选择预设硬度的铝基可以满足压合的要求,铝基开料后,预先用高温压机(200℃)热压1次,释放热应力,提高了铝基的热稳定性, 降低铝基热压涨缩变化;最后,用板翘整平机进行整平处理,进一步改善板面翘曲度,使PCB板的板面翘曲度≤0.75%,满足客户对产品的高平整度要求。
附图说明
图1为本发明的改善铝基混压结构层压板翘的控制方法的流程图;
图2为本发明的改善铝基混压结构层压板翘的控制方法的内层芯板制作的流程图;
图3为本发明的改善铝基混压结构层压板翘的控制方法的铝基部件制作的流程图;
图4为本发明的改善铝基混压结构层压板翘的控制方法的PCB板的结构示意图。
具体实施方式
为使本发明的上述目的、特征和优点能够更加明显易懂,下面结合附图对本发明的具体实施方式做详细的说明。在下面的描述中阐述了很多具体细节以便于充分理解本发明。但是本发明能够以很多不同于在此描述的其它方式来实施,本领域技术人员可以在不违背本发明内涵的情况下做类似改进,因此本发明不受下面公开的具体实施例的限制。
除非另有定义,本文所使用的所有的技术和科学术语与属于本发明的技术领域的技术人员通常理解的含义相同。本文中在本发明的说明书中所使用的术语只是为了描述具体的实施方式的目的,不是旨在于限制本发明。本文所使用的术语“和/或”包括一个或多个相关的所列项目的任意的和所有的组合。
在汽车电源模块应用的PCB板,通常对PCB板的耐高压性有很高的要求,所以要求PCB板的铝基100和内层芯板200中的芯板介质层210越厚越好,但是,为了控制PCB板的板翘,需要芯板介质层210越薄越好,所以经过大量的研究和实验,确定了铝基100和内层芯板200中的芯板介质层210的厚度比值,既能满足PCB板的耐高压要求,又能控制PCB板的板翘在标准范围内。
如图1所示,一种改善铝基混压结构层压板翘的控制方法,包括
S1、叠层结构优化,选取预设厚度和硬度的铝基100和内层芯板200,使铝基100和内层芯板200中的芯板介质层210的厚度比值≥10:1;
S2、内层芯板制作;
S3、铝基部件制作,铝基100开料后,对铝基100预先热压1次;
S4、压合,将内层芯板200和铝基100采用真空层压机压合在一起;
S5、板翘整平处理,压合后,用板翘整平机进行整平处理;
S6、X-Ray打靶;
S7、陶瓷研磨;
S8、外层线路制作;
S9、酸性蚀刻;
S10、阻焊;
S11、字符;
S12、沉金;
S13、E-T测试;
S14、CNC外形;
S15、成品检验。
在其中一个实施例中,所述芯板介质层210的厚度≤0.15mm。
在其中一个实施例中,所述铝基100和芯板介质层210的厚度比值为15:1。
如图2所示,在其中一个实施例中,所述S2中内层芯板200制作的方法为:
第一步、内层开料;
第二步、钻孔,按工程MI文件对内层芯板200进行钻孔作业;
第三步、沉铜,对孔壁进行金属化处理;
第四步、VCP一铜,采用VCP设备,将表铜及孔铜进行电镀加厚,并符合客户铜厚控制要求;
第五步、检验;
第六步、树脂塞孔,对内层盲孔进行树脂塞孔,防止层压时PP胶过度流失影响厚铜层压可靠性;
第七步、陶瓷研磨;
第八步、贴干膜;
第九步、内层线路制作,内层芯板双面贴干膜,然后按工程线路文件进行内层图形转移;
第十步、酸性蚀刻;
第十一步、内层蚀检,内层酸性蚀刻,退除保护干膜后即得到完整的内层图形;
第十二步、棕化。
如图3所示,在其中一个实施例中,所述铝基部件制作的方法为:
第一步、铝基开料;
第二步、铝基预热压处理;
第三步、钻定位孔;
第四步、砂带研磨;
第五步、化学粗化;
第六步、成品清洗。
在其中一个实施例中,所述芯板介质层210的厚度为0.1mm。
在其中一个实施例中,所述对铝基100预先热压包括常规热压方法和快速热压方法。
在其中一个实施例中,所述常规热压方法的参数为:进炉温度为140℃,升温速率1.8-2.2℃/min,压力30-40kg/cm2,200℃保温压合≥60min。
在其中一个实施例中,所述快速热压方法的参数为:进炉温度为160℃-200℃,升温速率5-10℃/min,压力30-40kg/cm2,200℃保温压合20min。
如图4所示,改善铝基混压结构层压板翘的控制方法得到的PCB板,所述PCB板包括铝基100和内层芯板200,所述铝基100和内层芯板200通过半固化片压合,所述内层芯板200包括芯板介质层210,铝基100和芯板介质层210的厚度比值≥10:1。
实施例1:一种改善铝基混压结构层压板翘的控制方法,包括
S1、叠层结构优化,选取预设厚度和硬度的铝基100和内层芯板200,使铝基100和内层芯板200中的芯板介质层210的厚度比值为10:1;
S2、内层芯板制作;
S3、铝基部件制作,铝基100开料后,采用常规热压方法对铝基100预先热压1次;常规热压方法的参数为:进炉温度为140℃,升温速率1.8℃-2.2℃/min,压力30 kg -40kg/cm2,200℃保温压合≥60min。
S4、压合,将内层芯板200和铝基100采用真空层压机压合在一起;
S5、板翘整平处理,压合后,用板翘整平机进行整平处理;
S6、X-Ray打靶;
S7、陶瓷研磨;
S8、外层线路制作,在压合后的PCB板表面完成外层线路的制作;
S9、酸性蚀刻,通过酸性溶液蚀去PCB板上无抗蚀层保护的铜面;
S10、阻焊,利用油墨对压合后的PCB板进行阻焊处理;
S11、字符,在压合后的PCB板上填写文字;
S12、沉金,直接在铜皮上面沉金;
S13、E-T测试,对压合后的PCB板进行测试;
S14、CNC外形,将压合后的PCB板放入锣机,按设计的外形尺寸锣出成品;
S15、成品检验,对压合后的PCB板外观进行检测。
这样,改善铝基混压结构层压板翘的控制方法,选取预设厚度的铝基和内层芯板,使铝基和内层芯板中的芯板介质层的厚度比值为10:1,既可以使整个PCB板更加轻薄降低板翘又能满足PCB板耐高压的要求,同时选择预设硬度的铝基可以满足压合的要求,铝基开料后,预先用高温压机(200℃)热压1次,释放热应力,提高了铝基的热稳定性, 降低铝基热压涨缩变化;最后,用板翘整平机进行整平处理,进一步改善板面翘曲度,使PCB板的板面翘曲度≤0.75%,满足客户对产品的高平整度要求。
进一步地,铝基100采用硬度较大的合金铝材料,例如5052/6061。
实施例2:一种改善铝基混压结构层压板翘的控制方法,包括
S1、叠层结构优化,选取预设厚度和硬度的铝基100和内层芯板200,使铝基100和内层芯板200中的芯板介质层210的厚度比值为15:1;
S2、内层芯板制作;
S3、铝基部件制作,铝基100开料后,采用快速热压方法对铝基100预先热压1次;快速热压方法的参数为:进炉温度为160℃-200℃,升温速率5℃-10℃/min,压力30 kg -40kg/cm2,200℃保温压合20min。
S4、压合,将内层芯板200和铝基100采用真空层压机压合在一起;
S5、板翘整平处理,压合后,用板翘整平机进行整平处理;
S6、X-Ray打靶;
S7、陶瓷研磨;
S8、外层线路制作,在压合后的PCB板表面完成外层线路的制作;
S9、酸性蚀刻,通过酸性溶液蚀去PCB板上无抗蚀层保护的铜面;
S10、阻焊,利用油墨对压合后的PCB板进行阻焊处理;
S11、字符,在压合后的PCB板上填写文字;
S12、沉金,直接在铜皮上面沉金;
S13、E-T测试,对压合后的PCB板进行测试;
S14、CNC外形,将压合后的PCB板放入锣机,按设计的外形尺寸锣出成品;
S15、成品检验,对压合后的PCB板外观进行检测。
这样,改善铝基混压结构层压板翘的控制方法,选取预设厚度的铝基和内层芯板,使铝基和内层芯板中的芯板介质层的厚度比值为15:1,既可以使整个PCB板更加轻薄降低板翘又能满足PCB板耐高压的要求,同时选择预设硬度的铝基可以满足压合的要求,铝基开料后,预先用高温压机(200℃)快速热压1次,释放热应力,提高了铝基的热稳定性, 降低铝基热压涨缩变化;最后,用板翘整平机进行整平处理,进一步改善板面翘曲度,使PCB板的板面翘曲度≤0.75%,满足客户对产品的高平整度要求。
进一步地,铝基100在开料后,采用快速热压方式对铝基100进行热压处理,在缩短热压时间并保证生产效率的同时,充分释放板材热应力,提高铝基100的热稳定性,降低铝基二次热压涨缩变化,热压时间将由常规3H缩短至1H,达到提高了热压效率。
进一步地,半固化片为高导热粘结片。
以上所述实施例的各技术特征可以进行任意的组合,为使描述简洁,未对上述实施例中的各个技术特征所有可能的组合都进行描述,然而,只要这些技术特征的组合不存在矛盾,都应当认为是本说明书记载的范围。
以上所述实施例仅表达了本发明的几种实施方式,其描述较为具体和详细,但并不能因此而理解为对发明专利范围的限制。应当指出的是,对于本领域的普通技术人员来说,在不脱离本发明构思的前提下,还可以做出若干变形和改进,这些都属于本发明的保护范围。因此,本发明专利的保护范围应以所附权利要求为准。
本文用于企业家、创业者技术爱好者查询,结果仅供参考。