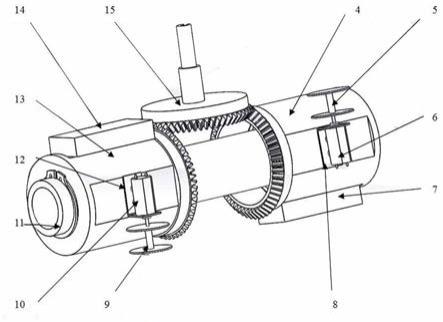
1.本实用新型涉及自动退缆领域,尤其是一种便携缆芯退纱装置。
背景技术:
2.在光缆缆芯的生产过程中,为了将正反左右绞合的光纤松套管以一定的绞合节距固定在中心加强钢丝上,现有技术是采用两根扎纱以相反方向的旋转绕扎方式对光纤松套管进行缠绕捆绑,里层的扎纱为扎纱a、外层的扎纱为扎纱b,使之形成一根光缆缆芯。但在生产过程中因某些设备、原材料或者操作等原因,会产生一些质量有隐患的缆芯,不能够正常流入护套工序,为了避免造成生产过程中更大的损失,则需要将这些质量有隐患的成型缆芯退缆拆开还原成几根松套管和钢丝,再重新绞合生产成质量指标合格的缆芯。现有方法都是采用人工退缆,但人工退缆时用刀片划断缆芯上的扎纱经常会将套管光纤划断,导致人为操作失误造成原材料损失及人工浪费。专利号201420375865.1,专利名称为“光缆自动退缆及松套管更换装置”,内容为“一种光缆自动退缆及松套管更换装置,包括第一退纱机、第二退纱机,第一退纱机的转动方向与第二退纱机的转动方向相反;第一退纱机的外侧部设置有第一退纱盘,第一退纱盘的转动方向与第一退纱机的转动方向相反;第二退纱机的外侧部设置有第二退纱盘,第二退纱盘的转动方向与第二退纱机的转动方向相反;第一退纱机上设置有第一主驱动装置和第一副驱动装置,第二退纱机上设置有第二主驱动装置和第二副驱动装置。缆芯通过设备就可以完成退纱,但是存在缺点,
3.1)第一退纱机和第二退纱机有两副装置驱动。两个退纱机同步性不好,可能会导致退纱失败。
4.2)退纱盘转动方向与缆芯运动方向垂直,退纱点距离退纱盘超过一定距离后,退纱盘收不上来纱。
5.3)该装置质量大,体积大,不可移动。应用场景小。
技术实现要素:
6.本实用新型的目的是提供一种便携缆芯退纱装置,用以解决两个退纱机同步性不好,退纱盘收不上来纱,装置体积大等问题。
7.本实用新型的技术方案:一种便携缆芯退纱装置,包括箱体、箱盖、轴承盖、出缆侧空心锥齿轮、出缆侧收纱盘、出缆侧电机、出缆侧电池盒、出缆侧电机支架、进缆侧收纱盘、进缆侧电机、空心轴、进缆侧电机支架、进缆侧空心锥齿轮、进缆侧电池盒、锥齿轮轴、出缆侧轴承、出缆侧挡圈、进缆侧挡圈、进缆侧轴承和轴承,箱盖用四根螺栓固定在箱体上,锥齿轮轴通过轴承盖和轴承固定在箱盖上,空心轴的底部通过焊接的方式连接在箱体的支柱上,出缆侧空心锥齿轮、进缆侧空心锥齿轮套在空心轴上,出缆侧空心锥齿轮与空心轴之间安装出缆侧轴承,进缆侧空心锥齿轮空心轴之间安装进缆侧轴承,出缆侧空心锥齿轮、进缆侧空心锥齿轮与锥齿轮轴齿轮互相咬合,出缆侧空心锥齿轮与进缆侧空心锥齿轮远离齿轮咬合的一侧安装出缆侧挡圈及进缆侧挡圈,两个挡圈安装在空心轴的沟槽里,通过两个挡
圈限制两个空心锥齿轮轴向移动,出缆侧收纱盘、进缆侧收纱盘分别安装在出缆侧电机、进缆侧电机的转轴上,缆芯穿过空心轴,两种扎纱绕过出缆侧收纱盘、进缆侧收纱盘上。
8.所述出缆侧空心锥齿轮及所述进缆侧空心锥齿轮上的侧面平台上安装出缆侧电机支架、进缆侧电机支架,通过螺钉分别连接在出缆侧空心锥齿轮、进缆侧空心锥齿轮上,出缆侧电机支架、进缆侧电机支架上通过螺钉分别连接出缆侧电机、进缆侧电机,所述出缆侧空心锥齿轮及所述进缆侧空心锥齿轮上的另一个侧面平台上还安装有出缆侧电池盒、进缆侧电池盒,通过螺钉连接固定,出缆侧电机、进缆侧电机与出缆侧电池盒进缆侧电池盒之间通过导线连接。
9.所述出缆侧空心锥齿轮和所述进缆侧空心锥齿轮沿相反方向转动。
10.出缆侧空心锥齿轮、进缆侧空心锥齿轮同轴同速转动。
11.所述出缆侧收纱盘、进缆侧收纱盘运动的方向与缆芯的运动方向平行。
12.所述出缆侧电机与进缆侧电机的转速大于退纱速度,保证扎纱一直是抻直状态。
13.所述出缆侧轴承与所述进缆侧轴承均为滚动轴承。
14.所述两种扎纱分别为黄扎纱及紫扎纱。
15.所述锥齿轮轴上方有驱动设备。
16.所述驱动设备为电动螺丝刀。
17.当有驱动力作用在锥齿轮轴上时,由于锥齿轮轴和箱盖之间有轴承,所以箱体和箱盖不跟着转动。出缆侧空心锥齿轮和进缆侧空心锥齿轮沿相反方向转动,这样出缆侧空心锥齿轮、出缆侧电池盒、出缆侧电机支架、出缆侧电机、出缆侧收纱盘沿着同一方向转动。进缆侧空心锥齿轮、进缆侧电池盒、进缆侧电机支架、进缆侧电机、进缆侧收纱盘沿着另一方向转动。由于出缆侧轴承及进缆侧轴承的存在,出缆侧轴承与进缆侧轴承均采用滚动轴承,利用滚动轴承的外圈不转动,内圈与轴一起转动的特点,保证空心轴不跟着转动。这样就能保证缆芯不受设备旋转的影响。从而不会对缆芯造成伤害。所述出缆侧电机与进缆侧电机的转速大于退纱速度,保证扎纱一直是抻直状态。
18.本实用新型的有益技术效果:通过锥齿轮啮合来实现正反转同步性极好。不会造成扎纱相互缠绕的情况。改善了现有技术采用两个单独的驱动分别控制正反转。同步性不好的问题。由于收纱盘运动的方向与缆芯的运动方向平行,解决了现有技术退纱盘转动方向与缆芯运动方向垂直,退纱点距离退纱盘超过一定距离后,退纱盘收不上来纱的问题。本装置便携性好体积小,质量轻。不需要外接电源。应用场景多。改善了现有技术质量大,体积大,不可移动。需要外接电源,应用场景小的问题。采用小电机带动收纱盘收纱的方式,当使用者的移动速度与设备不同步时,由于电机的扭矩有限所以不会造成扎纱勒伤缆芯。改善了现有技术的副驱动在缆芯运动速度不稳定的时候容易勒伤或勒断套管的问题。
附图说明
19.图1是本实用新型的整体结构示意图。
20.图2是本实用新型去掉箱体后的结构示意图。
21.图3是本实用新型的剖面图。
22.图4是本实用新型工作原理示意图。
具体实施方式
23.下面结合说明书附图,对本技术进行清楚、完整地描述,基于本实用新型中的实施例,本领域普通技术人员在没有作出创造性劳动前提下所获得的所有其他实施例,都属于本实用新型保护的范围。
24.实施例1
25.一种便携缆芯退纱装置,箱盖2用四根螺栓固定在箱体1上,锥齿轮轴15通过轴承盖3和轴承20固定在箱盖2上,空心轴11的底部通过焊接的方式连接在箱体1的支柱上,出缆侧空心锥齿轮4、进缆侧空心锥齿轮13套在空心轴11上,出缆侧空心锥齿轮4与空心轴11之间安装出缆侧轴承16,进缆侧空心锥齿轮13与空心轴11之间安装进缆侧轴承19,出缆侧空心锥齿轮4、进缆侧空心锥齿轮13与锥齿轮轴15齿轮互相咬合,出缆侧空心锥齿轮4、进缆侧空心锥齿轮13同步转动,出缆侧空心锥齿轮4与进缆侧空心锥齿轮13远离齿轮咬合的一侧安装出缆侧挡圈17及进缆侧挡圈18,两个挡圈安装在空心轴11的沟槽里,通过两个挡圈限制两个空心锥齿轮轴向移动,出缆侧收纱盘5、进缆侧收纱盘9分别安装在出缆侧电机6、进缆侧电机10的转轴上。缆芯22穿过空心轴11,两种扎纱绕过出缆侧收纱盘5、进缆侧收纱盘9上,出缆侧收纱盘5、进缆侧收纱盘9运动的方向与缆芯22的运动方向平行。出缆侧空心锥齿轮4、进缆侧空心锥齿轮13同轴同速转动。通过锥齿轮啮合来实现正反转同步性极好。不会造成扎纱相互缠绕的情况。改善了现有技术采用两个单独的驱动分别控制正反转。同步性不好的问题。由于收纱盘运动的方向与缆芯的运动方向平行,解决了现有技术退纱盘转动方向与缆芯运动方向垂直,退纱点距离退纱盘超过一定距离后,退纱盘收不上来纱的问题。
26.实施例2
27.其他结构与实施1均相同,区别于出缆侧电机6、进缆侧电机10为小扭矩电机,出缆侧电机支架8、进缆侧电机支架12通过螺钉分别连接在出缆侧空心锥齿轮4、进缆侧空心锥齿轮13的一个平台上,出缆侧电机6、进缆侧电机10通过螺钉分别连接在出缆侧电机支架8、进缆侧电机支架12上,所述出缆侧空心锥齿轮4及所述进缆侧空心锥齿轮13另一个侧面平台上安装出缆侧电池盒7、进缆侧电池盒14,通过螺钉连接固定,两个电机和两个电池盒中间由导线连接。采用小电机带动收纱盘收纱的方式,当使用者的移动速度与设备不同步时,由于电机的扭矩有限所以不会造成扎纱勒伤缆芯。改善了现有技术的副驱动在缆芯运动速度不稳定的时候容易勒伤或勒断套管的问题。
28.使用方式说明:
29.如图2图4所示:缆芯22上面的扎纱一个是顺时针缠绕一个是逆时针缠绕,所以在退纱的时候需要两个装置沿不同方向转动才能同时卸下扎纱。还需将卸下的扎纱收回。
30.使用时将缆芯22穿过空心轴11,手动卸下几圈黄扎纱21后,将黄扎纱21缠绕在进缆侧收纱盘5上。手动卸下几圈紫扎纱23后将紫扎纱23缠绕在出缆侧收纱盘9上。将电动螺丝刀(或其他驱动设备)夹在锥齿轮轴15的上端。打开出缆侧电池盒7、进缆侧电池盒14的开关,并启动电动螺丝刀(或其他驱动设备)。使用者提着电动螺丝刀(或其他驱动设备)沿着缆芯的方向匀速走动就可以完成退纱。打开设备工作的时候出缆侧电机6、进缆侧电机10都朝着锥齿轮轴15的方向转动。这样就能保证被退下来的纱能被出缆侧收纱盘5、进缆侧收纱盘9及时收回。以免造成退下来的扎纱发生缠绕现象。
再多了解一些
本文用于企业家、创业者技术爱好者查询,结果仅供参考。