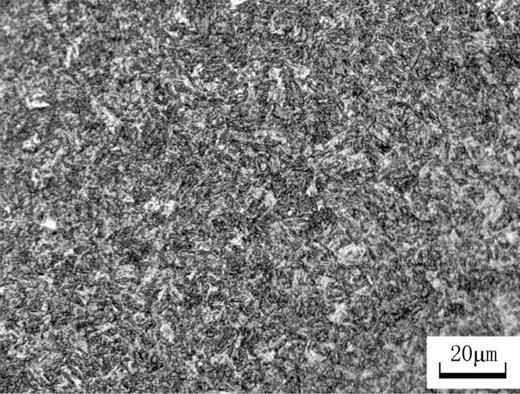
一种用csp生产抗拉强度为1800mpa级高塑韧性汽车结构件用钢及生产方法
技术领域
1.本发明涉及一种汽车用钢及生产方法,确切地属于一种抗拉强度为1800mpa级高塑韧性汽车结构件用钢及生产方法,其更适用于电动汽车的b级轿车结构件用钢。
背景技术:
2.随着汽车工业的发展,中国汽车市场出现了连续下滑现象。如2020年度,中国汽车产销量分别为2522.5万辆和2531.1万辆,产销量同比分别下降2.0%和1.9%。在汽车市场产销饱和的背景下,汽车质量提升与产业升级迫在眉睫,汽车制造逐渐向轻量化、智能化、网联化方向发展,因此对轻量化车身用超高强度材料提出了更高的要求。
3.目前世界范围内掀起了发展汽车用超高强度结构件用材料的研究高潮,主要分两类:一类是冷冲压成形超高强度汽车结构件,这类产品的设计主要是采用高合金含量钢铁材料,其是向钢中加入大量的合金元素,提高钢的淬透性的同时,提高奥氏体的室温稳定性,从而保证开发的钢具有超高强度和良好的成形性能。但是,这类钢的合金成本高、工艺复杂、制造过程困难、成材率低,且在零件制造过程中极易出现回弹、开裂、零件尺寸精度差等问题。另一类是在零件制造过程中采用合适的热处理工艺方式实现零件的高强化,这类零件用钢的合金含量较冷冲压成形零件用超高强度钢低,主要通过成形前或成形后的热处理工艺得到超高强度零件。但现有技术生产此类钢的强塑性较差,用来表征汽车用高强度零件用材成形能力及碰撞过程中吸收形变能大小的强塑积只有5~10gpa
·
%左右,不能满足汽车行业日益发展的车身轻量化及高碰撞安全与吸能性能的要求。
4.经检索:
5.中国专利公开号为cn 101381839b的文献,公开了《一种高强塑积合金钢及其热处理工艺》。该文献的高强塑积合金钢的化学成分百分含量为:c:0.03~0.05%,mn:30
±
0.5%,al:3
±
0.5%,si:3
±
0.5%,其余为铁;其需要加热到1100℃保温2~5小时,然后迅速投入水中淬火。所得工件的抗拉强度为650~700mpa,断后延伸率为55~70%,强塑积为35~49gpa
·
%。虽然此发明钢的强塑积较高,但是其合金含量也较高,尤其是锰含量达到了30%,同时其需要较长时间的热处理,其不仅工业化生产难度大,而且合金成本和能源消耗高,强度只有650~700mpa,其虽然强塑积较高,但是强度偏低,不能满足轻量化车身设计对高抗碰撞性和高吸能性能结构件的要求。
6.中国专利公开号为cn 107587052a的文献,公开了《一种汽车结构件用冷轧高强钢及其制造方法》。其主要成分的重量百分比为:c 0.06
‑
0.08%,mn 0.65
‑
0.95%,si≤0.05%,p≤0.015%,s≤0.015%,als 0.030
‑
0.055%,nb 0.025
‑
0.040%,ti 0.010
‑
0.030%。依次通过热轧轧制、酸洗冷连轧、连续退火、平整和拉矫,获得的高强度钢板屈服强度330
‑
400mpa,抗拉强度410
‑
500,pa,断后延伸率≥25.0%。该方法虽然能生产一种汽车结构件,但是由于其元素设计不合理,导致强度较低,不能满足汽车轻量化设计对超高强度零件的要求。
7.总之,虽然现有技术能够制造出汽车结构件,但是其强度及强塑积较低,不能满足轻量化车身设计对1800mpa级高抗碰撞性和高吸能性能结构件的要求。有的虽然通过大量的合金添加和长时间的热处理,能得到高强塑积的工件,但其强度较低、成本高、工业大批量生产困难,同样不能满足汽车轻量化设计对高抗碰撞性和高吸能性结构零件的要求。
8.众所周知,强度与延伸率及强塑积是成反向关系的,即强度越高,则延伸率及强塑积会降低,对汽车制造商来讲感到很矛盾,无法满足所用级别轿车结构件的要求。高强低用则会性价比低,生产成本高;反之安全性能的保障性又差。
技术实现要素:
9.本发明在于克服现有技术存在的不足,提供一种通过低的合金成分设计,匹配适合的组织调控工艺,实现不仅屈服强度在950~1250mpa,抗拉强度在1650~1950mpa,且伸长率≥10%,强塑积≥15gpa
·
%,从而满足电动汽车的b级轿车结构件高抗碰撞性能和碰撞吸能特性要求的高塑韧性汽车结构件用钢及生产方法。
10.实现上述目的的措施:
11.一种用csp生产抗拉强度为1800mpa级高塑韧性汽车结构件用钢,其化学成分及重量百分含量:c:0.28~0.32%,si:1.45~1.85%,mn:1.80~2.70%,p≤0.020%,s≤0.010%,als:0.012~0.080%,cr:0.41~0.55%,ti:0.015~0.085%,nb:0.046~0.055%,b:0.002~0.004%,n≤0.004%,其余为fe及不可避免的杂质;金相组织结构为:马氏体体积含量85~92%,贝氏体体积含量为2~5%,残余奥氏体体积含量为6~10%。
12.优选地:所述si的重量百分含量在1.51~1.85%。
13.优选地:所述mn的重量百分含量在1.91~2.70%。
14.优选地:所述cr的重量百分含量在0.47~0.55%。
15.优选地:所述nb的重量百分含量在0.051~0.055%。
16.优选地:所述ti的重量百分含量在0.026~0.85%。
17.一种用csp生产抗拉强度为1800mpa级高塑韧性汽车结构件用钢的生产方法,其步骤:
18.1)铁水脱硫,并控制s≤0.001%;
19.2)进行电炉或转炉冶炼及精炼;
20.3)进行连铸,控制中包钢水过热度在15~35℃,铸坯厚度在50~70mm,拉坯速度在3.0~5.0m/min;
21.4)对铸坯进行第一次除鳞,并控制除鳞水的压力不低于220bar;
22.5)对铸坯进行均热,控制铸坯出炉温度在1200~1230℃;
23.6)对铸坯进行第二次除鳞,并控制除鳞水压力不低于260bar;
24.7)进行轧制:并控制精轧出口厚度在0.80~4.0mm;控制第一、二道次压下率不低于50%;控制终轧温度在900~930℃;
25.8)层流冷却至卷取温度;
26.9)进行卷取,控制卷取温度在700~730℃;
27.10)直接开卷落料或酸洗后落料成所要制备的结构件的坯料;
28.11)对坯料进行加热,在加热速度为12~30℃/s下加热至820~900℃,并在此温度
下保温300~560s;
29.12)冲压成型:将被加热的坯料冲压成为所要制备的汽车结构件,其间,控制冷却速度在29~35℃/s,控制成型件在室温下金相组织结构为马氏体体积含量在85~92%,贝氏体体积含量在2~5%,残余奥氏体体积含量在6~10%;
30.13)进行零件表面的清理、切边、切孔。
31.优选地:所述坯料在加热速度为10~12℃/s下加热至850~873℃,并在此温度下保温395~600s。
32.优选地:所述冲压成型中控制冷却速度在36~44℃/s。
33.本发明中各元素及主要工艺的作用及机理
34.本发明之所以在三段保温式高温退火中:
35.c:碳对超高强度和多相组织的获得起关键性作用,碳含量及其在钢中的分布对最终产品的组织形态、类型和性能有较大影响,但是含量太高,在精轧后的冷却过程中易形成大量的贝氏体、马氏体等硬相,其含量愈高,强度愈高,从而造成塑性降低。所以在保证模压淬火处理强化的前提下,碳含量不易过高。故将其含量限定在0.28~0.32%范围。
36.si:硅有较强的固溶强化效果,可提高钢的强度,同时,硅能有效抑制碳化物形成,对碳元素在钢中的分布和状态起关键性作用,是钢兼具超高强度与高塑性的重要元素之一;同时,其能使钢在回火时硬度下降较慢,提高钢的回火稳定性及强度。所以,将其含量限定在1.45~1.85%范围,优选地含量在1.51~1.85%。
37.mn:锰起固溶强化作用,其能降低相变驱动力,使“c”曲线右移,提高钢的淬透性,扩大γ相区,另它可降低钢的ms点,故可保证在合适的冷却速度下得到马氏体。同时与一定的硅含量匹配加入钢中,能增强奥氏体的室温稳定性,是高强与高塑性匹配获得的重要元素,所以,将其含量限定在1.80~2.70%范围,优选地mn的含量在1.91~2.70%。
38.cr:铬能降低相变驱动力,也降低相变时碳化物的形核长大,所以提高钢的淬透性。另外,铬能提高钢的回火稳定性及抗高温氧化能力。所以,将其含量限定在0.41~0.55%范围。
39.b:硼是强烈提高淬透性元素,钢中加入微量的硼元素能显著提高钢的淬透性。但是其含量低于0.0005%,或者高于0.0050%,对提高淬透性的作用不明显。所以,为考虑生产实际及淬透性效果,将其含量限定在0.002~0.004%范围,优选地所述cr的含量在0.47~0.55%。
40.als,其在钢中起脱氧作用,应保证钢中有一定量的酸溶铝,否则不能发挥其效果,但过多的铝也会使钢中产生铝系夹杂,且不利于钢的冶炼和浇铸。同时钢中加入适量的铝可以消除钢中氮、氧原子对性能的不利影响。故将其含量限定在0.012~0.080%范围。
41.p:磷是钢中的有害元素,易引起铸坯中心偏析。在随后的热连轧加热过程中易偏聚到晶界,使钢的脆性显著增大。同时基于成本考虑且不影响钢的性能,将其含量控制在0.020%以下。
42.s:硫是非常有害的元素。钢中的硫常以锰的硫化物形态存在,这种硫化物夹杂会恶化钢的韧性,并造成性能的各向异性,因此,需将钢中硫含量控制得越低越好。基于对制造成本的考虑,将钢中硫含量控制在0.010%以下。
43.n:氮在加钛的钢中可与钛结合形成氮化钛,这种在高温下析出的第二相有利于强
化基体,并提高钢板的焊接性能。但是氮含量高于0.004%,氮与钛的溶度积较高,在高温时钢中就会形成颗粒粗大的氮化钛,严重损害钢的塑性和韧性;另外,较高的氮含量会使稳定氮元素所需的微合金化元素含量增加,从而增加成本。故将其含量控制在0.004%以下。
44.ti:钛是强c、n化物形成元素,钢中加入ti的目的是固定钢中的n元素,但是过量的ti会与c结合从而降低试验钢淬火后马氏体的硬度和强度。另外,钛的加入对钢的淬透性有一定的贡献。所以,将其含量限定在0.015~0.085%范围,优选地所述ti的含量在0.026~0.85%。
45.nb:铌是强c、n化物形成元素,能起到细化奥氏体晶粒的作用,钢中加入少量的铌可形成一定量的纳米级细小二相粒子,不仅能阻碍奥氏体晶粒长大,而且能提升钢的塑韧性,因此,其淬火后的马氏体板条尺寸较小,大大提高钢的强度与塑韧性。故将其含量均控制在0.046~0.055%之间,优选地所述nb的含量在0.051~0.055%。
46.本发明之所以控制第一、二道次压下率不低于50%,并控制终轧温度在900~930℃,是由于其可有效的增加畸变能,细化晶粒,同时匹配合适的轧制温度,控制晶粒的长大。
47.本发明之所以控制卷取温度在700~730℃,是由于其既可有效的获得均匀的组织和弥散分布的碳化物颗粒,而且可有效的控制钢卷的卷形,便于实现批量稳定制造。
48.本发明之所以对坯料在加热速度为12~30℃/s下加热至820~900℃,并在此温度下保温300~560s,优选地所述坯料在加热速度为10~12℃/s下加热至850~873℃,并在此温度下保温395~600s,是由于其可有效的保证钢中的各成分元素均匀分布在奥氏体上,为后续各相的调控提供有利条件。
49.本发明之所以在成型时控制冷却速度在29~35℃/s,优选地所述冲压成型中控制冷却速度在36~44℃/s,并使成型件在室温下金相组织结构为马氏体体积含量在85~92%,贝氏体体积含量在2~5%,残余奥氏体体积含量在6~10%,是由于其可有效的获得均匀的相分布和各相类型及其比例,为最终产品的高强塑积获得提供保证。
50.本发明与现有技术相比,不仅屈服强度≥980mpa,抗拉强度≥1750mpa,延伸率≥10%,还能使强塑积在17.9~22.3gpa
·
%,完全满足了电动汽车的b级轿车结构件高抗碰撞性能和碰撞吸能特性要求。
附图说明
51.图1为本发明金相组织图。
具体实施方式
52.下面对本发明予以详细描述:
53.表1为本发明各实施例与对比例的组分取值列表;
54.表2为本发明各实施例与对比例工艺参数取值;
55.表3为本发明各实施例与对比例力学性能检测结果列表。
56.本发明各实施例均按以下步骤生产:
57.1)铁水脱硫,并控制s≤0.001%;
58.2)进行电炉或转炉冶炼及精炼;
59.3)进行连铸,控制中包钢水过热度在15~35℃,铸坯厚度在50~70mm,拉坯速度在
3.0~5.0m/min;
60.4)对铸坯进行第一次除鳞,并控制除鳞水的压力不低于220bar;
61.5)对铸坯进行均热,控制铸坯出炉温度在1200~1230℃;
62.6)对铸坯进行第二次除鳞,并控制除鳞水压力不低于260bar;
63.7)进行轧制:并控制精轧出口厚度在0.80~4.0mm;控制第一、二道次压下率不低于50%;控制终轧温度在900~930℃;
64.8)层流冷却至卷取温度;
65.9)进行卷取,控制卷取温度在700~730℃;
66.10)直接开卷落料或酸洗后落料成所要制备的结构件的坯料;
67.11)对坯料进行加热,在加热速度为12~30℃/s下加热至820~900℃,并在此温度下保温300~560s;
68.12)冲压成型:将被加热的坯料冲压成为所要制备的汽车结构件,其间,控制冷却速度在29~35℃/s,控制成型件在室温下金相组织结构为马氏体体积含量在85~92%,贝氏体体积含量在2~5%,残余奥氏体体积含量在6~10%;
69.13)进行零件表面的清理、切边、切孔。
70.表1本发明各实施例及对比例的化学成分(wt.%)
[0071][0072]
表2本发明各实施例及对比例的主要工艺参数取值列表
[0073][0074]
表3本发明各实施例及对比例的的力学性能情况列表
[0075][0076][0077]
综上所述,本发明通过成分与工艺的匹配设计,成功实现了发明钢不仅具有较高的强度,而且具有高的强塑性,能够满足汽车轻量化车身设计对1800mpa级高抗碰撞性和高吸能性能结构件的要求,对于推进b级汽车轻量化及新能源的发展具有重大意义。
[0078]
本具体实施方式仅为最佳例举,并非对本发明技术方案的限制性实施。
再多了解一些
本文用于企业家、创业者技术爱好者查询,结果仅供参考。