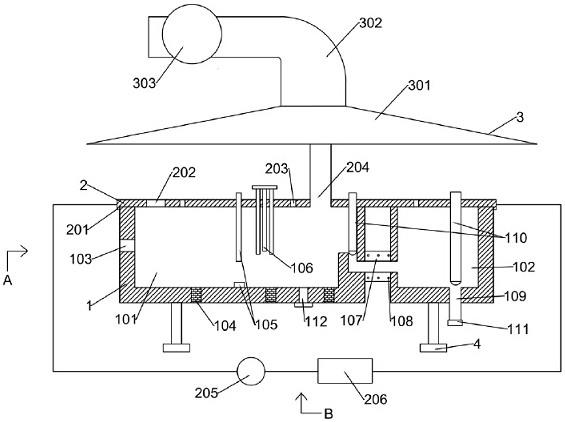
1.本发明涉及炼钢技术领域,具体是一种钢液连续在线精炼设备及生产工艺。
背景技术:
2.当前,合金脱氧,电极加热,白渣精炼,底吹搅拌等多种技术被应用于钢液精炼过程中,实现了钢液脱氧,脱硫,升温,合金化,去夹杂,均匀温度成分的要求,同时,随着钢铁生产技术的进步,初炼炉(包括转炉,电炉等)生产周期不断缩短,连铸机拉速不断提高。然而,由于传统的钢包精炼炉(lf)内动力学条件限制,钢渣接触面积小,钢液脱硫效率与钢液洁净度低,精炼时间长。同时,钢包精炼炉(lf)作为非连续生产工序,影响钢铁生产流程连续性与紧凑性。高效优质地保证精炼工序生产,实现炼钢工序,精炼工序与连铸工序的紧密衔接与流量匹配,开发新型钢液在线精炼设备及工艺,已成为当前发展的重要方向。
3.北京科技大学申请了一件申请号为202010406632.3,专利名称为《一种全连续超短电弧炉炼钢流程生产设备及工艺》的专利,该专利公开了一种稳定高效低成本高质量长寿命的全连续超短电弧炉炼钢流程生产设备及工艺,其中提出了钢液连续流动精炼的构思,然而,该专利提出的技术方案仍有不足,如:此技术方案中全连续超短电弧炉炼钢流程生产设备为整体设备,各单体设备通过刚性连接形成统一的生产整体,进而保证了设备的密闭性与系统的稳定运行,当精炼设备作为单体设备匹配传统的初炼炉(包括转炉,电炉等)与连铸机系统时,则无法保证其生产的连续性,难以实现系统的稳定运行,必须完善精炼设备的设计。
技术实现要素:
4.本发明的目的是克服现有钢液精炼设备及工艺的不足,提供一种钢液连续在线精炼设备及生产工艺,可以实现炼钢工序,精炼工序与连铸工序的紧密衔接与流量匹配,提高产量与产品质量。
5.一种钢液连续在线精炼设备(见图1,图2,图3),包括精炼床本体、精炼床盖、抽气除尘系统、液压倾动系统组成,本设备可以实现渣钢逆流,在冶炼过程中动态调节生产工艺,保证终点钢液达到合适的成分温度;所述精炼床本体由耐火材料砌筑,包括精炼段、存储段、出渣孔、底吹元件、直流电极和/或交流电极、、连接通道、感应线圈、出钢水口、塞棒、滑动水口、备用出钢水口;所述精炼段为钢液进口端,所述存储段为钢液出口段,所述连接通道连接所述精炼段与所述存储段,所述出渣孔位于精炼段壁面,所述备用出钢水口位于精炼段底部,所述出钢水口位于存储段底部,初炼钢液在精炼床本体中与精炼熔渣逆向流动,利用所述底吹元件喷吹搅拌,可选的,利用所述直流电极和/或交流电极加热钢液,完成钢液精炼;精炼完成的钢液,通过所述连接通道,利用所述感应线圈进行保温加热,进入存储段,利用所述塞棒控制连接通道中钢液的流速,利用所述塞棒或所述滑动水口调整出钢水口中的钢液流速;精炼段底部设置底吹透气元件,精炼段适宜位置设置直流电极和/或交流电极。
6.进一步的,所述精炼床盖为水冷结构,包括定位凹槽、加料口、孔道、烟道、循环泵与散热器,所述定位凹槽与所述精炼床本体上端边缘匹配,可保证精炼床盖与精炼床本体的相对固定;所述加料口、孔道与烟道竖向贯通所述精炼床盖,加料口位于精炼床盖靠近精炼段一端,孔道分布于精炼床盖适宜位置,布置5
‑
15个,烟道位于精炼段接近连接通道处;所述循环泵与散热器位于所述精炼床盖的水冷回路上,避免设备过热损坏;所述精炼床盖为水冷结构,下部具有定位凹槽与精炼床本体相接;所述精炼床盖开有加料口及若干孔道,能向其中插入加料溜槽、加料管、测温取样设备、直流电极和/或交流电极;烟道位于精炼段接近连接通道处。
7.进一步的,所述精炼床盖上方设有抽气除尘系统,包括罩盖、抽气烟道与风机,所述罩盖完全覆盖精炼床盖,通过所述抽气烟道与所述风机连接,在冶炼过程中不断通过风机抽取设备中通过加料口,孔道及烟道逸出的烟气。
8.进一步的,所述液压倾动系统位于精炼床本体底部,包括4
‑
16组液压件,在冶炼过程中,根据设备内钢液面与渣液面的高度变化,动态调整设备的空间位置,进行精炼床本体的倾动,实现对精炼床空间位置调节,保证生产稳定运行。
9.本发明还提供了一种钢液连续在线精炼生产工艺,利用上述的钢液连续在线精炼设备,初炼钢液通过加料口连续或间断加入所述钢液连续在线精炼设备中,通过塞棒控制连接通道中钢液流速,进入存储段的钢液通过由塞棒和/或滑动水口控制开度的出钢水口流出;在冶炼过程中,所述钢液连续在线精炼设备中始终保持一定量的钢液,当设备中钢液面较低时,调整连接通道中的钢水流速,避免熔渣流入存储段,出钢水口处的钢液流速匹配连铸机拉速。
10.进一步的,在冶炼过程中,通过孔道向设备中加入合金、脱氧剂、精炼渣形成熔渣,调整精炼床本体倾动,使得液态熔渣通过出渣孔排出,形成渣钢逆流状态,在此过程中进行钢液脱氧、脱硫及合金化,实现成分微调;通过感应线圈和/或直流电极和/或交流电极对流动钢液进行加热。特别的,在冶炼过程中,利用测温取样设备连续或间断的测量钢液在不同位置的温度成分,通过数据反馈实时调节精练生产工艺,保证钢液达到符合出钢要求的成分与温度。
11.进一步的,在冶炼过程中,利用所述底吹元件对设备中的钢液进行底吹搅拌,优化设备中冶金反应动力学条件,在设备内部实现微正压,避免空气渗入,保证设备内部还原性气氛;利用所述抽气除尘系统,抽取设备中通过加料口、孔道及烟道逸出的烟气,避免大气污染;所述出钢水口直接与连铸系统中间包相连接,避免了运输及倒包过程产生的温降与钢液增氧增氮。
12.进一步的,所述一种钢液连续在线精炼设备及生产工艺在正常生产时保持所述备用出钢水口闭合,在停炉维修时打开备用出钢水口出尽钢液。
13.进一步的,所述钢液连续在线精炼设备与连铸系统呈上下位布置,厂房高度比炼钢厂厂房高度高5
‑
20m;匹配公称容量为30
‑
300t的转炉或电弧炉。
14.本发明的有益效果为: a) 本发明包括精炼床本体、精炼床盖、抽气除尘系统、液压倾动系统四部分,可以实现渣钢逆流,设备内部保持微正压,避免空气渗入,保证设备内部还原性环境,形成良好的反应条件,根据生产状况动态调整冶炼工艺,保证终点钢液达到合适的成分温度。
[0015] b) 本发明可与连铸系统直接连接,实现精炼工序与连铸工序的一体化操作,实现炼钢工序,精炼工序与连铸工序的紧密衔接与流量匹配,提高钢铁生产流程的连续性与紧凑性,避免了运输及倒包过程产生的温降与钢液增氧增氮。
[0016] c) 利用本发明设备匹配炼钢工序与连铸工序可实现80小时以上连续生产,较传统工艺提高产量10%以上,铸坯中有害元素[s]、[o]、[n]、[h]等含量满足优质钢材需求。
附图说明
[0017]
图1所示为本发明实施一种钢液连续在线精炼设备纵截面结构示意图。
[0018]
图2所示为图1中b方向的剖视示意图。
[0019]
图3所示为图1中a方向的剖视示意图。
[0020]
其中:1
‑
精炼床本体;101
‑
精炼段;102
‑
存储段;103
‑
出渣孔;104
‑
底吹元件;105
‑
直流电极;106
‑
交流电极;107
‑
连接通道;108
‑
感应线圈;109
‑
出钢水口;110
‑
塞棒;111
‑
滑动水口;112
‑
备用出钢水口;2
‑
精炼床盖;201
‑
定位凹槽;202
‑
加料口;203
‑
孔道;204
‑
烟道;205
‑
循环泵;206
‑
散热器;3
‑
抽气除尘系统;301
‑
罩盖;302
‑
抽气烟道;303
‑
风机;4
‑
液压倾动系统。
具体实施方式
[0021]
一种钢液连续在线精炼设备(见图1,图2,图3),包括精炼床本体1,精炼床盖2、抽气除尘系统3以及液压倾动系统4。
[0022]
精炼床本体1包括精炼段101、存储段102、出渣孔103、底吹元件104、直流电极105、交流电极106、连接通道107、感应线圈108、出钢水口109、塞棒110、滑动水口111、备用出钢水口112;精炼段101为钢液进口端,存储段102为钢液出口段,连接通道107连接精炼段101与存储段102,出渣孔103位于精炼段101壁面,备用出钢水口112位于精炼段101底部,出钢水口109位于存储段102底部,初炼钢液在精炼床本体1中与精炼熔渣逆向流动,利用底吹元件104喷吹搅拌,直流电极105和/或交流电极106加热钢液,完成钢液精炼;精炼完成的钢液,通过连接通道107,利用感应线圈108进行保温加热,进入存储段102,利用塞棒110控制连接通道107中钢液的流速,可选的,利用塞棒110或滑动水口111调整出钢水口109中的钢液流速。
[0023]
精炼床盖2为水冷结构,包括定位凹槽201、加料口202、孔道203、烟道204、循环泵205与散热器206,定位凹槽201与精炼床本体1上端边缘匹配,可保证精炼床盖2与精炼床本体1的相对固定;加料口202、孔道203与烟道204竖向贯通精炼床盖2,加料口202位于精炼床盖2靠近精炼段101一端,孔道203分布于精炼床盖2适宜位置,布置5
‑
15个,烟道204位于精炼段101末端接近连接通道107处;循环泵205与散热器206位于精炼床盖2的水冷回路上,避免设备过热损坏。
[0024]
精炼床盖2上方设有抽气除尘系统3,包括罩盖301、抽气烟道302与风机303,罩盖301完全覆盖精炼床盖,在冶炼过程中使用风机303不断通过抽气烟道302抽取设备中通过加料口202、孔道203及烟道204逸出的烟气。
[0025]
液压倾动系统4位于精炼床本体1底部,包括4
‑
16组液压件,在冶炼过程中,根据设备内钢液面与渣液面的高度变化,动态调整设备的空间位置,进行精炼床本体1的倾动。
[0026]
下文将结合具体附图详细描述本发明具体实施例。应当注意的是,下述实施例中描述的技术特征或者技术特征的组合不应当被认为是孤立的,它们可以被相互组合从而达到更好的技术效果。在下述实施例的附图中,各附图所出现的相同标号代表相同的特征或者部件,可应用于不同实施例中。
[0027]
实施例1在本实施例中,本发明工艺应用于本发明实施一种公称容量为150t钢液连续在线精炼设备进行冶炼生产,本设备匹配1台100t转炉及1套2机2流200
×
200mm方坯连铸机:具体工艺为:使用钢包将初炼钢液由转炉工位转运到精炼工位,通过加料口202将钢液由钢包加入钢液在线连续精炼设备中,通过孔道203向精炼段101中加入合金,脱氧剂,精炼渣形成熔渣,倾动精炼床本体1,使得液态熔渣通过出渣孔103排出,实现渣钢逆流,进行钢液脱氧,脱硫及合金化,通过感应线圈108和/或直流电极105和/或交流电极106对钢液进行加热。通过控制连接通道107开度的塞棒110控制钢液由精炼段101进入存储段102的流速,进入存储段102的钢液通过由塞棒110和/或滑动水口111控制开度的出钢水口109流出。设备中始终保持有50t左右的钢液,出钢水口109处的钢液流速匹配连铸机拉速。
[0028]
在本实施方案中,通过孔道203插入测温取样设备,连续或间断的测量钢液在不同位置的温度成分,通过数据反馈实时调节精练生产工艺,保证钢液达到符合出钢要求的成分与温度。
[0029]
在本实施方案中,利用底吹元件104对设备中的钢液进行底吹搅拌,优化设备中冶金反应的动力学条件,在设备内部实现微正压,避免空气渗入,保证设备内部还原性气氛;利用抽气除尘系统3,抽取设备中通过加料口202、孔道203及烟道204逸出的烟气,避免大气污染;出钢水口109直接与连铸系统中间包相连接,避免了运输及倒包过程产生的温降与钢液增氧增氮。
[0030]
采用上述工艺后,钢液保持100小时连续生产不断流浇注,减少了冶炼过程中的能量、时间损失;产量较传统流程提高15%,铸坯中的有害元素 [s]、[o]、[n]、[h]等含量满足优质钢材需求。
[0031]
实施例2在本实施例中,本发明工艺应用于本发明实施一种公称容量为120t钢液连续在线精炼设备进行冶炼生产,本设备匹配2台70t电弧炉及1套3机3流200
×
200mm方坯连铸机:具体工艺为:使用钢包将初炼钢液由电弧炉工位转运到精炼工位,通过加料口202将钢液由钢包加入钢液在线连续精炼设备中,通过孔道203向精炼段101中加入合金,脱氧剂,精炼渣形成熔渣,倾动精炼床本体1,使得液态熔渣通过出渣孔103排出,实现渣钢逆流,进行钢液脱氧,脱硫及合金化,通过感应线圈108和/或直流电极105对钢液进行加热。通过控制连接通道107开度的塞棒110控制钢液由精炼段101进入存储段102的流速,进入存储段102的钢液通过由塞棒110和/或滑动水口111控制开度的出钢水口109流出。设备中始终保持有30t左右的钢液,出钢水口109处的钢液流速匹配连铸机拉速。
[0032]
在本实施方案中,通过孔道203插入测温取样设备,连续或间断的测量钢液在不同位置的温度成分,通过数据反馈实时调节精练生产工艺,保证钢液达到符合出钢要求的成
分与温度。
[0033]
在本实施方案中,利用底吹元件104对设备中的钢液进行底吹搅拌,优化设备中冶金反应的动力学条件,在设备内部实现微正压,避免空气渗入,保证设备内部还原性气氛;利用抽气除尘系统3,抽取设备中通过加料口202、孔道203及烟道204逸出的烟气,避免大气污染;出钢水口109直接与连铸系统中间包相连接,避免了运输及倒包过程产生的温降与钢液增氧增氮。
[0034]
采用上述工艺后,钢液保持120小时连续生产不断流浇注,减少了冶炼过程中的能量、时间损失;产量较传统流程提高10%,铸坯中的有害元素 [s]、[o]、[n]、[h]等含量满足优质钢材需求。
[0035]
在本发明的描述中,需要理解的是,术语“上”,“下”,“前”,“后”,“竖直”,“水平”,“底”,“顶”,“内”,“外”等指示的方向和位置关系为基于附图所示的方向或位置关系,仅是为了便于描述本发明,而不是指示或暗示所指的装置或元件必须具有特定的方位,以特定的方位构造和操作,因此不能理解为对本发明的限制。
[0036]
本文虽然已经给出了本发明的实施例,但是本领域的技术人员应当理解,在不脱离本发明精神的情况下,可以对本文的实施例进行改变。上述实施例只是示例性的,不应以本文的实施例作为本发明权利范围的限定。
再多了解一些
本文用于企业家、创业者技术爱好者查询,结果仅供参考。