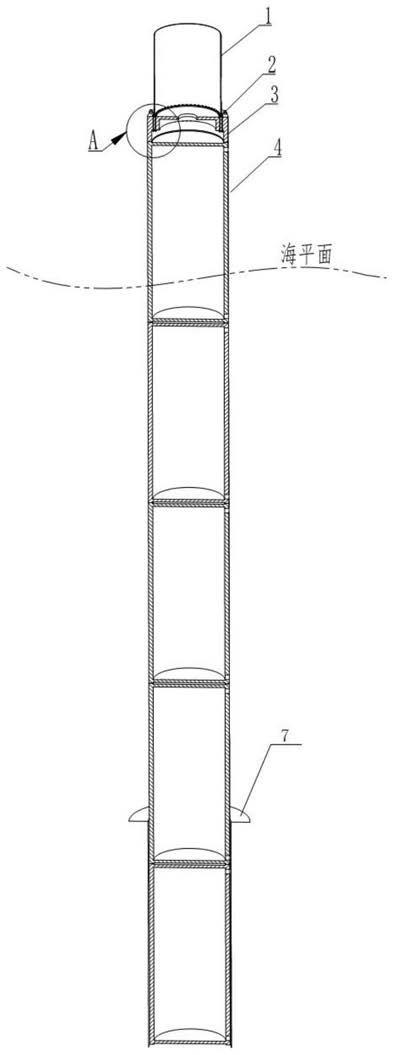
1.本发明涉及海上风力发电技术领域,具体涉及一种海上混凝土单桩基础、 混凝土单桩基础的安装方法以及混凝土单桩基础海上运输施工的方法。
背景技术:
2.目前海上固定式基础方案有单桩基础、多桩基础、导管架基础、重力式 基础、吸力筒基础等多种类型,其中单桩基础以其结构型式简单、制造工艺 成熟及施工方便、造价相对其他基础型式低等优点,成为海上风电基础的主 要形式,据统计单桩基础所占比例在65%以上。
3.目前现有的钢制单桩通常采用的是钢板卷制,具有直径大、重量大(500 —2400吨)等特点。近期报道国内超大型单桩基础直径8.7米,长度100米, 最大板厚90毫米,单体重量1740吨。
4.目前的超大单桩原材料为合金钢板,如果重量到2000吨的用钢量,成本 已很高。如何降低单桩基础成本成为研究的方向,减壁厚和增加直径受到径 厚比及制造限制。
5.对单桩设计来说,直径和壁厚的比值在90到120的范围内。如果管壁过 薄,在打桩过程中很容易局部屈曲导致爆桩。
6.超厚钢板卷制、焊接、运输和吊装施工都很困难。如2000吨的单桩在加 工、储存一般会放到滚轮上,当壁厚变得越来越薄时,将会导致应力集中, 造成塑性变形,损伤单桩。当管径很大时,自重也有可能压垮它,使它产生 很大的变形。另外焊接时要把两个直径很大o型的钢筒焊接起来是很困难的。
7.超大单桩重量大,对吊装船能力要求也高,可能需要双1500吨起重机(具 有3000吨的起重能力),或2000吨最先进吊机和安装船。
8.综上所述,目前的超大单桩用钢量巨大,生产制造、运输、吊装等都很 困难,导致超大单桩经济性受到其他基础形式的挑战。
技术实现要素:
9.本发明提出了一种混凝土单桩基础及其安装、施工方法,采用预应力混 凝土大直径单桩代替传统钢制单桩,降低超大钢制单桩的成本,并通过安装、 施工方法改善了单桩基础的安装及施工难度,以便继续在深海及大容量机组 上发挥单桩基础优势。
10.为了达到上述目的,本发明提出了一种混凝土单桩基础,包含:
11.混凝土桩,所述混凝土桩构成所述混凝土单桩基础的主体;
12.转换段,所述转换段通过预应力索、灌浆固定设置在所述混凝土桩的顶 部,用于连接风力发电机塔架;
13.所述混凝土桩包含若干个沿所述风力发电机塔架的高度方向固定连接的 预制单元,相邻两个预制单元间密封设置。
14.进一步地,所述预制单元为两端封闭的中空结构,所述预制单元的侧壁 上设有两
个排气孔;位于混凝土桩顶端的排气孔安装有排气阀,位于混凝土 桩底端的排气孔运输过程中封堵,混凝土桩上的其余的排气孔联通。
15.进一步地,若干个所述预制单元叠加设置,并通过预应力索固定连接; 所述预制单元的侧壁内均匀设置有若干个第一安装孔道,以便安装预应力索。
16.进一步地,所述转换段通过预应力索与所述混凝土桩固定连接;所述转 换段的侧壁内均匀设置有若干个第二安装孔道,所述第二安装孔道的数量及 尺寸与所述预制单元上的第一安装孔道的数量及尺寸相匹配;所述预应力索 依次穿过所述转换段的第二安装孔道及各个预制单元的第一安装孔道,将所 述转换段及所述混凝土桩连接为一个整体。
17.进一步地,所述预应力索的两端分别安装有上锚具及下锚具。
18.进一步地,所述预制单元为圆柱体或多边形体。
19.进一步地,所述转换段通过锚栓与风力发电机塔架连接。
20.进一步地,所述混凝土单桩基础还包含连接段,所述连接段通过预应力 索固定在所述混凝土桩的底部。
21.进一步地,所述连接段包含:环壁、与所述环壁固定连接的法兰,以及 固定设置在所述环壁及所述法兰之间的若干个加强肋;所述法兰上均匀设置 有若干个第一安装孔,所述第一安装孔的数量及尺寸与所述预制单元上的第 一安装孔道的数量及尺寸相匹配;所述预应力索依次穿过所述转换段的第二 安装孔道、各个预制单元的第一安装孔道以及法兰上的第一安装孔,将所述 转换段、混凝土桩及所述连接段连接为一个整体。
22.本发明还提出了一种混凝土单桩基础的安装方法,包含以下步骤:
23.将转换段定位放置到v形槽安装工装中,再依序放入若干个预制单元及 连接段;
24.依次调整各个预制单元、连接段的角度及位置,使得转换段上的第二安 装孔道以及各个预制单元上的第一安装孔道、连接段上的第一安装孔相互对 齐;连接段与预制单元、各个预制单元间以及预制单元与转换段间紧密贴合, 并在接触面上涂抹密封胶;
25.采用预应力索依次贯穿第一安装孔及各个第一安装孔道、第二安装孔道, 在预应力索两端安装上锚具及下锚具后张拉预应力索;
26.对预应力索进行张拉预紧操作后,向各个第一安装孔道、第二安装孔道 及第一安装孔内灌浆,以将所述转换段、各个预制单元及连接段固定连接为 混凝土单桩基础;
27.在位于混凝土单桩基础顶端的排气孔上安装排气阀,使位于混凝土单桩 基础底端的排气孔封堵,其余排气孔联通。
28.进一步地,所述的v形槽安装工装包含两个倾斜侧面,每个所述倾斜侧 面具有呈现凹凸状的表面,两个相邻的凸出状表面之间设置一个凹槽;两个 所述倾斜侧面的凹凸状表面彼此相对设置。
29.本发明又提出了一种混凝土单桩基础的施工方法,包含以下步骤:
30.使混凝土单桩基础漂浮在海面上,并拖运到机位点;
31.打开位于混凝土单桩基础底端封堵的排气孔,吊起混凝土单桩基础的顶 端使其下沉,并通过排气阀控制混凝土单桩基础的排气,以控制混凝土单桩 基础的浮力和下沉速度;
32.待混凝土单桩基础插入到海底中,全开排气阀,海水完全填充混凝土单 桩基础;
33.灌浆操作,将混凝土单桩基础固定在海底。
34.本发明具有以下优势:
35.本发明采用混凝土单桩基础替代传统的钢制单桩基础,节省钢材,降低 了超大钢制单桩基础的成本。混凝土单桩基础包含若干个预制单元,预制单 元可使用模具浇筑而成,制作容易,不需要使用大型设备。
36.本发明通过v形槽安装工装安装混凝土单桩基础,施工简单,不需要垂 直吊装施工,也无需高空作业,操作安全、方便。
37.本发明利用混凝土单桩基础自身浮力在海面上漂浮拖动,解决了超大重 量单桩基础的运输及安装难题,不需要大型运输、吊装船,操作容易,运输 及施工费用较低。
附图说明
38.图1为非打入型混凝土单桩基础固定在海底的示意图。
39.图2为打入型混凝土单桩基础固定在海底的示意图。
40.图3为非打入型混凝土单桩基础的结构示意图。
41.图4为图1中a处的局部放大图。
42.图5打入型混凝土单桩基础的结构示意图。
43.图6为图2中c处的局部放大图。
44.图7为v形槽安装工装的结构示意图。
45.图8为混凝土单桩基础的安装示意图。
46.图9为混凝土单桩基础的施工示意图。
具体实施方式
47.以下结合附图和具体实施例对本发明作进一步详细说明。根据下面说明 和权利要求书,本发明的优点和特征将更清楚。需说明的是,附图均采用非 常简化的形式且均使用非精准的比率,仅用以方便、明晰地辅助说明本发明 实施例的目的。
48.本发明提供了一种混凝土单桩基础,采用预应力混凝土大直径单桩基础 替代传统的钢制单桩基础。混凝土原材料造价低,一般为钢板造价的50%, 采用混凝土制造大直径单桩基础极大降低了大直径单桩基础的制造成本。传 统的钢制单桩基础需要采用大型设备,如卷板设备等,并需要钢板焊接。本 发明的混凝土单桩基础施工容易,仅需要使用模具浇筑而成,不需要大型设 备。而且,混凝土环径厚比小,刚度大,运输移动变形小,阻尼比大,减振 性能优越,可以不考虑屈曲问题。
49.根据单桩基础是否直接打入海底,将混凝土单桩基础划分为两种结构: 非打入型混凝土单桩基础与打入型混凝土单桩基础。如图1所示,非打入型 混凝土单桩基础施工时,先在海底钻孔,再将非打入型混凝土单桩基础放置 在海底孔7内,最后在混凝土单桩基础与海底孔7的侧隙内灌浆固定。如图 2所示,打入型混凝土单桩基础施工时,预先在海底打入一段钢桩6,再将打 入型混凝土单桩基础与钢桩6灌浆固定连接。
50.图3所示,为非打入型混凝土单桩基础的结构示意图。所述非打入型混 凝土单桩基础包含:
51.作为混凝土单桩基础的主体的混凝土桩4;
52.通过预应力索42、灌浆固定在所述混凝土桩4顶部的转换段3,所述转 换段3用于
连接风力发电机塔架1。
53.所述混凝土桩4包含多个通过预应力索42固定连接的预制单元41,多 个所述预制单元41在塔架的高度方向上叠加设置,且相邻两个预制单元41 间通过密封环氧胶密封设置。所述预制单元41为两端封闭的中空结构,可选 地,所述预制单元41采用圆柱体或多边形体。优选地,所述预制单元41采 用圆柱体。所述预制单元41的侧壁上设有至少两个排气孔45,位于混凝土 桩4顶端的排气孔安装有排气阀9,位于混凝土桩4底端的排气孔在运输时 封堵,相邻两个预制单元41的排气孔联通。本实施例中,预制单元41的侧 壁上设有两个排气孔45,位于混凝土桩4顶端的排气孔45安装有排气阀9, 位于混凝土桩4底端的排气孔45在运输过程中封堵,两个相邻预制单元41 中的相邻的两个排气孔45联通。所述预制单元41的侧壁内还设置有若干个 第一安装孔道46,以便安装预应力索42,以及后续灌浆。
54.所述转换段3的侧壁内也设置有若干个第二安装孔道,所述第二安装孔 道的数量与尺寸与所述预制单元41上的第一安装孔道46相匹配。所述预应 力索42依次穿过转换段3上的第二安装孔道、混凝土桩4中的各个预制单元 41上的第一安装孔道46,将所述转换段3与混凝土桩4连接为一个整体。所 述预应力索42的两端分别安装有上锚具43及下锚具44,以便张拉预紧预应 力索42。
55.所述转换段3为上端中间设有人孔,下端开放的混凝土结构,其侧壁上 还设有多个固定孔道。所述转换段3通过锚栓2与风力发电机的塔架1连接, 所述锚栓2位于所述转换段3内。
56.如图4所示为锚栓2与转换段3、塔架1的连接示意图。所述锚栓2包 含上锚板24、下锚板23以及固定在两者之间的若干个锚杆22,所述上锚板 24设置在所述转换段3的上端,所述锚杆22设置在所述转换段3的固定孔 道内,所述下锚板23位于所述转换段3内部。所述上锚杆22的数量及尺寸 与所述固定孔道的数量及尺寸相匹配。所述锚杆22依次穿过风力发电机塔架 1塔底的t法兰12、上锚板24、转换段3的固定孔道以及下锚板23,并通 过上下螺母21,将转换段3与风力发电机塔架1固定连接为一个整体。
57.如图2、图5所示,所述打入型混凝土单桩基础包含:
58.混凝土桩4;
59.固定在所述混凝土桩4顶部的转换段3,所述转换段3用于连接风力发 电机塔架1;以及
60.通过预应力索42固定在所述混凝土桩4底部的连接段5,所述连接段5 用于固定连接钢桩6。
61.打入型混凝土单桩基础的上部结构,即混凝土桩4与转换段3,与非打 入型混凝土单桩基础的结构相同。
62.所述连接段5包含:环壁53、与所述环壁53固定连接的法兰51,以及 固定设置在所述环壁53及所述法兰51之间的若干个加强肋52;所述法兰51 上均匀设置有若干个第一安装孔54,所述预应力索42依次穿过所述转换段3 的第二安装孔道、各个预制单元41的第一安装孔道46以及法兰51上的第一 安装孔54,将所述转换段3、混凝土桩4及所述连接段5连接为一个整体。
63.所述连接段5通过灌浆与所述钢桩6固定连接。如图6所示为连接段5 与钢桩6的连接示意图,所述钢桩6包含桩壁61以及固定在桩壁61底部的 法兰环62。所述桩壁61的尺寸
大于所述连接段5的环壁53的尺寸,所述法 兰环62用于支撑并定位所述连接段5的环壁53。所述连接段5安装在所述 钢桩6内,然后在所述连接段5的环壁53与所述钢桩6的桩壁61间的侧隙 内灌浆,固定连接所述连接段5与所述钢桩6。
64.由于海上情况恶劣,不可能按照传统的混凝土结构在机位点长时间现场 施工,因此,本发明提出了一种在岸上施工的混凝土单桩基础的安装方法, 以解决海上混凝土单桩基础安装难题,同时降低安装成本。
65.所述混凝土单桩基础的安装方法,通过v形槽安装工装8实现。如图7 所示,所述v形槽安装工装8包含两个倾斜侧面,每个倾斜面具有呈现凹凸 状的表面,两个相邻的凸出状表面之间设置一个凹槽81,所述两个倾斜侧面 的凹凸状表面彼此相对设置,即两个倾斜面的凸出状表面相对设置,凹槽也 相对设置。混凝土单桩基础在v形槽安装工装8上安装时,通过吊带将所述 转换段3、预制单元41或连接段5吊装到v形槽安装工装8内,并通过吊带 拖动所述转换段3、预制单元41或连接段5,以调整转换段3、预制单元41 或连接段5在v形槽安装工装8内的位置。在v形槽安装工装8的倾斜侧面 上设置面积较大的凸出状表面用于和v形槽安装工装8的底面共同支撑转换 段3、预制单元41和连接段5,而设置面积较小的凹槽81,使得v形槽安装 工装内有空隙空间便于吊带的安装和拆除。所述v形槽安装工装8制作时可 以为水平,也可斜切一定角度。
66.如图8所示为混凝土单桩基础的安装示意图,非打入型混凝土单桩基础 的安装方法,具体包含以下步骤:
67.a、将转换段3定位放置到v形槽安装工装8中;
68.b、放入第一个预制单元,转动第一个预制单元的角度,使其上的第一 安装孔道46与转换段3的第二安装孔道对齐,调整第一个预制单元的位置, 使其与转换段3紧密结合,第一个预制单元与转换段3的接触面涂抹密封胶 密封;具体地,第一个预制单元可直接放入v形槽安装工装8中,转动预制 单元的角度,使得第一个预制单元的第一安装孔道46与转换段3的第二安装 孔道对齐,第一个预制单元与转换段3的接触面涂抹密封胶密封,轴向拖动 预制单元,使得第一个预制单元与转换段3紧密结合;
69.c、放入第二个预制单元,转动第二个预制单元的角度,使得第二个预 制单元的第一安装孔道46与第一个预制单元的第一安装孔道46对齐;调整 第二个预制单元的位置,使得第二个预制单元与第一个预制单元紧密结合, 第二个预制单元与第一个预制单元的接触面涂抹密封胶密封;一般情况下, 预制单元41的安装精度满足作业要求,若误差较大,可在v形槽安装工装8 的v形侧面上加垫片;
70.d、重复上述操作,直至完成所有预制单元41的摆放;
71.e、预应力索42依次穿过转换段3的第二安装孔道及各个预制单元41 的第一安装孔道46,然后在预应力索42的两端分别安装上、下锚具44后, 张拉预紧预应力索42;
72.f、沿着预应力索42向各个第二安装孔道及第一安装孔道46灌浆,将 连接段5、各个预制单元41固定连接为一个整体;
73.h、相邻两个预制单元41上的相邻的两个排气孔45联通,并在靠近转 换段3的排气孔45上安装排气阀9,封堵靠近连接段5的排气孔45;完成非 打入型混凝土单桩基础的安装。
74.采用v形槽安装工装8在岸上安装打入型混凝土单桩基础的方法,与非 打入型混
凝土单桩基础的安装方法大体相同,区别点在于:在完成转换段3 及各个预制单元41的摆放后,在v形槽安装工装8中放入连接段5,转动连 接段5的角度使其上的第一安装孔54与相邻预制单元41的第一安装孔道46 对齐,调整连接段5的位置使其与相邻的预制单元41紧密贴合,连接段5 与相邻的预制单元41的接触面涂抹密封胶密封;紧接着,预应力索42依次 穿过转换段3的第二安装孔道、各个预制单元41的第一安装孔道46以及连 接段5的第一安装孔54,然后在预应力索42的两端分别安装上、下锚具44, 张拉预应力索42;其次,沿着预应力索42向各个第二安装孔道、第一安装 孔道46及第一安装孔54灌浆,将连接段5、各个预制单元41、转换段3固 定连接为一个整体。
75.采用v形槽安装工装8安装混凝土单桩基础,施工简单方便,不需要大 型吊车,作业面仅为预制单元41的直径高度,无需进行空中作业,降低施工 要求,节约了安装成本。而且,v形槽安装工装8制作时,已保证了v形槽 安装工装8的直线度和位置精度,转换段3、预制单元41以及连接段5放入 在v形槽安装工装8中,即可保证直线度,同轴度等。
76.由于混凝土单桩基础比传统钢桩单桩基础中,一般为钢桩单桩基础重量 的3
‑
4倍。若按照传统的施工方式将混凝土单桩基础定位投入到海内,则需 要的吊装设备及成本将急剧上升,甚至无法完成混凝土单桩基础的施工。因 此,本发明提出了一种混凝土单桩基础的施工方法,利用混凝土单桩基础自 身浮力,漂浮拖动混凝土单桩基础到预定施工机位,吊装混凝土单桩基础时, 通过控制混凝土单桩基础的浮力大小,控制混凝土单桩基础下沉的速度,混 凝土安装基础下沉至海底后固定,完成混凝土单桩基础在预定海域的施工。
77.如图9所示为混凝土单桩基础的施工示意图,所述混凝土单桩基础的施 工方法,具体包含以下步骤:
78.a、使混凝土单桩基础漂浮在海面上,并拖运到机位点;具体地, 将混凝土单桩基础从v形槽安装工装8中拖动到海面,此时,混凝 土单桩基础上的排气孔45均密封,依靠混凝土自身产生浮力漂浮于 海面上,并拖运到机位点;
79.b、打开位于混凝土单桩基础底端封堵的排气孔45,吊起混凝土 单桩基础的顶端使其下沉,通过排气阀9控制混凝土单桩基础的排气, 以控制混凝土单桩基础的浮力和下沉速度;具体地,混凝土单桩基础 拖动到机位点后,将混凝土单桩基础底端的排气孔45打开,吊装船 吊起混凝土单桩技术的上端,位于混凝土单桩基础底端的排气孔45 开始进水,混凝土单桩基础开始下沉;混凝土单桩基础内的空气经过
80.c、待混凝土单桩基础插入到海底中,全开排气阀9,海水完全 填充混凝土单桩基础;具体地,混凝土单桩基础插入到海底内的钢桩 6或海底孔7后,全开排气阀9,海水完全填充混凝土单桩基础;
81.d、灌浆操作,将混凝土单桩基础固定在海底;具体地,在混凝土单桩基 础与钢桩6间的侧隙内灌浆,或者,混凝土单桩基础与海底孔7的侧隙内灌 浆,将混凝体单桩基础固定在海底。
82.依靠混凝土单桩基础自身的浮力,并通过控制混凝土单桩基础内的空气 量控制混凝土单桩基础的浮力大小,解决了超大重量单桩基础的运输及施工 难题,不需要大型运输、吊装船,操作容易,运输及施工费用低。
83.尽管本发明的内容已经通过上述优选实施例作了详细介绍,但应当认识 到上述
的描述不应被认为是对本发明的限制。在本领域技术人员阅读了上述 内容后,对于本发明的多种修改和替代都将是显而易见的。因此,本发明的 保护范围应由所附的权利要求来限定。
再多了解一些
本文用于企业家、创业者技术爱好者查询,结果仅供参考。