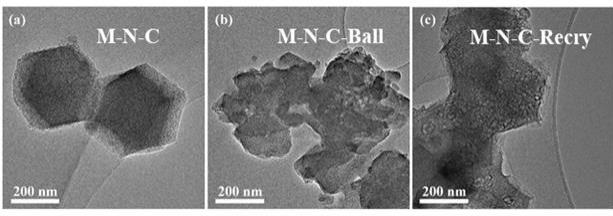
1.本发明涉及一种电极催化剂的制备方法及应用,尤其涉及一种燃料电池非贵金属阴极催化剂的制备方法及应用。
背景技术:
2.燃料电池是一种将化学物中化学能转化为电能的装置,由于其能量转化效率高,环境污染小和可调控性高等优点而备受重视。然而商业上广泛使用的燃料电池电催化剂仍然是以贵金属(铂、铑、钯、铱等)为主,贵金属价格高昂,资源稀罕,极大地制约了燃料电池的商业化发展与应用,因此研究并开发不含贵金属的催化剂材料具有重要意义。
3.早期研究人员便发现,过渡金属掺杂的氮碳材料具有优良的催化活性,在氧还原上表现得尤其突出。对此,研究人员在此展开了大量的研究,其中最具有代表性的为过渡金属掺杂的氮碳材料用作氧还原催化剂材料。虽然m
‑
n
‑
c催化剂材料其催化活性已经得到巨大的提升,但与贵金属如pt基催化剂仍有较大的差距,该差距表现在燃料电池中则尤为明显,无论在功率输出还是工况寿命,均远远不及。为此,进一步开发高催化活性阴极催化剂材料并实现高功率输出燃料电池具有非常重要意义。由mof衍生得到的单原子过渡金属掺杂的m
‑
n
‑
c具有优异的氧还原催化活性,但由于所得催化剂活性位大多是基于微孔限域的单原子m
‑
nx,因此极大地限制了反应物的可接触性,导致催化活性大幅度降低,因此,开发更高催化活性且高利用率m
‑
n
‑
c催化剂是实现高功率燃料电池的关键。
技术实现要素:
4.发明目的:本发明的目的是提供一种活性位点利用率高、电化学性能优异的燃料电池非贵金属催化剂的制备方法;本发明的第二个目的是提供一种燃料电池非贵金属催化剂的应用。
5.技术方案:本发明所述的燃料电池非贵金属阴极催化剂的制备方法,包括以下步骤:(1)将咪唑单体和金属配体盐分别溶解于溶剂中得到a溶液和b溶液,将两者混合后进行水热反应,反应结束后经离心、洗涤、干燥,即得沸石咪唑酯金属有机骨架材料zif;(2)取zif、含氮有机物和过渡金属盐加入到溶剂中,搅拌后蒸干,即得过渡金属掺杂的zif,记为m
‑
zif;(3)将m
‑
zif进行球磨,得到结构粉化且含有缺陷的m
‑
zif,记为m
‑
zif
‑
ball;(4)将m
‑
zif
‑
ball溶解于溶剂中,搅拌后静止以进行再结晶,经离心、洗涤、干燥,即得再结晶的m
‑
zif
‑
ball,记为m
‑
zif
‑
recry;然后经热解得到金属
‑
氮
‑
碳催化剂材料,记为m
‑
n
‑
c
‑
recry。
6.其中,所述步骤(3)中,球磨球料的质量比为100~10:1;球磨转速为200~1000rpm,球磨时长1~24h。
7.其中,所述步骤(4)中,室温再结晶的晶化时长为1~48h;热解的氛围为n2或ar惰性
气氛,热解温度800~1100,热解时长为0.5~2h。
8.其中,所述步骤(2)中,过渡金属盐、含氮有机物和zif的质量比为1:10~50:20~500。
9.其中,所述步骤(2)中,过渡金属盐为fe或co的乙酸盐、氯化物、硝酸盐、碳酸盐、磷酸盐、硫酸盐、草酸盐、柠檬酸盐、乙酰丙酮基化合物中的一种或几种;含氮有机物为邻菲啰啉、乙酰胺、乙胺、吡咯、苯胺、乙二胺、多巴胺、双氰胺、尿素、丁腈、三聚氰胺中的一种或几种。含氮有机物中的n元素与过渡金属配位形成过渡金属
‑
n键,确保了过渡金属元素以单原子形式分布;另一方面,含氮配合物在热解时充当造孔剂,更加利于介孔的生成。
10.其中,所述步骤(1)中,所述zif为zif
‑
8、zif
‑
67、zif
‑
7、zif
‑
9、zif
‑
11、zif
‑
14、zif
‑
68、zif
‑
69、zif
‑
70、zif
‑
90中的任意一种;咪唑单体和金属盐配体摩尔比例为1~100:1,溶剂热反应温度为100℃~240℃。
11.本发明所述的燃料电池非贵金属阴极催化剂,包括金属
‑
氮
‑
碳催化剂材料,所述金属
‑
氮
‑
碳催化剂材料为分布有过渡金属单原子的多级孔结构氮掺杂碳材料,所述过渡金属以单原子形式主要分布于金属
‑
氮
‑
碳催化剂材料表层;其中过渡金属含量为1wt%~4wt%,所述多级孔结构中的微孔和介孔占比为4~1:1。
12.其中,所述金属
‑
氮
‑
碳载体中的过渡金属为fe和/或co;金属
‑
氮
‑
碳催化剂材料为均匀分布有过渡金属单原子的多级孔结构氮掺杂碳材料。
13.利用上述燃料电池非贵金属阴极催化剂的制备方法制备的燃料电池非贵金属阴极催化剂在h2‑
o2燃料电池和甲醇燃料电池中的应用。
14.基本原理:球磨提供的巨大能量将zif晶体框架直接粉化及无序化,并生成大量介孔和大孔等缺陷,随后在重结晶时又重新成核并聚集成型,但由于zif的成核速率更快且稳定,因此金属有机配合物便在其成核后均匀配位在其外层周围,从而导致重结晶后的zif前驱体热解所得的m
‑
n
‑
c催化剂表层过渡金属原子含量更加丰富。而未经过球磨和重结晶的热解产物m
‑
n
‑
c主要以微孔为主,但是微孔对反应物进入有很大的限制,所以催化活性不高或者是利用率很低;经过重结晶的热解产物m
‑
n
‑
c
‑
recry介孔最多,介孔多有利于在燃料电池中的传质,因此,有助于提高催化活性。
15.有益效果:本发明与现有技术相比,取得如下显著效果:1、非贵金属阴极催化剂材料在表层富集过渡金属单原子,且具有优异的多级孔道结构,而表层富集过渡金属单原子则使得活性位点更容易与反应物接触,多级孔道结构有利于燃料电池中的传质,因此表现出超高的电催化活性;2、引入球磨和液相重结晶的方法,使所制备的m
‑
n
‑
c催化剂材料富含丰富的介孔结构及表层更加富集过渡金属单原子,有利于传质且极大地提高了活性位点利用率,当将该催化剂应用在燃料电池阴极时,表现出优异的电化学性能;3、制备方法简单可控,一致性高,易实现批量生产;4、应用在燃料电池中表现出超高的输出功率。
附图说明
16.图1是本发明非贵金属催化剂材料zif
‑
8系列的xrd衍射花样图;图2是本发明非贵金属催化剂材料zif
‑
8系列的m
‑
n
‑
c、m
‑
n
‑
c
‑
ball和m
‑
n
‑
c
‑
recry的透射电镜对比图;图3是实施例1中的fe
‑
n
‑
c、fe
‑
n
‑
c
‑
ball和fe
‑
n
‑
c
‑
recry的等温吸附曲线对比图;
图4是实施例1中fe
‑
n
‑
c、fe
‑
n
‑
c
‑
ball和fe
‑
n
‑
c
‑
recry的孔体积及微孔和介孔占比对比图;图5是实施例1中fe
‑
n
‑
c、fe
‑
n
‑
c
‑
ball和fe
‑
n
‑
c
‑
recry的电感耦合等离子光谱对fe元素的含量标定对比图;图6a、图6b、图6c分别是实施例1中fe
‑
n
‑
c、fe
‑
n
‑
c
‑
ball、fe
‑
n
‑
c
‑
recry的x射线光电子能谱曲线对比图;图6d是实施例1中fe
‑
n
‑
c、fe
‑
n
‑
c
‑
ball、fe
‑
n
‑
c
‑
recry的x射线光电子能谱对fe元素在颗粒表面的含量标定对比图;图7是实施例1中fe
‑
n
‑
c、fe
‑
n
‑
c
‑
ball和fe
‑
n
‑
c
‑
recry的线性扫描伏安曲线对比图;图8是实施例1中fe
‑
n
‑
c、fe
‑
n
‑
c
‑
ball和fe
‑
n
‑
c
‑
recry在h2‑
o2燃料电池应用中的极化曲线对比图;图9是由图8计算得到的功率密度曲线对比图;图10是实施例1、2和5中fe
‑
n
‑
c
‑
recry在h2‑
o2燃料电池应用中的极化曲线对比图;图11是实施例10和11中fe
‑
n
‑
c
‑
recry的线性扫描伏安曲线对比图;图12是实施例14和15中fe
‑
n
‑
c
‑
recry的线性扫描伏安曲线对比图。
具体实施方式
17.下面对本发明作进一步详细描述。
18.实施例1(1)取9.52 g zn(no3)2·
6h2o 溶于 240 ml 甲醇充分搅拌后得a溶液,取10.512 g 2
‑
甲基咪唑溶于 120 ml 甲醇充分搅拌后得到b溶液。将a溶液和b溶液混合,剧烈搅拌1h,后将白色乳液加入至50 ml ptfe反应釜内胆中,每个内胆约30 ml,将组装好的反应釜放入鼓风干燥箱中,120℃保温4h。离心、洗涤、干燥即制备出zif
‑
8。
19.(2)按照1:20:80的比例称取25 mg醋酸铁(ⅱ)、500 mg 1,10
‑
菲啰啉、2000 mg zif
‑
8加入烧杯中。加入100 ml甲醇,20 ml去离子水,搅拌2h。随后放入水浴锅中,85℃旋蒸,将蒸干后粉末放入鼓风干燥箱,60℃过夜即得到fe
‑
zif。
20.(3)称取2 g的fe
‑
zif粉末加入玛瑙球磨罐中,随后加入100 g球磨珠,即球料比为50:1,设置球磨转速为240rpm,球磨时长8h,将球磨结束后的固体刮出即得fe
‑
zif
‑
ball。
21.(4)称取1 g的fe
‑
zif
‑
ball粉末加入至100 ml甲醇中,充分搅拌1 h,然后静止12 h,待粉末完全晶化后进行离心、洗涤、干燥,即得fe
‑
zif
‑
recry。
22.(5)为表征球磨和再结晶对催化剂材料的性能和结构影响,分别取600 mg的fe
‑
zif、fe
‑
zif
‑
ball和fe
‑
zif
‑
recry置于不同的刚玉坩埚中,将坩埚放在石英管中,随后对各材料进行热解,其中,热解气氛为n2,热解温度为1000℃,热解时长1 h,待热解结束后即得到最终产物即为fe
‑
n
‑
c、fe
‑
n
‑
c
‑
ball和fe
‑
n
‑
c
‑
recry三种不同的催化剂材料。
23.如图1所示,为本实施例非贵金属催化剂材料zif
‑
8系列的xrd衍射花样图,可以看出,球磨后的材料由典型的zif
‑
8晶型转变为无定型,重结晶后又再次转变为zif
‑
8的晶型结构。
24.如图2所示,为本发明非贵金属催化剂材料zif
‑
8系列的m
‑
n
‑
c、m
‑
n
‑
c
‑
ball和m
‑
n
‑
c
‑
recry的透射电镜对比图;可以看出,图2中的(a)和(c)均为正十二面体结构,即,m
‑
n
‑
c、
m
‑
n
‑
c
‑
recry均为正十二面体结构,而图2中的(b)则表现为无规则粉体颗粒,即,m
‑
n
‑
c
‑
ball表现为无规则粉体颗粒。
25.如图3所示,为实施例1中fe
‑
n
‑
c、fe
‑
n
‑
c
‑
ball和fe
‑
n
‑
c
‑
recry的等温吸附曲线对比图;可以看出,fe
‑
n
‑
c
‑
ball出现明显地回归线地滞后,表明球磨使得材料结构发生巨大的破坏,出现大量的介孔结构。
26.如图4所示,为实施例1中fe
‑
n
‑
c、fe
‑
n
‑
c
‑
ball和fe
‑
n
‑
c
‑
recry的孔体积及微孔和介孔占比对比图;其中,未经过球磨和重结晶的热解产物fe
‑
n
‑
c微孔最多,而经过重结晶的热解产物fe
‑
n
‑
c
‑
recry介孔最多,介孔多有利于在燃料电池中的传质。
27.如图5所示,为实施例1中fe
‑
n
‑
c、fe
‑
n
‑
c
‑
ball和fe
‑
n
‑
c
‑
recry的电感耦合等离子光谱对fe元素的含量标定对比图;可以看出,三者的fe含量无明显差异。
28.图6a、图6b、图6c分别为实施例1中fe
‑
n
‑
c、fe
‑
n
‑
c
‑
ball和fe
‑
n
‑
c
‑
recry的x射线光电子能谱曲线对比图;可以看出,经过重结晶的热解产物fe
‑
n
‑
c
‑
recry所含fe
‑
nx配体最多,即表层活性位密度最高。如图6d所示,为实施例1中fe
‑
n
‑
c、fe
‑
n
‑
c
‑
ball和fe
‑
n
‑
c
‑
recry的x射线光电子能谱对fe元素在颗粒表面的含量标定对比图;可以看出,经过球磨和重结晶处理后的fe含量在表面富集量最多,因此表明球磨和重结晶均有利于fe元素在催化剂材料表面的富集。主要原理是:由于球磨时提供的巨大能量将zif
‑
8晶体框架直接粉化并无序化,随后在重结晶时又重新成核并聚集成型,但由于zif
‑
8的成核速率更快且稳定,因此铁的有机配合物便在其成核后均匀配位在其外层周围,从而导致重结晶后的fe
‑
zif前驱体热解所得的m
‑
n
‑
c催化剂表层过渡金属原子含量更加丰富。
29.如图7所示,为实施例1中fe
‑
n
‑
c、fe
‑
n
‑
c
‑
ball和fe
‑
n
‑
c
‑
recry的线性扫描伏安曲线对比图;其中,经过重结晶的热解产物fe
‑
n
‑
c
‑
recry表现出最高的半波电位,e
1/2
=0.806v,即催化活性最高。
30.如图8所示,为实施例1中fe
‑
n
‑
c、fe
‑
n
‑
c
‑
ball和fe
‑
n
‑
c
‑
recry在h2‑
o2燃料电池应用中的极化曲线对比图,可以看出,经过重结晶的热解产物fe
‑
n
‑
c
‑
recry表现出最优异的极化曲线。
31.如图9所示,为图8计算得到的功率密度曲线对比图;可以看出,经过重结晶的热解产物fe
‑
n
‑
c
‑
recry表现出最高的功率密度输出,典型的如峰值功率密度可达1.4 w/cm2。
32.实施例2本实施例与实施例1的区别是:步骤1中加入2
‑
甲基咪唑的质量为21.024 g。
33.实施例3本实施例与实施例1的区别是:步骤1中水热反应温度为160℃。
34.实施例4本实施例与实施例1的区别是:步骤2中使用的过渡金属盐为乙酰丙酮钴。
35.实施例5本实施例与实施例1的区别是:步骤2中所加入的醋酸铁(ⅱ)、1,10
‑
菲啰啉、zif
‑
8的质量分别为:25 mg、500 mg和4000 mg,即加入比为1:20:160。
36.实施例6本实施例与实施例1的区别是:步骤3中球磨转速为200 rpm,球磨时长为24h。
37.实施例7
本实施例与实施例1的区别是:步骤3中球磨转速为1000 rpm,球磨时长为1 h。
38.实施例8本实施例与实施例1的区别是:步骤3中所加入的fe
‑
zif和球磨珠质量分别为2 g和200 g,即球料质量比为100:1。
39.实施例9本实施例与实施例1的区别是:步骤4中晶化时长为24h。
40.实施例10本实施例与实施例1的区别是:步骤5中热解温度为1100℃,热解时长为0.5h。
41.实施例11本实施例与实施例1的区别是:步骤5中热解温度为800℃,热解时长为2h。
42.实施例12本实施例与实施例1的区别是:步骤4中晶化时长为1h。
43.实施例13本实施例与实施例1的区别是:步骤3中所加入的fe
‑
zif和球磨珠质量分别为20 g和200 g,即球料质量比为10:1。
44.实施例14本实施例与实施例1的区别是:步骤2中所加入的醋酸铁(ⅱ)、1,10
‑
菲啰啉、zif
‑
8的质量分别为:25 mg、250 mg和500 mg,即加入比为1:10:20。
45.实施例15本实施例与实施例1的区别是:步骤2中所加入的醋酸铁(ⅱ)、1,10
‑
菲啰啉、zif
‑
8的质量分别为:10 mg、 500 mg和5000 mg,即加入比为1:50:500。
46.实施例16本实施例与实施例1的区别是:步骤2中所加入的含氮有机物为多巴胺。
47.实施例17本实施例与实施例1的区别是:步骤1中所加入金属盐为co(no3)2·
6h2o,制备zif
‑
67。
48.实施例18本实施例与实施例1的区别是:步骤1中所加入的咪唑单体为苯丙咪唑,制备zif
‑
7。
49.实施例19本实施例与实施例1的区别是:步骤4中晶化时长为48h。
50.由图10、11、12可以看出,实施例1相比实施例2、5、10、11、14、15性能更优异。这是由于,在实施例1的条件下活性位密度最高,且材料结构中介孔比例最大。
再多了解一些
本文用于企业家、创业者技术爱好者查询,结果仅供参考。