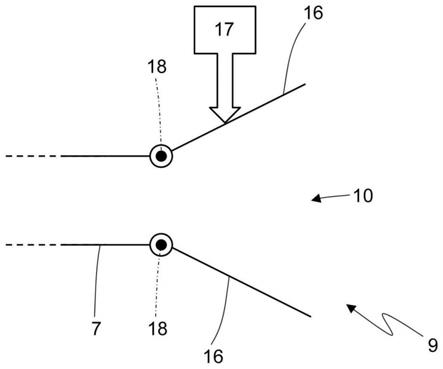
用于内燃机的排气系统
1.相关申请的交叉引用
2.本专利申请要求2020年4月9日提交的意大利专利申请第102020000007627号的优先权,其全部公开内容通过引用合并于此。
技术领域
3.本发明涉及一种用于内燃机的排气系统。
背景技术:
4.汽车型式批准法规(car type approval rule)迫使制造商限制声音排放水平,尤其是在汽车以中等速度行驶时(即,在其驶过市中心时)。因此,排气系统(实现将燃烧产生的气体释放到大气中、限制噪音和污染物质的含量的功能)始终设有至少一个消声器,该消声器沿着排气管道布置在污染物减少装置的下游。
5.一般而言,消声器包括管状主体,该管状主体通常具有椭圆形的横截面并且设有入口孔和出口孔。在管状主体内限定有曲折路径,该曲折路径决定了废气从入口孔到出口孔的路径;该曲折路径通常包括膜片(或隔板)和管,所述膜片横向(即,垂直于管状主体的纵向轴线)布置以在管状主体内限定腔室,所述管将各腔室彼此相连。在低发动机速度下确保高噪声衰减的传统的消声器中,由消声器产生的排气背压(即,当废气流过消声器时在废气中造成的压力损失)随着内燃机的每分钟转数的增加(即,随着废气的平均速度的增加)而呈指数增长。结果,为了避免在高发动机速度下太高的排气背压值(因此,避免在高发动机速度下过度损害性能),提供了与消声器平行布置(即,被设计为绕过消声器)并由旁通阀调节的旁通管道,该旁通阀在低发动机速度下保持关闭(以使消声作用最大,牺牲在低发动机速度下并不是必需的性能),而在高发动机速度下保持打开(以降低排气背压,牺牲在内燃机高速旋转时不应是首要重要的消声性)。
6.此外,在高性能跑车中,在车厢内感觉到的内燃机的噪声非常重要。特别是,高性能跑车的判断中的重要组成部分是排气系统发出的声音的“质量”(不只是也不主要在声音的强度方面,而且尤其还在发出的声音的“可能性”方面),即,高性能跑车的使用满意度还受到排气系统发出的声音的“质量”的显著影响。然而,已知的具有可变几何形状的排气系统(即,设有一个或多个电动或气动控制的阀,其可以改变废气的路径,并因此改变沿着排气系统的声音的路径)并不总是确保排气系统发出的声音符合用户的期望。
7.一般而言,涡轮增压式发动机是不利的,因为沿着排气管道的涡轮机和沿着进气管道的压缩机的存在增加了过滤器,并且要降低排气系统和进气系统两者的声音水平。
8.此外,最近的euro6c排放标准确立了废气处理装置的使用,废气处理装置严重损害了声音性能,因为即使在汽油发动机中,颗粒过滤器(也称为gpf,即“汽油颗粒过滤器”)也必须与催化转化器串联存在。
9.专利文献us1483354a、kr20160108625a和gb2274681a描述了一种用于内燃机的排气系统,其中源自于内燃机的排气管道具有端部部分,该端部部分以出口孔终止,废气通过
该出口孔被释放到大气中;排气管道的端部部分具有至少一个可移动壁,该可移动壁能移动到不同的位置以改变出口孔的宽度。特别是,可移动壁的移动可以手动进行(如us1483354a中所述),也可以由于废气的压力并克服由弹簧产生的弹性推力而自动发生,该弹簧倾向于使出口孔的宽度最小化(如kr20160108625a和gb2274681a中所述)。
技术实现要素:
10.本发明的目的是提供一种用于内燃机的排气系统;所述排气系统允许制造商在所有操作条件下获得自然排气噪声,该噪声能够满足驾驶员和可能的乘客的期望,同时符合型式批准法规的规定且不损害性能。
11.根据本发明,提供了一种用于内燃机的排气系统。
12.该排气系统包括至少一个第一排气管道,该第一排气管道源自于内燃机并且具有端部部分,该端部部分以第一出口孔终止,排气通过该第一出口孔被释放到大气中;
13.其中第一排气管道的端部部分具有至少一个可移动壁,该可移动壁能移动到不同的位置以改变出口孔的宽度;并且
14.该排气系统的特征在于,该排气系统包括:
15.马达驱动的致动器装置,该致动器装置被配置为有效地移动可移动壁,并能够以电子的方式被控制;以及
16.控制单元,该控制单元被配置为根据内燃机的转速和内燃机的发动机负荷,通过控制致动器装置来改变可移动壁的位置。
17.所附权利要求描述了本发明的优选实施方式,并且形成了描述的组成部分。
附图说明
18.现在将参照附图描述本发明,附图示出了本发明的一些非限制性实施方式,其中:
19.·
图1是由具有根据本发明的排气系统的内燃机驱动的汽车的示意图;
20.·
图2、图3和图4是具有排气系统的相应变型的图1的汽车的示意图;
21.·
图5是具有图1至图4的排气系统的排气管道的两个可移动壁的端部部分的示意图;
22.·
图6、图7和图8是在可移动壁位于不同的位置的情况下的图4的端部部分的示意图;
23.·
图9是图5的端部部分的示意性立体图;以及
24.·
图10是图5的端部部分的示意性立体分解图。
具体实施方式
25.在图1中,附图标记1总体上表示具有两个前轮2和两个后驱动轮3的汽车,后驱动轮3从内燃机4接收扭矩,内燃机4通过涡轮增压器增压并布置在前部位置。汽车1设有车厢5,该车厢5被设计为容纳驾驶员和可能的乘客。
26.根据一个可行但非限制性的实施方式,内燃机4是“v8”发动机,并且具有相对于彼此成一定角度布置以形成“v”的两个(双)具有四个汽缸的汽缸排。在每一排中,四个气缸通过两个进气阀连接至进气歧管(未被示出),并通过两个排气阀连接至排气歧管(未被示
出);每个排气歧管收集燃烧产生的气体,这些气体通过排气阀周期性地流出。
27.内燃机4设有排气系统6,排气系统6具有将燃烧产生的气体释放到大气中、限制噪声和污染物质的含量的功能。排气系统6包括两个(双)排气管道7,每个排气管道源自于对应的排气歧管以便从排气歧管接收燃烧产生的气体,并终止于汽车1的尾部区域。沿着每个排气管道7,存在已知的废气处理装置8:总是存在至少一个催化转化器,并且也可能存在颗粒过滤器(为了符合有关污染排放的新euro6c标准,汽车制造商还在汽油发动机中使用被称为gpf(是“gasoline particulate filter(汽油颗粒过滤器)”的缩写)的微粒过滤器。
28.每个排气管道7(源自于内燃机4)具有端部部分9,该端部部分9以出口孔10终止,废气通过该出口孔10被释放到大气中。
29.系统6包括两个附加排气管道11(即,除了两个排气管道7之外),每个附加排气管道源自于对应的排气管道7的接合部12的区域,并且具有出口孔13,废气通过该出口孔13被释放到大气中。换句话说,每个附加排气管道11是对应的排气管道7的最后区段的替代物。沿着每个附加排气管道11,(至少)存在传统的消声装置14,例如其包括具有椭圆形的横截面的管状主体,该管状主体具有入口孔、出口孔和内部的曲折路径,该曲折路径决定了废气从入口孔到出口孔的路径。另一方面,每个排气管道7没有设置任何传统的消声装置。
30.系统6包括两个调节阀15,每个调节阀沿着对应的排气管道7布置在排气管道11所源自的接合部12的下游(即,在排气管道11所源自的接合部12与端部部分9之间),并且被设计为调节朝着排气管道7的端部部分9的废气流。特别地,调节阀15朝着完全关闭位置移动,以防止废气流入排气管道7的最后区段,因此迫使废气流过设置有消声装置14的排气管道11,结果,在较大程度上衰减了噪声并具有较大的背压;反之亦然,调节阀15朝着完全打开位置移动,以将废气流引向排气管道7的最后区段(不需要关闭排气管道11,因为在存在可用的更自由的替代路径时,由消声装置14产生的较大的背压使沿着排气管道11的废气流最小化)。
31.在图2所示的变型中,没有调节阀15,并且调节阀15的功能(即,调节朝着排气管道7的端部部分9的排气流)直接由排气管道7的端部部分9的可变几何形状(如下所述)来实现。
32.在图3所示的变型中,没有排气管道11(因此也没有相关的消声装置14),但是另一方面,有调节阀15,每个调节阀与排气管道7相交,并且可在完全打开位置和完全关闭位置之间移动。
33.在该实施方式中,调节阀15具有减少向出口孔10的噪声传递的专用功能,因此,在完全关闭位置,调节阀15具有用于使废气通过的自由区段,该自由区段的面积非零,使得即使在阀15处于完全关闭位置时,废气也可以流过调节阀15。
34.在图4所示的变型中,没有排气管道11(因此没有相关的消声装置14),也没有调节阀15;结果,声音衰减策略的整个管理被完全分配给排气管道7的端部部分9的可变几何形状(在下面描述)。
35.根据图5至图10,每个排气管道7的端部部分9具有彼此反向且彼此面对的两个可移动壁16,该可移动壁可移动到不同的位置(比较图5至图8,看起来比较明显)。在每个端部部分9中设置有马达驱动的致动器装置17(即,设置有优选电动或气动的马达,该马达被设计为有效地产生移动),该致动器装置被配置为使可移动壁16移动;优选地,每个致动器装
置17被配置为使两个可移动壁16在相反的方向上一起移动,以使两个可移动壁16分开地移动或使可移动壁16彼此靠近地移动。换句话说,每个马达驱动的致动器装置17是有效的并且以电子的方式(电气的方式)被控制,以便产生决定可移动壁16的移动的力(转矩);结果,在每个端部部分9中,可移动壁16的位置是可调节的(通过控制对应的致动器装置17),而与流过端部部分9的废气的压力和流速完全无关(例如,当废气的压力和流速适中时,可以使可移动壁16移动到具有非常大的出口孔10,而当废气的压力和流速高时,可以使可移动壁16移动到具有非常小的出口孔10)。
36.根据一个优选实施方式,每个可移动壁16被铰接成以便围绕旋转轴线18旋转;结果,每个致动器装置17被配置为总是使两个可移动壁16围绕各自的旋转轴线18在相反的方向上旋转(通过这种方式,两个可移动壁16的移动使两个可移动壁16彼此分开地移动,或者其使两个可移动壁16彼此靠近地移动)。
37.在每个排气管道7的端部部分9中,两个可移动壁16可以在最大扩张位置(例如,在图5中示出)和最小扩张位置(例如,在图8中示出)之间移动;显然,当两个可移动壁16处于最大扩张位置时(例如,在图5中示出),出口孔10的面积(显著)大于两个可移动壁16处于最小扩张位置时的出口孔10的面积(例如,在图8中示出)。
38.在最大扩张位置(例如,在图5中示出)或者甚至在其他扩张位置(例如,在图6中示出),两个可移动壁16使排气管道7的端部部分9具有发散构造,该发散构造使接近出口孔10的横截面的面积逐渐增大;即,在最大扩张位置(在图5中示出)或者甚至在其他扩张位置(例如,在图6中示出),两个可移动壁16使排气管道7的端部部分9具有喇叭形状。
39.根据一个可行的实施方式,在最小扩张位置(在图7中示出),两个可移动壁16使排气管道7的端部部分9具有平行构造,该平行构造使接近出口孔10的横截面的面积保持恒定(基本上,两个可移动壁16平行于排气管道7的前部分的壁布置,以便不决定横截面的面积的任何显著变化)。
40.根据一个替代实施方式,在最小扩张位置(在图8中示出),两个可移动壁16使排气管道7的端部部分9具有会聚构造,该会聚构造使接近出口孔10的横截面的面积逐渐减小。
41.每个致动器装置17能够将两个可移动壁16设置并保持在最大扩张位置(例如,在图5中示出)与最小扩张位置(例如,在图8中示出)之间的中间位置。
42.根据图9和图10所示的可能的实施方式,在每个端部部分9中:两个可移动壁16面对彼此并且彼此反向,并且被铰接成以便围绕彼此平行的两个相应的旋转轴线18旋转,存在两个彼此平行且垂直于旋转轴线18的固定壁19(即,刚性地连接至支撑结构,因此不能进行任何类型的运动),并且两个可移动壁16被包围在固定壁19之间并且当两个可移动壁16移动时,在固定壁19上缓慢行进。在每个端部部分9中,两个固定壁19也可以彼此连接,以便形成在内部包含两个可移动壁16的“u”形结构,或者形成呈环形形状封闭并在内部包含两个可移动壁16的结构。
43.在附图所示的实施方式中,每个排气管道7的端部部分9具有两个彼此面对并且彼此对立的可移动壁16;根据未在本文中示出的不同实施方式,每个排气管道7的端部部分9具有单独一个可移动壁16或三个或更多个可移动壁16。
44.如上所述,每个排气管道7都没有任何传统的消声装置(即,除了可移动壁16之外并且布置在可移动壁16的上游)。
45.还设置有控制单元20(在图1至图4中示意性示出),该控制单元20被配置为根据以下条件改变每个端部部分9的可移动壁16的位置(通过控制对应的致动器装置17):内燃机4的转速、内燃机4的发动机负荷、在与内燃机4联接的变速箱中挂的档位、配备有内燃机4的汽车1的纵向速度以及配备有内燃机4的汽车1的纵向加速度。
46.即,控制单元20被配置为检测(例如,通过从汽车的bus网络读取它们):内燃机4的转速、内燃机4的发动机负荷、变速箱中挂的档位、汽车1的纵向速度和汽车1的纵向加速度;已知该信息(预先读取),控制单元20可以根据该信息确定每个端部部分9的可移动壁16的位置。
47.控制单元20可以被配置为还根据驾驶员选择的驾驶模式(即,可以是运动驾驶模式、赛车驾驶模式、城市驾驶模式、高速公路驾驶模式、湿滑道路驾驶模式
……
,这通常由驾驶员通过作用在称为“手操纵杆”的选择器上来进行选择)来改变每个端部部分9的可移动壁16的位置。
48.根据优选实施方式,控制单元20被配置为在内燃机4的低转速和低发动机负荷下,使每个端部部分9的可移动壁16朝着最小扩张位置移动,而在内燃机4的高转速和高发动机负荷下,使每个端部部分9的可移动壁16朝着最大扩张位置移动。此外,控制单元20被配置为在低档位时使每个端部部分9的可移动壁16朝着最小扩张位置移动,而在高档位时使每个端部部分9的可移动壁16朝着最大扩张位置移动。
49.根据一个优选实施方式,在控制单元20中存储了不同的图型(每个图型对应于一种或多种驾驶模式),这些图型基于作为输入提供的、关于内燃机4的转速和发动机负荷以及在与内燃机4联接的变速箱中挂的档位的数据,来提供每个端部部分9的可移动壁16的期望的(理想的)位置作为输出。显然,存储在控制单元20中的每个图型都包括有限数量的点,因此,控制单元20可以在图型的最接近的点之间执行插值,以便确定每个端部部分9的可移动壁16的期望(理想)位置。
50.在最大扩张位置(例如,在图5中示出),每个端部部分9的可移动壁16的“打开”(即“发散”)位置使排气管道7具有最小的排气背压(即,其使性能最大化),并且还使排气管道7具有最小的排气噪声衰减能力;另一方面,在最小扩张位置(例如,在图8中示出),每个端部部分9的可移动壁16的“关闭”(即“会聚”)位置使排气管道7具有最大的排气背压(即,其在较大程度上损害性能),并且还使排气管道7具有最大的排气噪声衰减能力。
51.控制单元20被配置为在偏向消声而不是性能是有必要的(有用处的)时,使每个端部部分9的可移动壁16朝着最小扩张位置(例如,在图8中示出)移动,而在偏向性能而不是消声是有必要的(有用处的)时,使每个端部部分9的可移动壁16朝着最大扩张位置(例如,在图5中示出)移动。
52.在附图所示的实施方式中,内燃机4具有布置成v形的八个汽缸6。显然,内燃机可以具有不同数量的汽缸和/或不同的汽缸布置;对于带有直列汽缸的内燃机(因此,具有单独一排汽缸),通常存在单独一个排气管道7,因此存在一个端部部分9。
53.在附图所示的实施方式中,内燃机4是增压式的;根据未在本文中示出的其他实施方式,内燃机4不是增压式的,即它是吸气式发动机。
54.本文描述的实施方式可以彼此组合,而不会因此超出本发明的保护范围。
55.上述排气系统6具有许多优点。
56.首先,上述排气系统6允许在低发动机速度下理想地消声,并且同时允许在高发动机速度下使排气背压最小化。
57.特别地,通过适当地调节每个出口孔10的宽度(即,通过适当地调节每个可变几何形状的端部部分9的声音放大/衰减能力),上面描述的排气系统6允许在任何可能的操作条件下优化每个可变几何形状端部部分9的频率响应。
58.此外,上述排气系统6特别轻且紧凑(特别是在图3和图4所示的实施方式中,其不包括消声装置14)。
59.最后,由于与类似的传统排气系统6相比,它需要添加少数易于制造的小尺寸部件,因此上述排气系统6易于制造且制造成本低廉。
60.附图标记列表
61.1 汽车
62.2 前轮
63.3 后轮
64.4 内燃热机
65.5 车厢
66.6 排气系统
67.7 排气管道
68.8 处理装置
69.9 端部部分
70.10 出口孔
71.11 排气管道
72.12 接合部
73.13 出口孔
74.14 消声装置
75.15 调节阀
76.16 可移动壁
77.17 致动器装置
78.18 旋转轴线
79.19 固定壁
80.20 控制单元
再多了解一些
本文用于企业家、创业者技术爱好者查询,结果仅供参考。