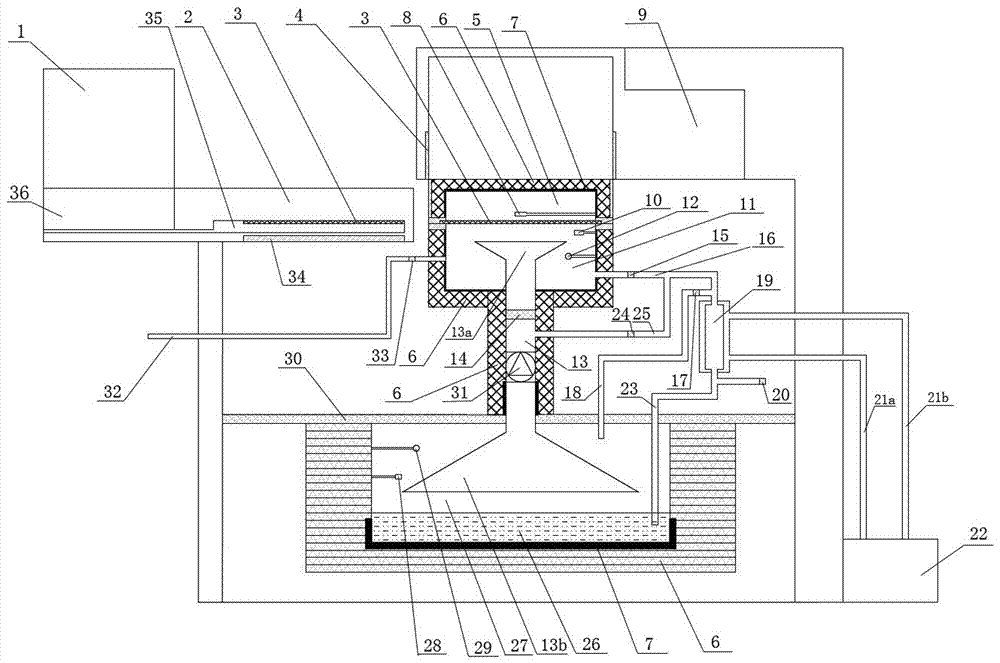
本发明属于半导体制造领域,具体是一种基于气相tmah的硅刻蚀系统。
背景技术:
mems(microeiectro-mechanicalsystem,微电子机械系统)技术是在半导体制造技术上发展起来的一种可批量制造微传感器、微执行器、信号处理和控制电路等于一体的制造技术。mems技术主要包含光刻、刻蚀、键合、薄膜生长、liga、硅微加工、非硅加工等工艺过程。
硅刻蚀工艺是mems技术中的关键工艺,目前常用的刻蚀方式可分为干法刻蚀和湿法刻蚀。湿法刻蚀主要使用koh和tmah(tetramethylammoniumhydroxide)等碱性溶液与硅发生化学反应,从而实现对硅的各向异性刻蚀。干法刻蚀主要采用icp(inductivelycoupledplasma)、rie(reactiveionetching)、drie(deepreactiveionetching)等技术对硅进行物理化学刻蚀,主要包括反应离子轰击刻蚀表面以及反应气体与刻蚀表面物质反应。
干法刻蚀具有较好的线宽控制,很好的侧壁剖面控制;不过干法刻蚀存在对下层材料的刻蚀选择比较差、等离子体诱导损伤、成本较高等缺点。湿法刻蚀虽然成本较低,但是结构暴露于碱溶液中,存在各步工艺过程难以兼容的问题。尤其是在硅的深刻蚀过程中,以上两种刻蚀技术的缺点将进一步显现,同时还存在刻蚀表面质量较、均匀性较差的问题。
技术实现要素:
本发明目的是提供一种基于气相tmah的硅刻蚀系统,该刻蚀系统采用一种介于湿法刻蚀和干法刻蚀之间的硅刻蚀技术,主要针对硅基mems器件的背腔深刻蚀工艺,可以实现低成本的同时能够很好的保证工艺的兼容性、良好的刻蚀表面、较高的刻蚀速率以及刻蚀均匀性,同时还实现了非刻蚀面结构的保护。
本发明是采用如下技术方案实现的:
一种基于气相tmah的硅刻蚀系统,包括加热腔和刻蚀腔,所述加热腔顶面采用密封法兰密封,所述刻蚀腔顶面放置晶元夹具、并通过背面保护腔盖合密封;所述加热腔、刻蚀腔及背面保护腔壁外设置有加热丝和保温层。
所述背面保护腔内安装背面保护腔温度传感器,所述刻蚀腔内安装刻蚀腔温度传感器和刻蚀腔压力传感器,所述加热腔内安装加热腔温度传感器和加热腔压力传感器。
所述加热腔和刻蚀腔通过中间管路连通,即中间管路的上端由刻蚀腔底面伸入、并安装小锥形管,所述小锥形管位于刻蚀腔内晶元夹具的下方,中间管路的下端由密封加热腔的密封法兰伸入、并安装大锥形管,所述大锥形管位于加热腔内tmah溶液上方;所述中间管路内依次安装刻蚀腔主阀和磁力泵。
所述刻蚀腔通过气体回流管与冷凝腔进口连通,所述气体回流管内安装回流阀;所述冷凝腔出口连接液体回流管,所述液体回流管穿过密封法兰后伸入加热腔;所述液体回流管上连接尾气出口接口;所述冷凝腔通过冷却水进水管路和冷却水回水管路连接水冷机。
所述冷凝腔进口通过分流管与位于中间管路上刻蚀腔主阀和磁力泵之间的空间连通,所述分流管上安装分流阀。
所述冷凝腔进口通过溢流管与加热腔连通,所述溢流管上安装溢流阀。
所述刻蚀腔通过氮气管路连接氮气源,所述氮气管路上安装氮气阀。
加热腔内装入浓度高于25%的tmah液体。打开背面保护腔,将晶元夹具放置在刻蚀腔顶面,然后将背面保护腔密封盖合在刻蚀腔上,夹具将背面保护腔和刻蚀腔分隔开。系统工作主要包括开机、初始化、送片、刻蚀、取片5个步骤。其中初始化主要完成各阀门的开关、加热各腔室使刻蚀系统达到相关温度气压要求;以满足下一步刻蚀条件。刻蚀过程主要分为刻蚀初始化以及刻蚀两个过程。刻蚀初始化主要完成刻蚀条件的准备,具体为调节加热丝的加热功率和各阀门的开度,以满足刻蚀所需的温度和压力条件。刻蚀过程主要包含刻蚀时间控制以及稳定刻蚀条件。在开机升温阶段,使用较大的加热功率加热tmah溶液,并通过加热腔温度传感器和压力传感器实时监测加热腔内的温度和气压,通过对比实际温度与目标温度的差值调整加热功率,从而使温度稳定的升至目标温度;同时调节回流阀开度,使加热腔温度气压维持在一个相对稳定的状态。刻蚀腔温度主要通过调节刻蚀腔周围的加热丝加热功率来保证刻蚀所需温度(110℃-125℃);刻蚀腔气压主要通过刻蚀腔压力传感器实测气压反馈到控制系统,控制系统通过调节刻蚀腔主阀、回流阀和分流阀开度以稳定刻蚀腔气压。
系统稳定后,刻蚀腔内刻蚀温度为(高于tmah沸点的)110℃-125℃;tmah气体在磁力泵驱动下,在大锥形管作用下,tmah气体均匀进入中间管路,通过刻蚀腔主阀进入刻蚀腔,在小锥形管作用下,tmah气体均匀流出,对硅片进行刻蚀。待刻蚀结束后关闭刻蚀腔主阀,打开氮气阀,通过氮气管路通入氮气,使刻蚀腔内残留的tmah气体被吹走,为打开刻蚀腔取片做准备。在刻蚀腔主阀门与磁力泵之间设置分流管路,用于将过量的气体通过冷凝系统流回加热腔,同时在刻蚀结束时需要关闭刻蚀腔主阀,过量的tmah气体经分流管进入冷凝腔,经冷凝后回流加热腔。如果冷凝腔内的tmah气体太多,则通过溢流管回流至加热腔内上部。加热腔和刻蚀腔分别设置有温度传感器和压力传感器,用于监测刻蚀腔和加热腔的温度和压强,将监测数据回传至控制中心,控制中心通过对数据进行处理,进而控制加热丝的加热功率、磁力泵转速以及阀门状态,以达到稳定刻蚀腔温度和气压的目的。刻蚀腔内tmah气体通过气体回流管路,进入冷凝腔,经冷凝后流回加热腔。水冷机控制冷却水温度约为20℃,并且提供动力使冷却水通过冷却水循环管路流经冷凝腔外壁,以达到冷凝tmah气体的目的。冷凝腔主要需要冷却来自刻蚀腔、分流管、溢流管的tmah气体。冷凝后的tmah液体通过液体回流管流回加热腔,剩余的尾气(主要包含反应生成h2和吹扫腔室的n2)通过尾气处理管路流入尾气处理装置。
本发明的气相刻蚀采用tmah气体作为刻蚀剂,与通常的湿法刻蚀使用60℃至90℃温度区间不同,tmah气相刻蚀主要利用了高于其沸点(100℃-110℃,tmah沸点与浓度有关)低于其分解温度(130℃)的温度区间,通常使用110℃-125℃。在高于tmah沸点的温度区间内,刻蚀表面处于tmah气体环境中,硅与碱发生化学反应,从而对硅进行各向异性腐蚀。在使用tmah对<100>晶向单晶硅刻蚀时,在浓度为4%的tmah溶液中刻蚀速率最大(约为1μm/min),同时刻蚀表面粗糙度也较大(数百纳米)。在tmah浓度大于4%的条件下,硅的刻蚀速率随tmah浓度增大而减小,刻蚀表面粗糙度随浓度增加而减小。本发明主要使用浓度大于25%的tmah溶液加热至沸腾产生的tmah气体与硅发生化学反应。通常,化学反应反应速率随温度呈指数增加;tmah气相刻蚀使用的刻蚀温度较常规湿法刻蚀高约30℃,速率比同浓度湿法刻蚀高4-8倍。实验研究证明,该系统实现了硅高速刻蚀(大于1.5μm/min),同时刻蚀表面较为光滑(粗糙度ra<10nm)。与此同时,气相刻蚀可以通过增大刻蚀腔体的气压以进一步提高刻蚀速率。该刻蚀系统通过背面保护腔实现了硅片背面已完成结构与刻蚀面的分离,从而保证了该步硅刻蚀工艺与以完成工艺之间的兼容性。
附图说明
图1表示tmah气相刻蚀系统框图。
图2表示基于tmah气相刻蚀系统的结构示意图。
图3表示系统工作流程图。
图4表示刻蚀系统送片工作流程图。
图5表示该刻蚀系统的取片流程图。
图6表示刻蚀过程工作流程图。
图7表示加热腔温度气压控制示意图。
图8表示刻蚀腔温度气压控制示意图。
图中:1-控制面板,2-传送腔,3-晶元夹具,4-液压传动机构,5-背面保护腔,6-保温层,7-加热丝,8-背面保护腔温度传感器,9-液压泵,10-刻蚀腔温度传感器,11-刻蚀腔,12-刻蚀腔压力传感器,13-中间管路,13a-小锥形管,13b-大锥形管,14-刻蚀腔主阀,15-回流阀,16-气体回流管,17-溢流阀,18-溢流管,19-冷凝腔,20-尾气处理接口,21a-冷却水进水管,21b-冷却水回水管,22-水冷机,23-液体回流管,24-分流阀,25-分流管,26-tmah溶液,27-加热腔,28-加热腔温度传感器,29-加热腔压力传感器,30-密封法兰,31-磁力泵,32-氮气管路,33-氮气阀,34-喷淋装置,35-机械臂,36-步进电机。
具体实施方式
下面结合附图对本发明的具体实施例进行详细说明。
一种基于气相tmah的硅刻蚀系统,如图1所示,包括:控制系统、传送系统、刻蚀系统和水冷系统;其中,水冷系统用于冷凝tmah气体;刻蚀系统用于产生tmah气体、输送刻蚀气体至刻蚀腔体以及刻蚀硅片;传送系统用于传输以及清洗刻蚀硅片;控制系统用于控制水冷系统、刻蚀系统、传送系统的协调工作,即分别控制控制传送电机以及液压泵的工作,同时还通过控制加热丝的加热功率以及各阀门的开度以控制刻蚀系统的温度和压力。
具体连接关系如图2所示,一种基于上述气相刻蚀系统的刻蚀装置。
传送系统主要包含电机、机械臂、喷淋装置、液压泵,液压传动机构。液压泵9通过液压传动机构4控制背面保护腔5的打开和密封盖合;步进电机36控制机械臂5实现晶元夹具3的放置和取出;机械臂35位于传送腔2内,传送腔2内设置喷淋装置34。当需要取出或放入所刻蚀硅片时,首先通过控制系统使液压泵工作,从而驱动刻蚀腔打开,接下来电机驱动机械臂将待刻蚀硅片连同晶元夹具传入刻蚀腔,最后收回机械臂,关闭刻蚀腔。喷淋装置主要用于清洗刻蚀后残留物的装置。特别地,夹具采用耐腐蚀的聚四氟乙烯材质制成,用于夹持待刻蚀硅片,夹持硅片时待刻蚀表面向下放置;机械臂的运动可以使用齿轮-齿条机构实现传动;电机可采用步进电机实现精确平稳传动,从而保证传动系统的可靠运行。
刻蚀系统主要包含加热腔、刻蚀腔、磁力泵、加热丝、保温层、tmah溶液、温度传感器、压力传感器组成。具体连接关系如图2所示,加热腔27顶面采用密封法兰30密封,刻蚀腔11顶面放置晶元夹具3、并通过背面保护腔5盖合密封,刻蚀腔、夹具、背面保护腔之间设置有密封垫圈;加热腔27、刻蚀腔11及背面保护腔5内壁外设置有加热丝7。背面保护腔5内安装背面保护腔温度传感器8,刻蚀腔11内安装刻蚀腔温度传感器10和刻蚀腔压力传感器12,加热腔27内安装加热腔温度传感器28和加热腔压力传感器29;加热腔27和刻蚀腔11通过中间管路13连通,即中间管路13的上端由刻蚀腔11底面伸入、并安装小锥形管13a,小锥形管13a位于刻蚀腔11内晶元夹具3的下方,中间管路13的下端由密封加热腔27的密封法兰30伸入、并安装大锥形管13b,大锥形管13b位于加热腔27内tmah溶液26上方;中间管路13内依次安装刻蚀腔主阀14和磁力泵13;刻蚀腔11通过气体回流管16与冷凝腔19进口连通,气体回流管16内安装回流阀15;冷凝腔19出口连接液体回流管23,液体回流管23穿过密封法兰30后伸入加热腔27;液体回流管23上连接尾气出口接口20;冷凝腔19进口通过分流管25与位于中间管路13上刻蚀腔主阀14和磁力泵31之间的空间连通,分流管25上安装分流阀24;冷凝腔19进口通过溢流管18与加热腔27连通,溢流管18上安装溢流阀17;述刻蚀腔11通过氮气管路32连接氮气源,氮气管路32上安装氮气阀33。加热腔27、刻蚀腔11、背面保护腔5及中间管路13外表面均设置有保温层6。加热腔和刻蚀腔可由石英等耐腐蚀材料制成,加热腔内为浓度高于25%的tmah液体。磁力泵可采用容积式泵,由于该磁力泵需要工作在110℃以上和强腐蚀性气体环境中,所以该磁力泵需要可以承受350℃高温的钐钴磁铁作为传动元件,采用聚四氟乙烯材料作为泵的箱体、齿轮以及其他部件。加热腔和刻蚀腔通过中间石英管路连接,同时该石英管路上还设置有流量阀(刻蚀腔主阀),通过刻蚀腔主阀控制流入刻蚀腔的气体流量。在该阀门与磁力泵之间设置分流管路,用于将过量的气体通过冷凝系统流回加热腔,同时在刻蚀结束时需要关闭刻蚀腔主阀,tmah气体需通过分流管流经冷凝腔流回加热腔。加热腔和刻蚀腔分别设置有温度传感器和压力传感器,用于监测刻蚀腔和加热腔的温度和压强,将监测数据回传至控制中心,控制中心通过对数据进行处理,进而控制加热丝的加热功率、磁力泵转速以及阀门开度,以达到稳定刻蚀腔温度和气压的目的。刻蚀系统通过背面保护腔实现了硅片背面已完成结构与刻蚀面的分离,从而保证了该步硅刻蚀工艺与以完成工艺之间的兼容性。
水冷系统主要包含水冷机、冷凝腔、冷却水进水和回水管路。如图2所示,冷凝腔19通过冷却水进水管路21a和冷却水回水管路21b连接水冷机22。水冷机控制冷却水温度约为20℃,并且提供动力使冷却水通过冷却水循环管路流经冷却腔外壁,以达到冷凝tmah气体的目的。冷凝腔主要需要冷却来自刻蚀腔、分流管、溢流管的tmah气体。冷凝后的tmah液体通过液体回流管流回刻蚀腔,剩余的尾气(主要包含反应生成h2和吹扫腔室的n2)通过尾气处理管路输送至尾气处理装置。
控制系统主要包含控制面板和数据传输线,主要控制硅片传送和稳定刻蚀。传送硅片时,控制系统需完成控制液压泵工作、传送腔打开和传送电机工作。在刻蚀过程中,控制系统需实时监测背面保护腔温度传感器、刻蚀腔温度传感器、加热腔温度传感器、刻蚀腔压力传感器和加热腔压力传感器;根据实时监测数据,控制加热腔、刻蚀腔、背面保护腔的加热丝加热功率,同时控制磁力泵转速、回流阀、分流阀、溢流阀和刻蚀腔主阀的协同工作,以达到稳定刻蚀过程的目的。
具体实施时,连接刻蚀腔11和加热腔27的各阀门(包括氮气阀33、回流阀15、分流阀24、溢流阀17、刻蚀腔主阀14)均采用耐腐蚀电磁阀;气体回流管16、液体回流管23、分流管25、溢流管18、氮气管路32均采用耐高温防腐蚀的聚四氟乙烯(长期使用温度为-180℃至250℃)或石英等材料制成;刻蚀腔11、加热腔27和背面保护腔5采用高纯石英制成;使用的各温度以及压力传感器均要通过防腐蚀处理;晶元夹具3采用耐腐蚀的聚四氟乙烯材料制成,同时分别针对3-8英寸硅片分别设计不同规格的夹具,以满足不同规格硅片的刻蚀;控制系统可采用labview等软件编写可视化控制系统,控制系统安装于pc上。
图3为系统工作流程图,主要包括开机、初始化、送片、刻蚀、取片5个步骤。其中初始化主要完成各阀门的开关、加热各腔室使刻蚀系统达到相关温度气压要求;以满足下一步刻蚀条件。
如图4所示为该刻蚀系统的送片流程图,送片主要可分为将刻蚀硅片放入传送腔内的夹具3、打开传送腔2、打开刻蚀腔11、机械臂35传送硅片至刻蚀腔11、收回机械臂35、关闭刻蚀腔11和传送腔2这6个步骤。具体地,根据所刻蚀晶元规格选择合适的夹具3;控制系统驱动步进电机36工作,以齿轮齿条机构将待刻蚀硅片和夹具3送入刻蚀腔;然后收回机械臂35,关闭刻蚀腔11和传送腔2。
图5为该刻蚀系统的取片流程图,取片过程可分为打开刻蚀腔11、打开传送腔2、机械臂35取片、收回机械臂35、关闭刻蚀腔11和传送腔2、去离子水清洗硅片。具体地,刻蚀腔11使用液压传动的方式控制其开关,主要是为了保证能平稳的打开关闭刻蚀腔11。
图6所示为刻蚀过程工作流程图,刻蚀过程主要分为刻蚀初始化以及刻蚀两个过程。刻蚀初始化主要完成刻蚀条件的准备,具体为调节加热丝7的加热功率和各阀门的开度,以满足刻蚀所需条件。刻蚀过程主要包含刻蚀时间控制以及稳定刻蚀条件。
图7所示为加热腔27温度气压控制示意图,在开机升温阶段,使用较大的加热功率加热tmah溶液26,并实时监测腔室内的温度和气压,通过判断实际温度与目标温度的差值调整加热功率,从而使温度稳定的升至目标温度;同时调节溢流阀17开度,使加热腔27温度气压维持在一个相对稳定的状态。
图8所示为刻蚀腔11温度气压控制示意图,刻蚀腔11温度主要通过调节刻蚀腔11周围的加热丝7加热功率来保证刻蚀所需温度(110℃-125℃);刻蚀腔气压主要通过实测气压反馈到控制系统,控制系统通过调节刻蚀腔主阀14、回流阀15和分流阀24开度以稳定刻蚀腔气压。
最后要说明的是,上述说明并非对本发明的限制,本发明也并不仅限于上述举例,尽管参照本发明实施例进行了详细的说明,本技术领域的普通技术人员也应当理解,在本发明的实质范围内所做的变化,改性,添加或替换,也应属于本发明的保护范围。
本文用于企业家、创业者技术爱好者查询,结果仅供参考。