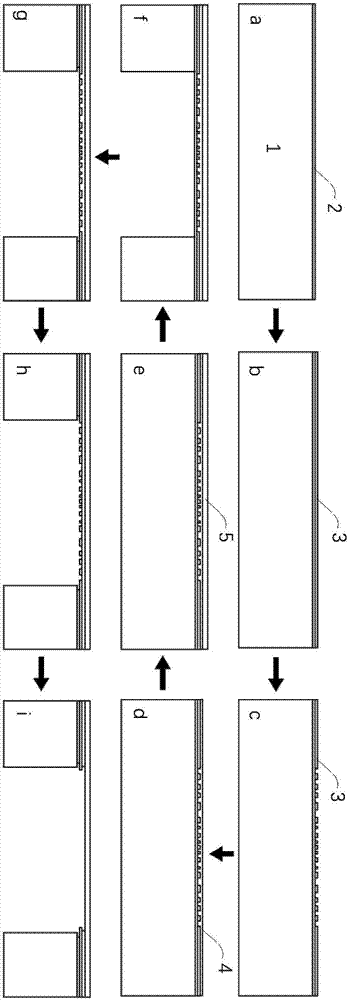
本发明属于硅微机械加工技术,具体涉及一种多晶硅振膜结构的制作方法。
背景技术:
多晶硅膜具有如单晶硅材料的高迁移率、与非晶硅薄膜生长工艺兼容、易于实现大面积生长、制备成本低等优良特性,被广泛用于微电子器件、光伏器件和液晶显示等领域。另外,多晶硅膜结构也常用于微机电系统(mems)中,特别是作为微纳器件的基本振动结构。例如,在电容式mems麦克风中,多晶硅薄膜结构被用作声音与振动的感知,因此,也被简称为多晶硅振膜。传统mems麦克风多晶硅振膜结构的制作方法主要存在两大不足:其一,对化学机械抛光的依赖导致工艺难度和制作成本上升;其二,背面深硅刻蚀的工艺误差显著影响通孔的形状及尺寸,从而会降低多晶硅振膜的工作性能。在形成多晶硅振膜的刻蚀停止层时,为了获得一个光滑平坦的表面,需要用到微电子工艺中最常用的表面平坦化技术,即化学机械抛光(cmp)。然而,cmp工艺的抛光一致性比较差,在cmp过程中很难控制材料去除均匀性,一个标准尺寸硅片上通常只能获得几百纳米的去除深度均匀性,因此,使用cmp工艺很难得到一个较为理想的刻蚀停止层。cmp工艺的抛光速率较慢,为了进一步提高cmp工艺的材料去除均匀性,往往要采用一些如分区处理和超精密抛光等手段,这一过程极为耗费时间,从而造成成本过高。此外,背面深硅刻蚀工艺制备的通孔的形状及尺寸和设计值往往存在一些偏差,从而容易导致薄膜的形状及尺寸偏离最优值,显著影响多晶硅振膜的工作性能。
综上所述,在多晶硅振膜结构的制作过程中,如何避免化学机械抛光工艺并精确控制振膜尺寸是亟待解决的问题。
技术实现要素:
本发明的目的就是针对现有技术的不足,提供一种多晶硅振膜结构的制作方法。
本发明中的多晶硅振膜结构从下往上依次包括基底、下sio2薄膜层、下多晶硅薄膜层、上sio2薄膜层、上多晶硅薄膜层;其中,基底的作用是支撑固定,其材料为硅片;下sio2薄膜层为深刻蚀的截止层;下多晶硅薄膜层为圆环沟槽结构层;上sio2薄膜层用于掩埋圆环沟槽结构;上多晶硅薄膜层用于感知声波与振动。
所述的下多晶硅薄膜层的上表面为圆环形的沟槽结构,相邻两沟槽间为圆环形的脊柱,脊柱与沟槽均匀相间分布;所述的沟槽和脊柱的宽度小于等于3000nm。
该多晶硅振膜结构的具体制作方法如下:
步骤a.采用化学气相沉积技术(cvd)、热氧化法或正硅酸乙酯(teos)热分解法在基底上制备厚度为200~1000nm的sio2薄膜,该sio2薄膜层即为下sio2薄膜层;
步骤b.在下sio2薄膜层上制备厚度为100~500nm的多晶硅薄膜,该多晶硅薄膜层即为下多晶硅薄膜层;
步骤c.按照设计的圆环形的沟槽图案,采用光刻刻蚀方法(litho-etch)将下多晶硅薄膜层刻穿,形成圆环形的沟槽结构;
步骤d.在下多晶硅薄膜层上采用正硅酸乙酯(teos)热分解法覆盖sio2薄膜,该sio2薄膜层即为上sio2薄膜层;上sio2薄膜层的厚度大于等于沟槽的最大宽度的一半;
步骤e.在上sio2薄膜层上制备厚度为100~500nm的多晶硅薄膜,该多晶硅薄膜层即为上多晶硅薄膜层;
步骤f.由基底的下表面开始,对应下多晶硅薄膜层的圆环形的沟槽结构的位置,通过光刻刻蚀方法(litho-etch)将基底刻穿,形成基底通孔;基底通孔截面完全覆盖圆环形的沟槽结构;
步骤g.由下sio2薄膜层的下表面开始,沿基底通孔通过气态氢氟酸腐蚀技术或氢氟酸湿法刻蚀方法将下sio2薄膜层刻穿,形成下sio2薄膜层通孔;
步骤h.通过气态氢氟酸腐蚀技术或氢氟酸湿法刻蚀方法将下多晶硅薄膜层的圆环形的沟槽内填充的sio2腐蚀干净;
步骤i.沿圆环形的沟槽,通过湿法刻蚀方法将上sio2薄膜层刻穿,圆环形的沟槽脱落,完全释放上多晶硅薄膜层以下的微腔,形成多晶硅振膜结构。
步骤b和e中制备下多晶硅薄膜层和上多晶硅薄膜层的具体制备方法采用以下两种方法之一:
(1)600℃以上高温下,采用化学气相沉积技术直接淀积多晶硅薄膜;淀积过程中采用气体在位掺杂技术进行磷元素掺杂。
(2)先通过化学气相沉积技术淀积非晶硅,再采用离子束注入技术进行磷元素掺杂,最后通过600℃以上高温退火结晶形成多晶硅薄膜。
以上两种方法中,磷元素的掺杂浓度为1012~1018atoms/cm3。
步骤f中所述的光刻刻蚀方法中的刻蚀工序采用深反应离子刻蚀方法(drie)。
本发明方法通过引入同心圆环结构和优化制作工艺流程,避免化学机械抛光工艺及其不利影响,能够精确控制多晶硅振膜的尺寸与形状,提高振膜的可靠性以及基于该振膜的器件的工作性能。
附图说明
图1为多晶硅振膜结构的剖面视图;
图2为多晶硅振膜的制作方法流程图;
图3为多晶硅环状沟槽结构示意图;
图4表示从基底背部观察到的环状沟槽结构示意图。
图中,1为基底、2为下sio2薄膜层、3为下多晶硅薄膜层、4为上sio2薄膜层、5为上多晶硅薄膜层。
具体实施方式
以下结合具体实施例并参照附图内容,对本发明技术特征和实施步骤加以详细叙述说明,以便于理解。
在本发明的一个优选实施例中,参照图1,典型的多晶硅振膜结构从下往上依次包括基底1、下sio2薄膜层2、下多晶硅薄膜层3、上sio2薄膜层4、上多晶硅薄膜层5;其中,基底1的作用是支撑固定,其材料为硅片;下sio2薄膜层2为深刻蚀的截止层;下多晶硅薄膜层3为圆环沟槽结构层;上sio2薄膜层4用于掩埋圆环沟槽结构;上多晶硅薄膜层5用于感知声波与振动。
下多晶硅薄膜层3的同心圆环沟槽结构如图3所示。在本发明的一个优选实施例中,下多晶硅薄膜层的上表面为圆环形的沟槽结构,相邻两沟槽间为圆环形的脊柱,脊柱与沟槽均匀相间分布;所述的沟槽和脊柱的宽度小于等于3000nm。值得注意的是,沟槽宽度和脊柱宽度的空间分布并不要求均匀,可以存在一定偏差,只要二者皆小于等于3000nm。
下多晶硅薄膜层3的圆环沟槽结构在整个方法中发挥着重要作用。一方面,可通过优化同心圆环状图案,减小淀积于其上的薄膜的表面起伏,提高上层二氧化硅薄膜的表面平整性,避免化学机械抛光工艺及其所带来的不利影响;另一方面,圆环沟槽结构中的同心圆环可精确限定及调节多晶硅振膜尺寸和形状,避免由于背面深硅刻蚀的圆孔不规整所引起的振膜尺寸及形状偏差,增大光刻背面对准的工艺容差,降低对准操作的难度。
为了制作出如图1所示的多晶硅振膜结构,本发明提出了一套完整的工艺流程(见图2)。该工艺流程大体上分为两个部分:基底正面的平面加工和基底背面的体加工。其中,基底正面的平面加工主要涉及薄膜生长和图形转移等工艺;基底背面的体加工主要涉及深硅刻蚀和湿法腐蚀等工艺。
具体来说,多晶硅振膜结构的制作工艺流程主要包括如下步骤(参照图2):
步骤a.采用化学气相沉积技术(cvd)、热氧化法或正硅酸乙酯(teos)热分解法在基底上制备厚度为200~1000nm的sio2薄膜,该sio2薄膜层即为下sio2薄膜层;
步骤b.在下sio2薄膜层上制备厚度为100~500nm的多晶硅薄膜,该多晶硅薄膜层即为下多晶硅薄膜层;
步骤c.按照设计的圆环形的沟槽图案,采用光刻刻蚀方法(litho-etch)将下多晶硅薄膜层刻穿,形成圆环形的沟槽结构;
步骤d.在下多晶硅薄膜层上采用正硅酸乙酯(teos)热分解法覆盖sio2薄膜,该sio2薄膜层即为上sio2薄膜层;上sio2薄膜层的厚度大于等于沟槽的最大宽度的一半;
步骤e.在上sio2薄膜层上制备厚度为100~500nm的多晶硅薄膜,该多晶硅薄膜层即为上多晶硅薄膜层;
步骤f.由基底的下表面开始,对应下多晶硅薄膜层的圆环形的沟槽结构的位置,通过光刻刻蚀方法(litho-etch)将基底刻穿,形成基底通孔;基底通孔截面完全覆盖圆环形的沟槽结构;
步骤g.由下sio2薄膜层的下表面开始,沿基底通孔通过气态氢氟酸腐蚀技术或氢氟酸湿法刻蚀方法将下sio2薄膜层刻穿,形成下sio2薄膜层通孔;
步骤h.通过气态氢氟酸腐蚀技术或氢氟酸湿法刻蚀方法将下多晶硅薄膜层的圆环形的沟槽内填充的sio2腐蚀干净;
步骤i.沿圆环形的沟槽,通过湿法刻蚀方法将上sio2薄膜层刻穿,圆环形的沟槽脱落,完全释放上多晶硅薄膜层以下的微腔,形成如图1所示多晶硅振膜结构。
步骤b和e中制备下多晶硅薄膜层和上多晶硅薄膜层的具体制备方法采用以下两种方法之一:
(1)600℃以上高温下,采用化学气相沉积技术直接淀积多晶硅薄膜;淀积过程中采用气体在位掺杂技术进行磷元素掺杂。
(2)先通过化学气相沉积技术淀积非晶硅,再采用离子束注入技术进行磷元素掺杂,最后通过600℃以上高温退火结晶形成多晶硅薄膜。
以上两种方法中,磷元素的掺杂浓度为1012~1018atoms/cm3。
步骤f中所述的光刻刻蚀方法中的刻蚀工序采用深反应离子刻蚀方法(drie)。
需要说明的是,步骤d优选正硅酸乙酯(teos)热分解法是为了填充下多晶硅薄膜层3的沟槽结构,并使上sio2薄膜层4上表面变得平坦光滑,再通过高温回流(reflow)可得到更平坦的上sio2薄膜层4上表面。本发明设计了如图3所示的圆环沟槽结构,在此处其主要优点是(圆环沟槽结构)容易被填充,防止该结构影响上层多晶硅振膜的表面形貌。
需要进一步说明的是,如图4所示,基底1背面通孔的形状通常是不规整的,与目标位置及形状都存在微小偏差,如果直接用该通孔限定多晶硅振膜下的微腔,势必影响多晶硅振膜结构的工作性能。为此,本发明设计了范围小于该通孔的圆环沟槽结构,在此处其主要优点是避免基底1背面通孔所引起的偏差,精确控制多晶硅振膜尺寸,提高整体工作性能。
另外,需要注意的是,本发明的优选实施例中展示了圆形外径的多晶硅振膜结构,所设计的圆环沟槽结构具有以上两个独特优点;在本发明的另一实施例中,制作多边形外径的多晶硅振膜,设计类似于圆环沟槽结构的多边形环状沟槽结构,也能体现以上两个独特优点;也就是说,任意与圆环沟槽结构具有同胚(topologicalisomorphism)关系并具备相同功能的设计都在本发明保护范围以内。
至此,已经结合附图对本发明进行了详细描述。依据以上描述,本领域技术人员应当对本发明所述多晶硅振膜结构的制作方法有了清楚的认识。以上所述的具体实施例,对本发明的目的、技术方案和有益效果进行了进一步详细说明,所应理解的是,以上所述仅为本发明的具体实施例而已,并不用于限制本发明,凡在本发明的精神和原则之内,所做的任何修改、等同替换、改进等,均应包含在本发明的保护范围之内。
本文用于企业家、创业者技术爱好者查询,结果仅供参考。