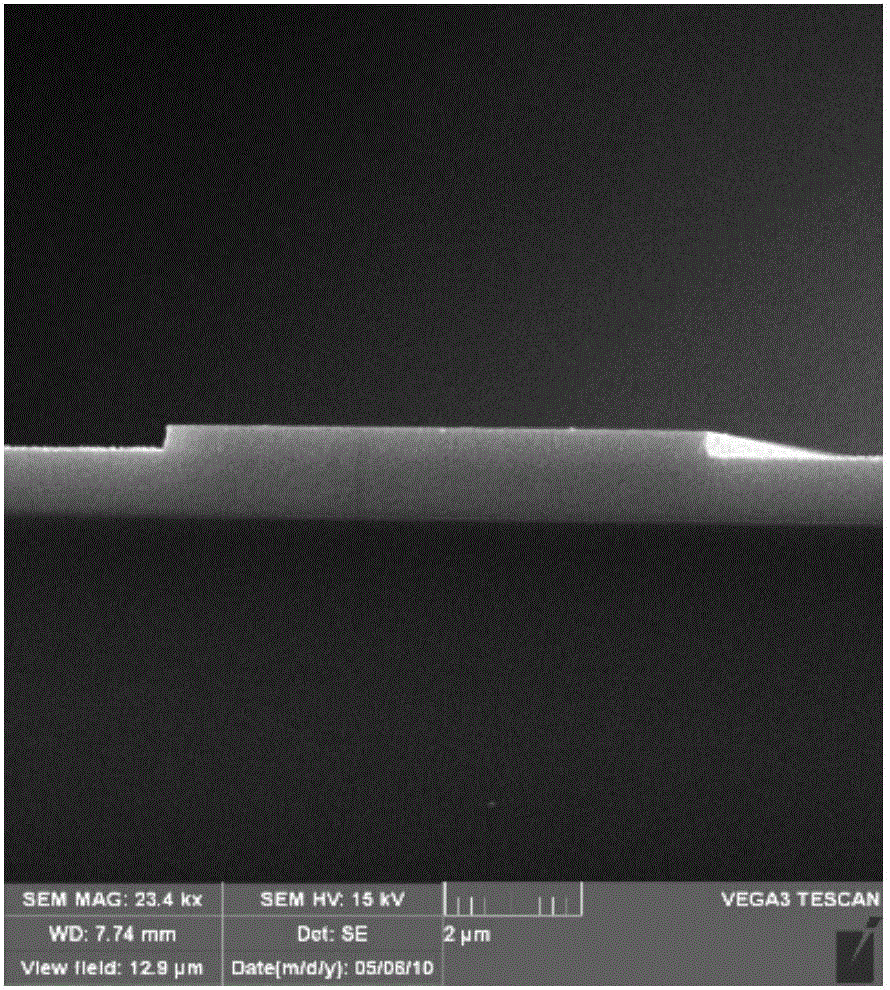
本发明涉及一种刻蚀方法。
背景技术:
微电子机械,是机械结构和电路集成在一起,具有信息采集、处理与执行的功能,具有体积小、重量轻、功耗低的优点。刻蚀工艺是微电子机械加工工艺中的重要部分,即在样品表面光刻图形后,通过刻蚀工艺将图形转移到光刻胶下边的层上。感应耦合等离子体技术(Inductively Couple Plasma,ICP)是刻蚀中发展起来的一种干法刻蚀工艺,目前在微电子技术中被广泛应用。
ICP刻蚀利用高密度等离子体与材料发生的化学反应和反应离子轰击样品表面产生的物理反应的共同作用进行微细尺寸的刻蚀。与湿法刻蚀及传统的等离子体刻蚀相比,具有以下优点:刻蚀速率快,选择比高,大面积均匀性好,刻蚀剖面的各向异性程度高,可进行高质量的精细线条刻蚀,获得优异的刻蚀形貌。
光波导传输损耗的大小直接影响光波导在通信和信息处理领域的应用,而波导侧壁粗糙所引起的散射损耗是波导传输损耗中的主要来源。目前,对于在GeSbSe薄膜上制备光波导的ICP刻蚀工艺还不够成熟,所制备的光波导的侧壁不够光滑,粗糙度较大,传输损耗较大,限制了其应用。
技术实现要素:
本发明所要解决的技术问题是提出一种采用三氟甲烷和四氟化碳作为混合刻蚀气体来改善波导侧壁的ICP刻蚀方法,以降低其传输损耗。
本发明解决上述技术问题所采用的技术方案为:一种改善波导侧壁的ICP刻蚀方法,其特征在于:包括以下步骤:
1)在Si/SiO2基片上镀上一层GeSbSe膜;
2)将清洗后的基片上涂覆光刻胶并且制备出光刻胶掩膜;
3)将带有光刻胶掩膜的基片在ICP刻蚀机内进行刻蚀,刻蚀时同时通入四氟化碳气体和三氟甲烷气体;
该四氟化碳气体和三氟甲烷气体的气体流量分别为5sccm-15sccm以及15sccm-30sccm;
4)刻蚀完成后去除残胶。
优选地,所述基片上的GeSbSe膜膜厚为800nm。
优选地,上述步骤1)的具体步骤为,将GeSbSe粉末放入真空镀膜机中的蒸发舟内,将基片清洗烘干,然后固定在样品旋转架上,抽真空至5×10-4Pa以下,先用Ar气体清洗,然后对蒸发舟进行预热100℃,再逐级加热到400℃,调节GeSbSe粉末的蒸发速率至5A/S左右直至加工结束。
优选地,上述步骤2)的具体步骤为:对带有GeSbSe膜的基片进行匀胶、前烘、曝光、显影、后烘和坚膜。
优选地,该步骤2)中的光刻胶为AZ5214,采用胶厚为1um-1.5um,匀胶机转速为4000-6000转,光刻机紫外曝光时间8S-10S,所用显影液为正胶显影液RZX3038,显影45S-60S,设置热板为120℃,坚膜时间为30min。
优选地,上述步骤3)中的刻蚀步骤,刻蚀功率为150W-400W,射频功率为80W-120W,刻蚀时间定为2min-6min。
优选地,刻蚀功率为300W,射频功率为100W,设置刻蚀时间为3min。
优选地,上述步骤4)中,分别用NMP、丙酮、异丙醇清洗基片以去除残胶。
优选地,所述四氟化碳气体流量为10sccm,三氟甲烷气体流量为20sccm。
与现有技术相比,本发明的优点在于利用两种气体的合理配比和通入量,能够实现对刻蚀的波导侧壁的形貌的改善,并且降低波导的传输损耗。
附图说明
图1为本发明实施例的刻蚀方法的步骤流程示意图。
图2为本发明实施例的刻蚀方法所刻蚀出来的波导在扫面电子显微镜下的形貌示意图。
具体实施方式
以下结合附图实施例对本发明作进一步详细描述。
如图1所示,本发明的刻蚀方法的具体步骤包括:把定量的GeSbSe粉末,例如小于2mm的GeSbSe粉末放入真空镀膜机中的蒸发舟内,然后将Si/SiO2基片清洗、烘干,然后固定在样品旋转架上,抽真空至5×10-4Pa以下。先用Ar气清洗基片几分钟,然后对蒸发舟预加热100℃,再逐级加热到400℃。调节GeSbSe粉末的蒸发速率至5A/S左右,等基片上的膜厚达到800nm左右后结束加工。
利用光刻胶材料将上述GeSbSe薄膜进行匀胶、前烘、曝光、显影、后烘和坚膜等工艺制备出光刻胶掩膜。光刻中所用正性光刻胶为AZ5214,采用胶厚为1um-1.5um,匀胶机转速为4000-6000转,光刻机紫外曝光时间8S-10S,所用显影液为正胶显影液RZX3038,显影45S-60S,设置热板为120℃,坚膜时间为30min。
本实例中将上述光刻好的样片,即带有光刻胶掩膜的基片,放入ICP刻蚀机腔室内,抽真空至10-3Pa以下,打开气体开关,然后通入四氟化碳和三氟甲烷气体,调节流量旋钮至四氟化碳气体流量为10sccm,三氟甲烷气体流量为20sccm,然后调节刻蚀功率为300W,射频功率为100W,设置刻蚀时间为3min,然后启动刻蚀按钮。刻蚀功率和射频功率这样设置有利于调节等离子体密度和轰击强度,控制刻蚀速率,有利于改善波导侧壁。时间设置为3min是为了使没被光刻胶掩膜保护的部分充分刻蚀掉而又不过多地刻蚀基片。上述气体四氟化碳气体的流量还可以为5sccm-15sccm,三氟甲烷气体流量为15sccm-30sccm。
刻蚀完成后,分别用NMP(N-甲基吡咯烷酮,一种强力去胶剂),丙酮,异丙醇清洗基片几分钟以去除残胶,最后得到的就是所需的GeSbSe波导,然后将刻蚀后清除残胶的GeSbSe波导在扫面电子显微镜下分析得到如图2所示形貌。图2中可以看出CHF3和CF4混合气体刻蚀所得波导侧壁粗糙度较低,与单一CF4气体刻蚀所得波导侧壁的粗糙度相比明显改善了很多,而且波导侧壁的陡直度也较好,效果较理想。而且波导的侧壁粗糙度和陡直度也可以通过改变气体流量比来进一步改善,以达到更好的效果。
本发明选择合适的CHF3和CF4的气体流量比,充分利用其各自的特性,CF4可以提供较大的刻蚀速率,而CHF3相对而言可以充当保护气体提供保护,这样保护和刻蚀过程同时进行,相比保护和刻蚀过程交替进行的刻蚀工艺,不需要交替转换刻蚀气体和保护气体,可以避免由此造成的侧壁的波纹效应,使得工艺更简单易控制,可获得更高的刻蚀效率。这样也可以增大刻蚀选择比,增加刻蚀速率,改善波导侧壁粗糙度和陡直度。
当刻蚀气体流量较小时,由于F原子的刻蚀占优势,刻蚀速率较高,没有得到充分保护的侧壁造成刻蚀边缘是各向同性的,难以形成垂直的剖面,同时侧壁很粗糙,呈颗粒状。随着刻蚀气体流量的增大,聚合物的沉积占优势。由于侧壁上增强的聚合物保护,刻蚀剖面由各向同性逐渐变得垂直,此时的钝化也可使侧壁变得光滑。随着流速进一步增大,过量的聚合物沉积会导致正斜率的侧壁,并生成密集的微掩膜,形成杂草状的刻蚀表面,刻蚀选择比变小。所以刻蚀气体CHF3和CF4的流量范围分别为15-45sccm和5-30sccm比较合适。一般CHF3的流量要大于CF4。
刻蚀功率的大小决定了等离子体的产生速率和效率。当刻蚀功率增大时,等离子体中的F原子、CFx基团以及离子的相对密度均增大,导致F原子的刻蚀作用、聚合物的沉积保护作用以及离子的轰击作用均增强。增强的离子轰击加强了对表面沉积的聚合物的去除作用,使得F/CFx的比值随之增大,此时F原子的侵蚀相对于聚合物层的保护来说占优势,刻蚀速率随之迅速增加。同时随着F原子密度和离子轰击能量的增加,两者共同作用也使光刻胶的刻蚀速率迅速增加,相应的刻蚀选择比也随之增大。在刻蚀过程中,若刻蚀功率过低,等离子体密度的降低会导致刻蚀很难进行。但如果刻蚀功率过高,硫系材料处于高刻蚀速率区,此时的刻蚀是各向同性的,很难获得垂直的侧壁。而且由于光刻胶的抗轰击能力限制,在过高的刻蚀功率下很容易碳化。
射频功率关系到离子加速和轰击能量,射频功率升高使离子轰击作用增强,此时激发的离子轰击方向性较强,在垂直方向上增强的离子作用能有效去除聚合物形成的微掩膜效应,使刻蚀顺利进行,而在侧向相对较弱的离子轰击可使侧向的刻蚀得到抑制,获得各向异性的刻蚀剖面。但增强的离子轰击能量也会增强对光刻胶的侵蚀,使光刻胶的刻蚀速率变大,刻蚀选择比变差。在硫系材料的刻蚀过程中,若射频功率过低,则离子轰击在垂直方向的动能减弱,各向同性刻蚀的本质就会显现出来。若刻蚀功率过高,由于对光刻胶的刻蚀作用加强,则刻蚀选择比变差,刻蚀图形会存在较大偏差。
所以本专利的刻蚀功率为150W-400W左右,射频功率为80W-120W。
刻蚀时间要根据具体的薄膜厚度和气体流量及刻蚀功率做相应的调整,因为刻蚀速率较快,一般把没有被光刻胶掩膜保护的薄膜刻蚀完就好。本专利的薄膜厚度为800nm左右,刻蚀时间太短,刻蚀不充分,一些残留的聚合物会在样品表面形成很多斑纹,样品表面质量不好;刻蚀时间过长,会在刻蚀完薄膜后继续刻蚀硅片,导致光刻胶掩膜保护不充分,侧壁粗糙度和选择比降低。所以刻蚀时间定为2min-6min。
以上所述的具体实施例,对本发明的目的、技术方案和有益效果进行了进一步详细说明,所应理解的是,以上所述仅为本发明的具体实施例而已,并不用于限制本发明,凡在本发明的精神和原则之内,所做的任何修改、等同替换、改进等,均应包含在本发明的保护范围之内。
本文用于企业家、创业者技术爱好者查询,结果仅供参考。