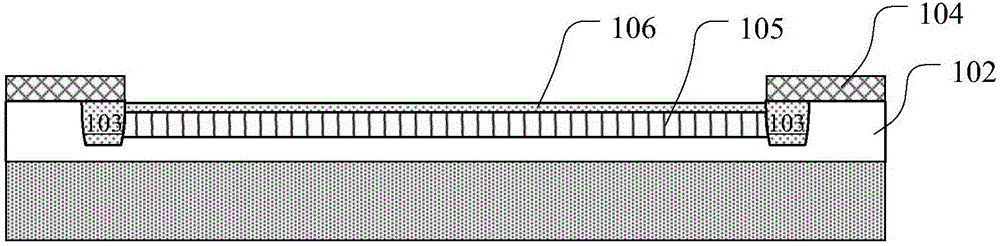
本实用新型属于微电子机械系统(MEMS)技术领域,更具体地,涉及单片集成的MEMS器件。
背景技术:
MEMS(Micro Electromechanical System,即微电子机械系统)是指集微型传感器、执行器以及信号处理和控制电路、接口电路、通信和电源于一体的微型机电系统。采用MEMS技术制作的微传感器、微执行器、微型构件、微机械光学器件、真空微电子器件、电力电子器件等在航空、航天、汽车、生物医学、环境监控、军事以及几乎人们所接触到的所有领域中都有着十分广阔的应用前景。目前,MEMS市场的主导产品为压力传感器、加速度计、微陀螺仪和硬盘驱动头等。
随着集成电路小型化和多功能化的发展,MEMS传感器与信号处理电路的集成已经成为一种必然趋势。二者的集成方法有三种:混合集成、半混合集成和完全单片集成。混合集成是将MEMS传感器与信号处理电路制造在不同的管芯中,然后封装成一个封装组件。半混合集成是将MEMS传感器和信号处理电路制作在不同的硅晶片上,采用硅晶片级的键合实现二者的互连,然后封装成一个封装组件。完全单片集成则是将MEMS传感器和信号处理电路制作在同一个硅晶片上,形成单个管芯。单片集成的MEMS器件是目前最主流和最先进的技术。
在现有的单片集成MEMS器件制造工艺中,首先在硅晶片的第一区域制作信号处理电路的晶体管等结构,然后采用牺牲层保护第一区域,在硅晶片的第二区域制作MEMS传感器。MEMS传感器和信号处理电路的晶体管形成平面结构,最后形成金属互联。在这种制造工艺中,MEMS传感器和晶体管的制作工艺彼此独立,互不兼容,因而存在着制造步骤多导致工艺复杂化的问题。
另外,由于MEMS传感器和信号处理电路按照平面结构布置,因此导致管芯面积增加。
技术实现要素:
鉴于上述问题,本实用新型的目的在于提供一种将MEMS传感器和晶体管堆叠形成垂直结构的MEMS器件,从而减小芯片尺寸、提高芯片性能以及降低器件成本。
根据本实用新型的一方面,提供一种MEMS器件,包括:衬底;位于衬底上的MEMS传感器,所述MEMS传感器包括在衬底上形成的空腔以及位于空腔上的结构层;以及位于MEMS传感器上的晶体管,其中,所述晶体管的至少一部分形成在所述MEMS传感器的结构层中。
优选地,所述MEMS传感器还包括:位于衬底上的第一种子层,在所述第一种子层中形成所述空腔;位于所述空腔上的第二种子层,其中,所述结构层包括所述第二种子层以及在所述第一种子层和所述第二种子层的表面上形成的外延层。
优选地,所述MEMS传感器还包括:位于所述第一种子层中的第一隔离结构,所述第一隔离结构围绕所述空腔,用于限定所述MEMS传感器的有源区域。
优选地,所述第一隔离结构为位于所述第一种子层中的掺杂区,所述第一隔离结构从所述第一种子层表面向下延伸,其结深为5微米以上。
优选地,所述晶体管为CMOS晶体管或双极性晶体管。
优选地,所述晶体管的阱区形成在所述MEMS传感器的结构层中,所述晶体管还包括形成在阱区中的源/漏区、以及形成在阱区上的第一栅叠层。
优选地,所述晶体管还包括位于第一栅叠层两侧的栅极侧墙,以及位于第一栅叠层表面上的硅化物层。
优选地,还包括:层间介质层;在层间介质层中形成的开口;以及在层间介质层上形成经由开口到达所述源/漏区和所述第一栅叠层的互连。
优选地,还包括:位于所述晶体管上的钝化层,用于保护所述MEMS器件的内部结构。
优选地,还包括:第二隔离结构,用于限定所述晶体管的有源区,其中,所述第二隔离结构为采用硅局部氧化工艺形成的氧化层。
优选地,还包括:第三隔离结构,用于限定所述晶体管的有源区,其中,所述第三隔离结构为浅沟槽隔离。
优选地,所述MEMS传感器为压阻式传感器。
优选地,还包括:多个敏感电阻,分别为位于所述外延层中的掺杂区,其中,所述多个敏感电阻位于所述晶体管的有源区的外部。
优选地,还包括:多个第二栅叠层,分别位于所述多个敏感电阻上,其中,所述多个第二栅叠层的一个与所述多个敏感电阻中的相应一个分别组成电阻元件,用于改善压敏电阻的温度系数。
优选地,所述多个敏感电阻的个数为四个,所述MEMS器件还包括:互连,用于将所述四个敏感电阻连接成惠斯通电桥。
优选地,所述MEMS传感器为电容式传感器。
优选地,还包括:接触区,所述接触区为位于所述外延层中的掺杂区,其中,所述接触区位于所述晶体管的有源区的外部。
优选地,所述结构层的厚度为6微米至10微米。
优选地,所述第一种子层的厚度为10微米至50微米。
优选地,所述阱区从所述结构层的表面向下延伸2微米至4微米。
优选地,所述源/漏区从所述阱区的表面向下延伸0.5微米至2微米。
根据本实用新型的另一方面,提供一种MEMS器件的制造方法,包括:在衬底上形成MEMS传感器,所述MEMS传感器包括在衬底上形成的空腔以及位于空腔上的结构层;以及在MEMS传感器上形成晶体管,其中,所述晶体管的至少一部分形成在所述MEMS传感器的结构层中。
优选地,形成所述MEMS传感器的步骤包括:在衬底上形成第一种子层;在所述第一种子层中形成第一隔离结构,所述第一隔离结构用于限定所述MEMS传感器的有源区域;在所述第一隔离结构限定的有源区域内进行电化学腐蚀,从而在所述第一种子层中形成彼此邻接的第一多孔层和第二多孔层,所述第一多孔层位于所述第二多孔层的下方,并且所述第一多孔层的孔隙率高于所述第二多孔层;进行退火,使得所述第一多孔层转变成所述空腔,以及所述第二多孔层转变成第二种子层。
优选地,所述第一多孔层的厚度为5.5至6.5微米,所述第二多孔层的厚度为0.5至1.5微米。
优选地,所述第一多孔层的孔隙率为70%-90%,所述第二多孔层的孔隙率为10%-40%。
优选地,所述第一种子层是P型硅层,所述第一隔离结构为N型掺杂区。
优选地,在电化学腐蚀中,所述第一种子层连接电源的正电极,所述衬底连接电源的负电极。
优选地,在所述电化学腐蚀中,先后施加第一电流和第二电流,其中,所述第一电流的电流密度小于所述第二电流的电流密度。
优选地,所述第一电流的电流密度为20至50毫安每平方厘米,第二电流的电流密度为50至100毫安每平方厘米。
优选地,在所述电化学腐蚀中采用酸性溶液。
优选地,所述退火的温度高于1050摄氏度。
优选地,在形成第一隔离结构的步骤和进行电化学腐蚀的步骤之间,还包括:在所述第一种子层上形成硬掩模,其中,所述硬掩模与所述第一隔离结构对准,并且与所述第一隔离结构一起限定所述MEMS传感器的有源区域。
优选地,所述硬掩模为氮化硅层。
优选地,形成结构层的步骤包括:在所述第一种子层和所述第二种子层的表面形成外延层。
优选地,所述结构层的厚度为6微米至10微米。
优选地,所述晶体管为CMOS晶体管或双极性晶体管。
优选地,所述晶体管的阱区形成在所述MEMS传感器的结构层中,所述晶体管还包括形成在阱区中的源/漏区、以及形成在阱区上的第一栅叠层。
优选地,在形成晶体管的步骤之后,还包括:在所述晶体管上形成层间介质层;在层间介质层中形成开口;以及在层间介质层上形成经由开口到达所述源/漏区和所述第一栅叠层的互连。
优选地,在形成晶体管的步骤之后,还包括:在所述晶体管上形成钝化层,用于保护所述MEMS器件的内部结构。
优选地,所述第一种子层的厚度为10微米至50微米。
优选地,所述阱区从所述结构层的表面向下延伸2微米至4微米。
优选地,所述源/漏区从所述阱区的表面向下延伸0.5微米至2微米。
优选地,形成晶体管的步骤还包括:形成第二隔离结构,用于限定所述晶体管的有源区,其中,所述第二隔离结构为采用硅局部氧化工艺形成的氧化层。
优选地,形成晶体管的步骤还包括:形成第三隔离结构,用于限定所述晶体管的有源区,其中,所述第三隔离结构为浅沟槽隔离。
优选地,所述MEMS传感器为压阻式传感器。
优选地,形成MEMS传感器的步骤还包括:在所述外延层中形成多个敏感电阻,其中,所述多个敏感电阻分别为位于所述晶体管的有源区的外部的多个掺杂区。
优选地,在形成多个敏感电阻的步骤之后,还包括:在所述多个敏感电阻上形成多个第二栅叠层,其中,所述多个第二栅叠层的一个与所述多个敏感电阻中的相应一个分别组成电阻元件,用于改善压敏电阻的温度系数。
优选地,所述敏感电阻的个数为四个,所述方法还包括,形成互连,所述互连将所述四个敏感电阻连接成惠斯通电桥。
优选地,所述MEMS传感器为电容式传感器。
优选地,还包括:在所述外延层中形成接触区,其中,所述接触区为位于所述晶体管的有源区的外部的掺杂区。
根据本实用新型实施例的MEMS器件,将信号处理电路的晶体管和MEMS传感器集成在单个芯片中,并且堆叠形成垂直结构的MEMS器件。MEMS传感器的结构层用于形成晶体管的阱区。该集成系统的体积减小,功耗降低。封装组件的管脚数量减少,从而有利于减小封装组件的体积、减小外部布线的复杂度以及提高可靠性。此外,外围元件的数量减少,从而可以降低电路成本。
进一步地,在该MEMS器件中,信号处理电路的晶体管位于MEMS传感器附近,从而减小寄生电容和分布电容,可以提高MEMS器件的精度。
在优选的实施例中,外延层的厚度例如是6微米至10微米,优选为8微米。晶体管的源/漏区仅位于外延层的表面2微米的范围内。因此,MEMS传感器的响应特性未受到上方的晶体管结构的显著影响。该MEMS器件可以兼顾MEMS传感器和信号处理电路的设计要求,从而实现二者的各自性能优化。
进一步地,该MEMS器件制造方法与现有的集成电路工艺兼容,可直接在集成电路生产线上应用,不需要为MEMS传感器的制作划分特别的制作区域。进一步地,由于本实用新型设计的工艺流程采用IC-MEMS-IC交叉工艺,即利用集成电路工艺的光刻、注入、刻蚀制作MEMS传感器的衬底与隔离层,然后利用MEMS电化学腐蚀工艺形成MEMS传感器的空腔结构,最后在垂直方向上采用电路工艺完成MEMS传感器与晶体管电路部分的集成,实现了MEMS传感器和信号处理电路的单片集成,不需要制作特定的MEMS或集成电路保护层,简化了工艺流程。
附图说明
通过以下参照附图对本实用新型实施例的描述,本实用新型的上述以及其他目的、特征和优点将更为清楚,在附图中:
图1至10分别示出根据本实用新型第一实施例的MEMS器件制造方法的各个阶段的示意性截面图。
图11示出根据本实用新型第二实施例的MEMS器件制造方法的一部分阶段的示意性截面图。
具体实施方式
以下将参照附图更详细地描述本实用新型的各种实施例。在各个附图中,相同的元件采用相同或类似的附图标记来表示。为了清楚起见,附图中的各个部分没有按比例绘制。
本实用新型可以各种形式呈现,以下将描述其中一些示例。
图1至10分别示出根据本实用新型第一实施例的MEMS器件制造方法的各个阶段的示意性截面图。
如图1所示,在衬底101上形成第一种子层102,以及在第一种子层102中形成第一隔离结构103以限定MEMS传感器的有源区域。
优选地,该衬底101可以为半导体衬底。更优选地,半导体衬底101例如是硅衬底。进一步优选地,半导体衬底101例如是晶向为<100>的P型硅衬底。控制衬底101的掺杂浓度,使其电阻率例如在0.5欧姆厘米的范围内。
优选地,第一种子层102例如是轻掺杂的P型硅层。控制第一种子层102的掺杂浓度,使其电阻率例如在1~5欧姆厘米的范围内。
例如,可以采用低压化学气相淀积(LPVCD)或者等离子增强型化学气相淀积(PECVD)等方法,在衬底101上淀积硅从而形成第一种子层102。第一种子层102的厚度为10微米至50微米,优选为30微米。
优选地,第一隔离结构103例如是轻掺杂的N型掺杂区。第一隔离结构103从第一种子层102的表面向下延伸,结深不小于5微米,优选为10微米。
在形成第一隔离结构103的步骤中,例如在第一种子层102的表面形成抗蚀剂层,采用光刻工艺在抗蚀剂层中形成包含开口的图案。以抗蚀剂层作为掩模,进行离子注入。在离子注入之后,可以通过灰化或溶剂中溶解来去除抗蚀剂层。
上述离子注入在第一种子层102的预定区域形成掺杂区作为第一隔离结构103。第一隔离结构103的图案与掩模中的开口图案的形状是相同的。
然后,在第一种子层102上形成硬掩模104,以及经由硬掩模104进行电化学腐蚀,将第一种子层102邻近表面的一部分转变成第一孔隙率的第一多孔层105和第二孔隙率的第二多孔层106,如图2所示。
在该实施例中,在电化学腐蚀中采用不同的电流进行两次腐蚀,使得形成的多孔层的典型特征为两层结构,分别为第一孔隙率的第一多孔层105和第二孔隙率的第二多孔层106。第一多孔层105位于第二多孔层106的下方,并且第一孔隙率大于第二孔隙率。
在形成硬掩模104的步骤中,例如在第一种子层102的表面形成绝缘层以及图案化绝缘层。该绝缘层的厚度例如为数百纳米,优选为150至200纳米。
可以采用磁控溅射或者等离子增强型化学气相淀积(PECVD)等方法,在第一种子层102淀积氮化硅从而形成绝缘层。
在图案化绝缘层的步骤中,例如在绝缘层的表面形成抗蚀剂层,采用光刻工艺在抗蚀剂层中形成包含开口的图案。以抗蚀剂层作为掩模,采用选择性的蚀刻剂去除绝缘层的暴露部分。由于蚀刻的选择性,该蚀刻可以在第一种子层102的表面停止。在蚀刻之后,可以通过灰化或溶剂中溶解来去除抗蚀剂层。
在电化学腐蚀的步骤中,将上述图案化的绝缘层作为硬掩模104。硬掩模104中的开口与第一隔离结构103限定的有源区域相对应,该开口的尺寸小于或等于有源区的尺寸。优选地,硬掩模104中的开口与第一隔离结构103对齐。
在第一种子层102经由硬掩模104中的开口暴露的表面上连接正电极,在衬底101与第一种子层102相对的表面上连接负电极,然后将整个半导体结构浸入酸性溶液中,例如乙醇/氢氟酸/水的混合液,或丙酮/氢氟酸/水的混合液。
将外部电源连接至正负电极,并且先后施加不同大小的电流。第一电流密度一般为20至50毫安每平方厘米,第二电流密度一般为50至100毫安每平方厘米。优选地,第一电流密度为30至40毫安每平方厘米,第二电流密度为60至70毫安每平方厘米。
在上述正极和负极之间流过的电流,在所述硬掩模104中的开口对应的种子层邻近表面的区域中产生电化学腐蚀,从而形成第一多孔层105和第二多孔层106。然后将正负电极从所述第一种子层102和衬底101上去除,停止电化学腐蚀。将整个半导体结构从腐蚀液中取出,进行清洗,从而完成电化学腐蚀步骤。然后,采用选择性的蚀刻剂去除硬掩模104,进行清洗和干燥,从而可以在随后的工艺中继续形成附加的层。
在上述的电化学腐蚀步骤中,采用硬掩模104和第一隔离结构103一起限定第一多孔层105和第二多孔层106的位置。进一步地,控制上述电化学腐蚀的腐蚀电流和腐蚀时间的大小,从而控制第一多孔层105和第二多孔层106的孔隙率和厚度。第一多孔层的厚度可以为5.5至6.5微米,第二多孔层的厚度可以为0.5至1.5微米,例如,第一多孔层105的孔隙率为70%-90%,厚度约为6微米,第二多孔层106的孔隙率10%-40%,厚度约为1微米。在该实施例中,第一多孔层105和第二多孔层106的总厚度小于第一隔离结构103的结深,使得所述第一隔离结构103可以限定第一多孔层105和第二多孔层106的横向延伸区域。
然后,在氢气环境中进行退火,使得第一多孔层105和第二多孔层106中的多孔硅相互融合。第一多孔层105由于孔隙率较大,在硅融合的过程中形成空腔107,第二多孔层106由于孔隙率较小,在硅融合的过程中致密化,从而形成覆盖在空腔上方致密的第二种子层108,如图3所示。
在上述的退火步骤中,退火温度一般高于1050摄氏度,时间为5分钟至30分钟。优选地,退火温度为1100至1300摄氏度,时间为20分钟。在该温度下的退火可以获得准单晶结构的第二种子层108。在该实施例中,采用氢气环境,以防止第二种子层的氧化。在替代的实施例中,可以采用惰性气体替代氢气,从而实现类似的效果。
第二种子层108主要由第二多孔层106的硅融合形成,二者的厚度相当。在该实施例中,第二种子层108的厚度约为1微米。
然后,在第一种子层102和第二种子层108的表面上形成外延层110,如图4所示。
例如,可以采用低压化学气相淀积(LPVCD)或者等离子增强型化学气相淀积(PECVD)等方法,在第一种子层102和第二种子层108的表面上外延生长单晶硅,从而形成外延层110。外延生长温度一般高于1050摄氏度。优选地,外延生长温度为1100至1300摄氏度。通过控制气相前驱体的组成和浓度以及淀积时间,可以控制外延层110的厚度。
在该实施例中,外延层110的厚度例如是6微米至10微米,优选为8微米。在外延层110和第二种子层108的厚度分别为8微米和1微米的情形下,由二者组成的结构层的厚度约为9微米。在最终的MEMS器件中,外延层110和第二种子层108一起作为MEMS传感器的结构层。结构层的厚度与MEMS传感器的灵敏度和结构强度相关。如果结构层的厚度过大,则灵敏度低,如果厚度过小,则结构强度低导致器件损坏和可靠性差。
该外延层110可以原位掺杂成N型,或者在淀积之后采用单独的离子注入掺杂成N型。控制外延层110的掺杂浓度,使其电阻率例如在1~5欧姆厘米的范围内。
然后,在外延层110中形成阱区112和第二隔离结构111,如图5所示。
该外延层110将用于形成晶体管,该晶体管可以是互补金属氧化物半导体场效应(CMOS)晶体管或双极性晶体管,第二隔离结构111用于限定晶体管的有源区。在晶体管为N型金属氧化物半导体场效应晶体管(N-MOSFET)的情形下,阱区112例如是轻掺杂的P型掺杂区。该阱区112从外延层110的表面向下延伸的深度小于5微米,优选为2微米至4微米,使得该阱区位于外延层110内。
在形成阱区112的步骤中,例如在外延层110的表面形成抗蚀剂层,采用光刻工艺在抗蚀剂层中形成包含开口的图案。以抗蚀剂层作为掩模,进行离子注入。在离子注入之后,可以通过灰化或溶剂中溶解来去除抗蚀剂层。
上述离子注入在外延层110的预定区域形成掺杂区作为阱区112。阱区112的图案与掩模中的开口图案的形状是相同的。
在形成第二隔离结构111的步骤中,例如在外延层110的表面采用硅局部氧化工艺(LOCOS)形成氧化层,作为第二隔离结构111。
LOCOS工艺是以氮化硅层作为硬掩模进行的局部区域氧化工艺,其中利用硬掩模的图案限定氧化区域。在形成第二隔离结构111之后,采用选择性的蚀刻剂去除硬掩模104,进行清洗和干燥。
然后,在MEMS传感器为压阻式传感器的情形下,在外延层110中形成例如四个敏感电阻113,如图6所示。所述四个敏感电阻113对称分布于晶体管的有源区外围,例如位于空腔107的外部区域中。
优选地,敏感电阻113例如是轻掺杂的P型掺杂区。敏感电阻113从外延层110的表面向下延伸,结深约为1微米至2微米。
在形成敏感电阻113的步骤中,例如在外延层110的表面形成抗蚀剂层,采用光刻工艺在抗蚀剂层中形成包含开口的图案。以抗蚀剂层作为掩模,进行离子注入,注入剂量例如约为E15每平方厘米。在离子注入之后,可以通过灰化或溶剂中溶解来去除抗蚀剂层。
上述离子注入在外延层110的预定区域形成掺杂区作为敏感电阻113。敏感电阻113的图案与掩模中的开口图案的形状是相同的。
在替代的实施例中,例如在MEMS传感器为电容式传感器的情形下,可以采用接触区代替压敏电阻。该接触区用于连接外部电极,从而可以检测结构层与衬底之间的电容变化。
然后,在半导体结构的表面上依次形成氧化物层和导体层,并且将氧化物层和导体层图案化成包括栅氧化物114和栅极导体115的栅叠层,以及在阱区112中形成源/漏区116,如图7所示。
在上述形成氧化物层的步骤中,例如,在阱区112和敏感电阻113的表面上,采用热氧化形成氧化物层。通过控制热氧化的温度和时间,可以控制氧化物层的厚度。
在上述形成导体层的步骤中,通过已知的淀积工艺,在氧化物层上形成导体层。上述淀积工艺例如是选自电子束蒸发(EBM)、化学气相淀积(CVD)、原子层淀积(ALD)、溅射中的一种。通过控制淀积工艺的参数,例如气相前驱体的浓度、淀积温度和淀积时间,可以控制导体层的厚度。
在上述步骤中形成的氧化物层和导体层例如覆盖半导体结构的整个表面。
在上述图案化的步骤中,例如在导体层的表面形成抗蚀剂层,采用光刻工艺在抗蚀剂层中形成包含开口的图案。以抗蚀剂层作为掩模,采用选择性的蚀刻剂去除导体层和氧化物层的暴露部分。由于蚀刻的选择性,该蚀刻可以在外延层110、阱区112、敏感电阻113的表面停止。在蚀刻之后,可以通过灰化或溶剂中溶解来去除抗蚀剂层。
在图案化步骤之后,在阱区112和敏感电阻113的表面上均形成由栅氧化物114和栅极导体115组成的栅叠层。在一个实例中,栅氧化物114例如由氧化硅组成,栅极导体例如由掺杂的多晶硅组成。栅氧化物114的厚度约为25纳米至30纳米,栅极导体115的厚度约为450纳米。
应当注意,尽管位于敏感电阻113上的栅叠层与阱区112上方的栅叠层的结构相同,但前者并非作为晶体管的一部分。实际上,位于敏感电阻113上的栅叠层与敏感电阻113串联连接,共同组成电阻元件,位于电流路径上。电阻元件利用栅叠层可以改善压敏电阻的温度系数。
在上述形成源/漏区的步骤中,可以形成光致抗蚀剂掩模,光致抗蚀剂掩模中的开口暴露晶体管的有源区,并且,光致抗蚀剂掩模遮挡半导体结构的剩余部分。以抗蚀剂层以及栅极导体一起作为掩模,进行离子注入。在离子注入之后,可以通过灰化或溶剂中溶解来去除抗蚀剂层。
上述离子注入在阱区112中的预定区域形成掺杂区作为源/漏区116,该源/漏区116例如与栅极导体115是自对准的。在晶体管为N型金属氧化物半导体场效应晶体管(N-MOSFET)的情形下,源/漏区116是N型掺杂区。该源/漏区116从阱区112的表面向下延伸的深度为0.5微米至2微米,使得该源/漏区116位于阱区112内。
然后,在晶体管的有源区中,在栅叠层的两侧形成栅极侧墙117,以及在栅极导体115的表面形成硅化物层118,如图8所示。
在上述形成栅极侧墙的步骤中,通过上述已知的淀积工艺,在半导体结构的表面上形成共形的(conformal)氮化物层。在一个示例中,该氮化物层为厚度约5纳米至30纳米的氮化硅层。在未使用掩模的情形下,通过各向异性的蚀刻工艺(例如,反应离子蚀刻),去除氮化物层的横向延伸的部分,使得氮化物层位于栅极导体115的垂直部分保留,从而形成栅极侧墙117。
在上述形成硅化物层的步骤中,通过上述已知的淀积工艺,在半导体结构的表面形成金属层。该金属层由选自Ni、W、Ti、Co以及这些元素与其它元素的合金构成的组中的一种组成。在一个示例中,该金属层是通过溅射淀积的Co层。然后,进行热退火,例如在300摄氏度至500摄氏度的温度下热退火1-10秒钟。
热退火使得金属层在栅极导体115的表面进行硅化反应以形成硅化物层118。硅化物层118可以减小栅极导体115的接触电阻。通过上述已知的干法蚀刻和湿法蚀刻于硅化物湿法蚀刻去除金属层未反应的部分。在优选的实施例中,在源/漏区116的表面也可以形成硅化物层118。
然后,在半导体结构的表面上形成层间介质层119,以及在层间介质层119中形成到栅极导体115和源/漏区116的开口,以及在层间介质层119上形成经由开口电连接栅极导体115和源/漏区116的互连120,如图9所示。
在上述形成层间介质层119的步骤中,例如通过上述已知的淀积工艺,优选地,采用化学气相淀积,在半导体结构的表面形成硼磷硅玻璃(BPSG)或正硅酸乙酯(TEOS)作为层间介质层119。
在上述形成开口的步骤中,例如在层间介质层119的表面形成抗蚀剂层,采用光刻工艺在抗蚀剂层中形成包含开口的图案。以抗蚀剂层作为掩模,采用选择性的蚀刻剂去除绝缘层的暴露部分。由于蚀刻的选择性,该蚀刻可以在栅极导体115和源/漏区116的表面停止。在蚀刻之后,可以通过灰化或溶剂中溶解来去除抗蚀剂层。
在上述形成互连的步骤中,例如通过溅射形成导体层,例如铝。该导体层填充层间介质层119中的开口,并且还覆盖层间介质层119的表面。优选地,可以进一步采用化学机械平面化(CMP)平整导体层的表面,以及将导体层图案化成互连120。
上述互连120不仅提供至晶体管的栅极导体115和源/漏区116的电连接,而且提供经由栅极导体115和栅氧化物114至敏感电阻113的电连接。在栅极导体115上形成硅化物层的情形下,互连120经由硅化物层118电连接至栅极导体115。
在MEMS传感器为压阻式传感器的情形下,上述互连120将四个敏感电阻113连接成惠斯通电桥。
然后,通过上述已知的淀积工艺,在半导体结构的整个表面上形成钝化层121,如图10所示。在该实施例中,钝化层例如由氧化硅或氮化硅组成,用于保护MEMS器件的内部结构。
图11示出根据本实用新型第二实施例的MEMS器件制造方法的一部分阶段的示意性截面图。在图11所示的步骤之前,已经执行图1至图4所示的步骤,在图11所示的步骤之后,将继续执行图6至图10所示的步骤。
如图11所示,在第二实施例中,采用第三隔离结构211代替第二隔离结构111。第三隔离结构211是浅沟槽隔离(STI)。
在上述形成第三隔离结构的步骤中,在外延层110的表面上形成抗蚀剂层,采用光刻工艺在抗蚀剂层中形成包含开口的图案。以抗蚀剂层作为掩模,采用选择性的蚀刻剂去除外延层的暴露部分,从而在外延层中形成浅沟槽。通过控制蚀刻时间,可以控制浅沟槽的深度。在蚀刻之后,可以通过灰化或溶剂中溶解来去除抗蚀剂层。
然后,通过已知的淀积工艺,在半导体结构的表面上形成绝缘层,该绝缘层的厚度至少足以填充浅沟槽。例如通过化学机械平面化(CMP)平整半导体结构的表面并且去除绝缘层位于浅沟槽外部的部分,形成浅沟槽隔离(STI)。
根据第二实施例的MEMS器件制造方法的其他方面与根据第一实施例的MEMS器件制造方法相同,在此不再详述。
在上述实施例的MEMS器件制造方法中,将信号处理电路的晶体管和MEMS传感器堆叠形成垂直结构的MEMS器件,从而可以将二者集成在单个芯片中。MEMS传感器的结构层用于形成晶体管的阱区。外延层的厚度例如是6微米至10微米,优选为8微米。晶体管的源/漏区仅位于外延层的表面2微米的范围内。因此,MEMS传感器的响应特性未受到上方的晶体管结构的显著影响。
进一步地,该MEMS器件制造方法与现有的集成电路工艺兼容,可直接在集成电路生产线上应用,不需要为MEMS传感器的制作划分特别的制作区域。进一步地,由于本实用新型设计的工艺流程采用IC-MEMS-IC交叉工艺,即利用集成电路工艺的光刻、注入、刻蚀制作MEMS传感器的衬底与隔离层,然后利用MEMS电化学腐蚀工艺形成MEMS传感器的空腔结构,最后在垂直方向上采用电路工艺完成MEMS传感器与晶体管电路部分的集成,实现了MEMS传感器和信号处理电路的单片集成,不需要制作特定的MEMS或集成电路保护层,简化了工艺流程。
进一步地,在该MEMS器件中,信号处理电路的晶体管位于MEMS传感器附近,垂直堆叠的方式使实际的管芯面积减小,从而减小寄生电容和分布电容,可以提高MEMS器件的精度。集成系统的体积减小,功耗降低。封装组件的管脚数量减少,从而有利于减小封装组件的体积、减小外部布线的复杂度以及提高可靠性。此外,外围元件的数量减少,从而可以降低电路成本。
依照本实用新型的实施例如上文所述,这些实施例并没有详尽叙述所有的细节,也不限制该实用新型仅为所述的具体实施例。显然,根据以上描述,可作很多的修改和变化。本说明书选取并具体描述这些实施例,是为了更好地解释本实用新型的原理和实际应用,从而使所属技术领域技术人员能很好地利用本实用新型以及在本实用新型基础上的修改使用。本实用新型的保护范围应当以本实用新型权利要求所界定的范围为准。
本文用于企业家、创业者技术爱好者查询,结果仅供参考。