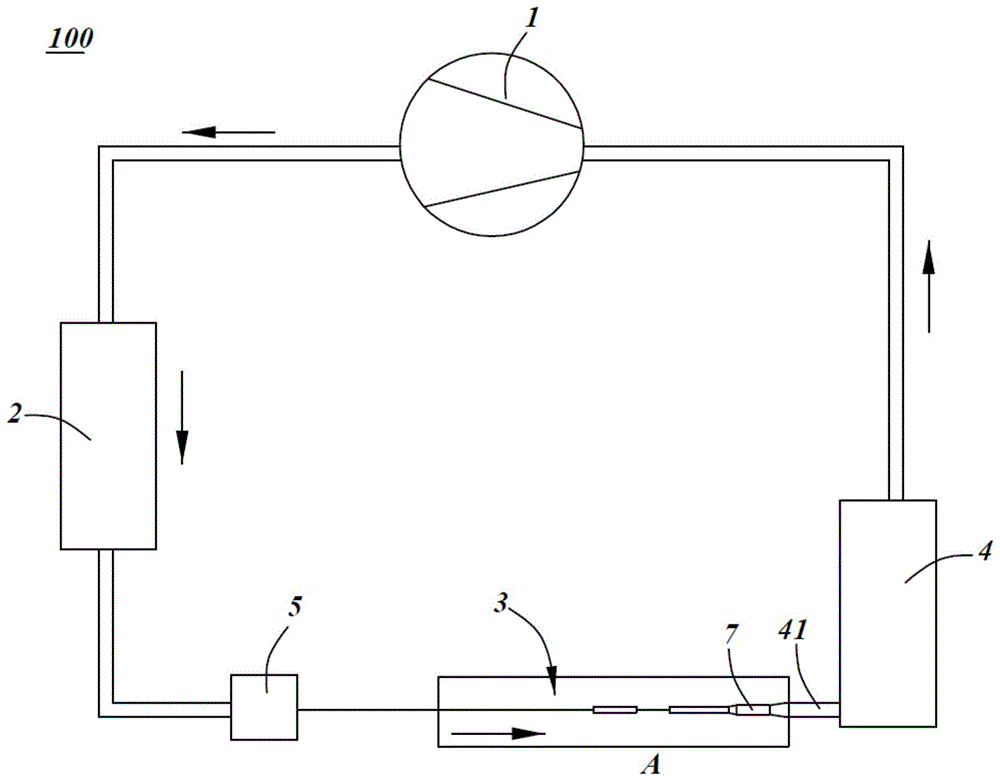
本实用新型涉及一种制冷系统,以及具有该制冷系统的制冷电器,属于家用电器技术领域。
背景技术:
目前常见的冰箱、冷柜等制冷电器,其制冷系统中,冷凝器和蒸发器之间通常采用毛细管进行节流降压。原理上讲,高压中温的液相制冷剂进入毛细管,在毛细管壁面的摩擦力作用下,制冷剂受到的阻力逐渐增大,制冷剂压力和温度也在逐渐降低,最终在毛细管出口处达到了蒸发压力下的两相制冷剂状态,高速进入蒸发器。
然而,在毛细管和蒸发器的连接处,由于管路内径陡然剧增而导致压力突变的影响,制冷剂从毛细管高速喷出后发生相变而产生大量气泡,随着压力持续降低,这些气泡增大直至破裂,由此产生喷发噪音,这些噪音会导致冰箱的整体噪音增大,用户体验感极差。
技术实现要素:
为了解决现有技术中的问题,本实用新型提供一种制冷系统,以及具有该制冷系统的制冷电器。
为实现上述目的,本实用新型一实施方式提供了一种制冷系统,包括依序连接的压缩机、冷凝器、节流管路、过渡管和蒸发器,所述节流管路包括毛细管主体和至少两个扩张管;
其中一个所述扩张管串接在所述毛细管主体和所述过渡管之间并构成末位扩张管;
其余所述扩张管串接在所述毛细管主体中以将所述毛细管主体分隔成至少两段毛细管,并构成中间扩张管;
每个所述扩张管的管内通道截面积大于所述毛细管主体的管内通道截面积且小于所述过渡管的管内通道截面积,所述过渡管的管内通道截面积小于所述蒸发器的制冷剂管的管内通道截面积。
作为本实用新型一实施方式的进一步改进,所述扩张管包括主体管;
所述主体管设为管内通道截面积恒定的第一等径管;
或者,所述主体管包括管内通道截面积恒定的第一等径管和串接在所述第一等径管后方的至少一段第二等径管,所述第二等径管的管内通道截面积大于所述第一等径管的管内通道截面积。
作为本实用新型一实施方式的进一步改进,所述第二等径管的数目设置为由前向后依次串接且管内通道截面积逐段增大的两段或以上。
作为本实用新型一实施方式的进一步改进,所述中间扩张管设置为:其主体管的前部末端与在前的一段所述毛细管的后部末端相接呈垂直台阶面,其主体管的后部末端与在后的一段所述毛细管的前部末端相接呈垂直台阶面;
所述末位扩张管设置为:其主体管的前部末端与最后一段所述毛细管的后部末端相接呈垂直台阶面,其主体管的后部末端与所述过渡管的前部末端相接。
作为本实用新型一实施方式的进一步改进,所述中间扩张管设置为:在前的一段所述毛细管的后部末端穿过该中间扩张管的主体管的前部末端并向后延伸入该中间扩张管内,在后的一段所述毛细管的前部末端穿过该中间扩张管的主体管的后部末端并向前延伸入该中间扩张管内;
所述末位扩张管设置为:最后一段所述毛细管的后部末端穿过该末位扩张管的主体管的前部末端并向后延伸入该末位扩张管内,该末位扩张管的主体管的后部末端与所述过渡管的前部末端相接。
作为本实用新型一实施方式的进一步改进,所述扩张管还包括串接在其主体管的前部末端和在前的一段所述毛细管的后部末端之间的扩口管,所述扩口管的管内通道截面积由前向后自所述毛细管主体的管内通道截面积逐渐增大成所述第一等径管的管内通道截面积。
作为本实用新型一实施方式的进一步改进,所述中间扩张管还包括串接在其主体管的后部末端和在后的一段所述毛细管的前部末端之间的收口管,所述收口管的管内通道截面积由前向后自主体管的管内通道截面积逐渐减小成所述毛细管主体的管内通道截面积;
所述末位扩张管主体管的后部末端与所述过渡管的前部末端相接。
作为本实用新型一实施方式的进一步改进,所述毛细管主体的管内通道截面积恒定,所述主体管的管内通道截面积是所述毛细管主体的管内通道截面积的4至75倍。
作为本实用新型一实施方式的进一步改进,所述过渡管包括:
第三等径管;
第二扩口管,串接在所述末位扩张管的主体管的后部末端和所述第三等径管的前部末端之间,其管内通道截面积由前向后自所述末位扩张管的主体管的后部末端管内通道截面积逐渐增大成所述第三等径管的管内通道截面积;以及,
第三扩口管,串接在所述第三等径管的后部末端和所述蒸发器的制冷剂管的前部末端之间,其管内通道截面积由前向后自所述第三等径管的管内通道截面积逐渐增大成所述蒸发器的制冷剂管的管内通道截面积。
作为本实用新型一实施方式的进一步改进,所述过渡管设置成扩口过渡管,该扩口过渡管的管内通道截面积由前向后自所述末位扩张管的主体管的后部末端管内通道截面积逐渐增大成所述蒸发器的制冷剂管的管内通道截面积。
作为本实用新型一实施方式的进一步改进,所述节流管路整体设置为由铜材或钢材一体成型的硬质管;
或者,所述节流管路整体设置为软管;
或者,所述节流管路设置为部分管段为软管且其余部分管段为由铜材或钢材一体成型的硬质管。
作为本实用新型一实施方式的进一步改进,所述节流管路中,自所述末位扩张管的后部末端,由后向前至少延续到最后一个所述中间扩张管的前部末端,均设置为软管。
作为本实用新型一实施方式的进一步改进,所述过渡管的全部或自其前部末端的部分设置为软管并且与所述节流管路的软管一体成型。
作为本实用新型一实施方式的进一步改进,所述节流管路设置在将所述冷凝器的排出端和所述蒸发器的进入端连通的唯一一条制冷剂流动路径中。
作为本实用新型一实施方式的进一步改进,所述冷凝器的排出端设置有干燥过滤器,所述节流管路的前部末端固定配接于所述干燥过滤器;
或者,所述冷凝器的排出端由前向后依次设置有干燥过滤器和电磁阀,所述节流管路的前部末端固定配接于所述电磁阀。
为实现上述目的,本实用新型一实施方式提供了一种包含所述制冷系统的制冷电器。
与现有技术相比,本实用新型的有益效果在于:通过在毛细管主体中间以及后部末端设置扩张管,以及在末位扩张管和蒸发器的制冷剂管之间设置过渡管,并设置毛细管主体、扩张管、过渡管和蒸发器的制冷剂管的管内通道横截面积的大小关系,实现了喷发和脉动的逐级衰减和平顺,大大降低喷发中气泡破裂所产生的噪音问题,减小喷发脉动沿制冷系统的管路向外、向前以及向后的传递,避免振动传递造成的噪音放大现象。
附图说明
图1是本实用新型第一实施例的制冷系统的示意图;
图2a是本实用新型第一实施例的节流管路的结构示意图;
图2b是本实用新型第一实施例的节流管路、过渡管及蒸发器的部分制冷剂管(对应图1中a区)的结构示意图;
图3a是本实用新型第一实施例的管连接机构的结构分解剖面示意图;
图3b是本实用新型第一实施例的管连接机构与软管配合的结构剖面示意图;
图4a是本实用新型第二实施例的节流管路的结构示意图;
图4b是本实用新型第二实施例的节流管路、过渡管及蒸发器的部分制冷剂管(对应图1中a区)的结构示意图;
图5a是本实用新型第三实施例的节流管路的结构示意图;
图5b是本实用新型第三实施例的节流管路、过渡管及蒸发器的部分制冷剂管(对应图1中a区)的结构示意图;
图6a是本实用新型第四实施例的节流管路的结构示意图;
图6b是本实用新型第四实施例的节流管路、过渡管及蒸发器的部分制冷剂管(对应图1中a区)的结构示意图;
图7是本实用新型第五实施例的制冷系统的示意图。
具体实施方式
以下将结合附图所示的具体实施方式对本实用新型进行详细描述。但这些实施方式并不限制本实用新型,本领域的普通技术人员根据这些实施方式所做出的结构、方法、或功能上的变换均包含在本实用新型的保护范围内。
参看图1至图3b示例了本实用新型第一实施例的制冷系统100。
参图1,制冷系统100具有供制冷剂循环流动的流动回路,沿着制冷剂流动方向限定由前向后的方向,制冷系统100包括依序串接连接的压缩机1、冷凝器2、节流管路3、过渡管7和蒸发器4。
具体地,压缩机1的排气管连接于冷凝器2的进入端,压缩机1的回气管连接于蒸发器4的排出端;节流管路3连通在冷凝器2的排出端和蒸发器4的进入端之间。
制冷系统100中制冷剂的循环过程理论上大致为:压缩机1排气管的高温高压过热制冷剂气体,进入冷凝器2被冷凝为高压的饱和或者过冷液体,而后进入节流管路3节流降压,再之后流经过渡管7后进入蒸发器4中汽化为低温低压的制冷剂气体,返回压缩机1内以被重新压缩成高温高压过热制冷剂气体,由此完成整个循环过程。
本实用新型中对节流管路3、过渡管7与蒸发器4的制冷剂管41的进入端所形成的管路结构予以改进,以解决现有技术中喷发噪音的问题。
具体地,节流管路3包括毛细管主体30和扩张管31。毛细管主体30即为管内通道截面积恒定的毛细管,其构造出节流管路3的一半以上的长度;扩张管31的管内通道截面积大于毛细管主体30的管内通道截面积。
参图2a和图2b,节流管路3包括由前向后依次间隔设置的至少两个扩张管31。其中一个扩张管31串接在毛细管主体30和过渡管7之间,也即该扩张管31限定出节流管路3的后部末端;其余扩张管31串接在毛细管主体30中,以将毛细管主体30分隔成至少两段毛细管。
在本申请中,将串接在毛细管主体30和过渡管7之间的一个扩张管31定义为末位扩张管31-2,将串接在毛细管主体30中的其余扩张管31定义为中间扩张管31-1,以进行区分,从而便于理解和表述。
如前所述,扩张管31的数目为至少两个,则中间扩张管31-1的数目为至少一个,相应的,该至少一个中间扩张管31-1将毛细管主体30分隔成至少两段毛细管。换个角度讲,毛细管主体30包括间隔设置的至少两段毛细管,相邻两段毛细管通过一中间扩张管31-1相连通,由此,节流管路3构成[毛细管——中间扩张管31-1]*n——毛细管——末位扩张管31-2的管路结构,其中n为正整数。
在本实施例中,扩张管31的数目示例为两个,一个末位扩张管31-2,一个中间扩张管31-1;其中,一个中间扩张管31-1将毛细管主体30分隔出两段毛细管,即毛细管30-1和毛细管30-2;一个末位扩张管31-2连接在最后一段毛细管(也即毛细管30-2)和过渡管7之间。当然,可以理解的,扩张管31的数目可以为三个甚至更多个,则相应的,毛细管主体30被分隔出三段甚至更多段毛细管。
另外,节流管路3的管内通道截面积小于过渡管7的管内通道截面积,也即,扩张管31的管内通道截面积小于过渡管7的管内通道截面积;并且,过渡管7的管内通道截面积则小于蒸发器4的制冷剂管41的管内通道截面积。
由此,本实施例的制冷系统100,相较于现有技术,通过在毛细管主体30中间以及后部末端设置扩张管31,以及在末位扩张管31-2和蒸发器4的制冷剂管41之间设置过渡管7,并设置毛细管主体30、扩张管31、过渡管7和蒸发器4的制冷剂管41的管内通道横截面积的大小关系,实现了喷发和脉动的逐级衰减和平顺,大大降低喷发中气泡破裂所产生的噪音问题,减小喷发脉动沿制冷系统100的管路向外、向前以及向后的传递,避免振动传递造成的噪音放大现象。
其中,一方面,由于中间扩张管31-1的后方具有毛细管30-2,在毛细管30-2的保压作用下,制冷剂在从毛细管30-1进入中间扩张管31-1时不会像现有毛细管喷发口一样的高速喷发,制冷剂在中间扩张管31-1内流动时也不会像现有毛细管喷发口一样的产生大量气泡,且气泡也是以较小体积下破裂,不会产生较大噪音;再一方面,制冷剂更多地在从毛细管30-2进入末位扩张管31-2、过渡管7时进行喷发,而由于在前方的中间扩张管31-1处制冷剂已经部分由液相转化为气相,进入末位扩张管31-2的制冷剂中气相比例更大(相对现有毛细管喷发口而言),之后从末位扩张管31-2经过渡管7至蒸发器4的制冷剂管41管内通道截面积逐级增大,液流脉动得到衰减和平顺,使得喷发噪音很小;另一方面,由于液流脉动经过至少两个扩张管31逐级得到衰减和平顺之后,振动大大减小,且沿着制冷剂的管路向前的振动会在中间扩张管31-1处被吸收,而向后的振动会在末位扩张管31-2处被吸收,大大减小了喷发时脉动向外传递而导致噪声放大的现象。
进一步地,继续参看图1,冷凝器2的排出端和蒸发器4的进入端通过唯一一条制冷剂流动路径相连通,而节流管路3设置在将冷凝器2的排出端和蒸发器4的进入端连通的该唯一一条制冷剂流动路径中,也即,在制冷系统100进行制冷时,冷凝器2中的制冷剂必然需要通过节流管路3进入蒸发器4。
在本实施例中,冷凝器2的排出端设置有干燥过滤器5,节流管路3的前部末端固定配接于干燥过滤器5,也即最前的一段毛细管30-1的前部末端固定配接于干燥过滤器5。
进一步地,任意两个扩张管31可以设置为形状相同或不同。
在本实施例中,任意两个扩张管31可以设置为形状相同。每个扩张管31包括主体管,所述主体管设为管内通道截面积恒定的第一等径管。更具体地,每个扩张管31设置为等径管结构。
具体地,对于中间扩张管31-1而言,其设置为:其主体管的前部末端与在前的一段毛细管30-1的后部末端相接呈垂直台阶面,并且,其主体管的后部末端与在后的一段毛细管30-2的前部末端相接呈垂直台阶面。
对于末位扩张管31-2而言,其设置为:其主体管的前部末端与毛细管30-2的后部末端相接呈垂直台阶面,并且,其主体管的后部末端与过渡管7的前部末端相接。
进一步地,每个扩张管31的主体管的管内通道截面积是毛细管主体30的管内通道截面积的4至75倍。
进一步地,在本实施例中,过渡管7包括等径管72、扩口管71和扩口管73。
扩口管71和扩口管73分别连接于等径管72的前部末端、后部末端。
其中,扩口管71串接在节流管路3的后部末端和等径管72的前部末端之间,具体来讲串接在末位扩张管31-2的主体管的后部末端和等径管72的前部末端之间,其管内通道截面积由前向后自末位扩张管31-2的主体管的后部末端的管内通道截面积逐渐增大成等径管72的管内通道截面积,也即,其前部末端的管内通道截面积等于末位扩张管31-2的主体管的后部末端的管内通道截面积,其后部末端的管内通道截面积等于等径管72的管内通道截面积。
扩口管73串接在等径管72的后部末端和蒸发器4的制冷剂管41的前部末端之间,其管内通道截面积由前向后自等径管72的管内通道截面积逐渐增大成蒸发器4的制冷剂管41的管内通道截面积。
这样,通过设置扩口管71和扩口管73,可以实现过渡管7的等径管72与节流管路3、蒸发器4之间管内通道截面积的平缓过渡,避免管内通道截面积的突变所引起的噪音问题。当然,在变化实施例中,过渡管7还可以设置为扩口过渡管,该扩口过渡管的管内通道截面积由前向后自末位扩张管31-2的主体管的后部末端的管内通道截面积逐渐增大成蒸发器4的制冷剂管41的管内通道截面积,也即节流管路3通过一扩口过渡管连接蒸发器4的制冷剂管41。
优选地,本实施例中,节流管路3和过渡管7均设置为圆形管,节流管路3和过渡管7的各个位置处的管内通道横截面为圆形。当然,节流管路3和过渡管7的各个位置处的管内通道横截面的形状不限于此,也可以是方形、六边形、椭圆形、腰形或其它可行的合适形状。
相对应的,前文中所述的各个管内通道截面积的大小关系,则对应于管内径的大小关系。例如,节流管路3的管内通道截面积小于过渡管7的管内通道截面积,则相应的,节流管路3的管内径小于过渡管7的管内径。
另外,本实施例中的扩口管71的管内壁可以设置为由前向后呈斜面或内凸弧面或外凹弧面,同样的,扩口管73的管内壁也可以设置为由前向后呈斜面或内凸弧面或外凹弧面,当然,变化实施例中的所述扩口过渡管的管内壁也可以设置为由前向后呈斜面或内凸弧面或外凹弧面。
优选地,节流管路3设置为:部分管段为软管且其余部分管段为由铜材或钢材一体成型的硬质管。具体地,节流管路3的后部管段为软管且前部管段为由铜材或钢材一体成型的硬质管。
在本实施例中,自末位扩张管31-2的后部末端(位置如图2b的c8指示),由后向前至少延续到最后一个中间扩张管31-1的前部末端(位置如图2b的c2指示),均设置为软管,也即,图2b中c2指示位置至c8指示位置之间的节流管路3管段为软管,而c2指示位置之前的节流管路3管段为硬质管,这样,一方面,末位扩张管31处的喷发中的气泡破裂的振动作用于软管管壁,该振动可以被软管所吸收,从而保证振动和噪声的有效降低;另一方面,软管还可以避免振动沿着节流管路3向前、向后传递,从而减小振动传递。
更为优选地,节流管路3中,自末位扩张管31-2的后部末端(位置如图2b的c8指示),由后向前延续到最前一个中间扩张管31-1的前部末端,均设置为软管,也即,全部扩张管31和位于扩张管31之间的毛细管都设置为软管,而仅有最前的一段毛细管30-1设置为硬质管;可以理解的,对应于附图中本实施例,如前所述仅有一个中间扩张管31-1,则最前一个中间扩张管31-1也即最后一个中间扩张管31-1也即全部中间扩张管31-1,则最前一个中间扩张管31-1的前部末端即图中c2指示位置处。这样,使得发生于每个扩张管31中的气泡破裂的振动都直接作用于软管管壁,该振动可以被软管所吸收,从而降低振动的向外传递。
进一步地,本实施例中,节流管路3的硬质管与干燥过滤器5可以通过焊接或其它方式固定配接,也即,毛细管主体30的前部末端与干燥过滤器5可以通过焊接或其它方式固定配接。
并且,节流管路3的软管与过渡管7的全部或部分一体成型,也即过渡管7的全部或部分也设置为软管并且过渡管7的软管和节流管路3的软管一体设置。例如,过渡管7可以是:扩口管71为软管而其余管段为硬质管,或者过渡管7可以是扩口管71和等径管72为软管而其余管段为硬质管,或者过渡管7全部为软管。这样,可以使得过渡管7处的气泡破裂的振动作用于软管管壁,该振动可以被软管所吸收,从而保证振动和噪声的有效降低。
结合前述可得,在本实施例中,由节流管路3、过渡管7和蒸发器4的制冷剂管41所构成的管路中,设置有一体成型的软管管体:该软管管体的前部末端位于图2b所示的c2指示位置处,其与前方的硬质管管体配接于该c2指示位置处;该软管管体的后部末端位于过渡管7的中部(例如c9或c10或c11指示位置处)或后部末端(例如c12指示位置处),其与后方的硬质管管体配接于该相应位置处。
当然,可以理解的,在变化实施例中,软管管体的前部末端还可以位于除了c2的其它位置处,比如任意一段毛细管的中部(位置如图2b的c1指示、c5指示)处、或者任意一个中间扩张管31-1的中部(位置如图2b的c3指示)或后部末端(位置如图2b的c4指示)处、或者末位扩张管31-2的前部末端(位置如图2b的c6指示)处;在再一变化实施例中,软管管体的后部末端也可以位于除了c9或c10或c11或c12的其它位置处,比如位于末位扩张管31-2的后部末端(图2b所示的c8指示位置处),这种情况也即过渡管7整体设置为由铜材或钢材一体成型的硬质管,并且与节流管路3组装配接;在再一变化实施例中,软管管体的后部末端也可以位于末位扩张管31-2的中部(位置如图2b的c7指示)处或者更靠前位置处,这种情况也即末位扩张管31-2的后部管段为由铜材或钢材一体成型的硬质管,其可以通过焊接或或其它方式固定连接过渡管7,也可以与过渡管7一体成型;在另一变化实施例中,节流管路3可以是整体设置为软管,其与干燥过滤器5可以组装配接,其与过渡管7可以是固定组装配接,也可以是与过渡管7的全部或部分一体成型;在另一变化实施例中,节流管路3可以是整体设置为由铜材或钢材或其它材料一体成型的硬质管,其与干燥过滤器5可以通过焊接或其它方式固定配接,其与过渡管7可以是通过焊接或其它方式固定配接,也可以是与过渡管7的全部或部分一体成型。
进一步地,在本实施例中,参图3a和图3b,前述的软管管体和硬质管管体可通过管连接机构9实现组装连接。也即,管连接机构9可将软管管体90和硬质管管体实现固定配接,由此使得制冷剂可顺利的从软管管体90中流入硬质管管体中,或者从硬质管管体中流入软管管体90中。
为便于理解和表述,下面以软管管体90的后部末端处的管连接机构9为例,对管连接机构9的结构进行详细介绍,也即,下文中关于管连接机构9中各个构件的前、后的方位表示,均是以软管管体90在前、硬质管管体在后的方位为参照前提;相应的,对于软管管体90的前部末端处的管连接机构9而言,也即以软管管体90在后、硬质管管体在前的方位为参照前提的话,则下文中关于管连接机构9中各个构件的前、后的方位表述均应当变化为反向,例如,下文中“第一管部922形成于接头管92的后端,第二管部921形成于接头管92的前端”则应当变为“第一管部922形成于接头管92的前端,第二管部921形成于接头管92的后端”。
具体地,以软管管体90的后部末端处的管连接机构9为例,管连接机构9包括接头管92和套管91。
接头管92设置为前后延伸的直管,其具有在相对两端分别设置的第一管部922和第二管部921,第一管部922形成于接头管92的后端,第二管部921形成于接头管92的前端。
第一管部922固定相接于硬质管管体,第二管部921自后向前插置入软管管体90内,且,第二管部921过盈地撑开软管管体90。
套管91套设在软管管体90外,其自前向后地趋近接头管92运动,并套接在第二管部921外,这样,套管91可以与第二管部921共同夹持固定软管管体90,也即第二管部921从内部过盈地支撑软管管体90,同时套管91从外部向内压紧软管管体90,使得软管管体90被紧密地夹持固定在套管91与第二管部921之间。
由此,管连接机构9通过第二管部921对软管管体90的过盈支撑,并结合套管91的外部压紧,保证了软管管体90和第二管部921之间的密封性,避免制冷剂沿着软管管体90和第二管部921之间的缝隙进行泄露,同时通过套管91和接头管92二者与软管管体90之间的插接操作,即可快速实现软管管体90和硬质管管体之间的连接,无需其它额外结构件(即管连接机构9只需由套管91和接头管92二者构成即可),结构简单,操作简单方便,组装效率高,兼顾了组装效率和密封性能两方面。
进一步地,第一管部922具体可通过焊接方式连接于硬质管管体。当然,在变化实施例中,接头管92还可以与硬质管管体为一体成型体,也即在硬质管管体的末端直接加工成型出接头管92。
优选地,第二管部921的外表面9210的横截面设置为圆形,对应的,套管91的内腔设置为圆形,也即其内表面的横截面为圆形,这样,可以便于配接,并避免尖锐角度下割伤软管管体90。
进一步地,套管91的内半径r1大于第二管部921的外半径r2,套管91的内半径r1与第二管部921的外半径r2的差值(r1-r2)小于软管管体90的管壁厚度h,由此可以保证通过套管91和第二管部921进一步夹紧软管管体90。
另外,在本实施例中,第二管部921的外表面9210设置有防滑结构,当第二管部921过盈地支撑软管管体90时,所述防滑结构增大软管管体90在第二管部921上的牢固度,可以防止软管管体90从第二管部921上脱离开,同时,还可以增大制冷剂从软管管体90和第二管部921之间泄露出来的难度,保证密封效果。
所述防滑结构构造为向外凸伸出第二管部921的外表面9210的凸起,或者构造为向内凹陷于第二管部921的外表面9210的凹槽。
进一步地,接头管92具有自第二管部921向外凸伸的限位凸台920,也即,限位凸台920的外表面相对第二管部921的外表面9210远离轴线t设置。其中,限位凸台920的前端面9201可抵持套管91的后端面,由此,以限定套管91向后运动的极限位置。
这样,在对软管管体90和硬质管管体进行组装时,当套管91的后端面抵持在限位凸台920的前端面9201时,就可以完成组装,由此可以方便操作者及时判断组装到位,避免盲目性地过度组装,同时,便于精准管控制冷系统中该软管管体90处的制冷剂流动路径的长度。
优选地,限位凸台920绕第二管部921的轴线t延伸呈环形凸台,也即其围绕轴线t圆周一圈,这样,在软管管体90和硬质管管体通过管连接机构9完成组装时,限位凸台920的前端面9201可以在圆周方向上均抵持套管91的后端面,由此,进一步延长制冷剂从管连接机构9中泄露出来所需要通过的路径,增强密封效果。
进一步地,套管91的前端管部911的外径小于套管91的后端管部912的外径,以使套管91的外表面呈台阶状,也即,前端管部911相对较细而后端管部912相对较粗。前端管部911的外表面和后端管部912的外表面之间通过面9121相连接,换个角度讲,面9121可看作是后端管部912的前端面。这样,通过设置呈前细后粗的结构,在将套管91向第二管部921外部套接时,可以通过从前方推动面9121来施加推力,以便于将套管91压向限位凸台920,也即便于安装过程中的施力。
类似的,限位凸台920还自第一管部922向外凸伸,也即,限位凸台920的外表面相对第一管部922的外表面远离轴线t设置。限位凸台920的外表面和第一管部922的外表面通过面9202相连接呈台阶状,换个角度讲,面9202可看作是限位凸台920的后端面。这样,在将套管91向第二管部921外部套接时,可以通过从后方推动面9202来施加推力,以便于将套管91压向限位凸台920,也即便于安装过程中的施力。
进一步地,套管91设置为一体成型的金属件,接头管92也设置为一体成型的金属件,二者均可采用铜材或钢材或其它材质。
以上仅提供了一种管连接机构9,以应用于本制冷系统100中,从而将硬质管管体和节流管路3以及/或者过渡管7的软管管体进行组装连接,当然,可以理解的,还可以采用本领域已知的其它管连接结构来实现硬质管管体和节流管路3以及/或者过渡管7的软管管体的配接,不限于此管连接机构9。
下面,参看图4a和图4b,提供了本实用新型的制冷系统的第二实施例,该实施例与前述第一实施例的区别仅在于:
在本实施例中,对于中间扩张管31a-1而言,其主体管的前部末端与在前的一段毛细管30a-1的后部末端并非如第一实施例相接呈垂直台阶面,而是设置为:在前的一段毛细管30a-1的后部末端穿过该中间扩张管31a-1的主体管的前部末端并向后延伸入该中间扩张管31a-1内;并且,其主体管的后部末端与在后的一段毛细管30a-2的前部末端也并非如第一实施例相接呈垂直台阶面,而是设置为:在后的一段毛细管30a-2的前部末端穿过该中间扩张管31a-1的主体管的后部末端并向前延伸入该中间扩张管31a-1内。
类似的,对于末位扩张管31a-2而言,其主体管的前部末端与毛细管30a-2的后部末端并非如第一实施例相接呈垂直台阶面,而是设置为:毛细管30a-2的后部末端穿过该末位扩张管31a-2的主体管的前部末端并向后延伸入该末位扩张管31a-2内。
也即,本实施例中,毛细管主体30a和各个扩张管31a之间采用插入式结构,毛细管主体30a的末端插入扩张管31a内,毛细管主体30a的末端被扩张管31a中的制冷剂从外部进行包裹。
本实施例其余技术内容与第一实施例相同,不再多加赘述。
下面,参看图5a和图5b,提供了本实用新型的制冷系统的第三实施例。该实施例与前述第一实施例的区别在于:
在前述第一实施例中,每个扩张管31设置为等径管结构,其包括主体管,所述主体管设为管内通道截面积恒定的第一等径管,该第一等径管也即所述主体管,也即扩张管31;
而本实施例中,扩张管31b并非设置为等径管结构,其除了包括设为第一等径管的主体管312b且主体管312b的管内通道截面积是毛细管主体10的管内通道截面积的4至75倍,每个扩张管31b还包括扩口管311b。
扩口管311b串接在主体管312b的前部末端和在前的一段毛细管30b-1的后部末端之间,也即,扩口管311b的前部末端起始于在前的一段毛细管30b-1的后部末端,且扩口管311b的后部末端终止于主体管312b的前部末端;并且,扩口管311b的管内通道截面积由前向后自毛细管主体30b的管内通道截面积逐渐增大成所述第一等径管(也即主体管312b)的管内通道截面积。
若对应于节流管路3设置为圆形管的情况,则扩口管311b的管内径由前向后呈斜面或内凸弧面或外凹弧面,并且扩口管311b的管内径自毛细管主体30b的管内径逐渐增大成所述第一等径管(也即主体管312b)的管内径。这样,可以实现制冷剂自毛细管较为平缓的进入到扩张管31b的主体管312b中,减小管内径突变而造成的流动噪音。
进一步地,该实施例与前述第一实施例的区别还在于:中间扩张管31b-1还包括收口管313b。
收口管313b串接在主体管312b的后部末端和在后的一段毛细管30b-2的前部末端之间,也即,收口管313b的前部末端起始于主体管312b的后部末端,且收口管313b的后部末端终止于在后的一段毛细管30b-2的前部末端;并且,收口管313b的管内通道截面积由前向后自主体管312b的管内通道截面积逐渐减小成毛细管主体30b的管内通道截面积。
对应于节流管路3设置为圆形管的情况,则收口管313b的管内径由前向后呈斜面或内凸弧面或外凹弧面,并且自所述第一等径管(也即主体管312b)的管内径逐渐减小成毛细管主体30b的管内径。这样,可以实现制冷剂自扩张管31b的主体管312b较为平缓的进入到毛细管中,减小管内径突变而造成的流动噪音。
本实施例其余技术内容与第一实施例相同,不再多加赘述。
下面,参看图6a和图6b,提供了本实用新型的制冷系统的第四实施例。
该实施例与前述第一实施例的区别仅在于:
在前述第一实施例中,每个扩张管31设置为等径管结构,其包括主体管,所述主体管设为管内通道截面积恒定的第一等径管,该第一等径管也即所述主体管,也即扩张管31;
而本实施例中,扩张管31c的主体管并非设置为等径管结构,具体地,扩张管31c的主体管除了包括第一等径管311c且第一等径管311c的管内通道截面积是毛细管主体10的管内通道截面积的4至75倍,扩张管31b的主体管还包括串接在第一等径管311c后方的一段或两段或更多段第二等径管312c,各段第二等径管312c的管内通道截面积大于第一等径管311c的管内通道截面积。
在附图中,第二等径管312c的数目设置为一段,由此,扩张管31c的主体管为由较细的第一等径管311c和较粗的第二等径管312c前后依次连接而成。当然,在变化实施例中,第二等径管312c的数目设置为两段或更多段,此时,各段第二等径管312c的管内通道截面积不同,且由前向后依次串接的各段第二等径管312的管内通道截面积逐段增大。
本实施例的其余技术内容与第一实施例相同,不再赘述,当然,在变化实施例中,该实施例的扩张管31c与毛细管主体30c之间的结构也可以设置为第二实施例的插入式结构,或者也可以与第三实施例的技术内容相结合得到相应结构变化。
下面,参图7,提供了本实用新型的制冷系统的第五实施例,该实施例与前述第一实施例的区别仅在于:
在第一实施例中,冷凝器2的排出端设置有干燥过滤器5,节流管路3的前部末端固定配接于干燥过滤器5;
而本实施例中,冷凝器2’的排出端由前向后依次设置有干燥过滤器5’和电磁阀6’,节流管路3’的前部末端固定配接于电磁阀6’。
除了上述区别之外,本实施例的其余技术内容与前述第一实施例相同,对此不再赘述。当然,在变化实施例中,本实施例还可以与前述第二实施例至第四实施例的任一个的技术内容相结合。
进一步地,本实用新型第六实施例还提供了一种制冷电器,该制冷电器具体可以是冰箱或冷冻,其包括如前第一实施例至第五实施例中任一所述的制冷系统,或者还可以包括如前第一实施例至第五实施例中各技术方案经适当组合而构造出的变化实施例的制冷系统。
应当理解,虽然本说明书按照实施方式加以描述,但并非每个实施方式仅包含一个独立的技术方案,说明书的这种叙述方式仅仅是为清楚起见,本领域技术人员应当将说明书作为一个整体,各实施方式中的技术方案也可以经适当组合,形成本领域技术人员可以理解的其他实施方式。
上文所列出的详细说明仅仅是针对本实用新型的可行性实施方式的具体说明,它们并非用以限制本实用新型的保护范围,凡未脱离本实用新型技艺精神所作的等效实施方式或变更均应包含在本实用新型的保护范围之内。
本文用于企业家、创业者技术爱好者查询,结果仅供参考。