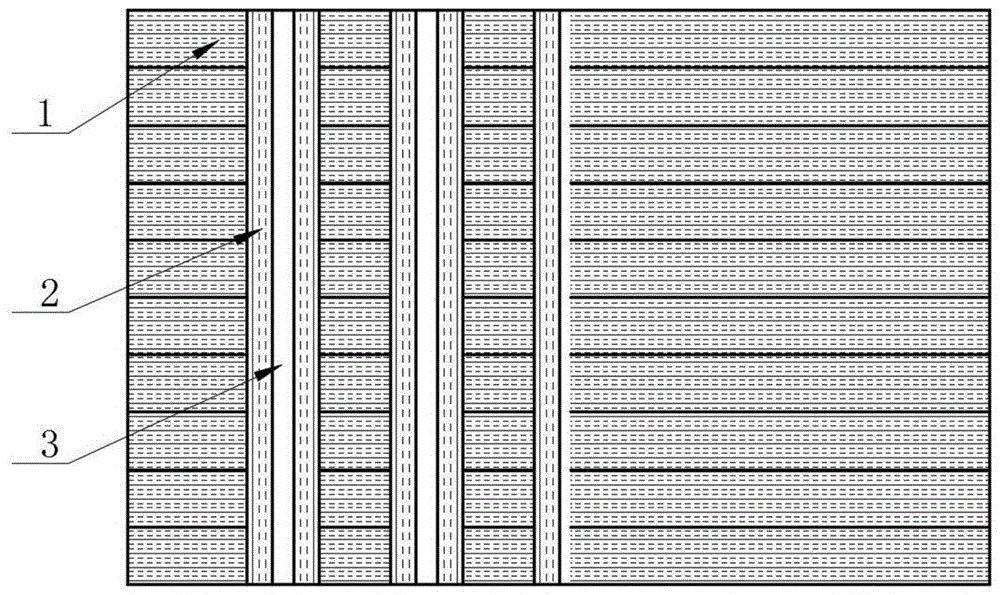
本发明涉及lng运输船领域,具体涉及一种用于lng运输船的减振层压块及其制备方法。
背景技术:
近年来随着人们对环境保护的重视,作为清洁化石燃料的天然气的消费需求逐年提升。根据国际能源机构预估,全球可采常规天然气总量超470万亿m3,但是这些天然气主要集中分布在俄罗斯、伊朗、卡塔尔等少数国家。这使得能源紧缺的用气地区与能源丰富的产气地区之间具有一定的地理位置的局限,因此,天然气运输成为需要解决的关键问题之一。目前主要有陆地运输、水上运输和管道运输等运输方式,其中水上运输主要是将常压下的气态天然气冷却至-162℃,体积缩小至气态时的1/625,凝结成液体后通过液化天然气(lng)运输船进行运输,可节约存储空间和运输成本。
由于lng特殊的物理化学性质,对lng运输船各方面的性能都有较高的要求,为了实现安全有效的运输,lng运输船需要有绝对的低温可靠性。目前一些新式的lng运输船的液货罐罐体和船体之间设有若干支撑单元,这些支撑单元通常采用的是一种环氧树脂与木材复合的层压木结构。但是这种层压木在外界温度发生冷热变化时易出现裂纹,会对其剪切强度尤其是平行于压合层方向的剪切强度产生很大的影响,给lng运输船带来很大的安全隐患。
技术实现要素:
为解决以上至少之一的技术问题,本发明提供一种用于lng运输船的减振层压块及其制备方法。本发明的减振层压块不仅具有良好的耐低温性能(使用温度可达-196℃),同时由于其特殊的结构设计使其不仅在垂直于压合层方向具有优异的抗剪切性能,而且在平行于压合层方向同样具有优异的抗剪切性能;可作为lng运输船液货罐罐体的耐低温支撑单元使用或其他耐低温抗冲击结构单元使用。
为了实现以上目的,本发明采用以下技术方案:
本发明一方面提供一种用于lng运输船的减振层压块,该减振层压块包括多层复合材料压合层和垂直穿插于所述多层复合材料压合层中的管状加强筋;
所述多层复合材料压合层是由耐低温浇注型聚氨酯与纤维布压合而成;
所述管状加强筋为中空管状结构,是由耐低温浇注型聚氨酯与纤维布旋转缠绕而成。
根据减振层压块在实际使用过程中的受力情况,管状加强筋垂直穿插增强可以保证垂直于多层复合材料压合层方向的抗压强度和抗剪强度不降低或少降低的前提下,最大限度提高平行于多层复合材料压合层方向的剪切强度。
本发明采用耐低温浇注型聚氨酯与纤维布复合的技术,将聚氨酯的耐低温性能与纤维布高强度高模量相结合,制备出的减振层压块不仅具有优异的低温性能而且具有优异的抗剪切性能,可以满足超低温环境和受力复杂的lng运输船液货罐罐体的支撑单元结构的使用。同时,本发明通过水平的多层复合材料压合层和垂直的管状加强筋的结构设计,使减振层压块在水平和垂直方向均具有优异的抗剪切性能。本发明减振层压块的抗压强度>100mpa,垂直于多层复合材料方向的剪切强度>60mpa,平行于多层复合材料方向的剪切强度>30mpa,使用温度可达到-196℃。
根据本发明的减振层压块,优选地,所述多层复合材料压合层与所述管状加强筋通过耐低温浇注型聚氨酯粘接。
根据本发明的减振层压块,优选地,所述耐低温浇注型聚氨酯包括a组分和b组分;
所述a组分的原料包括:聚醚多元醇20~50质量份(更优选为35~45质量份),二异氰酸酯70~120质量份(更优选为80~110质量份);
所述b组分的原料包括:聚醚多元醇80~130质量份(更优选为90~110质量份),扩链剂10~40质量份(更优选为20~25质量份),改性无机填料10~50质量份(更优选为25~35质量份),催化剂0.5~3质量份(更优选为0.5~1.5质量份)。
根据本发明的减振层压块,优选地,所述a组分与b组分的质量比为0.52~1.2;更优选为0.75~1.05。
根据本发明的减振层压块,优选地,所述a组分中的所述聚醚多元醇的数均分子量(mn)为2000~3000。
根据本发明的减振层压块,优选地,所述b组分中的所述聚醚多元醇的数均分子量为650~3000。
具体的聚醚多元醇的数均分子量是在兼顾性能和a、b组分的黏度以及混合后的反应速度考虑的,而a、b组分的黏度以及混合后的反应速度会影响到成型工艺。本发明经过探索优选出a组分中所述聚醚多元醇的数均分子量(mn)为2000~3000,b组分中的所述聚醚多元醇的数均分子量为650~3000。
根据本发明的减振层压块,优选地,所述a组分和b组分中的所述聚醚多元醇均包括聚四氢呋喃二醇、含支链聚四氢呋喃二醇ptg-l(其中ptg-l为商品代号)和四氢呋喃-氧化丙烯共聚醚二醇;更优选地,所述a组分和b组分中的所述聚醚多元醇均由聚四氢呋喃二醇、含支链聚四氢呋喃二醇ptg-l和四氢呋喃-氧化丙烯共聚醚二醇组成。
根据本发明的减振层压块,优选地,所述a组分中的所述二异氰酸酯包括2,4’-二苯基甲烷二异氰酸酯与4,4’-二苯基甲烷二异氰酸酯1:1的混合物(mdi-50)和碳化二亚胺改性4,4’-二苯基甲烷二异氰酸酯。更优选地,所述a组分中的所述二异氰酸酯由2,4’-二苯基甲烷二异氰酸酯与4,4’-二苯基甲烷二异氰酸酯1:1的混合物(mdi-50)和碳化二亚胺改性4,4’-二苯基甲烷二异氰酸酯组成;此时其性能能够满足使用要求和加工工艺。
根据本发明的减振层压块,优选地,所述b组分中的所述扩链剂包括1,4-丁二醇和乙二醇中的至少一种。
根据本发明的减振层压块,优选地,所述b组分中的所述改性无机填料包括炭黑(例如炭黑220)、多壁碳纳米管、1~4mm长的短切碳纤维和氧化石墨烯中的一种或两种以上的组合。
根据本发明的减振层压块,优选地,所述b组分中的所述催化剂包括有机铋催化剂dy20和有机锌催化剂dy5350中的至少一种;更优选地,所述b组分中的所述催化剂由有机铋催化剂dy20和有机锌催化剂dy5350组成,这两种催化剂需配合使用,催化效果最佳。
根据本发明的减振层压块,优选地,经过综合考虑性能、价格以及成型工艺,所述纤维布选自玻璃纤维布、玄武岩纤维布和碳纤维布中的至少一种。
根据本发明的减振层压块,优选地,所述纤维布的编织方式为平纹编织。一般纤维布的编织方式有平纹、斜纹和缎纹三种,经本发明探索,采用平纹编织时获得的减振层压块强度最优。
根据本发明的减振层压块,优选地,所述纤维布的厚度为0.3mm~0.5mm。
根据本发明的减振层压块,优选地,所述多层复合材料压合层在每毫米厚度上平铺的纤维布层数为0.5~3。
根据本发明的减振层压块,优选地,所述多层复合材料压合层中纤维布的体积占比为20%~50%。纤维布的体积占比与多层复合材料压合层的强度有相关性,纤维布过多或过少都会使多层复合材料压合层性能变差。
根据本发明的减振层压块,优选地,所述多层复合材料压合层的密度为1.3g/cm3~1.75g/cm3。
根据本发明的减振层压块,优选地,所述多层复合材料压合层上均匀的分布着用于穿插所述管状加强筋的安装孔;在所述多层复合材料压合层的表面上,所述安装孔的面积占比为30%~60%。综合考虑垂直方向和平行方向的强度。
所述安装孔的面积占比即对应着管状加强筋的分布密度。管状加强筋的密度和减振层压块的强度具体相关性,密度越大,平行于多层复合材料压合层方向的剪切强度越大,但垂直于多层复合材料压合层方向的抗剪强度会降低,本发明综合考虑垂直方向和平行方向的强度,优选安装孔的面积占比为30%~60%。
根据本发明的减振层压块,优选地,所述安装孔的孔径为8.5mm~25.5mm。安装孔的孔径尺寸是在安装孔的面积占比确定之后,为了适应减振层压块在使用过程的实际尺寸进行调整的。
根据本发明的减振层压块,优选地,所述管状加强筋在径向每毫米厚度上旋转缠绕的纤维布层数为0.5~3,具体的纤维布层数需要根据减振层压块的尺寸、形状以及强度要求进行确定。
根据本发明的减振层压块,优选地,所述管状加强筋的外径为8mm~25mm;内径为4mm~15mm。
根据本发明的减振层压块,优选地,所述管状加强筋的内孔中设置有压力传感器、应变传感器或温度传感器中的一种或两种以上的组合。
本发明另一方面提供一种上述减振层压块的制备方法,该制备方法包括以下步骤:
将所述耐低温浇注型聚氨酯涂抹在单层所述纤维布的表面,通过压合模具制备出单层复合片材;
在所述单层复合片材的两侧表面涂抹耐低温浇注型聚氨酯,之后在压合模具中叠加10~50层,制备出多层复合材料;
在所述多层复合材料上打孔作为所述管状加强筋的安装孔;
将所述耐低温浇注型聚氨酯涂抹在单层所述纤维布的表面,然后将其一端固定在圆柱形芯模上,转动所述芯模将纤维布均匀的缠绕至外径等于所述管状加强筋的外径;然后将其放入成型模具中,进行模压制备出管状加强筋;
将预定数量的具有安装孔的所述多层复合材料通过耐低温浇注型聚氨酯压合到模具中,然后在所述管状加强筋的外表面涂抹耐低温浇注型聚氨酯,再将其插入到所述安装孔中,之后进行模压制备出所述减振层压块。所述预定数量具体是根据减振层压块在实际使用过程中的尺寸要求来确定的,在lng船上使用的减振层压块的尺寸和形状有多种,在成型时需要使用不同的模具进行模压。
根据本发明的制备方法,优选地,所述压合模具制备单层复合片材时的条件包括:压合模具的厚度为0.32mm~0.52mm,模压力为10mpa~20mpa,模压温度为60~80℃,模压时间为10min~30min。
根据本发明的制备方法,优选地,所述压合模具制备多层复合材料时的条件包括:压合模具的厚度为5mm~20mm,模压力为10mpa~20mpa,模压温度为60~80℃,模压时间为20min~60min。
根据本发明的制备方法,优选地,所述模压制备出管状加强筋的条件包括:压力10mpa~20mpa,模压温度为60~80℃,模压时间为30min~60min。
根据本发明的制备方法,优选地,所述模压制备出所述减振层压块的条件包括:模压力10mpa~20mpa,模压温度为60~80℃,模压时间为60min~180min。
根据本发明的制备方法,优选地,所述制备方法在模压制备出所述减振层压块的步骤之后还包括:在所述管状加强筋的内孔中设置有压力传感器、应变传感器或温度传感器中的一种或两种以上的组合。
本发明再一方面提供上述减振层压块在lng运输船液货罐罐体的耐低温支撑单元结构中的使用。此外,本发明的减振层压块还可以在其他耐低温抗冲击结构中使用。
本发明的减振层压块通过将耐低温浇注型聚氨酯材料作为基体材料而获得了优异的耐低温性能,纤维布作为增强材料而获得了优异的抗剪切性能,并通过在水平方向多层复合材料上垂直插入管状加强筋,使其兼顾平行和垂直两个方向的抗剪切性能;进一步还可以在管状加强筋的内孔中设置压力传感器、应变传感器或温度传感器来实现实时监测层压块的工作状态和使用寿命。本发明的减振层压块应用于lng运输船液货罐罐体的耐低温支撑单元结构中可以极大的提高支撑单元的可靠性,进而提高lng运输船的可靠性。
附图说明
图1为本发明的减振层压块的结构示意图。
图2为本发明的减振层压块的水平截面示意图。
附图标记说明:
1-多层复合材料压合层,2-管状加强筋,3-内孔。
具体实施方式
为了更清楚地说明本发明,下面结合优选实施例和附图对本发明做进一步的说明。本领域技术人员应当理解,下面所具体描述的内容是说明性的而非限制性的,不应以此限制本发明的保护范围。
另外,在本发明中的实施例中所提到的一些方位词,例如“水平”、“垂直”等,这些方位词的含义与多层复合材料的放置情况有关,不应理解为对本发明保护范围的限制。
如图1和图2所示,本发明的减振层压块包括:水平方向的多层复合材料压合层1,垂直穿插与所述多层复合材料压合层1中的管状加强筋2,其穿插连接部位优选通过耐低温浇注型聚氨酯粘接。
所述管状加强筋2为中空管状结构,具有内孔3,其中可以进一步设置压力传感器、应变传感器或温度传感器中的至少一种来实现实时监测层压块的工作状态和使用寿命。
所述多层复合材料压合层1是由耐低温浇注型聚氨酯与纤维布压合而成;所述管状加强筋2是由耐低温浇注型聚氨酯与纤维布旋转缠绕而成。
本发明实施例中所使用的材料情况如下:
1)ptmeg2000:数均分子量2000的聚四氢呋喃二醇;
2)ptmeg1000:数均分子量1000的聚四氢呋喃二醇;
3)ptg-l2000:数均分子量2000的含支链聚四氢呋喃二醇ptg-l;
4)ptg-l3000:数均分子量3000的含支链聚四氢呋喃二醇ptg-l;
5)ptpg2000:数均分子量2000的四氢呋喃-氧化丙烯共聚醚二醇,其由四氢呋喃与环氧丙烷制备而成;
6)mdi-50:2,4’-二苯基甲烷二异氰酸酯与4,4’-二苯基甲烷二异氰酸酯1:1混合物,异氰酸根含量为33.5%;
7)mdi100l:碳化二亚胺改性的二苯基甲烷二异氰酸酯,异氰酸根含量为29%;
8)bdo:1,4-丁二醇;
9)n220:炭黑220;
10)cnt:碳纳米管;
11)cf:碳纤维;
12)go:氧化石墨烯;
13)dy20:有机铋催化剂dy20;
14)dy5350:有机锌催化剂dy5350。
本发明实施例中的份数均为质量份数。
本发明实施例中所制造的减振层压块中的密度测试标准参考din53420,抗压强度测试标准参考din53454,剪切强度测试标准参考din7707。
实施例1
本实施例制备一种减振层压块,其中的耐低温浇注型聚氨酯中的a组分和b组分的质量比为1:1,a组分和b组分的配方为:
a组分:聚醚多元醇ptmeg20005份,ptg-l200015份,ptpg200020份;二异氰酸酯mdi-505份,mdi100l80份。
b组分:ptmeg100060份,ptg-l200020份,ptpg200030份,bdo24份,n22010份,cnt5份,1mm短切cf15份,dy200.2份,dy53500.8份。
本实施例中,多层复合材料压合层和管状加强筋中的纤维布均为玻璃纤维布,编织方式为平纹编织,纤维布厚度为0.41mm。
本实施例中,多层复合材料压合层中每毫米厚度上平铺的纤维布层数为1.5,纤维布在多层复合材料压合层中的体积占比为29%,多层复合材料压合层的密度为1.46g/cm3。
本实施例中,多层复合材料压合层上均匀的分布着管状加强筋的安装孔,安装孔的面积占比为30%,孔径为10.5mm。
本实施例中,管状加强筋在径向每毫米厚度上旋转缠绕的纤维布层数为2。
本实施例中,管状加强筋的外径为10mm,内径为4mm。
本实施例的减振层压块的制备方法包括如下步骤:
1)将耐低温浇注型聚氨酯a、b组分按比例混合后均匀的涂抹在单层纤维布表面,控制压合模具厚度0.65mm,模压力15mpa,模压温度75℃,模压时间15min,制备出单层复合片材。
2)将所述单层复合片材的两侧表面均匀的涂抹上耐低温浇注型聚氨酯,然后将15层单层复合片材依次叠压到压合模具中,压合模具厚度10mm,模压力20mpa,模压温度75℃,模压时间30min,制备出多层复合材料压合层。
3)在所述多层复合材料压合层上按要求均匀地打上直径为10.5mm的安装孔,安装孔的面积占比为30%。
4)将耐低温浇注型聚氨酯a、b组分按比例混合后均匀的涂抹在单层纤维布表面,然后将涂有耐低温浇注型聚氨酯的纤维布的一端固定在圆柱形芯模上,芯模外径为4mm,转动芯模将纤维布均匀的缠绕至外径为10mm,然后将其放入成型模具中,进行模压,模压力15mpa,模压温度75℃,模压时间30min,制备出管状加强筋。
5)将50块带有安装孔的多层复合材料压合层通过耐低温浇注型聚氨酯压合到模具中,然后将所述管状加强筋外表面均匀涂抹耐低温浇注型聚氨酯,再将其插入到多层复合材料压合层的安装孔中,并插满,进行模压,模压力20mpa,模压温度80℃,模压时间120min,制备出减振层压块。
6)在减振层压块中的管状加强筋的内孔中设置压力传感器、应变传感器和温度传感器。
本实施例中所制备的减振层压块的抗压强度达到201mpa;其垂直于多层复合材料压合层方向的剪切强度在20℃时达到85mpa,在-196℃时达到81.5mpa;其平行于多层复合材料压合层方向的剪切强度在20℃时达到51mpa,-196℃时达到50.5mpa;因此其使用温度可达到-196℃。同时由于该减振层压块中植入了压力传感器、应变传感器和温度传感器,可以实现实时监测减振层压块的工作状态和使用寿命的功能。
实施例2
本实施例制备一种减振层压块,其中的耐低温浇注型聚氨酯中的a组分和b组分的质量比为0.91:1,a组分和b组分的配方为:
a组分:聚醚多元醇ptmeg200010份,ptg-l200010份,ptpg200020份;二异氰酸酯mdi-5015份,mdi100l80份。
b组分:ptmeg100050份,ptg-l200020份,ptpg200030份,bdo21.3份,n22010份,1mm短切cf15份,go5份,dy200.2份,dy53500.8份。
本实施例中,多层复合材料压合层和管状加强筋中的纤维布均为玻璃纤维布,编织方式为平纹编织,纤维布厚度为0.39mm。
本实施例中,多层复合材料压合层中每毫米厚度上平铺的纤维布层数为2,纤维布在多层复合材料压合层中的体积占比为32%,多层复合材料压合层的密度为1.5g/cm3。
本实施例中,多层复合材料压合层上均匀的分布着着管状加强筋的安装孔,安装孔的面积占比为35%,孔径为15.5mm。
本实施例中,管状加强筋在径向每毫米厚度上旋转缠绕的纤维布层数为2。
本实施例中,管状加强筋的外径为15mm,内径为6mm。
本实施例的减振层压块的制备方法包括如下步骤:
1)将耐低温浇注型聚氨酯a、b组分按比例混合后均匀的涂抹在单层纤维布表面,控制压合模具厚度0.48mm,模压力15mpa,模压温度75℃,模压时间15min,制备出单层复合片材。
2)将所述单层复合片材的两侧表面均匀的涂抹上耐低温浇注型聚氨酯,然后将20层单层复合片材依次叠压到压合模具中,压合模具厚度10mm,模压力20mpa,模压温度75℃,模压时间30min,制备出多层聚氨酯纤维复合板材。
3)在所述多层复合材料压合层上按要求均匀地打上直径为15.5mm的安装孔,安装孔的面积占比为35%。
4)将耐低温浇注型聚氨酯a、b组分按比例混合后均匀的涂抹在单层纤维布表面,然后将涂有耐低温浇注型聚氨酯的纤维布的一端固定在圆柱形芯模上,芯模外径为6mm,转动芯模将纤维布均匀的缠绕至外径为15mm,然后将其放入成型模具中,进行模压,模压力15mpa,模压温度75℃,模压时间30min,制备出管状加强筋。
5)将50块带有安装孔的多层复合材料压合层通过耐低温浇注型聚氨酯压合到模具中,然后将所述管状加强筋外表面均匀涂抹耐低温浇注型聚氨酯,再将其插入到多层复合材料压合层的安装孔中,并插满,进行模压,模压力20mpa,模压温度80℃,模压时间120min,制备出减振层压块。
6)在减振层压块中的管状加强筋的内孔中设置压力传感器、应变传感器和温度传感器。
本实施例中所制备的耐低温聚氨酯复合材料减振层压块,其抗压强度达到205mpa;其垂直于多层复合材料压合层方向的剪切强度在20℃时达到82mpa,在-196℃时达到78.3mpa;其平行于多层复合材料压合层方向的剪切强度在20℃时达到63mpa,-196℃时达到61.7mpa;因此其使用温度可达到-196℃。同时由于该减振层压块中植入了压力传感器、应变传感器和温度传感器,可以实现实时监测减振层压块的工作状态和使用寿命的功能。
实施例3
本实施例制备一种减振层压块,其中的耐低温浇注型聚氨酯中的a组分和b组分的质量比为0.79:1,a组分和b组分的配方为:
a组分:聚醚多元醇ptmeg200015份,ptg-l200015份,ptpg200010份;二异氰酸酯mdi-5025份,mdi100l80份。
b组分:ptmeg200020份,ptg-l300050份,ptpg200020份,bdo20.5份,n22010份,cnt5份,1mm短切cf10份,go5份,dy200.2份,dy53500.8份。
本实施例中,多层复合材料压合层和管状强筋中的纤维布均为玄武岩纤维布,编织方式为平纹编织,纤维布厚度为0.41mm。
本实施例中,多层复合材料压合层中每毫米厚度上平铺的纤维布层数为1.5,纤维布在多层复合材料压合层中的体积占比为31%,多层复合材料压合层的密度为1.48g/cm3。
本实施例中,多层复合材料压合层上均匀的分布着着管状加强筋的安装孔,安装孔的面积占比为45%,孔径为20.5mm。
本实施例中,管状加强筋在径向每毫米厚度上旋转缠绕的纤维布层数为2。
本实施例中,管状加强筋的外径为20mm,内径为10mm。
本实施例的减振层压块的制备方法包括如下步骤:
1)将耐低温浇注型聚氨酯a、b组分按比例混合后均匀的涂抹在单层纤维布表面,控制压合模具厚度0.65mm,模压力15mpa,模压温度75℃,模压时间15min,制备出单层复合片材。
2)将所述单层复合片材的两侧表面均匀的涂抹上耐低温浇注型聚氨酯,然后将15层单层复合片材依次叠压到压合模具中,压合模具厚度10mm,模压力20mpa,模压温度75℃,模压时间30min,制备出多层聚氨酯纤维复合板材。
3)在所述多层复合材料压合层上按要求均匀地打上直径为20.5mm的安装孔,安装孔的面积占比为45%。
4)将耐低温浇注型聚氨酯a、b组分按比例混合后均匀的涂抹在单层纤维布表面,然后将涂有耐低温浇注型聚氨酯的纤维布的一端固定在圆柱形芯模上,芯模外径为10mm,转动芯模将纤维布均匀的缠绕至外径为20mm,然后将其放入成型模具中,进行模压,模压力15mpa,模压温度75℃,模压时间30min,制备出管状加强筋。
5)将50块带有安装孔的多层复合材料压合层通过耐低温浇注型聚氨酯压合到模具中,然后将所述管状加强筋外表面均匀涂抹耐低温浇注型聚氨酯,再将其插入到多层复合材料压合层的安装孔中,并插满,进行模压,模压力20mpa,模压温度80℃,模压时间120min,制备出减振层压块。
6)在减振层压块中的管状加强筋的内孔中设置压力传感器、应变传感器和温度传感器。
本实施例中所制备的耐低温聚氨酯复合材料减振层压块,其抗压强度达到195mpa;其垂直于多层复合材料压合层方向的剪切强度在20℃时达到78mpa,在-196℃时达到75.4mpa;其平行于多层复合材料压合层方向的剪切强度在20℃时达到68mpa,-196℃时达到66.7mpa;因此其使用温度可达到-196℃。同时由于该减振层压块中植入了压力传感器、应变传感器和温度传感器,可以实现实时监测减振层压块的工作状态和使用寿命的功能。
实施例4
本实施例制备一种减振层压块,其中的耐低温浇注型聚氨酯中的a组分和b组分的质量比为0.85:1,a组分和b组分的配方为:
a组分:聚醚多元醇ptmeg200015份,ptg-l200015份,ptpg200010份;二异氰酸酯mdi-5025份,mdi100l80份。
b组分:ptmeg100050份,ptg-l200020份,ptpg200030份,bdo20.5份,n22010份,cnt5份,1mm短切cf10份,go5份,dy200.2份,dy53500.8份。
本实施例中,多层复合材料压合层中的纤维布为玄武岩纤维布,编织方式为平纹编织,纤维布厚度为0.39mm。
本实施例中,多层复合材料压合层中每毫米厚度上平铺的纤维布层数为2,纤维布在多层复合材料压合层中的体积占比为35%,多层复合材料压合层的密度为1.54g/cm3。
本实施例中,多层复合材料压合层上均匀的分布着着管状加强筋的安装孔,安装孔的面积占比为40%,孔径为24.5mm。
本本实施例中,管状加强筋在径向每毫米厚度上旋转缠绕的纤维布层数为2。
本实施例中,管状加强筋的外径为24mm,内径为10mm。
本实施例的减振层压块的制备方法包括如下步骤:
1)将耐低温浇注型聚氨酯a、b组分按比例混合后均匀的涂抹在单层纤维布表面,控制压合模具厚度0.48mm,模压力15mpa,模压温度75℃,模压时间15min,制备出单层复合片材。
2)将所述单层复合片材的两侧表面均匀的涂抹上耐低温浇注型聚氨酯,然后将20层片材依次叠压到压合模具中,单层复合片材依次叠压到压合模具中,压合模具厚度10mm,模压力20mpa,模压温度75℃,模压时间30min,制备出多层聚氨酯纤维复合板材。
3)在所述多层复合材料压合层上按要求均匀地打上直径为24.5mm的安装孔,安装孔的面积占比为40%。
4)将耐低温浇注型聚氨酯a、b组分按比例混合后均匀的涂抹在单层纤维布表面,然后将涂有耐低温浇注型聚氨酯的纤维布的一端固定在圆柱形芯模上,芯模外径为10mm,转动芯模将纤维布均匀的缠绕至外径为24mm,然后将其放入成型模具中,进行模压,模压力15mpa,模压温度75℃,模压时间30min,制备出管状加强筋。
5)将50块带有安装孔的多层复合材料压合层通过耐低温浇注型聚氨酯压合到模具中,然后将所述管状加强筋外表面均匀涂抹耐低温浇注型聚氨酯,再将其插入到多层复合材料压合层的安装孔中,并插满,进行模压,模压力20mpa,模压温度80℃,模压时间120min,制备出减振层压块。
6)在减振层压块中的管状加强筋的内孔中设置压力传感器、应变传感器和温度传感器。
本实施例中所制备的耐低温聚氨酯复合材料减振层压块,其抗压强度达到208mpa;其垂直于多层复合材料压合层方向的剪切强度在20℃时达到80mpa,在-196℃时达到77.2mpa;其平行于多层复合材料压合层方向的剪切强度在20℃时达到71mpa,-196℃时达到68.3mpa;因此其使用温度可达到-196℃。同时由于该减振层压块中植入了压力传感器、应变传感器和温度传感器,可以实现实时监测减振层压块的工作状态和使用寿命的功能。
对比例1
本对比例是将实施例1中耐低温浇注型聚氨酯配方换成以下方案:
a组分和b组分的质量比为0.5:1,a组分和b组分的配方分别为:
a组分:聚醚多元醇ptmeg20005份,ptg-l200015份,ptpg200020份;二异氰酸酯mdi-505份,mdi100l80份。
b组分:ptmeg100060份,ptg-l200020份,ptpg200030份,bdo6.5份,n22010份,cnt5份,1mm短切cf15份,dy200.2份,dy53500.8份。
其余制作方法及工艺与实施例1相同。
本对比例中所制备的减振层压块的抗压强度仅为105mpa;其垂直于多层复合材料压合层方向的剪切强度在20℃时仅为61mpa,在-196℃时仅为58.4mpa;其平行于多层复合材料压合层方向的剪切强度在20℃时仅为39.3mpa,-196℃时仅为38.2mpa。相比于实施例1性能下降较多。
对比例2
本对比例是将实施例2中耐低温浇注型聚氨酯配方换成以下方案:
a组分和b组分的质量比为0.5:1,a组分和b组分的配方分别为:
a组分:聚醚多元醇ptmeg200010份,ptg-l200010份,ptpg200020份;二异氰酸酯mdi-5015份,mdi100l80份。
b组分:ptmeg100050份,ptg-l200020份,ptpg200030份,bdo6份,n2208份,1mm短切cf9份,go2份,dy200.2份,dy53500.8份。
其余制作方法及工艺与实施例2相同。
本对比例中所制备的耐低温聚氨酯复合材料减振层压块,其抗压强度仅为108mpa;其垂直于多层复合材料压合层方向的剪切强度在20℃时达到63.2mpa,在-196℃时达到61.5mpa;其平行于多层复合材料压合层方向的剪切强度在20℃时达到51mpa,-196℃时达到49.4mpa。相比于实施例2性能下降较多。
对比例3
本对比例是将实施例3中耐低温浇注型聚氨酯配方换成以下方案:
a组分和b组分的质量比为1.25:1,a组分和b组分的配方分别为:
a组分:聚醚多元醇ptmeg200015份,ptg-l200015份,ptpg200010份;二异氰酸酯mdi-5025份,mdi100l80份。
b组分:ptmeg200020份,ptg-l300050份,ptpg200020份,bdo39.5份,n22010份,cnt5份,1mm短切cf10份,go5份,dy200.2份,dy53500.8份。
其余制作方法及工艺与实施例3相同。
本对比例中所制备的耐低温聚氨酯复合材料减振层压块,其抗压强度达到203mpa;其垂直于多层复合材料压合层方向的剪切强度在20℃时达到83mpa,在-196℃时仅为37mpa;其平行于多层复合材料压合层方向的剪切强度在20℃时达到72mpa,-196℃时仅为41mpa;相比于实施例3其-196℃时的剪切强度下降较多。
对比例4
本对比例是将实施例4中耐低温浇注型聚氨酯配方换成以下方案:
a组分和b组分的质量比为1.25:1,a组分和b组分的配方分别为:
a组分:聚醚多元醇ptmeg200015份,ptg-l200015份,ptpg200010份;二异氰酸酯mdi-5025份,mdi100l80份。
b组分:ptmeg100050份,ptg-l200020份,ptpg200030份,bdo41.5份,n22010份,cnt15份,1mm短切cf10份,go4份,dy200.2份,dy53500.8份。
其余制作方法及工艺与实施例4相同。
本对比例中所制备的耐低温聚氨酯复合材料减振层压块,其抗压强度达到215mpa;其垂直于多层复合材料压合层方向的剪切强度在20℃时达到83.5mpa,在-196℃时仅为42.8mpa;其平行于多层复合材料压合层方向的剪切强度在20℃时达到78mpa,-196℃时仅为44.7mpa;相比于实施例4其-196℃时的剪切强度下降较多。
显然,本发明的上述实施例仅仅是为清楚地说明本发明所作的举例,而并非是对本发明的实施方式的限定,对于所属领域的普通技术人员来说,在上述说明的基础上还可以做出其它不同形式的变化或变动,这里无法对所有的实施方式予以穷举,凡是属于本发明的技术方案所引伸出的显而易见的变化或变动仍处于本发明的保护范围之列。
本文用于企业家、创业者技术爱好者查询,结果仅供参考。