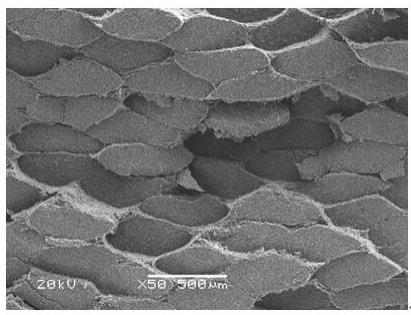
1.本发明涉及一种独石结构氮化硼高温自润滑材料,尤其涉及一种仿生纤维独石结构氮化硼高温自润滑材料,属于复合材料领域和自润滑材料领域。
技术背景
2.六方氮化硼(hbn)是一种典型的二维材料,其特殊的片层结构赋予了材料优异的自润滑性,且其较高的高温化学惰性及高温抗氧化性使之在空气中服役温度可达1000℃以上,因此是一种非常理想的高温固体润滑剂。而且,hbn质地轻软,密度仅为2.27g/cm3,具有良好的可加工性,可广泛用于机械装备的滑动部件及润滑密封件,且其高的导热系数也可满足滑动部件在高速运转时的摩擦热的散热需求。
3.制备高温自润滑复合陶瓷,利用hbn间片层的滑移实现材料的高温自润滑性能,同时陶瓷基体可促进hbn的烧结性能。现有技术(journal of the european ceramic society,27(2007)1425
‑
1430)以aln作为基体,引入不同含量的hbn粉体,在1800℃烧结,制备了aln
‑
hbn陶瓷复合材料,随着引入hbn含量的增加,其相对密度和力学性能显著降低,当引入hbn含量达到20 vol%时,复合材料的相对密度和强度仅为86.2%和120mpa。据文献(tribology international,154(2021)106748)报道,在zro2中引入30vol%的hbn作为高温固体润滑剂和10 vol%的sic粉体作为助剂制备的自润滑陶瓷复合材料,在室温至900℃范围内干摩擦条件下的摩擦系数为0.45。由于陶瓷本征的脆性,加之hbn较差的烧结性能,在基体中充当缺陷的角色,破坏了陶瓷基体的连续性,从而影响材料的承载能力,使得复合材料一经破坏便呈现出灾难性断裂特征,严重限制了其力学性能和服役可靠性及稳定性。因此,迫切需要开发兼具优异力学性能和高温自润滑性能的复合陶瓷材料,实现高可靠性且高耐磨性和优异自润滑性能的统一,以满足机械装备高速运转动密封部件对润滑、密封及高服役可靠性的需求。
技术实现要素:
4.本发明的目的是为了克服现有技术中存在的上述问题,提供一种兼具高温自润滑性能和优异服役可靠性的仿生纤维独石结构氮化硼高温自润滑材料及其制备方法。
5.本发明仿生纤维独石结构氮化硼高温自润滑材料的制备方法,由cbn作为纤维胞体,同种不同相的hbn作为界面层,其中cbn作为纤维胞体呈定向排列且被界面层分隔成独立的单元。cbn纤维胞体发挥其高承载作用,提高材料的强度;hbn弱界面润滑相起到润滑效果,同时通过诱导裂纹偏转、消解局部高应力及使裂纹尖端载荷重新分布等外部增韧机制提高材料的韧性及服役可靠性。
6.上述cbn纤维胞体是cbn基复合材料,可引入si3n4、al2o3、zro2、y2o3、aln等陶瓷中的一种或几种作为粘接剂,以降低制备过程中的烧结温度,促进致密性。cbn纤维胞体的直径为400~800μm,纤维胞体中cbn颗粒尺寸为5~10μm。粘接剂含量为30wt%~60wt%。作为一种优选方案,cbn纤维胞体的配方为:50wt�n+22wt%si3n4+10wt%al2o3+4wt%y2o3+14wt%
aln。
7.上述hbn界面层也可采用hbn基复合材料,通过添加陶瓷相如sio2、si3n4、al2o3等作为粘接剂,以提高自身强度和其与纤维胞体间的结合强度。hbn界面层中hbn尺寸为0.5~5μm,界面层厚度为5~25μm。粘接剂含量为2%~40%。作为一种优选方案,hbn界面层的配方为95 wt%hbn+2.2wt%si3n4+1.0wt%al2o3+0.4wt%y2o3+1.4wt%aln。
8.本发明仿生纤维独石结构氮化硼高温自润滑材料的制备方法,包括以下步骤:(1)cbn纤维胞体前驱体成型将cbn粉体以及粘接剂陶瓷粉体加入到pva(聚乙烯醇,聚合度1750
±
50,作为胶黏剂)水溶液中(pva水溶液的质量浓度为1~2%,球磨混合均匀形成陶瓷泥料(泥料固相含量质量百分数为30~50%),然后将陶瓷泥料通过挤制的方法形成纤维胞体前驱体,挤出的纤维胞体前驱体晾干后切割成所需的长度。纤维胞体前驱体的直径可通过挤出口的内径控制在400~800μm。
9.陶瓷粘接剂为si3n4、al2o3、zro2、y2o3、aln等陶瓷中的一种或几种;粘接剂含量为30wt%~60wt%。作为一种优选方案,cbn纤维胞体的配方为:50wt�n+22wt%si3n4+10wt%al2o3+4wt%y2o3+14wt%aln。
10.(2)界面层浆料制备及涂覆将hbn粉体及陶瓷粘接剂粉末分散在乙醇、异丙醇或蒸馏水溶液中形成浓度为0.8~1.5 g/ml的界面层浆料,再将界面层浆料通过浸蘸或喷涂的方法涂覆cbn纤维胞体前驱体表面,干燥,形成界面分隔层。界面分隔层的厚度可通过界面层浆料固相含量和浸蘸次数控制在为5~25μm。
11.作为一种优选方案,当以al2o3作为界面层粘接剂之一时,采用羟基聚合铝溶胶作为al2o3的前驱体。将hbn粉体与相应比例的羟基聚合铝溶胶混合,并球磨均匀形成一定流动性的浆料,通过调节羟基聚合铝溶胶的浓度和hbn与羟基聚合铝溶胶中的al的比例控制浆料的粘度和界面层中al2o3粘接剂的含量。羟基聚合铝溶胶在烧结过程中进行脱水分解,最终反应形成al2o3。羟基聚合铝溶胶中al的浓度为2.5~3mol/l。混合时还可加入一定量的纳米sio2、sio2、si3n4等第二相粘接剂从而形成多相粘结剂体系,促进界面层的致密化。
12.(3)坯体成型:将含有界面分隔层的陶瓷纤维胞体在钢模具中按一维定向排布,并加压250~350mpa成型,保压5~10 min;脱模后得到纤维独石结构陶瓷坯体。
13.(4)排胶与烧结:将纤维独石结构陶瓷坯体在真空炉中,200~500℃排胶1~3 h后,采用sps(放电等离子烧结)烧结,冷却脱模后得到仿生纤维独石结构氮化硼高温自润滑材料。sps烧结工艺:压力25~40 mpa;烧结温度1500℃~1700℃,烧结时间5~10 min。
14.本发明制备的仿生纤维独石结构氮化硼高温自润滑材料的呈现出典型的外部增韧机制,具有摩擦系数。
15.图1本发明制备的仿生纤维独石结构氮化硼高温自润滑材料断面照片。可见,其断面呈现出典型的网状结构,纤维胞体被界面层包裹,界面均匀的分布在整个材料中形成连续的界面润滑相,能保证在摩擦过程中界面润滑剂的充分供应。
16.图2、3分别为本发明制备的仿生纤维独石结构氮化硼高温自润滑材料的裂纹阻力曲线及裂纹扩展路径。由图可见,裂纹在扩展过程中受到的阻力不断上升(图2),这主要得益于裂纹偏转、裂纹分层和纤维拔出等外部增韧机制的存在(图3),这种外部增韧机制极大
地消解了局部高应力并耗散了断裂能,起到了优异的增韧效果。
17.图4为本发明制备的仿生纤维独石结构氮化硼高温自润滑材料在1000℃的高温裂纹阻力曲线。材料在1000℃的断裂过程中,裂纹受到的阻力不断上升,材料表现出较高的结构可靠性、良好的抗破坏性和显著的塑性断裂特征。
18.采用球盘式高温摩擦磨损实验机(ht
‑
1000)来测试样品的摩擦学性能,载荷为5~10 n,频率为3~5 hz,对偶为si3n4球或栓。图5为本发明制备的仿生纤维独石结构氮化硼高温自润滑材料在1000 ℃的高温摩擦系数曲线。可见材料在1000℃下摩擦系数约为0.3。
19.综上所述,本发明相对现有技术具有以下优点:1、采用相同材料的不同物相分别形成纤维胞体和胞界面层,利用cbn纤维胞体的承载作用及hbn弱界面层对裂纹的诱导和高温润滑作用,同时通过诱导裂纹偏转、消解局部高应力及使裂纹尖端载荷重新分布等外部增韧机制提高材料的韧性及服役可靠性,实现力学性能和高温润滑性能的统一,同时避免烧结过程中因立方氮化硼相变引入材料缺陷的问题;2、利用羟基聚合铝溶胶作为粘接剂前驱体可避免传统干混或湿混中团聚或不均匀,以及hbn难以烧结的问题,促进hbn界面层的致密化;3、通过纤维胞体和界面层中的粘接剂调控其致密性,从而调节材料的综合性能。
附图说明
20.图1本发明制备的仿生纤维独石结构氮化硼高温自润滑材料的断面照片。
21.图2本制备的仿生纤维独石结构氮化硼高温自润滑材料的裂纹阻力曲线。
22.图3 本发明制备的仿生纤维独石结构氮化硼高温自润滑材料的裂纹扩展路径。
23.图4本发明制备的仿生纤维独石结构氮化硼高温自润滑材料的高温裂纹阻力曲线。
24.图5本发明制备的仿生纤维独石结构氮化硼高温自润滑材料的高温摩擦系数曲线。
具体实施方式
25.实施例1以添加zro2(3y)粉体和α
‑
al2o3粉体为粘接剂的5~10μm的cbn粉体作为纤维胞体原料,其质量比为cbn:zro2(3y):al2o3=50:5:45。将纤维胞体原料粉末加入无水乙醇溶液,球磨20 h,球磨速度为150 r/min,球磨结束,放入70 ℃的干燥箱中干燥成粉体,并用0.1 mm的筛网过筛;将制备好的cbn纤维胞体原料粉末加入2wt%的pva胶黏剂,胶黏剂固相与粉体的质量比为1:32,得到纤维前驱体浆料,将浆料采用挤制成型的方法制成cbn纤维胞体,直径为0.6mm;将羟基聚合铝溶胶作为界面助剂前驱体,与1 μm的hbn粉体球磨混合10 h成均匀的界面浆料,其中,羟基聚合铝溶胶中al的浓度为2.5mol/l,hbn与al的质量比为77:1;将cbn纤维基体采用提拉浸渍的方式蘸取界面浆料,待其干燥后,采用单一轴向的排布方式,在320 mpa下干压成型,制成坯体;采用放电等离子烧结(sps)技术在1500℃、30 mpa下保温10 min,烧结成高可靠仿
生纤维独石结构氮化硼高温自润滑陶瓷材料。经检测,材料强度约为200 mpa,裂纹扩展阻力约为5~15 mpa
·
m
1/2
,1000℃摩擦系数约为0.35。
26.实施例2以添加si3n4粉体、aln粉体、α
‑
al2o3粉体及y2o3粉体为粘接剂的5~10μm的cbn粉体作为纤维胞体原料,其质量比为cbn:si3n4:aln:al2o3:y2o3=50:22:14:10:4。将纤维胞体原料粉末加入无水乙醇溶液,球磨20 h,球磨速度为150 r/min,球磨结束,放入60 ℃的干燥箱中干燥成粉体,并用0.1 mm的筛网过筛。将制备好的cbn纤维胞体原料粉末加入2wt%的pva胶黏剂,胶黏剂固相与粉体的质量比为1:33,得到纤维前驱体浆料,将浆料采用挤制成型的方法制成cbn纤维胞体,直径为0.8 mm;将si3n4粉体、aln粉体、α
‑
al2o3粉体及y2o3粉体作为粘接剂添加进3μm的hbn粉体中,其质量比为hbn:si3n4:aln:al2o3:y2o3=95:2.2:1.4:1.0:0.4,并将其配置成浓度为0.1 g/ml的界面浆料;将cbn纤维胞体采用提拉浸渍的方式蘸取界面浆料,待其干燥后,采用单一轴向的排布方式,在300 mpa下干压成型,制成坯体;采用放电等离子烧结(sps)技术在1600 ℃、40 mpa下保温时间10 min,烧结成高可靠仿生纤维独石结构氮化硼高温自润滑陶瓷材料。经检测,材料强度约为250 mpa,室温下裂纹扩展阻力约为4.7~20 mpa
·
m
1/2
,1000℃摩擦系数约为0.35,且摩擦过程中摩擦系数稳定。
27.实施例3以添加si3n4粉体、aln粉体、α
‑
al2o3粉体及y2o3粉体为粘接剂的5~10μm的cbn粉体作为纤维胞体原料,其质量比为cbn:si3n4:aln:al2o3:y2o3=50:22:14:10:4;将纤维胞体原料粉末加入无水乙醇溶液,球磨20 h,球磨速度为200 r/min,球磨结束,放入70 ℃的干燥箱中干燥成粉体,并用0.1 mm的筛网过筛;将制备好的cbn纤维胞体原料粉末加入2wt%的pva胶黏剂,胶黏剂固相与粉体的质量比为1:32,得到纤维前驱体浆料,将浆料采用挤制成型的方法制成纤维胞体,直径为0.6 mm;以1 μm的hbn粉体作为界面,以sic粉体、α
‑
al2o3粉体及y2o3粉体为界面粘接剂,其质量比为hbn:si3n4: al2o3:y2o3=66:25:5:4,加入无水乙醇配置成0.1 g/ml的界面浆料;将cbn纤维胞体采用提拉浸渍的方式蘸取界面层浆料,待其干燥后,采用单一轴向的排布方式,在250 mpa下干压成型,制成坯体;采用放电等离子烧结(sps)技术在1700 ℃、35 mpa下保温时间8 min,烧结成高可靠仿生纤维独石结构氮化硼高温自润滑陶瓷材料。经检测,材料强度约为230mpa,1000℃下裂纹扩展阻力约为5~16 mpa
·
m
1/2
,1000℃摩擦系数约为0.30,且摩擦过程中摩擦系数稳定。
再多了解一些
本文用于企业家、创业者技术爱好者查询,结果仅供参考。