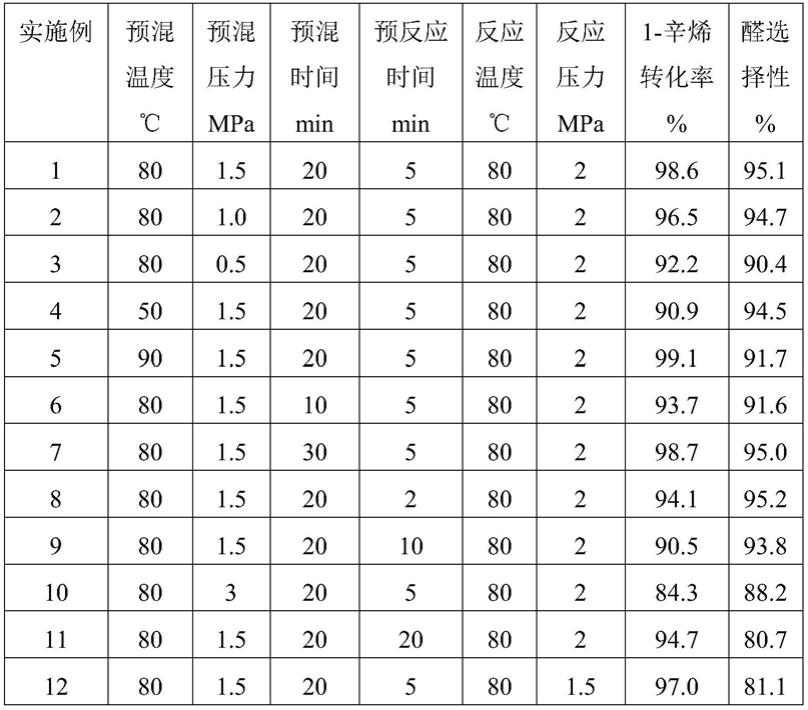
1.本发明涉及一种加氢甲酰化的方法,具体涉及一种具有改善铑催化剂体系活性和醛选择性的加氢甲酰化方法。
背景技术:
2.近年来,随着世界范围内塑料加工、汽车工业、电缆工业以及建筑业的快速发展,全球对增塑剂的需求越来越大,进而增加了增塑剂醇的需求。壬醇是目前需求量增长最快的增塑剂醇,主要是通过辛烯加氢甲酰化后,再经过氢化制得。
3.工业上加氢甲酰化生产使用的有机金属催化剂通常以钴(co)和铑(rh)作为金属活性中心。异壬醇这类高碳醇的工业生产以co系催化剂为主,但是由于钴催化工艺所需反应条件苛刻、选择性差、副反应多,且能耗高以及钴回收过程复杂等因素,其综合经济技术指标远不如rh催化工艺,因此基于rh催化工艺的研究非常重要。
4.使用铑催化剂进行高碳链烯烃氢甲酰化反应的不利之处在于,一方面rh是非常昂贵的贵金属,另一方面rh催化剂与配体的组合对于状态变化反应非常敏感,容易快速失活。因此提高rh/配体体系在反应中的活性和醛选择性十分必要。
5.rh系催化剂在加氢甲酰化过程中体现的活性以及所生产的n/i选择性(正构醛与异构醛的比值)取决于催化剂前驱体和配体的组合以及操作条件。
6.美国专利us8710276公开了配体chdp表示的环己烷二苯基膦配体,该配体虽然增加了催化剂稳定性,但是n/i选择性明显降低;美国专利us8507731在实施例8至14中公开了rh(co)2(acac)和杯芳烃双齿膦配体组合催化剂,该组合催化剂显示了较高的n/i选择性,但是反应活性较低,此外,该配体较为复杂,合成步骤繁琐,使用成本较高。另外,中国专利cn101293818公开了一种氢甲酰化方法,通过对混合丁烯氢甲酰化进行两段反应,很好的解决了两种烯烃的反应差异问题,提高烯烃利用率,但该种方法只局限于低碳链烯烃的氢甲酰化。中国专利cn103814006公开了一种在反应中具有改善的催化剂稳定性的氢甲酰化方法,通过在氢甲酰化反应中加入一种特殊的α,β-不饱和羰基化合物来抑制配体和催化剂的分解,这种方法在一定程度上增加了催化剂的稳定性,但同时也增加了反应成本。
技术实现要素:
7.针对现有技术的不足,本发明的目的是提供一种在反应中具有改善铑催化剂体系稳定性及活性的加氢甲酰化方法,设计合理的工艺流程,以便提高有机膦改性的铑催化剂体系在反应过程中的稳定性和活性,进而提高铑催化剂使用效率,降低生产成本。
8.本发明提供了一种在反应中具有改善铑催化剂体系活性的加氢甲酰化方法,具体涉及在有机膦改性的铑加氢甲酰化催化剂体系存在下以高碳烯烃为原料制备醛,其中需在一定条件下将一氧化碳和氢气与溶剂在反应釜内预混,再加入催化剂体系与原料高碳烯烃进行反应。
9.本发明将压力阶梯应用到本发明方法的反应阶段中,使得压力从预混阶段较低的
压力增加到反应阶段较高的压力。特别的,控制本发明方法反应阶段的压力比预混阶段的压力高至少0.5mpa。
10.本发明的第一方面提供了一种加氢甲酰化的方法,包括:
11.步骤a:将一氧化碳和氢气与有机溶剂进行混合,得到预混物。
12.根据本发明的一些实施方式,所述混合的温度为50-130℃,例如50℃、80℃、90℃。
13.根据本发明的优选实施方式,所述混合的温度为60-80℃。
14.根据本发明的一些实施方式,所述混合的压力为0-4mpa。
15.根据本发明的优选实施方式,所述混合的压力为0.5-3mpa。
16.根据本发明的优选实施方式,所述混合的压力为0.5-2.5mpa,例如0.5mpa、1mpa、1.5mpa。
17.根据本发明的一些实施方式,所述混合的时间为0.1-30min,例如10min、20min、30min。
18.根据本发明的优选实施方式,所述混合的时间为15-25min。
19.根据本发明的一些实施方式,所述一氧化碳和氢气的摩尔比为(0.1-20):1。
20.根据本发明的优选实施方式,所述一氧化碳和氢气的摩尔比为(1-10):1。
21.根据本发明的一个实施例,所述一氧化碳和氢气的摩尔比为1:1。
22.根据本发明的一些实施方式,所述方法还包括:
23.步骤b:将所述预混物与催化剂体系接触,进行预反应,得到预反应物;
24.步骤c:将所述预反应物与高碳烯烃接触,进行反应。
25.根据本发明的一些实施方式,所述预反应的时间为0.1-20min。
26.根据本发明的优选实施方式,所述预反应的时间为1-10min,例如2min、5min、10min。
27.根据本发明的一些实施方式,步骤c中所述反应的温度为60-140℃。
28.根据本发明的优选实施方式,步骤c中所述反应的温度为70-100℃,例如80℃。
29.根据本发明的一些实施方式,步骤c中所述反应的时间为30-120min。
30.根据本发明的优选实施方式,步骤c中所述反应的时间为60-105min,例如60min。
31.根据本发明的一些实施方式,步骤c中所述反应的压力高于步骤a中所述混合的压力。
32.根据本发明的优选实施方式,步骤c中所述反应的压力比步骤a中所述混合的压力高至少0.5mpa。
33.根据本发明的一些实施方式,步骤c中所述反应的压力为0-4mpa。
34.根据本发明的优选实施方式,步骤c中所述反应的压力为1-3mpa,例如1.5mpa、2mpa、3mpa。
35.根据本发明的一些实施方式,所述高碳烯烃为c6以上的烯烃。
36.根据本发明的优选实施方式,所述高碳烯烃为c8-c20的烯烃。
37.根据本发明的优选实施方式,所述高碳烯烃为辛烯。
38.根据本发明的一些实施方式,所述催化剂体系包括铑催化剂和有机膦化合物。
39.根据本发明的一些实施方式,所述铑催化剂由式(ⅰ)表示:
40.rh(l1)
x
(l2)
y
(l3)
z
ꢀꢀꢀꢀꢀꢀꢀ
(ⅰ)
41.其中,l1、l2和l3各自独立的选自氢、co、氯、三苯基膦和乙酰丙酮;x、y和z各自独立地选自0到5的整数,x、y和z中至少一个不为0。
42.根据本发明的一些实施方式,所述有机膦化合物选自含有c6-c10芳香基的有机膦化合物。
43.根据本发明的一些实施方式,所述有机膦化合物选自含有苯基的有机膦化合物。
44.根据本发明的一些实施方式,所述有机溶剂选自醛类化合物、酮类化合物、苯、苯的取代物、烷烃和取代烷烃中的至少一中。
45.根据本发明的优选实施方式,所述有机溶剂选自丁醛、戊醛、己醛、庚醛、辛醛、壬醛、甲基异丁基酮、乙酰苯、甲苯、二甲苯、氯苯和庚烷中的至少一种。
46.根据本发明的优选实施方式,所述有机溶剂选自甲苯和/或壬醛。
47.根据本发明的一些实施方式,以金属铑计,所述的铑催化剂的加入量为50-400ppm。
48.根据本发明的一些实施方式,以金属铑计,所述有机膦化合物与所述铑催化剂的摩尔比为0.5:1-200:1。
49.根据本发明的一些实施方式,以金属铑计,所述高碳烯烃与所述铑催化剂的摩尔比为100000:1-500:1。
50.根据本发明的优选实施方式,以金属铑计,所述高碳烯烃与所述铑催化剂的摩尔比为10000:1-2000:1。
51.本发明的另一方面提供了一种根据第一方面所述的方法在高碳烯烃加氢甲酰化制备醛中的应用。
52.根据本发明的一些实施方式,所述高碳烯烃为c6以上的烯烃。
53.根据本发明的优选实施方式,所述高碳烯烃为c8-c20的烯烃。
54.根据本发明的优选实施方式,所述高碳烯烃为辛烯。
55.本发明的有益效果为:本发明可以通过气相与液相预混,并对催化剂体系进行预活化提高催化剂的活性和醛选择性,以此提高铑催化剂利用效率,降低生产成本。
具体实施方式
56.下面通过实施例对本发明作进一步的阐述,但是这些实施例无论如何都不对本发明的范围构成限制。
57.实施例1
58.在惰性气氛下的手套箱内,将8.9mg三(三苯基膦)羰基氢化铑和330mg三苯基膦混合溶于2ml甲苯中,混合均匀后加入反应釜的进料瓶备用。本反应装置采用50ml高压釜反应装置。将高压釜加热到80℃,抽真空后用合成气体(co:h2=1:1)置换数次,将放空阀打开,然后迅速将20.86ml甲苯加入到反应釜内,设定压力为1.5mpa,向反应釜内通入合成气体(co:h2=1:1),预混合搅拌20min,然后将进样装置打开,将2ml催化剂体系完全加入反应釜内,关闭进样装置继续搅拌5min。将压力调节到2mpa,加入12.14ml的1-辛烯进行反应,反应60min。反应完成后,收集反应液。对过滤出催化剂的液相产品进行色谱分析,测得反应结果如表1所示。
59.实施例2
60.实验方法同实施例1,将预混压力改为1.0mpa,其余实验条件不变,测试结果如表1所示。
61.实施例3
62.实验方法同实施例1,将预混压力改为0.5mpa,其余实验条件不变,测试结果如表1所示。
63.实施例4
64.实验方法同实施例1,将预混温度改为50℃,反应温度仍然为80℃,其余实验条件不变,测试结果如表1所示。
65.实施例5
66.实验方法同实施例1,将预混温度改为90℃,反应温度仍然为80℃,其余实验条件不变,测试结果如表1所示。
67.实施例6
68.实验方法同实施例1,将溶剂与合成气预混时间改为10min,其余实验条件不变,测试结果如表1所示。
69.实施例7
70.实验方法同实施例1,将溶剂与合成气预混时间改为30min,其余实验条件不变,测试结果如表1所示。
71.实施例8
72.实验方法同实施例1,将混合液与催化剂预反应时间改为2min,其余实验条件不变,测试结果如表1所示。
73.实施例9
74.实验方法同实施例1,将混合液与催化剂预反应时间改为10min,其余实验条件不变,测试结果如表1所示。
75.实施例10
76.实验方法同实施例1,将预混压力改为3.0mpa,其余实验条件不变,测试结果如表1所示。
77.实施例11
78.实验方法同实施例1,将加入催化剂后的搅拌时间改为20min,其余实验条件不变,测试结果如表1所示。
79.实施例12
80.实验方法同实施例1,不改变压力,仍在1.5mpa下加入1-辛烯进行反应,其余实验条件不变,测试结果如表1所示。
81.对比例1
82.实验方法同实施例1,其中不对催化剂体系进行预反应,直接将催化剂和1-辛烯同时加入反应釜,实验结果如下:1-辛烯转化率:87.7%;醛选择性:89.7%。
83.从对比例中可以看出,不对催化剂体系进行预反应催化剂反应活性以及醛选择性都较低。
84.表1
[0085][0086]
应当注意的是,以上所述的实施例仅用于解释本发明,并不构成对本发明的任何限制。通过参照典型实施例对本发明进行了描述,但应当理解为其中所用的词语为描述性和解释性词汇,而不是限定性词汇。可以按规定在本发明权利要求的范围内对本发明作出修改,以及在不背离本发明的范围和精神内对本发明进行修订。尽管其中描述的本发明涉及特定的方法、材料和实施例,但是并不意味着本发明限于其中公开的特定例,相反,本发明可扩展至其他所有具有相同功能的方法和应用。
再多了解一些
本文用于企业家、创业者技术爱好者查询,结果仅供参考。