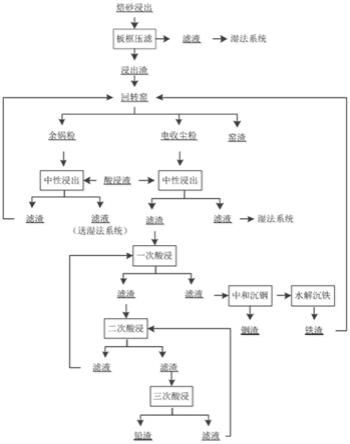
1.本发明涉及湿法炼锌领域,尤其涉及一种余锅粉的处理方法。
背景技术:
2.湿法炼锌过程中,锌焙砂经电解硫酸废液浸出,产出湿法矿浆,湿法矿浆经板框压滤后得到锌浸出渣(主要成分为铁酸锌,化学式为zno
·
fe2o3),锌浸出渣经回转窑火法还原挥发、收尘后,得到次氧化锌粉(主要成分为zno)。根据收尘设备位置及类型的区别,得到的次氧化锌粉的成分及具体名称不同。其中,在余热锅炉处收集得到的次氧化锌粉命名为余锅粉,按重量百分数计,其主要元素成分为zn<40%、fe>12%、pb>6%、s>3%、c>10%、有机物>14%;在电收尘处收集得到的次氧化锌粉命名为电收尘粉,按重量百分数计,其主要元素成分为zn>57%、fe<6%、pb>7%、s>3%、c<3%,有机物>6%。与电收尘相比,由于余热锅炉更靠近回转窑下料区域,机械夹带浸出渣与燃料的混合料严重,导致余锅粉中杂质含量高,有价金属品位偏低,且余锅粉中杂质fe含量是电收尘粉的2倍以上。
3.目前,处理该类次氧化锌粉的流程为:余锅粉与电收尘粉混合后,先加入酸浸液(主要成分为h2so4)将其中以zno形式存在的容易浸出的zn浸出,同时为进一步将次氧化锌粉中如铁酸锌等中等难浸出的zn浸出,需再依次进行一次酸浸、二次酸浸、三次酸浸,其中二次酸浸滤液(主要成分为h2so4)作为一次酸浸液、三次酸浸滤液(主要成分为h2so4)作为二次酸浸液。在一次酸浸、二次酸浸、三次酸浸过程中,电收尘粉与余锅粉中的铁进入溶液中,后续又需要沉铁产出大量铁渣并将大量铁渣进行处理,同时最终还会产出含锌约10%(质量百分数)的铅渣,由于外卖时铅渣中的锌不计价,导致大量金属锌损失。
4.因此,现有技术还有待于改进和发展。
技术实现要素:
5.鉴于上述现有技术的不足,本发明的目的在于提供一种余锅粉的处理方法,旨在解决现有工艺处理余锅粉产出铅渣夹带金属锌导致金属锌损失大的问题。
6.本发明的技术方案如下:
7.本发明的第一方面,提供一种余锅粉的处理方法,其中,包括步骤:
8.提供余锅粉,所述余锅粉由湿法炼锌过程中产出的锌浸出渣在回转窑中进行还原挥发后在余热锅炉处收集得到;
9.将所述余锅粉与酸浸液加入到反应槽中进行中性浸出反应,得到混合液;
10.将所述混合液进行过滤,得到滤液和滤渣;
11.将所述滤液送至湿法炼锌系统,将所述滤渣送至所述回转窑中进行还原挥发。
12.可选地,所述余锅粉的组分包括zno、zno
·
fe2o3、zns、pbo。
13.可选地,所述酸浸液的组分包括h2so4。
14.可选地,所述酸浸液的酸度大于100g/l。
15.可选地,所述中性浸出反应的温度为55
‑
65℃,所述中性浸出反应的时间为1.5
‑
3h。
16.可选地,所述混合液的ph为4.0
‑
4.5。
17.可选地,将所述混合液通过板框压滤机进行过滤。
18.可选地,将所述滤渣送至所述回转窑中进行还原挥发的具体步骤包括:
19.将所述滤渣与燃料混合后,送至所述回转窑中进行还原挥发。
20.本发明的第二方面,提供一种湿法炼锌过程中产出的锌浸出渣的处理方法,其中,包括步骤:
21.将所述湿法炼锌过程中产出的锌浸出渣送至回转窑中进行还原挥发,得到余锅粉和电收尘粉;
22.采用本发明所述的余锅粉的处理方法处理所述余锅粉。
23.可选地,所述将所述湿法炼锌过程中产出的锌浸出渣送至回转窑中进行还原挥发后,还可得到电收尘粉;依次采用中性浸出、一次酸浸、二次酸浸、三次酸浸处理所述电收尘粉。
24.有益效果:本发明提供了一种余锅粉的处理方法,将湿法炼锌过程中产出的锌浸出渣在回转窑中还原挥发后在余热锅炉处收集得到的余锅粉与酸浸液加入到反应槽中进行反应,得到混合液并将混合液进行过滤,得到含有锌离子的滤液和含有铅和铁等元素的滤渣,将含有锌离子的滤液送至湿法炼锌系统,将含有铅和铁等元素的滤渣送至回转窑中继续进行还原挥发处理,铅元素还原挥发进入氧化锌粉中进行回收,铁元素最终以铁的氧化物形式进入窑渣中。与现有技术中余锅粉与电收尘粉混合一起酸浸处理相比,本发明中将余锅粉与电收尘粉分开处理,由于已经先对余锅粉中的锌进行中性浸出并将含锌离子的滤液送至湿法炼锌系统,所以减少了铅渣夹带金属锌而导致的金属锌的损失;同时余锅粉中的铁进入窑渣中,避免了余锅粉与电收尘粉一起进行湿法酸浸处理时,含铁量高的余锅粉会产出大量铁渣的问题,进而减少了处理铁渣所需的成本。
附图说明
25.图1为余锅粉现有处理工艺流程图。
26.图2为本发明实施例中的余锅粉处理工艺流程图。
具体实施方式
27.本发明提供一种余锅粉的处理方法,为使本发明的目的、技术方案及效果更加清楚、明确,以下对本发明进一步详细说明。应当理解,此处所描述的具体实施例仅仅用以解释本发明,并不用于限定本发明。
28.现有技术中,将湿法炼锌过程中的浸出渣经回转窑火法还原挥发、收尘后得到的余锅粉(其铁含量是电收尘粉的两倍以上)和电收尘粉一起混合后进行酸浸处理,具体工艺流程如图1所示,将余锅粉和电收尘粉混合后先加入酸浸液(主要成分为h2so4)进行中性浸出,将其中以zno形式存在的容易浸出的zn浸出,得到滤液和滤渣,将得到的滤液送至湿法炼锌系统,同时为进一步将滤渣中中等难浸出的zn(如铁酸锌中的锌)浸出,需再将得到的滤渣依次进行一次酸浸、二次酸浸和三次酸浸,其中二次酸浸滤液(主要成分为h2so4)作为一次酸浸液、三次酸浸滤液(主要成分为h2so4)作为二次酸浸液。在一次酸浸、二次酸浸、三
次酸浸过程中,电收尘粉与余锅粉中的铁将进入溶液中,最终过滤后得到铅渣和含有铁离子的滤液,由于余锅粉中存在大量的铁,所以滤液中存在大量的铁离子,后续在一次酸浸滤液中需要进行水解沉铁产出大量铁渣,得到的铁渣需要进一步在回转窑中处理,最终进入窑渣,大量铁渣的处理耗费大量成本(例如回转窑的加工成本),所以在工艺过程中铁渣是不希望得到的。此外,产出的铅渣中含质量分数约为10%的金属锌,由于外卖时铅渣中的锌不计价,导致大量金属锌损失。也就是说,现有工艺中,余锅粉和电收尘粉混合后进行酸浸处理,由此带来的问题是最终会产出大量的铁渣和含有质量百分数为10%的金属锌的铅渣,前者导致铁渣处理成本增大,后者导致大量金属锌的损失。基于此,本发明实施例将余锅粉与电收尘粉分开处理,提供了一种余锅粉的处理方法,其工艺流程图参见图2中余锅粉的处理工艺部分,包括步骤:
29.s1、提供余锅粉,所述余锅粉由湿法炼锌过程中产出的锌浸出渣在回转窑中进行还原挥发后在余热锅炉处收集得到;
30.s2、将所述余锅粉与酸浸液加入到反应槽中进行中性浸出反应,得到混合液;
31.s3、将所述混合液进行过滤,得到滤液和滤渣;
32.s4、将所述滤液送至湿法炼锌系统,将所述滤渣送至所述回转窑中进行还原挥发。
33.湿法炼锌过程中产出的锌浸出渣不仅含有锌,还含有铅、铟等有价金属,将锌浸出渣在回转窑中被还原为金属而挥发后进入烟气,在烟气中被氧化为氧化物,随着烟气进入收尘系统被收集下来,其中,在余热锅炉处收集得到余锅粉,在电收尘处收集得到电收尘粉。本实施例中,仅将在余热锅炉处收集得到的余锅粉与酸浸液加入到反应槽中进行中性浸出反应,得到混合液并将混合液进行过滤,得到含有锌离子的滤液和含有铅和铁等元素的滤渣,将含有锌离子的滤液送至湿法炼锌系统,将含有铅和铁等元素的滤渣送至回转窑中继续进行还原挥发处理,铅元素还原挥发进入氧化锌粉中进行回收,铁元素最终以铁的氧化物形式进入窑渣中。与现有技术中余锅粉与电收尘粉混合一起酸浸处理相比,本实施例中将余锅粉与电收尘粉分开处理,由于已经先对余锅粉中的锌进行中性浸出并将含锌离子的滤液送至湿法炼锌系统,所以减少了铅渣夹带金属锌而导致的金属锌的损失;同时余锅粉中的铁和铅分别进入窑渣和氧化锌粉中,避免了余锅粉与电收尘粉混合一起进行湿法酸浸处理时,含铁量高的余锅粉会产出大量铁渣的问题,进而减少了处理铁渣所需的成本,此外也减少了铅渣量,进一步减少了铅渣夹带金属锌而导致的金属锌的损失。将本实施例中的余锅粉的处理方法应用到湿法炼锌过程中产出的锌浸出渣的处理工艺中时,不必改变现有主要工艺流程且可以利用现有设备,易于实现工业化改造生产,也即本实施例的处理方法不必改变现有电收尘粉的处理工艺(如图2中所示的电收尘粉处理工艺部分)。
34.湿法炼锌过程中产出的锌浸出渣在回转窑中挥发还原后,在余热锅炉处收集得到余锅粉,在电收尘处收集得到电收尘粉,步骤s1中,仅将在余热锅炉处收集得到的余锅粉与酸浸液加入到反应槽中进行中性浸出反应,得到混合液。
35.步骤s1中,在一种实施方式中,所述余锅粉的组分包括zno、zno
·
fe2o3、zns、pbo,但不限于此。本实施方式中,余锅粉的组分主要包括zno、zno
·
fe2o3、zns、pbo、zns,还包括一些有机物,本实施方式中余锅粉中的zn元素主要以zno、zno
·
fe2o3、zns的形式存在,余锅粉中的fe元素主要以zno
·
fe2o3的形式存在,余锅粉中的pb元素主要以pbo的形式存在,余锅粉中的s元素主要以zns的形式存在。
36.所述余锅粉中,按重量百分数计,包括以下元素:zn<40%、fe>12%、pb>6%、s>3%、c>10%。所述余锅粉中杂质fe元素的含量是电收尘粉(fe<6%)的2倍以上。
37.步骤s2中,在一种实施方式中,所述酸浸液的组分包括h2so4,所述酸浸液可以是湿法炼锌过程中产生的酸性溶液,但不限于此。
38.步骤s2中,主要是将余锅粉中以zno形式存在的zn浸出,所述余锅粉与酸浸液进行中性浸出反应的主要化学反应为:
39.zno h2so4=znso4 h2o
40.中性浸出反应后余锅粉中氧化锌的锌以zn
2
的形式存在于滤液中,而其他成分以滤渣的形式滤出。
41.在一种实施方式中,所述酸浸液的酸度大于100g/l。该酸度可以保证余锅粉中氧化锌中的锌的浸出。
42.在一种实施方式中,所述中性浸出反应的温度为55
‑
65℃,所述中性浸出反应的时间为1.5
‑
3h,所述混合液的ph为4.0
‑
4.5。也就是说,余锅粉与酸浸液在反应槽中混合反应时应该保持反应温度为55
‑
65℃,反应时间为1.5
‑
3h,并控制反应终点溶液体系的ph值为4.0
‑
4.5,该反应温度和反应时间可以使得余锅粉与酸浸液在反应槽中混合反应时锌有较高的浸出率同时又避免铁浸出。
43.在一种实施方式中,所述反应槽配套有蒸汽管道,通过所述蒸汽管道中的蒸汽调控所述反应槽中的温度,使得反应温度控制在55
‑
65℃。
44.步骤s3中,将所述混合液进行过滤,得到含有锌离子的滤液和含有铁元素和铅等元素的滤渣,当然,滤渣中除了含有铁元素和铅元素外,还含有未浸出的锌以及其他元素、这些元素以固体氧化物或硫化物等的形式存在于滤渣中,滤渣送至回转窑中继续进行还原挥发处理,最终进入到窑渣中。
45.在一种实施方式中,将所述混合液通过板框压滤机进行过滤,但不限于此。
46.步骤s4中,在一种实施方式中,将所述滤液送至湿法炼锌系统,经过净化和电积等工序,得到金属锌。
47.在一种实施方式,将所述滤渣送至所述回转窑中进行还原挥发的具体步骤包括:
48.将所述滤渣与燃料混合后,送至所述回转窑中进行还原挥发,可回收其中的铅等有价金属。
49.在一种实施方式中,所述燃料选自焦粉、无烟煤中的一种或两种,但不限于此。
50.本发明实施例还提供一种湿法炼锌过程中产出的锌浸出渣的处理方法,其工艺流程如图2所示,其中,包括步骤:
51.将所述锌浸出渣送至回转窑中进行还原挥发,得到余锅粉;
52.采用本发明上述实施例所述的余锅粉的处理方法处理所述余锅粉;
53.在一种实施方式中,所述将所述湿法炼锌过程中产出的锌浸出渣送至回转窑中进行还原挥发后,还可得到电收尘粉,依次采用中性浸出、一次酸浸、二次酸浸、三次酸浸处理所述电收尘粉。将所述电收尘粉依次经过中性浸出、一次酸浸、二次酸浸、三次酸浸,可以得到一次酸浸滤液和铅渣;将所述一次酸浸滤液依次进行中和沉铟、水解沉铁,得到铟渣和铁渣;将所述铁渣送至回转窑中进行还原挥发。
54.下面结合图2进行详细介绍:将锌焙砂经电解硫酸废液浸出,产出湿法矿浆,湿法
矿浆经板框机压滤后得到含锌离子的滤液和锌浸出渣(主要成分为铁酸锌,化学式为zno
·
fe2o3),将含锌离子的滤液送至湿法炼锌系统,将锌浸出渣送至回转窑中进行火法还原挥发、收尘后得到余锅粉、电收尘粉和窑渣。将余锅粉与酸浸液混合(可来自湿法炼锌过程中产生的酸性溶液,主要成分为h2so4)进行中性浸出,得到含锌离子的滤液和含有铁元素和铅元素的滤渣,将含锌离子的滤液送至湿法炼锌系统,将含有铁元素和铅元素的滤渣送至回转窑继续进行还原挥发,最终分别进入窑渣和氧化锌粉中。然后,将电收尘粉与酸浸液混合进行中性浸出,将大部分以zno形式存在的zn浸出,得到滤液(含锌离子)和滤渣,将滤液(含锌离子)送至湿法炼锌系统,滤渣进行一次酸浸(酸浸液为二次酸浸得到的二次酸浸滤液),得到一次酸浸滤渣和一次酸浸滤液,一次酸浸滤液分别进行中和沉铟和水解沉铁,得到铟渣和铁渣,铁渣送至回转窑继续进行还原挥发,中和沉铟和水解沉铁后得到的滤液送至湿法炼锌系统中(图中未标识出)。一次酸浸滤渣进行二次酸浸(酸浸液为三次酸浸得到的三次酸浸滤液),得到二次酸浸滤液和二次酸浸滤渣,二次酸浸滤液作为一次酸浸的酸浸液,二次酸浸滤渣进行三次酸浸,得到铅渣和三次酸浸滤液,三次酸浸滤液作为二次酸浸的酸浸液。
55.与现有技术相比,本实施方式中将锌浸出渣经回转窑火法还原挥发、收尘后得到余锅粉和电收尘粉分开处理,实现余锅粉中锌与铅、铁的初步分离,余锅粉中大部分锌以锌离子的形成存在于滤液中并送至湿法炼锌系统,余锅粉中的铁和铅在中性浸出过程中并没有浸出,而是以滤渣的形式进入到回转窑中,最终分别进入到窑渣和氧化锌粉中。因此,本实施例中仅对电收尘粉进行一次酸浸、二次酸浸、三次酸浸,避免了余锅粉与电收尘粉混合一起进行湿法酸浸处理时,含铁高的余锅粉产出大量铁渣的问题,同时可减少铅渣量,可减少铅渣夹带金属锌而导致的金属锌的损失,同时将本发明上述实施例中的余锅粉的处理方法应用到湿法炼锌过程中产出的锌浸出渣的处理工艺中时,不必改变现有主要工艺流程且可以利用现有设备,易于实现工业化改造生产。
56.下面通过具体的实施例对本发明作进一步地说明。
57.实施例1
58.某锌冶炼企业某月处理锌浸出渣9000吨,锌浸出渣经回转窑还原挥发后分别得到余锅粉988.2吨、电收尘粉1912.5吨。按重量百分数计,余锅粉主要元素成分为:zn~39.15%、fe~13.59%、pb~6.37%;电收尘粉主要元素成分为:zn~59.81%、fe~5.38%、pb~7.25%。按现有工艺流程(如图1所示),将该余锅粉与电收尘粉混合后经中性浸出
‑
一次酸浸
‑
二次酸浸
‑
三次酸浸处理后,共计产出铁渣643.80吨,产出铅渣1120.03吨,铅渣含锌10.1%,外卖铅渣造成金属锌损失113.12吨。
59.实施例2
60.某锌冶炼企业某月处理浸出渣8970.9吨,锌浸出渣经回转窑还原挥发后分别得到余锅粉924.3吨、电收尘粉1898.1吨。按重量百分数计,余锅粉主要元素成分为:zn~39.72%、fe~12.42%、pb~6.82%;电收尘粉主要元素成分为:zn~60.2%、fe~5.81%、pb~7.74%。采用本发明的余锅粉的处理工艺(如图2所示),将余锅粉与酸浸液在反应槽内混合,控制反应温度为60℃,反应终点溶液体系ph为4.5,反应时间为2h,反应结束后利用板框压滤机进行压滤,滤液送湿法炼锌系统,滤渣与燃料配料后进回转窑处理。将电收尘粉与酸浸液在反应槽内混合,控制反应温度为60℃,反应终点溶液体系ph为4.5,反应时间为2h,
反应结束后利用板框压滤机进行压滤,滤渣再经一次酸浸
‑
二次酸浸
‑
三次酸浸处理后,共计产出铁渣299.33吨,产出铅渣816.18吨,铅渣含锌9.6%,外卖铅渣造成金属锌损失78.35吨。
61.本发明的工艺流程与现有工艺流程相比,折算为处理量为9000吨/月的条件下,每月将减少产出铁渣344.47吨,减少铅渣造成金属锌损失34.77吨。
62.综上所述,本发明提供的一种余锅粉的处理方法,本发明将余锅粉与电收尘粉分开处理,将湿法炼锌过程中产出的锌浸出渣经回转窑还原挥发后在余热锅炉处收集得到的余锅粉与酸浸液加入到反应槽中进行反应,得到混合液并将混合液进行过滤,得到含有锌离子的滤液和含有铅和铁元素的滤渣,将含有锌离子的滤液送至湿法炼锌系统,将含有铅和铁等元素的滤渣送至回转窑中继续进行还原挥发处理,铁元素和铅元素最终分别进入窑渣和氧化锌粉中。与现有技术中余锅粉与电收尘粉混合一起酸浸处理相比,本发明中将余锅粉与电收尘粉分开处理,由于已经先对余锅粉中的锌进行中性浸出并将含锌滤液送至湿法炼锌系统,所以减少了铅渣夹带金属锌而导致的金属锌的损失;同时余锅粉中铁和铅分别进入窑渣和氧化锌粉中,避免了余锅粉与电收尘粉混合一起进行湿法酸浸处理时,含铁量高的余锅粉产出大量铁渣的问题,进而减少了处理铁渣所需的成本,此外相比于余锅粉与电收尘粉混合一起进行酸浸处理,本发明减少了铅渣量。同时本发明中的处理方法不必改变现有主要工艺流程且可以利用现有设备,易于实现工业化改造生产。
63.应当理解的是,本发明的应用不限于上述的举例,对本领域普通技术人员来说,可以根据上述说明加以改进或变换,所有这些改进和变换都应属于本发明所附权利要求的保护范围。
再多了解一些
本文用于企业家、创业者技术爱好者查询,结果仅供参考。