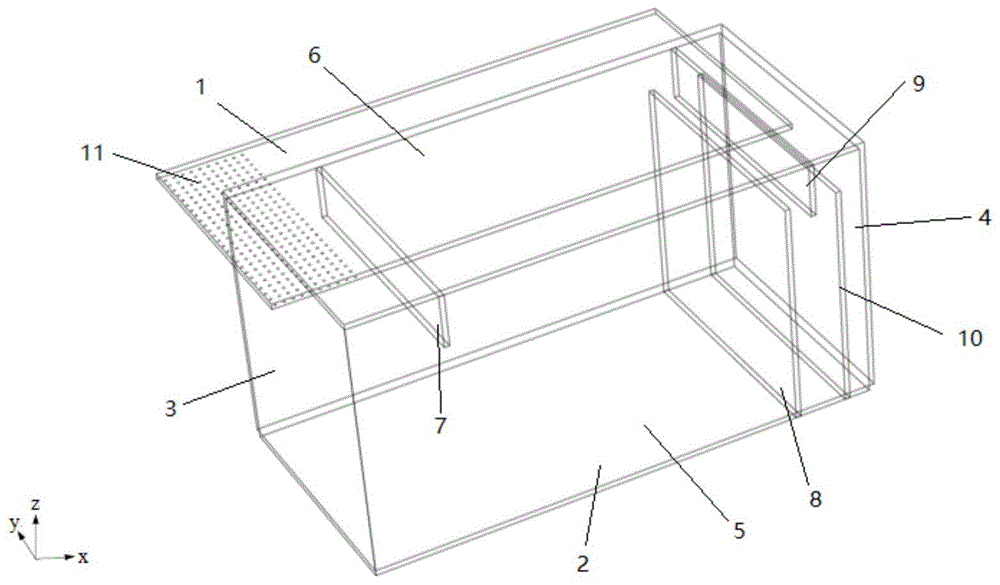
本发明属于低频吸声降噪领域,特别涉及穿孔板结构及应用该结构的变截面弯折空腔的低频带宽吸声超装置。
背景技术:
低频声波的穿透性强,普通材料的固有损耗弱,低频的降噪一直是具有挑战性的问题。根据经典的声学理论,多孔材料和微穿孔板吸声体通常具有与工作波长相当的结构厚度,在设计传统背衬空腔的微穿孔板吸声器时,在低频(<500hz)范围内其厚度大于5cm,容易受到空间制约。
近年来声学超材料的概念为低频吸声器提供了新思路,wu发表在appliedphysicsletters期刊中的文章low-frequencysoundabsorptionofhybridabsorberbasedonmicro-perforatedpanelandcoiled-upchannels,其设计重点是降低吸声峰值,从而没有考虑元胞结构的吸声带宽,在专利cn110767207a中,设计出盘绕型多吸收峰的低频吸声器,在417hz有吸收峰值,其吸收系数超过0.98,但是绝对带宽较窄(<100hz)。在专利号为cn110176223a中,设计出任意形状迷宫型低频吸声装置,可以实现吸声系数的绝对带宽为100hz,但此时的共振频率较高,为800hz。在专利号为cn112185327a中,设计出嵌套式微缝低频吸声单元,可以实现宽频带吸声,但是吸声结构需要层层嵌套且微缝的宽度仅为0.3~3毫米,在实际应用加工中容易产生误差,从而影响吸收带宽。这阻碍了在实际工程中的应用。
技术实现要素:
本发明解决的技术问题是:针对现有技术背景下具有宽频带的低频吸声结构太厚,以及相对应的共振频率过高,狭缝宽频带的吸声超结构不易于加工,迷宫型超结构低频吸声频带太窄,的问题,设计出将穿孔板结构和变截面弯折空腔相结合的低频带宽吸声超装置。
本发明的技术方案是:一种穿孔板结构,板体一端开有若干亚毫米至毫米级孔,且该若干亚毫米至毫米级孔均匀排列。
本发明进一步的技术方案是:所述亚毫米至毫米级孔孔径为0.35mm~0.75mm。
本发明进一步的技术方案是:所述板体的总穿孔率为1.8%~6%。
本发明进一步的技术方案是:所述亚毫米至毫米级孔的孔间距为1.26mm~5.00mm。
本发明进一步的技术方案是:变截面弯折空腔的低频带宽吸声超装置,其特征在于,包括壳体、若干第一空腔板和若干第二空腔板,其中若干第一空腔板一端与穿孔板内侧连接,和若干第二空腔板均位于壳体内;所述壳体内部为空腔体且一端开口有一端封闭,穿孔板盖在开口端上,且穿孔板朝向声源,穿孔板上的孔位于壳体一侧;其中一个第一空腔板与穿孔板内侧固定连接,未接触壳体底部,两个板面相处垂直且连接位置为穿孔板上亚毫米至毫米级孔的边界处;若干第二空腔板置于壳体内另一侧,与穿孔板内侧不接触形成间隙,第二空腔板和壳体底部和内壁形成密封;若干第二空腔板和第一空腔板交叉平行放置并留有空隙。
本发明进一步的技术方案是:当声源从亚毫米至毫米级孔进入后,经第一空腔板阻挡垂直向下,之后经过第二空腔板和另一第一空腔板形成的弯折路线后,最终落入离壳体另一侧最近的第二弯折板和壳体另一侧之间,最终能量耗散。
本发明进一步的技术方案是:所述第一空腔板和第二空腔板采用金属材料制成。
本发明进一步的技术方案是:所述壳体的厚度为0.50mm~1.00mm。
本发明进一步的技术方案是:所述隔板厚度为0.50mm~1.00mm。
发明效果
本发明的技术效果在于:本发明形状简单、使用范围广、吸声峰值低,吸收带宽大,在低频噪声控制工程中具有良好的应用前景。具体产生的有益效果如下:
(1)本发明设计穿孔板结构,声源首先通过穿亚毫米至毫米级孔,吸声结构变成具有空腔的穿孔吸声体;其次,空腔内将不等高度的隔板和穿孔板、下面板依次相连,构成和穿孔板、下面板相互平行的串联变截面弯折空腔,和传统微穿孔板吸声结构相比,使得吸声体的厚度明显减小;再者,变截面空腔在不改变外形尺寸的情况下,可以大幅度增加声波的传播路径,并且增加声波的损耗,使吸收峰更有效的向低频移动;最后,目前现有的折叠空腔超结构吸声带宽很窄,本发明针对此问题,引入变截面弯折空腔,声波吸收带宽增大,并且具有带宽可调节的优势。
(2)经验证,穿孔板的总穿孔率达到1.8%~6.0%。
(3)本发明相比于现有的具有相同弯折空腔数的迷宫型空腔吸声超结构,吸声系数的相对带宽(是指吸收系数的半最大值处的两个频率之差与共振频率的比值)由50%提升到83%。
(4)通过在传统穿孔板吸声体的基础上,引入由四个高度不同的隔板依次沿着穿孔板和下面板在x方向排列,在空腔内形成截面突变的空腔盘绕结构,从而实现吸声体可以在不增加总厚度的情况下,显著增强对低频噪声的吸收性能,极大地拓展了穿孔型吸声体的应用场景。
(5)将弯折空腔和微穿孔板耦合来设计宽频带超薄吸声体,传统的穿孔板在较高频段内有高效的吸收效率,弯折空腔具有减小结构厚度的优势。对空腔进行弯折设计,使得吸声体的厚度显著减小,并增强低频的吸收性能,拓宽吸收带宽。
附图说明
图1为本发明的坐标定义和单独结构、组合结构示意图
图2为本发明第二结构示意图
图3为本发明的声波路径示意图
图4为本实施例中吸声曲线示意图
附图标记说明:1-穿孔板;2-下面板;3-左框板;4-右框板;5-前框板;6-后框板;7-变截面弯折空腔板ⅰ;8-变截面弯折空腔板ⅱ;9-变截面弯折空腔板ⅲ;10-变截面弯折空腔板ⅳ;11-亚毫米至毫米级孔。
具体实施方式
在本发明的描述中,需要理解的是,术语“中心”、“纵向”、“横向”、“长度”、“宽度”、“厚度”、“上”、“下”、“前”、“后”、“左”、“右”、“竖直”、“水平”、“顶”、“底”、“内”、“外”、“顺时针”、“逆时针”等指示的方位或位置关系为基于附图所示的方位或位置关系,仅是为了便于描述本发明和简化描述,而不是指示或暗示所指的装置或元件必须具有特定的方位、以特定的方位构造和操作,因此不能理解为对本发明的限制。
参见图1-图4,一种基于变截面弯折空腔的低频带宽吸声超结构,包括穿孔板1、下面板2、左框板3、右框板4、前框板5、后框板6、变截面弯折空腔板-ⅰ7、变截面弯折空腔板-ⅱ8、变截面弯折空腔板-ⅲ9、变截面弯折空腔板-ⅳ10、亚毫米至毫米级孔11;穿孔板1和下面板2相互平行,左框板3和右框板4相互平行,并与下面板2相互垂直,前框板5和后框板6相互平行,并与下面板2相互垂直;穿孔板1朝向声源,下面板2背向声源,变截面弯折空腔板-ⅰ7、变截面弯折空腔板-ⅱ8、变截面弯折空腔板-ⅲ9、变截面弯折空腔板-ⅳ10位于穿孔板1、下面板2、左框板3、右框板4、前框板5和后框板6组成的立方体空腔内,在y方向止于前框板5和后框板6,如此形成连通的变截面弯折空腔;穿孔板1上有亚毫米至毫米级孔11,微穿孔11集中变截面弯折空腔板-ⅰ7和左框板3之间;以上所有结构钎焊(或胶粘)在一起构成一个元胞结构。
所述穿孔板、下面板、左框板、右框板、前框板、后框板和组成变截面弯折空腔的隔板;穿孔板和下面板相互平行,左框板和右框板相互平行,并与下面板相互垂直,前框板和后框板相互平行,并与下面板相互垂直;穿孔板朝向声源,下面板背向声源,变截面弯折空腔位于穿孔板、下面板、左框板、右框板、前框板和后框板组成的立方体空腔内,由具有不同结构参数的隔板相互穿插组成;空腔内隔板在x方向间隔一定的距离依次排开,在y方向止于前框板和后框板,在z方向,第一个隔板和穿孔板相接,第二个隔板和下面板相接,以此类推连接完所有空腔内的隔板,如此形成连通的空腔;穿孔板上有亚毫米至毫米级孔,微穿孔集中在第一个面板和左框板之间;左框板、右框板、前框板和后框板构成结构外框架,以上所有结构钎焊(或胶粘)在一起。
进一步,所述基于变截面弯折空腔的低频带宽吸声超结构上穿孔板的孔径为亚毫米至毫米级0.35mm~0.75mm。
进一步,基于变截面弯折空腔的低频带宽吸声超结构的穿孔板的总穿孔率为1.8%~6%。
进一步,穿孔板的厚度为0.8mm~1.00mm。
进一步,穿孔板上亚毫米至毫米级孔的孔间距为1.26mm~5.00mm
进一步,组成弯折空腔的隔板、下面板、左框板、右框板、前框板和后框板的厚度为0.50mm~1.00mm.。
进一步,组成弯折空腔的隔板高度为5.00mm~45.00mm。
进一步,穿孔板、组成弯折空腔的隔板、下面板、左框板、右框板、前框板和后框板的材质为金属,如铝、不锈钢等。
图1展示了本发明的基于变截面弯折空腔的低频带宽吸声超结构的一个实施例的三维解构示意图,该吸声超结构包括:穿孔板1、下面板2、左框板3、右框板4、前框板5、后框板6、变截面弯折空腔板-ⅰ7、变截面弯折空腔板-ⅱ8、变截面弯折空腔板-ⅲ9、变截面弯折空腔板-ⅳ10、亚毫米至毫米级孔11。
基于变截面弯折空腔的低频带宽吸声超结构的一个实施例的三维解构示意图,该吸声超结构包括:穿孔板1、下面板2、左框板3、右框板4、前框板5、后框板6、变截面弯折空腔板-ⅰ7、变截面弯折空腔板-ⅱ8、变截面弯折空腔板-ⅲ9、变截面弯折空腔板-ⅳ10、亚毫米至毫米级孔11;穿孔板1和下面板2互相平行,左框板3和右框板4相互平行,前框板5和后框板6相互平行,并与下面板2相垂直;穿孔板1朝向声源,下面板2背向声源,变截面弯折空腔板-ⅰ7、变截面弯折空腔板-ⅱ8、变截面弯折空腔板-ⅲ9、变截面弯折空腔板-ⅳ10、在x方向依次排开,变截面弯折空腔板-ⅰ7和穿孔孔板1相连接,变截面弯折空腔板-ⅱ8和下面板2相连接,变截面弯折空腔板-ⅲ9和穿孔板1相连接,变截面弯折空腔板-ⅳ10和下面板2相连接,在y方向,变截面弯折空腔板-ⅰ7、变截面弯折空腔板-ⅱ8、变截面弯折空腔板-ⅲ9、变截面弯折空腔板-ⅳ10止于前框板5和后框板6,如此构成空腔内折叠空腔,左框板3、右框板4、前框板5、后框板6构成结构外框架,以上所有结构钎焊(或胶粘)在一起;穿孔板1上穿有亚毫米至毫米级孔11,弯折空腔内的4个隔板沿着x方向依次分别和穿孔板1和下面板2连接,形成和穿孔板1和下面板2相互平行的空腔,实现变截面的弯折空腔。
图2是声波进入吸声单元内的声波路线示意图,声波由微穿孔板1进入空腔内部,在弯折空腔进行传输,其传输路径的横截面在弯折处发生变化。
所述穿孔板上的亚毫米至毫米级孔的直径为0.35mm~0.75mm。
所述穿孔板的总穿孔率为1.8%~6.0%。
所述穿孔板、下面板、左框板、右框板、前框板、后框板变截面弯折空腔板-ⅰ、变截面弯折空腔板-ⅱ、变截面弯折空腔板-ⅲ和变截面弯折空腔板-ⅳ的厚度为0.50mm~1.00mm。
所述穿孔板、下面板、左框板、右框板、前框板、后框板、变截面弯折空腔板-ⅰ、变截面弯折空腔板-ⅱ、变截面弯折空腔板-ⅲ和变截面弯折空腔板-ⅳ的材质为金属,如铝、不锈钢等。
在本发明实施例中,吸声超结构单元的外形尺寸是99.00mm×50.00mm×50.00mm,穿孔板1、下面板2、左框板3、右框板4、前框板5、后框板6、变截面弯折空腔板-ⅰ7、变截面弯折空腔板-ⅱ8、变截面弯折空腔板-ⅲ9、变截面弯折空腔板-ⅳ10的厚度都是1.00mm,穿孔板1和下面板2的边长均为97.00mm×48.00mm,左框板3和右框板4的边长均为48.00mm×48.00mm,前框板5和后框板6的边长均为97.00mm×48.00mm,变截面弯折空腔板-ⅰ尺寸为5.00mm×48.00mm,变截面弯折空腔板-ⅱ尺寸为45.00mm×48.00mm,变截面弯折空腔板-ⅲ尺寸为5.00mm×48.00mm,变截面弯折空腔板-ⅳ尺寸为45.00mm×48.00mm,左框板3和变截面弯折空腔板-ⅰ7的间距为17.96mm,变截面弯折空腔板-ⅰ7和变截面弯折空腔板-ⅱ8的间距为64.04mm,变截面弯折空腔板-ⅱ8和变截面弯折空腔板-ⅲ9的间距为5.00mm,变截面弯折空腔板-ⅲ9和变截面弯折空腔板-ⅳ10的间距为5.00mm,变截面弯折空腔板-ⅳ10和右框板4的间距为5.00mm,穿孔板1上穿孔孔径为0.45mm,穿孔率为4.5%,微穿孔位于左框板3和变截面弯折空腔板-ⅰ7之间。
在本实施例中,基于变截面弯折空腔的低频带宽吸声超结构的最高吸声系数和现有的具有相同弯折空腔数的迷宫型空腔吸声超结构的吸声系数相当。
在本实施例中,基于变截面弯折空腔的低频带宽吸声超结构相比于现有的具有相同弯折空腔数的迷宫型空腔吸声超结构,吸声系数的相对带宽(是指吸收系数的半最大值处的两个频率之差与共振频率的比值)由50%提升到83%,且共振频率小于500hz。
以上对本发明的特定实施例进行了说明,但本发明的保护内容不仅仅限定于以上实施例,在本发明的所述技术领域内,只要掌握基本理论,就可以在其技术要旨范围内进行多种多样的变换,如穿孔板的穿孔参数、变截面空腔的弯折空腔个数、变截面弯折空腔板的高度和排列方式;另外,在保证整个元胞结构z方向的外形总尺寸不变的前提下,对前、后左、右框板进行优化,使整个元胞呈多边形等。凡依本发明所申请范围所作的变化与改进等,均应归属于本发明的专利涵盖范围之内。
本文用于企业家、创业者技术爱好者查询,结果仅供参考。