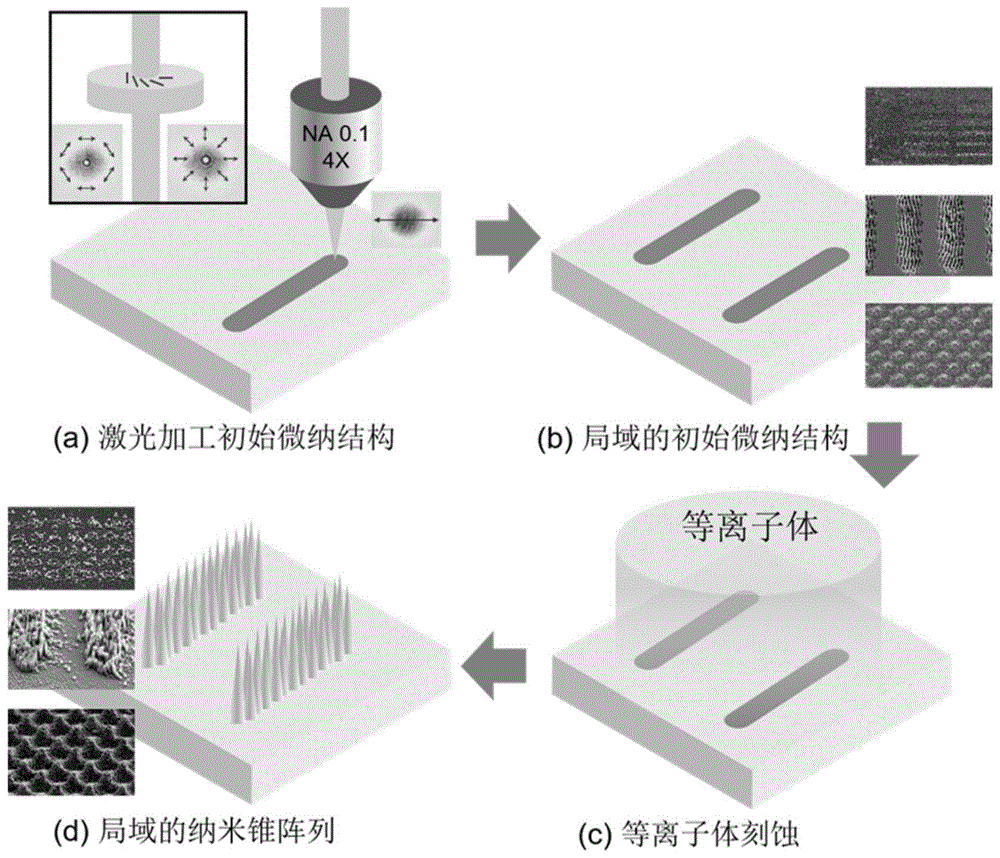
本发明涉及微纳加工领域,具体涉及一种纳米锥形阵列结构及其制备方法。
背景技术:
纳米锥阵列结构广泛用于生物传感、光学减反增透、高表面活性电极等。常用制备方法包括通过干法刻蚀或湿法刻蚀结合光刻掩模如电子束光刻,自组装掩模如聚乙烯颗粒,化学生长掩模如阳极氧化铝等。另外,利用晶体的不同晶向化学刻蚀速度差异也可以采用无掩膜刻蚀方法制备纳米锥阵列,此方法常用于太阳能硅片制绒。
如cn102779747a公开了,一种纳米柱/针森林结构的加工方法,所述纳米柱/针森林结构的加工方法包括如下步骤:a、准备并清洗所选用的衬底;b、在所述衬底土生长一层多晶硅;c、在所述生长有多晶硅的衬底土生长一层侧墙材料层,所述侧墙材料层覆盖于多晶硅层上;d、对上述覆盖侧墙材料层、多晶硅层的衬底进行多晶硅的各向异性刻蚀;e、调节各向异性刻蚀的时间,直至得到所需的纳米柱/针森林结构。有效的克服电子束光刻和聚焦离子束刻蚀技术在批量加工方面的限制,并可有效降低工艺复杂程度,实现具有高可调控性、均匀性的大面积或图形化纳米结构。
cn104386645a公开了一种白掩膜制备随机亚波长宽带减反射微结构的方法,将玻璃基体置于具有混合反应气体的反应室中实施等离子体刻蚀制程,通过控制刻蚀参数使刻蚀过程中在玻璃基体的表面生成的纳米级岛状聚合物薄膜作为刻蚀过程的掩膜,以便在所述的玻璃基体的表面生成随机分布的折射率渐变的锥形减反射微纳结构。无需任何掩膜技术仅需调整反应离子刻蚀的工艺即可在基体表面制备减反射效果明显的亚波长微结构,突破模版技术的诸多限制,大大简化了工艺流程:可以在不同种类的玻璃表面制备亚波长微结构,突破材料的限制;可以应用在任意形状光学元件表面而不会破坏原来结构,有利于实现具有复合功能的光学元件,有利于光学系统的集成化、小型化。
目前,传统方法存在如下不足:在无第二掩模辅助的情况下,仅可获得全覆盖的纳米锥阵列结构,并且存在大面积不均匀、加工工艺过程复杂繁琐等问题,影响了其工艺兼容性、可重复性、微纳尺度应用性。此外,目前未见可直接获得局域纳米锥追阵列结构方法的报道。值得注意的是,在传统半导体刻蚀工艺中存在微掩模现象造成刻蚀表面不均匀的缺陷,该现象会导致样品表面出现较浅的、不均匀、大面积分布的纳米锥阵列,影响了制备结果的表面形貌。
然而现有的制备方法在局部微纳结构制备中需要掩膜或预先设置局部层来实现了局部微纳结构的制备,存在制备过程复杂,制备方法精度差等问题。
技术实现要素:
鉴于现有技术中存在的问题,本发明的目的在于提供一种纳米锥形阵列结构及其制备方法,该制备方法兼容性好、制备区域灵活可控,可极大提升纳米锥阵列结构的制备工艺精度。还可解决现有技术工艺复杂、不可直接局域制备微纳结构的技术问题。
为达此目的,本发明采用以下技术方案:
第一方面,本发明提供了一种基于激光辅助干法刻蚀的纳米锥形阵列结构的制备方法,所述制备方法包括如下步骤:
(1)利用超快激光对基底进行加工,之后清洗得到中间基底;
(2)将步骤(1)得到的所述中间基底进行等离子体刻蚀,得到所述纳米锥形阵列结构。
本发明提供的方法,采用超快激光在表面制备微纳结构,在等离子体刻蚀过程中并利用微掩模效应在微纳结构区域的增强效果,即利用现有技术中缺陷制备了深宽比较大的纳米锥阵列结构,该方法兼容性好、制备区域灵活可控,可极大提升纳米锥阵列结构的制备工艺精度。
作为本发明优选的技术方案,步骤(1)所述超快激光包括飞秒激光、皮秒激光或纳秒激光中的1种。
优选地,步骤(1)所述超快激光的脉宽为脉宽为10-15-10-9s,例如可以是10-15s、10-14s、10-13s、10-12s、10-11s、10-10s或10-9s等,但不限于所列举的数值,该范围内其他未列举的数值同样适用。
优选地,步骤(1)所述超快激光的波长为300-1100nm,例如可以是300nm、400nm、500nm、600nm、700nm、800nm、900nm、1000nm或1100nm等,但不限于所列举的数值,该范围内其他未列举的数值同样适用。
优选地,步骤(1)所述超快激光的重频为0.1-10khz,例如可以是0.1khz、0.5khz、1khz、2khz、3khz、4khz、5khz、6khz、7khz、8khz、9khz或10khz等,但不限于所列举的数值,该范围内其他未列举的数值同样适用。
作为本发明优选的技术方案,步骤(1)所述基底包括碳化硅基底。
优选地,步骤(1)所述基底加工前进行洗涤。
优选地,所述洗涤中的洗涤剂包括丙酮、异丙醇、氢氟酸或水中的1种或至少2种的组合。
优选地,所述洗涤的时间≥30min,例如可以是30min、40min、50min、60min、70min或80min等,但不限于所列举的数值,该范围内其他未列举的数值同样适用。
优选地,所述洗涤中的洗涤剂包括丙酮或异丙醇中的1种时采用超声清洗。
优选地,所述超声清洗的时间≥7min,例如可以是7min、8min、9min、10min、11min、12min或13min等,但不限于所列举的数值,该范围内其他未列举的数值同样适用。
作为本发明优选的技术方案,步骤(1)所述清洗中的洗涤剂包括丙酮、异丙醇、氢氟酸或水中的1种或至少2种的组合。
优选地,步骤(1)所述清洗的时间≥30min,例如可以是30min、40min、50min、60min、70min或80min等,但不限于所列举的数值,该范围内其他未列举的数值同样适用。
优选地,步骤(1)所述清洗中的洗涤剂包括丙酮或异丙醇中的1种时采用超声清洗。
优选地,所述超声清洗的时间≥7min,例如可以是7min、8min、9min、10min、11min、12min或13min等,但不限于所列举的数值,该范围内其他未列举的数值同样适用。
本发明,中的洗涤或清洗过程可采用多种洗涤剂或清洗剂组合的方式进行,只需保证清洗时间达到规定时间即可,单洗涤剂或组合的洗涤方式不会影响产品的性能。
作为本发明优选的技术方案,步骤(1)所述加工的方式包括点加工、线加工或面加工中的一种。
优选地,步骤(1)所述加工中超快激光的能量密度为0.5-10j/cm2,例如可以是0.5j/cm2、1j/cm2、2j/cm2、3j/cm2、4j/cm2、5j/cm2、6j/cm2、7j/cm2、8j/cm2、9j/cm2或10j/cm2等,但不限于所列举的数值,该范围内其他未列举的数值同样适用。
本发明中,所述面加工可以采用多次线加工实现或采用别的方式实现面加工。
优选地,所述点加工中至少重复施加50个脉冲,例如可以是50个、60个、70个、80个、90个或100个等,但不限于所列举的数值,该范围内其他未列举的数值同样适用。
优选地,所述线加工中的扫描速度为20-3000μm/s,例如可以是20μm/s、20μm/s、40μm/s、60μm/s、80μm/s、100μm/s、500μm/s、1000μm/s、1500μm/s、2000μm/s、2500μm/s或3000μm/s等,但不限于所列举的数值,该范围内其他未列举的数值同样适用。
作为本发明优选的技术方案,步骤(2)所述等离子体刻蚀中的刻蚀气体包括六氟化硫和氧气。
优选地,所述刻蚀气体中六氟化硫和氧气的体积比为1:(0.125-0.8),例如可以是1:0.125、1:0.15、1:0.2、1:0.25、1:0.3、1:0.35、1:0.4、1:0.45、1:0.5、1:0.55、1:0.6、1:0.65、1:0.7、1:0.75或1:0.8等,但不限于所列举的数值,该范围内其他未列举的数值同样适用。
本发明中,刻蚀过程中,sf6作为主要刻蚀气体和si反应产生挥发物质,o2作为辅助刻蚀气体和c反应产生挥发物质,同时还和sf6引入的s反应生成雾化颗粒去除,稍过量的o2会和si、c复合生成si-c-o颗粒,作为微掩模的主要掩模颗粒,成为刻蚀中阻挡刻蚀的掩模阵列。
作为本发明优选的技术方案,步骤(2)所述等离子体刻蚀中刻蚀气体的流量为10-5-10-4m3/s,例如可以是10-5m3/s、2x10-5m3/s、3x10-5m3/s、4x10-5m3/s、5x10-5m3/s、6x10-5m3/s、7x10-5m3/s、8x10-5m3/s、9x10-5m3/s或10-4m3/s等,但不限于所列举的数值,该范围内其他未列举的数值同样适用。
本发明中,刻蚀气体的流量和比例控制,可通过单独控制流量实现但需保证单独气体的流量不能超过刻蚀中刻蚀气体的总流量,即六氟化硫和氧气的流量均符合10-5-10-4m3/s,也可先将气体按比例混合,然后控制流量实现。
优选地,步骤(2)所述等离子体刻蚀中刻蚀气体的压强为0.67-6.67pa,例如可以是0.67pa、1pa、2pa、3pa、4pa、5pa、6pa或6.67pa等,但不限于所列举的数值,该范围内其他未列举的数值同样适用。
优选地,步骤(2)所述等离子体刻蚀中线圈的功率为100-300w,例如可以是100w、150w、200w、250w或300w等,但不限于所列举的数值,该范围内其他未列举的数值同样适用。
优选地,步骤(2)所述等离子体刻蚀中的偏压功率为20-100w,例如可以是20w、30w、40w、50w、60w、70w、80w、90w或100w等,但不限于所列举的数值,该范围内其他未列举的数值同样适用。
作为本发明优选的技术方案,步骤(2)所述等离子体刻蚀的时间为3-5min,例如可以是3min、3.5min、4min、4.5min或5min等,但不限于所列举的数值,该范围内其他未列举的数值同样适用。
作为本发明优选的技术方案,所述制备方法包括如下步骤:
(1)利用超快激光对基底进行加工,之后清洗得到中间基底;
(2)将步骤(1)得到的所述中间基底进行等离子体刻蚀,得到所述纳米锥形阵列结构;
步骤(2)所述等离子体刻蚀中的刻蚀气体包括六氟化硫和氧气;所述刻蚀气体中六氟化硫和氧气的体积比为(0.125-0.8):1;刻蚀时间为3-5min。
第二方面,本发明提供了如第一方面所述制备方法制备得到的纳米锥形阵列结构,所述纳米锥形的深宽比为1.5-30,例如可以是1.5、2、5、10、12、14、16、18、20、25或30等,但不限于所列举的数值,该范围内其他未列举的数值同样适用。
与现有技术方案相比,本发明至少具有以下有益效果:
(1)在等离子体刻蚀过程中利用微掩模效应在微纳结构区域的增强效果,制备了高深宽比的纳米锥阵列结构,该方法兼容性好、制备区域灵活可控,可极大提升纳米锥阵列结构的制备工艺精度,可获得的纳米锥阵列特征尺寸直径30-500nm,高度300-1500nm,深宽比1.5-30,制备区域最小到1μm2。
(2)本发明所述的制备方法制备得到的纳米锥阵列结构,可实现局域化、大面积加工的控制,并且内部均匀密集,其结构具有良光学抗反射性能以及表面亲疏水性能,具有广泛的应用前景,纳米锥形的深宽比为1.5-30。
附图说明
图1是本发明实施例提供纳米锥形阵列结构的制备方法的示意图;
图2是本发明实施例1中飞秒激光加工后基底的扫描电镜照片;
图3是本发明实施例1中所得纳米锥形阵列结构的扫描电镜照片;
图4是本发明实施例2中飞秒激光加工后基底的扫描电镜照片;
图5是本发明实施例2中所得纳米锥形阵列结构的扫描电镜照片;
图6是本发明实施例3中飞秒激光加工后基底的扫描电镜照片;
图7是本发明实施例3中所得纳米锥形阵列结构的扫描电镜照片。
下面对本发明进一步详细说明。但下述的实例仅仅是本发明的简易例子,并不代表或限制本发明的权利保护范围,本发明的保护范围以权利要求书为准。
具体实施方式
为更好地说明本发明,便于理解本发明的技术方案,本发明的典型但非限制性的实施例如下:
实施例1
本实施例提供一种基于激光辅助干法刻蚀的纳米锥形阵列结构的制备方法,具体步骤如下:
步骤1:碳化硅基底上制备初始微纳结构,脉宽300fs、波长520nm、重频1khz的线偏振飞秒激光由激光器出射,经过光路,通过4倍物镜聚焦在碳化硅表面进行线加工(见图1),偏振方向和扫描方向垂直,扫描速度为2mm/s,能流密度为0.33j/cm2,扫描线间距为2μm,制备得到初始微纳结构,是微弱的单点烧蚀(见图2);
步骤2:清洗激光加工后的碳化硅基底,用40%体积比浓度的氢氟酸浸泡10分钟,再浸泡在丙酮中并进行超声清洗10分钟,再浸泡在异丙醇中并进行超声清洗10分钟,最后用氮气吹干;
步骤3:采用等离子体刻蚀处理碳化硅基底,使用电感耦合等离子体设备。对具有初始微纳结构的碳化硅基底采取如下的气体比例、腔室工作气压以及刻蚀时间,对应条件如下:
sf6气体流量7×10-5m3/s,o2气体流量2×10-5m3/s,线圈功率150w,偏压功率50w,刻蚀气体的压强为1.07pa,刻蚀时间900s。
等离子体刻蚀后在初始微纳结构区域得到周期性均匀分布的纳米锥结构(见图3)。以上给出了激光辅助微掩模刻蚀制备选定区域/大面积纳米锥阵列结构的工艺参数研究的实例。
检查最终样品效果:采用扫描电镜进行微观扫描检测,扫描电镜照片如图2和图3所示,刻蚀前后,在分布有初始微纳结构的区域基底表面,形成了周期性均匀分布的纳米锥,特征的纳米锥直径在300-400nm之间,高度在600-800nm之间,深宽比在1.5-2.7之间。
实施例2
本实施例提供一种基于激光辅助干法刻蚀的纳米锥形阵列结构的制备方法,具体步骤如下:
步骤1:碳化硅基底上制备初始微纳结构,脉宽300fs、波长520nm、重频1khz的线偏振飞秒激光由激光器出射,经过光路,通过4倍物镜聚焦在碳化硅表面进行线加工(见图1),偏振方向和扫描方向垂直,扫描速度为200μm/s,能流密度为0.53j/cm2,扫描线间距为3μm,制备得到初始微纳结构,是低频率的激光诱导表面周期性结构(见图4);
步骤2:清洗激光加工后的碳化硅基底,用40%体积比浓度的氢氟酸浸泡10分钟,再浸泡在丙酮中并进行超声清洗10分钟,再浸泡在异丙醇中并进行超声清洗10分钟,最后用氮气吹干;
步骤3:采用等离子体刻蚀处理碳化硅基底,使用电感耦合等离子体设备。对具有初始微纳结构的碳化硅基底采取如下的气体比例、腔室工作气压以及刻蚀时间,对应条件如下:
sf6气体流量6×10-5m3/s,o2气体流量3×10-5m3/s,线圈功率200w,偏压功率30w,等离子体刻蚀中刻蚀气体的压强为1.07pa,刻蚀时间900s。
等离子体刻蚀后在初始微纳结构区域得到周期性均匀分布的纳米锥结构(见图5)。以上给出了激光辅助微掩模刻蚀制备选定区域/大面积纳米锥阵列结构的工艺参数研究的实例。
检查最终样品效果:采用扫描电子显微镜进行微观扫描检测,扫描电镜照片详见图4和图5,从图中可知,刻蚀前后,在分布有初始微纳结构的区域基底表面,形成了周期性均匀分布的纳米锥,特征的纳米锥直径在300-400nm之间,高度在1200-1500nm之间,深宽比在3-5之间。
实施例3
本实施例提供一种基于激光辅助干法刻蚀的纳米锥形阵列结构的制备方法,具体步骤如下:
步骤1:碳化硅基底上制备初始微纳结构,脉宽300fs、波长520nm、重频1khz的线偏振飞秒激光由激光器出射,经过光路,通过s波片生成环形场强分布的角向偏振光,通过4倍物镜聚焦在碳化硅表面(见图1),进行脉冲点加工,单点加工重复施加50个脉冲,加工点位置间距水平横向10μm和纵向5μm,六边形分布点阵,单脉冲能流密度为2.25j/cm2,制备得到初始微纳结构,每个单点是径向分布的高频率激光诱导表面周期性结构(见图6);
步骤2:清洗激光加工后的碳化硅基底,用40%体积比浓度的氢氟酸浸泡10分钟,再浸泡在丙酮中并进行超声清洗10分钟,再浸泡在异丙醇中并进行超声清洗10分钟,最后用氮气吹干;
步骤3:采用等离子体刻蚀处理碳化硅基底,使用电感耦合等离子体设备。对具有初始微纳结构的碳化硅基底采取如下的气体比例、腔室工作气压以及刻蚀时间,对应条件如下:
sf6气体流量6×10-5m3/s,o2气体流量3×10-5m3/s,线圈功率200w,偏压功率30w,刻蚀气体的压强为6.67pa,刻蚀时间180s。
等离子体刻蚀后在初始微纳结构区域得到周期性均匀分布的纳米锥结构(见图7)。以上给出了激光辅助微掩模刻蚀制备选定区域/大面积纳米锥阵列结构的工艺参数研究的实例。
检查最终样品效果:采用扫描电子显微镜进行微观扫描检测,扫描电镜照片如图6和图7所示,刻蚀前后,在分布有初始微纳结构的区域基底表面,形成了周期性均匀分布的纳米锥,特征的纳米锥直径在35-50nm之间,高度在600-800nm之间,深宽比在15-20之间。
对比例1
与实施例1的区别仅在于对基底不采用超快激光进行处理,所得样品上分布不均匀、零散的纳米锥,是由基底污渍、表层缺陷造成的,且深宽比小于1。
对比例2
与实施例1的区别仅在于对将飞秒脉冲激光替换为连续激光,所得样品表面,由于热影响区域大,无均匀微纳结构或者局部小范围改性生成。
对比例3
与实施例1的区别仅在于对将刻蚀气体中的六氟化硫替换为等体积的氟气进行处理,等离子体刻蚀后表面无法生成纳米锥阵列,表面被刻蚀,刻蚀速度慢,表面粗糙。
对比例4
与实施例1的区别仅在于对将刻蚀气体中的氧气用等体积的六氟化硫代替进行处理,等离子体刻蚀后表面无法生成纳米锥阵列,表面被刻蚀后进一步平滑。
对比例5
与实施例1的区别仅在于六氟化硫和氧气的体积比为1:2,等离子体刻蚀后表面无法生成纳米锥阵列,表面被刻蚀,刻蚀速度很慢,进一步轻微平滑。
通过上述实施例和对比例的结果可知,本发明提供的方法,采用超快激光在表面制备微纳结构,在等离子体刻蚀过程中并利用微掩模效应在微纳结构区域的增强效果,即利用现有技术中缺陷制备了高深宽比的纳米锥阵列结构,该方法兼容性好、制备区域灵活可控,可极大提升纳米锥阵列结构的制备工艺精度。
申请人声明,本发明通过上述实施例来说明本发明的详细结构特征,但本发明并不局限于上述详细结构特征,即不意味着本发明必须依赖上述详细结构特征才能实施。所属技术领域的技术人员应该明了,对本发明的任何改进,对本发明所选用部件的等效替换以及辅助部件的增加、具体方式的选择等,均落在本发明的保护范围和公开范围之内。
以上详细描述了本发明的优选实施方式,但是,本发明并不限于上述实施方式中的具体细节,在本发明的技术构思范围内,可以对本发明的技术方案进行多种简单变型,这些简单变型均属于本发明的保护范围。
另外需要说明的是,在上述具体实施方式中所描述的各个具体技术特征,在不矛盾的情况下,可以通过任何合适的方式进行组合,为了避免不必要的重复,本发明对各种可能的组合方式不再另行说明。
此外,本发明的各种不同的实施方式之间也可以进行任意组合,只要其不违背本发明的思想,其同样应当视为本发明所公开的内容。
本文用于企业家、创业者技术爱好者查询,结果仅供参考。